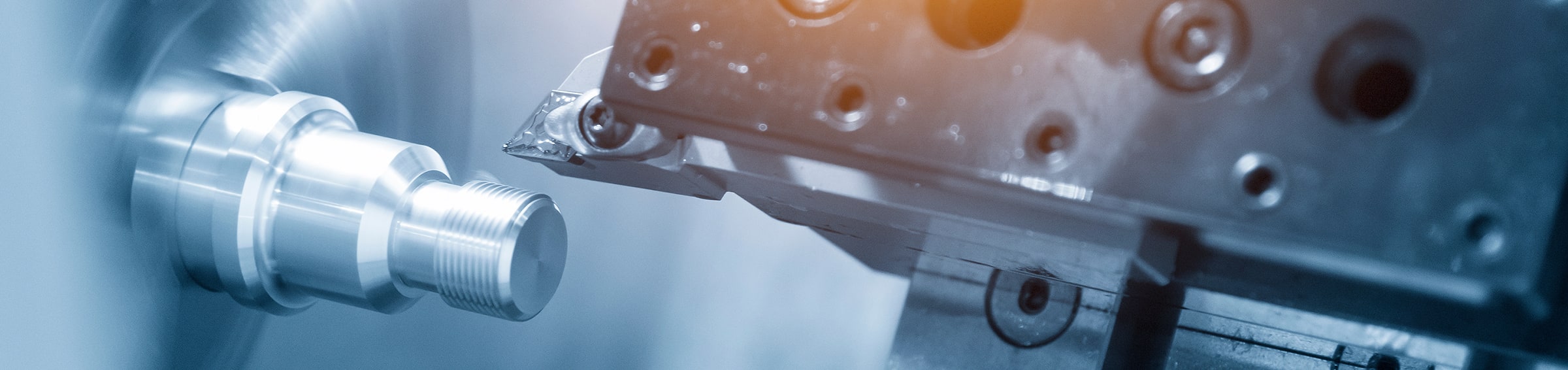
コラム column
アルミニウム合金A5052とA1050の違いとは?徹底比較で選ぶべき材料を解説
アルミニウム合金A5052とA1050、どちらを選ぶべきかお悩みではありませんか?これら二つの合金の違いや選ぶ際のポイントについて、こちらの記事では徹底的に比較して解説します。
アルミニウム合金は、さまざまな産業で広く使用されており、その中でもA5052とA1050は一般的なものです。しかし、それぞれの特性や用途によって適している場面が異なります。この記事を通じて、どちらを選ぶべきかを明確にするために必要な情報を提供いたします。
A5052とA1050の物性、強度、耐食性などの比較から、どちらがあなたのニーズに最適かを見極める手助けを致します。材料選びにおける重要なポイントを押さえ、適切な選択をするための知識を獲得しましょう。
アルミニウム合金とは
アルミニウム合金は、アルミニウムを主成分とし、他の金属や元素を加えて作られる合金です。これにより、アルミニウムの特性が強化され、より高い強度や耐腐食性、熱伝導性を持つようになります。
アルミニウム合金の基本
アルミニウム合金は主に以下の2つの種類に分けられます。
種類 | 特徴 |
---|---|
固溶体合金(アルミニウムが主) | アルミニウムに他の金属(銅、マグネシウム、シリコンなど)を溶かし込んだ合金 |
沈殿硬化型合金 | 他の金属元素を添加した後、熱処理を行って硬化させる合金 |
これらの合金は、さまざまな産業で使用されており、その特性を生かして強度や耐腐食性などの性能が向上しています。
アルミニウム合金の利点
アルミニウム合金には多くの利点があり、さまざまな分野で利用されています。
利点 | 詳細説明 |
---|---|
軽量性 | アルミニウムは非常に軽く、強度対重量比が高いため、軽量化が求められる製品に最適 |
高い耐腐食性 | アルミニウム合金は酸化皮膜を形成することで、耐腐食性が向上し、長期間使用可能 |
熱伝導性の良さ | 熱を効率よく伝えるため、電子機器や冷却システムに有用 |
加工性の良さ | 様々な形状に加工がしやすく、製造工程が効率的 |
リサイクルの容易さ | アルミニウム合金はリサイクルが可能で、環境にやさしい素材 |
アルミニウム合金は、その軽量で高強度な特性から、航空機や自動車、建設、電子機器など、さまざまな分野で利用されています。
アルミニウム合金A5052の特性
アルミニウム合金A5052は、特に耐食性や加工性に優れた合金であり、さまざまな工業用途に使用されます。以下に、A5052の化学成分、特徴、機械的性質について詳細に説明します。
A5052の化学成分と特徴
A5052合金は、主にマグネシウム(Mg)とクロム(Cr)を含むアルミニウム合金であり、その組成により優れた耐食性を持っています。また、この合金は軽量かつ高強度で、工業用途で広く使用されています。
A5052の化学成分
成分 | 含有量 (%) |
---|---|
アルミニウム (Al) | 残り成分(主成分) |
マグネシウム (Mg) | 2.2 – 2.8 |
クロム (Cr) | 0.15 – 0.35 |
鉄 (Fe) | 最大 0.4 |
銅 (Cu) | 最大 0.1 |
マンガン (Mn) | 最大 0.1 |
シリコン (Si) | 最大 0.25 |
A5052の特徴
A5052は、優れた耐食性、加工性、強度などを持つため、さまざまな産業で利用されています。
特徴 | 詳細説明 |
---|---|
優れた耐食性 | 海水や化学薬品に対して高い耐食性を持ち、船舶や化学プラントで使用される。 |
高い加工性 | 鋳造、溶接、冷間加工や熱間加工が可能で、さまざまな形状に加工できる。 |
軽量かつ強度が高い | 軽量でありながら高い強度を持ち、航空機や自動車部品に適している。 |
耐久性 | 厳しい環境下でも耐久性があり、圧力容器や機械構造物などで使用される。 |
良好な溶接性 | 溶接後の強度や耐久性を保持し、溶接作業が容易である。 |
A5052の利用例
A5052は、その耐食性、強度、加工性から多くの産業で使用されています。
用途 | 詳細説明 |
---|---|
船舶 | 海水環境で長期間使用可能な船体や防食材料に使用される。 |
圧力容器 | 高い耐圧性が求められる圧力容器に適しており、化学プラントなどでも利用される。 |
自動車部品 | 軽量化を目的とした自動車のボディ部品やその他の構造部品に使用される。 |
建築資材 | 外装材や屋根材、建築現場で使用されるさまざまな部品に使用される。 |
A5052の機械的性質
A5052の機械的性質は、耐摩耗性や高い強度、良好な伸びなどを示し、さまざまな厳しい環境で使用可能です。
性質 | 値 |
---|---|
引張強さ | 210 MPa(最小値) |
降伏強さ | 145 MPa(最小値) |
伸び | 12%(最小値) |
硬度 | 60〜70 HB(ブリネル硬度) |
引張モジュラス | 70 GPa |
密度 | 2.68 g/cm³ |
特徴
- 引張強さと降伏強さ: 引張強さが210 MPa、降伏強さが145 MPaと、高い強度を持ち、負荷のかかる構造物に最適です。
