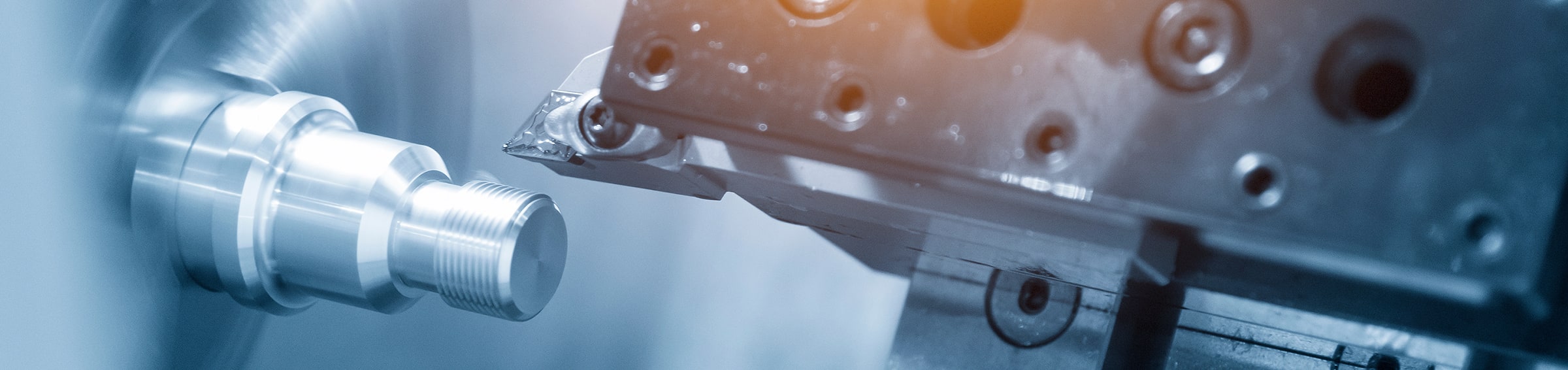
コラム column
A6061アルミニウム合金の特性解説!比重と強度の基礎知識
A6061アルミニウム合金は、航空機や自動車など幅広い産業で使用される重要な素材です。その優れた特性や強度により、多くの製品に採用されています。本記事では、A6061アルミニウム合金の特性に焦点を当て、比重や強度などの基礎知識を詳しく解説します。この合金がどのように利用され、どのような特性を持っているのかを理解することで、その重要性や利点について深く学ぶことができるでしょう。それでは、A6061アルミニウム合金の世界へようこそ。
Contents
A6061アルミニウム合金の概要
A6061アルミニウム合金は、広く使用されているアルミニウム合金の一つで、優れた強度、耐食性、加工性を持つため、多岐にわたる分野で利用されています。特に、航空機、車両、建材、そして日常的な製品の部品として重要な素材です。以下では、A6061アルミニウム合金の特徴とその位置づけについて詳しく説明します。A6061アルミニウム合金とは
A6061は、アルミニウムを基にした合金で、主にマグネシウムとシリコンを含んでいます。これにより、耐食性、強度、加工性のバランスが非常に優れています。A6061は、一般的に強度と軽量性が求められる用途で使用され、その性質から航空機、車両、スポーツ用品など様々な産業において重要な役割を果たしています。A6061の基本的な特性
A6061アルミニウム合金の基本的な特性は、以下の点にまとめられます:- 強度: A6061は良好な機械的強度を持ち、特に強度と重さのバランスが取れた合金です。
- 耐食性: マグネシウムとシリコンの成分により、耐食性が優れています。特に湿気の多い環境や海水中でも安定した耐腐食性を発揮します。
- 加工性: 高い可加工性を有し、溶接や切削、押出しなどの多様な加工方法に対応可能です。
- 軽量性: アルミニウム合金の特性により、軽量でありながら十分な強度を提供します。
- 熱処理: A6061は熱処理によって強度が増すため、成形後に熱処理を施すことで、要求される強度に応じた特性を得ることができます。
アルミニウム合金としての位置づけ
A6061は、アルミニウム合金の中でも最も広く使用されている合金の一つです。特に、強度と耐食性のバランスが取れているため、一般的なアルミニウム合金よりも優れた特性を持っています。そのため、構造材としての用途だけでなく、精密な部品や加工品にも利用されます。 その利用範囲は非常に広く、例えば、航空宇宙産業、海洋環境、車両の部品、電子機器、スポーツ用品などで見られます。また、成形性に優れており、異なる形態での製品加工が可能です。特に、押出し加工が得意な合金としても知られています。A6061の比重とその意味
A6061アルミニウム合金の比重は、材料選定や製品設計において重要な要素です。比重は、物質の密度と水の密度を比較した値であり、素材の重量に対する理解を深め、適切な選択を行うために役立ちます。以下では、比重に関する基礎知識とA6061の比重の特徴、そしてその意味について解説します。比重の基礎知識
比重(Specific Gravity)とは、物質の密度が水の密度に対してどれくらい大きいかを示す無次元の数値です。物質の密度はその質量と体積に依存し、比重は以下の式で求められます: [ \text{比重} = \frac{\text{物質の密度}}{\text{水の密度}} ] 水の密度は約1g/cm³(1,000kg/m³)と定義されているため、比重が1を超える場合、その物質は水よりも重く、1未満の場合は水より軽いことを示します。A6061の比重と利点
A6061アルミニウム合金の比重はおおよそ2.70g/cm³です。この値は、他の金属材料(例えば鉄や銅)に比べてかなり軽いです。鉄の比重は約7.85g/cm³、銅の比重は約8.96g/cm³であるため、A6061は軽量な金属であることがわかります。 A6061の比重が低いことには以下の利点があります:- 軽量化: 製品の総重量を抑えることができるため、輸送コストの削減や、航空機や車両の燃費向上、運搬の容易さなどが実現できます。
- 強度対重量比の向上: 軽量でありながら高い強度を持つため、強度と軽さのバランスが取れた製品を製造できます。これにより、設計の自由度が広がります。
- 耐久性と持続可能性: 軽量かつ耐食性が高いため、長期間にわたって安定した性能を維持できます。特に海洋や航空機部品などの過酷な環境下で優れた耐久性を発揮します。
比重が製品選定における意味合い
製品選定において、比重は重要な指標の一つです。A6061のような軽量な材料を選ぶことは、以下のような意味合いを持ちます:- コスト削減: 軽量化により輸送コストが削減され、製品全体のコストを抑えることができます。
- 強度・重量の最適化: 比重が低いことで軽量な部品を作成でき、強度を保ちながらも製品の重量を最小限に抑えることができます。これが特に重要な役割を果たすのは航空機や車両などの軽量化が求められる分野です。
- 環境への配慮: 軽量化はエネルギー消費を減らし、製品のライフサイクル全体における環境負荷を減少させます。特に輸送時のエネルギー効率向上や、燃費向上への貢献があります。
A6061の機械的性質
A6061アルミニウム合金は、その優れた機械的性質から多くの産業で使用されています。特に強度や耐久性、加工性において非常に優れたバランスを持っており、軽量でありながら高い性能を発揮します。ここでは、A6061の強度の概要と、その強度に影響を与える要因について解説します。強度とは何か?
強度とは、材料が外力を受けたときに破壊せずに耐えることができる能力を指します。具体的には、以下の2つの強度が特に重要です:- 引張強度(Tensile Strength): 材料が引っ張りに耐えられる最大の応力を示します。引張強度が高い材料は、引っ張られる力に対して耐久性が高いとされます。
- 降伏強度(Yield Strength): 材料が永久変形(塑性変形)を開始する前の最大応力を指します。降伏強度が高いと、材料は高い負荷を受けても変形しにくくなります。
A6061の強度と応用
A6061アルミニウム合金は、その強度と加工性において非常に優れており、次のような特性があります:- 引張強度: 約 290 MPa(メガパスカル)程度で、軽量ながらも強度を保持します。
- 降伏強度: 約 240 MPa程度で、塑性変形を起こすことなく、高い負荷を受けることができます。
- 航空機産業: 軽量で高強度な材料が求められるため、航空機のフレームや構造部品、翼などに使用されます。
- 自動車産業: 車両の構造部品やエンジン部品、ボディパネルなどに利用され、車両の軽量化と強度向上を実現します。
- 建築・建設: 高い耐食性と強度が求められる建築用部品や構造物に使用されます。
- スポーツ用品: 高強度と軽量化を求められるスポーツ用品(自転車フレーム、ゴルフクラブなど)にも採用されています。
強度を左右する要因
A6061の強度にはいくつかの要因が影響を与えます。これらの要因を理解することで、材料を最適に選定・加工することができます。- 合金成分: A6061は主にシリコン(Si)とマグネシウム(Mg)を含んでおり、これらの成分が強度に大きな影響を与えます。シリコンは材料の流動性を改善し、マグネシウムは強度と耐腐食性を向上させます。
- 熱処理: A6061は熱処理によってその強度を大きく向上させることができます。特にT6熱処理(加熱後、急冷し、再度焼鈍する)によって、強度が劇的に改善され、引張強度や降伏強度が大幅に向上します。
- 加工方法: 加工方法も強度に影響を与えます。圧延や鍛造などの加工技術は、結晶粒の細化を促進し、強度を向上させます。一方で、鋳造などの方法では、材料内に気泡や欠陥が入りやすく、強度が低下することがあります。
- 温度環境: 高温環境ではA6061の強度が低下します。高温下で使用する場合、A6061よりも高温に強い合金(例えばA2024など)を選択することが求められます。
- 応力集中: 部品形状によっては、応力が集中する部分が発生します。例えば、角部や穴の周りに応力集中が生じやすいため、これらの部分は強度に悪影響を与える可能性があります。
A6061の成分とその影響
A6061アルミニウム合金は、さまざまな成分が組み合わさっており、その化学組成は合金の特性、特に機械的性質に大きな影響を与えます。このセクションでは、A6061の化学組成と、それにより変化する特性について詳述します。A6061の化学組成
A6061合金は主に以下の成分を含んでいます:- アルミニウム(Al): 基本的な成分で、合金全体の大部分を占めます。アルミニウムは軽量であり、合金の耐食性や熱伝導性を高める役割を持っています。
- シリコン(Si): 約0.4%~0.8%が含まれ、アルミニウムの流動性を向上させ、鋳造性を良くします。シリコンはまた、溶接性や耐食性を向上させる効果もあります。
- マグネシウム(Mg): 約0.8%~1.2%のマグネシウムは、合金に強度と耐腐食性を与えます。マグネシウムは、特に航空宇宙産業で必要とされる高強度材料を提供するため、重要な役割を果たします。
- 銅(Cu): 約0.15%~0.4%が含まれ、強度や耐食性を向上させますが、過剰に含まれると耐食性が低下するため、適切な量が重要です。
- マンガン(Mn): 約0.15%以下が含まれ、耐食性を高める役割を果たします。
- クロム(Cr): 0.04%~0.35%が含まれ、耐食性を向上させるために重要です。
- 鉄(Fe): 約0.7%以下が含まれますが、過剰に含まれると合金の加工性に悪影響を与える可能性があります。
成分が機械的性質に与える影響
A6061の成分が機械的性質、特に強度、硬度、靭性に与える影響は以下のように考えられます:- アルミニウム(Al): 基本的な金属として、合金の軽量性を確保します。アルミニウムの含有量が多いため、A6061は軽量ながらも優れた強度を持ちます。
- シリコン(Si): 鋳造性や溶接性を改善し、合金を加工しやすくする効果がありますが、引張強度には影響を与えません。シリコンの含有量が多いと、強度は高まるものの、延性が若干低下することがあります。
- マグネシウム(Mg): 高い強度を提供します。マグネシウムの含有量が増えると、降伏強度や引張強度が高まります。また、耐腐食性も向上し、特に海洋環境や湿気の多い場所で使用する場合に有利です。
- 銅(Cu): 合金の強度や耐食性に影響を与えますが、銅の過剰は合金の耐食性を低下させる可能性があります。銅の適切な量が維持されると、A6061の強度が増し、耐食性も向上します。
- マンガン(Mn)とクロム(Cr): これらの成分は主に耐食性を向上させる役割を果たし、特に酸化環境や腐食の多い場所での使用に効果的です。
- 鉄(Fe): 鉄はA6061合金の硬さや強度に影響を与えますが、過剰な鉄は合金の脆さを増す可能性があります。鉄の含有量は低い方が望ましいです。
合金元素の役割と特性
A6061合金に含まれる各合金元素は、それぞれ特有の役割を持ち、合金全体の性能を調整します。以下にその役割を示します:- シリコン(Si): 鋳造性や溶接性を高め、全体の成形性を改善します。シリコンは、機械的特性に直接的な影響を与えるわけではありませんが、加工性の向上に寄与します。
- マグネシウム(Mg): 合金に強度を与える重要な成分で、A6061の主要な強化元素です。また、耐腐食性も高め、外的環境への耐性を向上させます。
- 銅(Cu): 合金の強度を増す役割を果たし、耐食性を若干低下させるが、適切なバランスで使用されることが多いです。
- マンガン(Mn)およびクロム(Cr): これらは耐食性を向上させ、特に酸化に強い合金としての特性を発揮します。特にクロムは、海水や湿気に対する耐性を強化します。
A6061の融点と加工性
A6061アルミニウム合金は、その優れた特性により、航空宇宙、自動車、電子機器など多くの産業で使用されています。その特性の一つが、融点と加工性です。ここでは、A6061の融点とその加工適性、さらに切削性について詳述します。融点の基本知識
融点とは、固体が液体に変化する温度のことを指します。金属や合金における融点は、素材の特性を理解するうえで非常に重要です。融点が低ければ加熱が容易で、加工がしやすくなります。一方で、高い融点を持つ金属は、高温での作業が求められ、特殊な機器や処理方法が必要です。A6061の融点と加工適性
A6061アルミニウム合金の融点は、おおよそ580~650℃です。この融点の範囲は、純粋なアルミニウムよりも高く、合金としての性質を反映しています。A6061はアルミニウム合金の中でも広く使用される合金であり、その融点は適度な高さを持ちながらも加工が比較的容易であるため、さまざまな製造プロセスに適しています。- 融点が低いため、A6061は熱処理が比較的簡単に行えます。これにより、合金の強度や硬度を調整することができ、特定の用途に最適化することが可能です。
- 良好な加工適性も特徴の一つです。例えば、A6061は、押出しや鋳造、押し出し成形、機械加工(CNC加工)などの方法で容易に加工できます。また、耐食性や靭性も高いため、構造部品に頻繁に使用されます。
切削性とは何か?
