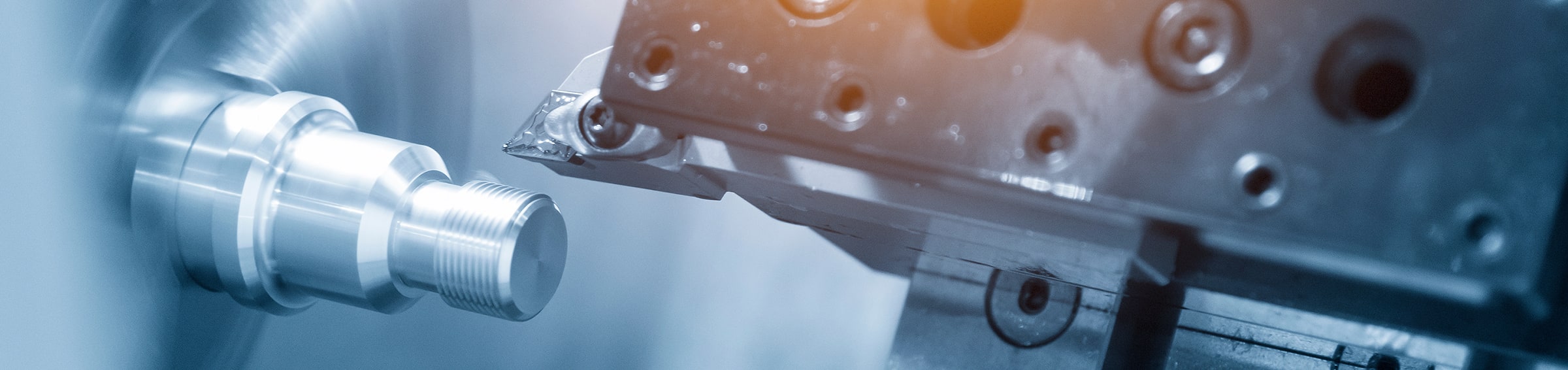
コラム column
アルミニウム加工の極意!旋盤を使った外径加工の基本
アルミニウム加工と言えば、多くの工業製品や日常用品に幅広く使われている素材です。その加工方法の一つに旋盤を使った外径加工があります。アルミニウム加工の極意を学ぶことで、製品の精度や品質を高めることができるでしょう。本記事では、外径加工の基本となる手法やポイントについて紹介します。アルミニウム加工における旋盤の活用方法を知り、未来に向けてスキルアップを目指す方々にとって、貴重な情報となることでしょう。
アルミニウム旋盤加工入門
アルミニウム加工とは
アルミニウム加工とは、アルミニウムを使って様々な製品や部品を作る加工技術のことです。その中でも、旋盤を使った外径加工は重要な基本技術の一つです。旋盤を使用することで、アルミニウム材料を回転させながら切削加工を行い、所定の形状や寸法に加工することができます。
外径加工は、アルミニウム製品の外側の形状を作る際に用いられます。例えば、自動車のホイールやエンジン部品など、さまざまな製品に外径加工が必要となります。この技術を使うことで、精密な加工が可能となり、製品の品質向上や効率化が図られます。
アルミニウム加工において外径加工の基本を理解し、正しく行うことは製品の品質や性能向上に繋がります。技術の習得と継続的な研鑽が重要です。
旋盤加工の基礎知識
アルミニウム加工において、旋盤を使った外径加工は非常に重要です。外径加工は、アルミニウムの円形部分を削る加工方法であり、製品の精度や品質を決定します。旋盤を使用することで、素材を回転させながら切削することができ、高い精度で加工が可能となります。
例えば、自動車のエンジン部品や航空機の構造部品など、さまざまな産業でアルミニウム製品の外径加工が求められています。これらの製品は高い強度と精度が求められるため、外径加工は欠かせない工程となっています。
外径加工を通じて、アルミニウム製品の性能や耐久性を向上させることができるため、この技術の習得は産業界で非常に重要です。正確な外径加工を行うことで、製品の価値を高めることができ、顧客からの信頼を得ることができます。
旋盤の種類と特徴
旋盤の種類と特徴を理解することは、アルミニウム加工における基本です。旋盤は、加工物の外径加工を行う際に重要な役割を果たします。主な旋盤の種類には、マニュアル旋盤とコンピュータ数値制御(CNC)旋盤があります。マニュアル旋盤は、オペレータが手動で操作し、加工を行うタイプです。一方、CNC旋盤はコンピュータによって制御され、高度な精度で素材を加工することができます。
例えば、アルミニウム製のパーツを加工する際、CNC旋盤は複雑な形状や細かい加工が必要な場合に効果的です。それに対し、マニュアル旋盤は簡単な形状や小規模な加工に適しています。
外径加工を行う際、旋盤の種類を適切に選択することが重要です。素材の特性や加工の精度要件に合わせて、最適な旋盤を選ぶことで、効率的な加工が可能となります。
アルミニウム旋盤加工のメリット
アルミニウムの旋盤加工は、様々なメリットがあります。まず第一に、旋盤を使った外径加工は高い精度で行える点が挙げられます。例えば、精密部品や機械部品の製造において、外径加工の正確さは非常に重要です。旋盤を使用することで、緻密な仕上がりや品質の向上が期待できます。
さらに、旋盤加工は効率的でスピーディーな加工が可能です。大量生産において、短時間で多数の部品を製造することができるため、生産性向上にもつながります。例えば、自動車産業や航空機産業などの大量生産ラインでは、旋盤加工が欠かせない要素となっています。
このように、アルミニウムを旋盤を使った外径加工することには精度と効率性の両面でメリットがあることから、産業界で広く活用されています。
工場選択のポイント
アルミニウム加工に適した工場の条件
アルミニウム加工に適した工場の条件は、まず、清潔で整然とした作業環境が重要です。クリーンな環境で作業することで、製品の品質を保ちやすくなります。また、旋盤を使った外径加工においては、正確な計測が欠かせません。加工精度を高めるためには、計測器や測定ツールの適切な使用が不可欠です。
さらに、外径加工においては、適切な切削速度や切削量を設定することも重要です。過度な速度や量ではなく、適切なバランスを保つことが、品質の向上につながります。例えば、アルミニウムの場合、適切な切削条件を設定することで、効率的かつ正確な加工が可能となります。
要するに、アルミニウム加工においては、清潔な環境で正確な計測を行い、適切な切削条件を設定することが重要です。これらの条件を整えることで、効率的で品質の高い加工が実現できるでしょう。
工場選びで重視すべき設備と技術力
アルミニウム加工の極意は、旋盤を使った外径加工の基本です。旋盤を使用することで精密な加工が可能となります。例えば、自動車部品や航空機部品など、様々な産業でアルミニウムが使用されています。外径加工は、円筒部分の加工を指し、直径を正確に加工することが重要です。適切な工具と切削条件を選定し、旋盤の操作技術を磨くことが成功の秘訣です。また、加工精度や仕上がりに影響する切削速度や切削深さの設定も重要です。工程ごとに適切な寸法を測定しながら進めることで、高品質なアルミニウム製品を生産することができます。外径加工において、技術力と機械設備の選定が重要です。
コストと品質のバランスの見極め方
アルミニウム加工において、旋盤を使った外径加工は重要な基本技術です。アルミニウムは軽くて丈夫な素材であり、様々な産業で使われています。外径加工は、アルミニウム製品の仕上げや形状を作るために必要な工程です。
外径加工の極意は、コストと品質のバランスを見極めることにあります。高品質な製品を求めるとコストが上がりますが、低品質だと耐久性や見た目に問題が生じる可能性があります。つまり、製品の用途やニーズに合わせて最適なバランスを見つけることが大切です。
例えば、自動車部品の外径加工では精度が求められるため、コストをかけても高品質な加工が必要です。一方、日常品や玩具などの製品ではコストを抑えつつ品質を保つことが重要です。外径加工においては、用途に応じたコストと品質のバランスを見極めることが成功のカギとなります。
旋盤加工の手順と種類
旋盤加工の一般的な流れ
アルミニウム加工における外径加工は、旋盤を使用することが基本です。旋盤加工の一般的な流れをご紹介します。まず、外径加工を行う際には、適切な切削速度や切りくずの除去方法を選択することが重要です。例えば、材料の種類や硬度によって最適な切削条件が異なります。次に、旋盤を使用して加工する際には、切削刃を適切に設定し、正確な寸法を保つことが求められます。また、加工中には定期的に刃物の状態を確認し、必要に応じて交換することも大切です。これらの基本的な手順を守ることで、アルミニウムの外径加工をスムーズに行うことができます。
外径加工の基本手順
アルミニウムの加工において、外径加工は非常に重要です。旋盤を使った外径加工の基本手順を理解することは、製品の精度や品質を保つ上で欠かせません。まず、外径加工とは、材料の外側を削り取ることで形状を整える加工方法です。この工程を正確に行うことで、製品の寸法や仕上がりに一貫性を持たせることができます。
旋盤を使用する場合、加工するアルミニウムの材料をセットし、適切な工具や刃先を使って加工を開始します。例えば、自動旋盤を使用する場合、プログラムを設定して自動的に加工を行うことも可能です。このように、旋盤を使った外径加工は効率的で精密な加工が可能となります。
外径加工の基本手順をマスターすることで、製品の品質向上や生産効率の向上につながることでしょう。
旋盤加工の種類とその用途
アルミニウム加工において、旋盤を使用した外径加工は非常に重要です。外径加工は、アルミニウムの円筒状の部品を作成する際に欠かせない基本的な技術です。例えば、自動車のエンジン部品や航空機の構造部品などの製造に広く活用されています。
旋盤を使用することで、アルミニウムの部品を正確かつ効率的に加工することが可能となります。外径加工の手法は、高い精度と仕上がりを実現するため、製品の品質向上にも貢献します。さらに、旋盤を活用することで、加工速度や生産性も向上させることができます。
アルミニウム加工において外径加工をマスターすることは、製品の品質向上や製造効率の向上につながります。この基本的な技術を習得することで、より高度な製品の製造にも挑戦できるでしょう。
A5052の外径仕上げのコツ
アルミニウム合金A5052とは
アルミニウム合金A5052は、アルミニウムにマグネシウムとクロムを添加した合金です。この合金は耐食性と溶接性に優れており、船舶や航空機、自動車など幅広い産業で使用されています。特に、軽自動車のボディパネルや船舶の部品として重宝されています。
旋盤を使った外径加工は、アルミニウム合金A5052の加工において重要な技術です。旋盤を使用することで、精密な外径加工が可能となります。例えば、車のアルミホイールやエンジン部品など、さまざまな製品にこの技術が活かされています。
外径加工には、正確な仕上がりが求められるため、高い技術と経験が必要です。アルミニウム合金A5052の特性を理解し、適切な旋盤の操作を行うことで、高品質な外径加工が実現できます。技術の進化や熟練した職人の技術により、アルミニウム加工の極意がさらに高度化しています。
A5052の旋盤加工のポイント
アルミニウムの加工において、旋盤を使った外径加工は重要な技術です。A5052というアルミニウム合金の旋盤加工を行う際のポイントをご紹介します。
まず、外径加工の基本は正確な寸法を守ることです。正確な寸法を保つことで、製品の品質を高めることができます。この点をしっかりと押さえることが重要です。
次に、適切な切削速度と切削量を設定することもポイントです。材料やツールに合わせた最適な条件を見極めることで、効率的な加工が可能となります。
例えば、A5052の場合、適切な切削速度と切削量を設定することで、きれいな仕上がりを実現できます。
これらのポイントを押さえて、旋盤を使った外径加工を行うことで、効率的で高品質な加工が可能となります。
外径加工における仕上げのコツ
アルミニウム加工における外径加工は、精度を求められる作業の基本です。旋盤を使った外径加工には、仕上げのコツがあります。まず、正確な寸法を測定して目標とする外径を設定します。この段階でミスを避けることが重要です。次に、切削工具を正確にセットし、適切な切削速度と切削量を設定します。これにより、きれいな仕上がりを実現できます。
例えば、アルミニウムの外径加工では、軽い圧力と適切な冷却液の使用が重要です。加工中に過度な熱が生成されると、加工精度が低下する可能性があります。適切な工具と技術を使い、外径加工を慎重かつ正確に行うことで、高品質な仕上がりを実現できます。
旋盤加工の流れと基本的な手順
加工前の準備
アルミニウム加工における外径加工の基本は、旋盤を利用することです。まず、加工前の準備が必要です。外径加工の前に、使用するアルミニウムの種類や形状、加工する部品の仕様を確認しましょう。次に、適切な刃具や工具を選んで準備します。具体的な例を挙げると、アルミニウム合金の場合は硬度に注意しながら工具を選定します。
[理由] この準備作業を怠ると、加工品質が低下したり、工具に損傷が生じたりする可能性があります。外径加工においては、正確な加工寸法が求められるため、準備段階での注意が重要です。
[具体例] 例えば、旋盤を使用してアルミニウムロッドの外径加工を行う際には、回転速度や切削量を適切に設定し、正確な寸法を実現します。また、刃先の状態を確認しながら加工を行うことで、良好な仕上がりを目指します。
[結論] アルミニウム加工における外径加工は、準備段階の丁寧な作業が重要です。適切な準備と工具の選定、加工時の注意を怠らずに行うことで、高品質な部品を生産することが可能となります。
旋盤設定の基本
アルミニウム加工において旋盤を使って外径加工を行う際の基本的な設定についてお話しします。まず、正確な外径加工を行うためには、適切な切削速度と切削量が重要です。切削速度は回転数によって決まり、材料と刃物の種類によって異なります。例えば、アルミニウムの場合は高速切削が一般的です。
次に、切削量は一度に削る量を指します。適切な切削量を設定することで、加工精度を向上させることができます。また、加工工具の選定も重要であり、適切な工具を選ぶことで効率的な外径加工が可能となります。
これらの基本設定を遵守することで、効率的かつ正確な外径加工を実現できます。是非、これらのポイントを念頭に置いてアルミニウム加工に取り組んでみてください。
加工プロセスのステップバイステップ
アルミニウム加工において、外径加工は重要な工程の一つです。旋盤を使用した外径加工は、精密で効率的に加工を行うための基本技術です。まず、旋盤を使用する理由として、高い加工精度と素早い加工速度が挙げられます。例えば、自動車のエンジン部品や航空機の部品など、幅広い産業で利用されています。
外径加工の手順には、まず加工対象物を旋盤にセットし、必要な加工条件を設定します。次に、切削工具を使って加工を開始し、所定の形状や寸法に仕上げます。このように、旋盤を用いた外径加工は、精度と効率性を両立させる重要なプロセスです。
アルミニウム加工において、外径加工をマスターすることで、製品の品質向上や生産性の向上が期待できます。この基本技術を習得し、工程をステップバイステップで確実に進めることで、より効果的な製品加工が可能となります。
旋盤加工の特徴と代表的な加工方法
旋盤加工の特徴とは
アルミニウム加工において、旋盤を使った外径加工は重要な工程です。旋盤加工の特徴とは何でしょうか?まず、旋盤を使用することで精密な加工が可能となります。外径加工では、アルミニウムの素材を回転させながら切削加工を行うことで、円柱状の部品を作成することができます。この方法は作業効率が高く、高精度な仕上がりを実現します。例えば、自動車のエンジン部品や航空機の部品など、さまざまな産業で活用されています。外径加工によってアルミニウム部品の精度や品質を向上させることができるため、その重要性はますます高まっています。アルミニウム加工において、旋盤を使った外径加工は確かな技術と知識が求められる工程です。
代表的な旋盤加工方法
アルミニウム加工において、旋盤を使った外径加工は重要な工程です。旋盤を使用することで、精密な加工が可能となります。初めに、旋盤を使用する理由は、高い精度を実現できるからです。たとえば、自動車部品や航空機部品など、厳密な寸法が求められる製品において外径加工が必要となります。
具体的な例を挙げると、航空機のエンジン部品では、アルミニウムの外径加工が欠かせません。エンジン部品は高い耐久性と精度が求められるため、旋盤を使用した外径加工が重要です。
結論として、アルミニウム加工において旋盤を使った外径加工は、高い精度と信頼性を実現するために欠かせない工程です。この技術をマスターすることで、さまざまな産業分野で優れた製品を提供することが可能となります。
複合加工とその利点
アルミニウム加工において、旋盤を使った外径加工は重要な技術です。外径加工は、アルミニウムの円筒形状を作る際に必要不可欠なプロセスです。まず、旋盤を使用して加工することで、高い精度で円筒形状を実現することができます。例えば、自動車部品や航空機部品など、様々な産業で利用されています。このような外径加工は、アルミニウム素材の特性を最大限に活かすことができるため、耐久性や軽量化が求められる製品において重要です。したがって、旋盤を使用した外径加工は、アルミニウム加工において欠かせない基本技術と言えるでしょう。
まとめ
アルミニウム加工において、旋盤を使った外径加工は重要な技術です。外径加工における基本的なポイントは、適切な切削速度と刃先形状を選ぶことです。また、適切な冷却および潤滑も重要な要素であり、これによって切削精度が向上し、加工表面の仕上がりも向上します。
アルミニウム加工で成功するためには、旋盤の適切なセットアップと安全な操作が欠かせません。素材特性を理解し、適切な切削速度と刃先形状を選定することが重要です。加工工程における正確な測定や検査を怠らず、確実な品質管理を実施することも重要です。
アルミニウム加工の悩み解決!旋盤でのビビりを抑える方法
アルミニウムを扱う際に、旋盤におけるビビりという問題に悩んだことはありませんか?アルミニウム加工は繊細で正確な技術が求められるため、ビビりが生じることは避けたいところです。そこで、本記事ではアルミニウム加工におけるビビりの解決方法に焦点を当ててご紹介します。アルミニウム素材の特性や旋盤の使い方について理解を深めることで、よりスムーズに作業を進めることが可能となります。さらに、おすすめのテクニックや注意すべきポイントについても詳しく解説します。アルミニウム加工におけるビビりの解決方法を知り、技術の向上に役立ててみてください。
アルミニウム旋盤加工の基礎知識
アルミニウムとは
アルミニウムは、軽くて耐久性があり、さまざまな産業で幅広く使用されている金属です。その特性から、旋盤などの加工工程でビビりが発生することがあります。ビビりが発生すると、加工精度が損なわれたり、製品の品質が低下したりする可能性があります。この問題を解決するためには、適切な工具や切削条件、加工速度などを調整することが重要です。
例えば、旋盤加工中にビビりを抑える方法として、適切な刃先形状の工具を選ぶことや加工中の振動を抑えるための工夫をすることが挙げられます。また、冷却潤滑剤を適切に使うことも重要です。これらの工夫により、アルミニウム加工におけるビビりを効果的に抑えることができます。加工効率を向上させるためにも、正しい工具選びや加工条件の最適化が重要です。
旋盤加工の概要
アルミニウム加工の悩み解決!旋盤でのビビりを抑える方法
アルミニウムを旋盤で加工する際、ビビりが起こることがあります。ビビりとは、加工中に材料が振動してしまうことで、正確な加工が難しくなる現象です。この問題を解決するためには、いくつかの対策があります。
まず、適切な切削条件を設定することが重要です。適切な切削速度や切削深さを選ぶことで、ビビりを抑えることができます。また、切削工具の選定も重要です。適切な刃先形状や加工材料に合った工具を選ぶことで、ビビりを軽減することができます。
これらの対策を適切に実施することで、アルミニウム加工におけるビビりを効果的に抑えることができます。適切な対策を行うことで、正確な加工が可能となり、製品の品質向上につながります。
アルミニウム旋盤加工の特徴
アルミニウム旋盤加工の特徴は、精密な加工が可能であり、軽量で強度があり、さまざまな産業で広く使用されていることです。しかし、ビビりという問題もあります。旋盤加工中に生じる振動や揺れで、加工が正確に行われないことがあります。このような問題を解決する方法として、刃物の刃先の形状や取り付け角度を適切に調整することが重要です。さらに、適切な切削速度や切削深さを設定することでビビりを抑えることができます。このような対策を講じることで、アルミニウム旋盤加工における品質向上と効率化が図れます。アルミニウムの特性を理解し、適切な技術を駆使することで、ビビりを克服し、高品質な加工を実現できます。
アルミニウム加工における一般的な問題点
ビビリの発生原因
アルミニウム加工において旋盤でのビビりが発生する原因はさまざまです。まず、加工速度が速すぎると、アルミニウムが振動しやすくなり、ビビリが発生しやすくなります。また、切削刃の状態が悪かったり、刃先の角度が適切でない場合も、ビビリの原因となります。さらに、適切な切削油や冷却液の使用が欠けていると、加工部が熱くなり、ビビリが起こりやすくなります。
これらの原因を解決するためには、加工速度を適切に調整し、切削刃を定期的にメンテナンスすることが重要です。また、適切な切削油や冷却液を使用して加工温度を抑えることも効果的です。これらの対策を講じることで、アルミニウム加工におけるビビりを抑えることができます。
むしれの発生と影響
アルミニウム加工において旋盤でのビビりが問題となることはよくあります。この問題を解決するためには、適切な対策が必要です。ビビりの原因は加工時の振動や刃物の切りくずなどが挙げられます。ビビりを抑えるためには、適切な切削条件や工具の選定が重要です。例えば、刃先の角度を適切に設定したり、適切な切削速度や送り速度を選ぶことが大切です。また、適切な冷却や潤滑もビビりを軽減するのに役立ちます。これらの対策を講じることで、アルミニウム加工におけるビビりを効果的に抑えることができます。しっかりとした対策を講じることで、より品質の高い製品を生産することができるでしょう。
加工精度への影響
アルミニウムの旋盤加工において、ビビり現象は加工精度に大きな影響を及ぼします。ビビりが生じると加工面にムラが生じ、精度が低下する可能性が高まります。この問題を解決するために、適切な対策が必要です。
まず、ビビり現象を抑えるためには、適切な切削条件を設定することが重要です。切削速度や切削量、ツールの選定などを慎重に行うことで、ビビりを最小限に抑えることができます。さらに、切削中に適切な冷却や潤滑を行うことも効果的です。
例えば、適切な刃先半径を選択し、適正な切削条件で加工を行うことで、ビビりを抑えることができます。また、適切な固定具や支えを使用することも重要です。これらの対策を適切に行うことで、アルミニウム加工におけるビビり現象を効果的に解決できます。
ビビリ抑制のためのアルミニウム旋盤加工テクニック
適切な工具の選択
アルミニウム加工の悩み解決!旋盤でのビビりを抑える方法
アルミニウムを旋盤加工する際、ビビりが起こることがあります。この問題を解決するためには、適切な工具の選択が重要です。例えば、適切な切削速度や刃先の形状を選ぶことで、ビビりを抑えることができます。また、十分な冷却や潤滑も重要な要素です。適切な冷却剤や潤滑油を使用することで、加工時の摩擦や熱を抑え、ビビりを最小限に抑えることができます。
工具の選択や適切な加工条件を整えることで、アルミニウム加工におけるビビりを効果的に解消することができます。これにより、旋盤作業の効率が向上し、品質の向上にもつながります。適切な対処法を取ることで、アルミニウム加工の品質向上につながることを覚えておきましょう。
切削条件の最適化
アルミニウムの旋盤加工において気になるビビり現象を上手く抑える方法を紹介します。ビビりは加工品質を損なう原因となることから、その解決方法は重要です。まず、ビビりを抑えるためには、切削条件を最適化することが大切です。適切な切削速度や切削量を設定することで、ビビりを最小限に抑えることができます。さらに、切削工具の適切な選択や刃先の状態管理も重要です。例えば、適切な刃先の磨き直しや交換を定期的に行うことで、ビビり現象を軽減することができます。これらの対策を実践することで、アルミニウムの旋盤加工におけるビビりを効果的に解決し、品質向上につなげることができます。
ワークの固定方法
アルミニウム加工で旋盤を使用する際に起こるビビリを抑える方法を解説します。アルミニウムは軽くて強度が高いため、加工時にビビりが発生しやすい特性があります。ビビリが発生すると加工精度が低下し、仕上がりに影響が出てしまいます。
ビビリを抑えるための方法は、まず適切な切削条件を設定することが重要です。適切な切削速度や切削量を設定することで、アルミニウムのビビリを最小限に抑えることができます。また、適切な刃先形状や工具の選定も重要です。
具体的な例として、適切な冷却液の使用や適切な刃先の状態を保つことが挙げられます。これらの対策を講じることで、アルミニウム加工におけるビビリを効果的に抑えることができます。アルミニウム加工におけるビビり対策を理解し、効果的な加工を行いましょう。
むしれの原因と対策
むしれを引き起こす要因
アルミニウム加工において、旋盤でのビビりが問題となることがあります。この問題を解決する方法について考えてみましょう。旋盤でのビビりを抑えるためには、まず適切な加工条件を設定することが重要です。適切な切削速度や切削量を選ぶことで、ビビりを抑えることができます。
また、適切な刃先の選定も重要です。刃先の形状や材質を適切に選ぶことで、ビビリを軽減することができます。さらに、工具の交換タイミングや刃先のメンテナンスも怠らないようにしましょう。
このように、適切な加工条件や工具の選定、メンテナンスを行うことで、アルミニウム加工における旋盤でのビビりを解消できます。しっかりとした対策を行い、品質の高い加工を実現しましょう。
むしれの防止策
アルミニウム加工の悩み解決!旋盤でのビビりを抑える方法
旋盤作業中にアルミニウムがビビる現象は、多くの加工業者の悩みの種です。この問題を解決するためには、まずビビりの原因を理解することが重要です。アルミニウムは柔らかい金属であり、切削時に振動を生じやすいため、ビビりが発生しやすくなります。
ビビりを抑えるためには、適切な切削条件や工具の選定が必要です。例えば、適切な切削速度や刃先の形状を選ぶことで、ビビりを最小限に抑えることができます。また、切削油の効果的な使用やワークホルダーの安定性確保も重要です。
これらの対策を講じることで、アルミニウム加工におけるビビりを効果的に防止できます。工程ごとに適切な対処を行うことで、作業効率の向上や加工精度の向上にも繋がります。
切削加工で対応可能なアルミ合金の種類
一般的なアルミ合金の特性
アルミニウム合金は、軽量で耐久性があり、多くの産業で幅広く使用されています。特に旋盤加工において、ビビりと呼ばれる問題が生じることがあります。このビビりは、加工中に振動が生じて部品の精度や仕上がりに影響を与えることがあります。そのため、ビビりを抑える方法が重要です。
ビビりを抑えるために、適切な切削条件や工具の選定が欠かせません。また、適切な固定や支持を行うことでビビりを軽減することができます。例えば、適切なクランプやチャックを使用することで、部品の安定性を確保し、ビビりを最小限に抑えることができます。
こうした対策を講じることで、アルミニウム合金の旋盤加工におけるビビりを効果的に解決し、部品の品質向上につなげることができます。
各アルミ合金の加工性
アルミニウム加工において、旋盤でのビビりが悩みの種となることがあります。ビビりが生じる原因は、材料や旋盤の不適切な設定など様々です。しかし、ビビりを抑える方法も存在します。例えば、適切な刃先形状や切削速度、切りくずの適切な排出などが挙げられます。
特にアルミニウム合金の場合、硬度や切削抵抗が異なるため、適切な加工条件を把握することが重要です。例えば、7000シリーズのアルミニウム合金はビビりが生じやすいため、切削条件を細かく調整する必要があります。このように、正しい加工条件を選定し、操作技術を磨くことで、旋盤でのビビりを効果的に抑えることができます。アルミニウム加工においては、適切な知識と技術が成功への近道となります。