- 耐摩耗性と硬度: 高い硬度を持ち、摩擦環境でも耐えることができるため、長期間の使用に適しています。
- 伸びと柔軟性: 伸びが12%と高く、加工性に優れ、成形や曲げ加工がしやすいです。
- 耐食性: 海水や化学薬品に対する優れた耐食性があり、過酷な環境でも使用可能です。
A5052はその多様な特性により、非常に広範な用途に対応しており、特に耐食性が求められる産業や製品で重宝されています。
A5052の加工性と溶接性
A5052は、優れた強度と耐食性を誇るアルミニウム合金であり、様々な加工方法に適しており、溶接性にも優れています。以下にその加工性や溶接性について整理します。
A5052の加工性
特性 | 詳細 |
---|---|
切削性 | 良好(硬度が高いため工具の摩耗に注意) |
曲げ性 | 良好(適切な工具と条件で成形可能) |
伸び | 12%(最小値) |
加工温度 | 300°C〜400°C |
A5052は、切削や曲げ加工において良好な性能を発揮しますが、強度が高いため、適切な工具と条件の選定が重要です。特に硬度が高いため、冷却を行うことで過度の摩耗を防ぐことが推奨されます。加工温度は300°C〜400°Cが最適です。
A5052の加工における注意点
- 切削や曲げ加工時における過度の摩耗を防ぐため、冷却を行うことが必要です。
- 加工温度範囲を守ることで、材料の変形を最小限に抑えつつ加工が可能です。
A5052の溶接性
特性 | 詳細 |
---|---|
溶接方法 | TIG、MIG(最適) |
溶接後の強度 | 高い(溶接部も強度が保たれる) |
熱影響範囲 | 軽微(熱変形や応力が少ない) |
注意点 | 適切なガスと電流設定が必要 |
A5052は、TIGやMIG溶接において優れた溶接性を発揮します。溶接後の強度も高く、熱影響範囲が小さいため、溶接部の強度低下リスクが少なく、信頼性の高い溶接が可能です。適切なガスや電流設定を選ぶことが、優れた溶接品質を確保するために重要です。
A5052の溶接における注意点
熱影響範囲が小さいとはいえ、過熱を避けるための注意が求められます。
TIGおよびMIG溶接が最適ですが、適切な溶接ガスと電流設定を選ぶことが必要です。
A1050の特性
A1050は、純度が高く、柔軟性に優れたアルミニウム合金であり、主に軽量化が求められる用途に適しています。耐食性は良好で、加工性にも優れていますが、強度や耐久性が重要な場合には他の合金(例えばA5052)に比べて劣ります。以下にA1050の特性をまとめます。
A1050の化学成分と特徴
成分 | 含有量 (%) |
---|---|
アルミニウム (Al) | 99.5%以上 |
シリコン (Si) | 0.25%以下 |
鉄 (Fe) | 0.40%以下 |
銅 (Cu) | 0.05%以下 |
マンガン (Mn) | 0.05%以下 |
マグネシウム (Mg) | 0.05%以下 |
亜鉛 (Zn) | 0.05%以下 |
チタン (Ti) | 0.05%以下 |
A1050は高純度のアルミニウム合金であり、成形や加工が非常に容易で柔軟性に優れています。耐食性も良好で、特に大気中や水中での腐食に強い特性を持ちます。
A1050の特徴
- 強度: 純度が高いため強度は低いですが、柔軟性に優れています。
- 耐食性: 大気や水中での腐食に強く、優れた耐食性を持っています。
- 加工性: 成形や加工が非常に容易で、柔らかく加工性に優れています。
- 重量: 軽量で、軽い部品や構造物に使用されます。
- 熱伝導性: 良好な熱伝導性を持ち、放熱を要する部品にも適しています。
A1050の機械的性質
A1050は柔軟性と加工性に優れ、主に軽量化や加工しやすさが求められる用途に使用されます。以下はA1050の主な機械的性質です。
特性 | 詳細 |
---|---|
引張強度 | 約 70-110 MPa |
降伏強度 | 約 40-90 MPa |
伸び(破断) | 15-30%(引っ張り試験における延び率) |
硬度 | 約 40-60 HB(ブリネル硬度) |
加工性 | 非常に優れた加工性を持ち、成形や加工が容易。 |
耐摩耗性 | 一般的には中程度の耐摩耗性を持つ。 |
耐食性 | 良好で、大気や水中での腐食に強い。 |
A1050は、柔軟性と加工性に優れた特性を活かして、軽量部品や複雑な形状を必要とする製品に最適です。
A1050の用途例
建築材料: 軽量で成形が容易なため、建材として使用されることがあります。
食品包装: 軽量で加工が容易なため、食品包装に使用されます。
電気製品のケース: 加工しやすいため、電気機器や家電の外装ケースに利用されます。
装飾品: 良好な耐食性を活かして、装飾品や家庭用品にも適しています。
リーマ加工の妙技!アルミニウムを高精度に仕上げるコツ
アルミニウムの仕上げにおいて、高精度な加工を行うために欠かせないのがリーマ加工です。リーマを使用することで、アルミニウム製品の仕上がりに際立った質感と精度をもたらすことができます。本記事では、リーマ加工の妙技に焦点を当て、アルミニウムをどのように高精度に仕上げるかについて探求していきます。旋盤技術やリーマの使い方、コツなど、アルミニウム加工における重要なポイントを詳しく解説します。アルミニウム加工への新たな知識や技術を身につけ、製品の品質向上に役立ててみませんか?
