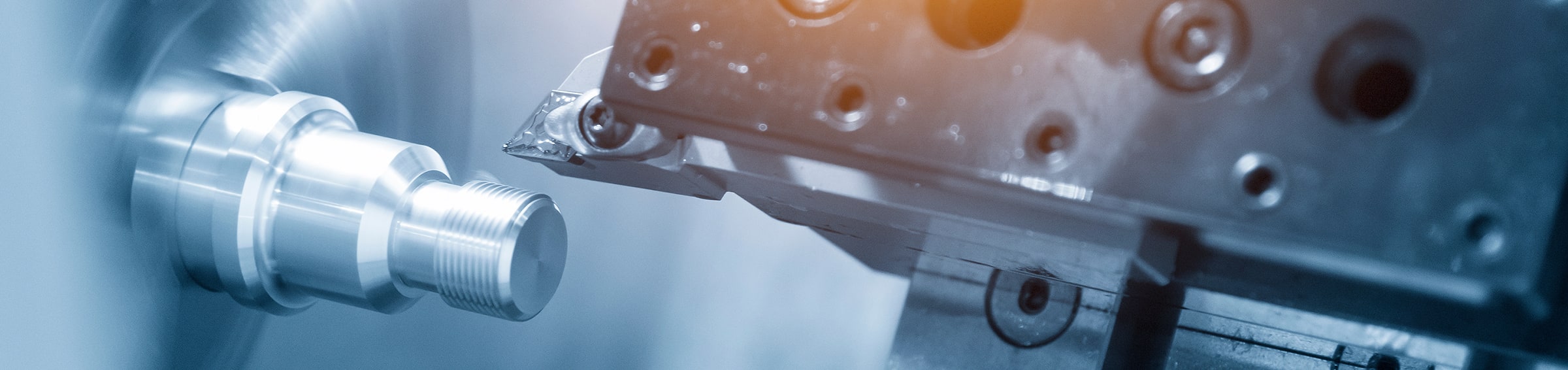
コラム column
A7003合金の特徴と用途を徹底解説!他のアルミニウムとの違いとは?
あなたは「A7003合金って何だろう?どんな特徴があって、どのように使われているのだろう?」と考えたことはありませんか?それなら、この記事はまさにあなたのためにあります。A7003合金は、特有の特性を持ち、さまざまな用途で活躍するアルミニウム合金の一つです。
私たちは、合金の基本的な構造から、その特性や利用例、さらには他のアルミニウム合金との違いまで、包括的にご紹介します。特に、その軽さや強度が求められる分野での活用方法については、多くの人々にとって興味深い知識となるでしょう。
A7003合金についての詳細を知りたい方、あるいは新たな材料選定の参考にしたい方は、ぜひこのガイドをお読みください。あなたの疑問が解消され、A7003合金の魅力を再発見する手助けとなるでしょう。
1. A7003の特徴と用途
1-1. A7003の基本的な特性
A7003は7xxx系アルミニウム合金に分類され、主に亜鉛(Zn)とマグネシウム(Mg)を主成分としています。この合金は中程度の強度と優れた耐食性を持ち、熱処理によって機械的性質を高めることができます。また、溶接性も良好で、構造材として利用されています。
1-2. A7003の主な用途
A7003は以下のような用途で多く使用されています:
- 自転車フレーム
- 鉄道車両のボディ構造
- スポーツ・レジャー機器の部品
- 建築用の構造部材
その軽量性と強度のバランスにより、特に構造材として広く利用されています。
1-3. A7003の利点と欠点
利点
- 溶接後の機械的性質が安定
- 高い耐食性
- 熱処理による性能向上が可能
- 軽量で加工性が良好
欠点
- 高強度が求められる用途ではA7075などに劣る
- 加工性はA6061に比べてやや劣る
- 溶接後の特性改善には適切な後熱処理が必要
2. A7003と他のアルミニウム合金の違い
2-1. A7003とA6061の比較
A7003はA6061よりも高い強度を持ち、特に構造材として有利です。一方で、加工性はA6061がやや勝ります。A7003は溶接後の特性が安定しているため、溶接が多い環境で有利です。
2-2. A7003とA7075の違い
A7075は非常に高い強度を持つ合金で、特に航空機部品や高強度が求められる製品に使用されます。しかし、A7075は溶接性や耐食性においてA7003より劣るため、用途に応じた選択が求められます。
2-3. A7003の選定理由
A7003は中強度で溶接性が高く、特に構造材や鉄道車両などの軽量かつ強度が必要な用途に適しています。また、高い耐食性を持ち、屋外環境でも使用可能です。
3. アルミニウム合金の選定方法
3-1. 用途に応じた合金の選び方
アルミニウム合金を選定する際は、使用環境、強度、加工性、溶接性、耐食性などを考慮する必要があります。特に、屋外で使用する場合は耐食性が重要な要素となり、強度や軽量化が求められる用途にはA7003が適しています。
3-2. 機械的性質の重要性
機械的性質は、材料選定において非常に重要な要素です。強度や硬度、疲労強度、延性などを考慮し、設計要求に最も適した合金を選ぶことが重要です。A7003は中程度の強度を持ち、構造用材料として信頼性が高いです。
3-3. 軽量化設計におけるポイント
軽量化設計を行う際は、強度対比重量が高い材料を選ぶことが重要です。A7003はその強度と軽さを兼ね備えており、軽量化設計に適した材料となります。肉厚や断面形状の最適化を行うことで、さらに効率的な設計が可能です。
4. アルミニウムの基礎知識
4-1. アルミニウムの特性
アルミニウムは軽量で、耐食性に優れた金属です。さらに、優れた熱伝導性と電気伝導性を持ち、加工性も良好です。高い引張強度と延性を兼ね備え、比較的低温でも強度が維持されるため、多岐にわたる用途に使用されます。その他、アルミニウムは非磁性であり、環境に優しい特性も持ちます。
4-2. アルミニウム合金の種類
アルミニウム合金は大きく分けて以下の種類に分類されます:
- 1xxx系(純アルミニウム): 純度が高く、耐食性に優れるが強度が低い。
- 2xxx系(銅合金): 高い強度を持つが、耐食性はやや劣る。
- 3xxx系(マンガン合金): 良好な耐食性と中程度の強度を持つ。
- 5xxx系(マグネシウム合金): 高い耐食性と強度を持ち、海水環境での使用に適している。
- 6xxx系(シリコン・マグネシウム合金): 良好な機械的特性と加工性を持ち、構造材や建材に広く使用される。
- 7xxx系(亜鉛合金): 非常に高い強度を持つが、耐食性は他の合金に劣る。
4-3. アルミニウムの加工方法
アルミニウムは加工しやすい材料であり、以下のような方法で処理されます:
- 押出し: 高温でアルミニウムを型に押し込む方法。パイプや棒状の製品を製造するのに使用。
- 鋳造: 融解したアルミニウムを型に流し込む方法で、複雑な形状の部品を作るのに適しています。
- 切削加工: フライス盤や旋盤を使い、アルミニウムを削って形状を作る方法。
- 溶接: アルミニウムは比較的溶接しやすく、TIG(ティグ)溶接やMIG(ミグ)溶接が一般的に使用されます。
5. A7003の機械的性質
5-1. 引張強度と降伏強度
A7003合金の引張強度は約280〜310 MPaで、降伏強度は約220〜250 MPaです。これにより、中程度の強度が要求される構造用途に適しています。また、A7003は非常に高い引張強度を持つため、部材が長期間使用される環境での信頼性も高いです。
5-2. 耐食性と耐摩耗性
A7003は優れた耐食性を持ち、特に海洋環境や湿度の高い地域での使用に向いています。耐摩耗性も良好で、摩擦がかかる部品にも適しています。これらの特性により、A7003は構造材としても信頼性があります。
5-3. 加工性と溶接性
A7003は加工性が良好で、一般的な切削加工や機械加工に適しています。さらに、溶接性も高く、適切な溶接技術を使用すれば、強固な接合が可能です。しかし、溶接後には後熱処理を行い、機械的性質を回復させることが重要です。
まとめ
A7003合金は、主にマグネシウムと亜鉛を含むアルミニウム合金で、優れた強度と耐腐食性が特徴です。自転車フレームや航空機部品など、高い強度が求められる用途に最適です。他のアルミニウム合金と比べて、軽量で加工性も良好なため、さまざまな産業での利用が広がっています。
A7204アルミニウムと他のアルミニウム合金の違いとは?
「A7204アルミニウムについて知りたいけれど、他のアルミニウム合金との違いがイマイチわからない…」そんな悩みを持つあなたにぴったりの情報をお届けします。このガイドでは、A7204アルミニウムの特徴や用途、さらには他のアルミニウム合金との違いを詳しく解説します。
A7204は、その優れた特性から様々な産業で利用されており、特に航空宇宙や自動車産業において注目されています。しかし、なぜこの合金が選ばれるのか、どのような状況でその力を発揮するのか、具体的に理解することは意外と難しいものです。
本記事では、A7204アルミニウムの基本情報をはじめ、その特性や用途、さらには他のアルミニウム合金との具体的な違いに焦点を当てていきます。これにより、あなたがA7204アルミニウムを正しく理解し、実際のプロジェクトに応じた選択ができるようになることでしょう。さあ、一緒にA7204の世界を探ってみましょう!