切削性とは、金属や合金を加工する際に必要とされる機械的な特性を指します。具体的には、金属が切削工具と接触したときに、どれだけスムーズに削り取ることができるか、またどれだけの工具摩耗が生じるかが、切削性の重要な要素です。 A6061の切削性は、アルミニウム合金の中でも比較的良好であり、一般的なCNC機械や切削工具での加工が容易です。以下に、A6061の切削性に関連するポイントを示します:- 良好な切削性: A6061は、アルミニウム合金の中でも比較的柔らかいため、切削時に大きな抵抗が生じにくく、加工しやすいです。また、熱伝導性が高いため、加工中に発生する熱が効率よく放出され、切削工具の摩耗を軽減します。
- 切削工具の選定: A6061の切削性を最大限に活用するためには、適切な切削工具を使用することが重要です。例えば、ハイス鋼や炭素鋼などの切削工具が一般的に使用されます。また、適切な冷却剤や潤滑剤を使用することで、加工精度が向上し、工具寿命が延びることがあります。
A6061のヤング率と硬度
A6061アルミニウム合金は、その優れた機械的特性と加工性から、多くの産業で利用されています。特に、ヤング率(弾性率)と硬度は、素材の性能を評価する際に重要な要素となります。ここでは、A6061のヤング率と硬度について解説し、両者の関係についても触れます。ヤング率の解説
ヤング率(弾性率)とは、物体が力を受けたときに、どれだけその物体が伸び縮みするかを示す物理的な指標です。ヤング率が高い素材は、外力に対して変形が少なく、強靭であることを意味します。逆に、ヤング率が低い素材は、力を受けた際に変形しやすいという特性を持ちます。 ヤング率は、弾性変形領域での応力(力)とひずみ(変形)の比率として定義され、数値が大きいほど物体が硬く、力に対して変形しにくいことを示します。A6061の硬度と耐久性
A6061の硬度は、アルミニウム合金の中では中程度ですが、他の材料と比較して非常に良好な耐久性を持っています。硬度は、材料がどれだけ外部の圧力や摩耗に抵抗できるかを示す性質で、特に機械的な部品においては重要な指標となります。- A6061の硬度: A6061アルミニウム合金は、通常、Brinell硬度で約95~150 HB(硬度単位)程度の範囲に位置します。合金の状態や熱処理によって、硬度が異なることがありますが、一般的には良好な摩耗耐性を持ちます。
- 耐久性: A6061は優れた耐久性を持ち、軽量であるにもかかわらず、長期間の使用に耐えうる性能を発揮します。これにより、航空機の構造部品や自動車のフレームなど、過酷な環境下でも使用されることが多いです。
ヤング率と硬度の関係
ヤング率と硬度はどちらも材料の機械的特性を示しますが、それぞれ異なる性質を表しています。ヤング率は物体が力に対してどれだけ変形しにくいかを示し、硬度は物体がどれだけ外部からの圧力に耐えるかを示します。- ヤング率が高いと、変形しにくい: 高いヤング率を持つ材料は、外部からの圧力や引張りに対して変形が少ないため、より強靭であり、形状を保持する能力が高いです。
- 硬度が高いと、摩耗に強い: 高い硬度を持つ材料は、摩耗や傷が付きにくく、長期間の使用において耐久性を発揮します。
A6061の耐食性と応用
A6061アルミニウム合金は、優れた耐食性を持ち、さまざまな産業で幅広く利用されています。耐食性は、金属が腐食からどれだけ守られるかを示す重要な性質で、特に外部環境にさらされる製品では必要不可欠な要素です。ここでは、A6061の耐食性について、またその応用分野や耐食性を高めるための要素について詳しく解説します。耐食性とは
耐食性とは、金属や合金が腐食や劣化に対してどれだけ耐えることができるかを示す特性です。腐食とは、金属が外的要因(湿気、酸素、化学物質など)と反応して表面が損傷する現象を指します。耐食性が高い材料は、これらの影響を受けにくく、長期間にわたって安定した性能を維持することができます。A6061の耐食性
A6061アルミニウム合金は、以下の理由で優れた耐食性を誇ります:- 酸化皮膜の形成: A6061は、使用環境で自然に酸化皮膜を形成します。この酸化皮膜が金属の表面を保護し、腐食から守ります。酸化皮膜は非常に強固で、外部の湿気や化学物質から金属を保護します。
- 海水環境での耐性: A6061は、海水や湿度が高い環境でも耐食性を発揮します。そのため、海洋構造物や船舶、航空機部品などでも広く使用されています。
- アルカリ性・酸性環境への対応: A6061は、弱酸性や弱アルカリ性環境においても耐食性を保持しています。ただし、強酸や強アルカリには注意が必要です。
耐食性を高める要素
A6061の耐食性はすでに優れていますが、さらなる性能向上が可能です。以下の方法で耐食性を強化することができます:- 表面処理:
- 陽極酸化処理: A6061の酸化皮膜を厚くして密度を高め、耐食性を強化します。これにより、金属表面がより堅牢になり、外部環境に対して強力に保護されます。
- アルマイト処理: 特に過酷な環境下で使用する場合、アルマイト処理を施すことで表面保護層を強化し、耐食性をさらに向上させます。
- 合金設計:
- 合金の化学組成を工夫することで、耐食性をさらに強化することが可能です。特に、銅やマグネシウムなどの合金元素を調整することで、腐食に対する耐性を向上させることができます。
- 環境管理:
- 使用環境や保管方法も耐食性に影響を与えます。湿気や塩分を多く含む環境では、定期的なメンテナンスやコーティング処理が重要です。
応用分野
A6061アルミニウム合金は、優れた耐食性を活かして、さまざまな産業で活躍しています。代表的な応用分野は以下の通りです:- 航空機部品: A6061は、航空機の構造部分や機器に使用され、過酷な環境に耐えるため、非常に重要です。
- 海洋構造物: 船舶や海上プラットフォームなど、海水に直接さらされる部品にも利用されています。耐食性が高いため、長期間にわたり安定した性能を維持します。
- 自動車産業: 車両のフレームやボディ部品にもA6061が使われています。軽量化を実現しつつ、耐久性と耐食性を提供します。
- 建築分野: A6061は建物や構造物における外装材や装飾用の部材としても利用され、外的要因に耐える能力が求められる用途に適しています。
A6061と他のアルミニウム合金との比較
A6061アルミニウム合金は、その優れた機械的特性や耐食性から多くの産業で使用されていますが、他のアルミニウム合金と比較すると、どのような特徴があるのでしょうか?ここでは、A6061と他の代表的なアルミニウム合金、特にA6063との比較を中心に、その違いや合金選定の際の考慮点について説明します。A6061とA6063の比較
A6061とA6063は、どちらも同じく熱処理型のアルミニウム合金で、非常に似た性質を持っていますが、いくつかの重要な違いも存在します。以下はその主要な比較ポイントです:1. 化学組成の違い
- A6061: この合金は、マグネシウムとシリコンを主要な合金元素として含んでいます。これにより、A6061は高い強度と耐食性を有し、構造的な用途に適しています。
- A6063: A6063もマグネシウムとシリコンを含みますが、その含有量がA6061よりも低めです。このため、A6063はA6061よりもやや低い強度を持っていますが、その代わりに加工性が非常に優れており、特に押出成形に適しています。
2. 機械的特性
- A6061: 高い強度を持ち、特に構造部品や荷重を支える用途に適しています。引っ張り強度や耐久性が高く、航空機部品や自動車部品などに使用されます。
- A6063: A6063は強度はA6061に劣りますが、引っ張り強度や耐摩耗性が十分であるため、装飾的な部品やインテリア用途に最適です。耐食性も良好ですが、構造用途には不向きです。
3. 加工性
- A6061: 加工性に優れており、CNC加工や切削加工において広く使用されています。しかし、A6061は硬度が高いため、加工には一定の技術と経験が必要です。
- A6063: A6063は押出し加工に特に適しており、複雑な形状や薄肉部品を簡単に成形できます。これにより、建築用のフレームや窓枠などの用途に理想的です。
4. 耐食性
- A6061: 優れた耐食性を持ち、特に酸化皮膜が厚く形成されるため、湿度や海水環境にも強い耐性を示します。
- A6063: A6063も良好な耐食性を有しますが、A6061に比べると若干劣ります。そのため、非常に過酷な環境にはA6061が推奨されることが多いです。
他のアルミ合金との違い
A6061は非常に多用途であるため、他のアルミ合金と比較する際に重要なポイントは、合金の特性に合わせてどのような用途に最適かを考えることです。例えば、以下の合金との比較を見てみましょう。A5052アルミニウム合金
- A5052は、マグネシウムが主成分の合金で、非常に優れた耐食性を持っていますが、A6061に比べて強度が低く、構造用途には適していません。主に耐食性が求められる用途(海洋環境や化学プラント)に使用されます。
A7075アルミニウム合金
- A7075は非常に高い強度を持つ合金で、航空機部品や軍事用途に多く使われます。しかし、A6061に比べて加工が難しく、耐食性もやや劣ります。A6061は、A7075ほどの強度を求めない用途で使われることが多いです。
A2011アルミニウム合金
- A2011は、非常に優れた切削加工性を持つ合金ですが、耐食性や強度が他のアルミ合金(A6061やA7075)に比べて劣ります。精密機械部品などの高い加工精度が求められる用途に使用されます。
合金選定の考慮点
アルミニウム合金を選定する際には、以下のポイントを考慮する必要があります:- 強度と耐久性: どれだけの強度が求められるのか、耐久性が必要な使用環境かどうかを考慮します。A6061は強度が高く、構造用途に適していますが、A6063は強度よりも加工性が重視される場合に適しています。
- 耐食性: 使用する環境が海洋環境や化学薬品にさらされる場合、A5052やA6061のような耐食性の高い合金を選ぶ必要があります。
- 加工性: 形状や加工方法に応じて、A6063のように加工しやすい合金を選択することも重要です。
- コストと目的: コスト面を重視する場合、強度や耐食性のバランスを考慮して最適な合金を選定します。高強度を求める場合はA7075が、コストを抑えつつ適度な強度と耐食性が求められる場合はA6061が適しています。
A6061の加工方法と使用用途
A6061アルミニウム合金は、その優れた機械的特性や耐食性により、さまざまな加工技術と多くの使用用途に適しています。本章では、A6061の加工方法、加工時の注意点、そして代表的な用途について解説します。A6061の加工技術
A6061は、その適度な強度と良好な加工性により、さまざまな加工技術で利用されます。以下の加工方法が一般的です。1. 切削加工
- 特徴: A6061は切削性が良好であり、フライス加工や旋盤加工など、精密な切削加工に適しています。特に、精密機器や航空機部品、機械部品の製造に使用されます。
- 加工方法: 高速鋼(HSS)や超硬工具を用いた切削加工が一般的です。切削液を使用して冷却しながら行うことで、切削面が滑らかになり、加工精度が向上します。
2. 押出し加工
- 特徴: A6061は押出し加工に非常に適しており、長尺部品や複雑な断面形状を作ることができます。この加工方法は、窓枠や建材、装飾用部品に広く使用されています。
- 加工方法: 加熱したA6061をダイ(型)を通して押し出し、所定の形状を作成します。冷却後に必要に応じて切断や仕上げを行います。
3. 溶接加工
- 特徴: A6061は溶接性が良好で、TIG溶接やMIG溶接が広く使用されます。溶接後の強度も十分に高く、構造部品の製造に適しています。
- 加工方法: 亜鉛やシリコンを含むフラックスを使用し、溶接部位の強度を確保します。溶接後の熱処理が必要な場合もあります。
4. プレス加工
- 特徴: A6061はプレス加工によって曲げや切断などの操作が行いやすいです。薄板での加工には特に向いており、成形後の硬化による変形が少なく、仕上がりも良好です。
- 加工方法: 高温に加熱したA6061を金型に挿入し、圧力をかけて所定の形状に成形します。精度が求められる部品には、高精度なプレス機を使用します。
加工時の注意点とポイント
A6061を加工する際には、いくつかの重要なポイントを押さえておくことが加工精度を高めるために重要です。- 工具の選定: A6061の加工には、適切な工具の選定が不可欠です。特に切削加工では、超硬や高速度鋼の工具を使用し、切削面の滑らかさを確保するために切削液を適切に使用します。
- 温度管理: A6061の加工では、特に溶接や押出し加工時に温度管理が重要です。過剰な熱を加えると、材質の強度が低下したり、歪みが生じることがあります。温度が適切であることを確認して加工を進めることが必要です。
- 適切な冷却: 加工中に過剰な摩擦を避けるため、冷却が十分に行われることが大切です。冷却剤を使用して、工具や加工面の温度をコントロールします。これにより、加工精度が向上し、工具の寿命も延びます。
- 歪み防止: 溶接や加熱加工時には、金属が膨張して歪みが発生することがあります。これを防ぐために、事前に熱処理を行うことや、適切な温度で加工を進めることが重要です。
A6061の一般的な用途と例
A6061はその優れた機械的特性と加工性を活かし、多くの産業で広く使用されています。代表的な用途をいくつか挙げてみましょう。1. 航空機および宇宙産業
- A6061はその高強度と軽量性から、航空機の構造部品や宇宙機器の部品に使用されます。特に、機体フレームや翼、エンジン部品などに活用されています。
2. 自動車産業
- 車両の軽量化が求められる自動車業界でも、A6061は使用されます。エンジン部品やシャーシ、ホイールなど、強度と軽量化が求められる部品に適しています。
3. 建築およびインフラ
- A6061はその耐食性と加工性を活かし、建築やインフラ関連の部品にも使用されています。特に、窓枠やカーテンウォール、建物の外装に多く使用されています。
4. スポーツ用品
- 軽量で強度が高いため、スポーツ用品、特に自転車のフレームやゴルフクラブ、スキーのポールなどに使用されています。
5. 電子機器
- 熱伝導性が高いため、A6061は電子機器の冷却板やヒートシンクに使用されます。コンピュータや冷却システムの部品に活用されます。
6. その他の精密機器
- A6061は精密機器や機械部品にも多く使用されます。特に、精密加工が可能であるため、カメラ部品や電子機器のハウジングなどに用いられます。
アルミ合金の種類と特性の概説
アルミニウム合金は、軽量で優れた機械的特性、耐食性、加工性を備えており、さまざまな産業で幅広く使用されています。本章では、アルミニウム合金の分類と、各種アルミ合金の特性を比較し、アルミ合金を選定する際の基準について解説します。アルミニウム合金の分類
アルミニウム合金は、主にその組成に基づいて次のように分類されます:1. 純アルミニウム(1xxx系)
- 特徴: 純度が高く、優れた耐食性と良好な加工性を持っています。強度は低めですが、耐食性を重視した用途に適しています。
- 用途: 電気導体、化学機器、食品・医薬品の包装材料など。
2. アルミマンガン合金(3xxx系)
- 特徴: 中程度の強度と優れた耐食性を持ち、特に耐海水性が良好です。加工性も優れています。
- 用途: 建材(屋根材、外装材)、熱交換器、ダクト類。
3. アルミシリコン合金(4xxx系)
- 特徴: 良好な溶接性と低膨張率を特徴とします。特に溶接や鋳造に向いています。
- 用途: 溶接材料、鋳造部品、自動車部品。
4. アルミマグネシウム合金(5xxx系)
- 特徴: 高い強度と耐食性、特に塩水環境下での耐食性に優れています。加工性も良好ですが、熱処理による強化が難しいのが特徴です。
- 用途: 航空機、船舶、オフショア構造物、トラック・トレーラー部品。
5. アルミ銅合金(2xxx系)
- 特徴: 高強度ですが、耐食性がやや低いため、主に強度が重視される用途に使用されます。熱処理により強度が向上します。
- 用途: 航空機、航空部品、自動車部品。
6. アルミ亜鉛合金(7xxx系)
- 特徴: 極めて高い強度を持ち、航空機や高強度が要求される部品に使用されます。耐食性はやや劣るため、表面処理が必要です。
- 用途: 航空機、軍事用途、高強度の構造部材。
7. アルミリチウム合金(8xxx系)
- 特徴: 軽量で高強度、さらに高温での耐性にも優れています。特に高温環境下での使用に適しています。
- 用途: 航空機、宇宙機器、高温環境下での使用部品。
各種アルミ合金の特性比較
アルミ合金は、使用目的や要求される特性に応じて選ばれます。各種アルミ合金の主な特性を比較すると、以下のような特徴があります。合金系統 | 主な特徴 | 強度 | 耐食性 | 機械加工性 | 溶接性 |
---|---|---|---|---|---|
1xxx系(純アルミ) | 高耐食性、良好な加工性 | 低 | 非常に高い | 良好 | 良好 |
3xxx系(アルミマンガン合金) | 中程度の強度、耐海水性が良好 | 中 | 高い | 良好 | 良好 |
4xxx系(アルミシリコン合金) | 良好な溶接性、鋳造に適している | 中 | 中 | 良好 | 非常に良い |
5xxx系(アルミマグネシウム合金) | 高強度、特に耐塩水性に優れる | 高 | 非常に高い | 中 | 良好 |
2xxx系(アルミ銅合金) | 高強度、熱処理で強化可能 | 非常に高い | やや低い | 中 | 良好 |
7xxx系(アルミ亜鉛合金) | 高強度、航空機用に使用 | 非常に高い | やや低い | 中 | 良好 |
8xxx系(アルミリチウム合金) | 高強度、軽量で高温耐性あり | 高 | 中 | 中 | 中 |
アルミ合金選定の基準