Contents
リーマ加工の基本
リーマ加工とは
リーマ加工とは、アルミニウムなどの金属を高精度に仕上げる技術のことです。この技術は、旋盤や工作機械を使用して、精密な穴や溝を作り出す際に活用されます。例えば、自動車や航空機などの産業では、エンジンや航空機部品の製造にリーマ加工が欠かせません。
リーマ加工の特長は、精度が高く、仕上がりが美しいことです。これにより、部品同士の緻密な組み合わせや優れた動作が可能となります。さらに、アルミニウムなどの軽量金属にも効果的であり、高い信頼性を持つ製品を生産することができます。
アルミニウムの利用が広がる中、リーマ加工の技術はますます注目されています。高い技術力と精密さを要求されるこの技術は、製造業において欠かせない存在となっています。
アルミニウムとリーマ加工の関係
アルミニウムを高精度に仕上げる上で重要な手法の一つが、リーマ加工です。旋盤を使用してアルミニウムを削る際、加工後の仕上がりをさらに精度良くするためにリーマが用いられます。この工程により、穴の精度や表面の滑らかさを向上させることが可能です。
例えば、航空機のエンジン部品や自動車のシャーシなど、高精度を要求される部品の製造においてリーマ加工は欠かせません。リーマは穴の直径や形状を正確に整えることができるため、パーツ同士の合う度合いや機能性を向上させる役割を果たします。
このように、アルミニウムを高精度に仕上げるためには、リーマ加工が重要な役割を果たしています。そのため、産業界においてリーマ技術の重要性が高まっています。
旋盤を用いたリーマ加工の概要
アルミニウムを高精度に仕上げるためのリーマ加工は、旋盤を活用する精密加工技術の一つです。リーマとは、穴を正確な寸法に加工する工具のことであり、アルミニウムの素材特性を活かすために重要です。例えば、航空機部品や自動車エンジン部品など、高精度が求められる分野で広く利用されています。
リーマ加工の利点は、高い精度を保ちながらスムーズに加工できることです。旋盤と組み合わせることで、アルミニウムの加工が効率的に行えます。つまり、正確な穴を確実に加工することが可能となり、製品の品質向上につながります。
このように、旋盤を用いたリーマ加工は、アルミニウム素材の高精度加工において重要な技術であり、様々な産業分野で活躍しています。
アルミニウムリーマ加工の精度向上
精度向上のためのリーマ選択
アルミニウムの加工において、高い精度を求める場合、リーマ加工は重要な役割を果たします。リーマは旋盤加工において、穴を精密に仕上げる工具です。アルミニウム素材の特性を考慮して、適切なリーマを選択することが精度向上の鍵となります。
リーマの選択には様々な要素があります。例えば、加工するアルミニウムの硬度や形状、加工する穴の大きさに合わせてリーマを選定する必要があります。柔らかいアルミニウムの場合は、刃先の形状やコーティングが重要です。また、加工する穴の精度要求に応じて、適切なリーマの径を選択することで、仕上がりの精度を向上させることができます。
このように、アルミニウムを高精度に加工するためには、適切なリーマの選択が重要です。リーマの使い方や選び方をマスターすることで、品質の向上や生産性の向上につながることを覚えておきましょう。
リーマ加工時のアルミニウムの挙動
アルミニウムを高精度に仕上げる際、リーマ加工の技術が欠かせません。リーマは、アルミニウムを正確に加工するための道具であり、回転させることで精密な穴加工を行います。アルミニウムは軽くて強度がありますが、加工が難しい特性も持ちます。リーマ加工を行うことで、精度が向上し、仕上がりが均一になります。たとえば、自動車エンジンのシリンダーブロック内の穴加工など、高い精度が求められる部品にリーマ加工が活用されています。アルミニウムの挙動を理解し、リーマ加工を上手に行うことで、高品質な製品が生まれるのです。アルミニウム加工において、リーマ加工の妙技は欠かせない要素と言えます。
加工精度を左右する要因
アルミニウムを旋盤加工する際に、リーマ加工は高精度な仕上がりを実現する重要な要素です。リーマとは、穴を正確に拡大する工具で、加工精度を左右する要因となります。例えば、適切なリーマの選択は加工結果に大きな影響を与えます。素材や加工条件に合った適切なリーマを選ぶことで、アルミニウムの仕上がりに一層の精度が求められます。また、リーマの刃先の状態や刃先の角度も重要です。良好な刃先状態を保つことで、加工精度を保つことができます。このように、リーマ加工はアルミニウム加工において精度を左右する要素であり、適切なリーマの選択や保守が高品質な仕上がりを実現するポイントとなります。
リーマ加工の効率的な方法
効率的な旋盤操作のコツ
アルミニウムの加工において、高い精度を求める際に活用されるリーマ加工は、旋盤操作において重要な技術の一つです。アルミニウムは軽量でありながら高い強度を持つため、様々な産業で利用されています。リーマ加工を行う際には、以下のポイントに注意することが重要です。
まず、リーマ加工を行う前に、アルミニウムの種類や硬度を正しく把握することが必要です。適切なリーマを選択することで、高精度な加工が可能となります。さらに、適切な切削速度や切削量を設定することで、作業効率を向上させることができます。
