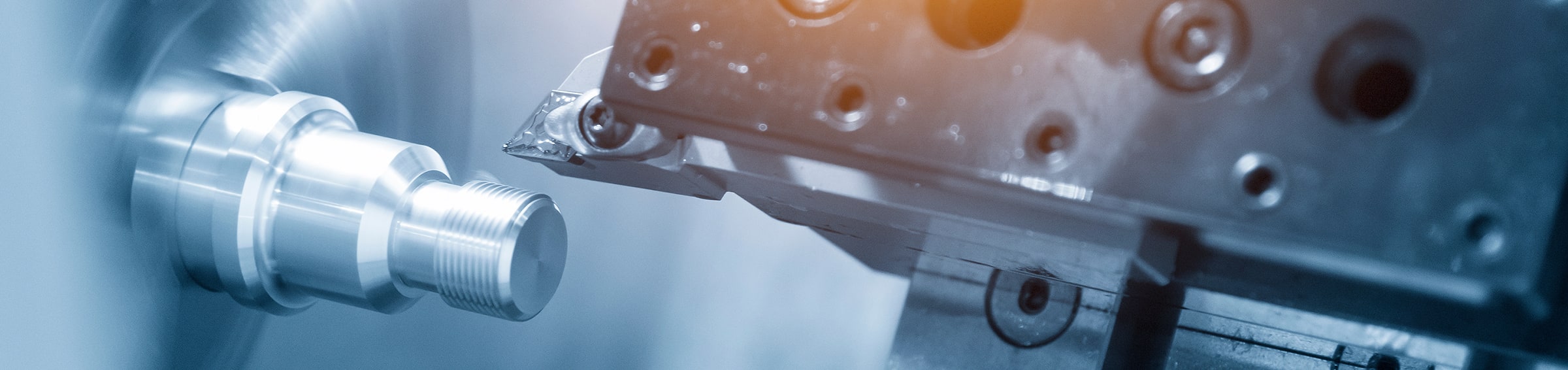
コラム column
アルミニウムA2017とは?その強度・比重・ヤング率・硬度について詳しく解説
A2017とは、アルミニウム合金の一種で、軽量でありながら非常に高い強度を持つことで知られています。日常生活ではあまり耳にしないかもしれませんが、航空機や自動車の部品、さらにはスポーツ用品に至るまで、さまざまな用途で利用されています。その魅力は、単に強度だけではなく、比重やヤング率、硬度といった物理的特性にも現れています。
「A2017を使ってみたいけれど、その特性について詳しく知りたい……」そんな疑問を抱える方も多いのではないでしょうか。そこで、本記事ではA2017の基本情報から、その強度、比重、ヤング率、硬度について詳しく解説します。これを読めば、A2017の特性を理解し、さらにその利活用の可能性を広げることができるでしょう。さあ、一緒にA2017の世界に足を踏み入れてみましょう。
1. A2017 とは 強度 比重 ヤング率 硬度の基本情報
A2017は、主に銅を合金元素として含むアルミニウム合金で、強度や耐久性が求められる用途に使用されます。航空宇宙産業や高強度部品に広く利用されています。
1-1. A2017の概要
A2017は、アルミニウム合金の中でも強度が高く、特に機械的特性が優れています。これにより、航空機部品や軍事機器、スポーツ機器など、強度を最優先にした用途に使用されることが多いです。
1-2. A2017の化学成分
A2017の主な化学成分は以下の通りです:
- アルミニウム (Al): 約93.5〜96.7%
- 銅 (Cu): 約3.8〜5.5%
- マンガン (Mn): 約0.3%
- シリコン (Si): 約0.5%
- マグネシウム (Mg): 約1.2〜1.8%
この合金は、銅の高含有により優れた強度を持ち、加えて耐食性を高める成分としてマンガンやシリコンが含まれています。
2. A2017 とは 強度 比重 ヤング率 硬度の機械的性質
A2017は、その高い強度と優れた加工性から、機械的性質が重要視される部品に使用されます。以下はA2017の各特性についての詳細です。
2-1. A2017の強度について
A2017は、非常に高い引張強度と耐疲労性を持ち、航空機の構造部品やエンジン部品に適しています。引張強度は約480〜520MPaに達し、圧縮強度や疲労強度も非常に高い特性を持っています。
2-2. A2017の比重とその影響
A2017の比重は約2.8で、他のアルミ合金と比較してやや重めですが、その強度を活かした使用が求められる場面で特に有用です。軽量化が重要視される用途には他のアルミ合金が選ばれることもありますが、強度を優先する場合はこの合金が最適です。
2-3. A2017のヤング率の特性
A2017のヤング率は約73GPaで、これは金属材料として高めの数値です。高いヤング率は、材料が変形しにくいことを意味し、高強度を維持しつつ、部品としての耐久性や形状の安定性が求められる用途に向いています。
2-4. A2017の硬度の測定方法
A2017の硬度は、主にロックウェル硬度(HRB)やブリネル硬度(HB)で測定されます。ロックウェル硬度は約80〜90HRB、ブリネル硬度は約150〜170HBが目安です。高強度と硬度を両立しているため、耐摩耗性が要求される環境において優れたパフォーマンスを発揮します。
3. A2017 とは 強度 比重 ヤング率 硬度と他のアルミ合金の違い
A2017は、他のアルミ合金と比較して特に強度に優れていますが、比重や耐食性などで他の合金と異なる特性があります。
3-1. A2017とA6061の比較
- 強度: A2017はA6061よりも高い強度を持ち、航空機などの高強度が必要な用途に適しています。
- 耐食性: A6061はA2017よりも耐食性に優れ、腐食環境に強いという特徴があります。
- 加工性: A6061はA2017に比べて加工がしやすいですが、A2017は熱処理によってその強度がさらに向上します。
3-2. A2017とA7075の違い
用途: A2017は、A7075に比べて価格が安価であるため、コストを抑えつつ高強度を確保したい場合に有効です。
強度: A7075はA2017よりもさらに高い強度を持ち、特に航空宇宙産業で広く使用されています。
耐食性: A7075はA2017に比べて若干劣る耐食性を持ちますが、強度重視の場面ではA7075が選ばれることが多いです。
4. A2017の用途や特徴
A2017は、特に高強度を求められる用途に適したアルミ合金で、航空宇宙産業や高性能な機械部品に広く使用されています。
4-1. A2017の主な用途
A2017は、以下のような分野でよく使用されています:
- 航空機の構造部品: 高い強度を要求されるため、航空機のフレームやエンジン部品に使用。
- 軍事用途: 軍用機器や装甲車両の一部に使用されることもあります。
- スポーツ用品: 高強度が求められる自転車フレームやゴルフクラブなど、軽量かつ強度が必要な部品。
- 自動車部品: 高強度を必要とする自動車のエンジン部品やシャーシにも使用されています。
4-2. A2017の特徴と利点
- 高強度: A2017は非常に高い引張強度を持ち、過酷な使用条件でも耐えられる能力があります。
- 耐疲労性: 繰り返し荷重がかかる環境でも良好な耐久性を発揮します。
- 良好な加工性: 熱処理によって強度をさらに高められるため、加工後でも高い機械的特性が維持されます。
- 適度な軽量性: 他の合金と比較して重量が軽く、機械部品の軽量化が求められる用途に適しています。
5. アルミ合金の選定基準
アルミ合金の選定においては、特に強度と硬度が重要な要素となります。使用する環境に応じて、適切な合金を選ぶことが必要です。
5-1. 強度と硬度の重要性
- 強度: 強度は、部品がどれだけの荷重に耐えられるかを示します。高強度が必要な用途では、A2017やA7075のような高強度合金が選ばれます。
- 硬度: 硬度は、材料がどれだけ外部の衝撃や摩擦に耐えられるかを示します。硬度が高い合金は、摩耗や変形に強い特性を持ちます。
5-2. 用途に応じた選定ポイント
- 高強度が求められる場合: A2017やA7075が適しています。特に航空機や軍事用途では強度が最優先されます。
- 耐食性が求められる場合: A6061やA5083など、耐食性の高い合金を選ぶことが適切です。
- 加工性が重視される場合: A6061やA1100のように加工しやすい合金を選ぶと良いでしょう。
6. A2017の強度や硬度について具体的な数値
A2017の具体的な機械的特性は、特に強度や硬度に関して明確な数値があります。これらの数値は、使用する環境によって異なる場合がありますが、一般的な目安となります。
6-1. A2017の引張強度の数値
A2017の引張強度は、約 480〜520 MPa で、非常に高い強度を持っています。これにより、高強度が要求される部品や構造物に使用されます。
6-2. A2017の硬度の具体的な数値
A2017のロックウェル硬度は約 80〜90 HRB で、ブリネル硬度は約 150〜170 HB です。この硬度範囲により、摩耗や疲労に強い特性を持ちます。
まとめ
A2017は、アルミニウム合金の一種で、高い強度と優れた加工性が特徴です。比重は約2.8 g/cm³、ヤング率は約70 GPaと、軽量ながらも剛性を持ちます。硬度はHB(ブリネル硬度)で約90~120程度で、耐摩耗性にも優れています。航空宇宙や自動車産業で広く利用されています。
アルミニウムA2024とは?強度・比重・ヤング率・硬度を徹底解説!