1. A7204 特徴 用途 他のアルミニウム 違い
1-1. A7204アルミ合金の基本特性
A7204は、7XXX系に分類される高強度アルミニウム合金で、主に亜鉛を主成分としています。優れた引張強さと耐力を持ち、構造部材として使用されることが多い合金です。熱処理による強化が可能で、T6処理を施すことで、極めて高い機械的性質が得られます。一方、耐食性はやや劣るため、防食処理や設計上の配慮が必要となります。
1-2. A7204の主な用途
A7204は以下のような高強度が求められる分野で活用されています。
- 航空機の構造部材(主翼、胴体フレームなど)
- 自動車の高剛性部品
- スポーツ機材(自転車フレーム、登山用品)
- 工業用高圧部品や金型部材
特に重量を抑えつつも高い強度が必要な用途に適しており、強度・剛性重視の設計に好まれます。
1-3. A7204と他のアルミニウム合金の違い
A7204はA7075と同様に高強度を誇る7XXX系合金でありながら、若干の組成差により、加工性や耐応力腐食割れに対する耐性に違いがあります。以下の点が主な違いです。
- A5052やA6061と比べて、はるかに高い強度を持つ
- A7075と同様に熱処理硬化型であり、引張強さが400MPaを超える
- 耐食性はA5052やA6061より劣るため、腐食環境下での使用には注意が必要
- A1100やA1050などの純アルミ系とは全く異なり、加工後の機械的特性重視
強度優先の選定をする場合に候補となる合金です。
2. アルミニウム合金の基礎知識
2-1. アルミニウム合金の種類
アルミニウム合金は大きく分けて「非熱処理型」と「熱処理型」の2種類に分類されます。
- 非熱処理型合金(1xxx、3xxx、5xxx系):冷間加工による強化が主で、耐食性や加工性が良好。
- 熱処理型合金(2xxx、6xxx、7xxx系):溶体化処理と時効処理により、非常に高い強度を得られる。
2-2. アルミニウム合金の特性
アルミニウム合金の特性は以下の点で異なります。
- 強度:7xxx系が最も高く、次いで6xxx系、5xxx系と続きます。
- 耐食性:5xxx系や1xxx系が優れています。
- 加工性:1xxx系、3xxx系が良好。7xxx系はやや劣る傾向。
- 溶接性:5xxx系や6xxx系が優れ、7xxx系や2xxx系は注意が必要。
2-3. アルミニウム合金の選定基準
合金を選定する際のポイントは以下の通りです。
- 用途の要求性能を明確にする(強度、耐食性、加工性、外観など)
- 使用環境を把握する(屋外/屋内、腐食性雰囲気、温度条件など)
- 加工方法に適合しているか確認する(切削、溶接、曲げなど)
- コストとのバランスを取る
例えば、強度と軽量化が最重要な場合はA7204やA7075が選ばれますが、耐食性や溶接性を重視する場合はA5052やA6061が有利です。
3. A7204合金の切削性について
3-1. 切削性の評価基準
アルミニウム合金の切削性を評価する際には、以下のような項目が基準とされます。
- 切削抵抗:工具にかかる負荷の大きさ
- 切りくず処理性:切りくずが細かく排出されやすいかどうか
- 工具寿命:刃先の摩耗や損傷のしやすさ
- 表面仕上げ性:切削後の面粗さや光沢
- 寸法精度:高精度加工への対応力
これらの項目は、使用する工具の材質やコーティング、切削条件(回転数、送り速度、冷却方法)にも左右されます。
3-2. A7204の切削性の特徴
A7204は7xxx系に属し、高強度を誇る反面、以下のような特徴があります。
- 切削抵抗が高め:高硬度のため、加工中の工具負荷が大きい
- 工具摩耗が早い:高硬度・高強度のため、刃先の寿命が短くなりがち
- 切りくずが細かくなりにくい:条件によっては長い切りくずが発生しやすい
- 表面品質は条件次第:適切な工具と条件を整えれば良好な面粗さも可能
そのため、A7204の切削には高剛性の工作機械や耐摩耗性の高い工具が求められます。
3-3. 切削加工における注意点
A7204を切削加工する際には、以下の点に注意が必要です。
- 超硬工具やコーティング工具の使用:工具寿命を延ばすため
- 切削油の適切な使用:発熱と工具摩耗を抑える
- 切削条件の最適化:送り速度・回転数のバランスを取る
- チャッキングの強化:振動によるビビりを防ぐ
- 切りくずの除去性確保:切りくず詰まりによる加工不良防止
適切な準備と工程設計によって、A7204でも高精度かつ効率的な加工が可能になります。
4. 軽量化設計に適したアルミニウムの選定方法
4-1. 軽量化設計の重要性
現代の製品設計では、エネルギー効率や環境負荷低減の観点から、軽量化は極めて重要です。特に以下の分野で軽量材料の使用が進んでいます。
- 自動車:燃費向上、EVの航続距離向上
- 航空機:燃料消費削減、搭載荷重の増加
- 建築資材:施工性向上、構造の合理化
- スポーツ用品:操作性やパフォーマンスの向上
軽量化は単に材料を軽くするだけでなく、強度とのバランスを取ることが求められます。
4-2. A7204の軽量化設計への適用
A7204は強度と剛性が非常に高いため、部材の肉厚を薄くしても十分な強度を確保できます。これにより、以下のような軽量化設計が可能になります。
- 構造部の最適断面化:厚みを減らしても強度が保てるため、部品重量を削減可能
- 高強度が必要な部位への適用:他材では対応できない応力に耐えながら軽量化を実現
- 一体成型による部品点数削減:強度があるため複雑な一体構造にしやすく、軽量化と製造簡略化を両立
4-3. 他のアルミニウム合金との比較
A7204は以下のような点で他合金よりも軽量化に貢献しやすい合金です。
- A6061との比較:A6061は溶接性・耐食性に優れるが、強度はA7204より劣る。強度を優先する場合、A7204が有利。
- A5052との比較:耐食性と成形性はA5052が上だが、機械的強度はA7204が圧倒的。重量あたりの強度に優れる。
- A7075との比較:A7075と同等の性能を持ちながら、加工性や応力腐食割れへの耐性に若干の違いがあるため、設計目的に応じて使い分けができる。
最終的な合金選定は、強度、腐食環境、加工性、コストのバランスに基づいて決定されます。
まとめ
A7204アルミニウムは、高い強度と耐食性を持つ合金で、特に航空宇宙や自動車産業で使用されます。他のアルミニウム合金と比較して、A7204は耐熱性に優れ、加工性が良いですが、コストが高くなる傾向があります。特に、A7000系と比べて、より優れた靭性を提供します。
A7N01の特徴と用途を徹底解説!他のアルミニウム合金との違いとは?
アルミニウム合金の世界には、数多くの種類が存在しますが、その中でA7N01は特に注目されています。あなたは、「A7N01って何?どんな特徴があるの?他のアルミニウム合金と何が違うの?」と疑問に思っていませんか?このガイドは、そんなあなたのために用意されました。
A7N01は、その特性から様々な用途に幅広く利用されています。建設や輸送、機械製造など、実に多彩な分野で活躍しているのです。本記事では、A7N01の基本的な特徴や具体的な用途を詳しく解説し、他のアルミニウム合金との違いについても触れていきます。これを読むことで、A7N01に対する理解が深まり、実際のニーズに応じた選択ができるようになるでしょう。
興味を引く内容が盛りだくさんのこのガイドを通じて、A7N01の魅力をしっかりと掴んでみてください。さあ、アルミニウム合金の奥深い世界へ一緒に飛び込んでみましょう!