アルミ加工の5つの方法とその注意点
旋盤加工
アルミニウム加工の悩み解決!旋盤でのビビりを抑える方法
アルミニウムを旋盤で加工する際に、ビビりが発生することは多くの工場で悩みの種となっています。ビビりが生じると、加工精度が損なわれ、製品の品質に悪影響を及ぼす可能性があります。
その原因は、切削時の振動や加工条件の調整不足などさまざまです。ビビリを抑えるためには、適切な工具選定や刃先の角度、切削速度、切りくずの排出方法など細かな工夫が必要です。
例えば、適切な切削速度と刃物の選択により、アルミニウムのビビりを最小限に抑えることができます。加工条件を適切に調整することで、品質向上と生産性の向上が期待できます。ビビり対策をしっかり行うことで、効率的なアルミニウム加工が可能となります。
フライス加工
アルミニウム加工の悩み解決!旋盤でのビビりを抑える方法
アルミニウムの加工において、旋盤を使用する際にビビりが生じることは問題となります。このビビりを抑える方法を考えることが重要です。ビビりが発生する原因はさまざまですが、適切な工具の選択や適切な切削条件を設定することで、ビビりを軽減することが可能です。
具体的には、適切な刃先形状や刃先角度の工具を選定することで、アルミニウムの旋盤加工におけるビビりを抑えることができます。また、適切な切削速度や切削深さを設定することも重要です。これらの工夫を行うことで、アルミニウム加工におけるビビりを効果的に防止できるでしょう。
ドリル加工
アルミニウム加工におけるビビりを抑える方法について考えてみましょう。旋盤での作業中、ビビりが生じると加工精度が低下し、作業効率も損なわれてしまいます。この問題を解決するためには、まず適切な切削速度や切り込み量を設定することが重要です。また、工具の状態を定期的に点検し、研磨することも大切です。さらに、適切な冷却液や切削油を使用することで、加工時の摩擦や熱を抑えることができます。これらの対策を講じることで、アルミニウム加工におけるビビりを抑えることが可能となります。工程を丁寧に確認し、上手に対処することで、効果的な加工作業が実現します。
研磨加工
アルミニウム加工の悩み解決!旋盤でのビビりを抑える方法
アルミニウムの旋盤加工において、旋盤でのビビりはよくある問題です。この問題を解決するためには、いくつかの工夫が必要です。
まず、ビビりを抑えるためには、適切な加工速度と切削条件を設定することが重要です。過剰な切削や速度の過大な設定はビビりを引き起こす原因となります。さらに、適切な刃先形状や切りくずの排出方法もビビりを軽減するのに役立ちます。
例えば、金属加工業者では、切削速度や刃先形状を工夫し、アルミニウムの旋盤加工におけるビビりを抑える取り組みが行われています。これらの工夫により、品質の向上と生産性の向上が期待できます。
ビビりを抑えるための工夫を行うことで、アルミニウムの旋盤加工における問題を解決し、効率的な加工作業を実現することができます。
鋳造
アルミニウム加工の悩み解決!旋盤でのビビりを抑える方法
アルミニウムの旋盤加工において、ビビりの問題はよく起こります。この問題を解決するためには、まず原因を理解することが重要です。アルミニウムは軽くて柔らかい素材であり、旋盤加工中に振動が生じやすいため、ビビりが発生しやすいのです。
ビビりを抑えるためには、まずは適切な刃先や加工条件を選定することが大切です。刃先が適切でない場合や加工速度が速すぎると、ビビりが生じやすくなります。加工条件を工夫し、適切な切削量や切削速度を設定することで、ビビりを抑えることができます。
さらに、クーリングシステムを適切に利用することも効果的です。適切な冷却によってアルミニウムの加工温度を下げ、ビビりを予防することができます。ビビりを抑えるために、これらの方法を組み合わせて効果的に対処しましょう。
アルミニウム旋盤加工の難易度と解決策
アルミニウム加工の難しい理由
アルミニウム加工の難しい理由は、旋盤作業中に生じるビビりです。旋盤での加工中、回転するアルミニウムが揺れ動くことによって、精密な加工が難しくなります。このビビリ現象は加工精度を損ない、製品の品質を低下させる可能性があります。
ビビリを抑える方法として、まずは適切な工具や切削条件を選択することが重要です。また、加工前にアルミニウムの固定方法や支持方法を工夫することでビビリを軽減することができます。さらに、最新の技術や加工ノウハウを取り入れることで、ビビリを最小限に抑えて効率的な加工を実現することが可能です。
これらの対策を講じることで、アルミニウム加工におけるビビりを効果的に抑え、精密な加工作業をスムーズに行うことができます。
各問題点の解決策
アルミニウム加工で旋盤を使用する際に生じるビビり問題を解決する方法についてご紹介します。アルミニウムは軽量で加工しやすい素材ですが、旋盤での加工時に振動が生じやすく、ビビりが発生することがあります。
この問題を解決するために、まずは適切な切削条件を設定することが重要です。適切な刃先形状や切りくず排出の工夫により、ビビりを抑えることができます。また、適切なクーリング液の使用や刃先の状態管理も効果的です。
例えば、切削速度や切削深さを適切に設定し、振動を最小限に抑えることが重要です。さらに、高品質の旋盤装置を使用することで、より精度の高い加工が可能となり、ビビりを解消することができます。これらの方法を実践することで、アルミニウム加工におけるビビり問題を効果的に解決することができます。
加工精度向上のためのコツ
アルミニウム加工において、旋盤でのビビりを抑える方法について解説します。ビビりは、加工精度を損ない、仕上がりに影響を及ぼすことがあります。ビビりを解決するためには、まず切削条件を適切に設定することが重要です。適切な切削速度や切削量を選定することで、ビビりを軽減できます。さらに、刃先の形状や切削油の適切な使用もビビり防止に効果的です。
例えば、刃先の角度を調整したり、加工中に切削油を適度に供給することで、ビビりを最小限に抑えることができます。これらの対策を講じることで、アルミニウム加工におけるビビりを効果的に防止し、加工精度を向上させることができます。
アルミニウム旋盤加工の成功事例
ビビリを克服した具体例
アルミニウム加工における旋盤作業でのビビり問題に悩む方々への解決方法をお伝えします。アルミニウムは加工時にビビりや振動が起こりやすい素材ですが、この問題を克服するための具体的な方法があります。例えば、適切な切削条件を設定することや、適切な切削工具を選定することが重要です。さらに、適切な冷却液の使用や旋盤機器の適切なメンテナンスもビビりを抑えるポイントです。これらの対策を講じることで、アルミニウム加工におけるビビりを効果的に改善することができます。ビビりの問題に悩む方々には、これらの具体的な対策を実践してみてください。その結果、作業効率が向上し、品質の向上にもつながるでしょう。
むしれ問題を解決した事例
アルミニウム加工の悩み解決!旋盤でのビビりを抑える方法
アルミニウムの旋盤加工において、ビビりが発生することは一般的な問題です。しかし、ビビりを抑える方法を知っておくことで、加工品質を向上させることが可能です。
まず、ビビりの原因を理解することが重要です。例えば、切削速度や刃先の角度など、加工条件によってビビりが発生することがあります。そのため、加工条件を適切に設定することが解決の第一歩となります。
さらに、適切な切削工具を選択することも重要です。例えば、硬度や形状が適切な工具を選ぶことで、ビビりを抑えることができます。
これらの対策を講じることで、アルミニウム加工におけるビビりの問題を解決し、より高品質な製品を生産することができます。
高品質なアルミ加工のポイント
アルミニウム加工における重要なポイントは、旋盤作業時のビビりを抑えることです。ビビりが生じると仕上がりの精度が低下し、作業効率も損なわれてしまいます。この問題を解決するために、まずは旋盤の切削速度や切削深さを適切に調整することが重要です。正確なパラメータ設定はビビりを最小限に抑えるのに役立ちます。
さらに、適切な冷却液の使用も重要です。冷却液が正しく設定されていると、切削プロセスがスムーズに進み、ビビりが発生しにくくなります。例えば、アルミニウムの場合は水溶性の冷却液が効果的です。
最後に、適切な切削工具の選択もビビりを軽減するポイントです。高品質な切削工具を選ぶことで、作業効率が向上し、精度の高い加工が可能となります。これらのポイントを遵守することで、アルミニウム加工におけるビビりを抑えることができます。
まとめ
アルミニウムの旋盤加工において、ビビリを抑える方法について考えてみましょう。アルミニウムの加工は軽量でありながらも硬度が高いため、ビビリが起こりやすい特性があります。この問題を解決するために、適切な工具やカッティング条件を使用することが重要です。また、適切なクーリングや切削速度の管理もビビリを軽減するポイントとなります。これらの方法を適用することで、アルミニウムの旋盤加工におけるビビリを抑えることができます。
航空機材料A5052対A7475!性能と用途での選択肢
航空機の製造において、材料の選択は非常に重要です。特にA5052とA7475の比較は興味深いトピックです。これらの材料は航空機産業において広く使用されており、それぞれ異なる性能と用途を持っています。本記事では、A5052とA7475の性能や適用分野に焦点を当て、両者の比較を探ります。航空機材料の選択に関心をお持ちの方々にとって、興味深い情報を提供できることを目指しています。材料選択の際にお悩みの方や航空機材料に興味がある方々にとって、この比較が参考になることでしょう。
航空機用アルミニウム合金とは
アルミニウム合金の基礎知識
アルミニウム合金にはさまざまな種類がありますが、今回比較するのはA5052とA7475です。これらの合金は航空機材料として広く使用されていますが、性能や用途で選択する際には注意が必要です。
まず、A5052は耐食性に優れ、溶接性も高い特徴があります。一方、A7475は強度が高く、耐疲労性に優れています。航空機の部品や構造物において、それぞれの特性を考慮して適切な合金を選択することが重要です。
例えば、A5052は船舶や食品加工機器などにも利用されており、汎用性が高い一方で、A7475は航空宇宙産業において高い信頼性が求められる部品に使用されています。
したがって、どちらの合金を選択するかは、使用用途や要件に合わせた適切な判断が必要です。
航空機材料としてのアルミニウム合金の重要性
航空機の材料として、アルミニウム合金は非常に重要です。特にA5052とA7475という二つの合金は航空機の部品や構造物に幅広く使用されています。A5052は耐食性に優れ、溶接性も高いため、燃料タンクやボディパネルなどに適しています。一方、A7475は非常に高い強度を持ち、主翼やエンジンパーツなどの高負荷部品に適しています。
これらの合金を選ぶ際には、使用する目的や性能要件に応じて適切なものを選択する必要があります。例えば、耐食性が重要な場合はA5052を、強度が求められる場合はA7475を選択することが一般的です。
航空機の安全性と信頼性を確保するためには、適切な合金の選択が欠かせません。航空機産業において、適切な合金を選択することは非常に重要な要素です。
航空機用アルミニウム合金の種類と特徴
航空機材料A5052とA7475の性能と用途を比較検討します。A5052は耐食性が優れ、腐食に強い性質があります。これは航空機の外殻や燃料タンクなどに適しています。一方、A7475は強度が高く、耐久性に優れています。このため、主翼やエンジン部分などの高負荷部品に使用されます。
航空機産業においては、用途に応じて材料を選択することが重要です。例えば、A5052は軽量で加工性に優れているため、航空機の外殻や内装パネルなどに適しています。一方、A7475は高強度を活かしてエンジン部品や着陸ギアなどに使用されます。
このように、A5052とA7475はそれぞれの特性によって異なる用途に適しています。航空機材料を選択する際には、性能と用途に応じて適切な合金を選ぶことが重要です。
A5052とA7475のアルミニウム合金比較
A5052の特性と用途
A5052とA7475という航空機材料は重要な役割を果たしています。これらの材料は航空機や自動車などの産業で広く使用されており、性能や用途によって適切な選択をすることが重要です。
まず、A5052は耐食性に優れ、加工性が高い特性を持っています。これにより、飛行機の外装パネルや車体の一部などに使用されています。一方、A7475は強度が高く、耐熱性に優れています。そのため、エンジン部品や着陸装置などの高強度が要求される箇所に使用されています。
どちらの材料も重要な役割を果たしており、産業界で広く信頼されています。性能や用途を理解し、適切に選択することが製品の品質向上につながることは言うまでもありません。
A7475の特性と用途
A5052とA7475は航空機材料として利用される際に選択肢となります。A5052は耐食性に優れ、溶接性が高いため、飛行機の外装パーツや構造材として広く使われています。一方、A7475は強度が高く、耐久性に優れているため、エンジンパーツや航空機の主要構造部品として採用されています。例えば、A5052は機体の外板や窓枠に使用され、A7475は主翼やエンジン部分に使用されています。A5052は軽量で加工が容易ですが、A7475は高温に耐える性能があります。そのため、使用する部位や要件に合わせて適切な材料を選択することが重要です。航空機産業においては、性能と用途に応じてA5052とA7475を適切に活用することが必要です。
A5052とA7475の物理的・化学的性質の比較
航空機産業において、航空機材料の選択は重要です。A5052とA7475は代表的な材料ですが、性能や用途には違いがあります。A5052は耐食性に優れ、加工性が高いため、船舶や車両の外装、建築材料などに広く使われています。一方、A7475は強度が高く、耐熱性にも優れており、主翼や胴体など高負荷部品に使用されます。例えば、A5052は飛行機の外装パネルに、A7475はエンジン部品に適しています。したがって、選択肢は使用する箇所や必要な性能によって異なります。航空機の安全性や効率性を考えると、正確な材料選択が不可欠です。
航空機用アルミニウム合金の選定方法
材料選定における基準と考慮点
航空機の構造において、適切な材料を選定することは非常に重要です。A5052とA7475は航空機材料として広く使われていますが、それぞれに性能や用途が異なります。
まず、A5052は耐食性に優れ、軽量です。一方、A7475は強度が高く、耐久性に優れています。材料を選定する際には、使用目的や要件に合わせて適切な材料を選ぶことが重要です。
例えば、航空機の主翼では強度が求められるため、A7475が適しています。一方、航空機のボディパネルでは軽量性が重要となるため、A5052が適しています。
適切な材料を選定することで、航空機の性能や耐久性を向上させることができます。そのため、材料選定には慎重に検討することが重要です。
A5052とA7475の適用範囲と限界
A5052とA7475は航空機材料として重要な素材です。A5052は一般的な航空機部品に広く使用されており、優れた耐食性と加工性を持っています。一方、A7475は高強度を誇り、主翼や胴体などの高負荷部品に適しています。両素材の適用範囲は異なりますが、性能と用途に応じて適切に選択されるべきです。
A5052は軽量で耐食性があり、航空機の外板や内装部品に適しています。一方、A7475は高い耐久性と強度を持ち、エンジン部品や主翼などの耐久性が求められる部位に適しています。例えば、A5052は航空機の外板やランディングギアに使用され、A7475は主翼の補強部分やエンジンの構造部品に使用されることがあります。
適切な素材の選択は航空機の安全性や性能に直結する重要な要素であり、それぞれの素材の特性を理解し、適切に選択することが重要です。
航空機設計における材料選択の戦略
航空機設計における材料選択の戦略
航空機の材料選択は、機体の性能や用途に大きな影響を与えます。A5052とA7475は航空機材料としてよく比較される素材です。例えば、A5052は耐食性に優れており、主に軽飛行機や小型機の構造部品に使用されています。一方、A7475は強度が高く、ジェットエンジンや大型航空機の主翼などの部品に適しています。
材料を選択する際には、どのような性能が求められるかをよく考慮することが重要です。例えば、耐食性が必要な部位にはA5052を、強度が求められる部位にはA7475を使用することが適切です。このように、適切な材料選択は航空機の安全性や性能向上につながります。
航空機材料のアルミニウム合金の機械的性質
強度と耐久性
A5052とA7475の航空機材料を比較すると、強度と耐久性が重要な要素となります。A5052は一般的な用途に適しており、軽量で加工性が高いため、航空機の外装や内装パーツによく使われています。一方、A7475は高強度で疲労耐性に優れており、エンジン部品や着陸装置などの重要な部位に使用されます。
例えば、A5052は燃料タンクやフレームなどの部品に使用され、A7475は主翼やエンジン部品に採用されています。そのため、使用する部位や要求される性能に合わせて適切な材料を選択することが重要です。
航空機の安全性や性能を確保するためには、適切な材料の選択が欠かせません。A5052とA7475はそれぞれの特性を活かして、航空機の機能を支えています。
比重と軽量化への貢献
A5052とA7475の航空機材料の比較では、それぞれの性能や用途によって選択肢が異なります。A5052は一般的なアルミニウム合金で、優れた耐食性や溶接性が特徴です。一方、A7475は高強度アルミニウム合金で、耐久性や強度に優れています。例えば、A5052は航空機の外板やフレームなどに使用されることが多く、軽量化が求められる部品に適しています。一方、A7475はエンジン部品や着陸ギアなどの高負荷箇所に使用されることが多いです。
選択肢を考える際には、使用する箇所の特性や要求される性能をよく理解し、適切な材料を選定することが重要です。両者の特性を十分に把握し、航空機の安全性や性能向上に貢献する材料として適切な選択が求められます。
ヤング率と剛性
A5052とA7475は航空機の材料として使用されることがありますが、どちらを選ぶべきかについて考えてみましょう。
まず、A5052は耐食性に優れ、軽量で加工しやすい特性があります。一方、A7475は強度が高く、耐疲労性に優れています。そのため、使用する目的によって適した材料を選ぶことが重要です。
例えば、A5052は飛行機の外板や構造部品などで使用されることがあります。一方、A7475はエンジン部品や着陸装置など、高い強度が求められる部品に適しています。
したがって、適切な性能と用途に合わせて、A5052とA7475を選択することで航空機の安全性や性能を向上させることができます。
アルミニウム合金の加工方法と航空機への応用
A5052とA7475の加工性
航空機材料A5052とA7475の比較を考えると、加工性は重要な要素です。A5052は一般的なアルミ合金であり、加工性が良く、溶接や曲げ加工に適しています。一方、A7475は強度が高いアルミ合金であり、加工性はやや難しいですが、高い強度を持っています。例えば、A5052は航空機の外板などの成形に向いていますが、A7475は主翼や胴体などの高強度部品に使用されます。したがって、用途によって選択すべき材料が異なります。加工性が重視される場合はA5052を選択し、高い強度が必要な場合はA7475が適しています。航空機の設計や構造において、それぞれの特性を理解し、適切に選択することが重要です。
航空機部品製造でのアルミニウム合金の利用
航空機の部品製造において、アルミニウム合金は広く使用されています。特にA5052とA7475は一般的な選択肢です。A5052は耐食性に優れ、溶接性も高いため、船舶や食器など幅広い用途に使用されています。一方、A7475は非常に強度が高いため、主翼などの高負荷を受ける部品に適しています。
A5052は一般的な航空機の構造部品や燃料タンクなどに使用される一方、A7475はリベットやストレスがかかる箇所に適しています。性能や用途によって適切なアルミニウム合金を選択することが重要です。航空機の安全性や効率性を向上させるためには、部品ごとに最適な素材を選定することが欠かせません。
航空機の性能向上に寄与するアルミニウム合金の役割
航空機の性能向上に寄与するアルミニウム合金の役割
航空機の製造において、A5052とA7475というアルミニウム合金は重要な役割を果たしています。これらの合金は飛行機の性能向上に貢献し、異なる用途に応じて選択肢として利用されています。
まず、A5052は耐食性や溶接性に優れており、主に機体の外装や構造部品に使用されています。一方、A7475は強度や耐熱性に優れており、エンジン部品や着陸装置などの高負荷部品に適しています。
例えば、A5052は軽量化が求められる部位に使われ、A7475は高強度が必要な箇所に活用されます。このように、それぞれの特性を活かして航空機の設計や製造において効果的に活用されています。
A5052対A7475:最適な材料の選択
ケーススタディ:実際の航空機での使用事例
A5052とA7475は航空機の材料として選択される際に重要なポイントです。性能や用途によって使い分けがされます。A5052は軽量で耐食性があり、一般的な部品に使用されます。一方、A7475は強度が高く、主翼やフレームなどの高負荷部品に適しています。例えば、A5052は航空機の外板や内装部品、A7475は機体の主要部品に使われます。このように、それぞれの特性を活かして設計された航空機は安全性と効率性が高まります。航空機の運用環境や要求に基づいて、A5052とA7475を使い分けることで最適な性能を発揮できるのです。
コスト対効果と材料選択
A5052とA7475の航空機材料を比較する際、性能と用途に注目することが重要です。 A5052は軽量で耐食性があり、船舶や航空機の部品などに広く使用されています。一方、A7475は耐熱性や強度に優れており、高温環境下での使用に適しています。例えば、ジェットエンジン部品や宇宙船の構造部品に適しています。したがって、どちらの材料を選択するかは、使用する環境や必要な性能によって異なります。機体の軽量化を重視する場合はA5052が適していますが、高い強度が求められる場合はA7475を選択することが適切です。航空機の安全性や性能を考慮し、適切な材料を選択することが重要です。
環境への影響と持続可能性の観点からの材料選択
航空機の材料選択においてA5052とA7475の比較は重要です。材料の性能や用途によって最適な選択肢が異なります。例えば、A5052は耐食性に優れており、一般的な航空機の構造部品や外装パネルに使用されます。一方、A7475は強度が高く、主翼やエンジン部品などの高負荷部位に適しています。
さらに、環境への影響や持続可能性の観点からも材料選択は重要です。例えば、A5052は再利用が比較的容易であり、エコフレンドリーな材料として注目されています。一方、A7475は高強度で軽量化が可能なため、航空機の燃費改善に貢献します。
したがって、航空機材料を選択する際には、性能、用途だけでなく、環境への影響や持続可能性も考慮した選択が求められます。そのため、A5052とA7475の適切な選択を行うことが航空機の安全性と環境への配慮につながります。
アルミニウム合金の未来と航空機材料としての展望
技術革新と新合金の開発
航空機材料A5052とA7475の比較について考えてみましょう。A5052は一般的なアルミニウム合金であり、軽量で加工性に優れています。一方、A7475は耐食性や強度に優れた新しい合金です。航空機の部品や構造において、どちらの材料を選ぶかは性能や用途によって異なります。
例えば、A5052は軽量で燃費効率を向上させることができます。一方、A7475は高温や高圧環境下でも安定した性能を発揮するため、エンジン部品などの耐久性が求められる箇所に使用されます。
こうした選択肢を理解し、適切に活用することで航空機の性能や安全性を向上させることができます。最適な材料選択は航空産業にとって重要な課題であり、技術革新と新合金の開発がその解決に貢献しています。
アルミニウム合金のリサイクルと環境負荷
航空機材料A5052対A7475!性能と用途での選択肢
航空機産業において、アルミニウム合金は重要な素材です。その中でも、A5052とA7475はよく比較される材料です。A5052は耐食性に優れ、溶接性も高いため、船舶や飛行機の外板に適しています。一方、A7475は強度が高く、主翼や胴体などの部品に使用されます。
航空機の設計において、材料の選択は重要です。例えば、A5052は軽量で加工しやすいため、燃費を重視した設計に適しています。一方、A7475は高強度なので、耐久性が求められる部位に使用されます。
したがって、航空機の性能や用途に合わせて、A5052とA7475の適切な選択が重要です。どちらの材料も航空機の安全性や効率性に貢献することが期待されます。
航空宇宙産業におけるアルミニウム合金の動向と予測
航空宇宙産業におけるアルミニウム合金の動向と予測
A5052とA7475は航空機材料として重要な役割を果たしています。どちらも優れた性能を持ち、異なる用途に適しています。A5052は耐食性に優れ、船舶や建築などに広く使用されています。一方、A7475は耐久性に優れ、航空宇宙産業で主に使用されています。これらの選択肢を理解し、適切に使用することが重要です。
航空機の場合、A7475は高強度が求められる部位に使用されます。例えば、主翼や胴体などに適しています。一方、A5052は内装や非構造部品に使用されることが多いです。性能と用途に応じて適切な素材を選択することは航空機の安全性や効率性に直結します。航空宇宙産業において、それぞれの素材の特性を理解し、適切な場面で使用することが重要です。
まとめ
航空機材料のA5052とA7475は、それぞれ異なる性能と用途を持っています。A5052は軽量で耐食性に優れており、一方のA7475は高強度と耐久性を兼ね備えています。これらの特性を比較することで、適切な用途に適した素材を選択できます。航空機産業における材料選択において、A5052とA7475は重要な選択肢となります。
「A6061とA6063のアルミ合金の性質と適用分野の解説」
アルミ合金A6061とA6063の基本
アルミ合金とは?