アルミニウムA2024とは、航空機や高性能な構造物に多く使用される、非常に優れた特性を持つ合金の一つです。しかし、「A2024って何?」「その強度や硬度はどれくらいなの?」といった疑問を抱えている方も多いのではないでしょうか。
本記事では、アルミニウムA2024について詳しく解説し、その特性や用途、さらには強度、比重、ヤング率、硬度についてもわかりやすくお伝えします。この情報を通じて、A2024がどのような素材であるかを理解し、実際の利用シーンについてもイメージを深めていただければ幸いです。
アルミニウムに関心がある方や、これから何かを作りたいと考えている方にとって、A2024は知っておくべき重要な素材です。それでは、さっそくこの魅力的な合金の世界に飛び込んでみましょう!
1. A2024 とは 強度 比重 ヤング率 硬度
A2024は、高強度のアルミニウム合金であり、特に航空機や高強度が求められる部品に使用されています。以下では、A2024の基本情報とその機械的特性について詳しく解説します。
1-1. A2024の基本情報
A2024は、アルミニウムと銅を主成分とする合金で、優れた強度と耐食性を持つことから、航空宇宙産業や高性能な構造部品に広く使用されています。これにより、A2024は特に軽量で高強度な材料が求められる場面に適しています。
1-2. A2024の強度と比重
- 強度: A2024は非常に高い引張強度を誇り、優れた機械的強度を持っています。この特性により、過酷な環境でも耐えうる強度が要求される航空機部品や構造物に使用されています。
- 比重: A2024の比重は約2.78 g/cm³です。この数値は、アルミニウム合金の中では標準的な比重ですが、その強度に対する軽さが特徴です。
1-3. A2024のヤング率と硬度
- ヤング率: A2024のヤング率は約73 GPaであり、これはその強度に見合った高い値で、構造的に安定した性能を提供します。
- 硬度: A2024は非常に硬い材料であり、硬度は約120~150HB(ブリネル硬度)程度です。この高い硬度により、摩耗や変形に強い特性を持っています。
2. A2024 とは 強度 比重 ヤング率 硬度と他のアルミ合金の違い
A2024は、他のアルミニウム合金と比較して、特に高い強度と良好な機械的特性を持っています。以下では、A2024と他の代表的なアルミ合金(A2017、A7075)との比較を行います。
2-1. A2017との比較
A2017は、A2024と似た特性を持つアルミニウム合金ですが、A2024の方がやや高い強度を持っています。A2017は銅含有量が少ないため、A2024よりも若干軽量ですが、耐食性にはA2024の方が優れています。
2-2. A7075との比較
A7075は、A2024よりもさらに高い強度を持つアルミニウム合金であり、航空機や軍事機器などで使用されることが多いです。しかし、A7075はA2024に比べて加工が難しく、また耐食性も若干劣ります。A2024はA7075よりも優れた溶接性を持ち、加工性が良好です。
2-3. 各合金の特性と用途
- A2024: 高強度で優れた耐食性が特徴。航空機部品や高強度を必要とする構造部品に使用。
- A2017: 軽量で加工が比較的容易。航空機の構造材や一般的な建築物に使用される。
- A7075: 最も高強度のアルミ合金。軍事機器や航空宇宙産業に多く使用される。
3. アルミのヤング率やその温度依存性
アルミニウム合金のヤング率は、合金の種類や使用温度に大きく影響されます。ヤング率の温度依存性について詳しく解説します。
3-1. ヤング率の定義と重要性
ヤング率(弾性率)は、材料が外力に対してどれだけ変形するかを示す物理的特性であり、構造物がどれだけ変形に耐えるかを判断する上で重要です。ヤング率が高いほど、材料は変形しにくく、より強固な構造を形成します。
3-2. 温度依存性の影響
アルミニウム合金は温度に敏感であり、温度が上がるとヤング率が低下します。高温環境下では、ヤング率が低下するため、構造物がより容易に変形し、強度や剛性が損なわれる可能性があります。
3-3. A2024のヤング率の特性
A2024のヤング率は温度によって変化しますが、常温での値は高く、特に機械的強度が必要な環境において非常に有用です。高温環境では、そのヤング率の低下に注意する必要がありますが、適切な使用温度範囲内では非常に安定した性能を発揮します。
4. A2024の耐食性や使用における利点
A2024は、高い強度と優れた耐食性を持つアルミニウム合金ですが、特に耐食性のメカニズムや使用時の利点について理解することが重要です。
4-1. 耐食性のメカニズム
A2024は、銅を主成分とするため、高強度でありながら耐食性にも優れています。銅の添加により、アルミニウムの自然酸化皮膜が強化され、腐食を防ぐ能力が向上します。ただし、他のアルミ合金と比較して、塩水や極端な腐食環境下ではやや劣ることがあります。そのため、適切な表面処理やコーティングを施すことで、さらに耐食性を向上させることができます。
4-2. A2024の利点と適用例
- 高強度: A2024は高い引張強度を持つため、軽量で強度が求められる航空機や宇宙産業の構造材に適しています。
- 良好な加工性: 熱処理により強度が向上し、さらに高強度を維持しながらも加工性が良好です。これにより複雑な形状の部品や精密な部品加工が可能です。
- 航空宇宙産業での使用: A2024は、航空機の構造部材やエンジン部品など、高い性能が要求される分野での使用に非常に適しています。
4-3. 使用上の注意点
- 腐食のリスク: 高い銅含有量のため、湿気や塩水環境では腐食が進みやすい。これに対して、適切な表面処理(例:アルマイト処理)を施すことが推奨されます。
- 高温下での使用制限: 高温下での使用時、ヤング率や強度が低下するため、高温環境下での使用には注意が必要です。
5. アルミ合金の選定基準や特性の比較
アルミニウム合金を選定する際には、強度、耐食性、加工性などの特性を総合的に考慮する必要があります。以下では、選定基準と他の合金との比較を行います。
5-1. 選定基準の概要
アルミ合金の選定基準には、以下の要素が含まれます:
- 強度: 使用する環境において必要な強度を確保できるか。
- 耐食性: 使用環境(湿度、塩水、酸性環境など)に対する耐食性。
- 加工性: 加工のしやすさや仕上がり品質。
- 重量: 特に航空機や自動車産業では、軽量化が求められます。
5-2. 特性比較表
合金 | 強度 | 比重 | ヤング率 | 硬度 | 耐食性 | 用途例 |
---|---|---|---|---|---|---|
A2024 | 高い | 2.78 | 73 GPa | 120-150 HB | 良好(塩水環境にはやや劣る) | 航空機、宇宙産業 |
A2017 | 中程度 | 2.77 | 70 GPa | 110-140 HB | 良好 | 航空機、車両 |
A7075 | 非常に高い | 2.81 | 71 GPa | 150-180 HB | やや劣る | 軍事、航空宇宙 |
A6061 | 中程度 | 2.70 | 69 GPa | 95-120 HB | 非常に良い | 構造材、一般建材 |
5-3. 適切な合金の選び方
合金の選定においては、使用する環境に応じた特性を重視することが重要です。例えば、強度が最重要視される航空機部品にはA2024やA7075が適していますが、腐食に強い材料が必要な場合はA6061がより適切です。さらに、加工の容易さやコストも選定基準の一部として考慮すべき要素です。
まとめ
アルミニウムA2024は、航空機などに使用される高強度のアルミニウム合金です。強度は高く、比重は約2.78、ヤング率は73GPa、硬度はHB 120-150程度です。優れた機械的特性と加工性を持ち、耐食性が課題ですが、熱処理により性能を向上させることが可能です。
アルミニウムA7075の特性とは?強度、比重、ヤング率、硬度を徹底解説
アルミニウム合金の中でも特に注目されるA7075。高い強度を持ちながらも軽量で、様々な分野で幅広く利用されていますが、その特性を詳しく理解している人は少ないのではないでしょうか。あなたも「A7075とは何か?その強度や比重、ヤング率、硬度について知りたい」と感じているかもしれません。
この記事では、A7075の基本的な特性を深掘りし、なぜこの合金が航空機やスポーツ用品、さらには自動車などに利用されるのかを明らかにします。強度や比重、ヤング率、硬度といった具体的な数値も紹介しながら、A7075が持つ優れた特性を理解できる内容に仕上げました。
このアルミニウム合金に興味がある方、または新たな素材選びを考えている方には、ぜひ読んでいただきたい情報が詰まっています。私たちと一緒に、A7075の魅力を探っていきましょう。
1. A7075とは強度比重ヤング率硬度の基本情報
A7075は、高強度のアルミニウム合金として広く使用されています。特に航空機の構造材料や自動車の高強度部品に多く使われています。このセクションでは、A7075の基本情報とその特性について詳しく解説します。
1-1. A7075の概要
A7075は、アルミニウムに亜鉛を主成分として含む合金で、高い強度と優れた機械的性質を持っています。これにより、航空機の構造部品や軍事用途に多く使用されることが特徴です。特に、軽量でありながら強度が求められるアプリケーションに適しています。
1-2. A7075の主な特性
- 強度: A7075は非常に高い引張強度を持ち、航空機やスポーツ用品などの高強度要求に対応します。
- 比重: 比重は約2.81 g/cm³で、アルミニウム合金としては中程度の重さです。
- ヤング率: 約71 GPaのヤング率を持ち、構造的な安定性が高いです。
- 硬度: 高い硬度を持ち、耐摩耗性が求められる部品にも適しています。
2. A7075とは強度比重ヤング率硬度と他のアルミ合金の違い
A7075は、他のアルミ合金と比較して非常に高い強度を誇りますが、その特性にはいくつかの違いもあります。ここでは、A7075と他のアルミ合金との特性を比較します。
2-1. A7075とA2017の比較
A7075とA2017は、どちらも高強度のアルミニウム合金ですが、いくつかの重要な違いがあります:
- A7075:
- 主に亜鉛を添加して高い強度を実現。
- 引張強度が非常に高い。
- 耐食性がやや低いため、特別なコーティングが必要。
- A2017:
- 主に銅を添加した合金。
- 強度はA7075に匹敵しますが、さらに良好な機械的性質を持つ一方で、耐食性が劣る。
- 特に航空宇宙産業に適していますが、一般的にはA7075がより広く利用されています。
2-2. 他のアルミ合金との特性比較
- A6061:
- A6061は中程度の強度を持ち、加工性と耐食性が非常に優れていますが、A7075ほどの強度はありません。軽量性や加工性を重視する用途に最適です。