アルミ合金を選定する際には、用途や特定の条件に応じて、以下の基準を考慮する必要があります。- 強度の要求: 部品に求められる強度によって、アルミ合金の種類を選定します。航空機や軍事用途など、強度が重要な場合は、2xxx系や7xxx系が適しています。一方、軽量化が求められる場合は、1xxx系や8xxx系が適しています。
- 耐食性: 塩水や化学物質にさらされる部品では、耐食性が重要です。耐食性が特に求められる場合は、1xxx系や5xxx系のアルミ合金が適しています。
- 加工性: 加工の容易さや精度が求められる場合、3xxx系や4xxx系のアルミ合金が良好な加工性を提供します。加工が難しい場合は、強度と耐食性のバランスが重要です。
- 溶接性: 溶接が必要な場合、溶接性が良好な合金を選ぶことが重要です。特に4xxx系は溶接性が高く、機械的強度も良好です。
- 価格とコスト: 最後に、コストが重要な場合、特に高価な合金(例:2xxx系や7xxx系)よりも、コストパフォーマンスの良い3xxx系や5xxx系が適していることがあります。
アルミの基礎知識と加工特性
アルミニウムは、軽量で耐食性に優れた金属材料として、さまざまな産業で広く使用されています。本章では、アルミニウムの物理的性質と加工特性について解説し、アルミ製品を設計する際に考慮すべきポイントを紹介します。アルミニウムの物理的性質
アルミニウムは、軽量で腐食に強く、良好な熱伝導性や電気伝導性を持っています。以下にその特徴を示します。- 比重: 約2.7 g/cm³。アルミニウムは非常に軽く、鉄(約7.8 g/cm³)に比べて約三分の一の重さです。
- 融点: 約660℃。これにより、高温での使用が可能で、加工しやすい特性があります。
- 耐食性: 自然に酸化膜を形成するため、腐食に非常に強い特性があります。特に海水や化学薬品に対する耐性があります。
- 導電性と熱伝導性: アルミニウムは非常に良好な熱と電気の導体です。この特性を活かして、電気配線や熱交換器などに利用されます。
- 延性と靭性: 良好な延性(引き伸ばし可能)と靭性(衝撃に強い)を持ち、さまざまな加工方法に対応します。
アルミの加工特性とは
アルミニウムは、加工性が非常に良い金属であり、以下のような特性を持ちます。- 成形性: アルミニウムは、熱間・冷間加工ともに優れた成形性を持っています。圧延や押出成形、鋳造などの技術で簡単に加工できます。
- 切削性: 軽く、軟らかいため、切削加工が容易です。CNC機械を用いて精密加工が可能で、複雑な形状の部品も作成できます。
- 溶接性: アルミニウムは溶接性が高く、TIG溶接やMIG溶接などで簡単に接合できます。ただし、合金によっては溶接後の強度低下や亀裂が発生することもあるため、適切な溶接技術が必要です。
- 圧延性: アルミニウムは圧延して薄い板状にすることができ、これをさらに加工して多くの製品に利用されます。
- 表面処理: アルミニウムは酸化皮膜の形成を促進し、耐食性を高めるために陽極酸化処理が行われることが多いです。また、塗装やメッキ処理も行いやすい金属です。
アルミ製品の設計上のヒント
アルミニウム製品の設計時には、以下のポイントを考慮することで、性能を最大限に引き出すことができます。1. 強度と耐久性のバランス
- アルミニウムは軽量ですが、強度が比較的低いため、使用する合金や加工方法を選定する際には強度と耐久性のバランスを取ることが重要です。強度が求められる場合は、アルミニウム合金(特に2xxx系や7xxx系)を選ぶと良いでしょう。
2. 熱膨張の影響
- アルミニウムは他の金属に比べて熱膨張係数が大きいため、温度変化による膨張や収縮を考慮した設計が求められます。設計においては、温度変化による影響を最小限に抑える設計が重要です。
3. 耐食性の強化
- アルミニウムは自然に酸化皮膜を形成しますが、腐食が懸念される場合には陽極酸化処理や塗装、メッキ処理を施すことが必要です。特に海洋環境や化学薬品を扱う場所では、耐食性の強化が設計において重要な要素となります。
4. 加工性を活かした設計
- アルミニウムは加工がしやすい素材であり、複雑な形状や精密な部品の製造が可能です。設計時には、加工方法に応じて形状を最適化し、無駄な加工を減らすことでコスト削減が可能です。
5. コストと性能の最適化
- アルミニウム合金の選定においては、性能とコストのバランスを取ることが重要です。高強度が必要な場合は高価な合金を選択する必要がありますが、軽量化を重視する場合は比較的安価な合金でも十分な性能を発揮します。
6. 溶接や接合方法
- 溶接や接合が必要な場合、アルミニウムは溶接性が良好ですが、熱による変形や亀裂を避けるために適切な溶接技術を使用することが大切です。アルミニウムの合金によっては溶接後に強度が低下することもあるため、設計段階でその点を考慮することが重要です。
A6061アルミニウム合金の総合的理解
A6061アルミニウム合金は、軽量で高い強度と耐食性を持つため、様々な産業において非常に人気のある材料です。本章では、A6061の特性を最大限に活かした設計方法と、総合的な材料選択のポイントについて解説します。A6061の特性を活かした設計
A6061合金は、その優れた機械的特性、耐食性、加工性を活かした設計が可能です。具体的には、以下のような特性を活かした設計方法が考えられます。- 強度と軽量化のバランス: A6061は、アルミニウム合金の中でも高い強度を誇り、軽量化を求められるアプリケーションに最適です。航空機、車両、スポーツ用品などでは、軽量化と強度のバランスが非常に重要であり、A6061はこれを実現できます。
- 耐食性の活用: 自然に酸化膜を形成するため、海洋や化学的に厳しい環境でも優れた耐食性を発揮します。例えば、海洋機器や水処理設備で使用される部品にA6061が使われる理由です。陽極酸化処理を施すことで、更に耐食性を高めることも可能です。
- 良好な加工性: 加工が容易で、切削や成形が簡単に行えるため、複雑な形状や精密な部品の製造にも適しています。これにより、設計者は製造過程での柔軟な調整が可能になります。また、溶接性も高いため、部品同士の接合が求められる場面でも問題なく使用できます。
- 熱伝導性と電気伝導性: 熱交換や電気機器に使われる場合、A6061の熱伝導性と電気伝導性が重要な要素となります。これらの特性を活かして、冷却システムや電気機器の部品に使用されることが多いです。
総合的な材料選択のポイント
A6061を選択する際には、その特性をどのように活用するかを検討する必要があります。以下の点を考慮し、最適な材料選定を行いましょう。1. 要求される強度と重量
- 製品が求める強度と重量の要件を明確にし、A6061がその基準を満たすかを判断します。軽量化が重要な場合でも、強度が確保されていることを確認する必要があります。
2. 耐食性と使用環境
- 使用環境が厳しい(海水中、化学薬品を使用するなど)場合、A6061の耐食性を活かすことができます。また、さらに耐食性を強化したい場合は、陽極酸化処理を施すことで、より長期間の使用が可能となります。
3. 加工性の重要性
- 加工のしやすさが求められる場合、A6061は非常に適した材料です。CNC加工や切削、圧延などの製造方法において優れた加工性を発揮します。複雑な形状を作る必要がある場合にも適しています。
4. 温度環境に対する適性
- A6061は高温でも比較的安定して使用できるため、温度変化が激しい環境での使用が求められる場合に有効です。ただし、極端な高温環境での使用には、より耐熱性の高い合金の選定が求められることもあります。
5. コスト対効果
- A6061はコストパフォーマンスの高い材料であり、多くの用途でバランスの取れた性能を提供します。しかし、特に高強度や特殊な耐食性が求められる場合は、他の高価な合金を検討することも重要です。
6. 耐久性と長寿命
- 製品の長寿命が求められる場合、A6061はその耐久性に優れています。耐食性や機械的性質を考慮した上で、耐久性を高めるための設計が可能です。
まとめ
A6061アルミニウム合金は比重が小さく、強度が高い特性を持っています。この合金は航空機や自動車など多くの産業で広く使用されています。その軽量性と高い強度から、様々な用途に適しており、特に高強度な部品や構造材として重要な材料となっています。この合金は耐食性も高く、耐久性があります。そのため、長期間使用される部品や構造に理想的な材料です。A6061アルミニウム合金は比重と強度の両方が優れており、その特性を理解することで、さまざまな産業のニーズに応えることができます。なぜA5052は業界で愛される?その特性と加工性の秘密
業界で広く愛されるアルミニウム合金の一つ、A5052。その特性と加工性には何が秘密があるのでしょうか?A5052はなぜ多くの産業分野で重宝されるのか、その秘密に迫ってみましょう。本記事では、A5052の特徴や利点、そしてその加工性に焦点を当て、なぜこの素材が業界で注目を集めているのかを探求します。A5052を知り尽くし、その魅力に触れてみましょう。
Contents
A5052の基本特性と業界での採用される理由
A5052はアルミニウム合金の一種で、優れた耐食性と加工性を持つため、さまざまな業界で広く採用されています。以下では、A5052の化学組成、物理的特性、耐食性の特徴と、それがもたらす業界別の利用例について詳しく解説します。A5052の化学組成と物理的特性
A5052は主にアルミニウムを基盤とし、マグネシウムを主成分に含んでいる合金です。以下にその化学組成と物理的特性を紹介します:- 化学組成:
- アルミニウム(Al): 約95.85~98.58%
- マグネシウム(Mg): 約2.2~2.8%
- その他の元素(鉄 Fe、銅 Cu、マンガン Mnなどが微量含まれる)
- 物理的特性:
- 比重: 2.68
- 引張強さ: 約210 MPa
- 耐熱性: 高温環境でも優れた安定性を発揮
- 電気伝導性: 低い
- 熱伝導性: 高い
A5052合金の耐食性とその影響
A5052合金は特に優れた耐食性を誇り、その特性が多くの業界で重宝されています。具体的には以下のような耐食性に関する特徴があります:- 耐塩害性: A5052は海水や湿気の多い環境に強く、船舶や海洋関連の構造物で使用されることが多いです。マグネシウムを主成分とすることで、塩害に対して非常に優れた耐性を発揮します。
- 酸化防止性: アルミニウム合金であるため、表面に自然に酸化皮膜を形成し、これがさらなる腐食を防ぎます。
- 耐アルカリ性: 強いアルカリ性の環境にも比較的耐えることができ、化学プラントなどで利用されています。
業界別で見るA5052の利用例とその魅力
A5052の優れた特性は、さまざまな業界で活かされています。特に以下のような分野で採用されている理由は、その特性に起因します。航空宇宙産業
A5052はその軽量で強度が高い特性から、航空機や宇宙産業で広く使用されています。特に、航空機の機体や部品での使用において、耐食性と高強度が求められるため、この合金が選ばれることが多いです。自動車産業
自動車の車体や部品にもA5052は多く使用されています。自動車は環境にさらされることが多いため、耐腐食性が重要であり、A5052の耐食性が非常に重宝されています。また、軽量化が進められている現代の自動車産業では、A5052の軽量性が求められる要素となっています。海洋・船舶産業
A5052は海水による腐食に強いため、船舶の構造材料として最適です。船舶の外装や海洋設備の一部などに使用され、長期間の耐久性が求められる分野で広く利用されています。建築・構造物
A5052は建築や構造物にも使用されます。特に屋外で使用される構造物において、その耐腐食性と強度が非常に重要な要素となるため、屋根材や外壁、橋梁などの建材として適しています。化学プラント
化学プラントにおいては、耐腐食性や高温環境への耐性が重要です。A5052はこれらの厳しい条件下でも問題なく使用できるため、プラント内の設備や配管に広く採用されています。アルミ合金A5052の加工性の秘密
A5052はその優れた物理的特性と耐食性で広く使われているアルミニウム合金です。加工性においても優れており、多くの業界で活用されています。以下では、A5052の成形性、溶接性、表面処理について詳しく解説します。A5052の成形性:加工しやすさの秘密
A5052の最大の特徴の一つは、その優れた成形性です。特に深絞りや曲げ加工、圧延などの加工が比較的容易で、製造業において高く評価されています。その理由として、A5052が持つ適度な強度と優れた塑性変形特性が挙げられます。具体的には以下のような特性があります:- 引張強度と伸び率: A5052は適度な引張強度を持ちながら、十分な伸びを持っています。このため、加工中に破断することなく、金属を大きく変形させることができます。
- 冷間加工: A5052は冷間での成形がしやすく、特に深絞りなど複雑な形状の部品の製造に適しています。これにより、機械部品の形状を精密に成形することができます。
- 熱間加工: 熱間での成形性も良好で、特に大規模な部品や長尺材の加工にも対応可能です。
A5052の溶接性:強度と安全性を保つ
A5052は溶接性にも優れ、強度を保ちながら安全に溶接することができます。溶接時におけるA5052の特性は以下のようなものがあります:- 良好な溶接適性: A5052はアルミニウム合金の中でも溶接性が良いとされ、アーク溶接やTIG溶接、MIG溶接などさまざまな方法で接合が可能です。特に、マグネシウムを含んでいるため、溶接後も良好な機械的特性を維持できます。
- 熱影響部の強度維持: 溶接時に発生する熱影響部(HAZ)にも注意を払いながら、強度を維持したまま溶接を行うことができます。これにより、溶接部位でも高い強度と耐久性を保つことが可能です。
- 溶接後の仕上げの簡便さ: A5052は溶接後の処理が比較的簡単で、後処理による強度低下や欠陥の発生を抑えることができます。
表面処理とA5052:美観と保護の両立
A5052はそのままでも優れた耐食性を持っていますが、さらにその特性を強化するために、さまざまな表面処理が施されます。これにより、外観の美しさと耐久性が一層高まります。代表的な表面処理方法は以下の通りです:- アルマイト処理(陽極酸化処理): A5052はアルマイト処理を施すことで、耐食性をさらに向上させ、表面に硬い酸化皮膜を形成します。この皮膜は非常に耐久性が高く、化学薬品や塩害に対する耐性を高めるとともに、装飾的な美しさを加えることもできます。
- 粉体塗装: 粉体塗装はA5052に美観を追加しつつ、耐食性や耐候性を高めるために行われます。これにより、特に外部で使用される製品に対して、長期間の美しい外観を維持することが可能です。
- 亜鉛メッキやクロムメッキ: A5052はメッキ処理を施すことで、さらに高い耐腐食性を持つことができます。これらの処理は特に海洋環境や化学プラントなど、非常に過酷な環境下でも使用される部品に適しています。
A5052の特性
A5052はアルミニウム合金の中でも特に耐食性と加工性に優れ、さまざまな産業で活用されています。以下では、A5052の機械的特性と熱伝導性について詳しく説明します。A5052の機械的特性とその影響
A5052はその優れた機械的特性により、強度と柔軟性を兼ね備えた合金です。これにより、特定の用途において非常に重要な役割を果たします。具体的な機械的特性としては以下の点が挙げられます:- 引張強度: A5052は良好な引張強度を持ち、構造的に安定した部品を作ることができます。引張強度は約210 MPa(メガパスカル)であり、これによりA5052は軽量でありながら高い強度を保持できます。これが自動車や航空機部品、建材などで使用される理由です。
- 伸び率(塑性): A5052は非常に高い伸び率を持ち、これにより複雑な形状の加工が可能になります。特に冷間加工や深絞り加工などで優れた性能を発揮します。この特性により、A5052は多様な加工方法に適用され、部品の形状変更が容易です。
- 疲労強度: A5052は比較的高い疲労強度を持ち、振動や繰り返し負荷がかかる環境でも性能を維持できます。これは特に自動車のシャシー部品や機械部品において重要な特性となります。
- 耐腐食性: A5052は高い耐腐食性を持ち、特に海洋環境や化学プラント、湿度が高い場所で使用される部品に最適です。この特性は合金に含まれるマグネシウムが大きな役割を果たしており、表面に酸化物層を形成することで腐食を防ぎます。
A5052の熱伝導性と冷却効果
A5052はその熱伝導性の面でも特長があります。アルミニウム合金として、A5052は比較的高い熱伝導性を持ち、冷却効果に優れています。以下の点が重要です:- 熱伝導性: A5052の熱伝導率は約138 W/mK(ワット毎メートルケルビン)であり、これはアルミニウム合金の中では標準的な値です。このため、熱を効率的に伝えることができるため、冷却が必要な機械部品や電子機器に適しています。
- 冷却効果: 熱を迅速に拡散する能力により、A5052は過熱を防ぐために重要な役割を果たします。電子機器のヒートシンクやエンジン部品など、熱が発生しやすい場所で使用されることが多いです。これにより、部品の温度管理がしやすくなり、性能を安定させることができます。
- 耐熱性: A5052は高温環境でも比較的安定しており、一定の温度範囲内では強度や形状が保たれます。ただし、A5052は高温になると硬度が低下する傾向があるため、過度の熱がかかる環境では他の高温耐性材料が選ばれることがあります。
アルミ合金A5052と他合金との比較
アルミ合金はその特性によってさまざまな用途に使用され、選ばれる合金が用途に応じて異なります。特にA5052とA5056はどちらもアルミニウム合金の中で優れた耐食性を持ち、加工性も良好ですが、いくつかの違いがあります。以下ではA5052とA5056の特性を比較し、A5052が選ばれる理由を説明します。A5052とA5056の特性比較:何が違う?