具体的な例を挙げると、航空機産業では、エンジン部品やフレームにアルミニウムが使用されており、高精度なリーマ加工が要求されています。このように、アルミニウムの高精度加工は様々な産業で重要な技術となっています。
リーマの速度と送りの最適化
リーマ加工は、アルミニウムを高精度に仕上げる重要な技術です。リーマの速度と送りを最適化することで、より精密な加工が可能となります。例えば、旋盤を使用してアルミニウムを削り出した後、リーマを使って穴を正確に拡大することができます。
このような工程により、アルミニウム製品の仕上がりや品質が向上し、製品の耐久性や精度が確保されます。また、リーマ加工は熱による歪みを最小限に抑えることができるため、加工後の製品がより安定した状態で利用できるでしょう。
つまり、リーマ加工はアルミニウム加工において欠かせないテクニックであり、速度と送りを適切に調整することで、高品質な製品を生産することが可能となります。
効率化に貢献する工具と機器
リーマ加工の妙技!アルミニウムを高精度に仕上げるコツ
アルミニウムを高精度に仕上げるためには、旋盤を使用するのが一般的です。アルミニウムは軽量で耐久性があり、工業製品や航空機部品などに広く使用されています。旋盤を使用することで、アルミニウムの表面を滑らかに仕上げることができます。
リーマと呼ばれる工具を使用することで、精密な穴加工が可能となります。リーマは穴の直径や形状を正確に整えるために使われ、高精度な加工が求められるアルミニウム加工において重要な役割を果たします。
例えば、航空機のエンジン部品や自動車のエンジンブロックなど、高い精度が求められる製品にはリーマ加工が欠かせません。リーマを使うことで、アルミニウム製品の品質と精度を向上させることができます。
穴径精度を上げるリーマ加工技術
穴径精度を高める前処理
アルミニウムを高精度に仕上げるための重要な工程として、穴径精度を高める前処理があります。アルミニウムを旋盤で加工する際、リーマを使用して穴を作る際に、穴径の精度が向上することが求められます。そのためには、まず適切な切削速度と切削量を設定し、リーマの位置を正確に調整する必要があります。
例えば、アルミニウムの穴径を高精度に仕上げる際には、旋盤の切削速度を適切に設定してリーマを使い、正確な穴を作成します。このように、穴径精度を高める前処理を丁寧に行うことで、アルミニウム加工の品質を向上させることができます。
穴径精度に影響するリーマの使用方法
アルミニウムを高精度に仕上げるためには、リーマの使用方法が重要です。リーマは穴径の精度に大きな影響を与えます。リーマを効果的に使用するためには、回転数や送り速度、適切な切削油の使用などがポイントです。
まず、リーマの適切な回転数と送り速度を設定することが重要です。高過ぎる回転数や送り速度は精度を損なう可能性がありますので、適切な条件を見極めることが必要です。
また、切削油を使用することで切削時の摩擦を減らし、アルミニウムの仕上がりを向上させることができます。適切な切削油を選択し、定期的に交換することで作業効率も向上します。
これらのコツを抑えることで、アルミニウムを高精度に仕上げることが可能となります。
穴径精度を確保するための後処理
アルミニウムの旋盤加工において、穴径の精度を確保するための重要な工程がリーマ加工です。リーマは、金属を高精度に仕上げる工具であり、加工後の仕上がりに大きく影響を与えます。例えば、自動車エンジンのシリンダーブロックでは、リーマを使用してピストンとの隙間を適切に設定することが重要です。このように、リーマ加工はアルミニウム部品の精度を高める上で欠かせない工程なのです。
リーマ加工によって、穴径の均一性や仕上がりの滑らかさを確保することができます。特に精密機器や航空機部品など、高い精度が求められる分野では、リーマ加工が欠かせません。したがって、アルミニウム部品の製造において、リーマ加工の技術や熟練した職人の技術は非常に重要となっています。リーマ加工の妙技を習得し、穴径精度を確保することで、高品質なアルミニウム部品の製造に貢献できるでしょう。
微細穴の設計とリーマの口径のマッチング
微細穴加工のためのリーマの選択
アルミニウムの加工において、高精度な仕上げを行うために欠かせないのがリーマ加工です。アルミニウムを旋盤で加工する際、微細穴を作る必要があるとき、リーマは非常に重要な役割を果たします。リーマは穴の直径や表面の仕上がりを均一に整えることができ、精密な加工を実現します。
リーマ加工には正確な選択が求められます。適切なリーマを選ぶことで、アルミニウムの加工精度を高めることができます。例えば、硬度や形状に合ったリーマを選ぶことが重要です。また、適切な刃先形状やコーティングを選択することで、寿命を延ばし、効率的な加工が可能となります。
したがって、アルミニウムを高精度に仕上げるためには、リーマ加工を適切に行うことが不可欠です。正しいリーマの選択を行い、精密な加工を実現しましょう。
リーマ口径の精度と微細穴設計
高精度な加工技術で知られるリーマ加工は、アルミニウムを精密に仕上げるために重要です。アルミニウムは軽くて丈夫な素材であり、さまざまな産業で使用されています。旋盤を使用することで、リーマを使ってアルミニウムを高精度に加工することができます。