- A5052:
- A5052は高い耐食性を持つが、A7075よりも強度は劣ります。主に海洋環境や湿度の高い環境で使用されます。
3. A7075の機械的性質:強度比重ヤング率硬度の詳細
A7075の機械的性質は、その使用において非常に重要な要素です。このセクションでは、A7075の強度、比重、ヤング率、硬度について、詳細に説明します。
3-1. A7075の強度について
A7075は、非常に高い引張強度を持つため、航空機やスポーツ用品、軍事用途など、高強度が求められる分野で重宝されます。引張強度は、A7075が200-570 MPaの範囲で、特に強度が求められる部品に最適です。
3-2. A7075の比重とその影響
A7075の比重は2.81 g/cm³であり、アルミニウム合金の中ではやや高い方に位置しますが、依然として軽量であるため、構造材料として非常に効率的です。この比重は、軽量化を目的とする航空機や自動車部品に適しています。
3-3. A7075のヤング率の重要性
A7075のヤング率は71 GPaで、これは構造的な安定性を確保するために重要な特性です。高いヤング率は、強度とともに物理的な安定性を提供し、特に応力のかかる環境での使用において重要です。
3-4. A7075の硬度とその測定方法
A7075は高い硬度を持ち、摩耗に強いため、耐久性が求められる部品に適しています。硬度はロックウェル硬度B(HRB)で約150-160とされています。硬度測定は通常、ロックウェル硬度試験やビッカース硬度試験を使用して行われます。
4. A7075の加工方法とポイント
A7075は高強度のアルミニウム合金であるため、加工時にはいくつかの注意点があります。適切な加工技術を使用することで、より良い結果を得ることができます。
4-1. A7075の加工技術
A7075の加工には、いくつかの技術が適しています。主な加工方法は以下の通りです:
- 切削加工: 高強度のA7075は、鋭い切削工具を使用して精密な加工が可能です。硬度が高いため、切削速度を調整し、冷却材を使用することが推奨されます。
- フライス加工: 高精度なフライス加工を行うことができ、特に航空機部品などの高精度が求められる部品に利用されます。
- 圧延加工: 圧延による加工が可能で、薄板やシート材の製造に使われます。圧延時の温度管理が重要です。
4-2. 加工時の注意点
A7075は高強度の合金であるため、加工時に注意すべきポイントがあります:
- 工具の摩耗: 高い硬度を持つため、工具が摩耗しやすいです。定期的な工具交換と、適切な切削速度が求められます。
- 温度管理: 加工中の熱膨張を避けるため、適切な冷却剤を使用し、温度を管理することが重要です。
- 機械の安定性: 高強度合金を加工するためには、強固で安定した機械が必要です。加工機の振動を抑えるために、重い加工機を選ぶことが推奨されます。
5. A7075の耐食性と腐食に関する知識
A7075は強度に優れる一方で、耐食性がやや劣るため、腐食に対する対策が重要です。
5-1. A7075の耐食性の特徴
A7075は、亜鉛を多く含むため、腐食には注意が必要です。特に以下の点が特徴として挙げられます:
- 局所腐食: 塩分や湿気が多い環境では、局所的に腐食が進行する可能性があります。
- 耐食性の改善: 表面処理(アルマイト処理など)を行うことで、耐食性を向上させることができます。これにより、特に航空機や海洋環境での使用において耐久性が向上します。
5-2. 腐食対策とメンテナンス
A7075の腐食対策には以下の方法が効果的です:
定期的なメンテナンス: 腐食を防ぐために、定期的な点検と洗浄が推奨されます。特に湿気や塩分が多い環境下では、腐食防止のための処置が必須です。
表面処理: アルマイト処理やその他のコーティングを施すことで、耐食性が大幅に向上します。
まとめ
A7075は、高強度アルミニウム合金で、航空機やスポーツ用品に広く使用されます。強度は非常に高く、比重は約2.81g/cm³、ヤング率は約71GPa、硬度はHRC 15-20と優れた特性を持っています。これにより、軽量でありながら耐久性に富む材料として評価されています。
アルミニウムA3003アルミニウム合金の特性とは?強度・比重・ヤング率・硬度を詳しく解説
あなたは「アルミニウムA3003合金の特性について詳しく知りたい」と思っているかもしれません。この合金は、様々な産業で利用される非常に重要な素材です。しかし、具体的にその特性や利点について理解している人は少ないのではないでしょうか?
このガイドでは、A3003合金の強度、比重、ヤング率、硬度といった基本的な物理特性を詳しく解説します。これらの特性がどのように実際の用途に影響を与えるのかを理解することで、A3003合金がなぜ選ばれるのか、その理由をより深く知ることができるでしょう。
また、さまざまな用途に応じた他のアルミニウム合金との違いについても触れ、A3003の魅力を余すところなくお伝えします。あなたのプロジェクトや研究に役立つ情報が満載のこのガイドを通じて、A3003アルミニウム合金の深い理解を得る手助けをいたします。
1. A3003 とは 強度 比重 ヤング率 硬度の概要
A3003は、アルミニウム合金の中でも特に汎用性が高く、軽量でありながら良好な成形性と耐食性を持つことで知られています。このセクションでは、A3003の基本的な情報とその機械的性質について解説します。
1-1. A3003の基本情報
A3003は、主にアルミニウムを基にした合金で、マンガン(Mn)を添加することにより、強度と耐食性が向上しています。アルミニウム合金の中でも広く使用されるタイプで、以下の特徴があります:
- 主成分: アルミニウム(Al)が約98%以上を占めており、残りの部分はマンガン(Mn)などの元素で構成されています。
- 強度: A3003は軽量でありながら中程度の強度を有し、一般的な用途に広く利用されます。
- 耐食性: 高い耐食性を持ち、海水や湿気が多い環境でも耐久性を発揮します。
- 加工性: 加工性が良好で、様々な形状に加工することができます。
1-2. A3003の機械的性質
A3003の機械的特性には以下の特徴があります:
- 引張強度: 約120 MPa程度で、一般的なアルミ合金に比べると低めですが、日常的な用途には十分です。
- 降伏強度: 約90 MPa程度で、A3003は中程度の強度を持つ合金です。
- ヤング率: 約70 GPaで、アルミニウム合金としては標準的な値です。これにより、A3003は比較的柔軟性があります。
- 硬度: A3003の硬度は一般的に70-80 HB(ブリネル硬度)程度であり、硬度が低いため加工が容易です。
2. A3003 とは 強度 比重 ヤング率 硬度の比較
A3003は、その特性において他のアルミ合金と比較してどのような位置にあるのかを見ていきます。
2-1. A3003と他のアルミ合金の強度比較
A3003は、中程度の強度を持ち、強度が高い合金には及びませんが、一般的な用途においては十分な性能を発揮します。以下は、代表的なアルミ合金との強度比較です:
- A3003: 引張強度120 MPa、降伏強度90 MPa
- A6061: 引張強度240 MPa、降伏強度160 MPa(A3003の倍以上の強度)
- A7075: 引張強度540 MPa、降伏強度470 MPa(さらに高い強度)
A3003は、これらの高強度合金に比べて強度が低いですが、軽量で加工が容易なため、耐食性が重要視される用途に適しています。
2-2. A3003の比重とその影響
A3003の比重は約2.73 g/cm³で、アルミニウム合金の中では標準的な値です。比重が軽いため、A3003は軽量構造部材としてよく使用されます。この軽さは、輸送や構造体への負荷を軽減するため、特に自動車や航空機の部品に適しています。
3. A3003 とは 強度 比重 ヤング率 硬度の化学成分
A3003は、その特性に影響を与える特定の化学成分を含んでいます。このセクションでは、A3003の化学成分と、主要な合金元素がどのような役割を果たしているかについて説明します。
3-1. A3003の化学成分の詳細
A3003の化学成分は、主に以下のような元素で構成されています:
- アルミニウム (Al): 約98%を占める主成分で、合金の基本となります。
- マンガン (Mn): 約1.0% – 1.5%が含まれ、合金の耐食性を向上させ、強度にも寄与します。
- 鉄 (Fe): 0.7% 以下で、微量の鉄が含まれています。
- その他の元素: 微量のシリコン(Si)、銅(Cu)などが含まれることもありますが、A3003では主にマンガンが特徴的な合金です。
これらの成分がA3003に優れた耐食性と加工性を与え、特に腐食環境下での使用に適しています。
3-2. A3003の合金元素の役割
鉄 (Fe): 微量の鉄が含まれていますが、鉄は主に合金の製造過程で不可避に存在します。鉄の含有量は少ないため、合金の性質には大きな影響を与えませんが、強度や耐食性を向上させることはありません。
マンガン (Mn): マンガンは、A3003の耐食性を大きく高める重要な成分です。また、マンガンがアルミニウムと結びつくことにより、強度も若干向上します。さらに、マンガンはアルミニウム合金において結晶粒を細かくし、均一性を保つ役割も果たします。
4. A3003 とは 強度 比重 ヤング率 硬度の用途
A3003は、その機械的性質と化学成分に基づき、多くの実際の用途に適しています。このセクションでは、A3003の一般的な用途と、特定の使用例を詳しく見ていきます。
4-1. A3003の一般的な用途
A3003は、主に軽量かつ耐食性が求められる分野で使用されます。代表的な用途には以下があります:
- 建築材料: A3003は耐食性が高いため、建物の外装材や屋根材に使われます。特に湿気の多い環境での使用に適しています。
- 自動車部品: 車両の軽量化を目的とした部品(内装、外装パネル、モールディングなど)に使用されます。
- 電子機器の部品: 熱を発散しやすい特性があるため、放熱板などに利用されることが多いです。
- 船舶や海洋機器: 高い耐食性を持つため、海水に接触する機器や部品にも適しています。
4-2. A3003の特定の使用例
A3003の特定の使用例としては、以下のものがあります:
- 冷却器のフィン: A3003は熱伝導性が良好なため、冷却システムのフィンや放熱板として使用されます。
- 食品加工業の機器: 耐食性が高いため、腐食環境にさらされることの多い食品加工機器の一部に使用されます。
- 航空機の内装材: 軽量で加工性が良いため、航空機の内装部品やキャビンの装飾部材として利用されます。
5. A3003 とは 強度 比重 ヤング率 硬度のまとめ