A5052とA5056は、どちらもアルミニウムにマグネシウムを含む合金ですが、いくつかの違いがあります。主な違いは、合金の化学組成や機械的特性です。- 化学組成:
- A5052: 主成分はアルミニウムで、マグネシウム(2.2-2.8%)が添加されています。マグネシウム含有量が比較的少なく、耐食性と強度のバランスが優れています。
- A5056: こちらはA5052よりもマグネシウムの含有量が高く(4.5-5.5%)、さらに耐食性が向上していますが、その分強度はA5052よりもやや低いことが多いです。
- 機械的特性:
- A5052: 引張強度は約210 MPaであり、伸び率も高く、非常に加工性が良いです。疲労強度も高く、衝撃を受ける部品や構造物に適しています。
- A5056: 引張強度はA5052と同程度または若干低いですが、耐食性がより優れているため、特に厳しい腐食環境において使用されます。
- 耐食性:
- A5052: 強度と耐食性がバランス良く、海水や化学薬品などの腐食環境でも優れた性能を発揮します。航空機や船舶の部品などに適しています。
- A5056: 高いマグネシウム含有量のおかげで、A5052よりもさらに耐食性が優れており、特に海洋環境で使用されることが多いです。
- 溶接性:
- A5052: 溶接性も良好で、溶接後の強度低下が少ないため、航空機や自動車部品などで使用されることがあります。
- A5056: A5056も溶接性が良好ですが、溶接後の強度や硬化がA5052に比べて劣るため、適用範囲が制限される場合があります。
合金選びのポイント:A5052が選ばれる理由
A5052はその特性から多くの業界で選ばれる理由があります。主なポイントを以下に示します。- バランスの良い特性: A5052は耐食性、強度、加工性のバランスが非常に良く、多くの用途に適しています。例えば、自動車部品、航空機の外装、建材、化学プラントの部品などで広く利用されています。
- 高い加工性: A5052は冷間加工や深絞り加工がしやすく、複雑な形状の部品にも対応できます。特に形状を変える加工が必要な部品において優れた性能を発揮します。
- コストパフォーマンス: A5052は比較的安価であり、必要な特性を満たしつつコストを抑えることができるため、広範な用途で採用されています。
- 良好な溶接性: A5052は溶接後の強度低下が少なく、構造部品においても安全性が保たれるため、溶接が必要な部品にも適しています。
- 軽量でありながら強度を保持: A5052は軽量でありながら高い強度を保持しており、特に重量が重要な航空機や自動車の部品などで採用されています。
まとめ
A5052は業界で愛されるアルミニウム合金であり、その特性と加工性が特に評価されています。この素材は耐食性に優れており、加工が容易であるため、多くの産業で利用されています。また、強度が高く軽量なため、様々な用途に適しています。これらの特性から、A5052は幅広く愛用されており、その特性と加工性が業界で高く評価されています。“A5052アルミニウム合金の基礎知識!比重と強度の関係を解説”
A5052アルミニウム合金は、工業製品や建築業界で広く使用されている重要な素材です。その独自の特性や耐力について理解することは、製品の設計や使用において重要です。本記事では、A5052アルミニウム合金についての基礎知識を解説します。比重や強度の関係に焦点を当て、その特性がどのように製品の性能に影響するかを明らかにします。A5052アルミニウム合金に関心がある方や素材工学に興味がある方にとって、この記事は貴重な情報源となることでしょう。では、一緒にA5052アルミニウム合金の世界に探究の旅に出かけましょう。
Contents
A5052アルミニウム合金とは
A5052アルミニウム合金は、優れた耐食性、加工性、耐久性を持ち、多くの産業分野で広く使用されています。特に、航空宇宙、海洋、建築、車両など、耐食性が要求される環境で利用されることが多いです。以下では、A5052合金の成分と特性、アルミニウム合金の分類における位置づけ、そして主な用途について詳述します。A5052合金の成分と特性
A5052は、主にアルミニウムにマグネシウム(Mg)を多く含んだ合金です。この合金は以下の成分で構成されています:- 主成分:アルミニウム(Al)
- 添加成分:マグネシウム(2.2~2.8%)、マンガン(0.1~0.4%)、クロム(0.15~0.35%)
- 優れた耐食性 A5052は非常に優れた耐食性を持ち、塩水環境など厳しい環境下でも長期間耐えることができます。この特性は、船舶や海洋構造物、化学プラントの設備で利用される理由です。
- 良好な加工性 溶接や圧延、深絞りなど、加工がしやすく、複雑な形状を作ることができます。
- 高強度 他のアルミニウム合金と比較しても、強度が高く、構造的な要求が高い用途にも適しています。
- 優れた耐摩耗性 摩擦や衝撃に強く、耐久性を求められる部品に適しています。
- 軽量 アルミニウム特有の軽さが、重量を抑えることが求められる産業や製品において大きなメリットとなります。
アルミニウム合金の分類とA5052の位置づけ
アルミニウム合金は、主に以下の4つの大きな分類に分けられます:- 純アルミニウム(1000番台) 純度が高いアルミニウムで、加工性や耐食性に優れていますが、強度が低いため、一般的には軽負荷の用途に使用されます。
- 合金系アルミニウム(2000番台、6000番台) 強度を高めるために銅やシリコンなどが加えられています。航空機の構造部品など、高強度が要求される用途に適しています。
- 耐食性に優れる合金(5000番台) A5052はこの5000番台に属し、マグネシウムを主成分とすることで、特に耐食性が向上しています。このシリーズは、海洋や化学産業で多く利用されます。
- 耐熱合金(7000番台) 高温での強度を要求される用途に使用される合金です。航空宇宙産業などで多く使用されています。
A5052の用途と産業での利用例
A5052合金はその特性により、さまざまな分野で利用されています。代表的な用途には以下があります:- 船舶および海洋構造物 高い耐食性と強度を持つA5052は、海水にさらされる環境でも長期間使用できるため、船舶の外装や海洋プラットフォームの一部に使用されます。
- 自動車および輸送機器 軽量でありながら高強度を持つため、車両のボディやトラックの貨物コンテナ、タンクなどに使用されます。
- 化学設備 化学プラントや製薬工場では、耐薬品性が求められるため、A5052合金が使用されます。
- 建築材料 外壁パネルや屋根材として使用されることが多く、特に耐食性が重要な環境下で活躍します。
- 電気機器および配電装置 電気機器の外装や電力機器にも使用され、耐久性が求められる場面で重要な役割を果たします。
A5052アルミニウム合金の物理的特性とその重要性
A5052アルミニウム合金は、軽量でありながら優れた強度と耐久性を持つため、さまざまな産業で使用されています。特にその物理的特性は、他のアルミニウム合金と比較しても独自の利点を持っています。ここでは、A5052の比重、融点、耐熱性、および比重と強度の関係について詳しく解説します。A5052の比重とその意味
A5052アルミニウム合金の比重は約2.68 g/cm³です。この値は、アルミニウム合金の中では比較的軽量であり、他の金属材料と比較しても非常に軽いという特徴を持っています。比重が低いため、A5052は多くの用途において軽量化を必要とする部品や製品に適しています。 軽量化が求められる分野では、A5052は非常に重要な役割を果たします。例えば、航空機や自動車の部品、輸送機器など、重量を削減しつつ強度を保つ必要がある場合に最適な選択肢です。比重が低いことは、耐久性を損なうことなく、効率的なエネルギー消費を促進するための理想的な特性です。A5052の融点と耐熱性
A5052アルミニウム合金の融点は約607℃です。この融点の高さは、A5052を高温環境下で使用するための適性を示しており、長期間にわたって熱にさらされても安定した性能を維持することができます。特に、航空機や車両のエンジン部品など、高温環境下で使用される部品にとって重要な特性です。 さらに、A5052は優れた耐熱性を備えており、熱膨張を最小限に抑えつつ、高温での安定性を維持します。この特性により、過酷な環境下でも長期にわたりその性能を発揮します。例えば、化学工業の装置や海洋機器など、高温かつ湿気の多い場所でも使用されることがあります。比重と強度の関係性
A5052の比重は軽量ですが、その強度は高いため、比重と強度のバランスが非常に良いことが特徴です。比重が低いことによって部品の重量が軽く、強度が高いことでその耐久性や機能が保証されます。この特性は特に航空機や車両の軽量化を求められる部品において非常に重要です。 A5052合金は、軽量でありながら優れた引張強度と耐衝撃性を備えています。このため、構造材や高強度が必要とされる用途での使用に最適です。また、比重が低いという点でも、その軽量化を求める分野で非常に重要な役割を果たします。例えば、航空機や輸送機器、化学機器において、軽量化を実現しながらも強度を保つために広く採用されています。A5052アルミニウム合金の応用分野
A5052の優れた物理的特性を活かして、さまざまな産業で使用されています。特にその軽量性と強度が求められる分野で重宝されており、主な使用例には以下のようなものがあります:- 航空機部品:軽量で強度の高い素材が求められる航空機の構造部品や外装に使用されます。
- 自動車産業:燃費向上のために車両の軽量化が進められており、A5052は車両部品やボディパーツに使用されています。
- 化学機器や海洋機器:耐腐食性や耐熱性が重要な化学機器や海洋機器にも使用されることが多いです。
A5052アルミニウム合金の機械的性質とその重要性
A5052アルミニウム合金は、軽量でありながら高い機械的強度を持つため、さまざまな産業での利用が広がっています。この記事では、A5052の耐力、強度に影響を与える因子、ヤング率、そして硬度について詳しく解説します。A5052の耐力とは
耐力は、材料が破壊されずに耐えられる最大の引張応力を指します。A5052アルミニウム合金の耐力は非常に高いとされ、特に引張耐力(引張強度)において優れた性能を示します。具体的には、A5052の引張強度は約210 MPaとされており、これは同クラスのアルミニウム合金と比較しても十分な強度を持っています。この耐力の高さにより、A5052は過酷な環境下でも安定した性能を発揮し、耐久性が求められる部品に適しています。 耐力が高いことは、特に構造材や機械部品において重要な要素となります。A5052はその耐力を活かし、航空機、車両、さらには化学プラントや海洋機器などの高強度が求められる部品に使用されます。強度に影響を与える因子
A5052アルミニウム合金の強度には、いくつかの要因が影響を与えます。主な因子は以下の通りです:- 合金元素:A5052は主にマグネシウムを含む合金であり、マグネシウムの含有量が強度に大きな影響を与えます。マグネシウムはアルミニウムの強度を増加させ、耐食性を向上させる重要な要素です。
- 熱処理:A5052合金は特定の熱処理を行うことで、さらに強度を向上させることができます。特に、冷間加工を施すことにより、強度が増します。
- 加工方法:加工方法も強度に影響を与えます。例えば、圧延や引き延ばしなどの加工を通じて、材料の強度が高まることがあります。
- 温度:高温になると、アルミニウム合金の強度は低下します。したがって、A5052を使用する際には、使用温度にも留意する必要があります。
ヤング率とは何か
ヤング率(弾性率)は、材料が引張や圧縮の力を受けた際に、その変形の程度を示す物理量です。A5052アルミニウム合金のヤング率は約70 GPaです。ヤング率が高い材料ほど、変形しにくく、弾性変形が小さいことを意味します。 A5052はヤング率が適度であり、弾性の範囲内で適切な変形を許容しつつも、強度を発揮できるため、軽量化と強度を両立させることができます。この特性は、構造材として使用する際に重要です。例えば、航空機や車両の部品では、変形の抑制とともに強度を確保する必要があり、A5052はその特性を活かして最適な素材となります。A5052の硬度について
A5052アルミニウム合金の硬度は、材料がどれだけ外力に抵抗するかを示す指標です。A5052の硬度は、一般的にH32(硬化状態)で約60〜80 HRB(ロックウェルB硬度)となります。この硬度は、一般的な用途において十分な耐摩耗性を提供し、特に機械的な強度が求められる部分で活用されています。 硬度は、A5052が衝撃に強いことを意味し、耐摩耗性や耐久性が求められる環境下で優れた性能を発揮します。また、硬度が適度であるため、加工性にも優れており、切削加工や成形加工を行う際にも問題が少ないという特性があります。A5052の機械的特性のまとめ
A5052アルミニウム合金は、優れた耐力、強度、ヤング率、硬度を兼ね備え、さまざまな産業での使用に最適な材料です。その機械的特性により、軽量化と高強度を必要とする航空機、自動車、化学機器、海洋機器など、さまざまな用途で重宝されています。特に、強度に影響を与える要因を理解し、適切に熱処理や加工を施すことで、その性能を最大限に引き出すことが可能です。A5052アルミニウム合金の加工性とその特徴
A5052アルミニウム合金は、優れた加工性を持つため、多くの製造プロセスで使用されています。この記事では、A5052の切削性、加工時の注意点、そして他のアルミニウム合金との切削性の比較について詳しく説明します。A5052の切削性について
A5052アルミニウム合金は、一般的に良好な切削性を持つとされ、精密な加工が可能です。A5052の切削性の良さは、アルミニウム合金の中でも特に優れた特性を示します。この合金は、切削時に生成される切りくずが比較的小さく、表面仕上げが良好であるため、金型や精密部品の加工に適しています。また、比較的低い切削力で加工できるため、加工中の工具への負担も少なく、長寿命を確保しやすい点も大きな利点です。 さらに、A5052は他のアルミニウム合金に比べて、加工時に過度な熱を発生させにくいという特性もあり、切削中の温度管理が容易です。これにより、精密な加工が求められる際にも安定した性能を発揮します。加工時の注意点と工夫
A5052の加工においては、いくつかの注意点と工夫が必要です。主なものを以下に挙げます:- 工具の選定:A5052の切削時には、適切な切削工具を選定することが重要です。特に、硬度が高いため、耐摩耗性の良い工具を使用することが求められます。ダイヤモンドコーティングやチタンコーティングされた工具が特に有効です。
- 切削速度の調整:A5052は適切な切削速度で加工することで、最良の結果を得ることができます。過度な切削速度を避け、低すぎる速度でも効果的に加工ができるよう調整します。切削液の使用も重要で、冷却と潤滑を確実に行うことが、工具寿命の延長に繋がります。
- 切りくずの処理:A5052を加工する際には、切りくずが生成されやすく、それが加工精度に影響を与えることがあります。したがって、切りくずを効率的に排出し、材料が詰まらないように注意する必要があります。適切な切削条件を設定し、切りくずが詰まらないようにすることが大切です。
- 熱管理:A5052は熱を発生しにくい合金ですが、長時間の加工や高い切削速度を使用すると熱が発生する可能性があります。これにより、変形や品質低下を招く可能性があるため、冷却効果の高い切削液や適切な冷却方式を使用して、熱の発生を抑える工夫が必要です。
他のアルミニウム合金との切削性比較
A5052の切削性を他のアルミニウム合金と比較すると、次のような特徴があります:- A2024:A2024は高強度のアルミニウム合金ですが、A5052よりも切削性は若干劣ります。特に、A2024は硬度が高いため、切削時に工具に対する負荷が大きく、冷却や切削条件の最適化がより重要です。
- A6061:A6061は汎用性の高い合金であり、A5052と同様に良好な切削性を持っていますが、A5052はより優れた耐食性を持ち、腐食環境下での利用が求められる場合にはA5052の方が適していることが多いです。
- A7075:A7075は非常に強度が高いアルミニウム合金であり、切削性はA5052よりも劣ります。A7075の切削時には、特に精密加工が難しく、切削条件や工具の選定に注意が必要です。
まとめ
A5052アルミニウム合金は、非常に軽量でありながらも高い強度を持っています。その比重は低く、耐力があるため、様々な産業分野で広く利用されています。この合金は航空機部品や自動車のボディパネル、建築材料などに使用され、その強度と軽さから高い評価を受けています。このような利点を活かし、A5052アルミニウム合金は幅広い用途において重要な役割を果たしています。アルミニウム合金A1050 H24完全ガイド!その特性と用途を徹底解説
アルミニウム合金A1050 H24について知りたいと思ったことはありませんか?それなら、この完全ガイドがお手伝いします。本記事では、アルミニウム合金A1050 H24の特性や用途について詳しく解説していきます。
アルミニウム合金A1050 H24は、どのような特性を持ち、どのような場面で活躍するのでしょうか?この記事では徹底的にその姿を明らかにします。さらに、その特性や用途を理解することで、製品の選定や活用方法に役立つ情報を提供します。
アルミニウム合金A1050 H24について知りたい方、その特性や用途に興味を持っている方、ぜひこの記事を参考にしてみてください。それでは、アルミニウム合金A1050 H24の魅力に迫っていきましょう。
Contents
アルミニウム合金A1050 H24の基礎知識
アルミニウム合金A1050 H24は、優れた加工性と耐腐食性を有するアルミニウム合金の一種です。以下では、A1050 H24の特徴、化学的組成、物理的性質について詳しく解説します。A1050 H24とは:アルミニウム合金の基本
A1050 H24は、主に純度99.5%以上のアルミニウムをベースにした合金で、アルミニウムと微量の他の金属を加えたものです。この合金は、優れた耐腐食性と成形性、良好な導電性を持ち、主に電子機器、建築材料、食品パッケージなどに使用されています。H24は、冷間加工後の半硬化状態を示しており、適度な強度と柔軟性を持っています。アルミニウム合金とは:概要と分類
アルミニウム合金は、アルミニウムに他の元素(主に銅、マグネシウム、マンガン、シリコン、亜鉛など)を加えた金属であり、強度や耐腐食性、加工性などの特性を向上させています。アルミニウム合金は、主に以下のシリーズに分類されます:- 1xxxシリーズ(純アルミニウム): 高い耐腐食性と導電性が特徴。A1050はこのシリーズに含まれます。
- 2xxxシリーズ(銅合金): 強度が高いが、耐腐食性は低い。
- 3xxxシリーズ(マンガン合金): 低至中程度の強度と良好な成形性。
- 5xxxシリーズ(マグネシウム合金): 高い耐腐食性と良好な溶接性。
- 6xxxシリーズ(シリコン・マグネシウム合金): 良好な機械的特性と成形性。
- 7xxxシリーズ(亜鉛合金): 高強度、主に航空機などの構造材に使用。
A1050 H24の化学的組成
A1050 H24の化学的組成は、次の通りです:- アルミニウム (Al): 約99.5%
- 銅 (Cu): 最大0.05%
- マグネシウム (Mg): 最大0.03%
- マンガン (Mn): 最大0.05%
- シリコン (Si): 最大0.25%
- 鉄 (Fe): 最大0.4%
アルミニウムの物理的性質
アルミニウム合金A1050 H24の主な物理的特性は以下の通りです:- 密度: 約2.7 g/cm³
- 引張強度: 約140〜180 MPa
- 耐腐食性: 非常に高い。特に海水や湿気の多い環境で優れた耐腐食性を発揮します。
- 熱伝導性: 高い熱伝導性を持ち、熱を迅速に分散する能力があります。
- 電気伝導性: 高い電気伝導性を持ち、電子機器や配線材として使用されることがあります。
- 延性と加工性: 高い延性を持ち、複雑な形状に成形しやすい特性があります。
アルミ調質H24の特性
アルミ調質H24は、冷間加工後に部分的な硬化が施されたアルミニウム合金の一種です。H24調質のアルミニウムは、良好な加工性、強度、耐食性を兼ね備えており、さまざまな用途に適しています。以下では、H24調質のアルミニウムの特性について詳しく解説します。調質とは:アルミニウムの熱処理
調質とは、金属材料に熱を加えて、その性質を変化させる熱処理プロセスのことです。アルミニウム合金においては、調質は主に以下のプロセスで行われます:- アニーリング(焼鈍):金属を高温に加熱した後、ゆっくり冷却して硬度や強度を低下させる。
- 焼き戻し:金属を高温で加熱し、その後急冷または冷却して機械的性質を変化させる。
- 冷間加工:金属を塑性変形させる加工方法で、強度を高めるために行われます。
H24調質のプロセス
H24調質のプロセスは、アルミニウム合金を冷間加工(圧延や引き伸ばしなど)した後、部分的に熱処理を加えます。この熱処理によって、金属の硬さや強度が増しつつも、完全な硬化(H28やH32など)には至りません。結果として、適度な強度と延性が確保されるため、加工性が良好で、さまざまな製造工程に適しています。 H24の調質状態では、アルミニウムは「半硬化」と呼ばれ、冷間加工後の強度と柔軟性のバランスが取れた状態です。これにより、機械的加工が可能で、部品の寸法精度を保ちやすくなります。H24調質の機械的性質
H24調質のアルミニウムは、次のような機械的特性を持ちます:- 引張強度: 約160〜230 MPa程度
- 伸び: 3〜8%(耐引張り性と延性がバランスよく確保されています)
- 硬度: 中程度の硬度を有し、適度な加工性と耐摩耗性を持っています。
- ねじり強度: 高いねじり強度を持ち、さまざまな機械的負荷に耐えることができます。
A1050 H24の耐食性と耐候性
A1050 H24は、特に耐食性に優れた特性を持っています。アルミニウム合金は、酸化防止層(アルミニウム酸化膜)を自然に形成するため、湿度や酸性環境などに強い耐食性を示します。A1050 H24の主な耐食性特性には以下の点が挙げられます:- 耐塩害性: 特に塩水環境(海水や塩害)に対して強い耐腐食性を持ち、海洋環境や沿岸地域での使用に適しています。
- 耐アルカリ性: アルミニウムはアルカリ性にも強いため、化学的な攻撃を受けにくい特性があります。
- 耐酸性: 酸性環境でも、酸化膜が保護層として働き、腐食を抑制します。
アルミニウム合金A1050 H24の機械的性質
アルミニウム合金A1050 H24は、主に冷間加工されたアルミニウムで、適度な強度と延性を兼ね備えています。以下では、A1050 H24の引張強度、降伏点、伸び、硬さ、そして疲労強度について解説します。引張強度と降伏点
- 引張強度: A1050 H24の引張強度は、約160〜230 MPa(メガパスカル)の範囲であり、この値は冷間加工による部分的な硬化状態を反映しています。引張強度は、材料が引っ張り力に耐えられる最大の強度を示し、A1050 H24は中程度の強度を持つため、一般的な構造部品や軽量化を求める用途に適しています。
- 降伏点: 降伏点は、材料が弾性変形から塑性変形に変わる応力のことを指します。A1050 H24の降伏点は約100〜130 MPa程度です。この範囲の降伏点は、軽荷重の構造物や部品において優れた性能を発揮します。
伸びと硬さ