アルミ合金A6061とA6063は、それぞれ独自の性質を持ち、異なる適用分野に使用されています。A6061合金は一般的に高い強度が求められる用途に適しており、そのために航空機部品や自動車のフレームなどに採用されることが多いです。対照的にA6063合金は、成形性が良く表面処理が容易であるため、建築材料やパイプ、照明器具などの外観が重視される製品に好んで使用されます。例えば、A6061は自転車のフレームに使用されることがあり、一方A6063は建物の窓枠やドアに見られます。最終的に、これらの合金を選ぶ際には、その特性を理解し、目的に最も適したものを選択することが重要です。それにより、耐久性、美観、コストのバランスを適切に取りながら、機能的かつ効率的な製品開発を実現することができます。A6061の基本的特性
特性項目 | 内容 |
---|---|
主な合金元素 | シリコン(Si)、マグネシウム(Mg)、銅(Cu) |
引張強度 | 約260-310 MPa |
降伏強度 | 約240 MPa |
伸び | 約12-17% |
密度 | 2.70 g/cm³ |
硬度 | 約95-105 HB |
熱伝導率 | 167 W/m・K |
電気伝導率 | 40-43% IACS |
比重 | 2.7 |
耐食性 | 良好 |
加工性 | 良好 |
溶接性 | 良好。ただし、溶接後に再熱処理が必要な場合あり |
熱処理性 | 熱処理(T6など)によって強度が大幅に向上 |
詳細な説明
- 強度と伸び: A6061は中程度の強度と高い延性を持ち、特にT6熱処理を施すことで引張強度が約310 MPaに達します。降伏強度も高く、機械的な強度が求められる用途に適しています。
- 耐食性: 耐食性が良好で、特に海水や湿潤な環境での使用に適しています。陽極酸化処理を行うことで耐食性がさらに向上します。
- 加工性: 冷間加工および熱間加工が可能で、加工性が良好です。特に削り出しや切削加工がしやすく、複雑な形状の部品製作に向いています。
- 溶接性: 溶接性も良好ですが、溶接後には再熱処理(T6など)を行うことで溶接部の強度が回復します。溶接によるひずみや変形が発生しやすいので注意が必要です。
- 熱処理性: A6061は熱処理により機械的特性が大幅に変化します。T6処理を行うことで強度が最大化され、様々な用途に適用できます。
A6063の基本的特性
特性項目 | 内容 |
---|---|
主な合金元素 | シリコン(Si)、マグネシウム(Mg) |
引張強度 | 約160-230 MPa |
降伏強度 | 約110-160 MPa |
伸び | 約8-12% |
密度 | 2.70 g/cm³ |
硬度 | 約60-70 HRB |
熱伝導率 | 200 W/m・K |
電気伝導率 | 約50% IACS |
比重 | 2.7 |
耐食性 | 非常に良好 |
加工性 | 優れており、押出成形に適している |
溶接性 | 良好で、溶接後の再熱処理は通常不要 |
熱処理性 | 熱処理(T5、T6)により強度向上 |
詳細な説明
- 強度と伸び: A6063は中程度の強度を持ち、引張強度は約160-230 MPaです。伸びは約8-12%で、柔軟性も持ち合わせています。特に強度よりも加工性や表面仕上げが重要な用途に向いています。
- 耐食性: 耐食性は非常に良好で、腐食環境や屋外での使用にも適しています。特に陽極酸化処理により、美しい外観と優れた耐食性を得ることができます。
- 加工性: A6063は特に押出加工に適しており、複雑な断面形状の製品を効率的に作成できます。また、加工がしやすく、曲げや切削などの作業も容易です。
- 溶接性: 溶接性は良好で、一般的なTIG溶接やMIG溶接に適しています。溶接後の強度低下も少なく、再熱処理が不要な場合が多いため、構造部材などに広く使用されます。
- 熱処理性: A6063は熱処理によって機械的特性を調整でき、T5やT6の熱処理を行うことで引張強度が向上します。熱処理後も形状が安定しやすく、押出加工後の処理に適しています。
A6061とA6063の物理的・化学的性質
A6061の成分と物理的性質
A6061の化学成分
元素 | 含有量(%) |
---|---|
シリコン (Si) | 0.4-0.8 |
鉄 (Fe) | 最大 0.7 |
銅 (Cu) | 0.15-0.4 |
マンガン (Mn) | 最大 0.15 |
マグネシウム (Mg) | 0.8-1.2 |
クロム (Cr) | 0.04-0.35 |
亜鉛 (Zn) | 最大 0.25 |
チタン (Ti) | 最大 0.15 |
その他の元素 | 最大 0.05 (個別), 0.15 (合計) |
アルミニウム (Al) | 残り |
A6061の物理的性質
性質項目 | 値 |
---|---|
密度 | 2.70 g/cm³ |
融点 | 582 – 652°C |
熱伝導率 | 167 W/m・K |
比熱 | 0.896 J/g・K |
電気伝導率 | 40-43% IACS |
引張強度 | 約260-310 MPa (T6処理後) |
降伏強度 | 約240 MPa (T6処理後) |
伸び | 約12-17% (T6処理後) |
硬度 | 約95-105 HB |
詳細な説明
- 成分: A6061は主にシリコン(Si)、マグネシウム(Mg)、銅(Cu)を含む合金で、これらの元素が合金の強度と加工性を高めています。特にマグネシウムとシリコンの組み合わせによって、強度と耐食性がバランスよく向上しています。
- 物理的性質: A6061は中程度の強度と高い耐食性を持ち、特にT6熱処理を施すことで機械的特性が向上します。熱伝導率や電気伝導率が高く、優れた熱管理と電気特性が求められる用途に適しています。また、密度が2.70 g/cm³と軽量で、強度と軽量性のバランスが取れているため、航空機や自動車部品に広く使用されています。
A6063の成分と物理的性質
A6063の化学成分
元素 | 含有量(%) |
---|---|
シリコン (Si) | 0.2-0.6 |
鉄 (Fe) | 最大 0.35 |
銅 (Cu) | 最大 0.10 |
マンガン (Mn) | 最大 0.10 |
マグネシウム (Mg) | 0.45-0.9 |
クロム (Cr) | 最大 0.10 |
亜鉛 (Zn) | 最大 0.10 |
チタン (Ti) | 最大 0.10 |
その他の元素 | 最大 0.05 (個別), 0.15 (合計) |
アルミニウム (Al) | 残り |
A6063の物理的性質
性質項目 | 値 |
---|---|
密度 | 2.70 g/cm³ |
融点 | 615°C |
熱伝導率 | 200 W/m・K |
比熱 | 0.900 J/g・K |
電気伝導率 | 約50% IACS |
引張強度 | 約160-230 MPa (T6処理後) |
降伏強度 | 約110-160 MPa (T6処理後) |
伸び | 約8-12% (T6処理後) |
硬度 | 約60-70 HRB |
詳細な説明
- 成分: A6063はシリコン(Si)とマグネシウム(Mg)を主成分とする合金で、これらの元素が押出加工性や耐食性を高めています。A6063は、他の元素が非常に少ないため、アルミニウムの純度が高く、美しい表面仕上げが可能です。
- 物理的性質: A6063は軽量で耐食性に優れており、特に押出加工が容易で、複雑な断面形状の製品に適しています。T6処理を施すことで、引張強度や降伏強度が向上し、建築材料やフレーム、構造材などの用途で使用されます。高い熱伝導率と電気伝導率を持ち、放熱性が重要なアプリケーションにも向いています。また、耐食性が高く、屋外使用や湿潤な環境にも適しています。
A6061とA6063の強度と耐久性の比較
項目 | A6061 | A6063 |
---|---|---|
引張強度 | 約260-310 MPa (T6処理後) | 約160-230 MPa (T6処理後) |
降伏強度 | 約240 MPa (T6処理後) | 約110-160 MPa (T6処理後) |
伸び | 約12-17% (T6処理後) | 約8-12% (T6処理後) |
耐久性 | 優れており、高負荷環境にも耐える | 良好、比較的軽負荷の用途に適している |
耐食性 | 良好 | 非常に良好 |
衝撃に対する耐性 | 高い | 中程度 |
耐摩耗性 | 良好 | 良好 |
加工後の強度回復 | 溶接後の再熱処理が必要な場合がある | 溶接後も比較的強度が維持される |
詳細な説明
- 強度: A6061はA6063に比べて高い引張強度と降伏強度を持ち、強度が重要な用途(例えば構造部材や機械部品)に適しています。一方、A6063は比較的低い強度ですが、押出加工性が優れており、建築やフレーム用途でよく使われます。
- 耐久性: A6061は機械的負荷が大きい環境でも優れた耐久性を発揮しますが、A6063は軽負荷の環境や装飾、建築物での使用が一般的です。A6061はその高い強度により、航空機や自動車の部品に広く使用されています。
- 耐食性: A6063は耐食性に優れており、特に屋外環境や腐食しやすい環境での使用が推奨されます。A6061も耐食性は良好ですが、A6063の方がやや優れています。
- 溶接後の強度: A6061は溶接後の強度が低下することがあり、再熱処理が必要な場合があります。一方、A6063は溶接後も比較的強度が維持されるため、溶接を多用する用途での使用が容易です。
A6061とA6063の加工性について
A6061とA6063の加工性の比較
項目 | A6061 | A6063 |
---|---|---|
切削加工性 | 良好 | 良好だが、A6061よりやや劣る |
曲げ加工性 | 良好だが、高強度のため曲げには制限がある | 優れており、複雑な形状の加工が容易 |
押出成形性 | 良好 | 非常に優れており、細かい断面形状が可能 |
溶接性 | 良好(溶接後、強度が低下する可能性あり) | 良好(溶接後も比較的強度を維持) |
陽極酸化処理性 | 良好 | 非常に良好、装飾的な用途にも最適 |
鍛造性 | 良好 | 良好だが、A6061には劣る |
再加工性 | 高強度を維持したままの再加工が可能 | 良好、特に押出成形後の再加工が容易 |
耐摩耗性 | 優れている | 良好 |
詳細な説明
- 切削加工性: A6061は強度が高いため、安定した切削が可能です。A6063も切削加工性は良好ですが、A6061と比較すると若干劣るため、切削時の速度や工具の選定に注意が必要です。
- 曲げ加工性: A6063はA6061に比べて曲げ加工性が高く、複雑な形状に曲げる際も割れや変形が起こりにくいです。A6061は強度が高いため、曲げ加工時に割れやすく、特に厚肉材では制限があります。
- 押出成形性: A6063は押出成形に非常に適しており、複雑な断面形状の部品を高精度で製造できます。A6061も押出成形性は良好ですが、A6063の方が優れています。
- 溶接性: 両者とも溶接性は良好ですが、A6061は溶接後に強度が低下することがあるため、再熱処理が必要な場合があります。A6063は溶接後の強度維持が比較的良好で、溶接を多用する構造材にも適しています。
- 陽極酸化処理性: A6063は表面処理後の外観が美しく、装飾的な用途にも多く使われます。A6061も陽極酸化処理が可能ですが、A6063の方がより美しい仕上がりが得られます。
- 再加工性: A6061は高い強度を維持しながら再加工が可能であり、精密な機械部品に適しています。A6063は押出成形後の加工が容易で、細かな仕上げや形状変更が求められる用途に向いています。
熱処理と表面処理の違い
A6061とA6063アルミ合金は、その特性と適用分野が異なることで知られています。A6061合金は、高い引張強度と優れた耐食性を持ち、航空機の部品や精密機器のフレームとしてよく使用されています。一方、A6063合金は成形性に優れ、建築資材や自動車の内装パーツなど、複雑な形状が求められる用途に適しています。たとえば、A6061は耐久性が要求される自転車のフレームやクライミング用具に使用されるのに対し、A6063はアルミサッシや家具の装飾品に選ばれることが多いです。このように、各合金の性質を理解することは、適切な材料選びに不可欠で、それぞれの合金が最大の性能を発揮する適用分野が存在します。A6061とA6063の適用分野
A6061の主な使用例
A6061とA6063は、いずれも一般的なアルミ合金であり、その性質と用途には顕著な違いがあります。A6061合金は、優れた機械的性質と耐食性を持ち合わせているため、自動車の部品や建築材料などの要求される強度が高い分野で使われています。特定の例としては、自動車のフレームや航空宇宙産業での構造材料が挙げられます。一方で、A6063合金は、表面処理が容易であり美観性に優れているため、建築の装飾用途やアルミサッシ、ライトフレームなどの見た目を重視する製品に利用されます。これらの合金はそれぞれ特有の特性を持っており、適した用途に応じて選択されることで、製品の機能性と経済性を高めることができます。A6063の主な使用例
A6061とA6063は、アルミニウム合金として広く利用されていますが、それぞれ異なる特性を持ち、適用分野も異なります。A6061は、高い強度と優れた耐食性、良好な加工性を兼ね備えており、航空機の部材や精密機器の部品など、強度が要求される用途に適しています。一方、A6063はA6061に比べて強度は低いものの、溶接性や表面処理の質が高く、家具や建築材料、自動車のインテリアトリムなどに用いられています。例えば、A6063は建築分野では窓枠やドアフレーム、照明器具としての利用が一般的です。このように、A6061とA6063はそれぞれの性質に応じて選ばれ、私たちの身の回りのさまざまな製品に不可欠な役割を果たしているのです。各合金の適用分野の選定基準
A6061とA6063のアルミ合金は、その特性が異なるため、適用分野においても異なる選定基準が求められます。A6061合金は、高い耐食性と優れた機械的性質を持っているため、航空宇宙産業や海洋設備などの要求される環境が厳しい分野で使用されます。具体例として、航空機の翼や船体の一部として採用されています。一方、A6063合金は表面処理が容易であり、建築材料や自動車の内装部品としての使用が多いです。例えば、窓枠やドアフレームなどの建築資材や、カーパーツへの応用が挙げられます。 それぞれの合金が持つ特性を理解し、それに基づいた適用分野の選定が重要です。A6061は強度と耐食性が求められる場所、A6063は加工性と表面の美しさが重視される場所での使用が最適であると言えるでしょう。A6061とA6063の違いと選択肢
A6061とA6063の主な違い
A6061とA6063は、いずれもアルミニウム合金であり、細かな特性の違いにより異なる用途に適しています。特に、A6061はその高い強度と耐食性により、航空機や船舶の部品、自動車のフレームやホイールなど、重要な強度が求められる製品に使われています。対してA6063は、その良好な加工性と表面処理の美しさから、ビルや家具のデザイン部材、建築用の窓枠やドアなどの装飾的な目的でよく使用されています。 例えば、A6061は、高い引張強度と耐蝕性を要する自動車のサスペンションシステムや航空機の構造部品に使用されることが多いです。一方、A6063は、押し出し性に優れているため、アルミニウムサッシや家具のフレームなどの形状が複雑な部品に適しています。 このような特徴から、A6061とA6063はそれぞれが持つ長所を活かした適切な応用分野が存在します。最終的には、使用目的に応じて、これらの合金を選定することが重要です。シナリオ別適用合金の選択
A6061とA6063は、アルミ合金の中でも特に一般的な素材です。これらの合金が選ばれる主な理由は、加工性、耐蝕性、強度のバランスに優れている点にあります。A6061は、引張強度が高く、耐疲労性にも富んでいるため、航空機の部品や精密機械のフレームなど、高い強度が求められる用途に適しています。一方、A6063は表面処理の仕上がりがきれいになる特長を持ち、建築材料やインテリアパーツなど、見た目が重視される場面でよく使用されます。 両合金の特性を理解し、目的に応じた適切な選択をすることが大切です。例えば、耐久性と美観の両方を求める場合はA6063が、より高い機械的強度を要する場合はA6061が適した選択肢となります。結論として、A6061とA6063は性質が異なるため、それぞれの特性を活かした適用分野での使用が推奨されます。類似素材との比較
アルミ合金のA6061とA6063は、共に多くの産業で用いられているが、その性質と適用分野には差があります。A6061は引張強度が高く、耐食性にも優れているため、構造材料としての用途に適しています。具体的には、オートバイのフレームや、航空機の部品、そしてクライミング用具などに使用されることが多いです。一方、A6063は表面処理がしやすく、加工性に優れているため、建築やインテリアの装飾材料に用いられることが多く、アルミサッシや家具のフレームなどが代表的な例です。 これらの違いは、アルミ合金を選択する際の重要な指標となります。耐久性や強度、加工のしやすさを考慮し、それぞれの特性に合った用途でA6061とA6063は活用されるべきです。さまざまなニーズに応じて適切なアルミ合金を選択することが、製品の品質と性能を最大限に引き出す鍵となります。まとめとしての選択ガイド
プロジェクトに最適な合金の選び方
A6061とA6063のアルミ合金は、共に優れた性質を持ち、多様な適用分野に対応していますが、その特性には微妙な違いが存在します。A6061合金は、高い引張強度と優れた耐食性を持ち、加工性にも優れているため、航空機の部品や精密機器、自動車の部品など、強度が求められる分野に適しています。一方、A6063合金は、表面処理の美しさと溶接性の良さが特長で、建築材料や家具のフレーム、アルミサッシなど見た目が重要視される用途に用いられています。例えば、A6061合金は自動車のフレームに使用されることが多いのに対し、A6063合金はオフィスビルの窓枠に使われることが多いです。これらの違いを理解することで、プロジェクトの要件に最適な合金を選択することが可能です。よって、使用目的に応じて、それぞれの合金の特性を考慮して選定することが重要であると結論づけられます。コストと性能のバランス
A6061とA6063アルミ合金は、その優れた性質とコストパフォーマンスから、幅広い分野で利用されています。A6061合金は、耐食性、溶接性、強度が高いため、航空宇宙、自動車、橋梁などの要求が厳しいアプリケーション向けに適しています。一方、A6063は表面処理が容易であり、建築資材やインテリア用途に好まれます。特に、A6061は高いテンサイルストレングスを持っており、機械部品や構造部材に適用されることが多いです。また、A6063は熱処理による硬化が可能で、アルミニウム窓枠やドア、各種フレーム製造に使用されることが一般的です。これらの特性により、A6061とA6063はそれぞれの用途に応じて選ばれ、ものづくりの現場において、その役割を果たし続けています。したがって、適切な合金を選択することが、製品の品質と経済性を決定づける重要な要素であるといえます。最終製品の品質に影響する要素
A6061とA6063のアルミ合金はそれぞれ異なる特性を持ち、使われる分野も異なります。A6061合金は強度が高く、優れた耐食性と加工性を併せ持つため、航空機の部品や精密機械のフレームなど高い信頼性が求められる用途に適しています。一方、A6063合金は表面処理の質が高く、加工が容易なため、建築材料やインテリアの装飾品など、見た目が重要視される分野で使用されることが多いです。 例えば、A6061は自転車のフレームやクライミング用カラビナなどに使われることがあり、これらは合金の強度や耐久性が非常に重要です。対照的に、A6063はドアや窓枠、サインボードなど、優れた外観を保ちつつ容易に成形できる製品に採用されます。 そうした特性を理解して適切な合金を選ぶことは、最終製品の品質に大きく寄与します。A6061合金であれば強度と耐久性が求められる箇所に、A6063合金ならば加工性と美観を優先する箇所に適用することで、製品はより長持ちし、使い勝手も向上するでしょう。それぞれの合金が最適な場に用いられることで、アルミ合金の特性を最大限に活かせるのです。まとめ
アルミニウム合金A6061とA6063は、それぞれ異なる特性と適用分野を持っています。これらのアルミニウム合金は、建築や自動車産業など多岐にわたる分野で使用されています。それぞれの特性や適用分野について理解することは、製品やプロジェクトの設計において重要です。異なる用途に応じて適切なアルミニウム合金を選択することで、製品の性能や品質を向上させることが可能です。「アルミニウム加工向け!旋盤の剛性を上げるコツと技術」
アルミニウムを使用した加工作業において、効率的で精密な加工を行うためには、旋盤の剛性が欠かせません。今回の記事では、「アルミニウム加工向け!旋盤の剛性を上げるコツと技術」と題しまして、この重要なテーマに焦点を当ててご紹介いたします。アルミニウムと旋盤、そして剛性というキーワードが織り成すテクニカルな世界に、一緒に深く探求していきましょう。どのようにして剛性を高めるか、どのような技術が存在するのか、そのヒントとなる情報を詳細に解説していきます。旋盤作業における新たな視点を手に入れ、より高度な加工技術を身につけるための一歩を踏み出してみませんか。
Contents
アルミニウム加工の基礎
アルミニウムとは:軽量で加工しやすい金属
アルミニウムは、軽量で加工しやすい金属です。その特性から、様々な産業分野で広く利用されています。例えば、航空機の部品から日常生活用品まで幅広い製品に使用されています。アルミニウムの特性を最大限に活かすためには、旋盤の剛性が重要です。
旋盤の剛性を上げるためには、適切な材料や設計が必要です。例えば、高品質な剛性を持つ材料を使用したり、剛性を高める補強部品を追加したりすることが効果的です。これにより、アルミニウム加工の精度や効率が向上し、製品の品質も向上します。
したがって、アルミニウム加工向けの旋盤を効果的に活用するためには、剛性を重視した設計や改良が不可欠です。剛性を高める技術を取り入れることで、アルミニウム加工の品質向上や生産性向上につながることが期待されます。
アルミニウム合金の種類と特性
アルミニウム合金には様々な種類があり、それぞれ特性が異なります。例えば、6061合金は一般的に使われ、強度と耐食性に優れています。一方、7075合金は非常に高い強度を持つため、航空機や自動車の部品に使用されます。また、剛性を上げるためには、旋盤の技術が重要です。例えば、適切な工具の選定や切削速度の調整などがポイントです。剛性を高めることで、加工精度や効率が向上し、製品の品質も向上します。熟練した技術と正しいコツを持つことが、アルミニウム加工向けの旋盤作業で成功する秘訣です。
アルミ加工の一般的な方法と応用
アルミニウム加工は産業界で広く利用されています。この加工において、旋盤の剛性を高めることは重要な要素です。剛性を高めることで、加工精度が向上し、より品質の高い製品が作られます。剛性を向上させるコツと技術は、機械の設計や材料の選定にあります。
例えば、旋盤機に適切な剛性を持たせるためには、堅牢な構造や適切な材料を使用することが重要です。さらに、振動を抑える技術や最新の制御システムを導入することも効果的です。これらの取り組みにより、アルミニウム加工における生産性や品質が向上し、競争力を強化することができます。
旋盤の剛性を上げることは、アルミニウム加工における重要な課題であり、技術の進化によりさらなる改善が期待されています。
アルミニウム旋盤加工の利点
アルミニウム旋盤加工の利点は、その軽さと耐食性にあります。アルミニウムは軽く、錆びにくい性質を持っているため、様々な産業で広く使用されています。旋盤を用いることで、アルミニウムの加工が容易になり、精密な部品や製品を作ることができます。
アルミニウムを旋盤で加工する際に、剛性が重要な要素となります。剛性が不足すると加工精度が低下したり、加工速度が制限される可能性があります。剛性を高めるためには、適切な工具や刃物を使用し、適切な切削条件を設定することが重要です。また、旋盤機そのもののメンテナンスや正確なセットアップも剛性を向上させるポイントです。
これらのコツと技術をマスターすることで、アルミニウム旋盤加工の効率と品質を向上させることができます。
アルミ旋盤加工に関するキホン
旋盤加工の基本工程
アルミニウムを使用した旋盤加工では、剛性が非常に重要です。剛性が不足すると、加工精度や加工速度が低下し、品質にも影響を及ぼす可能性があります。このため、旋盤の剛性を上げるコツと技術を紹介します。
まず、旋盤の安定性を高めるために、適切な材料を選択することが重要です。剛性の高い素材を使用することで、振動を抑えることができます。また、適切な切削条件を設定し、工具の適切な取り付けを行うことも剛性を向上させるポイントです。
例えば、加工時に振動が発生した場合、切削条件を見直したり、工具の取り付け角度を調整することで剛性を改善することができます。これらの工夫を行うことで、アルミニウム加工における旋盤の剛性を向上させることができるでしょう。
アルミニウム専用旋盤の概要
アルミニウム加工向けの旋盤は、剛性が重要です。剛性を上げるコツと技術は重要です。アルミニウムは軽量でありながらも強度が必要な素材です。そのため、しっかりとした剛性がある旋盤を使用することは、精密な加工を行うために欠かせません。例えば、剛性を高めるためには、旋盤の構造をしっかりとしたものにすることや、振動を抑えるための工夫をすることが重要です。また、適切な刃物や冷却方法を選ぶことも剛性向上に役立ちます。剛性を高めることで、アルミニウム加工の効率が向上し、品質の向上にもつながります。アルミニウム加工において、剛性を重視することは、高品質な製品を生産するために不可欠です。
旋盤工具の選定とアルミニウム加工への影響
アルミニウム加工における旋盤の剛性を上げるコツと技術について考えてみましょう。旋盤工具の選定は非常に重要です。剛性のある旋盤工具を選ぶことで加工時の振動を抑えることができ、精密な加工作業が可能となります。例えば、高品質な刃物やクランプを使用することで、安定した加工を実現できます。
剛性を高めるためには、旋盤の設置場所や環境も考慮することが重要です。振動や揺れを最小限に抑えるために、しっかりとした基盤の上に設置することがおすすめです。また、定期的なメンテナンスや調整を行うことで、旋盤の性能を維持することも大切です。
旋盤の剛性を高めることで、アルミニウム加工の精度や効率が向上し、高品質な製品を提供することができます。剛性向上のポイントを押さえて、より効果的な加工を行いましょう。
旋盤操作の基本テクニック
アルミニウム加工を行う際に、旋盤の剛性を上げることは非常に重要です。なぜなら、剛性が不足していると加工精度が低下し、加工品質が損なわれる可能性があるからです。剛性を高めるためのコツと技術をご紹介します。
まず、旋盤を正しく据えることがポイントです。地盤やフロアの平坦性を確保し、適切なレベリングを行うことで剛性を向上させることができます。さらに、ツールホルダーの固定をしっかりと行い、振動を抑える工夫も必要です。
例えば、切削時に振動が発生すると加工精度が落ちるため、振動対策も重要です。適切な切りくずの排出、刃先の状態管理などにも注意が必要です。これらの技術を取り入れることで、アルミニウム加工における旋盤の剛性をしっかりと向上させることができます。
アルミ加工は難しい?加工のポイント解説
アルミ合金の加工における課題
アルミニウム合金の加工における課題は、旋盤の剛性が十分でないことです。剛性が不足していると、加工精度や品質に影響が出る可能性があります。そのため、剛性を上げることが重要です。
剛性を上げるためには、機械の基盤を強化したり、適切な部品を使用したりすることが必要です。例えば、旋盤のベッドやヘッドストックをより堅牢な素材で作ることで剛性を高めることができます。これにより、加工時の振動や歪みを抑え、より精密な加工が可能となります。
旋盤の剛性を上げる技術を積極的に取り入れることで、アルミニウム合金の加工作業が効率化され、品質も向上するでしょう。剛性向上による効果は、加工業界において大きなメリットとなることが期待されます。
アルミ加工時の品質管理