1. A7N01の特徴・用途・他のアルミニウムとの違いについての概要
1-1. A7N01の基本的な特性
A7N01はアルミニウムと亜鉛を主成分とする7XXX系の合金で、高い強度と優れた耐食性を両立した材料です。特に溶接性に優れており、構造用材としても高く評価されています。冷間加工性にも優れており、引張強さや疲労強度も良好です。
1-2. A7N01の用途と適用分野
A7N01は、以下のような分野で多く使用されています:
- 鉄道車両(特に新幹線などの構体材)
- 航空機の内装材
- 高速道路や橋梁などの構造部材
- 輸送機器や建築構造物の溶接構造材
その軽量性と溶接性から、重量削減が求められる分野で多用されます。
1-3. 他のアルミニウム合金との違い
A7N01は、同じ7XXX系の中でも比較的溶接性に優れるという点が特徴です。たとえばA7075は非常に高い強度を持ちますが、溶接性に劣ります。一方、A7N01は強度と溶接性をバランス良く持っており、構造用途に最適な合金とされています。
2. アルミニウムの種類や特性
2-1. アルミニウムの基本特性
純アルミニウムは以下のような特性を持ちます:
- 軽量(比重:約2.7)
- 耐食性が高い
- 熱伝導性・電気伝導性に優れる
- 非磁性体で、加工性が良い
ただし、純度が高いものほど強度は低くなります。
2-2. アルミニウム合金の分類
アルミニウム合金は大きく分けて以下の2系統に分類されます:
- 非熱処理型合金(1000番台・3000番台・5000番台など):加工硬化によって強度を増す
- 熱処理型合金(2000番台・6000番台・7000番台など):析出硬化により強度を増す
2-3. 各種アルミニウム合金の特徴
系列 | 主な合金元素 | 特徴 | 用途例 |
---|---|---|---|
1000番台 | 純アルミ | 高耐食性・良導電性 | 電気機器・装飾 |
5000番台 | Mg | 高耐食性・中強度 | 船舶・車体 |
6000番台 | Mg+Si | 高い加工性・中強度 | 建築・機械部品 |
7000番台 | Zn | 高強度・一部溶接性良好 | 航空・輸送・構造材(A7N01など) |
3. アルミニウム合金の熱処理の違い
3-1. 熱処理の基本概念
熱処理とは、加熱・冷却を通じて金属の性質を制御する技術です。アルミニウム合金の場合、主に次の2つの処理が使われます:
- 溶体化処理:合金成分を固溶させる
- 時効処理:析出物を生成し、強度を高める
このプロセスにより、高強度化や靭性の向上が可能になります。
3-2. A7N01の熱処理方法
A7N01は「T5」や「T6」などの時効処理を経て使用されることが多く、特に人工時効によって機械的性質が大きく向上します。加工後に焼き戻しを行うことで、寸法安定性や強度の均一化も図られます。
3-3. 他のアルミニウム合金との熱処理の違い
- A7075:T6処理で最高レベルの強度を発揮するが、溶接には不向き
- A6061:T6処理により中程度の強度と良好な加工性を両立
- A7N01:T5やT6により強度と溶接性の両立が可能
つまり、A7N01は熱処理によって強度を確保しつつ、構造用途にも適応できる柔軟性の高い素材として使われます。
4. アルミ合金の用途や適切な選び方
4-1. アルミ合金の一般的な用途
アルミ合金は軽量で加工性や耐食性に優れるため、幅広い分野で使用されています。代表的な用途として、自動車や航空機などの輸送機器、建築用外装材、電子機器の筐体、食品包装、厨房器具、そして工業機械の構造部品などが挙げられます。用途によって求められる特性(強度、耐食性、溶接性など)が異なるため、それに応じた適切な合金が選ばれます。
4-2. 用途に応じたアルミ合金の選び方
アルミ合金を選定する際は、以下の点を考慮します。
- 強度が求められる場合は、A7075やA7N01のような高強度合金を選定。
- 溶接性が重視される場合は、A5052やA6061、A7N01などが適しています。
- 耐食性が重要な用途には、A1100やA5005、A5052などが推奨されます。
- 見た目や装飾性が重視される用途には、A3003やA1050などの純アルミ系合金が向いています。
また、加工方法(押出、圧延、鋳造)や熱処理の可否も重要な選定基準となります。
4-3. A7N01の特定用途
A7N01は構造材として多くの分野で採用されており、特に次のような用途に適しています。
- 鉄道車両の車体構造(例:新幹線)
- 建築構造材や橋梁の床材などの大型構造物
- パネルやフレームなどの一般構造用材
- 溶接を多用する建設部材
強度と溶接性のバランスに優れ、過酷な条件下でも安定した性能を発揮します。
5. A7N01の機械的性質
5-1. A7N01の強度と硬度
A7N01は中~高強度の7XXX系アルミ合金で、T6処理を行うことで以下のような機械的性質を示します。
引張強さはおおよそ400〜450MPa、耐力は約300MPa前後に達し、強度と加工性のバランスが良好です。硬度はブリネル硬度で90〜120程度であり、構造用部材として安心して使用できる性能を有しています。
5-2. 耐食性と耐熱性
A7N01は、7XXX系の中では耐食性に優れており、屋外や海水にさらされる環境でも使用可能です。耐熱性については、おおよそ150℃程度までの使用が適していますが、長時間の高温使用では機械的性質が劣化する恐れがあるため、注意が必要です。
5-3. 他のアルミニウム合金との機械的性質の比較
A5052は中程度の強度で加工性と耐食性に優れ、A6061は強度と溶接性のバランスが良い汎用合金です。A7075は非常に高い強度を持つ一方、溶接性は劣ります。これに対してA7N01は、A5052やA6061よりも高い強度を持ちながら、A7075よりも溶接性が良好という特長があり、構造用材として非常に優れたバランスを誇ります。
6. アルミニウムの加工方法やポイント
6-1. アルミニウムの加工技術
アルミニウムには多様な加工方法が存在し、以下のようなものがあります。
- 切削加工(フライス加工、旋盤加工など)
- 曲げ加工(プレス加工、ロール曲げ)
- 溶接(TIG溶接、MIG溶接)
- 押出成形、圧延加工
- 表面処理(アルマイト、塗装)
製品の仕様や用途に応じて、これらを適切に組み合わせることが重要です。
6-2. A7N01の加工時の注意点
A7N01を加工する際には、以下の点に注意する必要があります。
- 加工硬化を起こしやすいため、切削条件は適切に調整する必要があります。
- 溶接部の強度が低下しやすいので、溶接後に必要に応じて熱処理や強度設計を行います。
- 曲げ加工では、急なRでの曲げは割れの原因になるため、曲げ半径に十分な余裕を持たせることが推奨されます。
6-3. 加工方法の選び方
加工方法の選定は、目的・ロット数・コスト・精度要求・形状などによって変わります。
- 少量試作や複雑形状には切削加工が適しています。
- シンプルな形状や大量生産品には押出やプレス加工が効率的です。
- 高精度や高強度が求められる構造部品では、熱処理や表面処理を組み合わせた複合加工が有効です。
用途に最適な加工方法を選定することで、品質とコストの両立が可能になります。
まとめ
A7N01は、優れた耐食性と強度を持つアルミニウム合金で、主に航空機や自動車の部品に使用されます。他のアルミ合金と比較して、特に高い強度対重量比を誇ります。熱処理が可能で、加工性にも優れているため、幅広い用途に適しています。この特性により、軽量で耐久性のある製品が求められる分野で重宝されています。
アルミニウムA1100の機械的性質と耐食性を徹底解説!
アルミニウム合金の一つであるA1100は、その優れた機械的性質と耐食性から、多くの産業で広く利用されています。しかし、「A1100の特性について詳しく知りたいが、どこから始めればいいのか分からない」と感じている方もいらっしゃるかもしれません。そこで今回は「A1100の機械的性質と耐食性を徹底解説!」というテーマで、知識を深めていきましょう。
この記事では、A1100の基本的な特性について詳しく説明し、なぜこの合金が様々な用途で重宝されているのかを解き明かします。また、機械的性質の具体例や耐食性のメカニズムについても掘り下げていきます。これからA1100を使用したプロジェクトを計画している方や、素材選びにお悩みの方にとって、必見の情報が満載です。
さあ、A1100の魅力を一緒に探求し、実践的な知識を身につけていきましょう!
1. A1100の特性と用途
1-1. A1100とは何か
A1100は1xxx系アルミニウム合金に属し、アルミ純度99%以上の純アルミです。軽量で加工性・耐食性・熱伝導性・電気伝導性に優れます。熱処理はできませんが、極めて柔らかく深絞り加工などに適しています。
1-2. A1100の主な用途
主に建築材や電気部材、食品容器、調理器具、装飾材、照明器具などに使用されます。特に耐食性や加工性を活かした用途が多く、電線や反射板、パッケージ用のホイルなどでも見られます。
1-3. 他のアルミ合金との違い
他の合金と比較すると、A1100は機械的強度が最も低い反面、加工のしやすさ、耐食性、コスト面で有利です。たとえば、A5052は強度・耐熱性に優れますが、加工性ではA1100のほうが勝ります。
2. A1100の機械的性質
2-1. A1100の強度
A1100の引張強さは約90~130 MPa、耐力は約30~60 MPaであり、機械的強度はアルミ合金の中でも最低レベルです。これは、精密部品や高応力がかからない箇所に適していることを意味します。
2-2. A1100の比重
比重は約2.71 g/cm³で、他のアルミニウム合金とほぼ同様の軽さを持ちます。
2-3. A1100のヤング率
ヤング率は約70 GPaです。これはしなやかで柔軟な材質であることを示しており、曲げ加工に向いています。
2-4. A1100の硬度
ブリネル硬度は約25~35と非常に低く、キズがつきやすい一方で、極めて加工しやすい特徴を持ちます。
3. A1100とA5052の比較
3-1. A1100とA5052の機械的性質の違い
A5052は引張強さ210~260 MPa、耐力130~200 MPa、硬度も約60~70と、A1100に比べて圧倒的に高い強度を持ちます。対してA1100は加工性、導電性、耐食性、コストで優れており、使用目的により選択が分かれます。
3-2. どちらを選ぶべきか
A1100は、加工性・導電性が重視される電気部品や食品容器などに適し、コストを抑えたい用途に最適です。一方、A5052は強度・耐久性が要求される構造部材や自動車・船舶関連のパーツに向いています。選定の際は、使用環境と必要な物性を考慮して判断します。
4. アルミ板の強度と機械的性質
4-1. アルミ板の強度の重要性
アルミ板の強度は、構造物や製品の安全性・耐久性を左右する重要な要素です。特に自動車や建築、輸送分野では、衝撃や荷重に耐えるために高強度が求められます。一方で、用途によっては柔軟性や成形性が重視されるケースもあり、バランスの取れた強度設計が求められます。
4-2. 機械的性質の理解
アルミ板の機械的性質には以下のような項目があります:
- 引張強さ:材料が引張荷重に耐える最大強度
- 耐力(降伏点):永久変形が始まる応力
- 延性:塑性変形に耐える性質(破断時の伸び率)
- 硬度:表面が傷やへこみに耐える強さ
- ヤング率:弾性変形のしやすさを示す値
これらの特性を理解することで、適切な合金を適切な用途に選定することが可能になります。
5. A1100の耐食性
5-1. A1100の耐食性の特性
A1100は純度が高いため、腐食に非常に強い性質を持っています。とくに大気中、淡水、海洋性環境、食品と接触する場面においても安定した耐食性能を示します。塩害や酸性雨の影響を受けにくく、外装材や配管、厨房設備などにも広く利用されています。
5-2. 耐食性を高める方法
A1100自体が高い耐食性を持ちますが、さらなる向上を図る方法として以下が挙げられます:
- アルマイト処理(陽極酸化処理):酸化皮膜を人工的に形成し、耐食性・耐摩耗性を向上
- 塗装やコーティング:ポリマー塗装やフッ素樹脂コートで保護
- 異種金属との接触防止:ガルバニック腐食を防ぐため、絶縁材を介在させる
これらの処理を行うことで、過酷な環境下でも長期間の使用が可能になります。
まとめ
A1100は、アルミニウムの合金であり、優れた機械的性質を持つことで知られています。軽量で加工性が高く、耐食性にも優れているため、さまざまな産業で使用されています。特に、耐腐食性が求められる環境でもその性能を発揮し、長寿命を実現します。
A6063の特徴と用途を徹底解説!他のアルミニウム合金との違いとは?