- 伸び: 伸びは、材料が破断するまでにどれだけ引き伸ばされるかを示す指標であり、A1050 H24の伸びは約3〜8%です。この値は、適度な延性を持つことを意味しており、冷間加工後でも材料の加工性や延性が保たれています。軽量構造部品の製造において重要な特性です。
- 硬さ: A1050 H24の硬さは中程度であり、Rockwell Bスケールで約40〜50 HRB(硬さ値)に相当します。この値は、材料が機械的加工を受けやすく、切削や成形加工などに適していることを示しています。硬さは材料の耐摩耗性にも関係しており、日常的な使用には十分な耐久性を持っています。
A1050 H24の疲労強度
- 疲労強度: 疲労強度は、繰り返し荷重がかかる条件下で材料が破壊される前に耐えられる最大応力を示します。A1050 H24の疲労強度は、約100〜150 MPaの範囲です。この値は、繰り返しの応力が加わる環境でも一定の耐久性を持ち、軽負荷の機械部品や構造部品において信頼性の高い性能を提供します。
アルミニウム合金A1050 H24の加工と試作
アルミニウム合金A1050 H24は、軽量で加工性に優れており、さまざまな製造プロセスで使用されています。以下では、A1050 H24の加工方法について、切削加工、曲げ加工、溶接性を中心に解説します。加工方法の概要
A1050 H24は冷間加工されたアルミニウム合金であり、加工性が良好であり、軽量かつ高い延性を持つため、複雑な形状の部品や試作に広く使用されています。A1050 H24の加工には、切削、曲げ、溶接などのさまざまな手法があり、それぞれの手法に対する適切な技術と注意点があります。切削加工とその特徴
切削加工は、A1050 H24の製造で最も一般的に使用される方法の一つです。この合金は、比較的柔らかく、切削性に優れているため、高い精度を持つ部品を製造することができます。具体的には、フライス盤や旋盤を使用した加工が行われます。- 特徴:
- A1050 H24は切削加工時に材料が比較的軽く切削でき、工具の摩耗も少ないです。
- 高精度の部品を製造でき、複雑な形状にも対応可能。
- 切削速度や工具の種類を適切に選ぶことで、加工の効率性を高めることができます。
- 注意点:
- 切削中に発生する熱を適切に管理するため、冷却剤の使用が推奨されます。
- 精度の高い加工には、工具の磨耗に注意し、定期的なメンテナンスが必要です。
曲げ加工とその注意点
曲げ加工は、A1050 H24を使用した製品においてもよく行われる加工方法であり、金型を使って所定の形状に材料を曲げるプロセスです。この合金は比較的柔軟であり、曲げ加工が容易です。- 特徴:
- A1050 H24は高い延性を持ち、適度な硬さのため、曲げ加工に向いています。
- 複雑な形状や小さな角度の曲げ加工も可能です。
- 注意点:
- 曲げ半径が小さすぎると、ひび割れや割れの原因になることがあるため、曲げ半径を適切に選定することが重要です。
- 過度な変形を避けるため、加工中の圧力や温度を調整する必要があります。
A1050 H24の溶接性
A1050 H24は、比較的優れた溶接性を持ち、アルミニウム合金の中でも溶接が比較的簡単に行えます。溶接には、TIG(タングステン・インターナル・ガス)溶接やMIG(メタル・インターナル・ガス)溶接が適しています。- 特徴:
- 良好な溶接性を持ち、溶接後に強度や耐久性のある接合が得られます。
- アルミニウム合金の中でも低温で溶接が可能なため、低温でも割れにくい性質を持っています。
- 注意点:
- 溶接中に熱による変形が発生しやすいため、適切な冷却と加熱が必要です。
- アルミニウムの酸化皮膜が溶接不良を引き起こすことがあるため、表面処理を十分に行ってから溶接を行うことが求められます。
アルミニウム合金の種類と特性の比較
アルミニウム合金は、その特性や用途に応じて多くの種類に分類され、各合金には異なる強度、耐食性、加工性、耐熱性などの特徴があります。以下では、A1050と他の代表的なアルミニウム合金との比較を行い、用途に応じた合金の選定基準について説明します。A1050と他の合金との比較
アルミニウム合金は主に1xxx、2xxx、3xxx、5xxx、6xxx、7xxxなどの系統に分けられ、それぞれに特性が異なります。A1050は1xxx系合金であり、主に純度の高いアルミニウムをベースにしています。- A1050 (1xxx系):
- 主成分: 99.5%以上のアルミニウム
- 特性: 高い耐食性、優れた加工性、低い強度
- 用途: 化学機器、電気機器、建材など、軽量で腐食に強い材料が求められる分野
- A2024 (2xxx系):
- 主成分: アルミニウムに銅を加えた合金
- 特性: 高い強度と耐久性、疲労強度に優れるが、耐食性は低い
- 用途: 航空機の構造材、運動部品、機械的要求の厳しい分野
- A3003 (3xxx系):
- 主成分: アルミニウムにマンガンを加えた合金
- 特性: 高い耐食性と加工性、普通の強度、良好な溶接性
- 用途: 銀行の建材、屋根材、化学設備など、軽い負荷がかかるが耐食性が重要な用途
- A5052 (5xxx系):
- 主成分: アルミニウムにマグネシウムを加えた合金
- 特性: 良好な強度と耐食性を持ち、海水に対しても耐性がある
- 用途: 船舶の構造材、海洋機器、自動車など、強度と耐食性が重要な用途
- A6061 (6xxx系):
- 主成分: アルミニウムにマグネシウムとシリコンを加えた合金
- 特性: 良好な強度と耐食性、優れた加工性、溶接性に優れる
- 用途: 建設、航空、車両の構造材など、強度と加工性が重要な用途
- A7075 (7xxx系):
- 主成分: アルミニウムに亜鉛を加えた合金
- 特性: 非常に高い強度を持つが、耐食性はやや劣る
- 用途: 航空機、軍事、運動部品など、高強度が求められる用途
合金ごとの特性と選定基準
アルミニウム合金を選定する際には、目的に応じて以下の要素を考慮することが重要です。- 強度:
- 高強度が必要な場合は、A2024やA7075などの2xxx系や7xxx系が適しています。これらの合金は機械的要求が高い用途に最適です。
- 耐食性:
- 高い耐食性が求められる用途には、A1050やA3003、A5052など、マンガンやマグネシウムを含む合金が適しています。これらの合金は腐食が厳しい環境に適しています。
- 加工性:
- 加工のしやすさが求められる場合、A1050やA6061などが良い選択肢です。これらの合金は加工性に優れており、切削や溶接が容易です。
- 溶接性:
- 溶接が重要な用途には、A3003やA6061などの合金が適しています。これらは溶接性に優れ、強度を保ちながら接合できます。
- 重量:
- 軽量が求められる用途には、A1050などの低強度で軽い合金が向いています。航空機や車両の構造材などで使用されます。
用途に応じた合金の選び方
- 耐食性重視: A1050、A5052など。腐食に強いアルミニウム合金が必要な場合に最適です。
- 高強度重視: A2024、A7075など。高強度や高耐久性が求められる航空機や軍事用途に適しています。
- 優れた加工性と溶接性: A6061、A3003など。加工がしやすく、溶接性も良好なため、建設や車両製造に適しています。
- 軽量化重視: A1050、A3003など。軽量でありながら耐食性を保持し、車両や運搬用の部品などに使われます。
まとめ
アルミニウム合金A1050 H24は、耐食性と耐久性に優れた特性を持っています。これは、建築や自動車産業などの幅広い用途で利用されています。A1050 H24の特性は、軽量でありながらも十分な強度を持ち、加工性にも優れています。そのため、製造業界では成形加工や溶接加工に適しています。さらに、耐食性も高いため、海洋環境や食品加工業界など、腐食にさらされる環境でも優れた性能を発揮します。A1050 H24は、多くの産業分野で重要な役割を果たしており、その用途の幅広さと特性の優れた点から、今後も需要が増えることが期待されています。“A2017合金の切削性と加工のポイント”
A2017合金は、その高い強度と耐食性から幅広い産業で使用されています。しかし、その切削性能には課題があります。本記事では、A2017合金の切削性と加工のポイントに焦点を当てて解説します。A2017合金を効果的に加工するためには、どのようなポイントに注意すべきなのか、そのノウハウをご紹介します。切削性に関する理解が深まれば、加工品質の向上や生産効率の向上に繋がることでしょう。さあ、A2017合金における切削性と加工のポイントを探求してみましょう。
Contents
A2017合金の基本
A2017合金は、アルミニウムを基盤とした合金で、特に高い強度を持ちながらも軽量で、航空宇宙産業や自動車産業などで広く使用されています。これらの合金は、優れた機械的性質と耐食性を備えており、特定の環境条件での性能が求められる部品に適しています。A2017合金とは
A2017合金は、アルミニウムと銅を主成分として構成されるアルミニウム合金で、主に航空機や構造部材に使用される材料です。アルミニウム合金の中でも特に高強度を誇り、耐食性にも優れており、航空機や車両などの高負荷がかかる部品での使用が一般的です。 この合金は、強度が求められる用途において、特に重要な役割を果たします。銅の添加により、アルミニウム合金の強度が向上し、高い耐摩耗性を実現しています。A2017合金の成分と特性
A2017合金の成分には、以下の主な金属が含まれています:- アルミニウム (Al):主成分で、軽量で加工しやすい性質を持つ。
- 銅 (Cu):合金の強度を向上させる。特に耐摩耗性や強度が必要な部品に有効。
- シリコン (Si):鋳造性や耐食性を向上させるために微量添加されることがある。
- マグネシウム (Mg):強度をさらに強化し、合金の耐食性を向上させる。
- 鉄 (Fe)、マンガン (Mn)、クロム (Cr):微量成分として含まれ、耐食性や機械的性質に寄与する。
- 高強度:銅がアルミニウムに加えられることで、強度が大幅に向上します。これにより、航空機や自動車部品に使用されることが多いです。
- 耐食性:特に耐食性が求められる環境での使用に適しており、一定の耐腐食性を持っています。
- 軽量性:アルミニウム合金であるため、比較的軽量で、重量制限が厳しい用途にも適しています。
- 加工性:強度が高い一方で、加工しやすい特性を持っています。
A2017合金の機械的性質
A2017合金は、その優れた機械的性質から、特に高負荷を受ける部品や構造部材に利用されます。主な機械的特性は以下の通りです:- 引張強さ:A2017合金は非常に高い引張強さを持ち、構造部材として強度が求められる部品に適しています。
- 降伏強度:降伏強度が高いため、強い力を加えても変形しにくい性質を持っています。
- 硬度:硬度が高く、摩擦や磨耗に強いです。これにより、機械的な部品やエンジン部品などの長寿命化が期待できます。
- 延性:延性が低めであるため、過度の引張りや曲げには注意が必要ですが、適切な使用範囲内では十分な性能を発揮します。
A2017合金の切削性について
A2017合金は高強度で耐摩耗性が優れているため、切削性に関して特有の課題が存在します。しかし、その特性を理解し、適切な加工方法を採用することで、効率的に加工することができます。ここでは、A2017合金の切削性の概要、特徴、課題、解決策について詳しく解説します。切削性の概要
切削性とは、金属や合金を切削工具で加工する際の難易度や効率を指します。切削性が良い材料は、加工中に工具の摩耗や発熱が少なく、加工速度が速く、仕上がりも良好である一方、切削性が悪い材料は逆に加工が困難で、工具の寿命が短くなることがあります。A2017合金は、高強度であるため、切削性が一般的に難しいとされますが、適切な技術と工具を使用することで効率的に加工することが可能です。A2017合金の切削性の特徴
A2017合金の切削性にはいくつかの特徴があります:- 硬度が高い:A2017合金は強度と硬度が高いため、切削中に高い切削力が必要です。このため、一般的な鋼やアルミニウム合金に比べて切削加工が難しくなることがあります。
- 摩耗が早い:合金中の銅成分が硬く、摩耗が激しくなるため、切削工具の消耗が早くなる傾向があります。これにより、加工の際には適切な冷却や切削条件の調整が必要です。
- 熱伝導性が低い:A2017合金は熱伝導性が低いため、切削中に発生する熱が工具に伝わりにくく、工具の温度が上昇しやすいです。これにより、工具の寿命が短くなり、加工精度に悪影響を及ぼす可能性があります。
- 切削時のチッピングやひび割れ:硬度が高いため、切削中にチッピング(欠け)やひび割れが発生することがあります。特に急激な温度変化や強い力が加わる場合に注意が必要です。
切削加工時の課題と解決策
A2017合金の切削加工において直面する課題とその解決策は以下の通りです:- 工具の摩耗が早い
- 解決策:切削工具の材料として、耐摩耗性に優れた超硬工具やコーティングツールを使用することが推奨されます。これにより、工具の寿命が延び、効率的に加工を進めることができます。
- 発熱による工具の劣化
- 解決策:冷却液の使用や適切な切削条件(切削速度、送り速度)を調整することで、工具の温度上昇を抑制できます。高圧冷却やエアブローなどの冷却方法を導入することも効果的です。
- 切削力が大きいため、加工が困難
- 解決策:切削条件(切削速度、送り量)を適切に調整し、最適な切削力を選定することが重要です。また、複数回に分けて切削を行うことで、切削力を分散させ、安定した加工を行います。
- 仕上がり面に不良が生じやすい
- 解決策:最適な切削工具と条件を使用し、仕上げ加工の際に細かい調整を行うことで、仕上げ面の品質を向上させることができます。また、切削油や冷却液を十分に使用することで、表面の仕上がりを改善できます。
- チッピングやひび割れの発生
- 解決策:切削条件を慎重に設定し、急激な温度変化や強い力を避けることが重要です。また、切削工具の先端角度や切削パラメータを最適化することで、ひび割れのリスクを低減できます。
A2017合金の加工方法
A2017合金は高強度・高硬度であり、その特性を活かした加工が求められます。適切な加工方法を選択することで、効率よく、精度の高い製品を作成することが可能です。以下では、A2017合金の加工方法について、加工前の準備から主要な加工技術、加工精度を高めるためのポイントまで詳しく解説します。加工前の準備
A2017合金を加工する前には、いくつかの準備が重要です:- 素材の選定:A2017合金の特性を理解し、用途に適した形状やサイズを選ぶことが重要です。例えば、強度や耐摩耗性が必要な部品には、この合金を選択します。
- 切削条件の設定:A2017合金は硬度が高く、切削時に発生する熱が工具に与える影響を抑えるために、冷却液や切削油を使用します。切削速度、送り速度、切り込み深さを最適化することが加工の効率を高めます。
- 工具の選定:A2017合金は硬度が高いため、耐摩耗性に優れた工具を選ぶ必要があります。超硬工具やコーティング工具が効果的です。また、工具の研磨やメンテナンスを行い、長時間の加工に耐えられる状態を保つことが重要です。
主要な加工技術
A2017合金の加工には、主に以下の技術が使用されます:- 旋削加工:A2017合金の旋削加工では、高精度な切削が求められます。工具の摩耗が早いため、適切な切削条件と冷却手段を確保することが必要です。
- フライス加工:フライス盤を使用した加工は、複雑な形状の部品にも対応可能です。切削中の発熱や摩耗を抑えるため、冷却液を使用し、最適な切削パラメータを設定します。
- 穴あけ加工:A2017合金の穴あけは、適切なドリルの選定と切削条件が必要です。低速での切削を行い、発熱を抑制します。ドリル先端のコーティングが摩耗を減らす助けになります。
- 研削加工:高精度な仕上げ加工が求められる場合、研削加工が用いられます。A2017合金の硬度に対応した研削盤と適切な砥石を使用することが、品質向上につながります。
加工精度を高めるポイント
A2017合金はその高強度により、加工精度が求められる場合があります。精度を高めるためのポイントは以下の通りです:- 適切な切削条件の選定:切削速度や送り速度を最適化することが加工精度に直結します。切削中の振動や温度変化を最小限に抑えることが、精度を保つための基本です。
- 高精度な工具管理:工具の摩耗は加工精度に大きな影響を与えます。工具の状態を常に監視し、適切なタイミングで交換することが重要です。また、工具の冷却と研磨を定期的に行うことも精度維持に役立ちます。
- 冷却方法の最適化:A2017合金は熱膨張や温度変化に敏感なため、冷却液やエアブローによる冷却方法を最適化し、加工中の熱管理を徹底します。冷却液は切削面や工具に均等に供給することが精度向上につながります。
- 加工機械の安定性の確保:加工中の振動や変形を最小化するために、機械の剛性を高め、振動を抑える対策を講じます。さらに、加工機の定期的なメンテナンスも精度向上に寄与します。
A2017合金の加工工具と設備
A2017合金はその高強度と硬度により、加工が難しい材料ですが、適切な工具と加工設備を選定することで、効率的に加工を行うことができます。以下では、A2017合金の加工における切削工具の選択、工具の保守管理、そして加工設備の特性と選定について解説します。適切な切削工具の選択
A2017合金の加工には、以下のような特性を持つ切削工具が求められます:- 超硬工具:A2017合金は硬度が高く、通常の工具では摩耗が早く進行するため、超硬工具やセラミック工具がよく使用されます。これらの工具は、高温に強く、摩耗に対する耐性が高いため、長時間の加工に適しています。
- コーティング工具:A2017合金のような難加工材料には、コーティングされた工具(例えば、TiAlNやTiNコーティング)が効果的です。これにより、工具の摩耗を減少させ、切削性能を向上させます。また、コーティングは切削中の発熱を抑える役割も果たします。
- 微細な刃先の工具:精密加工が求められる場合には、微細な刃先を持つ工具を使用することが、切削精度を保つために重要です。これにより、細かい加工や高精度な仕上げが可能になります。
工具の保守と管理
切削工具の性能を最大限に引き出すためには、工具の適切な保守と管理が必要です:- 定期的な検査と点検:工具の摩耗具合や損傷状態を定期的にチェックし、必要に応じて交換や修正を行います。特に、工具の刃先部分は摩耗が早いため、定期的な検査が重要です。
- 工具の研磨:摩耗が進んだ工具は、研磨して再利用することができます。研磨を行うことで、工具の寿命を延ばし、経済的な負担を軽減できます。
- 工具交換のタイミング:切削条件や加工時間に基づいて、適切なタイミングで工具を交換することが重要です。工具が摩耗すると加工精度が低下し、製品の品質に影響を与えるため、交換のタイミングを見極めることが求められます。
加工設備の特性と選定
A2017合金の加工には、特定の加工設備の特性に合った選定が必要です:- 高剛性の加工機械:A2017合金は硬度が高いため、加工中に発生する振動や変形を最小限に抑えるために、高剛性の加工機械を選ぶことが重要です。加工機の剛性が不足していると、切削精度や仕上がりに影響が出ます。
- 冷却システムの整備:A2017合金は切削中に高温になりやすいため、冷却システムの有無やその性能が重要です。エアブローや冷却液の供給が適切に行われることで、加工時の発熱を抑制し、工具寿命を延ばします。
- 高速加工機械:A2017合金のような難加工材料を効率よく加工するためには、高速加工機械が求められます。これにより、切削速度や送り速度を最適化し、加工時間を短縮することができます。
- CNC制御機械:精密な加工が要求される場合、CNC(コンピュータ数値制御)機械を使用することで、加工精度を向上させることが可能です。CNC機械は、複雑な形状や高精度な加工を自動で行うことができ、加工ミスを減らすことができます。
A2024合金の特性:ヤング率を中心にした材料解析
A2024合金は、航空機や自動車などの様々な産業で広く使用されている特殊な金属です。その特性を理解することは、材料工学や設計において重要な課題です。特に、ヤング率はこの合金の重要な特性の一つであり、その材料解析は様々な工学上の応用に影響を与えます。本稿では、A2024合金の特性に焦点を当て、その中でも特にヤング率について詳しく解説していきます。材料工学や設計に興味がある方々にとって、この記事は貴重な情報源となるでしょう。
Contents
超ジュラルミン(A2024)の基本的理解
A2024は、アルミニウム合金の一種であり、特に航空機や高性能な構造物に使用されることが多い「超ジュラルミン」として知られています。この合金は、強度、軽さ、耐食性に優れており、さまざまな高強度用途に適しています。以下では、A2024合金の定義、特徴、化学組成について詳しく説明します。A2024合金の定義と一般的な用途
A2024合金は、アルミニウム(Al)を基にして、銅(Cu)を主要な合金元素として添加した合金です。この合金は、主に高い強度と優れた耐食性を持っているため、航空機の構造材料や軍事用途に広く使用されています。 主な用途:- 航空機の構造部品: A2024は、飛行機の翼や胴体部分に使用され、軽量でありながら高い強度を持つため、航空業界で非常に重要です。
- 自動車部品: 高強度を要求される自動車の部品にも利用されます。特にレーシングカーやスポーツカーのパーツとして使用されることがあります。
- 船舶部品: 航空機と同様に、耐食性が要求される船舶部品にも使用されることがあります。
超ジュラルミンとしてのA2024の特徴
「超ジュラルミン」として知られるA2024合金は、非常に高い引張強度と耐食性が特徴です。これらの特性により、過酷な条件下でも使用可能です。 特徴:- 高強度: A2024は、軽量でありながら引張強度が高く、航空機などの構造部品に理想的な特性を持っています。
- 優れた耐食性: 特に機械的性質に加え、耐食性も高く、過酷な環境においても腐食に強い特性を発揮します。
- 熱処理による強化: A2024は熱処理によってその強度を向上させることができます。特に、人工時効処理を施すことで、強度が大きく向上します。
A2024合金の化学組成と処理
A2024合金の化学組成には、主に以下の元素が含まれます。これらの元素は、合金の特性を決定付ける重要な要素です。 化学組成:- アルミニウム(Al): 基本材料であり、合金の基盤となります。
- 銅(Cu): A2024合金の主要合金元素で、強度と耐食性を向上させます。
- マグネシウム(Mg): 合金の強度を高めるために使用されます。
- マンガン(Mn): 強度と耐食性をサポートする役割を果たします。
- シリコン(Si): 合金の流動性を向上させるために微量添加されます。
- 溶体化処理(Solution Heat Treatment): 高温で溶体化処理を行い、合金成分を均一にします。
- 時効硬化(Aging): 時効処理により、合金内部の析出物が硬化し、強度が向上します。人工時効によって特に強度が増します。
A2024合金のヤング率
A2024合金は、航空機や高強度構造物に使用されるアルミニウム合金であり、その物理的特性の一つに「ヤング率」があります。ヤング率は、材料の弾性を表す指標として、材料の変形に対する抵抗力を示します。以下では、ヤング率の定義や測定方法、A2024合金におけるヤング率がどのような性質を示すのかについて詳しく解説します。ヤング率とは何か?