リーマ口径の精度は、微細な穴設計において特に重要です。例えば、自動車のエンジン部品や航空機の機械部品など、高い精度が求められる分野でリーマ加工は欠かせません。リーマの正確な設計と適切な使用は、製品の品質と信頼性に直結します。
アルミニウムの高精度加工には、リーマ加工が不可欠であり、その効果は各産業で大きな影響を与えています。リーマ加工の妙技を活用することで、アルミニウム製品の品質向上や生産効率の向上が期待されます。
微細穴加工におけるリーマの調整
アルミニウムを高精度に仕上げるための妙技、それが旋盤とリーマを使った微細穴加工です。リーマは穴を正確な寸法に拡張する工具であり、加工の精度を高める重要な役割を果たします。アルミニウムは加工が難しい素材の1つであり、微細な穴を作る際には特に注意が必要です。
旋盤による穴の開始処理を経て、リーマを使用して精密に仕上げることで、アルミニウム製品の品質が向上します。この技術は航空機部品や自動車部品など、高い精度が求められる産業分野で広く活用されています。
アルミニウム加工におけるリーマの適切な調整と使い方は、製品の品質と耐久性に直結します。技術の習得には熟練と経験が必要ですが、正しく活用することで高精度なアルミニウム製品を生み出すことが可能です。
アルミニウムリーマ加工の注意点と方法
アルミニウム加工時の一般的な注意点
アルミニウムを高精度に仕上げる際のポイントについてお伝えします。アルミ加工において、特に重要なのが旋盤やリーマの適切な使用です。アルミニウムは加工が難しい素材の一つであり、旋盤加工やリーマ加工においては、適切な刃先の選択や適正な工具の使い方がポイントとなります。
例えば、リーマはアルミニウムの柔らかさを考慮して適切な刃先を選ぶことが必要です。また、旋盤を使用する際には、適切な切削速度と切削深さを確保することが重要です。これらの工程を正確に行うことで、アルミニウムを高精度に仕上げることが可能となります。
加工時には、素材特性や工具の使い方に留意し、慎重に作業を行うことが重要です。適切な加工方法を選択し、細部まで気を配ることで、高品質な仕上がりを実現できます。
リーマ加工固有の注意事項
リーマ加工は、アルミニウムを高精度に仕上げるための技術です。この加工方法を使うと、旋盤で加工した部品の仕上がりをより精密にすることができます。例えば、自動車のエンジン部品や航空機の部品など、高い精度が求められる製品に利用されています。
リーマ加工を行う際には、注意が必要です。加工するアルミニウムの種類や硬度、切削条件などを適切に設定することが重要です。また、加工中に適切な冷却や潤滑を行うことで、部品の品質を確保できます。
リーマ加工は、素材を細かく削り取るため、正確な加工が求められます。この技術を使うことで、アルミニウム部品の精度や耐久性を向上させることができます。
アルミニウムリーマ加工のベストプラクティス
アルミニウムリーマ加工は、精密な仕上げが求められる作業です。旋盤での加工においてリーマ技術を駆使することで、高精度な加工が可能となります。例えば、アルミニウム製の部品や構造物に対して、正確な穴加工が必要な場合、リーマ加工は欠かせません。リーマは、精密な切削工具であり、微細な調整を行うことで、部品同士のシームレスな組み合わせが可能となります。このように、アルミニウムリーマ加工は、部品の精度や耐久性を向上させる重要な技術と言えるでしょう。高品質なアルミニウム製品を生産するためには、リーマ加工のノウハウを熟知し、最新の技術を取り入れることが肝要です。
リーマ加工のトラブルシューティング
よくあるリーマ加工の問題
リーマ加工は、アルミニウムを高精度に仕上げるために重要な技術です。しかし、よくあるリーマ加工の問題点も存在します。例えば、旋盤の操作ミスによる加工精度の低下やリーマの摩耗による耐久性の問題が挙げられます。このような問題を避けるためには、適切な設備の保守や定期的な交換が必要です。
具体的な対策として、適切な切削速度や切削量を設定することで加工精度を向上させることができます。また、高品質なリーマの選定やリーマの適切な洗浄・保管も重要です。これらの対策をしっかりと行うことで、アルミニウム製品の仕上がりにおける問題を最小限に抑えることができます。リーマ加工における問題点を適切に対処することで、高品質なアルミニウム製品を生産することが可能となります。
問題発生時の対処法
アルミニウム製品を高精度に仕上げるためには、リーマ加工が重要です。アルミニウムは加工が難しい素材であり、その特性を理解することがポイントです。旋盤を使用して加工を進める際に、リーマを使用することで精度を向上させることができます。
例えば、自動車エンジン部品の加工において、リーマ加工を行うことで穴の精度を高め、部品同士の正確な組み合わせを実現します。また、航空機の部品製造においても、アルミニウム製品の高精度加工は安全性と信頼性を担保する重要な要素となります。
つまり、アルミニウム製品のリーマ加工は精密さと信頼性を求められるさまざまな産業分野で重要な役割を果たしています。高品質な製品を提供するためには、リーマ加工の技術を磨き、効果的に活用することが必要です。
トラブルを避けるための予防策
アルミニウムの加工技術において、高精度な仕上げを実現するために欠かせないのが旋盤とリーマという工具です。アルミニウムのような柔らかい金属を精密に加工するには、専門知識と技術が必要です。例えば、旋盤を使用して加工を行い、その後リーマを使って穴を精密に仕上げることで、高品質な製品が作られます。