「A6063って何だろう?」「このアルミニウム合金の特性や使い道について知りたい!」と感じているあなたへ。本記事では、A6063の特徴や用途を詳しく解説し、他のアルミニウム合金との違いを明確にします。
A6063は、特に建材や自動車部品、さらには家庭用品に至るまで幅広い分野で利用されていますが、その秘密はどこにあるのでしょうか?軽量ながらも強度に優れ、加工性が高いこの合金は、多くのニーズに応えることができるのです。しかし、ただ特徴を知るだけでは不十分です。他のアルミニウム合金と比べて何が優れているのか、どういった場面で選ばれるべきなのか、詳しく理解することが重要です。
この記事では、A6063に関する基本的な情報を押さえつつ、具体的な用途や他の合金との比較を通じて、あなたがこの合金の魅力を存分に理解できるようお手伝いします。さあ、A6063の世界へ一緒に踏み出してみましょう!
1. A6063の特徴と用途
A6063は、特に建築や装飾分野で広く使用されるアルミニウム合金です。その優れた加工性と耐食性により、さまざまな用途に適しています。
1-1. A6063の基本的な特性
- 強度: A6063は比較的低強度の合金ですが、十分な耐久性を持っています。
- 耐食性: 高い耐食性を持ち、特に外部環境にさらされる用途に適しています。
- 加工性: 熱処理によって優れた加工性を発揮し、複雑な形状への加工も容易です。
- 成形性: 成形性が高く、押出し成形に適した合金です。
1-2. A6063の主な用途
- 建築: 窓枠、ドアフレーム、カーテンウォールなどの建築用部材に広く使用されます。
- 装飾: 高い表面仕上げが可能で、装飾的な目的での使用も多いです。
- 輸送機器: 軽量性が求められる部品に使用されることがあります。
- 電子機器: 熱伝導性が必要な機器の部品としても使用されます。
1-3. A6063の利点と欠点
- 利点:
- 高い耐食性と加工性。
- 成形性が良く、複雑な形状の部品にも適応。
- 美しい表面仕上げが可能。
- 欠点:
- 他のアルミニウム合金(例えばA7075)と比べると強度が劣る。
- 重い荷重を支えるような用途には適さない。
2. A6063と他のアルミニウムの違い
A6063は、特に加工性と表面仕上げの美しさが求められる用途に適しており、他のアルミニウム合金と比較しても独自の特性があります。
2-1. A6063とA6061の比較
- 強度: A6061はA6063よりも高い強度を持っています。A6061は構造材や機械部品に適している一方、A6063は軽量化が求められる装飾的な部品に適しています。
- 耐食性: A6063はA6061よりも若干高い耐食性を誇り、特に外部環境に強いです。
- 加工性: A6063はA6061よりも加工が容易で、複雑な形状を作るのに優れています。
2-2. A6063とA5052の違い
- 強度: A5052はA6063よりも強度が高く、特に耐圧性のある用途に向いています。一方、A6063は強度よりも加工性や装飾性が重視されます。
- 耐食性: 両者ともに高い耐食性を持っていますが、A5052は海洋環境や化学的環境において優れた耐久性を発揮します。
- 用途: A5052は主に防食が重要な用途(海洋環境など)に使用され、A6063は主に建築や装飾用途に使用されます。
2-3. A6063の特性が他のアルミニウム合金に与える影響
A6063の加工性や表面仕上げの美しさは、建築や装飾分野での利用を促進しており、A6061やA5052に比べて強度を求められない用途においてその特性が生きています。
3. 特定の用途に適したアルミ合金の選び方
用途に最適なアルミニウム合金を選ぶには、求められる特性(強度、耐食性、加工性など)を慎重に考慮する必要があります。
3-1. 建築用途におけるアルミ合金の選定
- A6063: 成形性が良く、表面仕上げが美しく、高い耐食性を持つため、建築の外装や装飾的部品に最適です。
- A5052: より高い耐食性が求められる場合(例えば海沿いの地域)にはA5052が選ばれます。
3-2. 自動車産業でのアルミ合金の利用
- A6061: 自動車部品において、強度と軽量化が重要な場合にはA6061が選ばれることが多いです。
- A7075: 高強度が求められる部品にはA7075が使用されます。
3-3. 電子機器に適したアルミ合金
A5052: 電子機器での使用には、A5052も耐腐食性や耐久性が求められる場合に適しています。
A6063: 良好な熱伝導性と加工性を持っており、電子機器のヒートシンクなどに使用されます。
4. 軽量化設計における材料選定
軽量化は現代の設計において重要な課題であり、特に輸送機器や建築、電子機器などの分野で求められています。アルミニウム合金はその優れた軽量性と強度から、軽量化設計において多く使用されています。
4-1. 軽量化の重要性
- 燃費向上: 自動車や航空機などの輸送機器で軽量化を行うことで、燃費効率を向上させることができます。
- 耐久性の向上: 軽量な部品は、全体的な耐久性にも寄与することがあり、特に長期間の使用が要求される場合に重要です。
- コスト削減: 軽量化により材料費や運搬コストを削減でき、全体的なコスト効率が向上します。
4-2. A6063を使用した軽量化の事例
A6063はその加工性と耐食性を活かして、軽量化を目的とした設計に多く使用されています。例えば、建築物の外装材や装飾部品では、軽量化しながらも強度を保つためにA6063が最適とされています。
- 自動車産業: A6063は軽量でありながら、耐食性が高いため、自動車の外装や内部部品に使用されています。
- 建築: 高層ビルの窓枠や外装において、A6063は軽量化と美しい仕上げが求められるため頻繁に使用されます。
4-3. 他のアルミ合金との比較による選定基準
- A6061: A6061はA6063に比べて高い強度を持っているため、より強度が必要な部品(例えば自動車部品や機械部品)には適していますが、加工性ではA6063に劣ります。
- A5052: A5052はA6063よりも強度が高く、特に海洋環境などでの使用に適していますが、加工性にはA6063に軍配が上がります。
5. A6061とA6063の選び方
A6061とA6063は似た特性を持ちながらも、用途において異なる強みを発揮します。選定にあたっては、求められる性能や加工性を考慮する必要があります。
5-1. A6061とA6063の特性比較
- 強度: A6061はA6063よりも高い強度を持ち、構造部材などの高強度が求められる用途に適しています。
- 加工性: A6063はA6061よりも優れた加工性を持ち、複雑な形状や美しい表面仕上げが求められる用途に最適です。
- 耐食性: 両者ともに高い耐食性を有していますが、A6063のほうが一般的に耐食性に優れています。
5-2. 用途別の選択ガイド
- 高強度が必要な場合: A6061が適しています。特に、機械部品や構造材など、高い強度と耐久性が求められる用途に使用されます。
- 加工性と美しい仕上げが求められる場合: A6063が適しています。特に建築用途や装飾部品において、複雑な形状や美しい表面仕上げが必要な場合に最適です。
5-3. どちらを選ぶべきかの判断基準
加工性・外観重視: A6063は加工性が良く、美しい表面仕上げが可能であるため、建築や装飾的な用途に向いています。
強度重視: A6061は高い強度を持っているため、機械部品や負荷がかかる部品に最適です。
まとめ
A6063は、優れた加工性と耐食性を持つアルミニウム合金です。主に建築やインフラ、家具、電気機器の部品に使用されます。他の合金と比べて、押出成形が容易で、表面処理にも適しています。軽量で強度も高く、デザイン性にも優れた特性が特徴です。
A6061の優れた特性と選び方他のアルミニウム合金との違いとは?