ヤング率(Young’s Modulus)は、材料がどれだけ引っ張りに対して抵抗するかを示す物理的な定数です。具体的には、材料に引っ張り応力を加えたときに、どれだけ変形するかを定量的に示します。ヤング率が高いほど、その材料は変形しにくく、弾性が高いことを意味します。 ヤング率の定義:- 弾性領域内の応力/ひずみの比: ヤング率は、材料にかかる応力(力/面積)とひずみ(変形量)との比として定義されます。
- 弾性領域内では、応力とひずみは比例関係にあります。この比例定数がヤング率です。
A2024のヤング率の測定方法
A2024合金のヤング率は、材料に引っ張り試験を行うことによって測定されます。この試験では、標準的な試験片に引っ張り力を加え、変形量を測定します。その後、応力とひずみの関係を求めることで、ヤング率が算出されます。 測定手順:- 引っ張り試験: A2024合金の標本を指定された形状に加工し、一定の速度で引っ張り力を加えます。
- 応力とひずみの測定: 引っ張り中の応力(力/断面積)とひずみ(元の長さに対する伸び)を測定します。
- ヤング率の計算: 応力とひずみの関係をプロットし、線形領域での傾きを計算することにより、ヤング率が得られます。
ヤング率が示すA2024の性質
A2024合金のヤング率は、材料の弾性特性を理解するために重要です。A2024のヤング率は約73 GPa(ギガパスカル)であり、アルミニウム合金の中では比較的高い部類に入ります。この特性により、A2024合金は高強度かつ高剛性の要求されるアプリケーションに適しています。 A2024のヤング率が示す性質:- 高剛性: ヤング率が高いA2024合金は、外力がかかっても変形しにくく、構造物や部品として高い剛性を持っています。このため、航空機の構造部材や機械部品に広く使用されます。
- 適切な弾性範囲: ヤング率が示す弾性範囲内では、材料は応力を解放した際に元の形状に戻ります。A2024はこの範囲で使用することで、優れた耐久性と強度を維持します。
- 高い耐力: 強度が高いだけでなく、変形に対しても高い抵抗力を持つため、A2024合金は過酷な環境下でも安定した性能を発揮します。
金属材料の物理的・機械的特性
金属材料は、その使用環境や目的に応じて多くの物理的および機械的特性を持っています。これらの特性は、金属の選定や加工、使用時におけるパフォーマンスに大きな影響を与えます。以下では、金属材料の物理的および機械的特性について解説し、特にA2024合金の特性に焦点を当てます。物理的特性について
物理的特性は、金属の基本的な性質を示すもので、外部の力が加わった場合にどのように反応するかを理解するために重要です。これには以下のような特性が含まれます:- 密度: 金属の単位体積あたりの質量。密度が高いほど、金属は重くなり、その応用分野や設計に影響を与える。
- 熱伝導性: 熱エネルギーが金属内をどれだけ速く伝わるかを示す特性。高い熱伝導性を持つ金属は、熱を効率的に分散させます。
- 膨張率: 温度の変化に応じた金属の体積の変化率。膨張率が低いほど、温度変化に対する金属の寸法変化が小さく、精密な部品に有利です。
- 電気伝導性: 電気の流れやすさを示す特性。電気的な性能を必要とする場合、この特性が重要となります。
機械的特性の概要
機械的特性は、金属が力を受けたときにどのように反応するかを示すもので、金属の耐久性や強度に関わる重要な要素です。主な機械的特性には次のものがあります:- 引張強さ: 引っ張り応力に耐える能力を示す特性で、金属が破断するまでの最大応力に相当します。
- 降伏強さ: 金属が塑性変形を始める点で、これを超えると元の形状には戻りません。
- 硬さ: 金属が外部の圧力にどれだけ耐えるかを示し、切削や摩耗に関する耐性を表します。
- 延性: 引っ張られたときに金属がどれだけ伸びるかを示す特性で、延性が高いほど加工がしやすく、破壊に至りにくいです。
- 衝撃強さ: 金属が衝撃や急激な力に対してどれだけ耐えるかを示す特性で、過酷な条件で使用される部品に重要です。
A2024合金の物理的・機械的特性分析
A2024合金は、航空機や高強度構造物に使用されるアルミニウム合金で、優れた物理的および機械的特性を持っています。以下はその特性分析です:- 物理的特性:
- 密度: 約2.78 g/cm³。この密度により、軽量でありながら高強度を実現しています。
- 熱伝導性: 高い熱伝導性を有しており、温度変化に対応しやすい特性を持ちます。航空機部品などでは重要な特性です。
- 膨張率: 比較的低い膨張率を持っており、温度変化による寸法変化が少ないため、高精度な加工が求められるアプリケーションに適しています。
- 電気伝導性: 良好な電気伝導性を持ち、電気回路を構成する際にも使用されることがあります。
- 機械的特性:
- 引張強さ: 約470 MPa。高強度を必要とする航空機や構造物の部材に適しています。
- 降伏強さ: 約350 MPa。強い荷重がかかる状況でも、安定した性能を発揮します。
- 硬さ: 高い硬度を持ち、摩耗や疲労に強い特性を発揮します。
- 延性: 中程度の延性を持ち、加工においても十分な可塑性を示します。
- 衝撃強さ: 高い衝撃強さを持ち、航空機などの過酷な条件でも使用に耐えられます。
アルミ合金の強度と比較
アルミ合金は、その軽量さ、耐食性、加工性の良さから、さまざまな産業で広く利用されています。特に、航空機や自動車など、高強度が求められる分野で使用されるアルミ合金は、その強度や性能の違いによって適切な選定が重要です。以下では、アルミ合金の種類とその強度特性、そしてA2024合金の強度と他のアルミ合金との比較を行います。アルミ合金の種類とその強度特性
アルミ合金は主に以下の種類に分けられ、それぞれに特性があります:- 1系(純アルミニウム):
- 主成分:アルミニウム
- 強度:低いが、優れた耐食性と良好な加工性を持つ。
- 用途:化学設備、電気機器、建築材料など。
- 2系(アルミニウム-銅合金):
- 主成分:アルミニウム+銅
- 強度:非常に高い。特に航空機や高強度構造物に使用される。
- 用途:航空機の構造部品、飛行機の翼など。
- 3系(アルミニウム-マンガン合金):
- 主成分:アルミニウム+マンガン
- 強度:中程度。耐食性が高く、特に海洋環境に強い。
- 用途:船舶、海洋設備など。
- 5系(アルミニウム-マグネシウム合金):
- 主成分:アルミニウム+マグネシウム
- 強度:中程度から高い。軽量かつ良好な耐食性を持つ。
- 用途:車両の構造部品、圧力容器など。
- 6系(アルミニウム-シリコン合金):
- 主成分:アルミニウム+シリコン
- 強度:中程度。耐摩耗性が高く、溶接性に優れる。
- 用途:エンジン部品、機械部品など。
- 7系(アルミニウム-亜鉛合金):
- 主成分:アルミニウム+亜鉛
- 強度:非常に高い。特に軽量で高強度な部品に使用される。
- 用途:航空機、軍事用機器、戦闘機の部品など。
A2024合金の強度と他合金との比較
A2024合金は、アルミニウム合金の中でも非常に高い強度を誇り、特に航空機や高強度部品に広く使用されています。他のアルミ合金と比較した場合、A2024は以下のような強度特性を持っています:- A2024合金:
- 主成分:アルミニウム+銅
- 引張強さ:約470 MPa
- 降伏強さ:約350 MPa
- 用途:航空機の構造部品、戦闘機の部品など。
- 特徴:非常に高い強度と良好な疲労特性を持ち、過酷な条件での使用に耐えます。
- A7075合金(アルミニウム-亜鉛合金):
- 引張強さ:約570 MPa
- 降伏強さ:約505 MPa
- 用途:航空機、軍事用機器など。
- 特徴:A2024よりもさらに高い強度を持ちますが、加工性や耐食性はA2024に劣ることがあります。
- A6061合金(アルミニウム-マグネシウム-シリコン合金):
- 引張強さ:約310 MPa
- 降伏強さ:約250 MPa
- 用途:自動車、建築、機械部品など。
- 特徴:A2024よりは強度は低いものの、非常に優れた耐食性を持ち、溶接性に優れています。
- A5052合金(アルミニウム-マグネシウム合金):
- 引張強さ:約300 MPa
- 降伏強さ:約215 MPa
- 用途:海洋部品、化学設備など。
- 特徴:高い耐食性を持ち、特に海洋環境や化学環境での使用に適していますが、強度はA2024より低めです。
まとめ
A2024合金は、その高い強度と耐食性から航空機部品や自転車フレームなどの製造に広く使用されています。この合金の特性を理解する際には、特にヤング率に注目する必要があります。ヤング率は材料の剛性を示す指標であり、A2024合金は高いヤング率を持つことが知られています。これにより、耐久性や剛性が求められる構造部品の製造に適しています。この特性を活かして、さまざまな産業分野での利用が期待されています。A5083とA5052の違いは何?アルミ材質徹底比較
A5083とA5052の違いについて知識をお持ちですか?アルミニウム合金にはさまざまな種類がありますが、A5083とA5052は何が違うのでしょうか?それぞれの特性や用途、特徴について徹底比較してみましょう。
アルミ材料を使用する際に、正しい合金を選択することは非常に重要です。A5083とA5052は両方とも一般的に使用される合金ですが、それぞれ異なる特性を持っています。この比較を通じて、どちらがあなたのニーズやプロジェクトに適しているかを理解する手助けとなるでしょう。さあ、A5083とA5052の違いについて深く探求していきましょう。
Contents
A5052とA5083の基本的な違い
A5052の特徴と用途
A5052は、アルミニウム合金の一つで、主にマグネシウムを含む合金です。優れた耐食性と中程度の強度を持ち、軽量で加工性が良いため、幅広い用途に適しています。- 特徴:
- 優れた耐食性: 塩水や海洋環境に対する耐腐食性が高いため、海洋産業や化学設備などに多く使用されます。
- 中程度の強度: 強度が高くないため、重い荷重を支える用途には向きませんが、軽量化が求められる場面では非常に有効です。
- 良好な加工性: 溶接性や曲げ加工性に優れています。
- 用途:
- 船舶や海洋構造物: 海水環境での使用が多いため、船舶や海洋機器に適しています。
- 車両や自動車産業: 車両の軽量化のために使用されることがあります。
- 化学機器: 化学薬品や腐食性物質を取り扱う機器に使用されます。
A5083の特徴と用途
A5083は、A5052よりもさらに高い強度と優れた耐食性を持つアルミニウム合金です。特に高強度を必要とするアプリケーションにおいて使用されます。- 特徴:
- 優れた耐食性: A5052と同様に優れた耐食性を持ちながら、特に海水環境や化学物質に対して非常に高い耐性があります。
- 高い強度: 高強度が求められる用途に適しており、特に船舶や軍事用途に重宝されています。
- 難加工性: 高強度ゆえに、加工はA5052に比べて難しく、特に溶接時に注意が必要です。
- 用途:
- 船舶や海洋構造物: 高強度を必要とする船体や海洋構造物に多く使用されます。
- 軍事用途: 特に高強度が求められる装甲材や軍事機器に使用されます。
- 航空機産業: 航空機の一部部品に使用されることがあります。
A5052とA5083の化学成分の比較
成分 | A5052 | A5083 |
---|---|---|
アルミニウム | 残部 | 残部 |
マグネシウム | 2.2-2.8% | 4.0-4.9% |
銅 | 0.10%以下 | 0.10%以下 |
鉄 | 0.4%以下 | 0.4%以下 |
シリコン | 0.25%以下 | 0.25%以下 |
マンガン | 0.10%以下 | 1.0-1.5% |
クロム | 0.15-0.35% | 0.05%以下 |
- A5052: 主にマグネシウムとわずかなクロムを含んでおり、耐食性と加工性が特徴的です。
- A5083: マグネシウムの含有量が高く、マンガンを一定量含むことで強度と耐食性が向上しています。
物理的性質の比較
性質 | A5052 | A5083 |
---|---|---|
密度 | 2.68 g/cm³ | 2.66 g/cm³ |
引張強さ | 210-260 MPa | 315-380 MPa |
伸び率 | 12-20% | 10-15% |
屈服強さ | 190-220 MPa | 280-320 MPa |
熱伝導率 | 150 W/m·K | 140 W/m·K |
- A5052: 密度がA5083とほぼ同じですが、引張強さが低く、伸び率が高いため、柔軟な用途に適しています。
- A5083: 引張強さが高く、屈服強さも大きいため、強度が求められる用途に適しています。ただし、伸び率はA5052より低くなります。
アルミ材料の選び方
アルミ合金の種類と分類
アルミニウム合金は、その主成分によって分類され、それぞれが特有の特性を持ちます。アルミ合金の選択においては、強度、耐食性、加工性などの要素を基に最適な種類を選ぶことが重要です。以下の分類と特徴を参考にしてください。- 1000シリーズ(純アルミ) 99%以上の純度を持ち、優れた耐食性がありますが、強度は低いです。主に軽量かつ耐食性が要求される用途で使用されます。例えば、電線や化学プラントなどです。
- 2000シリーズ(銅系アルミ合金) 高い強度を持つが、耐食性が低い特徴があります。主に航空機やスポーツ機器などの高強度が必要な用途で使用されます。
- 3000シリーズ(マンガン系アルミ合金) 高い耐食性と優れた加工性を持ちますが、強度は中程度です。冷蔵庫、厨房機器、車両など、耐食性を重視する製品に適しています。
- 4000シリーズ(シリコン系アルミ合金) 溶接性が良く、耐摩耗性に優れる合金で、自動車部品などで使用されます。
- 5000シリーズ(マグネシウム系アルミ合金) 高い耐食性を持ち、特に海洋環境に強いです。船舶や化学機器、車両に多く使用されます。
- 6000シリーズ(マグネシウム・シリコン系アルミ合金) 強度と耐食性のバランスが良く、加工性にも優れています。建築材料や機械部品、交通機器などで広く使用されます。
- 7000シリーズ(亜鉛系アルミ合金) 高い強度を持ち、航空機やスポーツ機器に使用されますが、耐食性は低めです。
コストパフォーマンスの考慮