A3003は、その機械的性質と化学成分によって、さまざまな用途において適切な選択となることが分かりました。このセクションでは、A3003の特性を総括し、選定基準について整理します。
5-1. A3003の特性の総括
A3003は、以下の特徴を持つアルミニウム合金です:
- 強度: 中程度の強度を持ち、一般的な用途には十分な性能を発揮しますが、非常に高い強度が必要な場合には他の合金(例: A6061, A7075)に比べて劣ります。
- 比重: 約2.73 g/cm³で、軽量な合金として構造体に適しています。
- ヤング率: 約70 GPaと比較的柔軟性があり、加工が容易です。
- 硬度: 約70-80 HBと低めで、加工性に優れています。
- 耐食性: 高い耐食性を持ち、腐食環境に強いです。
これらの特性から、A3003は主に耐食性や軽量性が重要な用途に適しており、強度があまり求められない場合に理想的な選択です。
5-2. A3003の選定基準
A3003を選定する際の基準は以下の通りです:
- 耐食性が重要な用途: 海水や湿気の多い環境で使用する場合に適しています。
- 軽量化が求められる場合: 他の合金に比べて軽量であるため、航空機や自動車などでの軽量化に適しています。
- 加工性重視の場面: A3003は加工が容易なため、成形や加工が重要な場合に選ばれます。
A3003は、そのバランスの取れた特性により、様々な業界で広く採用されています。強度や耐久性が最優先される場合には他の合金を検討する必要がありますが、耐食性や加工性が重要な場合には最適な選択となります。
まとめ
アルミニウムA3003は、良好な加工性と耐食性を持つアルミニウム合金です。強度は中程度で、比重は約2.73 g/cm³、ヤング率は約70 GPa、硬度は約60 HBです。これにより、食品加工や化学工業など、さまざまな用途に適しています。軽量で扱いやすく、成形性にも優れています。
アルミニウムA5052合金の特性ガイド:強度・比重・ヤング率・硬度を徹底分析
「A5052ってどんな合金なんだろう?」と疑問に思ったことはありませんか?また、「どのように使われているのか」、「その強度や比重、ヤング率、硬度はどうなのか」といった詳細を知りたい方も多いでしょう。そんなあなたのために、アルミニウムA5052合金の特性について、わかりやすく解説するガイドを用意しました。
この記事では、A5052が持つ特性を詳しく分析し、実際の使用例やメリット・デメリットについても触れます。アルミニウム合金の中でも高い耐食性と加工性を誇るA5052合金は、自動車や船舶、建築などさまざまな分野で重宝されています。その特性を知ることで、より効果的に活用するためのヒントを得ることができるでしょう。
このガイドを通じて、A5052合金の強度、比重、ヤング率、硬度についての理解を深め、実際のプロジェクトに役立てていただければ幸いです。さあ、一緒にA5052合金の世界を探求してみましょう。
1. A5052 とは 強度 比重 ヤング率 硬度の基本情報
A5052は、主にマグネシウムを含むアルミニウム合金で、耐食性や加工性に優れた特性を持つ材料です。特に海洋環境や化学プラントなどで使用されることが多いです。このセクションでは、A5052の基本的な特性を紹介します。
1-1. A5052アルミ合金の概要
A5052は、アルミニウムに約2.5~4.0%のマグネシウムを含有した合金です。この合金は、高い耐食性と中程度の強度を持つため、特に海水や化学的な環境において優れたパフォーマンスを発揮します。溶接性や加工性にも優れ、さまざまな形状への加工が可能です。
- 主な特徴:
- 耐食性に優れる
- 良好な加工性
- 中程度の強度
- 良好な溶接性
1-2. A5052の主な特性
A5052の特性は以下の通りです:
- 強度: 中程度の強度を持ちますが、A7075などの合金に比べるとやや低めです。
- 比重: 約2.68と、アルミニウム合金の中では比較的軽量です。
- ヤング率: 約70 GPaで、加工性と強度のバランスが取れています。
- 硬度: モース硬度で約60を示し、比較的高い硬度を持っています。
2. A5052 とは 強度 比重 ヤング率 硬度と他のアルミ合金の比較
A5052は、他のアルミ合金と比較して、特に耐食性や溶接性に優れた特性がありますが、その強度は他の合金に比べると中程度です。次に、A5052と他の代表的なアルミ合金との特性を比較してみましょう。
2-1. A5052とA6061の違い
A5052とA6061は、用途や特性が異なります。A5052は、耐食性に優れており、海洋環境や化学プラントなどで使用されることが多いですが、A6061はより高い強度と溶接性を持ち、汎用性の高い合金です。
- A5052:
- 高い耐食性(特に塩水環境に強い)
- 良好な加工性
- 強度は中程度
- A6061:
- 強度が高い
- 優れた溶接性
- 汎用性が高い(航空機や自動車の部品に使用)
2-2. A5052とA7075の違い
A7075は、航空機や軍事産業などで使用される高強度アルミ合金です。A5052と比較すると、強度が大きく異なりますが、A5052は耐食性が高いため、耐腐食性が重要な用途に向いています。
- A5052:
- 耐食性に優れる
- 強度は中程度
- 良好な加工性と溶接性
- A7075:
- 非常に高い強度
- 耐食性はA5052に劣る
- 主に航空宇宙産業向け
3. A5052の機械的性質
A5052の機械的性質には、強度、比重、ヤング率、硬度が含まれます。これらの性質は、その適切な使用方法を選ぶ上で重要な要素となります。
3-1. A5052の強度について
A5052は、一般的に中程度の強度を持ちます。具体的には、引張強度は約215 MPaであり、比較的柔軟で加工しやすい材料です。高い強度が求められる用途には向かないため、耐食性や加工性が重要視される場面で最適です。
- 引張強度: 約215 MPa
- 降伏強度: 約95 MPa
3-2. A5052の比重の特性
A5052の比重は約2.68です。この比重は、他のアルミ合金と比較して標準的であり、軽量であるため、軽量化が求められる部品や構造物に適しています。
- 比重: 約2.68(アルミニウム合金の中では標準的)
3-3. A5052のヤング率の理解
A5052のヤング率は約70 GPaであり、これは金属材料の弾性を示す指標です。この値は、強度と加工性のバランスが取れていることを意味しており、特に機械加工や溶接の際に重要な要素となります。
- ヤング率: 約70 GPa
3-4. A5052の硬度の測定
A5052の硬度はモース硬度で約60、ブリネル硬度で約60 HBを示します。これは、他のアルミ合金よりも高めの硬度を持ち、耐摩耗性が求められる用途にも適しています。
ブリネル硬度: 約60 HB
モース硬度: 約60
4. A5052の加工時のポイント
A5052は優れた加工性を持つアルミ合金ですが、加工時に特定の注意点を押さえておくことが重要です。このセクションでは、A5052の加工方法の選択肢と注意点を紹介します。
4-1. 加工方法の選択
A5052の加工は、一般的に以下の方法が使用されます:
- 切削加工: A5052は比較的加工がしやすいため、旋盤やフライス盤を使用した切削加工が広く行われます。特に薄板や中厚板に対して優れた加工性を発揮します。
- 溶接: A5052は溶接性が高いため、TIG溶接やMIG溶接が適しています。特にアルゴンガスを用いたTIG溶接は高品質な接合が可能です。
- 圧延加工: 冷間圧延や熱間圧延による加工も適用可能で、厚板や薄板の成形に向いています。
- 曲げ加工: A5052は優れた曲げ加工性を持ち、特に角度のつけやすい形状に加工することができます。
4-2. 加工時の注意点
A5052の加工時には、以下の注意点を考慮することが必要です:
- 熱処理の影響: A5052は熱処理によって強度が若干変化するため、加工後の仕上げで熱処理を行う場合は、強度変化を予測しておく必要があります。
- 応力集中の防止: 加工中に高温が発生することがあります。過度な熱を加えすぎると、材料の性質に悪影響を与える可能性があるため、適切な温度管理が求められます。
- 適切な切削条件の選定: 高速切削を行う場合、工具の摩耗が速くなることがあるため、適切な切削条件を選定することが重要です。これにより、加工精度が保たれ、加工面が美しく仕上がります。
5. A5052の材料選定における適性
A5052はその耐食性や加工性から、特定の用途に非常に適しています。このセクションでは、A5052が適している用途と選定基準について解説します。
5-1. A5052が適している用途
A5052は、特に以下の用途に適しています:
- 海洋環境での使用: 高い耐食性を誇るため、船舶や海洋構造物の部品に最適です。
- 化学プラント: 化学薬品に耐性があり、腐食環境でも優れた性能を発揮します。
- 自動車部品: 軽量であり、加工性が良いため、自動車のボディや車両部品に使用されます。
- 航空機部品: 良好な強度と耐食性を持ち、軽量化が求められる航空機部品にも使用されます。
- 電気機器のケース: 高い耐食性と加工性を生かし、電子機器のケースや部品にも適しています。
5-2. A5052の選定基準
A5052を選定する際には、以下の基準を考慮することが重要です:
コスト: 高価ではないため、コストを抑えつつ高い耐食性を持つ材料を求める場合に最適です。
耐食性: 使用環境が湿気や化学薬品に曝される場所である場合、A5052は最適な選択肢となります。
強度要件: A5052は中程度の強度を持つため、高強度が必要ない用途に向いています。強度が求められる場合は、A7075やA6061を検討することが推奨されます。
加工性: 加工が容易であるため、複雑な形状を持つ部品や溶接が必要な部品に最適です。
まとめ
アルミニウムA5052合金は、優れた強度と耐食性を持ち、軽量な特性が特徴です。比重は約2.68、ヤング率は約70 GPa、硬度はHB 60-80と、加工性にも優れています。これにより、自動車や船舶など多様な用途で利用されています。
アルミニウムA5056とは?その強度・比重・ヤング率・硬度を徹底解説
あなたは「A5056とは何か、具体的な強度や比重、ヤング率、硬度について知りたい」と思ったことはありませんか?そのような疑問を持つ方に向けて、私たちはこの「A5056徹底解説ガイド」を作成しました。
この記事では、A5056の基本的な特性や、実際の応用における利点を詳しく解説します。特に、A5056がどのように他の材料と比較され、どのような強度や硬度を持っているのかについて詳しく知りたい方には、非常に役立つ情報が満載です。
もし、あなたが金属材料に興味を持ち、それを活用したいと考えているのであれば、A5056はその候補の一つです。この記事では、A5056の特性を詳しく掘り下げ、その魅力を余すところなくお伝えします。さあ、A5056の世界に一緒に飛び込んでみましょう!