「A6061というアルミニウム合金は、どんな特性を持っているのだろう?」と考えたことはありませんか?また、「さまざまな合金がある中で、A6061を選ぶべき理由は何だろう?」と疑問に思う方も多いことでしょう。この記事では、A6061の特徴や用途、さらに他のアルミニウム合金との違いについて詳しく解説していきます。
アルミニウム合金は、軽量で耐腐食性に優れ、さまざまな産業で利用されていますが、それぞれの合金には特有の特性があります。A6061は、その中でも特に人気のある合金の一つで、構造材や機械部品、さらには自転車や航空機の部品など、多岐にわたる用途で活躍しています。
本記事では、A6061の特性を明らかにし、他のアルミニウム合金と比較することで、選択のポイントや最適な活用法についての知識を深めていきます。これからの製品選びやプロジェクトにおいて、A6061の特性を理解することが、成功への第一歩となるでしょう。さあ、一緒にその魅力を探っていきましょう。
1. A6061の特徴と用途
A6061は、非常に人気のあるアルミニウム合金で、様々な産業で広く使用されています。軽量でありながら強度と耐食性に優れ、加工もしやすい特徴を持っています。
1-1. A6061の基本的な特性
- 合金種: 6xxx系(シリコンとマグネシウムの合金)
- 強度: 中程度の強度を持ちます。溶接性も良好で、成形性に優れています。
- 耐食性: 高い耐食性を誇り、海洋環境や化学環境に強い耐性があります。
- 用途: 主に建設業や輸送機器、機械部品などに使用されます。
1-2. A6061の主な用途
A6061は、様々な分野で活躍しています。以下の用途が代表的です。
- 建築材料: 建築業界では、特に構造材や窓枠、ドアの枠などで使用されます。
- 自動車・輸送機器: 軽量化が求められる自動車や航空機の部品としても利用されています。
- 機械部品: 複雑な形状が求められる機械部品にも適しています。
- スポーツ用品: 自転車のフレームなど、高強度で軽量な部品が求められる製品にも使用されます。
2. A6061の特徴と他のアルミニウム合金の違い
A6061は多用途に対応可能な優れた特性を持っていますが、他のアルミニウム合金と比較した場合、いくつかの顕著な違いがあります。
2-1. A6061とA5052の比較
- 強度: A5052は耐食性に優れますが、A6061の方が強度が高いです。特に、A6061は溶接後でも強度を維持します。
- 加工性: A6061は加工しやすく、特に機械加工に優れています。A5052は、加工性も良好ですが、強度や耐食性ではA6061が上回ります。
- 用途: A5052は主に海洋環境や化学プラントでの使用に最適です。一方、A6061は機械部品や構造材、輸送機器などに広く使用されます。
2-2. A6061とA7075の比較
- 強度: A7075は非常に高い強度を誇りますが、A6061はその強度が中程度で、A7075に劣ります。
- 耐食性: A6061はA7075よりも優れた耐食性を持っています。特にA7075は海水環境などでは腐食しやすくなります。
- 用途: A7075は主に航空機や高強度が求められる部品に使用されるのに対し、A6061は一般的な構造部材や機械部品に適しています。
3. A6061の機械加工における利点と欠点
A6061はその優れた加工性により、機械加工において非常に扱いやすい合金です。しかし、いくつかの注意点もあります。
3-1. A6061の加工性
- 切削性: A6061は非常に優れた切削性を持ち、機械加工が比較的容易です。
- 溶接性: 溶接性も良好で、特にT6熱処理後でも溶接を行うことができます。
- 成形性: 軽い形状の部品の成形が容易で、精度の高い部品の加工が可能です。
3-2. A6061の加工における注意点
腐食のリスク: 高温や湿気の多い環境では、A6061が腐食する可能性があるため、表面処理やコーティングが重要です。
熱処理: A6061は熱処理を施すことで強度が向上しますが、溶接後に再熱処理が必要な場合があります。特に溶接部分は強度が低くなるため注意が必要です。
4. A6061のコストパフォーマンス
A6061は、その特性とバランスの取れた性能からコストパフォーマンスに優れたアルミニウム合金として広く評価されています。
4-1. A6061の価格と市場動向
- 価格: A6061は市場で非常に広く取引されており、比較的安価な価格帯に位置します。そのため、コストパフォーマンスを重視する場合、A6061は非常に魅力的な選択肢です。
- 市場動向: A6061の需要は、特に建設業や輸送機器、機械部品において高いです。これにより価格は安定していますが、鋼材やその他の素材の価格変動によって影響を受ける可能性もあります。
4-2. 他のアルミニウム合金とのコスト比較
- A5052との比較: A5052は耐食性に優れていますが、強度においてはA6061が優れています。そのため、強度を求める用途にはA6061がコストパフォーマンスに優れた選択です。一方で、A5052はコストが若干高めとなる場合があります。
- A7075との比較: A7075は非常に高強度ですが、価格も高いため、強度が求められる特殊な用途以外では、A6061が経済的な選択となります。A7075の使用は主に航空宇宙分野や軍事用途に限られることが多く、一般的な用途ではA6061の方がコスト効率が良いです。
5. 特定の用途に最適なアルミニウム合金の選び方
用途によっては、他のアルミニウム合金の方が適している場合もありますが、A6061は非常に汎用性が高いため、幅広い用途に対応しています。
5-1. A6061が適している用途
- 構造材: A6061は軽量で強度が中程度のため、建設業の構造材や建材に広く使用されています。
- 輸送機器: 自動車や航空機の部品に使用されることが多く、耐食性や加工性の良さから、耐久性のある部品として適しています。
- 機械部品: 高精度が要求される機械部品にも適しており、特に加工性が求められる部品に最適です。
5-2. 他のアルミニウム合金の選択肢
- A5052: 耐食性が特に優れているため、海洋環境や化学プラントの部品に適しています。
- A7075: 高強度を必要とする航空機や軍事用途にはA7075が適していますが、コスト面ではA6061に比べて高くなる場合があります。
- A2011: より高い切削性を求める場合、A2011も適した選択肢です。
6. A6061の物性について
A6061は機械的性質において非常に優れたバランスを持つため、多くの産業で使われています。
6-1. A6061の比重と融点
- 比重: 約2.70 g/cm³
- 融点: 約660°C (鋳造温度において変動あり)
6-2. A6061の切削性と機械的特性
機械的特性: 引張強さや耐久性が高く、広範囲な使用に適しています。特にT6熱処理を施した場合の強度は高く、構造部材としての利用が推奨されます。
切削性: A6061は非常に良好な切削性を持っており、精密加工が可能です。そのため、複雑な形状の部品加工にも対応できます。
まとめ
A6061は、優れた耐腐食性と加工性を持つアルミニウム合金です。軽量で強度も高く、溶接性に優れています。他の合金と比べて、機械的特性がバランス良く、さまざまな用途に適しています。選ぶ際は、使用目的や環境条件を考慮することが重要です。
【A5083アルミニウムの特性と他の種類との違いとは?】
「A5083アルミニウムって、どんな特性があるのだろう?」と疑問に思ったことはありませんか?アルミニウムは軽量かつ強度が高い素材として、さまざまな分野で利用されていますが、特にA5083はその独自の特性によって注目されています。
このガイドでは、A5083アルミニウムの特徴や具体的な用途、さらには他のアルミニウム合金との違いについて詳しく解説します。これからA5083を利用したいと考えている方や、その特性を深く理解したい方には必見の内容です。例えば、A5083が持つ耐食性や溶接性、どのような環境で特に効果を発揮するのかなど、実際の利用例を交えながらお話ししていきます。
もしあなたがアルミニウムの特性をより深く理解し、活用方法を見つけたいと考えているなら、ぜひ最後までお読みください。A5083の魅力を知ることで、あなたのプロジェクトやビジネスに新たな可能性をもたらすことでしょう。