アルミ合金の選択においては、コストパフォーマンスも重要な要素です。以下のポイントを考慮し、用途に最適な合金を選ぶことが求められます。- 強度と耐食性のバランス 高強度が必要な場合には2000シリーズや7000シリーズを選ぶことが考えられますが、これらは高価であるため、実際に必要な強度に応じた合金を選ぶことが重要です。一方で、5000シリーズや3000シリーズは適度な強度を持ちつつ、コストを抑えることができます。
- 加工性の重視 加工性が良好な1000シリーズや3000シリーズは、コストパフォーマンスが高く、加工費用を抑えることができます。これらはコスト面で有利です。
- 耐食性の重要性 海洋環境や化学的に厳しい環境下で使用する場合、耐食性が非常に重要です。5000シリーズや3000シリーズなどが特に適しており、長期間使用しても耐久性が高いです。しかし、これらの合金はやや高価であるため、使用場所に応じて選定する必要があります。
アルミ材の特性と加工方法
アルミ材の一般的な特性
アルミニウムは軽量であり、耐食性に優れ、加工性が良好な特性を持つため、さまざまな産業で広く使用されています。以下はアルミ材の主な特性です。- 軽量性 アルミニウムは非常に軽い金属で、密度が約2.7 g/cm³と鉄の約1/3に過ぎません。この特性により、軽量化が重要な航空機、車両、運搬機器などで重宝されています。
- 耐食性 アルミニウムは自然に酸化膜を形成するため、耐食性に優れています。特に海洋環境や化学プラントで使用される際にこの特性が生かされます。
- 加工性 アルミ材は非常に加工しやすく、切断、溶接、圧延、成形などの加工が容易です。これにより、さまざまな形状や製品を効率的に作ることができます。
- 熱伝導性 アルミニウムは熱伝導性が高く、熱処理や冷却の効率が求められる用途にも適しています。
- 電気伝導性 アルミは電気伝導性にも優れており、電力ケーブルや電気機器の部品に多く使用されています。
A5052の加工性
A5052は、マグネシウムを主成分としたアルミ合金で、特に良好な耐食性と加工性を持っています。その加工性に関して以下の特徴があります。- 切削加工 A5052は切削性が良好で、ドリル加工やフライス加工などの機械加工が容易に行えます。ただし、硬さが他の合金と比べてやや低いため、高精度な加工には注意が必要です。
- 溶接性 A5052は溶接性が非常に良好で、TIG(タングステン・インターナル・ガス)溶接やMIG(メタル・インターナル・ガス)溶接に適しています。また、耐食性を損なうことなく溶接が可能です。
- 冷間圧延と成形 A5052は冷間圧延や深絞り加工などにも適しており、複雑な形状に成形することができます。特に、薄板での加工が得意です。
- 硬化性 A5052は他のアルミ合金と比べて硬化が比較的緩やかです。そのため、熱処理による強度向上はあまり効果的ではないですが、鋳造や圧延などの成形工程で強度を得ることができます。
A5083の加工性
A5083は、マグネシウムとマンガンを主成分とするアルミ合金で、海水や強酸性環境に強い耐食性を持ちます。A5052と比較して、以下の加工性が特徴です。- 切削加工 A5083はA5052よりも硬く、切削性はやや劣る場合があります。そのため、高速回転の切削工具や適切な冷却を行う必要があります。
- 溶接性 A5083は溶接性が非常に良好で、TIG溶接やMIG溶接に広く使用されています。特に海洋環境や化学プラントなどで使用される場合、溶接後でもその優れた耐食性が発揮されます。
- 冷間圧延と成形 A5083は深絞りや成形の難易度が高い場合がありますが、圧延加工は十分に行うことができます。特に大きな荷重がかかる構造物に適しています。
- 硬化性 A5083は冷間加工で強度が向上しますが、熱処理による強度向上効果はA5052に比べて顕著です。そのため、必要に応じて適切な熱処理を施して強度を得ることができます。
加工方法による材質の選定
アルミ材の選定は、加工方法と最終的な用途に大きく依存します。以下のポイントを参考に、適切な合金を選定することが重要です。- 強度と耐食性が求められる場合 船舶や海洋機器、化学プラントでの使用が考えられる場合、A5083などの耐食性の高いアルミ合金を選ぶことが重要です。これにより、過酷な環境下でも長期間使用できます。
- 加工性を重視する場合 薄板や精密な加工が求められる場合、A5052はその良好な加工性とバランスの取れた特性により、最適な選択となります。特に金型による成形や深絞りが必要な場合に適しています。
- 溶接性が求められる場合 両方の合金、A5052とA5083は溶接性が高いですが、耐食性を重視する場合はA5083が有利です。A5052は温暖な環境での使用に適しています。
まとめ
A5083とA5052のアルミ材質について徹底的に比較します。これらの材質は特性と用途において異なる点があります。例えば、A5083は耐食性に優れ、海水環境においても優れた性能を発揮します。一方、A5052は溶接性に優れており、機械部品や自動車部品など幅広い用途で利用されています。それぞれの特性を理解し、適切な用途に活用することが重要です。A6061 T6の表面処理とその効果についての解説
A6061 T6という素材は、多くの工業製品や構造物に幅広く使用されています。その表面処理は、製品の性能や耐久性を向上させる大切な工程です。本記事では、A6061 T6の表面処理とその効果について詳しく解説します。A6061 T6処理の種類や適用方法、処理後の特性など、これからA6061 T6を使用する方や処理方法に興味がある方にとって役立つ情報が満載です。さらに、どのような効果が期待できるのか、そのポイントも紹介しています。A6061 T6の表面処理に関する知識を深めたい方は、ぜひご一読ください。
Contents
A6061アルミ合金の基礎知識
A6061は、アルミニウム-マグネシウム-シリコン(Al-Mg-Si)系の合金であり、適度な強度と耐食性を持つ。特に、自動車部品や航空機の構造材料、建築用途など幅広い分野で使用されている。A6061とは?-アルミ合金の分類と基本
A6061は「6xxx系」の熱処理型アルミ合金に分類され、析出硬化(T6処理など)によって強度を向上させることができる。主な特長は以下の通り。- 優れた耐食性:海水や大気中でも耐食性が高い。
- 高い機械的強度:T6処理を施すことで310 MPa程度の引張強度を持つ。
- 加工性の良さ:切削加工、塑性加工、表面処理が容易。
- 溶接性:溶接可能だが、熱影響部で強度が低下する場合がある。
A6061の化学成分と物理的特性
A6061は主にアルミニウム(Al)を主体とし、マグネシウム(Mg)やシリコン(Si)を含むことで強度と耐食性を向上させている。- 比重:2.7 g/cm³
- 引張強度(T6処理時):約310 MPa
- 降伏強度:約270 MPa
- 伸び:約10%
- 熱伝導率:約170 W/m・K
- 熱膨張率:23.6 × 10⁻⁶ /K
A6061の加工性と溶接性について
加工性
A6061は加工性に優れるが、熱処理状態によって切削性や成形性が変化する。- 切削加工:T6処理後は硬度が増し、工具摩耗に注意が必要。
- 塑性加工:冷間加工や押し出し加工が可能だが、熱処理状態によって適切な条件を設定する必要がある。
- 表面処理:陽極酸化(アルマイト処理)によって耐食性や装飾性を向上可能。
溶接性
A6061はTIG溶接やMIG溶接に適しているが、熱影響部での強度低下が課題となる。- 適した溶接方法:TIG溶接、MIG溶接が一般的。
- 溶接後の強度低下:T6処理材の場合、溶接熱の影響で強度が低下するため、必要に応じて後処理が求められる。
- 推奨溶接棒:ER4045やER5356などが使用される。
A6061 T6処理の解説
A6061は熱処理によって強度を向上させることができるアルミ合金であり、特に「T6処理」は最も一般的な熱処理方法の一つである。T6処理を施すことで、高い機械的特性を持ちながらも加工性と耐食性を維持することが可能となる。T6処理とは-熱処理のプロセス概要
T6処理は、「溶体化熱処理」と「人工時効処理」の2つのステップで構成される。これにより、A6061の組織が均一化し、析出強化によって強度が向上する。- 溶体化熱処理(Solution Heat Treatment)
- 530~560℃の高温に加熱し、合金元素を固溶させる。
- 急冷(通常は水冷)を行い、合金元素を過飽和状態で固定する。
- 人工時効処理(Aging Treatment)
- 160~180℃で数時間保持し、析出物を形成させることで強度を向上させる。
- 時効処理の時間や温度により、機械的特性が変化する。
T6処理によるA6061の性質変化
T6処理を行うことで、A6061の機械的特性が大幅に向上する。主な変化は以下の通り。- 引張強度の向上:
- T6処理前(O状態):約124 MPa
- T6処理後:約310 MPa
- 降伏強度の向上:
- T6処理前:約55 MPa
- T6処理後:約275 MPa
- 硬度の向上:
- T6処理後はBrinell硬度(HB)で95~100程度となり、耐摩耗性が向上する。
- 加工性の変化:
- T6処理後は硬度が上昇し、切削加工時の工具摩耗が増えるため、適切な切削条件が必要。
- 溶接性の影響:
- T6処理後のA6061は溶接可能だが、熱影響部(HAZ)で強度低下が起こる。
- 必要に応じて溶接後に再熱処理を行うことで強度を回復できる。
A6061と他のアルミ合金との比較
A6061は、強度・耐食性・加工性のバランスに優れたアルミ合金であり、他のアルミ合金と比較して幅広い用途に適している。以下では、A6061と他の主要なアルミ合金との特性を比較し、それぞれの選択基準について解説する。A6061とA6063の特性比較
A6061とA6063は同じ6xxx系アルミ合金であるが、強度や加工性に違いがある。- A6061:
- 高い強度(T6処理後:約310 MPa)
- 優れた耐食性
- 良好な溶接性(ただし強度低下の可能性あり)
- 良好な押出成形性
- 用途:構造材、航空機、船舶部品など
- A6063:
- 中程度の強度(T6処理後:約250 MPa)
- 非常に優れた耐食性
- 非常に良好な溶接性
- 押出成形性が非常に良好
- 用途:建築材、フレーム、装飾品など
- 高い強度が必要な場合はA6061
- 耐食性と押出成形性を重視する場合はA6063
他の規格との比較-A2024、A7075など
A6061は汎用性が高いが、特定の用途ではA2024やA7075の方が適している場合がある。- A6061:
- 中程度の強度(T6処理後:約310 MPa)
- 優れた耐食性
- 良好な溶接性
- 良好な加工性
- 用途:一般構造材、船舶、航空機部品
- A2024:
- 高い強度(約430 MPa)
- 低い耐食性
- 溶接性が悪い
- 良好な加工性
- 用途:航空機構造材、車両部品
- A7075:
- 非常に高い強度(約560 MPa)
- 低い耐食性
- 溶接性が悪い
- 加工が難しい
- 用途:航空機、高負荷部品
- 強度を最優先する場合はA7075
- 軽量で高強度の部品が必要な場合(航空機など)はA2024
- 耐食性・溶接性・加工性のバランスを重視する場合はA6061
類似素材との違いと選択基準
A6061の代替となる素材としては、以下のようなものがある。- A5052(5xxx系アルミ合金):
- 耐食性に優れ、溶接性も高いが、A6061より強度が低い。
- 選択基準:耐食性や溶接性が最優先の場合。
- A6082(6xxx系アルミ合金):
- A6061と類似しているが、強度がやや高い。
- 選択基準:A6061より強度を求める場合。
- A3003(3xxx系アルミ合金):
- 耐食性と成形性に優れるが、強度は低い。
- 選択基準:成形加工が重視される場合。
A6061 T6の表面処理とその効果
A6061 T6は、優れた機械的特性と耐食性を備えたアルミニウム合金ですが、表面処理を施すことでさらにその性能を向上させることができます。ここでは、A6061 T6の表面処理の種類と、それぞれの目的や効果について解説します。表面処理の種類と目的
陽極酸化処理 (Anodizing)- 目的: A6061 T6の表面に酸化皮膜を形成し、耐食性を向上させる。
- 効果:
- 耐食性の向上
- 外観の改善(色を付けることができる)
- 表面硬度の増加
- 摩擦係数の低減
- 目的: 耐食性を高めるとともに、後の塗装の密着性を向上させる。
- 効果:
- 優れた耐食性を提供
- 塗装の前処理として使われる
- 軽量で均一なコーティング
- 目的: A6061 T6の表面に金属や金属酸化物の薄膜を蒸着し、耐摩耗性や耐食性を向上させる。
- 効果:
- 高い耐摩耗性
- 高温環境での耐性向上
- 外観の改善
- 目的: 粉末塗料を用いて均一な塗膜を形成し、耐食性や美観を改善する。
- 効果:
- 耐食性の向上
- 表面に高い耐摩耗性を付与
- 外観の改善(カラーバリエーションが豊富)
表面処理による耐食性と耐摩耗性の向上
- 耐食性: 表面処理を施すことで、A6061 T6は水分や化学物質による腐食から守られます。特に陽極酸化処理では、酸化アルミニウムの皮膜が腐食を防ぐバリアとして機能し、製品寿命を延ばします。また、アルマイト処理やPVDコーティングでも耐食性が大きく向上します。
- 耐摩耗性: 表面硬度を高めることで、摩擦や摩耗に対する耐性が向上します。PVDコーティングや陽極酸化処理により、A6061 T6の表面は摩擦に強くなり、機械的な摩耗や傷が付きにくくなります。また、焼き付け塗装にも耐摩耗性があるため、特に外部での使用が多い部品に有効です。
まとめ
A6061 T6のアルミニウム合金は非常に強度が高く、耐食性に優れています。そのため、特定の表面処理を行うことでさらなる性能向上が期待できます。注目すべきポイントは、表面処理による耐摩耗性や耐食性の向上、そして外観の美しさです。これにより、A6061 T6の使用範囲が拡大し、より長期的な利用が可能となります。工業用アルミA6063と切削性:加工のポイントを徹底解説
工業用アルミニウムA6063は、加工業界で広く使用されている素材の1つです。その特性や切削性能は、加工の品質や効率に大きな影響を与えます。本記事では、A6063の特性や切削性に焦点を当て、加工のポイントを徹底解説していきます。A6063の加工に携わる皆さんにとって、この記事が新たな知識や技術の獲得につながることを期待します。加工における成功を目指す方々にとって、お役立ちの情報となることでしょう。A6063を使った加工作業において、効果的な方法や注意すべきポイントを共に学んでいきましょう。
Contents
A6063とは?