これらの工程を丁寧に実施することで、アルミニウム製品の寸法精度や表面仕上げの質を向上させることが可能です。また、適切な切削条件や冷却方法を選択することも重要です。限られた材料を最大限に活かし、無駄を極力減らすことで製品のコストパフォーマンスを向上させることができます。
アルミニウム加工において、旋盤とリーマを上手に活用することで、高い精度と品質を実現し、製品の価値を向上させることができます。
アルミニウムリーマ加工の応用
精密部品への応用例
リーマ加工は、アルミニウム製品を高精度に仕上げるための妙技です。旋盤加工に比べて表面仕上げの品質が向上し、精密部品製造に欠かせません。リーマの回転運動によって精密な穴加工が可能となります。例えば、航空機や自動車などで使用されるエンジン部品や歯車などが挙げられます。これらの部品は高い精度が求められるため、リーマ加工は欠かせない技術となっています。アルミニウムは軽量で耐久性に優れているため、さまざまな産業で幅広く使用されています。リーマ加工によって、アルミニウム製品の品質と信頼性が向上し、製品の競争力を高めることができます。
複雑な形状とリーマ加工
アルミニウムの加工において、高精度な仕上げを実現するために欠かせないのが、旋盤とリーマ加工です。リーマ加工は複雑な形状を持つ部品や穴を精密に加工する技術であり、特にアルミニウムのような加工が難しい素材においては重要な要素となります。例えば、航空機の部品や自動車のエンジン部品など、高い精度が求められる製品にはリーマ加工が欠かせません。
この技術を使うことで、アルミニウム部品の寸法精度や仕上げの質を向上させることができます。また、金属加工全般において、リーマ加工は製品の品質向上や生産性の向上につながる重要な工程と言えます。アルミニウムを高精度に加工するためには、リーマ加工の技術を正しく理解し、適切に適用することが不可欠です。
高精度加工を求める業界での事例
『リーマ加工の妙技!アルミニウムを高精度に仕上げるコツ』
アルミニウム製品の製造では、旋盤やリーマ加工が欠かせない技術です。高い精度を求められる業界では、この技術が重要視されています。例えば、航空宇宙産業や自動車産業など、厳密な仕様が求められる分野では、アルミニウム製品の精密加工が必要不可欠です。
このような業界での事例として、航空機のエンジン部品や自動車のエンジン部品の製造プロセスでリーマ加工が活躍しています。リーマは、穴の精度を向上させ、表面仕上げを美しくするために使われます。これにより、部品同士の正確な組み合わせが可能になり、製品の品質向上に繋がります。
アルミニウム製品の高精度加工には、旋盤やリーマ加工の技術が欠かせないことを理解することが重要です。これらの技術を熟練させることで、製品の品質向上や市場競争力の強化につながることが期待されています。
経験から学ぶリーマ加工のコツ
熟練工の技術と知恵
アルミニウムを高精度に仕上げるためのリーマ加工は、熟練工の技術と知恵が必要です。アルミニウムは軽くて丈夫な金属であり、旋盤やリーマを使用して加工することが一般的です。リーマ加工では、回転する刃が複雑な形状を創り出すため、正確な加工が求められます。
そのため、熟練工は豊富な経験と技術を持っており、微細な調整や計測を行いながら、高精度な仕上げを実現します。例えば、航空機や自動車のエンジン部品など、高い品質が求められる製品においてリーマ加工は欠かせません。
熟練工の技術と知恵によって、アルミニウム製品は精密で信頼性の高い製品として多くの産業で活躍しています。そのため、リーマ加工は産業界において重要な役割を果たしています。
加工精度を上げる実践テクニック
アルミニウムを高精度に仕上げるための重要なテクニックは、リーマ加工です。リーマとは工具の一種で、抜群の加工精度を提供します。この技術の鍵は、回転軸を中心に正確に位置決めし、徐々に加工することです。例えば、アルミニウムの旋盤加工において、リーマを用いることで穴の精度を向上させることができます。このように、リーマ加工は、アルミニウムを精密に仕上げる際に欠かせない技術となっています。高品質な製品を製造するためには、リーマ加工を熟知し、適切に実践することが重要です。その結果、製品の精度が向上し、顧客満足度も高まるでしょう。
効率と精度を両立させるコツ
アルミニウムを高精度に仕上げるためのリーマ加工の妙技についてお伝えします。アルミニウムの旋盤加工において、効率と精度を両立させるコツは重要です。リーマ加工は、加工表面の仕上げを整える工程で、微細な加工精度が求められます。そのため、正確な寸法や形状に仕上げるためには、適切なリーマの選択が欠かせません。
例えば、特定の形状やサイズに合ったリーマを使用することで、アルミニウムの加工精度を高めることができます。また、適切な刃先形状や刃先加工面積を選定することで、作業効率を向上させることが可能です。
したがって、アルミニウムを高精度に仕上げるためには、リーマ加工において効率と精度を両立させる工夫が重要です。適切なリーマの選択や工具の使い方を工夫することで、より品質の高い加工が実現できます。
リーマ加工における新技術と未来
最新のリーマ加工技術