1. A5083 特徴 用途 他のアルミニウム 違い
A5083は高い耐食性を持ち、特に海洋環境や化学的に厳しい条件下で使用されるアルミニウム合金です。航空機や船舶などで広く使用されます。
1-1. A5083の基本特性
- 耐食性:A5083は非常に優れた耐食性を持ち、特に海水や化学薬品に対して強い抵抗力を示します。これにより、船舶、海洋設備、化学プラントなどで重宝されています。
- 強度:引張強度は中程度で、特に海洋環境や水辺の構造物に適しています。高い耐食性が必要でありながらも、一定の強度を維持する特性を持っています。
- 加工性:A5083は加工が比較的容易であり、溶接性にも優れています。特に溶接後も強度が保たれるため、複雑な形状の部品に利用されます。
1-2. A5083の主な用途
- 海洋構造物:船舶の船体や海洋施設、油田の設備に広く使用されています。
- 化学プラント:腐食性の強い化学物質を扱う施設でも使用され、その耐食性が重要な役割を果たします。
- 車両・機械部品:特に高強度と耐食性が求められる部品で使用されます。
1-3. A5052との比較:強度と耐食性の違い
- 強度:A5052はA5083よりもやや低い強度を持ちますが、軽量で柔軟性があります。A5083は高い強度を誇るため、より過酷な条件下でも耐久性が高いです。
- 耐食性:A5083はA5052に比べて優れた耐食性を持ち、海水や化学薬品に強い抵抗力があります。そのため、海洋環境や化学プラントなどで使用される場合は、A5083が優れた選択となります。
1-4. A5083と他のアルミニウム合金の違い
- A5083とA5056:A5056は耐食性が非常に高い合金ですが、A5083の方がさらに強度が高く、極端な環境でも使用可能です。A5056は加工性が良好であり、A5083に比べて耐食性に特化していますが、強度が重視される場合はA5083が選ばれます。
- A5083とA7075:A7075は非常に高い強度を持つ合金ですが、A5083ほど耐食性に優れていません。A7075は航空機などの強度が最優先される用途に適しており、A5083はより厳しい環境での使用に適しています。
2. A5083の加工技術
A5083は、海洋や化学プラントでの使用に適した高い耐食性を持つアルミニウム合金です。そのため、加工方法にも特有の注意点があります。
2-1. A5083の切削加工のポイント
- 工具の選定:A5083は比較的加工がしやすい合金ですが、耐食性を維持するためには適切な工具選びが重要です。硬度が比較的高いので、耐摩耗性のある工具を使用することが推奨されます。
- 切削速度:A5083は切削加工中に熱を持ちやすいため、適切な冷却を行いながら加工を進めることが重要です。過熱を防ぐために、低めの切削速度を使用することが有効です。
- 切削液の使用:切削液を適切に使用し、加工中の温度上昇を抑えることが重要です。これにより、工具の寿命を延ばすとともに、加工精度を保つことができます。
2-2. 加工時の注意点と推奨方法
接合技術:A5083は溶接性が良好であり、溶接後の機械的性質の低下が少ないため、複雑な構造物の組み立てに利用することができます。溶接後は、接合部の強度を確保するために適切な検査を行うことが重要です。
熱処理後の注意:A5083は溶接後でも強度が保たれますが、熱処理後に変形が生じやすい場合があります。適切な冷却方法を取り入れて、加工後の歪みを最小限に抑えることが必要です。
表面処理:A5083は表面処理を施すことで、さらに耐食性を向上させることができます。特に海洋環境で使用する場合、アルマイト処理などの表面保護処理を行うことが推奨されます。
3. アルミニウム合金の種類と用途
アルミニウム合金は、その成分や特性によって多くの種類があり、さまざまな用途に使用されています。それぞれの合金は、特定の要求に応じた特性を持っており、選定には目的に応じた理解が必要です。
3-1. アルミニウム合金の分類
アルミニウム合金は主に次の4つのカテゴリーに分類されます:
- 1xxx系 (純アルミニウム):99%以上の純度を持ち、非常に良好な耐食性と加工性がありますが、強度は低めです。主に電気・電子機器や食品包装などに使用されます。
- 2xxx系 (銅系アルミニウム合金):強度が高く、航空機や軍事用途で使用されることが多いですが、耐食性は比較的低いです。
- 5xxx系 (マグネシウム系アルミニウム合金):優れた耐食性を持ち、特に海洋環境に適しています。強度も高めで、船舶や化学プラントで広く使用されています。
- 6xxx系 (シリコンとマグネシウムの合金):良好な耐食性と加工性を持ち、建築材や一般的な工業用途に広く使用されます。
3-2. 各合金の特性と用途
- 1xxx系:優れた耐食性と優れた加工性を持ちますが、強度は低く、主に電気機器、包装材料、家庭用品に使用されます。
- 2xxx系:非常に高い強度を持ち、航空機や航空宇宙産業で多く使われますが、耐食性が低く、特に腐食環境には不向きです。
- 5xxx系:特に海水環境や化学プラントでの使用に適しており、耐食性に優れた特性を持っています。船舶、オフショア構造物、化学設備などで利用されます。
- 6xxx系:良好な耐食性と中程度の強度を持ち、建築物や機械部品、輸送機器に利用されています。
4. A5052とA5083の選び方
A5052とA5083は、どちらも高い耐食性を持つアルミニウム合金ですが、使用目的に応じて選定基準が異なります。それぞれの特性に基づいて適切な選択をすることが重要です。
4-1. 使用目的に応じた選択基準
- A5052:耐食性が非常に高く、軽量化が求められる環境に最適です。強度は中程度で、主に海洋、化学プラント、車両部品、屋外構造物などで使用されます。加工性も良好で、機械的な加工が容易です。
- A5083:A5052よりも高い強度と耐食性を持ち、特に過酷な環境に耐える能力が求められる用途に適しています。海水や化学薬品に長期間晒されるような状況で使用され、船舶、オフショア構造物、航空機などで重視されます。
4-2. 具体的な事例紹介
A5052の事例:
海洋構造物:海洋環境で使用される船舶や浮き桟橋などの部品にA5052が使用されています。強度と耐食性をバランスよく備えており、設計や加工がしやすいことから広く採用されています。
自動車部品:自動車の外装部品などでも、軽量化と耐食性を両立させるためにA5052が選ばれることがあります。
A5083の事例:
船舶の船体構造:A5083は特に耐食性と強度が求められる船舶の船体に使用されます。船の外壁や亜鉛コーティングが施された部品に使用されることで、長期的な耐久性が保証されます。
オフショア施設:海洋環境で使用されるオフショア構造物では、A5083が高い強度と耐食性を提供し、厳しい条件でも安定した性能を発揮します。
まとめ
A5083アルミニウムは、高い耐食性と優れた機械的特性を持つ合金です。特に海洋環境や化学プラントでの使用に適しています。他のアルミニウム合金と比べて、強度と耐久性が優れており、溶接性も良好です。軽量で加工しやすく、さまざまな産業で広く利用されています。
比較してわかる!アルミニウムA7204と他素材の強度・比重・硬度の違い
「A7204とは一体何だろう?」「他の素材とどのように違うのか知りたい…」そんな疑問を抱えているあなたに捧げる、A7204の完全ガイドがここにあります。
この文章では、A7204の特性を徹底的に解説し、強度や比重、ヤング率、さらには硬度といった重要な指標を他の素材と比較しながらわかりやすくお伝えします。工業や製造業での使用が期待されるA7204は、その特性を知ることで、あなたの選択肢を広げる重要な材料となることでしょう。
もし、あなたが以下のようなことに興味を持っているのなら、ぜひこのまま読み進めてください。
- A7204の基本的な特性とは?
- 他の金属や合金と比べて、A7204の強度はどのくらいなのか?
- どの素材が特定の用途に適しているのかを知りたい!
あなたの疑問にお答えし、A7204についての理解を深めるための情報をたっぷりと提供します。この記事を通じて、素材選びの新たな知見を得て、より良い判断を下せるようになることを目指します。さあ、一緒にA7204の魅力を探求していきましょう!