A6063は、アルミニウム合金の一種で、主に押出成形に適した合金です。高い耐食性と優れた加工性を持ち、特に建築業界や自動車部品、ヒートシンクなどで広く使用されています。この合金は、Mg(マグネシウム)とSi(シリコン)を主な合金元素としており、その特性により、非常に優れた押出性を提供します。アルミ合金A6063の基本情報
A6063合金は、Al-Mg-Si系の6000系アルミニウム合金に分類されます。主要な合金元素であるマグネシウム(0.45~0.9%)とシリコン(0.2~0.6%)が特徴で、これらは合金の耐食性と加工性を高める要素です。主な用途としては、建築用のアルミサッシや手すり、車両部品、ヒートシンクなどがあり、その特性は高い耐食性と優れた陽極酸化性を含みます。A6063の押出材とその特徴
A6063合金は、特に押出成形に優れた特性を持ちます。複雑な断面形状を作るのに適しており、建築業界や製造業において非常に重宝されています。押出性が非常に高いため、細かい形状の製造が可能で、アルミサッシやパイプ、チャンネルなどがこれに該当します。また、押出後に陽極酸化処理を施すことで、外観の向上と耐久性の向上が期待できます。A6063と他のアルミ合金(A6061、A1070、A3003、A6005C)の比較
A6063は、他のアルミ合金と比較して、特に押出性と耐食性が優れていますが、その強度はA6061やA6005Cに比べてやや低めです。以下のように特徴が異なります。- A6061:この合金は、強度が高く、機械加工にも適していますが、押出性はA6063ほど高くありません。耐食性もA6063より劣りますが、より強い構造部品が求められる場合に使用されます。
- A1070:純アルミニウム系の合金であり、非常に高い耐食性を持ちますが、強度はA6063やA6061に比べて低く、主に電気や化学工業で使用されます。
- A3003:マンガン(Mn)が含まれ、耐食性が向上している合金です。A6063よりも若干低い強度ですが、優れた耐食性を提供します。屋根材や配管部品に適しています。
- A6005C:A6063よりも高い強度を持ち、押出成形性も良好です。耐食性も高く、構造材や産業機械部品に適しています。
アルミ合金A6063の性質
A6063は、特に押出成形に適したアルミ合金で、様々な特性を持っています。ここではその化学成分、機械的性質、熱処理による強度向上について詳述します。A6063の化学成分
A6063合金は主にマグネシウム(Mg)とシリコン(Si)を合金元素として含んでいます。これらの元素は合金の耐食性や強度、加工性に大きな影響を与えます。A6063の一般的な化学成分は以下の通りです:- アルミニウム(Al):残りの大部分
- マグネシウム(Mg):0.45~0.9%
- シリコン(Si):0.2~0.6%
- 銅(Cu):最大0.1%
- 鉄(Fe):最大0.35%
- マンガン(Mn):最大0.1%
- その他(Cr, Znなど):微量
A6063の機械的性質
A6063合金は、強度よりも加工性や耐食性を重視した合金であり、以下のような機械的性質を持っています:- 引張強度: 160~230 MPa(熱処理なし)
- 降伏強度: 110~150 MPa
- 伸び(引張り延性): 8~12%
- 硬度: 約50~70 HB(ビッカース硬さ)
- 密度: 約2.70 g/cm³
A6063の熱処理と強度
A6063合金は熱処理を施すことで、強度が大きく変化します。一般的には、A6063の主な熱処理プロセスとして「T5」「T6」があります。- T5処理:押出後に冷却し、後に人工時効を行う処理方法で、強度は向上しますが、T6よりは低めです。この処理により、良好な加工性が維持されます。
- 引張強度:190~220 MPa
- 降伏強度:130~160 MPa
- T6処理:高温で加熱し、その後急冷、さらに時効処理を行うことで、A6063の強度が最大化されます。この処理により、強度が大幅に向上し、機械的性質も強化されます。
- 引張強度:240~270 MPa
- 降伏強度:190~220 MPa
A6063の切削性
A6063は、押出成形に適したアルミ合金として広く使用されていますが、切削加工においても非常に優れた加工性を発揮します。ただし、切削加工においてはいくつかの利点と課題が存在します。以下に、A6063の切削加工における挙動、利点、課題、そして加工性を向上させる方法について詳述します。切削加工におけるA6063の挙動
A6063合金は、その化学成分と物理特性から、切削加工時に次のような挙動を示します:- 切削抵抗:A6063は比較的軟らかい材料であり、切削抵抗は低めですが、適切な切削条件を選定しないと、加工時にチップの引き攣れや切屑が溶着しやすくなることがあります。
- 熱伝導性:A6063の高い熱伝導性により、切削中に発生する熱を効率的に拡散させることができますが、過度の熱が発生すると工具の寿命が短くなる可能性があります。
- 表面仕上げ:適切な切削条件の下でA6063は滑らかな表面仕上げが得られますが、不適切な工具や切削条件では、表面に傷がつくことがあります。
A6063切削加工の利点と課題
A6063の切削加工には多くの利点がありますが、同時にいくつかの課題も存在します。利点:
- 良好な加工性:A6063は柔らかく、機械的性質も比較的低いため、切削加工が非常にしやすいです。特に旋盤やフライス盤などでの加工に適しています。
- 良好な表面仕上げ:適切な工具と切削条件を使用することで、非常に滑らかな表面が得られます。これにより、仕上げ作業が少なくて済みます。
- 切削速度が高い:低い切削抵抗と良好な熱伝導性により、高速切削が可能で、生産性が向上します。
課題:
- チップの溶着:A6063は柔らかいため、切削時にチップが工具に溶着しやすく、切削品質に影響を与えることがあります。
- 工具の摩耗:アルミ合金は軟らかいものの、粘着性があるため、工具の摩耗が早く進行する可能性があります。
- バリの発生:切削時にバリ(切りかけ部分の突起)が発生しやすいです。特に高速切削や粗加工時にこの問題が顕著になります。
A6063の加工性を向上させる方法
A6063の加工性をさらに向上させるためには、以下の方法が有効です:- 適切な工具の選択:A6063の切削には、強度が高く、耐摩耗性に優れた工具を選ぶことが重要です。チップの溶着を防ぐために、コーティングされた工具(例:TiNコーティング)を使用すると効果的です。
- 切削条件の最適化:切削速度や送り速度を適切に設定することで、チップの溶着や工具摩耗を減少させ、加工精度と表面品質を向上させます。特に、切削中の温度管理を意識することが大切です。
- 冷却液の使用:切削中の熱管理を行うために、冷却液を使用することが推奨されます。冷却液は工具の冷却や切削面の温度低下に寄与し、工具寿命を延ばし、切削品質を保つのに役立ちます。
- 適切なバリ処理:バリの発生を抑制するために、切削後の仕上げ工程でバリ取り作業を行うことが重要です。また、バリを最小限に抑えるために、微細な切削条件や精密な工具選定を行います。
A6063(ジュラルミン)の切削加工
A6063は、ジュラルミンとして知られるアルミニウム合金の一種で、特に押出成形材としてよく使用されます。この合金は、その軽量性と優れた加工性から、航空機や自動車産業など多くの分野で利用されています。A6063の切削加工においては、いくつかの重要なポイントがあります。ジュラルミンとしてのA6063の特性
A6063はアルミニウム合金の一種で、主にマグネシウムとシリコンを基にした合金です。ジュラルミンとしての特徴は以下の通りです:- 軽量で強度が高い:A6063は比較的低い密度を持ちながら、十分な強度を備えており、強化材が少ないため加工しやすいです。
- 良好な耐食性:A6063は、自然酸化皮膜を形成し、腐食に対して高い耐性を示します。この特性は加工後も維持されるため、厳しい環境下でも使用できます。
- 優れた加工性:A6063はその化学成分と物理特性により、切削加工に適しており、工具の摩耗が少ないため、加工性が良好です。
切削工具とA6063の相性
A6063の切削加工においては、切削工具の選定が重要です。A6063の特徴に適した工具を選ぶことで、切削品質を向上させ、加工効率を最大化することができます。- ツール材料:A6063のような軟らかいアルミ合金を切削する際は、耐摩耗性が高く、熱伝導性に優れた工具を選ぶことが推奨されます。例えば、炭化タングステン(WC)やコバルト合金を使用した工具が一般的です。
- ツールコーティング:A6063は比較的軟らかいため、切削時にチップの溶着や摩耗が発生することがあります。これを防ぐために、TiN(窒化チタン)やTiAlN(窒化チタン・アルミ)などのコーティングが施された工具を使用すると、摩耗を抑制できます。
- 切削形状:切削工具の形状としては、鋭角的な切れ刃を持つ工具が適しています。これにより、切削力を効率よく伝達でき、スムーズな切削が可能となります。
切削パラメータの最適化
A6063の切削加工では、切削パラメータを最適化することで、加工品質を向上させ、工具の寿命を延ばすことができます。以下のパラメータに注意を払いながら、最適化を行います:- 切削速度:A6063は比較的軟らかい材料であるため、切削速度は高めに設定することができます。適切な切削速度を選定することで、切削効率が向上し、熱の発生を抑えることができます。
- 送り速度:送り速度は切削面の仕上がりに影響を与えます。送り速度が速すぎると表面に傷がつく可能性があるため、適度な送り速度を設定します。
- 切削深さ:切削深さは一度に除去する材料量を示しますが、過剰に深く設定すると工具に過剰な負担がかかり、工具の摩耗が早まる可能性があります。適切な切削深さを設定し、効率的に加工します。
まとめ
アルミA6063合金は、その切削性の特性から工業用途に広く利用されています。この合金は切削加工時に非常に高い切りくず形成能力を持ち、加工中に熱が逃げやすい優れた熱伝導性を持っています。これにより、作業効率を向上させることができます。さらに、適切な刃物や切削条件を選択することで、高い精度で綺麗な仕上がりを実現することができます。 A6063合金を使用した工業製品の加工においては、適切な冷却液の使用や適正な刃物の選択が重要です。さらに、適切な切削速度と刃先の角度を選択することで、切削時の振動や加工精度の低下を防ぐことができます。これらのポイントを踏まえた上で、A6063合金の切削加工を行うことが重要です。高強度A7075アルミ合金の比重とは?その用途と特性を徹底解説
高強度A7075アルミ合金は、産業界で広く使用される素材の一つです。その軽量性と耐久性から、さまざまな用途に活用されています。この合金は、どのような特性を持ち、なぜその比重が注目されるのでしょうか。本記事では、A7075アルミ合金の比重に焦点を当て、その用途と特性を徹底解説します。どのようにして高い強度が実現されるのか、さらにその特性がどのような産業で活躍しているのか、詳細に掘り下げていきましょう。高強度A7075アルミ合金の世界に迫る興味深い情報をご紹介します。
Contents
A7075アルミ合金の基本情報
A7075アルミ合金は、非常に高い強度を誇るアルミニウム合金の一種で、特に航空機や軍事用途、その他高強度が要求される構造部品に多く使用されています。その特性や分類について以下のように説明します。A7075アルミ合金とは
A7075は、アルミニウムに亜鉛を主成分とし、他にマグネシウムや銅などを加えた合金です。強度が非常に高いため、耐久性が求められる部品に使用されることが多いです。一般的には航空機や自動車のフレーム、工具、ダイキャスト部品などに適しています。- 主な成分:
- アルミニウム (Al):主成分
- 亜鉛 (Zn):強度向上に貢献
- マグネシウム (Mg):耐腐食性や機械的特性向上
- 銅 (Cu):強度や硬度を高めるために加えられます
アルミ合金の分類とA7075の位置づけ
アルミニウム合金は、主に以下のように分類されます:- 1xxx系:純アルミニウム
- 2xxx系:銅を主成分とする合金
- 3xxx系:マンガンを主成分とする合金
- 4xxx系:シリコンを主成分とする合金
- 5xxx系:マグネシウムを主成分とする合金
- 6xxx系:シリコンとマグネシウムを主成分とする合金
- 7xxx系:亜鉛を主成分とする合金
- 7xxx系の特性:
- 高強度
- 良好な耐腐食性
- 良好な機械的特性
- 熱処理によりさらに強度が向上(T6など)
A7075アルミ合金の比重について
A7075アルミ合金の比重に関しては、合金の密度と軽量性を理解するために重要です。比重は、物質の密度を水の密度と比較した相対的な値であり、合金の適用範囲を決定する際に役立つ情報となります。比重とは
比重は、物質の密度を基準物質(通常は水)の密度で割った値です。単位がないため、物質間で比較が簡単にできます。比重が低いほど軽く、高いほど重いということを意味します。- 比重 = 物質の密度 / 水の密度(4°Cで約1 g/cm³)
A7075の比重とその意義
A7075アルミ合金の比重は約2.81 g/cm³です。この値は、A7075が比較的高い強度を持ちながら、軽量であることを示しています。比重が低いため、航空機や自動車など、軽量化が求められる分野で広く使用されます。- A7075比重:約2.81 g/cm³
比重と他のアルミ合金との比較
A7075の比重を他のアルミ合金と比較すると、その強度を保ちながらも軽量であることがわかります。- A6061(比重:2.70 g/cm³):A6061は一般的なアルミ合金で、強度はA7075ほど高くありませんが、比重はA7075より低く、加工しやすい特徴があります。
- A2024(比重:2.78 g/cm³):A2024は銅を多く含むアルミ合金で、高い強度を持っていますが、A7075と比較して比重が若干低いです。航空機や航空宇宙産業にも使用されます。
A7075アルミ合金の強度特性
A7075アルミ合金はその高い強度特性により、航空機や軍事用途、スポーツ用品などの高強度を求められる分野で広く利用されています。その強度の秘密と、強度に影響を与える要素について詳しく説明します。強度とは
強度は、材料が破壊や変形せずにどれだけの力を受けることができるかを示す性質です。強度にはいくつかの種類があり、以下のようなものがあります。- 引張強度:材料が引っ張られる力に耐える能力。
- 圧縮強度:圧縮される力に耐える能力。
- 曲げ強度:曲げられたときに材料が破壊されない力。
- 靭性:破壊される前にどれだけのエネルギーを吸収できるか。
A7075の高強度の秘密
A7075アルミ合金の高強度は、その成分と熱処理によって得られます。A7075は、主に亜鉛(Zn)を多く含むアルミ合金であり、この亜鉛の含有量が高いことが強度の向上に寄与しています。- 亜鉛(Zn):この元素が合金に含まれることによって、強度が向上します。A7075は約5-6%の亜鉛を含んでおり、これがアルミニウム合金の中でも強度を高める主な要因です。
- 熱処理(T6処理):A7075はT6処理を施すことで、さらに強度が向上します。T6処理は溶体化処理と時効処理から成り、これにより強度が最大化されます。
強度を左右する要素とA7075
A7075の強度は、その成分や処理方法だけでなく、加工方法にも影響されます。- 合金成分:A7075は亜鉛の含有量が多いため、強度が高い一方で、耐食性や延性は若干低下します。亜鉛の割合を調整することで、強度と他の特性とのバランスを取ることができます。
- 熱処理:T6処理を受けたA7075は、最高の強度を持ちますが、処理の時間と温度によって強度特性が変化するため、最適な条件を選定することが重要です。
- 加工方法:A7075は硬いため、加工が難しく、特に切削加工時には工具の摩耗が激しくなります。これにより、強度に影響を与える微細な欠陥や歪みが生じることがあります。
A7075アルミ合金の加工性
A7075アルミ合金はその高強度が特徴ですが、その加工性には特別な注意が必要です。以下に、A7075の加工方法や加工時の注意点、そして加工性と強度の関係について説明します。A7075の加工方法
A7075アルミ合金は強度が非常に高いため、加工が難しい場合があります。適切な加工方法を選定することで、良好な結果を得ることが可能です。- 切削加工:A7075は高硬度のため、切削時の工具摩耗が速く進みます。工具の選定や切削条件を最適化することが重要です。冷却液を使用し、切削速度を調整することで、加工効率と工具の寿命を延ばすことができます。
- フライス加工:フライス加工でも、A7075の高強度を考慮して適切な切削条件を設定する必要があります。切削中の振動や工具の負荷を最小限に抑えるために、加工速度や送り速度を慎重に選ぶことが大切です。
- 旋削加工:旋削加工では、工具の耐摩耗性が重要です。硬度が高いため、加工中の発熱を抑えるために適切な冷却を施し、加工速度を管理することが必要です。
加工時の注意点
A7075の加工時には以下の点に特に注意を払いましょう。- 工具の選定:高強度のA7075を加工する際には、耐摩耗性の高い工具(例えばコバルト合金工具など)を使用することが推奨されます。工具の摩耗を防ぐために、硬度の高い刃先を持つものを選ぶと良いです。
- 冷却の重要性:切削時の熱が工具やワークに悪影響を与えないよう、冷却液を使用して温度上昇を抑えます。冷却不足は工具の早期摩耗や加工面の品質低下につながるため、適切な冷却管理が必須です。
- 切削条件の調整:A7075は高強度なため、加工時に過剰な力を加えると部品に微小な亀裂が生じる可能性があります。適切な切削速度や送り速度、回転数を設定し、工具に過度の負荷をかけないようにしましょう。
加工性と強度の関係
A7075アルミ合金は、その強度が高いことにより加工性に影響を与えます。強度が高いと、加工時に工具にかかる負荷が大きくなり、摩耗が早く進行するため、加工においては特別な配慮が必要です。- 高強度と加工難易度:A7075は高強度のため、切削加工時に工具への圧力が強くなり、摩耗が早く進む傾向があります。そのため、工具選定や冷却、切削条件の適切な管理が求められます。
- 強度と加工精度のトレードオフ:強度が高いほど、加工中に発生する熱や応力の影響で部品に変形やひずみが生じる可能性があります。精度の高い加工を目指すためには、適切な加工条件を設定し、強度と加工精度のバランスを取ることが必要です。
7075アルミ合金の耐久性とメンテナンス
A7075アルミ合金は、その優れた機械的特性と高強度が求められる分野で使用されますが、耐久性やメンテナンスについても重要なポイントがあります。以下では、耐腐食性、疲労耐性、そしてメンテナンス方法について説明します。耐腐食性について
A7075は、アルミニウム合金の中でも高強度を誇りますが、耐腐食性には限界があります。特に、塩水や酸性環境、湿気の多い環境では腐食のリスクが高まります。以下のポイントに注意が必要です。- 表面処理:A7075の耐腐食性を高めるためには、陽極酸化処理やコーティングを施すことが一般的です。これにより、アルミニウムの表面に保護膜が形成され、腐食を防ぐことができます。
- 環境による影響:A7075は塩水や酸性環境に弱いため、これらの環境で使用する際には、腐食対策を十分に施す必要があります。耐食性が高い合金に比べて、注意深い取り扱いが求められます。
疲労耐性とは
疲労耐性は、繰り返し荷重に耐える能力を指します。A7075は高強度な合金ですが、疲労耐性にも限界があります。- 応力集中の影響:高強度なA7075は、急激な力や繰り返し負荷を受けると、応力集中が起こりやすく、ひび割れや破壊を引き起こすことがあります。これを防ぐためには、部品設計時に応力集中を避ける形状にすることが重要です。
- 疲労強度向上のための対策:A7075の疲労耐性を向上させるためには、適切な熱処理や表面処理が有効です。特に、表面の微細な欠陥を除去することや、表面を硬化させる処理(例:ショットピーニング)を施すことで、疲労耐性を向上させることができます。
A7075のメンテナンス方法
A7075アルミ合金を使用する際には、定期的なメンテナンスが必要です。特に高強度の合金であるため、摩耗や腐食、疲労に対する配慮が求められます。- 定期的な清掃:A7075の表面に汚れや腐食の前兆が見られる場合は、早期に清掃を行い、腐食を防ぐために適切な処理を施します。アルカリ性の洗浄剤を使用することが一般的ですが、強い化学薬品は避けるべきです。
- 腐食の予防:湿気や塩分にさらされる可能性がある場所で使用される場合は、定期的にコーティングや酸化処理を再施工することが推奨されます。また、破損が見られた場合は早期に修理を行い、腐食の進行を防ぐことが重要です。
- 疲労確認:定期的に部品に疲労の兆候がないか確認します。亀裂が見られる場合は、早急に交換や修理を行うことで、疲労破壊を未然に防ぐことができます。