“A7075アルミニウム合金の切削性とは?加工しやすさを徹底解説”
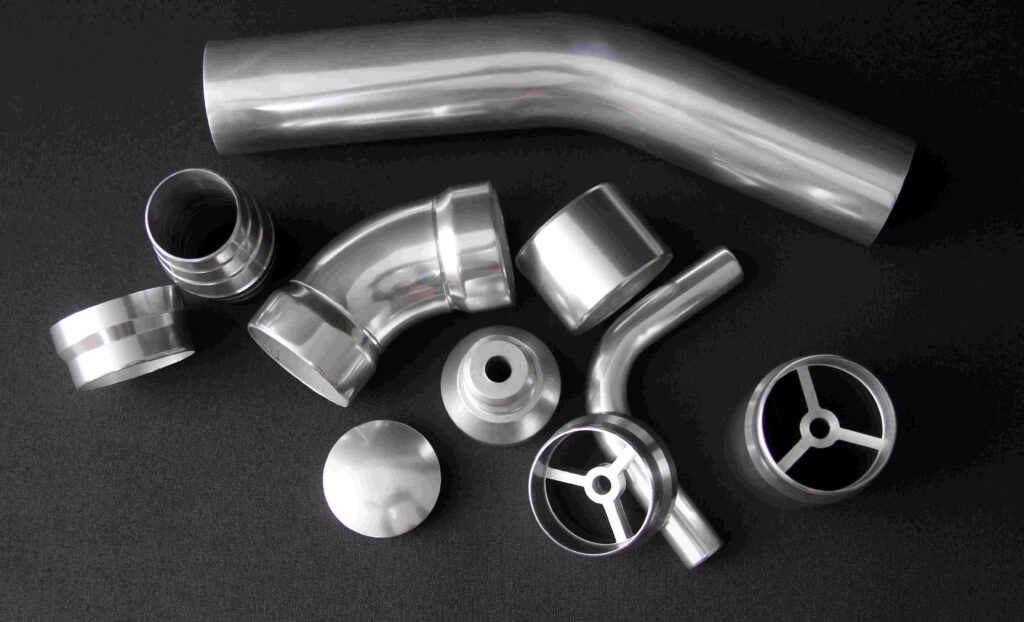
A7075アルミニウム合金は、工業製品や航空機部品など様々な分野で幅広く使用されている素材です。その中でも、切削性は加工において重要な要素の一つです。A7075アルミニウム合金の切削性について知識を深めることで、加工作業を効率的かつ効果的に行うことができます。本記事では、A7075アルミニウム合金の切削性に焦点を当て、加工しやすさについて徹底解説します。切削性の基本から具体的な加工方法まで、A7075アルミニウム合金の特性を理解し、加工に役立てるための情報をお届けします。この記事を通じて、A7075アルミニウム合金に対する理解を深め、より良い加工結果を実現する手助けとなることでしょう。
Contents
A7075アルミニウム合金とは
A7075アルミニウム合金は、高強度と軽量性を特徴とするアルミニウム合金であり、特に航空宇宙産業や高性能製品で広く利用されています。この合金の基本情報、物理的・化学的特性、そして主な用途について詳しく説明します。A7075アルミニウム合金の基本情報
- 材質分類:アルミニウム-亜鉛-マグネシウム-銅合金(7XXX系)
- 主成分:アルミニウムを基材とし、亜鉛(Zn)、マグネシウム(Mg)、銅(Cu)を添加。
- 特徴:高い強度、優れた疲労特性、比較的軽量。
A7075の物理的・化学的特性
- 物理的特性
- 密度:2.81 g/cm³
- 引張強度(T6処理時):570~580 MPa
- 降伏強度(T6処理時):500~510 MPa
- 伸び率:10~12%(熱処理状態による)
- 化学的特性
- 耐食性:比較的劣るが、T73処理で耐食性を改善可能。
- 熱膨張率:23.2 × 10⁻⁶ /K
- 導電率:約36% IACS(銅基準での導電性)。
- 加工性
- 切削加工性は良好。
- 溶接性はあまり良くないため、特殊な溶接方法や接合技術が必要。
アルミニウム合金A7075の用途
A7075の高い強度と軽量性を活かし、以下のような分野で利用されています:- 航空宇宙分野
- 航空機の構造部材や翼、フレーム部分。
- 軽量化と高強度を必要とする部分に適用。
- 自動車・モータースポーツ
- 高性能車両のサスペンション部品やホイール。
- 耐久性と軽量化が求められるパーツに採用。
- スポーツ用品
- 自転車フレーム、ゴルフクラブ、アーチェリー部品など。
- 高強度と軽量性が競技性能に直結する製品。
- 産業機器
- 高強度を必要とするロボットアームやフレーム。
- 機械部品、治工具など。
超々ジュラルミン(A7075)の切削性
超々ジュラルミン(A7075)は、高い強度と軽量性を持つアルミニウム合金であり、航空宇宙産業や自動車産業など、さまざまな分野で利用されています。この合金の切削性について理解することで、効率的で高精度な加工を実現できます。切削性とは
切削性とは、材料の加工のしやすさを示す特性です。これには、工具の摩耗速度、表面仕上げの品質、加工速度、加工中の熱の発生量などの要素が関係します。切削性が高い材料は、工具に対する負荷が少なく、スムーズな加工が可能です。 A7075は、熱処理によって強度が向上する一方、適切な加工条件を選ぶことで、十分な切削性を保つことができます。A7075の切削性の評価
A7075は高強度を持つため、切削性は中程度とされています。ただし、熱処理状態(例:T6やT651)によって特性が変化し、加工性にも影響を及ぼします。以下の点が特徴です:- T6処理状態:高い強度と適度な加工性のバランスが取れているため、一般的な加工に適しています。
- 高硬度の影響:強度が高いため、工具への負荷が増加し、適切な工具選定が重要になります。
- 表面仕上げ:適切な条件下では非常に滑らかな表面を得ることが可能です。
切削時の注意点と工夫
- 適切な工具の選定 高硬度材料向けの工具(超硬工具やダイヤモンドコーティング工具)を使用することで、工具摩耗を軽減し、加工精度を向上させることができます。
- 加工条件の最適化
- 切削速度:高速切削が可能ですが、熱の発生を抑えるための冷却が必要です。
- 送り速度:表面仕上げを重視する場合には、低速送りが推奨されます。