アルミニウム加工において、旋盤の剛性は品質管理において重要な要素です。剛性が不足していると、加工精度が低下し、仕上がりに影響が出る可能性があります。そのため、旋盤の剛性を上げるためには、適切な技術とコツが必要となります。
まず、旋盤の剛性を高めるためには、適切な切削条件を設定することが重要です。切削速度や切削量を適切に調整することで、加工中の振動を最小限に抑えることができます。また、適切な刃物や工具を選択し、正しい切削方法を適用することも剛性向上につながります。
具体的な例として、適切な冷却方法を選択することで、加工時の熱による変形を防ぐことができます。さらに、旋盤装置の定期的なメンテナンスや調整も剛性を保つために重要です。
以上のような技術とコツを活用することで、アルミニウム加工時の品質管理が向上し、より精度の高い加工が可能となります。
加工精度を左右する要因
アルミニウム加工において、旋盤の剛性は非常に重要です。剛性が不足していると、加工精度が低下し、仕上がりに影響が出る可能性があります。剛性を高めるコツと技術を考えてみましょう。まず、旋盤の基盤をしっかりと固定することが重要です。基盤が揺れると、加工時に振動が生じてしまい精度が損なわれます。また、切削時には適切な切削条件を選定することも大切です。材料の種類や加工する形状によって最適な切削条件が異なるため、注意が必要です。例えば、アルミニウム合金の場合は、適切な切削速度や刃先形状を選ぶことが重要です。これらの工夫を行うことで、旋盤の剛性を上げ、加工精度を向上させることができます。
アルミニウムの表面処理と仕上げ
アルミニウム加工において、旋盤の剛性を上げるコツと技術は重要です。剛性を高めることで、加工精度や安定性が向上し、品質の向上につながります。例えば、旋盤のベッドやキャリッジに適切な材料を使用することで剛性を確保することができます。また、振動を抑制するために適切なダンパーを設置することも効果的です。これにより、加工時の振動が軽減され、仕上がりにムラが生じにくくなります。さらに、切削加工時には適切な切削条件を設定することも重要です。適切な切削速度や切削深さを設定することで、旋盤の剛性を活かした効率的な加工が可能となります。剛性を高める工夫を凝らすことで、アルミニウム加工における品質向上につながることが期待されます。
アルミ加工5つの方法とその注意点
旋削加工
アルミニウム加工において、旋盤の剛性を上げることは非常に重要です。剛性が不足していると、加工精度や安定性が損なわれる可能性があります。剛性を上げるためのコツと技術について考えてみましょう。
まず、旋盤の基盤をしっかりと固定することが重要です。剛性が十分でない基盤だと、振動が生じたり加工時に不安定になる恐れがあります。例えば、専用の基盤を設置することで剛性を高めることができます。
さらに、切削時の刃先の角度や刃先形状なども剛性に影響を与えます。適切な刃先の設定や刃先の定期的なメンテナンスを行うことで、剛性を維持することができます。
以上のように、剛性を高めるためには、基盤の固定や刃先の管理に注意を払うことが重要です。これらのコツと技術を実践することで、アルミニウム加工における旋盤の性能向上が期待できます。
フライス加工
アルミニウム加工において、旋盤の剛性を上げるコツと技術についてご紹介します。剛性を高めることは、切削時に生じる振動や歪みを抑え、加工精度を向上させる重要なポイントです。例えば、旋盤の床面には適切な地盤補強を施すことで、振動を吸収し剛性を高めることができます。さらに、旋盤本体の構造を最適化し、剛性の向上を図る工夫も重要です。同様に、切削条件や工具の選定なども剛性向上に貢献します。これらの技術を組み合わせることで、アルミニウム加工における旋盤の性能を飛躍的に向上させることが可能です。剛性向上の取り組みは、加工効率や品質の向上につながります。
ドリリング加工
アルミニウム加工において、旋盤の剛性向上は非常に重要です。剛性が不足していると、加工精度が低下し、加工中の振動や変形が発生する可能性があります。そのため、剛性を上げるコツと技術を理解することが必要です。
まず、旋盤の基盤をしっかりと固定することが重要です。適切な設置と固定により、旋盤の振動を最小限に抑えることができます。さらに、加工時の切削力に耐えるために、剛性の高い素材で製作された旋盤を選ぶことも重要です。
例えば、最近の日本の製造業では、アルミニウム合金を加工する際に剛性の高い旋盤が求められています。このようなニーズに応えるため、旋盤メーカーは剛性を重視した新しい技術を開発しています。
剛性を高めることで、アルミニウム加工の効率性や精度を向上させることができます。したがって、旋盤の剛性向上は、製造業における重要な課題であり、技術革新が進む中で、より高度な加工技術が求められています。
バリ取り加工
アルミニウム加工業界において、旋盤の剛性を強化することは非常に重要です。剛性を高めるためのコツと技術を理解することで、加工精度や効率を向上させることが可能となります。例えば、旋盤の基盤やスライド部分に剛性を持たせる工夫が効果的です。
剛性を高めることで、アルミニウムなどの素材をより正確に加工することができます。旋盤作業において、剛性が不足していると加工精度が低下し、品質に影響を及ぼす可能性があります。そのため、剛性を向上させる技術を取り入れることは、製品の品質向上につながります。
アルミニウム加工において剛性を高めるためには、材料選定から工程設計まで様々な要素が関わってきます。そのため、剛性向上のポイントを押さえることが重要です。技術やノウハウを活用し、旋盤の剛性をしっかりと確保することで、効率的な加工作業が実現できるでしょう。
研磨加工
アルミニウム加工において、旋盤の剛性を上げるコツと技術について考えてみましょう。旋盤の剛性を向上させることは、精密な加工を行う上で非常に重要です。剛性が不十分だと、加工精度が低下したり、加工速度が制限されたりする可能性があります。
そこで、剛性を上げるためには、まずは適切な材料を選ぶことがポイントです。旋盤に使用する部品や構造物は、剛性に影響を与えるため、適切な素材を選ぶことで剛性を向上させることができます。また、適切なレイアウトや強化の技術を取り入れることも効果的です。
例えば、強固な支持構造を設計することで剛性を高めることができます。また、適切な補強材料を使用することも重要です。これらの工夫によって、旋盤の剛性を向上させることができ、より高品質な加工が可能になります。
各加工方法の難易度と対策
アルミニウム加工において、旋盤の剛性を上げることは重要です。剛性が不足すると、切削時に振動が発生し加工精度が低下する可能性があります。そのため、剛性を確保するコツや技術が必要です。
剛性を上げるためには、まず旋盤の基盤をしっかりと固定することが大切です。また、適切な切削条件を設定し、刃先の寿命を延ばすことも重要です。さらに、最新の切削工具やクーリングシステムを導入することで、効率的な加工が可能となります。
例えば、国内の自動車産業では、アルミニウム部品の需要が増加しており、剛性の高い旋盤が求められています。このように、剛性を上げる技術は産業界においても重要な要素となっています。旋盤の剛性を向上させることで、より高品質なアルミニウム加工が可能となります。
切削加工を行う際の剛性の重要性
剛性とは:切削加工の基本概念
旋盤加工における剛性の重要性を理解するために、まず「剛性」という概念を考えてみましょう。剛性とは、物体が変形しにくい性質を指します。旋盤加工において剛性が高いとは、切削時に生じる振動や変形が少なく、精度が向上することを意味します。
剛性を上げるためには、適切な素材や設計が重要です。アルミニウム加工においても、旋盤の剛性を高めるためには、剛性の高い素材を使用したり、剛性を高める機構を取り入れたりすることが求められます。
例えば、旋盤のベッド部分にリブ(肋)を設けることで剛性を向上させることができます。また、適切な切削条件を設定することも剛性向上に役立ちます。
剛性を高める工夫をすることで、アルミニウム加工における精度や効率を向上させることができます。是非、剛性向上のコツや技術を活かして生産性を高めていきましょう。
旋盤の剛性を上げるメリット
アルミニウム加工において旋盤の剛性を高めることのメリットは多岐にわたります。剛性が向上することで、加工精度が向上し、仕上がりの質も向上します。例えば、アルミニウムの微細加工や複雑な形状加工など、高度な加工作業においては剛性が大切です。剛性が不足していると振動が生じ、加工面の粗さや寸法精度の低下につながります。また、剛性向上により工具の摩耗が抑えられ、作業効率が向上します。旋盤の剛性を高めるためには、適切な材料や製造技術、設計を導入することが重要です。これらの取り組みが、アルミニウム加工における高品質な製品の製造や生産性向上に貢献します。
剛性不足がもたらす加工上の問題点
旋盤はアルミニウムの加工において重要な役割を果たしますが、剛性不足が生じると加工品質に悪影響を及ぼすことがあります。その理由は、剛性不足により切削時の振動や歪みが生じ、加工精度が低下するからです。例えば、加工面の粗さや寸法精度の劣化、歪みによる部品の不良等が挙げられます。
剛性を上げるためには、旋盤機械の設計やメンテナンスが重要です。例えば、剛性を高めるために適切な材料を使用し、構造の強化を図ることが必要です。また、正しい切削条件を設定して適切な切削を行うことも大切です。
剛性不足がもたらす問題を理解し、旋盤の剛性を向上させる努力が、アルミニウム加工の品質向上につながります。最終的には、正確で高品質な加工が可能となり、顧客満足度の向上や生産性の向上につながるでしょう。
旋盤の剛性を上げるコツと技術
旋盤の構造的剛性の向上
旋盤の構造的剛性を上げることは、アルミニウム加工において重要なポイントです。剛性が不十分だと、加工精度や作業効率に影響が出てしまいます。そのため、旋盤の剛性を向上させるためには、いくつかのポイントがあります。
まず、旋盤の基本構造をしっかりと理解することが重要です。剛性が不足している箇所を特定し、それに合わせて改良を行うことができます。例えば、ベッドやスライド台の補強、バラネスの調整などが考えられます。
また、適切な工作機械オイルや冷却液を使用することも重要です。これによって摩擦や熱の影響を抑え、剛性を保つことができます。
さらに、最新のテクノロジーや部品を導入することで、旋盤の剛性を向上させることが可能です。例えば、高剛性ベッドや新型の刃物ホルダーを導入することで、より安定した加工が行えます。
剛性を向上させるためには、機械全体のバランスや各部の補強、適切なメンテナンスなどが欠かせません。これらの取り組みを行うことで、旋盤の性能を最大限引き出し、効果的なアルミニウム加工を実現できるでしょう。
加工条件の最適化による剛性の活用
アルミニウム加工において、旋盤の剛性を向上させるためには、加工条件の最適化が重要です。剛性が不足すると、加工精度や作業効率が低下し、品質面で問題が生じる可能性があります。例えば、適切な切削速度や切り込み量、冷却方法などを設定することで、剛性を最大限に活かすことができます。このような最適化により、アルミニウム加工における旋盤の性能を向上させることができます。剛性を高めることで、加工時の振動や歪みを抑え、より精密な加工が可能となります。加工条件の適切な設定によって、効率的で品質の高いアルミニウム加工が実現できるのです。
振動抑制と精度向上のテクニック
アルミニウム加工において、旋盤の剛性を高めることは非常に重要です。剛性を上げることで、精度が向上し、加工時の振動が抑制されます。例えば、適切な刃先の選定や切削条件の最適化などが効果的です。また、工具や切削液の適切な選定も剛性向上につながります。
例えば、過去にアルミニウム加工において、旋盤の剛性を高めるために、振動を抑制するためのテクニックが取り入れられました。これにより、加工精度が向上し、作業効率が向上しました。その結果、製品の品質向上と生産性の向上が実現されました。
剛性を高める技術は、アルミニウム加工において重要な要素となっています。適切な技術を取り入れることで、より効率的な加工が可能となります。
アルミニウム加工に適した旋盤設備の選び方
「アルミニウム加工向け!旋盤の剛性を上げるコツと技術」
旋盤を選ぶ際、アルミニウム加工に適した剛性が重要です。剛性の高い旋盤を選ぶことで、加工精度や作業効率を向上させることができます。
剛性が高いということは、旋盤がしっかりとした基盤を持ち、振動や歪みが少ないことを意味します。これにより、切削時の安定性が増し、仕上がりも良くなります。
例えば、高速加工時に剛性の低い旋盤を使用すると、加工精度が低下し、加工面にムラが生じる可能性があります。そのため、アルミニウムのように柔らかい素材を扱う際は、剛性の高い旋盤を選ぶことが重要です。
剛性を高めるためには、旋盤の構造や素材、加工方法などを工夫することがポイントです。適切な旋盤を選ぶことで、アルミニウム加工における作業効率や品質の向上につながります。
定期的なメンテナンスと剛性維持
アルミニウム加工で旋盤を効果的に使用するためには、定期的なメンテナンスと剛性維持が重要です。剛性とは、加工時に生じる振動や負荷に対する機械のしなやかさを指します。この剛性を保つことで、旋盤の精度と安定性が向上し、作業効率も向上します。
例えば、旋盤の剛性を維持するには、定期的なベッドの清掃やガイドウェイのオイル注入が必要です。これにより、精密な加工作業が可能となります。また、適切な刃物の選択や加工条件の最適化も剛性を維持するために重要です。
剛性維持によって、アルミニウム加工における旋盤の性能を最大限に引き出すことができます。定期的なメンテナンスと的確な技術を取り入れることで、効率的な加工が可能となります。
まとめ
アルミニウム加工において、旋盤の剛性を上げることは重要です。剛性が不足していると、加工精度や安定性に影響を及ぼし、作業効率や品質に影響を与えます。アルミニウムの特性を考慮し、剛性を向上させるためのコツや技術を理解することが重要です。さまざまな加工条件に合わせて、適切な剛性を確保することで、高品質なアルミニウム加工が可能となります。
「A6061とA6063の違いとは?アルミの選び方ガイド」
アルミニウム合金A6061とA6063の基本
アルミニウム合金とは?
アルミニウム合金A6061とA6063は、どちらも工業用途に広く使用されており、その特性には明確な違いがあります。A6061は高強度が特徴で、航空機の部品や精密機械など要求される強度が高い用途に適しています。一方、A6063は加工性に優れ、建築材料や自動車の部品など表面仕上げが重要視される領域でよく用いられます。例えば、A6061は自転車のフレームやクライミング用のカラビナに使用されることが多く、これはその強度と耐久性が求められるからです。A6063は、ドアフレームや窓枠など建築分野での利用が一般的で、優れた断面特性を発揮します。結論として、用途に応じて最適なアルミニウム合金を選択することが重要です。A6061はその強度を、A6063は加工性と外観の美しさを活かしたい場合に選ばれるべきでしょう。A6061とA6063の基本的な特性
A6061の基本的な特性
特徴 | 詳細説明 |
---|---|
主な合金成分 | アルミニウム、マグネシウム、シリコン |
機械的特性 | 高い強度と耐久性、優れた強度対重量比。引張強度が約260〜310 MPa、伸びが12〜17%(T6硬化状態)。 |
耐食性 | 良好で、酸化膜により耐腐食性が向上。海水環境での使用も可能。 |
加工性 | 切削、圧延、溶接が容易。熱処理により機械的特性を大幅に改善できる。 |
主な用途 | 機械部品、航空機構造材、車両部品、橋梁、建築構造材。 |
熱処理 | T6(溶体化処理後の人工老化)やT5(自然老化)など、多様な熱処理が可能で、強度や硬度を調整できる。 |
A6063の基本的な特性
特徴 | 詳細説明 |
---|---|
主な合金成分 | アルミニウム、シリコン、マグネシウム |
機械的特性 | 強度は比較的低いが、良好な延性と加工性を持つ。引張強度が約180〜240 MPa、伸びが30%以上(T5硬化状態)。 |
耐食性 | 優れた耐食性を持ち、特に外装材や建築材に適している。 |
加工性 | 切削、圧延、押出しが非常に容易で、複雑な形状の部品も加工可能。 |
主な用途 | 建築用押出材、窓枠、サイディング、内装材。 |
熱処理 | 主にT5(自然老化)状態で使用され、強度はT6に比べて低いが、加工性と外観の美しさが優れている。 |
A6061とA6063の主な違い
化学的組成の違い
成分 | A6061 | A6063 |
---|---|---|
主な成分 | アルミニウム、マグネシウム、シリコン | アルミニウム、シリコン、マグネシウム |
シリコン | 約0.60〜0.90% | 約0.20〜0.60% |
マグネシウム | 約0.80〜1.20% | 約0.45〜0.90% |
銅 | 約0.15〜0.40% | 最大0.10% |
その他 | 少量のクロム(0.04〜0.35%)、鉄(0.70%以下) | 少量のクロム(0.10%以下)、鉄(0.35%以下) |
機械的特性の比較
特徴 | A6061 | A6063 |
---|---|---|
引張強度 | 約260〜310 MPa(T6硬化状態) | 約180〜240 MPa(T5硬化状態) |
伸び | 約12〜17%(T6硬化状態) | 約30%以上(T5硬化状態) |
硬度 | 高い硬度(特にT6処理後) | 比較的低いが、良好な加工性を提供 |
耐久性 | 高い強度と耐久性 | 良好な延性と加工性 |
熱処理とその影響
熱処理状態 | A6061 | A6063 |
---|---|---|
T6 | 溶体化処理後の人工老化、引張強度が最大に、硬度も高い | 使用しない、通常T5が使用される |
T5 | 使用されない | 自然老化処理、加工性が良好で、外観が美しい |
T4 | 溶体化処理後の自然老化、機械的特性がやや劣るが、加工性が良好 | 使用しない |
A6061の特徴と加工性
A6061の物理的特性
特性 | 値 |
---|---|
比重(密度) | 約2.70 g/cm³ |
融点 | 約655°C(1211°F) |
熱伝導率 | 約167 W/mK |
電気伝導率 | 約40% IACS(国際電気伝導率基準) |
線膨張係数 | 約23.1 × 10⁻⁶ /K |
弾性係数(ヤング率) | 約68.9 GPa |
ポアソン比 | 約0.33 |
硬度(ブリネル) | 約95 HB(T6処理後) |
詳細説明
- 比重(密度): A6061の比重はアルミニウム合金として標準的な値で、軽量でありながら高い強度を持ちます。
- 融点: 融点は比較的高く、耐熱性を示しますが、アルミニウム合金の中ではそれほど高くありません。
- 熱伝導率: 高い熱伝導率を持ち、熱を効率的に伝導するため、熱管理が必要な部品に適しています。
- 電気伝導率: 一般的な電気伝導率の40% IACSで、電気的な導電性を持ちますが、銅や銀ほど高くはありません。
- 線膨張係数: 温度変化に対する膨張率を示し、温度変化による寸法変化が予測可能です。
- 弾性係数(ヤング率): 高い弾性係数により、力が加わったときの変形が比較的小さいです。
- ポアソン比: 引っ張り時に横方向の変形が縦方向の変形に対してどう変化するかを示します。
- 硬度(ブリネル): 高い硬度により、摩耗や傷に対する耐性がありますが、加工性と強度のバランスが取れています。
A6061の切削加工性
A6061の概要
A6061は、アルミニウム合金の一種で、主に強度、耐食性、加工性に優れた特性を持っています。以下はA6061の一般的な特性です。- 主な成分: アルミニウム、シリコン、マグネシウム
- 特長: 高強度、良好な耐食性、優れた加工性
- 用途: 自動車部品、航空機部品、建材
切削加工性の特性
特性 | 説明 |
---|---|
加工性 | 良好であり、切削加工が比較的容易。硬化処理(T6など)の状態では加工性が低下することがある。 |
工具摩耗 | 中程度。適切な切削条件を選定することで工具寿命を延ばせる。 |
切削条件 | 高速回転での切削が推奨されるが、加工条件に応じて調整が必要。 |
表面仕上げ | 良好。適切な切削条件下で、表面が滑らかに仕上がる。 |
チップ排出 | 良好。切削中にチップが適切に排出されるため、加工がスムーズ。 |
詳細な説明
- 加工性: A6061は、切削加工において比較的良好な性能を発揮します。特に未処理の状態では加工が容易ですが、熱処理された状態(例えばT6処理)では硬度が上がり、加工が難しくなることがあります。そのため、加工条件を調整することが重要です。
- 工具摩耗: A6061の加工中に工具が摩耗する程度は中程度です。切削速度や送り速度を最適化することで、工具寿命を延ばすことが可能です。通常、超硬工具やコーティングされた工具が推奨されます。
- 切削条件: 高速回転での切削が推奨されることが多いですが、切削条件(回転数、送り速度、切削深さなど)を適切に設定することで、より良い加工結果が得られます。
- 表面仕上げ: A6061は、適切な切削条件下で非常に良好な表面仕上げが可能です。切削液の使用や適切な工具の選定が、さらに良好な仕上がりを実現します。
- チップ排出: 切削中のチップ排出はスムーズで、適切な切削条件であれば、チップが適切に排出され、加工が安定します。これにより、加工中の問題が減少します。
A6061の一般的な使用用途
当然のことながら、アルミニウム合金の選択は、用途に合わせて慎重に行う必要があります。特にA6061とA6063は、似て非なる特性を持っているため、それぞれの違いを理解し選び方を知ることが重要です。A6061は、高い強度と優れた耐食性を持ち合わせており、そのため自動車の部品や航空機の構造材料として一般的に使用されています。さらに、良好な機械加工性を持つため、精密な加工が必要な工業用途にも適しています。一方、A6063は加工性と表面仕上がりの良さが特長で、建築用の窓枠やドア、サッシなどの建材としてよく使われています。これらの具体例を踏まえれば、用途によってA6061とA6063のどちらを選ぶかが明確になります。最終的に、A6061とA6063の違いを理解することで、プロジェクトに最適なアルミニウム合金を選ぶことができるのです。A6063の特徴と加工性
A6063の物理的特性
A6063の概要
A6063は、アルミニウム合金の一種で、主に加工性や耐食性に優れた特性を持つ合金です。一般的に押出し材として使用され、建材や構造部品に広く利用されています。A6063の物理的特性
特性 | 値 |
---|---|
密度 | 約2.70 g/cm³ |
引張強度 | 約160-230 MPa |
伸び | 約8-12% |
硬度 | 約60-70 HRB |
熱伝導率 | 約200 W/m·K |
比熱 | 約0.90 J/g·K |
融点 | 約606°C |
詳細な説明
- 密度: A6063の密度は約2.70 g/cm³で、軽量な材料として知られています。これは、アルミニウム合金全般の特性であり、他の構造材に比べて軽量です。
- 引張強度: 引張強度は約160-230 MPaであり、A6063は比較的低めの強度を持つものの、加工性と耐食性が高く、さまざまな用途で使用されます。
- 伸び: 約8-12%の伸びを持ち、一定の延性を確保しています。これにより、成形や加工がしやすい特性を持っています。
- 硬度: A6063の硬度は約60-70 HRBで、一般的に中程度の硬さを持ちます。これにより、切削加工や成形が比較的容易です。
- 熱伝導率: 約200 W/m·Kの熱伝導率を持ち、良好な熱伝導性を有しています。これにより、熱管理が必要なアプリケーションにも適しています。
- 比熱: 約0.90 J/g·Kの比熱を持ち、熱の蓄積や放出に関する特性も考慮されています。
- 融点: 約606°Cの融点を持ち、高温での使用に対する耐性がありますが、アルミニウム合金の中では比較的低い融点です。
A6063の切削加工性
A6063の概要
A6063は、アルミニウム合金の一種で、特に押出し材として使用されることが多い合金です。良好な加工性と耐食性を持ち、建材や構造部品に幅広く利用されています。切削加工性の特性
特性 | 説明 |
---|---|
加工性 | 非常に良好。容易に加工でき、複雑な形状や精密な部品の製造が可能。 |
工具摩耗 | 中程度。適切な切削条件と工具選定により、工具寿命を長く保つことができる。 |
切削条件 | 高速回転での切削が推奨されるが、加工条件に応じた調整が必要。 |
表面仕上げ | 良好。適切な切削条件で、滑らかで均一な表面仕上げが得られる。 |
チップ排出 | 良好。切削中にチップが適切に排出され、加工がスムーズ。 |
詳細な説明
- 加工性: A6063は切削加工において非常に優れた特性を持ち、複雑な形状や精密な部品の製造が可能です。押出し材として使用されるため、加工しやすく、形状変更や部品製造が容易です。
- 工具摩耗: A6063の切削中に工具が摩耗する程度は中程度です。適切な切削速度や送り速度を選定し、超硬工具やコーティング工具を使用することで、工具寿命を延ばすことができます。
- 切削条件: 高速回転での切削が推奨されますが、具体的な切削条件(回転数、送り速度、切削深さなど)は、材料の状態や加工内容に応じて調整が必要です。
- 表面仕上げ: A6063は適切な切削条件で非常に良好な表面仕上げが可能です。切削液の使用や工具の選定によって、滑らかで均一な仕上がりを実現します。
- チップ排出: 切削中のチップ排出はスムーズで、適切な切削条件であれば、チップが適切に排出され、加工が安定します。これにより、加工中の問題が少なくなります。
A6063の一般的な使用用途
A6061とA6063のアルミニウム合金は多くの点で似ていますが、その違いを理解することは重要です。A6061は一般的に高い強度が求められる用途に使用されます。これは、強度や耐食性がより重視される場合に適しているためです。たとえば、自動車の部品や精密機器によく用いられます。一方、A6063は表面仕上げが重視される用途に適しており、建築材料やインテリアデザインに使用されることが多いです。これは、外観が美しく、加工が容易であるため、特に建築分野で好んで選ばれます。よって、用途に応じてこれらの特性を考慮し、最適なアルミニウム合金を選ぶことが重要です。この理解は、耐久性やコスト効率を考慮したうえで、より適した材料選びに繋がるでしょう。A6061とA6063の適用範囲と選択ガイド
各種プロジェクトにおける適切な選択
アルミニウム合金のA6061とA6063は、似ているようでいて実は特性に違いがあります。A6061は、高い強度と耐食性を備え、要求される耐久性が高いプロジェクトに適しています。例えば、航空宇宙産業や自動車部品などがその用途として挙げられます。一方、A6063は、加工性が良く表面処理が容易なため、建築材料やインテリアデザインによく使用されます。これらは、A6061が一般的にはより高価である一方で、A6063はコスト面で有利であり、それがプロジェクトによってどちらを選ぶかの基準となり得ることを示しています。したがって、プロジェクトの目的や予算に応じて、適切なアルミニウム合金を選択することが重要です。最終的に、A6061とA6063の選び方を理解し、違いを把握することで、より効果的でコスト効率の良い選択をすることができます。耐久性とコストのバランス
A6061とA6063は、どちらもアルミニウム合金であるが、用途に応じて選ぶべき違いがある。A6061は、高い耐蝕性と強度を持つため、航空宇宙産業や建築分野での使用が適している。一方、A6063は加工性に優れ、表面仕上がりが良いことから、建築材料やインテリアデザインに好まれている。 たとえば、A6061は耐久性が求められる場所での建築用材料や自動車部品に使用されることが多い。この合金は、一定の強度を保ちつつも、比較的軽量であるため、効率的な設計が可能である。また、A6063は、より複雑な形状への加工や、美しい外観が必要とされるプロファイル材に適しており、家具や額縁などの装飾品に利用されることが多い。 最終的な選択は、求められる特性とコストのバランスを見極めることが重要である。耐久性が必須ならばA6061、加工性と見た目を重視するならばA6063を選ぶべきである。それぞれの用途に合った材料選びが、望む結果を得るための鍵となる。環境への影響と持続可能性