1. A5056 とは 強度 比重 ヤング率 硬度の概要
A5056は、主にマグネシウムを含んだアルミニウム合金で、特に優れた耐食性と強度を持つことで知られています。特に海洋環境や塩水に対する耐性が求められる用途に適しています。以下では、A5056の基本情報とその化学成分について詳しく解説します。
1-1. A5056の基本情報
A5056は、アルミニウム・マグネシウム合金の一種で、特にその優れた耐食性と機械的特性から、海洋産業や化学産業で多く使用されています。鋳造性が良く、溶接性にも優れ、さまざまな製造プロセスに適しています。
- 主成分:アルミニウム(Al)、マグネシウム(Mg)、少量のマンガン(Mn)やシリコン(Si)
- 特長:耐食性が高く、特に海水環境に強い
- 利用用途:船舶、海洋設備、航空機、化学プラントの部品など
1-2. A5056の化学成分
A5056は、以下の主成分を含む合金であり、その成分比率が特性に大きな影響を与えます。
- アルミニウム(Al):残余成分
- マグネシウム(Mg):4.5~5.5%
- マンガン(Mn):0.2~0.8%
- シリコン(Si):0.4% 以下
- 銅(Cu):0.1% 以下
- 鉄(Fe):0.5% 以下
- その他:微量のクロム(Cr)や亜鉛(Zn)など
これらの成分が、A5056の耐食性、強度、加工性に影響を与えています。
2. A5056 とは 強度 比重 ヤング率 硬度の機械的性質
A5056は、機械的特性においても特に優れた性能を発揮します。以下では、A5056の強度、比重、ヤング率、硬度に関して具体的に見ていきます。
2-1. A5056の強度について
A5056は、比較的高い強度を持つ合金で、耐食性とともに機械的特性が重要視されます。通常の使用では非常に安定した強度を発揮し、特に高温環境や化学的に過酷な条件での使用に適しています。
- 引張強度:200~250 MPa(MPa単位で記載される)
- 降伏強度:130~150 MPa
- 特徴:溶接性が良好で、加工性に優れているため、製造現場での取り扱いが容易です。
2-2. A5056の比重とその影響
A5056の比重は、他のアルミニウム合金と比べてわずかに高いですが、その強度や耐食性の良さを考慮すれば十分にバランスの取れた特性を持っています。
- 比重:2.64~2.70
- 影響:比重が低いため、軽量化を求められる部品に適しており、航空機や船舶などで使用されることが多いです。
2-3. A5056のヤング率の重要性
ヤング率は、材料が力を受けた際にどれほど変形するかを示す指標です。A5056は、比較的高いヤング率を有し、強度とともに耐荷重性も優れています。
- ヤング率:70~80 GPa
- 重要性:強度だけでなく、材料の変形特性も重要な要素となる構造部材や機械部品に使用されます。
2-4. A5056の硬度とその測定方法
A5056の硬度は、使用する環境や求められる耐摩耗性によって重要な要素となります。硬度を測定する方法には、ビッカース硬度(HV)やロックウェル硬度(HR)などがあり、実際の使用環境に適した方法で測定されます。
- ビッカース硬度:80~100 HV
- ロックウェル硬度:Bスケールで60~70 HRB
- 測定方法:通常、ビッカース硬度が一般的に使用されますが、用途によって異なる測定法が選ばれることがあります。
A5056は、硬度が適度であり、摩耗に対する耐性が求められる部品に適しています。
3. A5056 とは 強度 比重 ヤング率 硬度と他のアルミ合金の比較
A5056は、他のアルミニウム合金と比較して特に耐食性に優れており、特に海洋環境や塩水環境に強い特性を持っています。他の合金と比較することで、その特性の違いや適切な使用用途をより明確に理解できます。
3-1. A5056とA6061の違い
A5056とA6061は、共にアルミニウム合金ですが、それぞれ異なる特性を持っています。A5056は特にマグネシウム含有量が高く、海水環境に強い耐食性を持つため、海洋産業に向いています。一方、A6061は一般的な用途で広く使われ、強度や加工性に優れており、特に構造部材に適しています。
- A5056:
- 主に海水環境向け
- 優れた耐食性
- 中程度の強度と良好な加工性
- A6061:
- 構造部材や汎用的な使用向け
- 高い強度と良好な溶接性
- 比較的高い加工性と耐久性
このように、A5056は特に腐食環境に強みを持ち、A6061は強度や耐久性が求められる場所に適しています。
3-2. A5056とA7075の特性比較
A7075は、航空宇宙産業などでよく使用される高強度アルミ合金であり、A5056とは異なる特性を持っています。A5056は比較的強度が低いですが、耐食性と溶接性に優れており、A7075は高い引張強度を誇りますが、耐食性や溶接性に関してはA5056ほど優れていません。
- A5056:
- 強度:中程度(200~250 MPa)
- 耐食性:非常に高い(海水環境向け)
- 加工性:良好
- A7075:
- 強度:非常に高い(500 MPa以上)
- 耐食性:A5056に比べて低い
- 加工性:やや難しい
A5056は耐食性が最も重要な用途に適し、A7075は高強度が要求される部品に適しています。
4. A5056 とは 強度 比重 ヤング率 硬度の影響と使用方法
A5056の強度や比重、ヤング率、硬度は、その使用方法に大きな影響を与えます。適切な使用方法を選ぶことが、材料の性能を最大限に活かすことに繋がります。
4-1. A5056の適切な使用方法
A5056は、主に高い耐食性を活かした使用方法に適しています。海水環境や化学プラント、航空機部品、船舶の部品など、耐腐食性が求められる場所での使用が推奨されます。特に、溶接が可能なため、複雑な形状の部品にも適応できます。
- 使用例:
- 船舶の外装部品
- 化学プラントの耐腐食部品
- 航空機の構造部材
4-2. A5056の加工ポイント
A5056は、良好な加工性を持ち、溶接が可能なため、加工時の注意点もあります。特に溶接時には、適切な溶接方法と前処理が必要です。また、加工中に硬化が進むことがあり、その場合には熱処理を行うことで強度を増すことができます。
- 加工ポイント:
- 溶接性が高いが、適切な溶接方法が必要
- 熱処理を行うことで強度を向上させる
- 一部の酸化物除去処理が必要
4-3. A5056の強度や硬度が影響する場面
A5056は、強度と硬度のバランスが取れているため、使用環境において耐久性が求められる場面で重要です。特に海洋産業などでは、耐食性が強調されますが、強度や硬度も機械的な負荷に対する耐性に関わるため、適切な選択が必要です。
- 強度や硬度が影響する場面:
- 船舶や海洋設備の構造部材
- 化学プラントでの部品
- 高い耐摩耗性が求められる場面
A5056は、強度や硬度の面でも優れた特性を示すため、長期間の使用が必要な部品に最適です。
まとめ
A5056は、アルミニウム合金の一種で、主にマグネシウムを含みます。優れた耐食性と加工性を持ち、強度は中程度で、比重は約2.66 g/cm³です。ヤング率は約70 GPa、硬度はHB 80-100程度です。これにより、航空機や自動車部品など、軽量かつ強度が求められる用途に広く利用されています。
アルミニウムA6061とは?強度・比重・ヤング率・硬度を徹底解説
アルミニウムA6061とは、軽量でありながら高い強度を誇るアルミニウム合金の一つです。工業用途や日常の製品に幅広く利用されているこの素材について、具体的にどのような特性があるのか、詳細に解説していきます。
「A6061って何だろう?」「どれくらい強いのか知りたい」「比重やヤング率、硬度について教えてほしい」といった疑問を持っている方も多いのではないでしょうか。このガイドでは、A6061の基本情報から、その特性や用途まで、わかりやすく紹介します。
特に、A6061の強度や比重、ヤング率、硬度といった物理的特性は、最適な素材選びに欠かせません。この知識を身につけることで、あなたのプロジェクトに最適な素材を見つける手助けとなるでしょう。それでは、A6061の魅力的な世界に一緒に踏み込んでみましょう。
1. A6061とは 強度 比重 ヤング率 硬度の基本情報
A6061は、アルミニウム合金の一種で、特に強度と加工性のバランスが優れた材料として広く使用されています。この合金は、軽量でありながら高い強度を誇り、耐食性や熱処理による強化が可能なため、航空機や自動車など、様々な産業で活用されています。
1-1. A6061の概要
A6061は、アルミニウムをベースにした合金で、主にマグネシウム(Mg)とシリコン(Si)を含んでいます。これらの元素が合金内で特定の特性を発揮し、A6061は非常に優れた機械的特性と耐食性を持っています。この合金は熱処理による強化が可能で、T6(熱処理後)などの状態で使用されることが多いです。
1-2. A6061の化学成分