最新のリーマ加工技術がアルミニウムを高精度に仕上げることにどのような妙技を発揮するのでしょうか。リーマ加工は、旋盤を使用して加工を行い、精密な穴を作る技術です。この技術を用いることで、アルミニウム製品の精度を向上させることが可能です。例えば、航空機部品や自動車部品などで、リーマ加工が重要な役割を果たしています。
リーマ加工は、素材の硬度や粘りを考慮して適切な切削条件を設定し、微細な穴を作ることができます。これにより、アルミニウム製品の耐久性や精度が向上し、製品の品質が向上します。また、リーマ加工は高い再現性を持ち、大量生産にも適しています。
最新のリーマ加工技術は、アルミニウム製品の製造業に革新をもたらし、高精度な製品を生み出すことが期待されています。そのため、リーマ加工技術は、製造業界において欠かせない重要な技術となっています。
産業の変化とリーマ加工
アルミニウムの高精度加工において、旋盤加工だけでなくリーマ加工も重要な役割を果たしています。リーマ加工は、精密な穴加工や仕上げ加工に適しており、アルミニウム製品の品質向上に貢献しています。例えば、自動車部品や航空機の構造部品など、高精度を要求される製品の製造において欠かせない技術です。
リーマ加工は、旋盤で作られた穴の精度をさらに向上させることができます。このように、アルミニウム加工においてリーマ加工を適切に活用することで、製品の精度と仕上がりを向上させることが可能です。そのため、製造業においてリーマ加工の技術がますます重要視されています。高品質なアルミニウム製品を生産するためには、リーマ加工の技術を熟達させることが肝要です。
未来を見据えたリーマ加工の展望
アルミニウムを高精度に仕上げるリーマ加工は、工業製品の製造において欠かせない技術です。旋盤を使用して微細な加工を施すことで、アルミニウム製品の精度と仕上がりを向上させることができます。例えば、精密機器や航空機部品など、高精度を要求される製品にはリーマ加工が活用されています。
リーマ加工の魅力は、その高い精度と安定性にあります。工作物の寸法や表面仕上げに一貫性を持たせることができるため、製品の品質向上につながります。また、アルミニウムの軽さや耐久性を活かした製品を製造する際にも、リーマ加工は重要な役割を果たします。
未来を見据えると、製造業におけるリーマ加工の需要はますます高まると予想されます。高精度・高品質な製品が求められる市場では、リーマ加工技術は不可欠な存在となるでしょう。アルミニウム製品の高精度加工において、リーマ加工の技術は今後もますます注目されるでしょう。
まとめ
アルミニウムを加工する際、リーマを使用すると高精度な仕上がりを実現できます。リーマ加工の妙技を駆使すれば、アルミニウムの加工精度を向上させることが可能です。また、旋盤を使用して加工することで、さらなる精度向上が期待できます。これらのテクニックを駆使することで、アルミニウムの加工において高い品質を実現できます。
【素材の達人】A5052とA1070、耐食性と加工性の違いとは?
素材選定は製品性能に大きな影響を与えます。今回は、A5052とA1070という2つの異なる素材に焦点を当て、その耐食性と加工性の違いについて探っていきましょう。これらの素材は様々な産業で使用されており、その特性を理解することは製品設計や製造プロセスにおいて重要です。耐食性と加工性の違いを知ることで、素材選定における適切な決定を行う手助けになるでしょう。さあ、A5052とA1070を比較し、その特性に迫ってみましょう。
Contents
アルミニウム合金の基礎知識
アルミニウムとは?その特性とは
アルミニウム合金A5052とA1070は、耐食性や加工性において異なる特性を持っています。A5052はマグネシウムとクロムを含有し、耐食性に優れています。一方、A1070は純度が高く、加工性に優れています。例えば、A5052は海水などの腐食環境に強く、船舶や車両の部品によく使われます。一方、A1070はアルミホイルや調理器具などの加工に向いており、食品業界で広く使用されています。加工性や用途に合わせて適切な合金を選ぶことが重要です。したがって、A5052とA1070の選択は、耐食性や加工性などの特性を考慮して行われるべきです。
アルミ合金の種類と分類
A5052とA1070というアルミ合金には、耐食性や加工性といった違いがあります。A5052は非常に優れた耐食性を持ち、海水や塩分にさらされても錆びにくい特徴があります。一方、A1070は加工性が非常に高く、軟らかい性質を持っています。これらの違いは、それぞれの特性に合わせて異なる用途に活かされています。例えば、A5052は船舶や海洋関連の部品、屋外建築などの耐食性が求められる場面で使用されます。一方、A1070は食品包装や製缶業など、加工性が重要な分野で利用されています。両者は異なる特性を持ちながらも、それぞれの得意分野で優れた性能を発揮しているのです。
アルミ合金の選び方の基準
アルミ合金を選ぶ際に重要な基準は何でしょうか?A5052とA1070の違いに焦点を当てて考えてみましょう。A5052は耐食性に優れ、海水などの腐食に強い特徴があります。一方、A1070は加工性が高く、折り曲げや成形加工に向いています。例えば、A5052は船舶の船体や飛行機の胴体などの耐久性が求められる部分に使用されることが多いです。一方、A1070は食器や容器などの加工が必要な製品に適しています。適切な素材を選ぶことで製品の性能や品質が向上し、用途に最適な材料を選ぶことが大切です。