A6061とA6063の選び方について理解するためには、これらのアルミ合金の違いを知ることが肝心です。A6061は、高い強度と優れた耐食性を持つため、構造材料や自動車の部品などに広く使用されています。それに対し、A6063は表面処理が容易で、特に建築用のアルミニウム材料として好んで選ばれます。A6061は、より加工が難しく、強度が必要な用途に適しているのに対して、A6063は加工性に優れ、仕上がりの美しさを重視する場合に選択されます。例えば、A6061は自転車のフレームなどに用いられ、A6063は建築の窓枠やドアフレームに使用されることが多いです。最終的な用途を考え、それぞれの特徴を生かす形で選ぶことが大切です。アルミニウム選びでは、これらの違いを把握し、目的に合致した素材を選んでください。A6061とA6063の加工方法
表面処理の種類と特徴
A6061とA6063の加工方法
特性 | A6061 | A6063 |
---|---|---|
加工性 | 良好だが、T6処理などの熱処理された状態では加工が難しくなる。 | 非常に良好で、複雑な形状や精密な部品の加工が容易。 |
切削条件 | 高速回転での切削が推奨されるが、加工条件の調整が必要。 | 高速回転での切削が推奨されるが、具体的な条件に応じて調整が必要。 |
工具摩耗 | 中程度で、適切な条件設定と工具選定が重要。 | 中程度で、適切な切削条件と工具選定により寿命を延ばせる。 |
表面仕上げ | 良好で、適切な条件下で滑らかに仕上がる。 | 非常に良好で、均一な表面仕上げが可能。 |
チップ排出 | 良好で、切削中にチップが適切に排出される。 | 良好で、切削中にチップがスムーズに排出される。 |
A6061とA6063の表面処理の種類と特徴
表面処理方法 | A6061の特徴 | A6063の特徴 |
---|---|---|
陽極酸化 | 高い耐食性と耐摩耗性を提供し、表面が硬化します。多様な色付けが可能。 | 高い耐食性と装飾的な外観を提供し、表面が硬化します。色付けも可能で、美観が向上します。 |
電気メッキ | 一般的に使用されるが、耐食性向上のためには陽極酸化が推奨される。 | 同様に使用されるが、耐食性をさらに向上させるためには陽極酸化が推奨される。 |
粉体塗装 | 高い耐久性と装飾性を提供し、厚い塗膜が形成される。 | 高い耐久性と装飾性を提供し、厚い塗膜が形成される。 |
化学的処理 | 特殊な化学処理(例:クロメート処理)で耐食性を向上させる。 | クロメート処理などで耐食性を向上させることが可能ですが、陽極酸化の方が一般的。 |
詳細な説明
- 加工方法:
- A6061: A6061は切削加工において良好な性能を持ちますが、熱処理(T6など)の状態では硬度が上がり、加工が難しくなることがあります。適切な切削条件を設定し、工具選定を行うことが重要です。
- A6063: A6063は、押出し材として多く使われるため、非常に良好な加工性を持ちます。複雑な形状や精密な部品の加工が容易で、適切な切削条件と工具の選定で高品質な仕上がりが得られます。
- 表面処理:
- 陽極酸化: A6061とA6063の両方に対して高い耐食性と耐摩耗性を提供し、外観の美化にも適しています。特にA6063は装飾的な外観が求められる用途で使用されます。
- 電気メッキ: A6061やA6063の表面処理として使用されますが、耐食性を向上させるためには陽極酸化が推奨されます。
- 粉体塗装: A6061とA6063の両方に適用可能で、高い耐久性と装飾性を提供します。厚い塗膜が形成され、耐摩耗性や耐候性が向上します。
- 化学的処理: クロメート処理などが可能ですが、A6061やA6063では陽極酸化が一般的に推奨される処理方法です。
A6061とA6063の溶接と組み立ての考慮事項
溶接の考慮事項
特性 | A6061 | A6063 |
---|---|---|
溶接性 | 良好ですが、熱処理状態によっては難しい場合がある。 | 良好で、一般的に溶接がしやすい。 |
溶接法 | TIG溶接、MIG溶接が推奨される。溶接後の熱処理(T6など)が必要な場合がある。 | TIG溶接、MIG溶接が一般的。 |
熱処理 | 溶接後に再熱処理(T6処理など)が必要な場合が多い。 | 溶接後の再熱処理は通常不要だが、使用条件に応じて考慮する。 |
ひずみ | 溶接時に熱変形が発生しやすいため、適切な冷却や加工後の矯正が必要。 | 熱変形が発生しにくく、比較的安定した溶接が可能。 |
強度低下 | 溶接部での強度低下が見られる場合があり、熱処理で回復することが多い。 | 溶接部の強度低下は少なく、安定した強度を保持する。 |
組み立ての考慮事項
特性 | A6061 | A6063 |
---|---|---|
接合方法 | ボルト接合、リベット接合、溶接が一般的。 | ボルト接合、リベット接合が主に使用される。 |
クリンチング | 必要に応じて行うが、溶接やボルト接合が主流。 | 一般的にクリンチングやリベット接合が使用される。 |
精度 | 高精度の部品が求められるが、加工後の表面仕上げや調整が必要な場合がある。 | 精度が高く、組み立て時の調整が少ない。 |
コスト | 高強度が必要な部品にはコストが高くなる場合がある。 | 比較的低コストでの組み立てが可能。 |
詳細な説明
- 溶接:
- A6061: A6061は良好な溶接性を持ちますが、特に熱処理(T6など)の状態では溶接が難しくなる場合があります。溶接後には再熱処理が必要なことが多く、熱変形や強度低下に注意が必要です。TIG溶接やMIG溶接が推奨され、適切な冷却と加工後の矯正が重要です。
- A6063: A6063は比較的溶接しやすく、溶接後の熱処理は通常不要ですが、使用条件に応じて考慮する必要があります。熱変形が発生しにくく、強度の安定性が高いのが特徴です。
- 組み立て:
- A6061: A6061はボルト接合、リベット接合、溶接などの方法が用いられます。高精度の部品が求められますが、表面仕上げや調整が必要な場合があります。強度が高い一方で、コストが高くなる場合があります。
- A6063: 組み立て時にはボルト接合やリベット接合が主に使用されます。精度が高く、組み立て時の調整が少ないため、比較的低コストでの組み立てが可能です。クリンチングやリベット接合がよく用いられます。
A6061とA6063の類似素材との比較
他のアルミニウム合金との比較
合金 | 主な用途 | 引張強度 | 伸び | 硬度 | 特徴 |
---|---|---|---|---|---|
A2024 | 航空機部品、構造部品 | 約470-520 MPa | 約10-20% | 約120-150 HB | 高強度だが、耐食性が劣る。 |
A7075 | 高強度部品、航空機部品 | 約500-570 MPa | 約8-15% | 約150-160 HB | 非常に高い強度だが、加工性と耐食性が劣る。 |
A5052 | 自動車部品、船舶用部品 | 約240-280 MPa | 約12-25% | 約60-70 HRB | 良好な耐食性と加工性を持つ。 |
A6082 | 機械部品、構造部品 | 約310-350 MPa | 約8-12% | 約80-90 HB | 高い強度と良好な耐食性を持つ。 |
詳細な説明
- A6061とA6063:
- A6061は、強度と耐食性のバランスが取れた合金で、特に強度が高い部品に使用されます。加工性が良好ですが、熱処理後の加工が難しいことがあります。
- A6063は、優れた加工性を持ち、押出し材として多く使用されます。引張強度はA6061に劣りますが、耐食性は非常に良好です。
- A2024:
- 高い強度を持ち、航空機部品などに使用されますが、耐食性はA6061やA6063に比べて劣ります。強度を重視する場合に選ばれます。
- A7075:
- 非常に高い強度を持ち、航空機や高強度部品に使用されますが、加工性と耐食性が劣るため、強度を最優先する用途に向いています。
- A5052:
- 良好な耐食性と加工性を持ち、自動車部品や船舶用部品に使用されます。引張強度はA6061より低いですが、耐食性と加工性が優れています。
- A6082:
- 高い強度と良好な耐食性を持ち、機械部品や構造部品に使用されます。A6061とA6063の中間の特性を持ち、幅広い用途に対応可能です。
A6061とA6063以外の材料選択
A6061とA6063のアルミニウム合金は、それぞれ特有の性質を持っており、使用するアプリケーションによって適した選択が異なることが重要です。A6061は、高い強度と優れた耐食性を持つ一方で、A6063は加工性に優れ、表面処理が容易なため、建築材料や装飾品によく使用されます。たとえば、自動車の部品には衝撃や荷重に耐えるA6061が適していますが、家具や建築の装飾的な要素では、見た目を重視するため、加工しやすいA6063が好まれることがあります。最終的には、A6061もA6063もそれぞれの用途に応じて適した特性を持っており、ユーザーはプロジェクトの要求を慎重に考慮して適切な材料を選ぶ必要があります。特定用途における材料の選択基準
アルミニウム合金のA6061とA6063は、化学成分と機械的性質に微細な違いがあります。この違いが、特定用途における材料の選択基準となります。A6061は、高い引張強度と優れた耐食性を持ち、構造材料や自動車部品、航空機の構造材として広く用いられています。一方、A6063は通常、建築材料や内装デザイン、管材などに利用され、加工性と表面処理の美しさが特徴です。 たとえば、自動車のフレームを製作する場合、強度が必要なためA6061が選ばれる傾向にあります。逆に、アルミサッシや家具などのデザイン性が求められる場合には、A6063が好まれます。このように用途に適したアルミニウム合金を選ぶことが重要であり、その際はそれぞれの特性を理解し選択することが求められます。 最終的に、アルミニウム合金の選択は、その用途の要件に最適なものを選ぶことで、製品の性能や耐久性を最大限に引き出すことができます。A6061とA6063の違いを把握し、目的に応じた材料選びを行うべきです。アルミA6061とA6063を選ぶ際の注意点
購入前のチェックリスト
A6061とA6063のアルミは似ているようでいて実は用途に応じた重要な違いがあります。A6061は強度が高く、機械部品や構造材料に適している一方で、A6063は表面処理がしやすく、建築材料やインテリアデザインに多用されます。たとえば、A6061は自動車のフレームや航空機の部品として、その高い耐久性と耐食性を活かされます。一方、A6063はアルミサッシや家具の装飾部品としてその加工性の良さが求められます。選ぶ際は、使用目的を明確にして、それぞれの特性を理解した上で最適な材料を選びましょう。このように、A6061とA6063はそれぞれ特徴が異なるため、用途に適した材料選びが重要です。コストと品質のトレードオフ
A6061とA6063の違いを理解し、適切なアルミ材の選択が重要です。まずA6061は、強度が高く、耐食性に優れ、加工性も良好であるため、精密機械や構造材に使用されます。一方、A6063は、A6061よりも加工性が優れており、表面仕上がりが良いため、建築の装飾材や家具のアルミ部品に多用されています。具体例を挙げると、A6061は自動車の車体や航空機の部品などに、A6063はドアや窓のフレーム、手すりなどに使用されることが多いです。これらの違いを考慮し、使用目的に合ったアルミ材を選ぶことがコストと品質のバランスを取る上で重要です。適切な材料の選定によって、長期にわたる耐久性と経済性を確保することができます。供給者選びのポイント
A6061とA6063というアルミニウム合金は似ているようでいて異なる特性を持っています。A6061は、強度が高く、耐食性に優れ、加工性が良いことで知られています。一方、A6063は、耐食性に優れ、表面処理の性質が良く、特に陽極酸化処理を施す際に美しい仕上がりが得られます。 具体的な違いを例として挙げれば、A6061は自動車の部品や建築の構造材料としてよく使用されるのに対し、A6063は建築の装飾材料や家具の枠材として使用されることが多いです。このように使われる場面に応じて適したアルミニウム合金を選ぶことが大切です。 選び方のガイドとしては、製品の要求される強度、表面処理の要件、形状加工のしやすさなどを考慮し、それぞれの特性を生かせる材質を選ぶことが重要です。供給者を選ぶ際にはこれらの違いを理解しておき、用途に合ったアルミニウム合金を選びましょう。A6061とA6063の将来と革新
アルミニウム合金の新たな開発
A6061とA6063は、どちらもアルミニウム合金であり、外観上似ているものの実は用途や性質に違いがあります。一般的に、A6061は強度が高く、耐食性に優れているため、航空宇宙産業や自動車の部品など負荷のかかる環境での使用が適しています。対してA6063は、加工性が良く、表面が非常に滑らかになるため建築材料や家具の装飾部品などの見た目が重要な用途に適しています。たとえば、家庭で使われる窓枠やドアノブにA6063が使われるのは、この加工性と美しい仕上がりが理由です。選択する際は、使用目的に応じた強度や加工性を考慮し、それぞれの特性を活かす形で選ぶことが大切です。最終的には、A6061とA6063では目的に応じて適した合金を選ぶべきであり、その違いを理解することが賢明な選択に繋がるでしょう。エコフレンドリーなアルミニウムの利用
A6061とA6063のアルミニウム合金は、工業用材料として広く利用されていますが、それぞれ特徴が異なります。A6061は強度が高く、機械加工性に優れているため、航空機の部品や精密機器に適しています。一方、A6063は加工性に富んでおり、表面処理が容易なため、建築資材やインテリア用途で好んで選ばれます。例えば、A6061は自動車のフレームやバイクの部品として、その耐久性と耐食性を活かしています。A6063は、ドアフレームや窓枠といった建材に使われることが多く、その加工のしやすさから多様なデザインが可能になります。選択する際には、用途に最も適した特性を持つアルミニウム合金を選ぶことが重要です。したがって、A6061とA6063の違いを理解し、それぞれの用途に応じた適切な選択を行うことが、アルミニウムの利用においては不可欠となるのです。業界における技術革新の影響
A6061とA6063のアルミ合金は、類似しているように見えて、それぞれ独自の特性を持っています。A6061は、優れた機械的特性と耐食性を持ち、複雑な形状の押し出しや、精密な加工が必要な用途で広く使用されています。例えば、自動車の部品や建築の構造材料、さらには航空宇宙産業においても採用されることがあります。一方、A6063は表面処理が非常に優れており、特に建築やインテリアデザインでの利用が目立ちます。光沢を出しやすいことから、建物のフレームや家具の装飾材料として選ばれることが多いです。適用する場面に応じて、これらの特性を考慮しながら選択することが大切です。最終的には、それぞれのアルミ合金の特性を理解し、用途に合わせた適切な選択をすることが重要です。まとめ
アルミニウム合金A6061とA6063は似ていますが、微妙な違いがあります。それぞれの特性や適用分野を理解することが重要です。また、適切な選び方を知ることで、製品やプロジェクトに最適な素材を選択することができます。A6061とA6063の特性や適用分野について詳しく解説します。技術者必見!A5052とA5056の化学組成と加工特性の徹底比較
A5052とA5056アルミニウム合金の基礎知識
A5052の化学組成と一般特性
化学組成
成分 | 含有量 (%) |
---|---|
アルミニウム (Al) | 残部(約95% 以上) |
マグネシウム (Mg) | 2.2 – 2.8 |
クロム (Cr) | 0.15 – 0.35 |
鉄 (Fe) | 最大 0.4 |
シリコン (Si) | 最大 0.25 |
銅 (Cu) | 最大 0.1 |
その他 (その他元素) | 各元素の合計最大0.15% |
一般特性
特性 | 詳細説明 |
---|---|
比重 | 約2.68 g/cm³ |
引張強度 | 約 230 MPa (引張強度) |
耐屈曲強度 | 約 200 MPa (耐屈曲強度) |
硬度 | 約 60 HB (ブリネル硬度) |
延性 | 良好な延性を持ち、成形しやすい。 |
耐食性 | 海水や湿気に対する耐食性が高く、腐食しにくい。 |
溶接性 | TIG溶接やMIG溶接に適しており、接合部の強度が高い。 |
熱処理性 | 熱処理による強化は難しく、強度の向上に限界がある。 |
加工性 | 切削、圧延、曲げ加工が容易で、精度の高い部品が得られる。 |
延性 | 高い延性を持ち、加工時の変形が少ない。 |
詳細情報
- 化学組成: A5052は主にアルミニウムを基にし、マグネシウムとクロムを主要な合金成分としています。これにより、高い耐食性と優れた加工性を実現しています。
- 一般特性: A5052は高い引張強度と優れた延性を持ち、加工や溶接が容易です。耐食性が高いため、海水環境や湿気の多い場所での使用に適しています。熱処理による強化には限界があり、熱処理を必要とする用途には不向きです。
A5056の化学組成と一般特性
化学組成
成分 | 含有量 (%) |
---|---|
アルミニウム (Al) | 残部(約94% 以上) |
マグネシウム (Mg) | 5.0 – 5.6 |
クロム (Cr) | 0.10 – 0.35 |
鉄 (Fe) | 最大 0.7 |
シリコン (Si) | 最大 0.30 |
銅 (Cu) | 最大 0.10 |
その他 (その他元素) | 各元素の合計最大0.15% |
一般特性
特性 | 詳細説明 |
---|---|
比重 | 約2.66 g/cm³ |
引張強度 | 約 310 MPa (引張強度) |
耐屈曲強度 | 約 275 MPa (耐屈曲強度) |
硬度 | 約 70 HB (ブリネル硬度) |
延性 | 良好な延性を持ち、加工性が良好。 |
耐食性 | A5056は特に耐食性が高く、海水や化学薬品に対する耐性が優れる。 |
溶接性 | TIG溶接やMIG溶接に適しており、強度の高い接合が可能。 |
熱処理性 | 熱処理による強化が難しく、強度向上に限界がある。 |
加工性 | 加工性が良好で、切削や圧延がスムーズに行える。 |
延性 | 高い延性を持ち、成形しやすい。 |
詳細情報
- 化学組成: A5056は、マグネシウムを多く含み、高い強度と優れた耐食性を持つアルミニウム合金です。クロムを含むことでさらなる耐食性の向上が図られています。
- 一般特性: A5056は、A5052に比べて高い引張強度を持ち、特に高ストレスの環境に適しています。耐食性が非常に高く、海水や化学薬品に対する耐性が優れていますが、熱処理による強化は難しい点に注意が必要です。加工性も良好で、精密な部品製造が可能です。
アルミニウム合金の分類と基準
アルミニウム合金の分類
カテゴリー | 系列 | 特徴 | 代表例 | 用途 |
---|---|---|---|---|
主合金 | 1000系列 | 高純度、主に加工性と耐食性が良い | A1050、A1100 | 食品包装、化学設備 |
合金 | 2000系列 | 銅を含み、高強度 | A2024 | 航空機部品、車両部品 |
3000系列 | マンガンを含み、耐食性と加工性が良い | A3003 | 自動車部品、冷蔵庫部品 | |
4000系列 | シリコンを含み、耐摩耗性が優れる | A4032 | エンジン部品、耐摩耗部品 | |
5000系列 | マグネシウムを含み、耐食性が良好 | A5052、A5083 | 船舶部品、建築材料 | |
6000系列 | マグネシウムとシリコンを含み、バランスの取れた特性 | A6061 | 機械部品、構造材 | |
7000系列 | 亜鉛を含み、高強度 | A7075 | 軍事用途、航空宇宙部品 | |
8000系列 | その他の元素を含む特殊合金 | A8090 | 電気ケーブル、包装材料 |
基準と規格
基準 | 説明 | 用途 |
---|---|---|
JIS(日本工業規格) | 日本国内での合金材料の規格と試験方法 | 日本国内での材料規格 |
ASTM(アメリカ材料試験協会) | アメリカでの合金材料の規格と試験方法 | アメリカ国内および国際規格 |
ISO(国際標準化機構) | 国際的な標準規格で、世界中で通用する | 世界的な材料規格 |
EN(欧州規格) | ヨーロッパでの合金材料の規格と試験方法 | ヨーロッパでの材料規格 |
A5052とA5056の化学組成の比較
主要成分の比較
成分 | A5052 | A5056 |
---|---|---|
アルミニウム (Al) | 残部 | 残部 |
マグネシウム (Mg) | 2.2% – 2.8% | 4.5% – 5.5% |
銅 (Cu) | 最大0.10% | 最大0.10% |
マンガン (Mn) | 最大0.10% | 最大0.10% |
シリコン (Si) | 最大0.25% | 最大0.30% |
クロム (Cr) | 0.15% – 0.35% | 0.05% – 0.20% |
亜鉛 (Zn) | 最大0.10% | 最大0.10% |
鉄 (Fe) | 最大0.40% | 最大0.50% |
詳細な比較
- A5052:
- マグネシウム: 2.2% – 2.8% で、軽量で耐食性が高い特性を持つ。加工性も良好。
- クロム: 0.15% – 0.35% で、耐食性を向上させる。
- シリコン: 最大0.25% で、耐摩耗性を向上させる効果がある。
- A5056:
- マグネシウム: 4.5% – 5.5% で、A5052よりも高い強度を提供する。耐食性も非常に高い。
- クロム: 0.05% – 0.20% で、耐食性がさらに向上している。
- シリコン: 最大0.30% で、加工性や耐摩耗性が改善される。
微量成分の影響
技術者がアルミニウム合金の選択に際して重視すべきポイントは、材料の化学組成と加工特性の理解です。A5052とA5056は、その微細な化学組成の違いによって、加工特性に顕著な差が生じています。具体的にA5052はマグネシウム含有量が2.2-2.8%と比較的少なく、優れた耐食性と成形性を有しているため、海水での使用や複雑な形状が要求される部品に適しています。一方A5056はマグネシウム含有量が4.5-5.6%と高く、高い強度を持つ一方で成形性は劣るため、強度が要求される構造部材や高応力部品に用いられることが多いです。従って、その用途に最も適した材料を選ぶためには、化学組成と加工特性を総合的に比較検討することが不可欠です。このように、微量成分が材料の性能に大きく影響をもたらすことを認識し、適切な選択を行うことが、技術者にとって重要となります。合金化元素の役割
A5052とA5056は、いずれもアルミニウム合金の一種であり、その化学組成と加工特性には顕著な違いがあります。主に、これらの合金は海洋構造物や輸送用機器部材に使用され、その理由は耐食性と加工性に優れる点にあります。 A5052合金はマグネシウムを2.2から2.8%含有しており、優れた耐食性を持つ一方で、A5056合金はマグネシウムを含む割合が4.5から5.6%と高く、さらに優れた強度と耐食性を誇ります。特に、A5056は高い強度が求められる海洋関連の用途に適しています。 具体例を挙げると、A5052は加工性が良いため、曲げ加工やフレーム製作に適しています。一方、A5056は、高い張力に耐えることが求められる船体や圧力容器などに使用されることが多いです。 このような特性から、A5052とA5056の選択はその用途に大きく左右されると言えます。耐食性と加工性を優先する場合はA5052が、高い強度を要する用途ではA5056が適しているという結論に至ります。A5052とA5056の加工特性
加工方法の選定
A5052とA5056の化学組成と加工特性には、細かい違いがあります。これらの差異を理解することは、材料選定や加工方法の決定において極めて重要です。A5052は、耐食性に優れ、加工しやすい特徴を持ちます。これは、アルミニウムとマグネシウムを主成分とし、特にマグネシウムの含有量が適度であるためです。一方、A5056はマグネシウムの含有量が高く、強度が高いという特性を持っていますが、A5052に比べて加工性は若干落ちるとされます。 たとえば、A5052は冷間加工が容易であり、自動車の内装部品や建築材料などに利用されます。A5056は航空機の部品や高強度を必要とする構造物に用いられることが多いです。このように、それぞれの特性を踏まえた上で、用途や加工方法に応じて最適なアルミニウム合金を選択することが肝要です。 結論として、A5052は加工性と耐食性を重視する場合に、A5056は強度が求められる用途に適していると言えます。適材適所にこれらの素材を選択することで、製品の品質と性能を最大限に引き出すことが可能になります。成形加工性の比較
特徴 | A5052 | A5056 |
---|---|---|
延性 | 良好。複雑な形状や大面積の成形が可能。 | 良好だが、A5052よりもやや硬いため、成形時に工夫が必要。 |
冷間加工性 | 優れており、冷間圧延や打抜き加工が容易。 | 冷間加工性は良好だが、A5052に比べて難易度がわずかに高い。 |
加工性の容易さ | 加工性が高く、鋳造や切削もスムーズに行える。 | 加工性は良好だが、A5052よりもやや難易度が高い場合がある。 |
成形時の変形量 | 加工中の変形が少なく、高精度な製品が得られる。 | 変形量は少ないが、A5052よりも少し多い可能性がある。 |
熱間加工性 | 熱間加工にも適しており、加工中の強度低下が少ない。 | 熱間加工も可能だが、A5052よりも熱間加工時に注意が必要。 |
接合性 | TIG溶接やMIG溶接が容易で、接合部の強度が高い。 | TIG溶接やMIG溶接に適しているが、A5052に比べてやや難しい。 |
詳細な比較
- A5052:
- 延性: 高い延性により、複雑な形状の部品や大面積の製品が成形しやすい。
- 冷間加工性: 冷間圧延や打抜き加工が非常にスムーズで、設計の自由度が広がる。
- 加工性の容易さ: 切削や鋳造も容易で、高精度な部品が得られる。
- A5056:
- 延性: 延性は良好だが、A5052よりも若干硬いため、成形時に注意が必要。
- 冷間加工性: 冷間加工も可能だが、A5052よりも難易度がわずかに高い。
- 加工性の容易さ: 加工性は良好だが、加工時にA5052よりもやや困難な場合がある。
溶接性の評価
溶接性の比較
特徴 | A5052 | A5056 |
---|---|---|
TIG溶接 | 良好。TIG溶接において安定した溶接が可能で、溶接後の機械的特性も良好。 | 良好。TIG溶接でも安定した接合が可能だが、若干の技術が必要。 |
MIG溶接 | 良好。MIG溶接も容易で、溶接部の強度が高い。 | 良好。MIG溶接にも対応しており、強度が高い接合が可能。 |
溶接後の特性 | 溶接後の機械的特性が優れており、接合部の強度が高い。 | 溶接後も高い機械的特性を維持するが、溶接技術がやや要求される。 |
焼きなまし | 焼きなまし処理が可能で、溶接部の応力を緩和できる。 | 焼きなまし処理も可能で、応力緩和が行えるが、処理条件が異なる。 |
溶接時の変色 | 溶接時の変色が少なく、美しい仕上がりが得られる。 | 溶接時の変色が発生する可能性があり、注意が必要。 |
詳細な比較
- A5052:
- TIG溶接: 高い安定性と優れた機械的特性を持ち、溶接部の強度が保たれるため、品質の高い接合が実現できる。
- MIG溶接: 操作が容易で、高い強度の接合が可能。溶接部の品質も良好。
- 焼きなまし: 焼きなまし処理によって溶接部の応力を緩和し、さらに強度を高めることができる。
- A5056:
- TIG溶接: TIG溶接でも高い性能を発揮するが、A5052よりも溶接技術が若干要求される場合がある。
- MIG溶接: MIG溶接にも適しており、高強度の接合が可能。溶接後の機械的特性も良好。
- 焼きなまし: 焼きなまし処理も可能で、応力緩和が行えるが、処理条件の違いに注意が必要。
A5052とA5056の使用用途
各合金の適用分野