A6061合金の主な化学成分は以下の通りです:
- アルミニウム (Al):残留成分
- マグネシウム (Mg):0.8% – 1.2%
- シリコン (Si):0.4% – 0.8%
- 銅 (Cu):0.15% – 0.4%
- マンガン (Mn):0.15% – 0.8%
- クロム (Cr):0.04% – 0.35%
その他にも少量の鉄(Fe)、チタン(Ti)などが含まれていますが、主に上記の成分が特性を決定します。
2. A6061とは 強度 比重 ヤング率 硬度の機械的特性
A6061は、軽量で高強度を持ちながらも、加工性や溶接性にも優れているため、非常に広範囲にわたる用途で使用されています。次に、A6061の主要な機械的特性を見ていきます。
2-1. A6061の強度
A6061の強度は、その熱処理の状態(特にT6状態)によって異なります。T6状態では、引張強さは約310 MPa、降伏強さは275 MPa程度となります。これにより、強度が高く、負荷がかかる構造部品などに適しています。
- 引張強さ (T6):310 MPa
- 降伏強さ (T6):275 MPa
2-2. A6061の比重
A6061の比重は、アルミニウム合金としては軽量で、約2.7 g/cm³です。この低比重により、航空機や自動車、船舶などの軽量化が求められる分野で広く使用されています。
- 比重:2.7 g/cm³
2-3. A6061のヤング率
A6061のヤング率(弾性係数)は、約68.9 GPaです。この値は、合金の弾性特性を示しており、特に高強度が求められる構造材料において重要な指標となります。
- ヤング率:68.9 GPa
2-4. A6061の硬度
A6061の硬度は、その熱処理状態に依存します。T6状態では、硬度は約95 HB(ブリネル硬度)程度となります。これにより、強度と硬度がバランスよく提供され、耐摩耗性が求められる用途にも対応します。
- 硬度 (T6):95 HB
3. A6061とは 強度 比重 ヤング率 硬度と他のアルミニウム合金の違い
A6061は、他のアルミニウム合金と比較して、特に強度と加工性のバランスが取れていることが特徴です。次に、A6061と他の代表的なアルミニウム合金との違いを見ていきます。
3-1. A6061とA5052の比較
A5052は、アルミニウム合金の中でも耐食性に優れた合金であり、特に海水環境などで使用されます。A6061は強度が高く、加工性にも優れていますが、耐食性はA5052ほど高くはありません。
- A6061:強度が高い(引張強さ310 MPa)、良好な加工性、熱処理による強化可能
- A5052:非常に高い耐食性、引張強さは低め(約230 MPa)、強度はA6061に劣る
3-2. A6061とA7075の比較
A7075は、非常に高い強度を誇るアルミニウム合金で、航空機や軍事用途などで使用されます。A6061はA7075よりも若干低い強度を持ちますが、その分、加工性や溶接性が優れており、より汎用性があります。
- A6061:加工性と溶接性が優れ、汎用性が高い
- A7075:非常に高い強度(引張強さ約570 MPa)だが、加工性は劣る
4. A6061の耐食性と使用用途
A6061は、その優れた機械的特性に加えて、耐食性も高いという特徴があります。これにより、さまざまな環境で使用できるため、幅広い用途に対応しています。
4-1. A6061の耐食性の特徴
A6061は、マグネシウムとシリコンを主成分とする合金であり、優れた耐食性を持っています。特に大気中での腐食や塩水環境に対しても高い耐性を示し、これにより海洋産業や航空産業などで利用されることが多いです。しかし、腐食をさらに防ぐために表面処理(アルマイト処理やコーティング)が施されることもあります。
- 耐食性:良好(特に大気中や塩水環境)
- 表面処理:アルマイト処理やコーティングで強化可能
4-2. A6061の一般的な使用用途
A6061は、その優れた耐食性と機械的特性から、さまざまな産業で使用されています。特に軽量で強度が求められる用途に適しており、以下の分野で広く採用されています。
- 航空機産業:構造部材や機体フレーム、エンジン部品などに使用
- 自動車産業:軽量化を目的とした車両部品(ボディやシャーシ)
- 建設業:橋梁や建物の構造材
- スポーツ用品:自転車フレーム、スノーボードなど
- 船舶産業:船の構造部品やその他海洋設備
A6061はその特性から、特に強度と耐食性が求められる部品や構造物に多く使用されています。
5. アルミニウム合金の選び方と適切な用途
アルミニウム合金は、特性に応じてさまざまな用途に使い分けることが重要です。適切な合金を選ぶことで、製品の性能やコストを最適化することができます。
5-1. アルミニウム合金の選定基準
アルミニウム合金を選定する際は、以下の基準を考慮することが重要です:
- 強度:用途に求められる強度レベルを満たすこと
- 耐食性:使用環境に応じた耐食性を備えていること
- 加工性:加工や成形が容易であること
- 溶接性:溶接が必要な場合、その適性を持っていること
- コスト:予算内で最適な性能を発揮すること
これらの要素をバランスよく考慮し、適切なアルミニウム合金を選定します。
5-2. A6061の適切な用途
A6061は、強度と加工性のバランスが取れた合金であるため、以下の用途に適しています:
- 軽量化が求められる構造物:航空機や自動車、スポーツ用品などで使用
- 耐食性が必要な環境:海洋環境や高湿度地域など
- 加工性が重要な部品:複雑な形状を持つ部品や溶接が必要な部品
- 汎用的な構造材:建設業や機械工業で広く使用される
A6061は、特に多用途で柔軟な合金であり、一般的な産業用途において非常に適しています。
まとめ
アルミニウムA6061は、優れた強度と耐腐食性を持つアルミニウム合金です。比重は約2.7g/cm³、ヤング率は約68.9GPa、硬度はHB 95-105とされています。これにより、航空機や自動車、建築など多様な分野で利用され、加工性にも優れています。軽量でありながら高い強度を発揮するため、現代の技術に欠かせない素材です。
アルミニウムA1100とは?強度・比重・ヤング率・硬度を徹底解説
アルミニウムA1100とは、一体どのような素材なのでしょうか?強度、比重、ヤング率、硬度といった特性を知ることで、より深くその特性を理解し、適切に活用することが可能になります。特に、耐腐食性や加工のしやすさから、多くの産業で利用されているA1100ですが、実際にどのような場面でその特性が生かされるのかを知ることは、素材選びにおいて非常に重要です。
「A1100の強度はどのくらいなの?」「比重って何だろう?」「ヤング率や硬度は、実際の使用にどう影響するの?」といった疑問をお持ちの方も多いのではないでしょうか。そこで、本記事ではアルミニウムA1100の基本情報や特性について詳しく解説します。素材選びの参考にしていただければ幸いです。あなたのプロジェクトに最適な素材を見つけるための手助けとなることを目指しています。
A1100 とは 強度 比重 ヤング率 硬度の概要
A1100の基本情報
- A1100は、純アルミニウムを基にした合金で、アルミニウム含有率が99%以上です。この合金は、特に高い耐食性、優れた加工性、優れた成形性を特徴としており、主に軽量化が求められる用途に使用されます。また、電気伝導性や熱伝導性も高いため、電気機器や熱交換器などに使用されることがあります。
A1100の機械的性質の重要性
- A1100の機械的性質は、主に加工や使用環境におけるパフォーマンスに直結します。特に強度と硬度の適正値は、製品の耐久性や使用条件に対する適応性に大きな影響を与えます。A1100は比較的低い強度と硬度を持っていますが、その軽さと加工性の良さから、特定の用途には非常に優れた性能を発揮します。
A1100の強度と硬度
A1100の強度の特性
- 強度: A1100は、比較的低い強度を持ちます。引張強度は約90-150 MPa程度で、強度が求められる構造用途には向いていません。そのため、軽量かつ耐食性が重視される用途に最適です。強度が低い一方で、耐食性が非常に高く、酸性やアルカリ性の環境でも優れた耐久性を発揮します。
A1100の硬度の測定方法
- 硬度: A1100の硬度は比較的低く、通常の硬度試験(例えば、ブリネル硬度試験やロックウェル硬度試験)で計測できます。ロックウェル硬度は約30-40 HRC程度となり、他の高強度アルミニウム合金と比較して低めです。このため、耐摩耗性や衝撃に対する耐性が求められる用途には適しません。
他の材料との強度・硬度比較
- A1100は、A5052やA6061、A7075などのアルミニウム合金と比較して、強度や硬度が低いことが特徴です。しかし、その分加工が容易であり、耐食性が非常に高いため、特定の軽量化が求められる用途や腐食環境において優れた選択肢となります。
A1100の比重とヤング率
A1100の比重の特性