- 切込み深さ:材料の強度に応じて適切に調整します。
- 冷却と潤滑の徹底 切削中に発生する熱を抑えるため、冷却性能の高い切削液を使用します。これにより、熱変形を防ぎ、工具寿命を延ばせます。
- 振動の抑制 ワークピースをしっかりと固定し、振動を最小限に抑えることで、加工精度と表面品質を向上させることができます。
- 加工後の応力緩和 加工後には、残留応力を除去するために熱処理を行うことが推奨されます。これにより、部品の長期的な寸法安定性が向上します。
超々ジュラルミン(A7075)の加工方法
超々ジュラルミン(A7075)は高強度と軽量性を兼ね備えたアルミニウム合金であり、航空宇宙や自動車産業をはじめとする多くの分野で広く利用されています。この合金を最大限に活用するためには、その加工適性を理解し、適切な技術を選択することが不可欠です。A7075の加工適性
A7075は高い強度を持つ一方で、加工性は中程度とされています。例えば、この材料は高硬度ゆえに工具の摩耗が起きやすいことが課題として挙げられます。また、T6やT651のような熱処理状態によって加工性が変化し、加工中の熱や歪みへの対処が求められることもあります。そのため、加工工程では寸法の安定性を確保するための対策が重要です。様々な加工技術とA7075
A7075は切削加工、フライス加工、旋盤加工などのさまざまな加工方法に適用できます。例えば、切削加工では高硬度向けの工具を選び、切削液を適切に使用することで、熱の発生を抑えながら高品質な表面仕上げを実現することができます。フライス加工では、高速加工が可能ですが、振動を抑えるために固定具の工夫が必要です。また、旋盤加工では、均一な表面仕上げを目指して冷却や潤滑をしっかり管理することがポイントとなります。 穴あけ加工においては、切屑の排出効率を高めるために適切なドリルと切削液を選ぶことが重要です。一方、溶接加工はA7075の難点の一つであり、特殊な溶接技術や追加の熱処理を考慮する必要があります。また、仕上げ工程では、耐腐食性を向上させるために陽極酸化処理や塗装が施されることが一般的です。これらの処理の前には、十分なクリーニングを行うことで最終製品の品質が向上します。加工精度と品質管理
A7075を加工する際には、精度を高めると同時に品質管理を徹底することが求められます。例えば、工具の摩耗を定期的にチェックし、必要に応じて交換することで、加工精度を維持することができます。また、加工中や加工後に寸法測定を行い、設計仕様を確実に満たしているか確認することも重要です。 さらに、加工後に発生する残留応力を熱処理で除去することで、部品の長期的な安定性を確保することが可能です。加工条件や工具の使用履歴を記録・管理することにより、一貫した品質を保ちながら効率的な製造が実現します。 A7075の加工では、これらの特性を十分に理解し、適切な技術と管理手法を組み合わせることで、優れた性能と信頼性を持つ製品を生産することが可能です。アルミニウム合金A7075の特徴
アルミニウム合金A7075は、高い強度と軽量性を兼ね備えたアルミニウム合金の一つで、特に航空宇宙や高性能機器の分野で広く使用されています。この合金は、亜鉛を主成分とする7000番台の代表的な材料であり、優れた機械的特性や熱処理による性能向上が特徴です。A7075の機械的特性
A7075は、特に引張強度や降伏強度に優れており、その値は熱処理状態によってさらに向上します。T6やT651などの熱処理が施された状態では、引張強度が500MPaを超えることが一般的です。また、優れた剛性により、高負荷がかかる用途にも対応可能です。一方で、延性がやや低いことが課題とされており、設計や加工の際にはその特性を考慮する必要があります。 機械的特性の一例:- 引張強度:500~580 MPa(T6処理の場合)
- 降伏強度:430~510 MPa
- 硬度:150~175 HB(ブリネル硬さ)
A7075の熱処理とその効果
A7075は熱処理による性質向上が可能な材料であり、特に人工時効処理(T6処理)がよく行われます。この処理により、合金内部に微細な析出物が形成され、引張強度と降伏強度が大幅に向上します。また、T651のように応力除去を目的とした処理を組み合わせることで、残留応力を抑えた加工が可能です。 さらに、熱処理によって切削性や機械加工性も改善されるため、製造工程での効率化が図れます。ただし、熱処理後の寸法安定性や表面品質の管理が求められます。A7075合金の耐食性