A5052とA5056の化学組成と加工特性は、それぞれ独特な特徴を有しており、適用分野に違いがあります。A5052は、マグネシウムを2.2~2.8%含有する合金で、優れた耐食性と加工性、そして低温での強度も保持する特徴があります。これに対して、A5056はマグネシウム含有量が4.5~5.6%と高く、さらに高い強度と優れた耐海水性を持ちます。たとえば、A5052は自動車の部品や建築材料に適しているのに対し、A5056は船舶や高負荷がかかる構造物により適しています。そのため、A5052は成型性を重視する場面で、A5056は高強度が求められる用途で選ばれる傾向があります。最終的に、どちらの材料を使用するかは、製品の用途と要求される性能によって決定されるべきです。実用例とその理由
技術者の皆様が材料選定に際して、A5052とA5056の違いを理解することは、製品の性能や加工性を最大限に引き出す上で重要です。A5052は優れた耐食性を持ちながら加工性も高く、一般的なプレス成形や曲げ加工に適しています。たとえば、建築物の装飾材や照明器具によく使用されます。一方、A5056は強度が特に高く、海洋関連の部品や高強度を必要とする構造材に適しているのが特徴です。このようにA5052とA5056はそれぞれ異なる特性を持ち、使用用途に応じて選択が重要です。最終的に、これらの違いを踏まえた上で、目的に合ったアルミニウム合金を選定することが、製品の品質とコスト効率を両立させるカギとなるでしょう。A5052とA5056の類似素材との違い
近似合金との物理的特性比較
特徴 | A5052 | A5056 | A6061 | A7075 |
---|---|---|---|---|
主な用途 | 自動車パネル、建築材料、電子機器筐体 | 船舶部品、高ストレス構造材料 | 機械部品、航空機部品、構造材 | 航空機部品、軍事用途、高強度部品 |
耐食性 | 高い耐食性。海水や湿気に対する耐性が優れている。 | さらに高い耐食性。特に海水に対して優れている。 | 中程度の耐食性。表面処理で改善可能。 | 比較的低い耐食性。防食処理が必要。 |
強度 | 中程度の強度。通常の構造材料として使用。 | 高い強度。高ストレス環境に対応。 | 中程度の強度。良好な機械的特性を持つ。 | 高い強度。特に引張強度に優れている。 |
延性 | 良好な延性。加工や成形が容易。 | 良好な延性。成形や加工も比較的容易。 | 良好な延性。機械加工しやすい。 | 限られた延性。加工が難しい場合がある。 |
溶接性 | 良好。TIG、MIG溶接に適しており、高品質の接合が可能。 | 良好。TIG、MIG溶接に適しており、強度の高い接合が可能。 | 良好。TIG、MIG溶接が可能で、機械的特性を保持。 | 良好。TIG、MIG溶接可能だが、技術が要求される。 |
熱処理性 | 熱処理による強化が難しい。硬度や強度の向上に限界。 | 熱処理による強化が難しいが、高強度を持つ。 | 熱処理により強度向上が可能。 | 熱処理により高い強度を得ることができる。 |
密度 (g/cm³) | 約2.68 | 約2.68 | 約2.70 | 約2.81 |
引張強度 (MPa) | 約215 | 約260 | 約310 | 約570 |
伸び (%) | 約12 | 約8 | 約12 | 約11 |
詳細な比較
- A5052:
- 用途: 自動車部品や建築材料に適しており、耐食性の高い部品を提供する。
- 耐食性: 海水や湿気に対する耐性があり、様々な環境条件に対応可能。
- 強度: 中程度の強度で、一般的な構造材料として使用される。
- 延性と加工性: 良好な延性で加工が容易。複雑な部品や形状の成形がスムーズ。
- 溶接性: TIGやMIG溶接が適しており、高い接合品質を保持する。
- A5056:
- 用途: 高ストレス環境や船舶部品など、強度が重要な用途に適している。
- 耐食性: A5052よりもさらに高い耐食性を持ち、特に海水環境で優れる。
- 強度: 高い強度を持ち、強い荷重に耐える能力がある。
- 延性と加工性: 延性も良好で加工が容易だが、若干の技術が必要な場合がある。
- 溶接性: TIGやMIG溶接に適し、高い接合強度を維持する。
- A6061:
- 用途: 航空機部品や機械部品など、強度と加工性が求められる場面で使用される。
- 耐食性: 中程度の耐食性で、表面処理により改善可能。
- 強度: 良好な強度を持ち、熱処理によりさらなる強化が可能。
- 延性と加工性: 良好な延性で、機械加工しやすい。
- 溶接性: TIGやMIG溶接が可能で、機械的特性を保持。
- A7075:
- 用途: 高強度が要求される航空機部品や軍事用途で使用される。
- 耐食性: 比較的低い耐食性で、防食処理が必要。
- 強度: 非常に高い強度を持ち、特に引張強度が優れている。
- 延性と加工性: 限られた延性で、加工が難しい場合がある。
- 溶接性: TIGやMIG溶接が可能だが、高い技術が要求される場合がある。
選定における考慮点
A5052とA5056は、アルミニウム合金の一種であり、それぞれに特徴があります。A5052は、優れた耐食性を持っているため、海水や化学薬品に触れる環境での使用に適しています。一方、A5056は、A5052よりも高い強度を誇り、特に高張力が求められる構造材料に適しています。例えば、船舶の部品や圧力容器など、強度が要求される製品に良く使用されます。 加工特性においても両者に違いがあります。A5052は成形性に優れ、複雑な形状への加工が可能ですが、A5056は硬度が高いため加工が難しい面があります。しかし、A5056は溶接性に優れており、その点でA5052を上回ります。 結論として、A5052は耐食性と成形性が求められる場合に適しており、A5056は強度と溶接性が重要視される用途に適しています。それぞれの特性を理解し、使用目的に応じて適切な合金を選定することが重要です。A5052とA5056のアルマイト処理とその違い
アルマイト処理の基礎
アルマイト処理とは
特徴 | 詳細説明 |
---|---|
定義 | アルミニウム表面に酸化膜を形成し、耐食性や耐摩耗性を向上させる処理方法。美化や絶縁性の向上も目的。 |
処理のプロセス
ステップ | 詳細説明 |
---|---|
前処理 | 洗浄: 表面の汚れや油分を取り除く。 エッチング: 酸化膜や不純物を除去し、表面を粗くする。 |
酸化処理 | 電解酸化: 電流を流し、酸化膜を形成。一般的には硫酸を使用。 膜の厚さ: 5〜25μmに調整可能。 |
後処理 | 封孔処理: 酸化膜の孔を閉じ、耐食性を向上。 着色: 必要に応じて色を付ける。 |
アルマイト処理のメリット
メリット | 詳細説明 |
---|---|
耐食性の向上 | アルミニウムの自然酸化膜よりも強固で、塩水や酸性環境にも耐える。 |
耐摩耗性の向上 | 表面の硬度が増し、摩耗や傷に強くなる。 |
絶縁性の向上 | 電気絶縁体として使用可能。 |
外観の美化 | 光沢や色を調整することで、美しい外観を持たせる。 |
アルマイト処理の限界
限界 | 詳細説明 |
---|---|
引張強度の低下 | 極端な条件下で強度が低下する可能性がある。 |
均一性の問題 | 複雑な形状や厚さの均一性に問題が生じることがある。 |
コスト | 高品質な処理はコストが高くなる場合がある。 |
使用される分野
分野 | 詳細説明 |
---|---|
航空機 | 軽量で耐食性が求められる部品に使用。 |
自動車 | 外装部品や耐摩耗性が求められる部品に使用。 |
建材 | 外装パネルや構造部材などに利用される。 |
電子機器 | 絶縁性が求められる部品や外装に使用される。 |
A5052とA5056のアルマイト性の比較
特徴 | A5052 | A5056 |
---|---|---|
アルマイト性 | 良好なアルマイト性を持ち、均一な酸化膜が形成されやすい。 | アルマイト性は良好だが、A5052に比べて膜の均一性がやや劣ることがある。 |
酸化膜の厚さ | アルマイト処理後の膜厚は5〜25μmで、適切な厚さに調整可能。 | 同様に5〜25μmで調整可能。ただし、膜厚の均一性に若干の差が出ることがある。 |
耐食性の向上 | 酸化膜により、耐食性が大幅に向上し、特に海水や湿気の多い環境での耐久性が高い。 | 酸化膜の耐食性は高いが、A5052よりも耐食性が若干劣る場合がある。 |
耐摩耗性の向上 | 酸化膜がしっかりと形成され、耐摩耗性が向上。 | 酸化膜の耐摩耗性も高いが、A5052と比較して耐摩耗性がやや劣る場合がある。 |
外観の美化 | 光沢や色の調整が可能で、美しい外観を持たせることができる。 | 外観の美化も可能だが、膜の均一性に差が出ることがあるため、外観の仕上がりに影響が出る場合がある。 |
コスト | アルマイト処理のコストは比較的低めで、広く利用されている。 | コストはA5052と比較して若干高めになることがあるが、高強度が求められる用途には適している。 |
比較の要点
- アルマイト性の良好さ: A5052は均一な酸化膜を形成しやすく、耐食性と耐摩耗性が高い。A5056も良好なアルマイト性を持つが、膜の均一性や耐食性で若干の差が見られる。
- 膜の厚さと耐食性: 両方の合金で膜の厚さは調整可能だが、A5052の方が均一な膜形成が得られることが多い。
- 外観の美化とコスト: A5052はコストが比較的低く、外観の美化も容易。A5056は高強度を持ちつつも、外観仕上がりやコストに若干の違いがある。
アルミニウム合金選定のための総合的アドバイス
製品設計における材料選定のポイント
製品設計における材料選定において、A5052とA5056というアルミニウム合金の選択は重要なポイントとなります。これらの合金は化学組成と加工特性において違いがあり、用途に応じて適切な選択が求められます。まず、A5052はマグネシウムを2.2〜2.8%含む合金で、優れた耐食性と加工性を持ち、特に冷間加工が容易であることが特徴です。これに対し、A5056はマグネシウムを4.5〜5.6%含み、より高い強度を持ちながらも良好な耐食性を保持していますが、加工性はA5052に劣る面があります。例えば、海水にさらされる製品には、耐食性が高いA5056が適していますが、複雑な形状に加工する必要がある場合はA5052の選択が優れています。結論として、製品の用途や必要とされる特性を総合的に考え、A5052とA5056の特性を比較検討し選定することが重要です。コストと性能のバランス
技術者にとって材料選択は非常に重要ですが、アルミ合金A5052とA5056の違いを理解することは、最適な選択をする上で不可欠です。特にA5052は耐食性に優れ、A5056はその高い強度が魅力です。これらの特性は、化学組成の違いに起因します。例えば、A5052にはマグネシウムが2.2-2.8%含まれているのに対し、A5056は4.5-5.6%と高濃度です。このため、A5056は、より高い強度を必要とする航空機の部品やマリン用途に適しています。 一方で、加工特性にも注目が必要です。A5052は良好な成形性を持ち加工が容易なため、プレス成形などに使用されることが多いです。また、A5056は加工硬化が早く、特に冷間加工時には注意が必要とされます。しかし、適切な加工方法を選ぶことで、この合金も高い性能を引き出すことが可能です。従って、コストと性能のバランスを考慮した上で、用途に応じた適切な材料選択が求められます。A5052とA5056の特性をよく理解し、それぞれの優れた特性を活かすことで、製品の品質と経済性を高めることができるのです。総合的な材料選定の戦略
A5052とA5056はアルミニウム合金として広く利用されており、その適用の違いを知ることは技術者にとって重要です。A5052は良好な耐食性を有し、海洋関連の部材やタンクなどに使われます。加工性に優れる点もまた、この合金が選ばれる理由です。一方、A5056は強度が高く、特に航空宇宙産業や自動車業界での需要が高いです。これは、A5056の合金に含まれるマグネシウムの量が多いためです。 具体的には、A5052にはマグネシウムが2.2-2.8%含まれているのに対し、A5056では4.5-5.6%と大きく異なります。これによって、A5056のほうが硬度が増すとともに、耐熱性にも優れているのです。しかし、これが加工時の難しさを増すことも忘れてはならず、特に加工温度や工具の選定には注意が必要となります。 結論として、A5052とA5056の選択は用途に応じて慎重に行う必要があります。例えば、海洋部品で耐食性を最優先する場合はA5052が、強度が求められる航空宇宙や車両部品ではA5056が適しています。技術者は、これらの化学組成と加工特性を十分に理解し、最適な材料を選定することが求められます。まとめ
A5052とA5056は、どちらもアルミニウム合金の一種であり、それぞれ異なる化学組成と加工特性を持っています。これらの材料は、航空機や自動車、造船などの産業で幅広く使用されています。A5052は耐食性に優れ、一方でA5056は溶接性に優れています。これらの特性を理解することで、それぞれの材料を適切に選択し、最適な加工方法を選ぶことができます。技術者がこれらの違いを理解し、適切に活用することで、製品の品質向上やコスト削減につながる可能性があります。アルミニウム合金A5052とA5056の性質の違いと選び方
アルミニウム合金とは
アルミニウム合金とはアルミニウム合金の基本的理解
特徴 | 説明 |
---|---|
成分 | アルミニウムに他の元素(銅、マグネシウム、シリコンなど)を加えた合金です。 |
種類 | 主に2つのカテゴリがあり、鋳造合金(例:AC4A)と圧延合金(例:6061)があります。 |
特性 | – 軽量: 比重が小さく、軽量な部品の製造に適しています。 – 耐食性: 自然に酸化皮膜を形成し、腐食に強い。 – 機械的強度: 合金の種類により、高い強度を持つものもあります。 – 加工性: 軽量で加工しやすく、成形や切削が容易です。 |
用途 | – 自動車産業: 車体やエンジン部品。 – 航空産業: 機体や構造部品。 – 建設業: 窓枠やドアフレーム。 – 電気機器: 放熱器や電線。 |
処理方法 | 熱処理(例:T6処理)や表面処理(例:陽極酸化)などが行われ、特性が強化されます。 |
アルミニウム合金の分類と一般的な用途
アルミニウム合金の分類
分類 | 特徴 | 主な合金例 |
---|---|---|
シリーズ | アルミニウム合金は、特定の合金元素によって分類され、主に1000番台から7000番台までがあります。 | 1000系, 2000系, 3000系, 4000系, 5000系, 6000系, 7000系 |
鋳造合金 | 鋳造用に調整された合金で、鋳造時の流動性や強度が特化されています。 | AC4A, AC7A |
圧延合金 | 主に押出しや圧延で使用される合金で、建材や部品の製造に用いられます。 | 6061, 7075 |
一般的な用途
合金系列 | 用途 |
---|---|
1000系 | – 一般工業用途: コイル、シート、板 – 電気機器: 電線やケーブル |
2000系 | – 航空機産業: 高強度部品 – 機械部品: 構造部品やシャーシ |
3000系 | – 建築用材料: 窓枠、屋根材 – 食品容器: 缶詰や包装材料 |
4000系 | – 自動車部品: シリンダーヘッド – 鋳造部品: エンジン部品 |
5000系 | – 船舶産業: 船体や構造部材 – 建材: 外装パネルやサイディング |
6000系 | – 構造部材: 構造梁や支柱 – 建設用部品: アルミニウムフレーム |
7000系 | – 航空機産業: 高強度部品 – スポーツ用品: 自転車フレームやゴルフクラブ |
アルミニウム合金の選定方法と特性
アルミニウム合金A5052とA5056は、それぞれ異なる特性を持っており、用途に応じて選定することが重要です。A5052合金は一般的に優れた耐蝕性を持ち、海水や化学薬品に強いため、食品工業や建築材料としての利用が適しています。一方、A5056合金はA5052よりも高い強度を有し、特に機械的性質が求められる航空機の部品やスポーツ用品に用いられます。 例として、船舶の部材では海水の影響を受けやすいため、耐蝕性が必要です。この場合、A5052が適するでしょう。しかし、高強度が要求されるクライミング用具などは、A5056が適しています。 したがって、アルミニウム合金を選択する際は、その用途に最適な合金の特性を理解し、適切なものを選ぶことが肝心です。用途に応じた正しいアルミニウム合金の選定が、製品の性能と寿命に直結するため、特性の違いを把握することは非常に重要です。A5052合金の特性
A5052の化学組成と特性
化学組成
成分 | 含有量 (%) |
---|---|
アルミニウム | 残部 (主成分) |
マグネシウム | 2.2 – 2.8 |
クロム | 0.15 – 0.35 |
銅 | 最大 0.10 |
鉄 | 最大 0.40 |
シリコン | 最大 0.25 |
その他 | 各成分が最大で0.05以下 |
特性
特性 | 内容 |
---|---|
機械的特性 | – 引張強度: 約 210 – 230 MPa – 降伏強度: 約 140 – 150 MPa – 伸び: 約 12 – 20% |
耐食性 | – 良好な耐食性を持ち、海洋環境や化学薬品にも耐える |
加工性 | – 良好な加工性を持ち、溶接、切削、圧延などが容易 |
耐熱性 | – 最大使用温度は約 65 – 75°C – 高温下での機械的特性の維持が可能 |
硬さ | – 約 60 – 75 HB (ブリネル硬さ) |
耐摩耗性 | – 良好な耐摩耗性を持ち、一般的な使用条件下での摩耗に耐える |
密度 | – 約 2.68 g/cm³ |
A5052の主な用途と加工性
主な用途
用途 | 詳細説明 |
---|---|
船舶部品 | – 海洋環境に強い耐食性を活かして、船体やボートの構造材、船舶用タンクなどに使用されます。 |
化学機器 | – 化学薬品に対する耐性を活かし、タンクや配管、反応容器などの製造に利用されます。 |
自動車部品 | – 軽量で強度があり、特に車両の外装部品やフューエルタンクなどに使われます。 |
航空機部品 | – 軽量で高強度な特性を活かして、航空機の部品や構造材に使用されることがあります。 |
建築材料 | – 外装パネルや装飾材、建物のファサードに利用されます。 |
機械部品 | – 機械のフレームやカバーなど、多用途にわたって使用されることがあります。 |
加工性
加工方法 | 詳細説明 |
---|---|
切削加工 | – 良好な切削性を持ち、フライス加工や旋盤加工が容易です。 |
溶接 | – アルミニウム合金用の適切な溶接手法(TIG溶接やMIG溶接など)で溶接が可能です。 |
圧延 | – 冷間圧延や熱間圧延が可能で、薄板やシートなどの製造に適しています。 |
曲げ加工 | – 良好な曲げ性を持ち、板材やシートの曲げ加工が容易です。 |
成形 | – 圧延や押出し成形が可能で、複雑な形状の部品も製造できます。 |
研磨 | – 表面の研磨がしやすく、外観を美しく仕上げることができます。 |
A5056合金の特性
A5056の化学組成と特性
化学組成
成分 | 含有量(%) |
---|---|
アルミニウム (Al) | 余分(99.0%以上) |
マグネシウム (Mg) | 5.0 – 6.0 |
クロム (Cr) | 0.10 – 0.35 |
銅 (Cu) | 最大 0.10 |
マンガン (Mn) | 最大 0.10 |
シリコン (Si) | 最大 0.10 |
鉄 (Fe) | 最大 0.40 |
その他の成分 | 残余 |
特性
特性 | 詳細説明 |
---|---|
耐食性 | – 高い耐食性を持ち、海洋環境や化学薬品に対して優れた耐性があります。 |
強度 | – 強度が高く、耐荷重性に優れています。 |
延性 | – 良好な延性を持ち、成形や加工が容易です。 |
耐摩耗性 | – 摩耗に対して高い耐性を持ち、長期間使用しても安定した性能を維持します。 |
溶接性 | – 良好な溶接性があり、特にTIG溶接やMIG溶接に適しています。 |
熱処理性 | – 一部の合金と比べて熱処理による強化が難しいですが、適切な処理により特性が改善されます。 |
加工性 | – 切削加工や圧延加工が容易で、複雑な部品の製造が可能です。 |
外観 | – 良好な外観仕上げが可能で、美しい表面仕上げを提供します。 |
A5056の主な用途と加工性
主な用途
特徴 | 詳細説明 |
---|---|
船舶部品 | A5056は海水や過酷な環境に強く、耐食性が非常に高いため、船舶の部品として使用されることが多い。 |
高ストレス構造材 | 高い強度を持ち、機械部品や高ストレス環境での使用に適している。例えば、橋梁や機械の構造材として利用される。 |
軍事用途 | 高い強度と耐食性が求められる軍事用途に適しており、装甲部品やその他の高ストレス部品に使用される。 |
- 主な用途の詳細:
- 船舶部品: 高い耐食性により、船舶の部品に適しており、長期間の海水曝露に耐えることができるため、耐久性が求められる船舶の部品に使用されます。
- 高ストレス構造材: 高い強度を活かして橋梁や機械部品など、重い荷重やストレスを受ける構造材として利用されます。
- 軍事用途: 強度と耐食性が求められる軍事用途において、装甲部品や高ストレス環境での使用に適しています。
加工性
特徴 | 詳細説明 |
---|---|
溶接性 | TIG溶接やMIG溶接が可能で、接合部の強度が高い。ただし、溶接後の後処理が必要な場合がある。 |
切削性 | 高強度のため、切削加工が難しい場合があるが、適切な工具と条件で加工が可能。 |
成形性 | 高強度により成形が難しいことがあるが、設計と加工方法を工夫することで成形可能。 |
- 加工性の詳細:
- 溶接性: TIG溶接やMIG溶接が可能で、強度の高い接合部が得られますが、溶接後の後処理が必要な場合があります。
- 切削性: 高強度により切削加工が難しくなることがありますが、適切な工具と条件で加工が可能です。
- 成形性: 高強度により成形が難しいことがありますが、設計と加工方法を工夫することで成形が可能です。
A5056合金のメリットと限界
メリット
特徴 | 詳細説明 |
---|---|
優れた耐食性 | A5056は海水や過酷な環境に対する耐食性が非常に高い。腐食による劣化が少なく、長期間の使用が可能。 |
高い強度 | A5052よりも高い強度を持ち、機械部品や構造材としての使用に適している。強い荷重やストレスにも耐えられる。 |
- メリットの詳細:
- 優れた耐食性: 海水や過酷な環境に対する耐食性が高く、腐食による劣化が少ないため、長期間の使用が可能です。
- 高い強度: 機械部品や構造材としての使用に適しており、高い荷重やストレスにも耐えられます。
限界
特徴 | 詳細説明 |
---|---|
加工の難しさ | 高強度のため、加工が難しい場合がある。特に切削や成形には注意が必要。 |
コストの高さ | 他のアルミニウム合金に比べてコストが高い場合がある。コストと性能のバランスを考慮する必要がある。 |
- 限界の詳細:
- 加工の難しさ: 高強度のため、加工が難しくなることがあり、特に切削や成形には注意が必要です。
- コストの高さ: 他のアルミニウム合金に比べてコストが高いことがあり、コストと性能のバランスを考慮する必要があります。
A5052とA5056の違い
化学組成の比較
成分 | A5052 | A5056 |
---|---|---|
アルミニウム (Al) | 残部 | 残部 |
マグネシウム (Mg) | 2.2% – 2.8% | 5.0% – 5.6% |
クロム (Cr) | 0.15% – 0.35% | 0.15% – 0.35% |
鉄 (Fe) | 最大 0.7% | 最大 0.7% |
銅 (Cu) | 最大 0.1% | 最大 0.1% |
マンガン (Mn) | 最大 0.1% | 最大 0.1% |
シリコン (Si) | 最大 0.25% | 最大 0.25% |
ゼル (Zn) | 最大 0.1% | 最大 0.1% |
詳細情報
- A5052:
- マグネシウム (Mg): 2.2% – 2.8%。中程度のマグネシウム含有量が特徴で、耐食性や機械的特性をバランスよく提供します。
- クロム (Cr): 0.15% – 0.35%。耐食性を向上させる役割があります。
- A5056:
- マグネシウム (Mg): 5.0% – 5.6%。より高いマグネシウム含有量により、高い強度と耐食性を提供します。
- クロム (Cr): 0.15% – 0.35%。耐食性を強化するために使用されています。
- マグネシウムの含有量: A5056はA5052よりも高いマグネシウム含有量を持ち、より高い強度と耐食性を提供します。
- 用途の違い: A5052は一般的な耐食性や加工性が重視される用途に対して、A5056はより高い強度と耐食性が要求される環境で使用されます。
機械的性質の比較
性質 | A5052 | A5056 |
---|---|---|
引張強さ (Tensile Strength) | 約 230 MPa – 260 MPa | 約 290 MPa – 350 MPa |
伸び (Elongation) | 約 12% – 20% | 約 8% – 12% |
硬度 (Hardness) | 約 60 – 75 HB | 約 70 – 90 HB |
屈曲強さ (Yield Strength) | 約 150 MPa – 210 MPa | 約 260 MPa – 310 MPa |
引張り強さの割合 (Ultimate Tensile Strength Ratio) | 約 0.9 – 1.0 | 約 1.1 – 1.3 |
詳細情報
- 引張強さ (Tensile Strength):
- A5052: 約 230 MPa – 260 MPa。中程度の強度で、一般的な構造部品や自動車部品に適しています。
- A5056: 約 290 MPa – 350 MPa。高い引張強さを持ち、より強度が求められる用途に適しています。
- 伸び (Elongation):
- A5052: 約 12% – 20%。高い伸び性があり、成形や加工が容易です。
- A5056: 約 8% – 12%。伸びはやや低めで、高強度に対するトレードオフです。
- 硬度 (Hardness):
- A5052: 約 60 – 75 HB。適度な硬度を持ち、加工が比較的容易です。
- A5056: 約 70 – 90 HB。より高い硬度を持ち、高い強度と耐摩耗性が特徴です。
- 屈曲強さ (Yield Strength):
- A5052: 約 150 MPa – 210 MPa。比較的低い屈曲強さで、一般的な負荷に耐えることができます。
- A5056: 約 260 MPa – 310 MPa。高い屈曲強さを持ち、強度が要求される構造部品に適しています。
- 引張り強さの割合 (Ultimate Tensile Strength Ratio):
- A5052: 約 0.9 – 1.0。引張り強さに対する割合が標準的で、通常の用途に適しています。
- A5056: 約 1.1 – 1.3。引張り強さに対する割合が高く、より高い強度が求められる用途に適しています。
- 引張強さと屈曲強さ: A5056はA5052よりも高い引張強さと屈曲強さを持ち、強度が要求される環境に適しています。
- 伸びと硬度: A5052は高い伸び性と適度な硬度を持ち、加工性が優れています。一方、A5056は硬度が高く、強度に対するトレードオフとして伸びが少なくなります。
耐食性と耐久性の違い
性質 | A5052 | A5056 |
---|---|---|
耐食性 | 高い耐食性。特に海水や湿気に対する耐性が良好。化学薬品にも比較的強い。 | 非常に高い耐食性。特に塩水や腐食性環境に対して優れた保護性能を発揮。 |
耐久性 | 高い耐久性。一般的な使用環境で安定した性能を持ち、長期間にわたって使用可能。 | 非常に高い耐久性。高ストレス環境や厳しい条件下での使用に適しており、長寿命を提供。 |
詳細情報
- 耐食性:
- A5052: 高い耐食性を持ち、特に海水や湿気、化学薬品に対して耐性があります。船舶部品や化学処理装置など、腐食が問題となる環境に適しています。ただし、A5056に比べると若干の劣位にあります。
- A5056: 非常に高い耐食性を持ち、塩水や腐食性環境に対して優れた保護性能を発揮します。過酷な腐食環境でも長期間の使用が可能で、船舶部品や極端な環境下での用途に最適です。
- 耐久性:
- A5052: 高い耐久性を持ち、一般的な使用環境において安定した性能を発揮します。耐荷重性や耐摩耗性も良好で、多様な用途に対応できます。ただし、A5056に比べると極限の条件下では耐久性が劣る場合があります。
- A5056: 非常に高い耐久性を持ち、高ストレス環境や厳しい条件下でも安定した性能を発揮します。耐荷重性や耐摩耗性が非常に高く、長寿命の部品や構造材料として使用されます。
- 耐食性: A5056はA5052よりも更に優れた耐食性を持ち、特に塩水や腐食性の環境での使用に適しています。
- 耐久性: A5056はA5052よりも高い耐久性を持ち、高ストレスや厳しい環境下での使用に適しています。
用途に応じた適切な選択
アルミニウム合金A5052とA5056は、どちらも海洋や化学プラントなどの耐食性が要求される用途に使用されますが、それぞれの性質の違いを理解することが選び方のポイントです。A5052は優れた加工性を持ち、A5056に比べて強度はやや劣りますが、冷間加工に強く、曲げ加工や成形加工が容易です。例えば、複雑な形状の部品やパネルの加工に適しています。一方、A5056はマグネシウムの含有量が高く、A5052よりも高い強度を誇ります。特に、引張強度や耐疲労性に優れており、要求される強度が高い船舶の部品や構造材として選ばれることが多いです。 したがって、加工のしやすさを重視する場合はA5052を、より高い強度を必要とする場合はA5056を選択すると良いでしょう。最終製品の用途と要求される特性を熟考し、適したアルミニウム合金を選定することが重要です。アルミニウム合金の選定方法
合金選定の基準
アルミニウム合金A5052とA5056は、それぞれ特有の特性を有しており、適切な選択が求められます。A5052は一般的に耐食性に優れ、加工性が良いため、多くのアプリケーションに適しています。一方、A5056は強度が高く、特に海洋環境での使用に適している点が特徴です。例えば、船舶の部品や高強度を必要とする構造材にはA5056が推奨されます。これらの違いを理解することで、耐食性を重視する場合はA5052を、強度が求められる場所ではA5056を選択するという基準が設けられます。最終的には、用途に合った適切な合金を選定することが、製品の性能を最大限に引き出し、長期にわたって使用する上での信頼性を確保する鍵となります。用途に合わせた合金の選び方
アルミニウム合金A5052とA5056は、共に優れた特性を有していますが、その用途に応じて選択することが重要です。A5052は一般に耐食性に優れ、加工性が良いため、食品機械や化学工場などの設備に適しています。一方A5056は、より高い強度と優れた耐海水性を持っているため、船舶や高負荷を伴う構造物に使用されます。 具体的な例を挙げると、A5052は、その優れた可とう性から薄板や曲げ加工品に利用されることが多く、一方A5056はリベットやワイヤーなど、より強度が要求される部品に適しています。 結論として、A5052とA5056はそれぞれ異なる特性を持つため、耐食性と加工性を最優先する場合はA5052を、高強度と耐海水性を求める場合はA5056を選択することが望ましいです。機能性に加えて、コストや入手性も選択には重要な要素となります。適切な合金を選ぶことで、製品の性能を最大限に引き出し、長期にわたる耐久性を確保することができます。A5052とA5056の類似素材との比較
性質 | A5052 | A5056 | A6061 | A7075 |
---|---|---|---|---|
耐食性 | 高い耐食性。特に海水や湿気に強い。 | 非常に高い耐食性。塩水や腐食環境に優れた性能。 | 良好な耐食性。ただし、A5052やA5056よりは劣る。 | 耐食性が低め。腐食環境での使用には不向き。 |
耐久性 | 高い耐久性。一般的な使用環境で安定。 | 非常に高い耐久性。高ストレス環境に最適。 | 良好な耐久性。強度と耐荷重性が高い。 | 非常に高い強度。高ストレス環境や航空機部品に最適。 |
加工性 | 良好。切削や圧延、溶接が容易。 | 良好。加工性がA5052と同等、強度が高い。 | 良好。切削や機械加工が容易。溶接性も良好。 | 比較的加工が難しい。硬度が高く、溶接が難しい。 |
強度 | 中程度。耐荷重性は良好だが、他の合金に比べると劣る。 | 高い強度。特に高ストレス環境での使用に適している。 | 中程度から高め。良好なバランス。 | 非常に高い強度。極端な負荷や要求される強度に対応。 |
コスト | 比較的コストが低め。 | 中程度から高め。耐食性と強度の高さから高コスト。 | 中程度。性能とコストのバランスが良い。 | 高いコスト。高強度から高コスト。 |
選択肢の比較
- A5052: 耐食性と加工性に優れ、比較的コストが低いため、一般的な使用や腐食環境での部品に適しています。例えば、自動車の部品や一般的な建材など。
- A5056: さらに高い耐食性と耐久性を持ち、特に高ストレスや腐食環境で使用する場合に適しています。船舶部品や高強度が求められる構造材料に最適です。
- A6061: バランスの取れた性能を持ち、加工性が良く、強度も高いです。航空機部品や機械部品など、広範な用途に対応できますが、耐食性はA5052やA5056に比べて劣ります。
- A7075: 非常に高い強度を持ち、航空機や高ストレス部品に適していますが、耐食性が低く、腐食環境での使用には注意が必要です。また、コストが高いです。
- 耐食性が最優先: A5056(特に塩水環境で)またはA5052(一般的な耐食性が必要な場合)。
- 高い強度が必要: A7075(極端な負荷に対応)またはA5056(高ストレス環境)。
- 加工性を重視: A5052またはA6061(良好な加工性)。
- コストを抑えたい: A5052(比較的低コストで高性能)。
アルミニウム合金の加工方法
A5052とA5056の加工方法と加工性の比較
加工方法
加工方法 | A5052 | A5056 |
---|---|---|
切削加工 | 切削性が良好。精密な部品の製造が可能。 | 切削性も良好だが、強度が高いため、A5052よりも少し難しい。 |
圧延加工 | 圧延が容易。複雑な形状や薄板の製造に適している。 | 圧延も可能だが、A5052に比べて少し難易度が高い。 |
溶接加工 | TIG溶接やMIG溶接が可能。接合部の強度が高い。 | TIG溶接やMIG溶接が可能。接合部の強度が高い。 |
曲げ加工 | 曲げ加工が比較的容易。加工性が良好。 | 曲げ加工も可能だが、A5052よりも硬いため、少し難しい。 |
引張試験 | 高い延性を持ち、引張加工が容易。 | 高い強度を持ち、引張試験での性能が良好。 |
加工性の比較
性質 | A5052 | A5056 |
---|---|---|
加工のしやすさ | 高い加工性を持ち、切削や圧延、曲げ加工が容易。 | 高い加工性を持つが、強度が高いため、A5052よりも若干難しい。 |
切削性 | 切削加工がスムーズで、精度の高い部品が得られる。 | 切削加工も良好だが、A5052よりも少し手間がかかる。 |
圧延性 | 圧延が容易で、薄板や複雑な形状の製造が可能。 | 圧延も可能だが、強度が高いため加工がやや難しい。 |
溶接性 | TIG溶接やMIG溶接が適しており、接合部の強度が高い。 | TIG溶接やMIG溶接も可能で、強度の高い接合ができる。 |
曲げ加工 | 曲げ加工が比較的容易で、変形が少ない。 | 曲げ加工も可能だが、硬度が高いため、A5052よりも難易度が上がる。 |
延性 | 高い延性を持ち、加工時の変形が少ない。 | 高い強度を持ち、引張試験での性能が良好。 |
結論
- A5052: 加工性が非常に良好で、切削、圧延、曲げ加工が容易です。精度の高い部品や複雑な形状の製造に向いています。また、溶接性も良好で、一般的な用途に適しています。
- A5056: 加工性は良好ですが、強度が高いため、A5052よりも加工がやや難しい場合があります。しかし、A5056も切削、圧延、曲げ加工が可能で、強度が必要な部品の製造に適しています。特に耐食性や耐久性が求められる環境での使用に向いています。
合金ごとの加工上の注意点
アルミニウム合金A5052とA5056は、それぞれ特有の性質を持ち、適した用途が異なります。まず、A5052合金は耐食性に優れているため、海水にさらされる環境や、化学薬品を扱う装置の材料として適しています。具体的には、船舶の部品や化学工業関連の容器などに用いられます。一方、A5056合金はA5052よりも高い強度を持ち、耐食性も良いため、より過酷なストレスがかかる部分に使用されます。例えば、航空機の部品や高負荷がかかる建築物の構造材料に適するでしょう。 選び方については、使用環境や必要な強度、耐食性を考慮する必要があります。耐食性を最優先する場合はA5052、強度と耐食性を両立させたい場合はA5056が適していると言えます。最終的に、合金選びはその用途に最も合った特性を持つものを選ぶことが重要です。アルミニウム合金の用途区分
各種アルミニウム合金の用途例
アルミニウム合金A5052とA5056は、それぞれ特有の性質を持っており、用途に応じて選び方が重要です。A5052合金は、優れた耐食性を持つため海水に触れることの多いマリン用品や、化学プラントにおいて使用されます。一方、A5056合金はA5052よりも高い強度を持ち、構造材料としての要求が特に厳しい部分に用いられることが多いです。たとえば、高い強度が必要な航空宇宙産業や、耐振性が要求される建築資材などがあります。選び方のポイントとしては、耐蝕性を最優先する場合はA5052を、より高強度を要求する場面ではA5056が適しています。最終用途に即した特性を考慮して適切な合金を選ぶことが重要と言えます。A5052とA5056の用途における違い
アルミニウム合金のA5052とA5056は、それぞれ異なる性質を持ち、用途によって選び方が重要です。A5052は優れた耐食性を持ち、加工性が良いため、海水にさらされる部品や容器、建築材料に適しています。一方、A5056はA5052よりも高い強度を持ち、特に溶接性に優れていることが特徴です。そのため、要求される強度が高い船舶の構造材や圧力容器などによく使用されます。 具体的な例として、A5052は自動車の部品や電子機器の筐体に用いられることが多く、耐食性と成形性のバランスが求められる場面で選ばれます。一方でA5056は、高い機械的強度が求められるマリン用品や釣り具などに用いられることが多いです。 このようにA5052とA5056は、それぞれ異なる特徴を持ち、使われる場面に応じて適切に選ばれるべきです。最適な合金を選択することで、製品の性能を最大限に引き出すことができます。選択の際には、耐食性、強度、加工性など、求められる性質を総合的に考慮し、目的に適した合金を選ぶことが重要です。特定の条件下での合金選定ガイドライン
アルミニウム合金A5052とA5056の性質は似ていますが、用途によって選択すべき合金が異なります。A5052は一般的に優れた耐食性と加工性を兼ね備えており、海水や塩水にさらされる環境でよく使用されます。例えば、船舶の部品や圧力容器などに適しています。一方、A5056は更に高い耐食性と強度を持ち、強度が要求される航空機の部品や建築構造物に使われることが多いです。 この二つの合金を選択する際は、対象となる製品の使用環境と必要とされる物性を考慮する必要があります。たとえば、海の近くで使う製品であれば、耐食性を重視してA5052を選ぶべきですし、より高い機械的負荷に耐える必要がある場合はA5056が適していると言えるでしょう。最終的には、それぞれの合金の性質を理解し、具体的な用途に合わせて適切な選択をすることが重要です。結論としてのアルミニウム合金A5052とA5056の選び方
総合的な性質の比較
アルミニウム合金A5052とA5056は、それぞれ独自の特性を持ち、用途に応じて選ばれるべきです。主要な違いとして、A5052は優れた耐食性と加工性を持つ一方で、A5056はより高い強度と優れた溶接性を有しています。例えば、海水に晒される環境で使うには、耐食性が求められるためA5052が適していますが、構造材や高い強度が求められる用途では、A5056の方が望ましい選択となるでしょう。結論として、アルミニウム合金の選択はその使用目的に基づいて慎重に行うべきであり、A5052とA5056の性質を理解することが重要です。そうすることで、最も効果的で経済的な選択を行うことができるでしょう。用途に応じた合金の絞り込み
アルミニウム合金A5052とA5056は、それぞれ異なる特性を持ち、使用目的によって選び方も変わってきます。A5052は耐食性に優れ、特に海水に強いため、船舶や化学プラントに適しています。一方、A5056はA5052よりも高い強度を持ち、機械部品や建築材料など、強度が求められる用途に適しています。例えば、高い疲労強度が求められる航空機の部品や、耐海水性が必要なマリングレードの材料などにA5056が用いられることがあります。最適な合金を選ぶには、その特性を理解し、用途に合ったものを絞り込むことが重要です。結論として、A5052は耐食性重視、A5056は高強度が必要な場合に選択すると良いでしょう。最終的な選定におけるポイント
アルミニウム合金のA5052とA5056は、機械的性質や化学的成分においてそれぞれ違いを持っているため、用途に応じて適切な選択が重要です。A5052合金は、優れた耐食性を有し、特に海水や塩水にさらされる環境での使用に適しています。一方、A5056合金は、A5052よりも高い強度を持つため、より強度が求められる構造材料として適しています。例えば、A5052は船舶の部品や海洋構造物に、A5056は航空機のフレームや高強度を必要とする工業製品に使用されることが多いです。最終選定にあたっては、製品の使用環境や必要とされる特性を慎重に考慮し、それぞれの合金の特性を最大限に活かせるように選びましょう。まとめ
アルミニウム合金A5052とA5056にはそれぞれ異なる特性があります。それぞれの特性を理解することは材料の選択において非常に重要です。A5052は耐食性に優れ、一方でA5056は溶接性に優れています。どちらの合金を選択するにせよ、使用目的や環境条件を考慮することが重要です。適切な合金を選ぶことで、製品の性能や耐久性を向上させることができます。A5052とA8011アルミニウム合金の違いとは?特性と用途を徹底比較
A5052とA8011というアルミニウム合金についてご存知ですか?今回の記事では、この二つの合金の違いについて徹底的に比較してみます。それぞれの特性や用途に焦点を当て、どのような場面でどちらが適しているのかを明らかにします。アルミニウム合金は日常生活から産業用途まで幅広く使われており、その違いを知ることで理解を深めることができるでしょう。さあ、A5052とA8011の違いを探求してみましょう。
Contents
A5052とA8011アルミニウム合金の基本
アルミニウム合金とは
アルミニウム合金は、様々な種類がありますが、その中でもA5052とA8011は代表的なものです。これらの合金の違いを理解することは重要です。まず、A5052は耐食性や溶接性に優れ、船舶や車両の部品などの用途に適しています。一方、A8011は食品包装や建築材料などに広く使用される軟らかい合金です。特性を比較すると、A5052は強度が高く、A8011は加工性に優れています。例えば、A5052は海水に対して優れた耐性を持ちますが、A8011は曲げ加工に適しています。用途によって最適な合金を選択することが重要です。このように、A5052とA8011は異なる特性を持ち、適切な用途に使われることで素晴らしい製品が生まれます。
A5052アルミニウム合金の概要
A5052アルミニウム合金は、A8011アルミニウム合金と比べて耐食性に優れています。海水や化学物質に強い特性を持ち、外部環境にさらされる部品や構造材として広く使用されています。例えば、船舶の構造部品や液体の貯蔵槽、車両のボディパネルなどに使用されています。
一方、A8011アルミニウム合金は、加工性や表面の美観に優れています。食品包装や建築材料、家庭用品などに使用され、見た目や使い勝手にこだわる製品に適しています。簡単に言うと、A5052は耐環境性が特に優れており、A8011は加工性や美観が主な特長です。
どちらのアルミニウム合金も異なる特性を持ち、用途に合わせて適切な素材を選択することが重要です。工業製品や日常品など、それぞれの特性を理解することで効果的に活用することができます。
A8011アルミニウム合金の概要
A8011アルミニウム合金は、軽量で加工がしやすい特性を持つことから、様々な産業で幅広く使用されています。これは日本を含む多くの国で建築や自動車部品、包装材料などに利用されています。一方、A5052アルミニウム合金は、耐食性や強度が高いため、船舶の部品や車体パネルなどに適しています。
特に、A8011は食品包装や飲料製品の缶などによく使われており、その食品衛生への適合性が重要な要素となっています。一方、A5052は海洋環境下での使用に適しており、塩害に強い特性を持っています。
両合金にはそれぞれ適した特性と用途があり、正しい選択が製品の性能や品質に大きな影響を与えることがあるため、材料選定は重要です。
A5052とA8011の物理的特性の比較
化学成分の違い
A5052とA8011アルミニウム合金は、化学成分において異なる特性を持っています。A5052はマグネシウムとクロムを主な成分とし、耐食性や強度に優れています。一方、A8011は鉄やシリコンを主成分とし、加工性や溶接性に優れています。例えば、A5052は船舶の外板や燃料タンク、A8011は食品包装や建材によく使われます。
この違いから、使用目的や環境に応じて適切な合金を選択することが重要です。船舶などの耐食性が求められる用途ではA5052が適していますが、食品包装などの加工性が重要な場合にはA8011が適しています。合金の特性を理解し、適切に使用することで、製品の品質や性能を最大限に引き出すことができます。
強度と硬度
A5052とA8011アルミニウム合金の違いを理解するためには、強度と硬度の特性を比較することが重要です。A5052は、強度が高く、耐久性に優れています。一方、A8011は、軽量で加工性が良いという特性があります。例えば、自動車の車体パネルに使用されるA5052は、衝撃に強い性質が求められます。一方、A8011は、缶の製造などの用途で使われることが多く、加工しやすい性質が役立ちます。つまり、用途によって適したアルミニウム合金を選ぶことが重要です。強度を重視する場合はA5052、加工性を重視する場合はA8011を選択すると良いでしょう。
延性と靭性
A5052とA8011アルミニウム合金はどう異なるのでしょうか?特性と用途について徹底的に比較してみましょう。A5052は耐食性、溶接性に優れており、主に船舶や飛行機の構造部品、薄板材料として使われます。一方、A8011は食品包装や建築材料に使われることが多く、軽量で加工性にも優れています。A5052は強度が高く、A8011は加工がしやすい特性があります。例えば、A5052は船の船体や燃料タンク、A8011は缶や包装材に使われています。合金ごとに異なる特性と用途があり、適切な材料を選ぶことが重要です。このように、合金の違いによって使われる場面や性質が異なります。
加工性の比較
成形性
A5052とA8011アルミニウム合金は、成形性において異なる特性を持っています。例えば、A5052は強度が高く耐食性に優れており、一方でA8011は腐食に強く表面処理がしやすいといった違いがあります。この特性の違いから、それぞれ異なる用途に向いています。
具体的には、A5052は自動車や船舶の部品、圧力容器などの製造に向いています。一方、A8011は食品包装や建築材料、電子部品などの分野でよく使用されます。そのため、製品の要求される特性に合わせて適切な合金を選択することが重要です。
まとめると、A5052とA8011はそれぞれ独自の特性を持ち、異なる用途に適しています。製品を製造する際には、適切な合金を選択することが重要であることを覚えておきましょう。
溶接性
A5052とA8011アルミニウム合金の違いは何でしょうか?これらのアルミニウム合金は異なる特性や用途を持っています。まず、A5052は耐食性に優れているため、海洋環境や塩害の影響を受けやすい場所での使用に適しています。一方、A8011は食品包装や建材などの加工に適しており、表面処理などが比較的容易です。
また、溶接性も違いがあります。A5052は溶接が難しい特性がありますが、A8011は溶接が比較的容易です。例えば、車両のボディパネルや船舶の製造などでは溶接性が重要な要素となるため、素材選定が大切です。
要するに、それぞれのアルミニウム合金には異なる特性と用途があります。用途や条件に応じて最適な合金を選択することが大切です。
表面処理の適性
アルミニウム合金の中でA5052とA8011は何が違うのでしょうか? 両者の特性や用途を徹底比較してみましょう。まず、A5052は耐食性や耐久性に優れ、海水などの腐食性環境にも適しています。一方、A8011は軽量で加工性が高く、食品包装や建材などに広く使用されています。例えば、A5052は船舶の部品や燃料タンク、A8011は缶や包装用箔などに使われます。要するに、A5052は耐久性が必要な場面で、A8011は軽さや加工性が重要な場面で使われる傾向があります。選択する際は、使用目的や環境に応じて適切な合金を選ぶことがポイントです。
アルミニウム合金の種類と特徴
合金の分類と基準
A5052とA8011のアルミニウム合金は、両者の特性や用途に違いがあります。まず、A5052は耐食性に優れ、塩水や有機酸に強いため、船舶や薬品容器などの海洋環境での使用に適しています。一方、A8011は加工性に優れ、飲料缶や包装材料などの加工に適しています。例えば、A5052は海洋機器や車両部品に使用されることが一般的であり、A8011は飲料缶やフィルム容器などに使われています。このように、それぞれの合金は異なる特性を持ち、異なる用途に最適化されています。したがって、製品を選択する際には、使用環境や加工方法などを考慮することが重要です。
A5052の特徴と適用分野
A5052とA8011アルミニウム合金は両者とも主に日本の産業で利用される素材ですが、それぞれ異なる特性や適用分野があります。A5052は耐食性に優れており、海洋環境などの湿気の多い場所でも優れたパフォーマンスを発揮します。一方、A8011は比較的軽量で加工しやすい特性があり、食品容器や包装材料などに広く使用されています。
例えば、A5052は船舶の部品や自動車の車体パネルなどで利用され、耐食性が求められる場面で活躍します。一方、A8011は缶詰やフィルム容器、調理器具などの食品関連製品に広く使われています。
このように、それぞれのアルミニウム合金は異なる特性を持ち、異なる用途に適しています。産業や製品の要件に合わせて適切な合金を選択することが重要です。
A8011の特徴と適用分野
A5052とA8011のアルミニウム合金には、特性と用途において違いがあります。まず、A5052は耐食性に優れ、海水環境下での使用に適しています。逆に、A8011は電気伝導性に優れており、電解コンデンサーやパッキング用箔などの用途に適しています。例えば、A5052は船舶の部品や食品加工機器などに使用される一方、A8011は電気製品や包装資材など幅広い分野で利用されています。このように、それぞれの特性や用途に合わせて選択されることが重要です。したがって、使用目的や必要条件に応じて、A5052とA8011のどちらが最適かを検討することが大切です。
特定の用途におけるA5052とA8011の利用方法
輸送機器への応用
A5052とA8011アルミニウム合金は、金属の種類や特性、用途において異なります。例えば、A5052は耐食性や強度が高く、主に船舶や飛行機などの輸送機器に使用されます。一方、A8011は軟らかく加工しやすい特性があり、缶や包装材などの製造に適しています。
A5052は海水などの腐食環境に強く、強度も優れているため、船舶の船体や飛行機の構造部品に広く使用されています。一方、A8011は軽量で加工しやすいため、缶の製造に向いており、食品や飲料の包装資材として広く利用されています。
このように、A5052とA8011はそれぞれの特性や用途に合わせて異なるメリットを持っており、適切な場面で使い分けることが重要です。
建築材料としての利用
A5052とA8011アルミニウム合金は、建築や製造業界において重要な素材として使われています。A5052は耐食性に優れ、海洋環境などの厳しい条件下でも優れた性能を発揮します。一方、A8011は強度が高く、加工しやすい特性があります。例えば、A5052は船舶や車両の外装パーツ、A8011は食品容器や缶として利用されています。
A5052とA8011の違いを簡単にまとめると、A5052は耐食性が高く、A8011は強度が重視される特性があります。アルミニウム合金を使用する際には、用途や必要とされる特性に合わせて適切な合金を選択することが重要です。建築や製造業における材料選定において、適切な合金を選ぶことで製品の品質や性能を向上させることができます。
包装材料としての特性
A5052とA8011アルミニウム合金の違いを理解するためには、それぞれの特性と用途を比較することが重要です。A5052は耐食性に優れ、海洋環境に適しています。一方、A8011は食品包装などに向いており、食品の保護や鮮度を保つ性能が特長です。例えば、A5052は船舶や海洋関連の部品に利用される一方、A8011は缶詰や包装フィルムなどに広く使われています。A5052は強度が高く、A8011は加工性に優れているという違いもあります。そのため、使用する環境や目的に合わせて適切なアルミニウム合金を選択することが重要です。このように、A5052とA8011はそれぞれの特性を活かして様々な分野で使われています。
アルミニウム合金板蓋材の選び方
必要な特性の理解
A5052とA8011のアルミニウム合金は、用途や特性において異なる点があります。まず、A5052は耐食性に優れ、海水や塩分の影響を受けにくい特性があります。これに対して、A8011は加工性に優れ、薄い箔状に加工するのに適しています。例えば、A5052は船舶の部品や食品容器、A8011は飲料缶や包装材料などに広く利用されています。このように、それぞれのアルミニウム合金は異なる特性を持ち、異なる用途に適しています。したがって、使用する場面や要求される特性に応じて適切な合金を選択することが重要です。
用途に応じた材料選定のポイント
A5052とA8011アルミニウム合金は、どのような違いがあるのでしょうか?それぞれの特性や用途を比較してみましょう。
まず、A5052は耐食性に優れ、海洋環境などの厳しい条件下でも優れた性能を発揮します。一方、A8011は加工性に優れており、軽量でありながら強度があります。例えば、A5052は船舶の外装や食器などに利用されることが多く、A8011は食品包装や建築材料などに適しています。
したがって、どちらの合金を選ぶかは使用する環境や目的によって異なります。選定の際には、耐食性や加工性などの特性を考慮し、最適な合金を選択することが重要です。
コストパフォーマンスの考慮
A5052とA8011アルミニウム合金は、どのように異なるのでしょうか?まず、A5052はマグネシウムを主成分としており、耐食性に優れ、海水環境にも適しています。一方、A8011は純度が高く、加工性が良い特徴があります。
この違いが、それぞれの用途にも影響を与えています。例えば、A5052は船舶や海洋関連の部品、車両のパーツなどによく使用されます。一方、A8011はパッケージングや建築材料、食品容器などに広く利用されています。
つまり、A5052は耐久性が求められる環境で、A8011は加工性や純度が重要な場面で活躍します。それぞれの特性を理解し、適切な用途に活かすことが大切です。
カラーアルミ板・コイルの選択と利用
カラーアルミの特性
A5052とA8011アルミニウム合金は、それぞれ異なる特性や用途を持っています。A5052は耐食性が優れており、海洋環境などの厳しい条件下でも劣化しにくい特徴があります。一方、A8011は加工性が高く、軽量でありながら強度があります。例えば、A5052は船舶や車両の造船に向いている一方、A8011は食品容器や缶などの包装用途に適しています。このように、それぞれのアルミニウム合金は異なる環境や用途に適しているため、選定時にはこれらの特性を考慮することが重要です。