- 比重: A1100の比重は約2.71 g/cm³であり、アルミニウム合金としては標準的な値です。軽量性が求められる用途において、他の金属材料に比べて大きなアドバンテージとなります。比重が低いため、軽量化が必要な製品や構造部品に適しています。
A1100のヤング率の重要性
- ヤング率: A1100のヤング率は約70-80 GPa程度であり、アルミニウム合金の中ではやや低めです。ヤング率が低いため、柔軟性を求められる用途に適しており、加工性にも優れていますが、耐荷重性が求められる部品には不向きです。ヤング率は材料の剛性に関わるため、使用する環境や部品の役割に応じて選定することが重要です。
比重とヤング率がもたらす影響
比重とヤング率の影響: A1100の軽さ(低い比重)は、特に移動機器や航空機部品など、軽量化が求められる用途に適しています。一方で、ヤング率が低いため、変形しやすい特性も持っており、強い負荷や高い剛性が求められる部品には他の合金を選ぶ必要があります。比重とヤング率のバランスを考慮し、用途に応じた適切な合金選定が重要です。
A1100の具体的な用途と適用例
A1100の一般的な用途
- A1100は、非常に高い耐食性を持つ純アルミニウム合金であり、特に腐食環境に適した材料として広く使用されています。主な用途には以下が含まれます:
- 食品加工業:高い耐食性が求められるため、食品機器や容器などに使用されます。
- 化学機器:酸性やアルカリ性の環境下でも腐食しにくいため、化学設備や配管などに使用されます。
- 建材:外装材や看板など、屋外での使用に適しています。
- 電子機器:電気機器の部品、ヒートシンク(熱交換器)などに使用されることがあります。
A1100の産業別適用例
- 自動車産業:軽量化が求められる車両の外装部品や内装部品に利用されることがあります。特に耐食性が必要な部分に適しています。
- 航空産業:軽量で高い耐食性が求められる航空機の構造部品や部品などに使用されます。
- 建設産業:特に腐食が懸念される環境で使用される外壁材や屋根材に利用されることが多いです。
- エレクトロニクス業界:放熱が必要な機器のヒートシンクやケースなどに使用されます。
A1100の選定基準
- 耐食性が最も重要な選定基準となります。特に腐食性の高い環境や屋外で使用される場合に適しています。
- 加工性:A1100は非常に加工しやすいため、形状変更や溶接などが簡単に行える点が選定のポイントです。
- コスト効率:A1100は比較的低価格で入手可能であるため、コストパフォーマンスが求められる場面で選ばれます。
A1100と他のアルミ合金との違い
A1100とA1050の比較
- A1100とA1050は、どちらも純アルミニウム合金ですが、A1100は少量の他の元素(例:鉄)を含んでおり、A1050よりわずかに強度が高くなっています。
- A1100:より優れた加工性、より高い耐食性を提供し、食品や化学工業でよく使用されます。
- A1050:より純度が高く、さらに優れた導電性と熱伝導性を提供しますが、強度や耐久性ではA1100に劣ります。
A1100とA6061の比較
- A6061は、熱処理が可能なアルミニウム合金で、強度や耐摩耗性が高いのが特徴です。
- A1100:耐食性が高く、主に加工性や腐食環境での使用が重視される場合に使用されます。
- A6061:高強度が求められる部品(例えば、自動車部品、航空機部品)や構造材料に適しています。A6061は、機械的特性が優れているため、荷重がかかる用途にはA1100よりも適しています。
A1100の選択理由
コストパフォーマンス:他のアルミニウム合金と比較して、A1100は比較的低価格であり、コスト効率の良い選択肢です。
耐食性の高さ:A1100は高い耐食性を持ち、腐食環境での使用に最適です。
優れた加工性:A1100は非常に加工しやすく、溶接や成形などが容易です。そのため、複雑な形状の部品に適しています。
まとめ
アルミニウムA1100は、優れた成形性と耐食性を持つ純度99%のアルミニウム合金です。強度は比較的低いものの、比重は約2.7 g/cm³、ヤング率は約69 GPa、硬度は約60 HBです。これにより、食品加工や化学機器など多様な用途に適しています。軽量で加工しやすい特性が魅力です。
アルミニウムA1050の特性とは?強度、比重、ヤング率、硬度を徹底解説
アルミニウム合金の中でも、A1050はその優れた特性によって多くの産業で重宝されています。「A1050とは一体何なのか?」「その強度や比重、ヤング率、硬度はどうなっているのか?」と疑問を持つ方も多いことでしょう。このガイドでは、A1050の基本的な特性を詳細に解説し、どのように活用されるかを明らかにします。
A1050は、主に電気伝導性や耐食性が求められる用途に適しているため、電子機器や食品加工業界などで広く利用されています。これらの特性を理解することで、A1050の応用可能性を広げる手助けになるでしょう。この記事では、A1050の強度、比重、ヤング率、硬度といった重要なパラメーターについて詳しく掘り下げ、実際の使用例や選定ポイントまでご紹介します。
この情報が、A1050を使用したいと考えている方々にとって、大いに役立つことを願っています。一緒にA1050の魅力を探っていきましょう。
A1050 とは 強度 比重 ヤング率 硬度の基本情報
A1050の概要
- A1050は、アルミニウム純度が99%以上の純アルミニウム合金で、非常に高い耐食性を持っています。主に電気機器や建築材料、食品加工などに使用されます。A1050はその軽さと加工性が求められる用途に適しています。
A1050の強度と比重
- 強度: A1050は純度が高いため、一般的に強度は他のアルミニウム合金に比べて低いです。引張強さは約70〜100 MPa程度であり、これは他の合金に比べて低い部類に入ります。
- 比重: 比重はおおよそ2.70 g/cm³で、アルミニウム合金としては標準的な値です。アルミニウムは非常に軽い金属であり、軽量化が求められる用途に適しています。
A1050のヤング率と硬度
- ヤング率: A1050のヤング率は約69 GPaで、アルミニウム合金全体としても比較的低い部類に入ります。この値は、アルミニウムの柔軟性を示しており、強度よりも加工性を重視する用途に適しています。
- 硬度: A1050の硬度は、おおよそ50〜60 HRB(ロックウェル硬度B)程度であり、硬度が比較的低いため、機械的な加工が容易です。
A1050 とは 強度 比重 ヤング率 硬度と他のアルミニウム合金の比較
A1050とA5052の違い
- A1050は純度が高く、主に耐食性と加工性に優れていますが、強度は低いです。これに対して、A5052はマグネシウムを含む合金で、強度が高く、耐食性にも優れていますが、A1050よりも少し加工性が劣ります。A5052は、強度が要求される自動車や船舶、化学プラントの部品に使用されます。
他のアルミニウム合金との特性比較
- A1050とA6061: A6061はシリコンとマグネシウムを含む合金で、強度がA1050よりも高く、また溶接性や耐腐食性に優れています。A1050は加工性と軽量性に優れますが、A6061は機械的強度や耐衝撃性が求められる用途に適しています。
A1050 とは 強度 比重 ヤング率 硬度と鉄との比較
アルミニウムと鉄の強度の違い
- 強度: 鉄はアルミニウムよりもはるかに強度が高い金属です。例えば、鉄の引張強さは250 MPa以上であり、A1050の引張強さの約2.5〜3倍程度です。ただし、鉄はアルミニウムよりも重いため、軽量化を求められる用途ではアルミニウムが選ばれます。
ヤング率の比較とその影響
ヤング率: 鉄のヤング率は約210 GPaであり、A1050(約69 GPa)よりもかなり高い値です。これは、鉄がより硬くて剛性が高いため、構造物や耐荷重が求められる用途に向いています。一方、A1050は比較的柔軟で、加工が容易ですが、構造的な用途には適しません。
A1050の耐食性と使用環境
A1050の耐食性の特性
- 耐食性: A1050は非常に高い耐食性を持っています。純アルミニウム合金であるため、酸性やアルカリ性の環境にも強く、塩水や湿気に対しても優れた耐久性を示します。この特性は特に建築や食品業界、化学プラントでの使用に適しています。
- 酸化被膜: A1050は、表面に自然酸化膜を形成し、これが耐食性を高める役割を果たします。この酸化膜は外的な腐食要因から金属を保護し、アルミニウムの美観を保つとともに、劣化を防ぐ働きがあります。
A1050が適した使用環境
- 屋外使用: 高い耐食性により、A1050は屋外で使用される構造物や建材(例えば、外装材やパネル)に適しています。また、海岸付近など湿気が多い環境でも腐食が抑えられます。
- 食品業界: A1050は食品に触れる機器や容器、設備にも使用されることが多いです。耐食性が高いため、長期的に安定した性能を発揮し、衛生的な環境が求められる用途に適しています。