A7075は機械的特性が優れている一方で、耐食性がやや劣るという課題があります。この特性は、主成分である亜鉛の影響によるもので、特に腐食環境下では注意が必要です。そのため、耐食性を向上させるための表面処理が一般的に施されます。 代表的な表面処理には以下の方法があります:- 陽極酸化処理(アルマイト処理):酸化皮膜を形成し、耐食性を向上。
- 防食コーティング:塗装や特殊フィルムで保護。
- 防錆剤の使用:使用環境に応じた適切な保護策。
A7075の用途と重要性
A7075の特徴である高強度、軽量性、加工性により、航空機の構造材、自動車部品、スポーツ用品(ゴルフクラブ、登山用具)など、多岐にわたる分野で活用されています。この合金の性能を最大限に引き出すには、材料特性を理解し、適切な熱処理や表面処理を組み合わせることが重要です。超々ジュラルミン(A7075)と他素材との比較
A7075は、航空宇宙や高負荷部品に多く使用される高強度アルミニウム合金で、その性能は他のアルミニウム合金や鉄鋼材料と比較しても非常に優れています。ここでは、A7075と他のアルミニウム合金、および鉄や鋼との比較を行い、素材選びのポイントについて解説します。A7075と他のアルミニウム合金との比較
A7075は、7000番台アルミニウム合金に分類され、主に亜鉛(Zn)を合金元素として使用しています。そのため、強度が非常に高く、航空機の構造部品や高強度を必要とする部品に多く使われます。 他のアルミニウム合金と比較した場合、以下の特徴があります:- A2024(2024合金):A2024は、銅(Cu)を主成分としたアルミニウム合金で、強度がA7075に近いものの、耐食性は劣ります。特に湿気の多い環境で使用される場合、A7075の方が耐食性に優れています。A2024は主に航空機の構造材に使用され、衝撃強度が求められる場所ではA7075が好まれます。
- A6061(6061合金):A6061は、シリコンとマグネシウムを主成分とするアルミニウム合金で、加工性が非常に良く、一般的な構造部品に広く使用されています。しかし、A7075に比べて強度が低いため、軽量である必要があり、加工がしやすいといった特性が求められる部品に向いています。
A7075と鉄や鋼との比較
A7075はアルミニウム合金であり、鉄や鋼と比較した場合にいくつかの顕著な違いがあります。主な比較ポイントは以下の通りです:- 強度と重量:A7075は、鉄や鋼に匹敵する高強度を誇りながら、非常に軽量です。鉄鋼の密度は7.85 g/cm³に対して、A7075は2.81 g/cm³と約三分の一の重さです。これにより、A7075は軽量化が求められる航空機や自動車部品に理想的な素材となります。
- 耐食性:A7075は鉄や鋼と比べて耐食性が劣るため、使用環境によっては表面処理が必要です。一方、鉄や鋼は錆びやすいため、コーティングや防錆処理を施す必要がありますが、耐食性を高める技術が進んでおり、環境に適した処理を施せば長期間使用が可能です。
- 加工性:A7075はその高強度がゆえに加工が難しく、切削加工の際に高精度な機械や工具が求められます。鉄や鋼に比べて加工時の摩耗が激しく、加工コストが高くなることがあります。しかし、加工精度が確保できる場合、A7075の優れた強度と軽量性が際立ちます。
素材選びのポイント
素材選びは、主に使用する環境や求められる性能によって決まります。以下のポイントを考慮すると良いでしょう:- 強度と軽さ:軽量かつ高強度が求められる用途には、A7075が最適です。特に航空機や自動車の高強度部品では、その特性が活かされます。
- 耐食性:使用環境が湿気の多い場所や海上であれば、A7075は表面処理を施すことで耐食性を向上させ、鉄や鋼に対抗できます。
- 加工性:加工性を重視する場合、A6061などのアルミニウム合金や、加工しやすい鋼を選ぶと良いでしょう。高精度な加工が求められる場合には、A7075の優れた機械的特性を最大限活用することが可能です。
- コスト:A7075は高強度である一方、材料費や加工費が高くなる傾向があります。そのため、コスト面も考慮し、最適な素材を選定することが重要です。