色の選び方とデザインへの影響
A5052とA8011アルミニウム合金にはそれぞれ異なる特性と用途があります。A5052は耐食性が高く、強度もあり、主に船舶や車両の製造に使われています。一方、A8011は加工しやすく、軽量で耐食性があり、主に食品包装や建築材料に利用されています。例えば、A5052は海水にさらされる船舶の外装や自動車のボディパネルに使用される一方、A8011は食品用のアルミホイルや建物の外装パネルに使われます。そのため、用途に応じて適切な合金を選ぶことが重要です。両者の比較を通じて、どちらのアルミニウム合金がより適しているかを理解することが大切です。
維持管理と耐久性の観点から
A5052とA8011アルミニウム合金は、日本の建設や製造業で広く使用されています。これらの合金にはそれぞれ異なる特性があります。例えば、A5052は耐食性に優れており、海洋環境下での使用に適しています。一方、A8011は加工性が良く、食品包装や建築材料などに適しています。
A5052とA8011の違いを具体的に比較すると、A5052はマグネシウムを主成分とし、強度が高く、溶接性にも優れています。一方、A8011は純度が高く、軽量で加工がしやすい特性があります。例えば、A5052は車両のボディパネルなどに使用される一方、A8011は缶詰や包装材などに広く利用されています。
維持管理や耐久性の観点から、適切なアルミニウム合金を選択することは重要です。それぞれの特性を理解し、用途に応じて最適な合金を選定することが、製品の品質向上やコスト削減につながります。
アルミニウム合金の購入と取り扱いの注意点
品質保証とメーカー選び
A5052とA8011アルミニウム合金は、様々な点で異なります。A5052は耐食性、強度、溶接性に優れており、主に船舶や飛行機の部品、圧力容器、板金部品などに使われます。一方、A8011は軟らかく加工しやすい性質を持ち、缶、包装、建築用材料などに使用されます。例えば、A5052は海水に触れる環境での耐食性が求められる場面で使われます。一方、A8011は食品包装用のアルミ箔やコンテナなどに使用されます。そのため、用途に合わせて適切なアルミニウム合金を選ぶことが重要です。これらの特性や用途を比較することで、製品の品質や長寿命につながることが理解できます。
取り扱い上の注意と保管方法
A5052とA8011アルミニウム合金の違いを理解することは重要です。A5052は耐食性に優れており、海洋環境で使用するのに適しています。一方、A8011は加工性が高く、缶や包装材料などに広く使われています。例えば、A5052は船舶の船殻や車両のボディパネルに良く使われます。一方、A8011は食品包装や飲料缶などの製造に適しています。この違いにより、それぞれが異なる用途に最適化されています。そのため、製品を選択する際には、その特性と用途を理解しておくことが重要です。どちらのアルミニウム合金も自動車産業や建築業界などで幅広く使用されており、その違いを把握することで、より適切な材料を選択できるでしょう。
環境への配慮とリサイクル
アルミニウム合金の中でも、A5052とA8011はそれぞれ異なる特性と用途を持っています。A5052は強度が高く、耐食性に優れているため、造船や航空機の部品、自動車のボディパネルなどに広く利用されています。一方、A8011は加工性に優れ、食品包装や建材、家具の製造などに適しています。
例えば、A5052は海水や食塩水に対して耐性があり、外部環境にさらされる部品に適しています。一方、A8011は薄い板状に加工しやすく、食品包装や建材などの分野で幅広く使用されています。
このように、異なる特性と用途を持つA5052とA8011。適切に選択することで、製品の品質や性能を向上させることができます。
まとめと選択のためのチェックリスト
A5052とA8011の比較チェックポイント
A5052とA8011の比較にはいくつかのポイントがあります。まず、A5052は耐食性が高く、塩水に対しても耐性があります。一方、A8011は薄い板に最適で、着色処理もしやすい特性があります。例えば、A5052は船舶の部品や液体タンク、A8011は食品包装や建材によく使われています。用途によって適したアルミニウム合金を選ぶことが重要です。特性の違いを理解し、それぞれの強みを活かすことで、効果的に製品や部品を選択できます。工業製品から日常生活用品まで、アルミニウム合金の使い分けが重要です。
最終選択のための総合評価
A5052とA8011アルミニウム合金は、それぞれ異なる特性と用途を持っています。A5052は耐食性や加工性に優れており、船舶や飛行機などの構造部品に広く使用されています。一方、A8011は食品包装や建築材料などの分野で主に使用される軟質アルミニウム合金です。このように、それぞれの合金は異なる環境や目的に適した特性を持っています。
例えば、A5052は海洋環境下での耐食性が求められる場面で重宝されます。一方、A8011は食品包装など、軽量で加工しやすく安全性が求められる場面に最適です。両者の違いを理解することで、適切な材料を選択し、最適な製品を提供することができます。A5052とA8011の違いを理解し、用途に合わせた選択を行うことが重要です。
まとめ
A5052とA8011アルミニウム合金は異なる特性と用途を持っています。これらのアルミニウム合金を比較することで、それぞれの特徴を理解し、適切な用途に活用することが重要です。一般的な比較ポイントとしては、強度、耐食性、加工性などが挙げられます。それぞれの特性を理解し、用途に適した合金を選択することが重要です。
「プロが伝授:アルミニウムを旋盤で加工するコツ」
アルミニウムを熟練した技術で加工することは、製造業やDIY愛好家にとって重要なスキルです。しかし、旋盤を使ったこのプロセスには専門知識やノウハウが必要です。本日は、「プロが伝授:アルミニウムを旋盤で加工するコツ」と題した記事をお届けします。アルミニウム加工における旋盤とドリルの技術に関する専門家のアドバイスをご紹介し、初心者から上級者まで幅広い読者の方々に役立つ情報を提供します。アルミニウム加工の世界への入り口を開くために、この貴重なガイドを是非ご覧ください。
Contents
アルミニウム加工の基礎
アルミニウムの物理的・化学的特性
アルミニウムは軽量で強度がある金属で、熱や電気をよく伝導します。これらの特性から、航空機や自動車、電化製品などに幅広く利用されています。旋盤を使用してアルミニウムを加工する際には、適切な工具や切削条件が重要です。例えば、ドリルの選び方や回転数、切削速度などを適切に設定することが大切です。これによって、作業効率が向上し、加工精度が高まります。さらに、クーリング液の使用や適切な切削量を守ることも、加工品質向上につながります。アルミニウムは扱いやすい金属ですが、正しい加工手法を理解することが重要です。これらのポイントを押さえて、旋盤でのアルミニウム加工をスムーズに行いましょう。
アルミニウム加工のための旋盤の種類
アルミニウムを旋盤で加工する際には、適切な旋盤の種類を選ぶことが重要です。たとえば、小型のドリル旋盤は、細かい部品や加工精度が必要な部分に適しています。一方、大型の旋盤は、大きなアルミニウム部品を効率的に加工するのに適しています。具体的な例を挙げると、自動車産業ではエンジン部品やホイールなどの大型アルミニウム部品を加工するために大型旋盤が使用されています。このように、旋盤の種類を選ぶことで、効率的にアルミニウム加工が行えます。結果として、製品の品質向上や生産性の向上につながります。
旋盤加工におけるアルミニウムの利点と課題
アルミニウムの旋盤加工には、その軽さや耐食性といった利点があります。例えば、自動車部品や航空機部品などで幅広く利用されています。しかし、アルミニウムは柔らかい金属であるため、旋盤加工において取り扱いが難しい場面もあります。ドリルで加工する際には、適切な選択と高い技術が求められます。アルミニウムの性質を理解し、正確な切削条件を設定することが重要です。例えば、旋盤速度やドリルの刃先形状を適切に設定することで、綺麗な仕上がりや高い精度を実現することができます。アルミニウムの利点を最大限に活かし、課題をクリアするためには、熟練した技術と正しい知識を持つことが必要です。
アルミニウム切削加工の基本
切削工具の選択基準
アルミニウムを旋盤で加工する際に重要なポイントは、適切な切削工具を選ぶことです。アルミニウムは軟らかい金属であり、適切な工具を使用しなければうまく加工できません。例えば、アルミニウム加工に適したドリルや切削工具を使用することで、作業効率が向上し、加工精度が高まります。
アルミニウムは熱に敏感な性質を持つため、旋盤での加工時には適切な工具や冷却液を使用することが重要です。また、切削速度や切削量などの設定も適切に行うことで、加工品質を向上させることができます。
適切な切削工具を選ぶことで、アルミニウムの旋盤加工を効率的かつ正確に行うことができます。これにより、製品の品質向上や生産性の向上が期待できます。
アルミニウム旋盤加工におけるドリルの役割
アルミニウムを旋盤で加工する際に、ドリルが果たす重要な役割について考えてみましょう。まず、ドリルは加工する部品に穴を開ける際に欠かせません。例えば、アルミニウム製のパーツや部品を作る際には、正確な位置に穴を開ける必要があります。その際にドリルが使用され、素早く穴を開けることができます。これにより、製品の品質や精度を向上させることができます。また、ドリルは加工速度を上げるためにも重要です。効率的な加工を行うためには、適切なドリルの選択や使い方が欠かせません。したがって、アルミニウムを旋盤で加工する際には、適切なドリルの選定と使い方をしっかり考えることが重要です。
切削速度と送り速度の基本原則
アルミニウムを旋盤で加工する際の基本原則は、切削速度と送り速度にあります。アルミニウムは軽くて加工が比較的容易ですが、正しい速度設定が重要です。まず、切削速度は高すぎず低すぎず、適切な速度で設定することが大切です。高速すぎると刃物が早く摩耗し、低速だと加工が遅くなります。そして、送り速度は加工されるアルミニウムの種類や形状によって異なります。例えば、削り取るべき量が多い場合は高い送り速度が効果的です。逆に、精密な加工が必要な場合は低い送り速度を選ぶべきです。これらの基本原則を守ることで、アルミニウムを効果的に旋盤で加工することができます。
アルミ加工の難しさと対策
アルミニウム加工時の一般的な問題点
アルミニウムを旋盤で加工する際に一般的な問題点があります。アルミニウムは軽量で耐食性に優れた金属ですが、加工時に取り扱いに注意が必要です。例えば、アルミニウムは柔らかいため、旋盤での切削時に振動や加熱が起こりやすいことが挙げられます。これにより、加工精度が低下してしまう可能性があります。
そのため、ドリルや切削工具を使う際には十分な冷却や切削油の使用が重要です。さらに、適切な切削速度や切削量を設定することも大切です。例えば、高速旋削を行うことでアルミニウムの切削精度を向上させることができます。
アルミニウムの加工は繊細な作業ですが、適切な技術と注意を払うことで問題を解決できることを覚えておきましょう。
加工精度を左右する要因
アルミニウムを旋盤で加工する際、加工精度を左右する要因はいくつかあります。まず、適切なツールと工具の使用が重要です。例えば、正確なドリルやカッターを使用することで、正確な加工が可能となります。さらに、適切な切削速度や切削量を設定することもポイントです。過度な速度や過剰な圧力は加工精度を損なう可能性があります。
また、材料自体の質も重要な要素です。アルミニウム合金の品質や硬度が加工のしやすさに影響を与えます。最適な材料を選択することが、精密な加工を実現するために欠かせません。
加工精度を向上させるためには、これらの要素に注意を払うことが不可欠です。適切なツールと工具を使用し、材料の特性を理解して適切な加工条件を設定することで、アルミニウムを効果的に旋盤で加工することが可能となります。
加工難易度に影響するアルミ合金の種類
「プロが伝授:アルミニウムを旋盤で加工するコツ」
アルミニウムを旋盤で加工する際、加工難易度に影響を与える要素として、アルミ合金の種類が挙げられます。異なる種類のアルミ合金は硬さや加工性が異なるため、正確な取り扱いが必要です。例えば、アルミニウム合金の中でもアルミニウム7000シリーズは強度が高いが加工が難しいという特性があります。これに対して、アルミニウム6000シリーズは加工しやすいが強度はやや低い特徴があります。したがって、旋盤でアルミニウムを加工する際は、使用するアルミ合金の種類によって適切な加工方法や工具を選定することが重要です。アルミニウム合金の種類を理解し、それに合わせた取り扱いを行うことで、より効率的かつ正確な加工が可能となります。
アルミ旋盤加工の特徴とポイント
旋盤加工のプロセス概要
アルミニウムを旋盤で加工する際のプロセスは、まず素材を旋盤にセットします。続いて、適切なスピードと切削条件を設定し、旋盤を回転させながら切削工具を素材に接触させて削り取ります。この際、冷却液を使用して熱を逃がすことが重要です。例えば、アルミニウムは熱を吸収しやすいので、十分な冷却が必要です。精密な加工が必要な場合は、切削工具の角度や速度を微調整することも重要です。加工が終了したら、仕上げを行い、加工精度や表面仕上げを確認します。これにより、アルミニウムを効率的かつ正確に旋盤で加工することができます。
アルミニウムの旋盤加工で重要なポイント
アルミニウムの旋盤加工で重要なポイントについて紹介します。アルミニウムは軽くて加工しやすい素材ですが、旋盤での加工には注意が必要です。まず、正しい刃物と適切な速度を選ぶことが重要です。刃物の選択は加工するアルミニウムの種類や形状によって異なります。適切な速度設定は加工精度や切削寿命に影響します。
また、切削時の冷却も欠かせません。加工中に適度な冷却液を使うことで切削時の摩擦熱を抑え、加工精度を保つことができます。さらに、切削の際には適切な切削量を設定し、過剰な負荷をかけないようにすることも重要です。
これらのポイントを抑えることで、アルミニウムの旋盤加工を効果的に行うことができます。加工精度や効率を向上させるために、適切な設定と注意を払いながら作業を行いましょう。
効率的なアルミ加工のための技術とコツ
アルミニウムを旋盤で効率的に加工するための技術やコツについて紹介します。アルミニウムは軽くて耐食性があり、様々な産業で広く使用されています。旋盤を使用する際には、適切な刃物や切削速度、切削深さを選ぶことが重要です。また、適切な冷却液を使用して過熱を防ぎ、切削時の振動を最小限に抑えることも大切です。
例えば、適切な刃物を選択することで、加工時間を短縮し、精度を向上させることができます。さらに、定期的なメンテナンスや刃物の交換を行うことで、加工品質を維持することができます。これらの技術やコツを実践することで、アルミニウムの旋盤加工を効率的に行うことができます。
アルミ合金の特性と旋盤加工のコツ
アルミ合金の種類とその特性
アルミニウムは軽量で耐食性があり、様々な用途に使われる素材です。アルミ合金は、純粋なアルミニウムに他の元素を添加したもので、強度や耐久性を向上させます。例えば、アルミニウム合金の中でも航空機や自動車部品によく使われるのが「アルミニウム7075」です。この合金は強度が高く、耐久性に優れています。
旋盤を使ってアルミニウムを加工する際には、適切な切削速度や刃先の選択が重要です。例えば、ソフトなアルミニウム合金を旋盤で加工する場合には、高速で切削することが効果的です。一方、硬質なアルミニウム合金を加工する際には、刃先の材質や形状に注意する必要があります。
これらのポイントを押さえてアルミニウムを旋盤で加工すると、効率的に作業が進み、良い仕上がりを得ることができます。
各種アルミ合金の加工ポイント
アルミニウムを旋盤で加工する際のポイントについて紹介します。 アルミニウムは軽量で耐食性に優れ、様々な産業で広く使用されています。旋盤を使用する際には、適切なドリルの選択が重要です。アルミニウム合金には硬度の異なる種類があり、適切な刃先形状や切削速度を選ぶことが重要です。例えば、アルミニウム合金6000シリーズは、高速度鋼製のドリルが適しています。また、十分な潤滑剤を使用することで切削時の摩擦を軽減し、加工精度を向上させます。このように、適切な道具と適切な加工条件を選択することが、アルミニウムの旋盤加工において重要です。
高品質な旋盤加工を実現するためのコツ
アルミニウムを旋盤で加工する際、高品質な仕上がりを実現するためにはいくつかのコツがあります。まず、適切な切削速度と切り込み量を設定することが重要です。これにより、アルミニウムの加工時に過度な熱が発生しにくくなり、精度の高い加工が可能となります。さらに、刃先の適切な形状や精度を保つこともポイントです。刃先が正確であれば、加工時の振動や歪みを最小限に抑えることができます。例えば、適切なドリルを使用することで、穴あけ作業においても安定した加工が期待できます。これらのコツを念頭において、アルミニウムの旋盤加工に取り組むと、より効果的な加工が可能となります。
アルミニウム旋盤加工におけるドリルの使用術
ドリル選びの基準とその理由
アルミニウムを旋盤で加工する際、適切なドリルを選ぶ基準とその理由についてお伝えします。まず、アルミニウムは柔らかい素材であるため、加工する際には高速回転が必要です。このため、ドリルの素材は耐摩耗性が高く、刃先が鋭いものが適しています。さらに、適切な冷却液を使用することで、加工中の摩擦熱を逃がし、作業効率を向上させることができます。
具体例として、高速鋼(HSS)製のドリルやコバルト合金製のドリルがアルミニウム加工に適しています。これらの素材は耐摩耗性が高く、長時間の使用でも刃先が鈍らず、作業効率を保つことができます。
まとめると、アルミニウムを旋盤で加工する際には、刃先が鋭く耐摩耗性の高いドリルを選び、適切な冷却液を用いることが重要です。これらのポイントを押さえることで、効果的にアルミニウム加工が行えるでしょう。
ドリル加工の際の冷却技術
アルミニウムを旋盤で加工する際の重要なポイントは、冷却技術です。アルミニウムは加工中に熱を持ちやすく、過熱すると加工精度が低下します。そのため、ドリル加工時には適切な冷却を行うことが重要です。
なぜ冷却が必要なのでしょうか?アルミニウムは熱に敏感な素材であり、加工中に生じる摩擦熱や切削時の熱によって急速に温度が上昇します。この過熱を防ぎ、アルミニウムの性質を損なわないために、冷却が欠かせません。
たとえば、水や切削液を使用して適切な冷却を施すことで、アルミニウムの加工精度を高めることができます。冷却によって熱を逃がし、加工効率と品質を向上させることができるのです。アルミニウムを効果的に加工するためには、冷却技術の適切な活用が欠かせません。
ドリルの寿命を延ばすメンテナンス方法
「プロが伝授:アルミニウムを旋盤で加工するコツ」
アルミニウムを旋盤で加工する際には、いくつかのコツがあります。まず、切削速度や切り込み深さを適切に設定することが重要です。これにより、加工精度が向上し、加工過程での問題を最小限に抑えることができます。さらに、適切な切削油を使用することも大切です。切削油は摩擦を減らし、刃先の摩耗を抑える役割があります。
例えば、アルミニウム製の部品を旋盤で加工する際に、切削速度を上げ過ぎると刃先の寿命が短くなることがあります。逆に、適切な切削速度を設定することで、ドリルの寿命を延ばすことができます。このように、正しい加工方法を選択することが、アルミニウム加工におけるポイントとなります。
アルミ加工のための旋盤設定と操作
旋盤のセットアップと調整
アルミニウムを旋盤で加工する際に重要なのは、旋盤のセットアップと調整です。まず、正確な加工を実現するために、旋盤の刃物を適切にセットアップする必要があります。刃物の切れ味や位置を調整し、加工するアルミニウムに適した刃物を選択します。さらに、適切な速度や切削深さを設定することも重要です。例えば、アルミニウムはやわらかい金属なので、高速で切削することが一般的です。
また、適切なドリルを使用することも大切です。アルミニウムの特性を考慮して、適切な種類のドリルを選択し、正確な穴を加工します。これらのコツを理解し、旋盤のセットアップと調整を行うことで、効率的にアルミニウムを加工することが可能となるのです。
アルミニウム加工のための旋盤操作テクニック
アルミニウムを旋盤で加工する際のコツをご紹介します。まず、旋盤操作のテクニックをマスターすることが重要です。アルミニウムは柔らかい金属であり、正確な操作が必要です。例えば、ドリルの適切な使用や研磨方法の確認など、旋盤での加工に必要なスキルが求められます。アルミニウムは熱伝導率が高いため、高速の切削や適切な冷却が必要です。さらに、適切な工具の選択や加工速度の調整も重要です。これらの要点を押さえることで、アルミニウムを効率的に加工することができます。旋盤を使ったアルミニウム加工は、正しいテクニックと注意深い操作が成功の鍵となります。
加工誤差を減らすための工夫
アルミニウムを旋盤で加工する際に、加工誤差を減らすための工夫が重要です。まず、正確な設定が必要です。適切な切削速度や切削量を設定することで加工精度を向上させることができます。また、切削油や冷却液を使用することで加工中の熱を逃がし、加工誤差を軽減することができます。
さらに、適切なドリルを使用することも重要です。アルミニウムに適したドリルを選択することで、加工時の振動やずれを最小限に抑えることができます。このような工夫をすることで、アルミニウムを旋盤で精密に加工する際の誤差を効果的に減らすことができます。
実践!アルミ旋盤加工のためのステップバイステップ
加工前の準備工程
アルミニウムを旋盤で加工する際の準備工程についてご紹介します。まず、加工前には適切な固定が必要です。アルミニウムは柔らかい金属であり、しっかり固定しないと正確な加工が難しくなります。次に、適切な刃物や工具を用意することも重要です。アルミニウムは切削しやすい素材ですが、適切な刃物を選ばないと加工面が荒れてしまうことがあります。例えば、適切なドリルを使用することで、滑らかな仕上がりを実現できます。
このように、アルミニウムを旋盤で加工する際には、適切な固定と適切な工具の選択が重要です。これらの準備工程をしっかりと行うことで、正確かつ美しい加工が可能となります。是非、これらのポイントを意識してアルミニウム加工に挑戦してみてください。
実際の加工プロセス
アルミニウムを旋盤で加工する際のコツを知りたいと思っている方へ、実際の加工プロセスについてお伝えします。アルミニウムは軽くて耐食性に優れた金属であり、旋盤を使用する際には適切な工具と技術が必要です。まず、適切なドリルビットを選び、適切な回転数と切削速度を確保します。アルミニウムは柔らかい金属なので、高速で切削することが重要です。また、加工する際には冷却液を使用して過熱を防ぎます。このように、正しい工具と技術を使いながら、丁寧にアルミニウムを旋盤で加工することがポイントです。これらのコツを抑えて作業を行うことで、きれいな仕上がりを得ることができます。
加工後の仕上げと検査
アルミニウムを旋盤で加工する際に、重要なポイントは加工後の仕上げと検査です。アルミニウムの特性を理解し、正確な加工を行うことが大切です。加工後の仕上げ作業では、表面の滑らかさや寸法の精度を確認します。さらに、検査工程では、製品の品質を確保するために、隅々まで細部をチェックします。例えば、ドリルで穴を開ける際には、穴の位置や深さを正確に測定し、製品の仕様に適合しているかを確認します。こうした工程を丁寧に行うことで、アルミニウム製品の品質を高めることができます。加工後の仕上げと検査を丁寧に行い、確かな製品を提供することが重要です。
アルミ旋盤加工のトラブルシューティング
よくある加工トラブルとその原因
アルミニウムを旋盤で加工する際によくある加工トラブルとその原因について考えてみましょう。例えば、ドリルが詰まることがあります。この問題の原因は、適切な切削速度や切りくずの適切な排出ができていない可能性が考えられます。また、アルミニウムは熱に弱いため、加工中に過剰な熱が発生すると刃先がドリルされてしまうこともあります。
このようなトラブルを避けるためには、適切な加工条件を設定することが重要です。例えば、切削速度や送り速度を適切に調整することで、ドリル詰まりを防ぐことができます。また、冷却液を使用して加工中の熱を逃がすことも重要です。
アルミニウムの旋盤加工においては、適切な知識と技術が必要ですが、適切な対策を講じることでスムーズな加工が可能となります。
トラブル発生時の対処方法
アルミニウムを旋盤で加工する際のコツを紹介します。旋盤作業は正しい手順と注意が必要です。まず、安全を最優先にしましょう。適切な保護具を着用し、作業場を整えます。加工するアルミニウムの種類やサイズによっては、適切なドリルや切削工具を選択する必要があります。また、適切な回転数や切削速度を設定し、加工する際には適切な冷却液を使用します。
例えば、アルミニウム製の部品を作る際には、旋盤での正確な切削が重要です。適切な道具や設備を使い、作業中は慎重に動作します。これらのポイントを押さえてアルミニウム加工を行うと、安全かつ効率的に作業を行うことができます。
トラブルを未然に防ぐためのチェックリスト
【プロが伝授:アルミニウムを旋盤で加工するコツ】
アルミニウムの加工は、旋盤を使用することで効果的に行うことができます。アルミニウムは軽量で耐食性に優れ、様々な産業で使用されています。旋盤を使った加工は、精密さと効率性を両立させることができるため重要です。
アルミニウムを旋盤で加工する際のコツは、正しい切削速度と適切な刃物の選択です。高速での切削や適切な刃物の使用により、綺麗で正確な加工が可能となります。また、定期的な刃物のメンテナンスも忘れずに行い、効率的な加工を実現しましょう。
これらのポイントを押さえることで、アルミニウムの旋盤加工をスムーズに行うことができ、高品質な製品を生み出すことができます。
アルミ旋盤加工のための安全管理
旋盤作業時の安全対策
アルミニウムを旋盤で加工する時に安全が重要です。旋盤作業中は、保護メガネを着用することが必要です。これによって、目を金属粉や他の粒子から守ることができます。また、適切な作業服や手袋の着用も忘れずに。アルミニウムは熱や切削時に発生する鋭利なエッジが危険ですので、皮膚にダメージを与えないように気をつけましょう。具体的な例を挙げると、例えば、アルミニウムの旋盤作業中に金属粒子が飛散し、目に入ってしまうと大変危険です。そのため、保護メガネの着用は必須です。安全対策をしっかりと講じて、作業を行いましょう。
正しい保護具の選択と使用方法
「プロが伝授:アルミニウムを旋盤で加工するコツ」
アルミニウムは軽量で優れた特性を持つ素材ですが、旋盤での加工には独特のコツが必要です。旋盤作業を行う際には、適切な保護具を着用することが重要です。例えば、安全メガネや手袋、マスクなどを着用して作業しましょう。
アルミニウムは比較的柔らかい素材なので、適切な切削速度や切削深さを設定することが大切です。また、刃物やドリルの使い方も注意が必要です。高速回転する刃物を使用する際には、安全に注意して作業を行いましょう。
プロの技術や経験を参考にしながら、アルミニウムを旋盤で加工するコツを身につけることで、安全かつ効率的に作業を行うことができます。しっかりとした知識と技術を身につけて、アルミニウム加工のスキルを向上させましょう。
安全な作業環境を維持するための規則と指導
アルミニウムを旋盤で加工する際のコツをお伝えします。アルミニウムは軽くて丈夫な金属で、旋盤を使用する際にはいくつかのポイントに気を付けることが重要です。
まず、安全な作業環境を維持するために、規則と指導が必要です。工場や作業場での作業時には、保護メガネや手袋の着用が必須です。これにより、粉塵や金属片が目や皮膚に入るのを防ぐことができます。
さらに、旋盤を使用する際は、適切なドリルや工具を選択しましょう。アルミニウムは柔らかい金属ですが、適切な刃物や加工方法を選択することで、スムーズに加工することができます。
これらのコツを守りながら、アルミニウムを旋盤で加工することで、安全かつ効率的に作業を行うことができます。
まとめ
アルミニウムを旋盤で加工する際のプロのコツを伝授します。アルミニウム加工において、適切なドリルの選定が重要です。また、旋盤の回転数や切削速度にも注意が必要です。これらのポイントを押さえることで、より効率的にアルミニウムを加工することができます。