- 化学環境: 軽度の酸やアルカリに対しても耐性があり、化学プラントの設備や容器に使用されることがあります。特に化学的な腐食が発生しやすい環境においてその特性を活かせます。
アルミニウム合金の選定における特性の重視点
強度と硬度の重要性
- 強度: 使用する製品の機械的強度が重要な場合、合金の選定では強度を重視する必要があります。A1050は比較的低い強度を持っているため、機械的な負荷がかかる構造物や部品には不向きですが、軽量化と耐食性が重要な用途には適しています。
- 硬度: 硬度は、合金がどれだけ耐摩耗性を持ち、機械的にどれだけ強靭かを示す指標です。A1050は比較的低い硬度を持つため、衝撃や摩耗に強い合金が必要な場合は、他の合金(例えば、A6061など)を選ぶことが望ましいです。
使用環境に応じた選定基準
使用負荷: 高い機械的負荷がかかる場合や耐衝撃性が必要な用途では、A1050はあまり適していません。強度や硬度が求められる用途では、A6061やA7075など、より高強度の合金が選ばれます。
環境条件: 使用環境が厳しい場合(高温、高湿、化学的腐食環境など)、合金の選定はその環境条件を満たす耐食性や強度を持つものを選びます。例えば、海水や塩水環境で使用する場合は、A5052やA6061など、より耐食性が高い合金を選定することが適切です。
まとめ
アルミニウムA1050は、優れた耐食性と加工性を持つ純アルミニウム合金です。強度は比較的低く、比重は約2.7 g/cm³、ヤング率は約70 GPa、硬度は約25-30 HBです。これらの特性により、軽量で高い導電性を求める用途に適しています。
知っておきたい!アルミニウムの質別記号とその分類
「アルミニウムについてもっと知りたいけれど、その質別記号や種類が多すぎて混乱している……」そんな悩みを抱えている方はいませんか?本記事では、アルミニウムの質別記号やその分類について、わかりやすく解説します。
アルミニウムは軽量で耐食性に優れ、様々な産業で活用されています。しかし、その特性や用途に応じて、数多くの種類が存在することを知っていますか?質別記号は、どのアルミニウムがどのような特性を持っているかを示す大切な情報です。自分に適したアルミニウムを選ぶためには、まずこれらの基本を理解することが重要です。
このガイドでは、アルミニウムの質別記号の意味、各種類の特徴、そして実際の使用例を詳しくご紹介します。あなたのアルミニウム選びに役立つ知識を身につけ、より良い選択をするための手助けとなれば幸いです。さあ、一緒にアルミニウムの世界を探求していきましょう!
アルミニウム 質別記号 種類 解説
アルミニウム合金の基本知識
- アルミニウム合金は、純度の高いアルミニウムに他の金属を加えたもので、特性を向上させるために利用されます。主に銅、マグネシウム、シリコン、マンガンなどが含まれることが多く、それぞれの金属が合金の性質に影響を与えます。
- 合金の番号によって、成分や用途が分類されており、アルミニウム合金は主に「シリーズ番号」で識別されます。例えば、1000シリーズは純アルミニウム、2000シリーズは銅を主成分とする合金、3000シリーズはマンガンが主成分です。
アルミニウムの質別記号とは
- 質別記号は、アルミニウムの合金を示す番号や符号で、合金の組成や特性、調質などの情報を表します。たとえば、A6061-T6という表記では、6061が合金の種類、T6が熱処理状態(調質)を示します。
- 質別記号の構成:
- 数字部分: 合金の主要成分を示す番号。アルミニウム合金は番号ごとにその成分や性質が異なります。
- アルファベット部分: 熱処理や加工状態を示す符号(T表示)。
- 調質記号: 加工や熱処理方法による性質の状態を表します。
アルミニウム合金の調質について
- 調質は、合金の機械的性質を向上させるための処理方法です。これには、熱処理(焼なまし、焼入れ、焼戻し)や冷間加工(引き抜き、押出し)などが含まれます。
- 調質後、合金はその特性が変わり、強度、耐食性、加工性などが改善されます。アルミニウム合金の調質には主に次の方法があり、それぞれの処理方法に応じて、合金の強度や硬度が増加します。
アルミニウム 質別記号 種類 解説:熱処理の種類
アルミニウムの熱処理方法
- 焼なまし: アルミニウムを高温に加熱し、ゆっくりと冷却して、内的応力を減少させ、柔軟性を増します。これにより、加工がしやすくなります。
- 焼入れ: 高温で加熱し、急速に冷却することで、強度や硬度を増加させます。これにより、合金がより強靭になります。
- 焼戻し: 焼入れ後、再度加熱して冷却し、硬さを適切に調整することで、脆性を低減し、機械的性質を最適化します。
各熱処理の特徴と用途
- 焼なまし:
- 特徴: 柔らかくなる、内的応力が解消される。
- 用途: 加工しやすさが求められる場面で使用される。
- 焼入れ:
- 特徴: 強度と硬度が増加、靭性が低下する可能性あり。
- 用途: 高強度が求められる部品、例えば航空機の部品や構造材などで利用。
- 焼戻し:
- 特徴: 焼入れ後の脆さを減少させ、強度と靭性のバランスを取る。
- 用途: 機械的強度が必要な部品の最終調整。
熱処理による性質の変化
耐食性の向上: 熱処理後に形成される酸化膜が強化され、耐食性が改善されることがあります。
強度の向上: 焼入れによって、アルミニウム合金の引張強度や硬度が増加し、使用条件に応じた強度が提供されます。
延性と靭性の調整: 焼戻しによって、強度を保ちながら延性や靭性を調整し、過度に脆くならないようにします。
アルミニウム 質別記号 種類 解説:合金の選び方
アルミニウム合金の選定基準
- 目的に応じた強度: 使用する環境における強度要求に基づいて合金を選定します。例えば、航空機や自動車などの高強度が求められる用途には、特に強度の高い合金(2000シリーズや7000シリーズ)が選ばれます。
- 耐食性: 耐食性が重要な場合は、海水環境などでの使用を想定して、3000シリーズや5000シリーズなど、マグネシウムを主成分とした合金が適しています。
- 加工性: 加工が容易な合金が必要な場合、1000シリーズや6000シリーズ(特に6061)は、優れた加工性とバランスの取れた性能を持っています。
- コスト: 一般的に、合金の成分が複雑なほどコストが高くなるため、コストパフォーマンスを考慮することも選定基準に含まれます。
用途別のアルミニウム合金
- 自動車: 軽量化が求められる自動車産業では、6061などの中程度の強度を持ちながら良好な加工性を誇る合金が多く使われます。
- 航空機: 高強度かつ耐食性に優れた2000シリーズ(特に2024)や7000シリーズ(7075)などが航空機の構造材に使用されます。
- 建築: 建築材料には、耐食性に優れ、加工が容易な5000シリーズ(特に5052)が多く使用されます。
- 電子機器: 軽量化と耐食性が求められる電子機器では、6000シリーズ(6061や6063)が一般的に使用されます。
機械部品に適したアルミニウム合金
- 強度: 機械部品には、強度が必要な場合が多く、7075や2024のような高強度合金が適しています。
- 耐摩耗性: 高い耐摩耗性を求められる場合には、硬質アルマイト処理を施した7075や2011などが有効です。
- 耐食性: 海上環境や化学薬品が触れる場所で使用される部品には、耐食性に優れた5000シリーズ(5052や5083)や6000シリーズが選ばれます。
アルミニウム 質別記号 種類 解説:専門知識の深化
アルミニウムの物理的特性
- 密度: アルミニウムは非常に軽い金属で、密度は約2.7 g/cm³であり、鋼鉄に比べて約1/3の軽さです。この特性が、航空機や自動車など軽量化が求められる分野での使用を促進しています。
- 熱伝導性: アルミニウムは良好な熱伝導性を持ち、熱処理や冷却が必要な部品に適しています。
- 電気伝導性: アルミニウムは高い電気伝導性を持ち、電気ケーブルや配線などに広く使用されています。
- 膨張率: アルミニウムは比較的高い膨張率を持つため、温度変化に敏感な用途には注意が必要です。
アルミニウムの化学的特性
熱安定性: 高温に対しても比較的安定しており、600℃程度までは機械的性質を維持しますが、より高温では強度が低下します。
耐食性: アルミニウムは、酸化アルミニウムの薄い膜が自然に形成されることで耐食性を持ちます。この膜は薄くて強力で、アルミニウムが腐食するのを防ぎます。
反応性: アルミニウムは非常に反応性が高い金属であり、酸やアルカリと反応します。しかし、酸化膜がこの反応を抑えるため、通常の環境下では安定しています。
まとめ
アルミニウムの質別記号は、主にJIS(日本工業規格)やISO(国際標準化機構)で定められています。代表的な分類には、純アルミニウム(1000系)や合金(2000系、6000系など)があり、それぞれ特性や用途が異なります。正しい質別記号の理解は、適切な材料選定に不可欠です。