1. A7204 とは 強度 比重 ヤング率 硬度の概要
A7204合金は、アルミニウム合金の一種であり、特に高強度を求められる用途に適しています。強度、比重、ヤング率、硬度などの機械的特性は、適切な材料選定において非常に重要な役割を果たします。
1-1. A7204合金の基本情報
A7204は、アルミニウムと銅を主成分とする合金で、高強度を持つことから航空機やスポーツ機器、車両の構造材などで多く使用されます。軽量で高い耐久性を兼ね備えており、特に負荷がかかる部分に最適です。
1-2. A7204合金の用途
A7204合金は、高強度と耐食性が求められる構造部材に使用されます。主な用途には、航空機の部品、車両のシャーシ、スポーツ用品などが含まれます。これらの分野では、軽量化と高強度のバランスが求められるため、A7204が適しています。
2. A7204 とは 強度 比重 ヤング率 硬度の機械的特性
A7204合金の強度、比重、ヤング率、硬度は、主に使用環境や負荷のかかる用途に対応するために調整されています。これらの特性を理解することは、適切な材料選定において欠かせません。
2-1. 強度と硬度の関係
A7204合金は、高い強度を持つと同時に、適度な硬度を維持しています。強度が高ければ、外部からの力に対する耐性も強くなり、硬度が高いと加工性が悪化することがあります。A7204では、強度と硬度がバランスよく設計されており、耐摩耗性と加工性を両立させています。
2-2. ヤング率と剛性の違い
ヤング率は、材料が変形する際の剛性を示す指標です。A7204合金は、比較的高いヤング率を持っており、これにより外力を受けても変形しにくい特性を持っています。ヤング率が高いほど、材料は剛性が高いとされますが、これは必ずしも強度の高さを意味するわけではありません。剛性と強度は関連性があるものの、別の特性であるため、用途に応じたバランスが求められます。
2-3. 比重の重要性
比重は、材料の密度を示す値で、軽量性が求められる分野では非常に重要です。A7204合金の比重は比較的軽いため、重量制限のある構造材として使用されることが多いです。比重が低いと、軽量化が可能になり、航空機や自動車の燃費向上にも寄与します。
3. A7204 とは 強度 比重 ヤング率 硬度の選定基準
A7204合金を選定する際は、強度、比重、ヤング率、硬度のバランスを考慮することが重要です。適切な合金の選定は、用途に合わせた性能発揮を確実にするために必要不可欠です。
3-1. アルミニウム合金の選定基準
アルミニウム合金を選定する際の基準は、以下の要素に基づいています:
- 強度:高い引張強度と耐久性が必要な場合、高強度合金(例:A7204、A7075)を選びます。
- 比重:軽量性が求められる場合、比重の低い合金(例:A6061)を選択します。
- 硬度:耐摩耗性や耐腐食性が重要な場合、硬度の高い合金(例:A7204)を選びます。
- 加工性:加工のしやすさや切削性を重視する場合は、比較的軟らかい合金(例:A6061)を選びます。
選定基準は、使用環境(温度、腐食性、荷重など)や要求性能に基づいて、最適な合金を選定するために重要です。
3-2. 切削性の良い材料の特徴
切削性の良い材料には、以下の特徴があります:
- 適度な硬度:硬すぎると工具が摩耗しやすく、柔らかすぎると加工が難しくなります。適度な硬度を持つ合金が最適です。
- 均一な組織:金属の結晶構造が均一であることが、加工時の安定性に寄与します。
- 良好な熱伝導性:熱が効率的に発散されるため、過熱による工具の劣化を防ぎます。
- 低い引張強度:引張強度が低いと、切削中の応力が少なく、加工が容易になります。
これらの要素を踏まえて、切削性が良い材料を選定することが重要です。
4. A7204 とは 強度 比重 ヤング率 硬度と他のアルミ合金の比較
A7204合金は他のアルミ合金と比較して、特に高い強度を持っていますが、それぞれの合金には異なる特徴があります。用途に応じて、最適なアルミ合金を選ぶための比較が必要です。
4-1. A7204とA6061の特性比較
A7204は強度が高いため、特に航空機や車両の構造部材に適しています。一方、A6061は加工性が良く、軽量であり、幅広い用途に使われますが、強度はA7204ほど高くはありません。
4-2. A7204とA7075の違い
A7075はA7204よりも強度がさらに高く、特に高強度を必要とする航空機や軍事用途に適しています。A7204も高強度でありますが、A7075に比べると若干低い強度で、コストや加工性を重視する場面において選ばれることが多いです。
まとめ
A7204はアルミニウム合金の一種で、軽量ながら高強度を誇ります。他の素材と比較すると、鋼鉄よりも比重が軽く、加工性に優れています。硬度も高く、耐食性があるため、航空機や自動車部品に最適です。これに対し、ステンレス鋼は耐腐食性が高いものの、重量が重く、加工が難しい点があります。A7204は、強度と軽さを兼ね備えた優れた選択肢です。
アルミニウムA7N01の特性を徹底解説!強度・比重・ヤング率・硬度の全貌とは
「A7N01って何だろう?その特性を詳しく知りたい!」と思っている方は多いのではないでしょうか。この合金は、航空機や構造物などの重要な材料として非常に注目されています。しかし、具体的にどのような特性を持ち、どのように活用されているのかは、あまり知られていないかもしれません。
この記事では、A7N01の基本情報から、強度、比重、ヤング率、硬度といった重要な物理特性まで、詳しく解説します。A7N01を理解することで、設計や製造における選択肢が広がります。そして、あなたのプロジェクトに最適な材料選びに役立つことでしょう。これから一緒に、A7N01の世界を探求していきましょう!
1. A7N01 とは 強度 比重 ヤング率 硬度の基本知識
A7N01はアルミニウム合金の一種で、特定の強度、比重、ヤング率、硬度を持つ材料です。これらの機械的特性を理解することは、適切な用途や加工方法を選定する上で非常に重要です。
1-1. A7N01の概要
A7N01は、主に耐食性と強度を兼ね備えたアルミニウム合金です。マグネシウムやシリコンを主要な成分としており、軽量でありながら高い強度を誇ります。航空機、車両部品など、特に軽量化が求められる構造材として使用されます。
1-2. A7N01の強度と比重
- 強度: A7N01は高い引張強度を有しており、引張強度は通常300~400 MPa程度です。これにより、構造材や部品としての信頼性が高いです。
- 比重: 比重は約2.7 g/cm³で、アルミニウム合金としては一般的な値です。軽量であり、航空機や車両などの軽量化に寄与します。
1-3. A7N01のヤング率と硬度
- ヤング率: A7N01のヤング率は約70 GPaです。これにより、力が加わった際の変形のしにくさ(剛性)が示されます。
- 硬度: A7N01の硬度は約90~110 HB(ブリネル硬度)で、他のアルミニウム合金と比較しても中程度の硬さを持ちます。
2. A7N01の機械的性質について
A7N01はその強度や硬度だけでなく、引張強度、圧縮強度、耐久性においても重要な特性を持っています。
2-1. 引張強度と圧縮強度
- 引張強度: A7N01は優れた引張強度を持ち、荷重が加わったときの破壊を防ぎます。引張強度が高いため、構造用部材として広く使われています。
- 圧縮強度: 圧縮強度は引張強度に近い値であり、圧縮荷重にも強い耐性を持っています。この特性により、圧縮される部材にも適しています。
2-2. 耐久性と疲労強度
A7N01は高い疲労強度を持っており、繰り返し荷重に対しても良好な耐久性を示します。これにより、長期間の使用においても信頼性を発揮し、航空機や車両などの高強度が求められる部品に適しています。
2-3. A7N01の硬度測定
A7N01の硬度測定は、ブリネル硬度計やロックウェル硬度計を用いて行われます。硬度は加工性に影響を与える重要なパラメータであり、硬すぎると加工が困難になるため、適切な硬度設定が必要です。
3. アルミニウム合金の選び方
アルミニウム合金を選定する際には、強度、耐食性、加工性、コストなどを総合的に考慮する必要があります。A7N01はそのバランスの取れた特性から多くの分野で利用されています。
3-1. 用途に応じた合金の選定
用途に応じたアルミニウム合金の選定は、強度、耐食性、熱伝導性、成形性、コストなどを基に行われます。A7N01は特に強度が求められる構造材に適しており、耐食性も優れているため、外部環境での使用に適しています。
3-2. A7N01と他のアルミニウム合金の比較
A7N01は、他のアルミニウム合金と比較して強度が高く、耐食性にも優れています。例えば、A6063やA5052は加工性が良いですが、A7N01の方が高強度を誇ります。したがって、構造部材や負荷がかかる部品にはA7N01が適しています。
3-3. 強度と比重のバランス
A7N01は強度と比重のバランスが良好で、軽量でありながら高強度を維持します。このため、軽量化が求められるが強度も必要とされる用途に最適です。例えば、航空機や車両部品、スポーツ用品などで活用されます。
4. 剛性と強度の違いを理解する
剛性と強度は、材料や構造物の機械的特性を表す重要な概念ですが、両者は異なる意味を持ちます。ここでは、それぞれの概念を説明し、その関係を理解します。
4-1. 剛性とは何か
剛性とは、物体が外部からの力に対してどれだけ変形しにくいかを示す特性です。剛性が高い材料は、外力が加わった際に変形しにくく、逆に剛性が低い材料は、同じ力でも大きく変形します。剛性は、材料のヤング率や寸法に依存します。
4-2. 強度とは何か
強度は、材料が破壊されることなく耐えられる最大の応力(力/面積)を示します。これには、引張強度、圧縮強度、曲げ強度などが含まれます。強度が高い材料は、大きな力を受けても破壊されにくいという特性を持ちます。
4-3. 剛性と強度の関係
剛性と強度は密接に関連していますが、異なる概念です。剛性は材料の変形のしにくさに関係し、強度は材料が破壊される前に耐えられる力に関係します。例えば、強度が高くても剛性が低い場合、材料は力を受けても大きく変形してしまうことがあります。逆に、強度が低くても剛性が高い材料は、変形はしにくいが、破壊には至る場合もあります。
5. A6063アルミニウム合金の特性
A6063は、アルミニウム合金の中でも特に加工性や耐食性に優れた材料で、さまざまな用途に使用されています。
5-1. A6063の基本特性
A6063は主にマグネシウムとシリコンを含むアルミニウム合金で、優れた耐食性と良好な加工性を持っています。主な特性は以下の通りです:
- 強度: 中程度の強度を持ち、軽量かつ強度を求める用途に適しています。
- 耐食性: 海水や湿気の多い環境でも腐食に強く、建材や外装部品に使用されます。
- 加工性: 成形性が良好で、押出成形や溶接に優れています。
5-2. A6063の用途と利点
A6063は主に以下の用途に使用されます:
- 建築材料: 窓枠、ドア、サッシ、カーテンウォールなど。
- 自動車部品: 軽量化と強度が要求される車両部品。
- 電子機器: 熱伝導性や耐食性が求められるケースや部品。
その利点は、耐食性が高く、軽量でありながら強度を持つことです。また、加工が容易なため、複雑な形状や設計にも対応できます。
5-3. A6063とA7N01の比較
A6063とA7N01は異なる特性を持ち、用途に応じた選択が求められます。A6063は優れた加工性と耐食性を持ちますが、A7N01はより高い強度を誇ります。A7N01は、強度が要求される航空機や自動車部品に適しており、A6063は耐食性と加工性を重視する建築部材や外装部品に適しています。
6. A7003の特性や用途について
A7003は高強度を有するアルミニウム合金で、特に構造部品に適しています。その特性と用途について詳しく説明します。
6-1. A7003の機械的性質
A7003は高強度のアルミニウム合金であり、引張強度が高く、構造的な用途に適しています。また、耐腐食性にも優れており、過酷な環境で使用されることが多いです。A7003の特性は以下の通り:
- 引張強度: 高い
- 耐食性: 優れている
- 加工性: 中程度であり、強度が高いため加工が少し難しくなることもあります。
6-2. A7003の用途と市場での位置付け
A7003は、主に自動車、航空機、建設機械など、高強度が要求される分野で使用されます。特に構造部材やフレーム部分などの部品に適しており、軽量化と強度を兼ね備えた部品として活用されています。
6-3. A7003とA7N01の違い
A7003とA7N01はどちらも高強度アルミニウム合金ですが、A7003はより高い引張強度と耐久性を持っています。A7N01は加工性や耐食性が優れており、比較的軽量な部品に使用されますが、A7003はより重い負荷がかかる環境での使用に適しています。
まとめ
A7N01は、アルミニウム合金の一種で、優れた強度と軽量性を兼ね備えています。比重は約2.7g/cm³で、ヤング率は約70GPa。硬度はHBで約100-120と、加工性にも優れています。この合金は、航空機や自動車部品など、耐久性が求められる用途に最適です。
アルミニウムA1070の特性を知る!強度と比重、ヤング率、硬度の詳細ガイド
「A1070って何だろう?その特性や強度について知りたいけれど、どこから手を付ければいいのかわからない…」。そんなあなたのために、私たちは「A1070詳細ガイド」を作成しました。
この記事では次のようなことを知りたい方に向けてお届けします。
- A1070とは何か、その基本的な特性は?
- A1070の強度と比重、どのような特徴があるのか知りたい!
- ヤング率や硬度についての具体的な数値や説明を教えてほしい!
A1070は、さまざまな産業で使用される重要な合金の一つです。その特性を理解することで、より適切な用途を見極める助けとなるでしょう。本記事では、A1070の強度、比重、ヤング率、そして硬度について詳しく解説し、読み進めることでその魅力を存分に感じていただける内容をお届けします。これからA1070についての理解を深め、あなたの知識を広げていきましょう!
1. A1070 とは 強度 比重 ヤング率 硬度の概要
A1070は、主に純度の高いアルミニウム合金で、軽量かつ加工しやすい特性を持っています。ここでは、A1070の基本情報とその特性について詳しく説明します。
1-1. A1070の基本情報
A1070は、99.7%のアルミニウムを基にした合金で、純度の高いアルミニウム合金です。この合金は、加工性や耐食性が優れているため、特に装飾的な用途や精密部品に使用されます。
1-2. A1070の化学成分
A1070の化学成分は以下の通りです:
- アルミニウム (Al): 約99.7%
- 鉄 (Fe): 最大0.3%
- シリコン (Si): 最大0.1%
- 銅 (Cu): 最大0.05%
- マンガン (Mn): 最大0.03%
この合金は非常に高いアルミニウム純度を持ち、少量の他の元素が含まれています。
2. A1070 とは 強度 比重 ヤング率 硬度の機械的性質
A1070の機械的性質は、主にその強度、比重、ヤング率、硬度に関連しています。以下では、これらの特性について詳細に説明します。
2-1. A1070の強度について
A1070の引張強度は約 70–90 MPa で、他のアルミニウム合金と比較して強度は比較的低めですが、軽量で優れた加工性を持ちます。強度よりも加工の容易さや耐食性が重要な用途に向いています。
2-2. A1070の比重とその影響
A1070の比重は約 2.70 で、アルミニウム合金の中では標準的な値です。軽量であり、軽量構造が求められる用途に最適です。比重が低いため、他の重い材料と比較して運搬や使用時に便利です。
2-3. A1070のヤング率の特性
A1070のヤング率は約 69 GPa で、アルミニウム合金としては標準的な値です。この値は、材料の弾性挙動に関連し、引っ張りや圧縮の際の変形の程度を示します。
2-4. A1070の硬度とその測定方法
A1070のロックウェル硬度は約 35 HRB で、柔軟性と成形性が高いことを示しています。硬度は、材料の耐摩耗性や衝撃への耐性を示す指標であり、A1070は加工しやすい一方で摩耗には比較的弱いとされます。
3. A1070 とは 強度 比重 ヤング率 硬度とアルミニウムの特性
3-1. アルミニウムの一般的な特性
アルミニウムは、軽量で耐食性が高いという特性があります。腐食に強く、酸化被膜により自然に保護されるため、耐久性が高いです。さらに、良好な熱伝導性と電気伝導性を持っています。
3-2. A1070の用途と利点
A1070は以下の用途に適しています:
- 装飾用部品: 高い光沢感と美しい外観を持ち、エクステリアや装飾的な用途に最適です。
- 精密部品: 加工性が良いため、精密な機械部品や工業用部品に使用されます。
- 耐食性が重要な用途: 高い耐食性を持つため、外部環境にさらされる部品にも利用されます。
- 電気・電子機器: 良好な電気伝導性を活かし、電子機器や電気部品にも利用されています。
A1070は、高い純度のアルミニウムが求められる軽量かつ加工しやすい用途に非常に有用な合金です。
4. A1070 とは 強度 比重 ヤング率 硬度と他のアルミ合金との比較
A1070は、主に高い純度を持つアルミニウム合金ですが、他のアルミ合金との比較において、特性に違いがあります。以下では、A1070と他のアルミ合金との比較を行います。
4-1. A5052との比較
A5052は、A1070と比較して、より高い強度と優れた耐食性を持っています。A5052は合金成分にマグネシウムを含んでおり、腐食環境での耐性が高いです。以下の特性比較を見てみましょう:
- 強度: A1070は約70–90 MPaの引張強度に対し、A5052は約210–230 MPaで、A5052の方が強度が高い。
- 比重: A1070とA5052の比重はほぼ同じ(A1070: 2.70、A5052: 2.68)。
- ヤング率: A1070のヤング率は69 GPaに対し、A5052は71 GPaと、A5052が少し高い。
- 硬度: A1070はロックウェル硬度35 HRBに対し、A5052は50–65 HRBと、A5052が硬い。
A5052は、強度や耐食性が重要な用途に優れており、A1070は主に加工性や軽さが求められる用途に向いています。
4-2. 他のアルミ合金との違い
他のアルミ合金と比較した場合、A1070は主にその高い純度が特徴であり、強度や硬度が他の合金より低い傾向があります。以下の合金との比較を簡単に見てみましょう:
- A6061との比較: A6061はマグネシウムとシリコンを含む合金で、強度が高く、成形性も良好ですが、A1070の方が純度が高く、より柔らかく加工しやすいです。A6061は構造部品や航空機部品に使われることが多いです。
- A7075との比較: A7075は非常に高い強度を持ち、航空機や軍事用途に利用されます。A1070はそれに比べて強度が低く、耐食性や加工性が重視される場面で適しています。
A1070は、強度が重視されない場合や高純度のアルミニウムが必要な用途に最適です。
5. A1070 とは 強度 比重 ヤング率 硬度に基づくアルミ合金の選び方
アルミ合金の選定においては、強度、比重、ヤング率、硬度などの特性に基づいて最適な合金を選ぶことが重要です。
5-1. 適切な用途の選定
A1070は、以下のような用途に適しています:
- 装飾用途: 高い純度と光沢感を活かし、装飾部品や外装パーツに使用されます。
- 精密部品: 加工性が良いため、精密部品や細かい加工が求められる部品に適しています。
- 軽量構造: 軽量化が重要な構造物や機械部品にも使用されます。
A1070は、強度よりも加工性や耐食性を重視する用途に向いています。
5-2. 材料選定のポイント
アルミ合金を選定する際には、以下のポイントを考慮します:
- 強度: 構造部品や高荷重がかかる部品には、A7075やA6061など、高強度のアルミ合金を選ぶべきです。
- 耐食性: 耐食性が重要な場合は、A5052やA6061のような耐食性に優れた合金を選びます。
- 加工性: 加工が重要な場合は、A1070やA1100のような純度の高い合金が適しています。
選定基準は、用途によって異なるため、特性に合わせた材料選びが重要です。
まとめ
A1070は、アルミニウム合金の一種で、優れた強度と軽量性が特徴です。比重は約2.7g/cm³で、ヤング率は約70GPa、硬度はHB 60程度です。この合金は、耐食性にも優れ、航空機や自動車部品に広く利用されています。特性を理解することで、適切な用途に活用できます。