A5052とA1070の基本的な特徴
A5052の成分と特性
A5052とA1070、耐食性と加工性の違いは何でしょうか?A5052はアルミニウム合金で、耐食性が高く、また、加工性も優れています。一方、A1070はより純度が高く、軽量であるという特性があります。例えば、A5052は船舶や航空機の部品として使用されることが多く、耐食性が必要な場面で活躍します。一方、A1070は電気製品や包装資材などに使用され、純度と軽量性が求められる場面で重宝されます。このように、それぞれの特性や用途によって適した材料が異なります。ですので、用途や要件に合わせて適切な材料を選択することが重要です。
A1070の成分と特性
A1070の成分と特性
A1070はアルミニウム合金の一種であり、純度が高いことが特徴です。この高い純度によって、A1070は優れた腐食耐性を持っています。例えば、食品加工業界や医療機器など、腐食に強い素材が必要な分野で広く使用されています。また、A1070は加工性も優れており、曲げや切削などの加工が容易です。そのため、さまざまな製品や部品に利用されています。
一方、A5052は耐食性と強度を兼ね備えたアルミニウム合金です。海洋環境や塩害のある場所で使用される船舶部品や建築材料などに適しています。A5052は加工しやすい性質も持っており、溶接や加工がしやすいため、幅広い産業で利用されています。
A1070とA5052はそれぞれ特性に違いがありますが、用途に合わせて使い分けることで、効率的な素材選択が可能です。
A5052とA1070の物理的性質の比較
A5052とA1070の物理的性質を比較すると、A5052は耐腐食性に優れており、加工性も高い特徴を持っています。一方、A1070は比較的加工性が高いが、A5052ほどの耐食性はありません。例えば、A5052は海水などの腐食性の高い環境でも長期間耐えることができますが、A1070は同様の環境下では劣化しやすい傾向があります。そのため、環境や使用目的によって適した素材を選択することが重要です。総じて言えることは、A5052は耐食性に優れ、A1070は加工性が高いという特性があります。素材の選択には様々な要素が影響しますが、使用環境や耐久性を考慮して適切な素材を選ぶことが重要です。
A5052とA1070の耐食性の違い
耐食性とは何か?
A5052とA1070というアルミニウム合金は、耐食性と加工性の面で異なる特性を持っています。耐食性とは、金属が錆びや腐食から守られている程度を表す性質です。A5052はマグネシウムを含むことで耐食性に優れており、海水や化学物質に対しても強い特長があります。一方、A1070はより純度が高く、比較的加工性に優れています。そのため、A1070は食品容器や電気製品などの加工に適しています。耐食性を求める場合はA5052が適しており、加工性を重視する場合はA1070が選ばれる傾向があります。それぞれの用途や環境に合わせて適切な素材を選ぶことが重要です。
A5052の耐食性について
A5052とA1070の比較を考える際に、A5052は耐食性に優れている特徴があります。これは、A5052がアルミニウム合金であり、鉄や銅と比較して錆びにくいからです。例えば、A5052は海洋環境下でも優れた持続性を示し、船舶部品や海洋構造物に広く使用されています。
一方、A1070はグレードが異なり、耐食性においてA5052よりも劣る面があります。A1070は純度の高いアルミニウムであり、主に電気製品や包装材料などに使用されますが、耐食性が求められる環境では適していません。
したがって、耐食性を重視する場合はA5052を選択することが重要です。その特性を理解し、適切な材料を使用することで、製品の耐久性や品質向上につながることが確認されています。
A1070の耐食性について
A5052とA1070、耐食性と加工性の違いとは?A1070の耐食性について考えると、一般的にアルミニウム合金は酸化皮膜を形成することで耐食性を得ます。しかし、A1070は純度が高く、他の要素が少ないため、酸化皮膜の形成が遅い傾向があります。そのため、A1070はA5052に比べて耐食性が低いと言えます。
A5052と比較すると、A5052はマグネシウムやクロムを含有しており、酸化皮膜がより早く形成され、耐食性が高い特性があります。このため、塩害の強い環境や海水に触れるような場所に使用されることが多いです。
加工性においても、A5052は曲げや切削などの加工が比較的容易であり、建築や自動車部品など幅広い分野で利用されています。一方、A1070は比較的軟らかいため、深絞りやプレス加工などの加工性に優れていますが、耐食性が低いため、使用する環境によって適した材料を選ぶ必要があります。
A5052とA1070の耐食性の比較と適用分野
A5052とA1070というアルミニウム合金は、耐食性と加工性において異なる特性を持っています。A5052は耐食性に優れており、海洋環境や化学工業などの耐食性が重要な用途に適しています。一方、A1070は加工性に優れており、薄板や成形加工が必要な製品に適しています。
例えば、A5052は船舶の外装や車両のボディパネルなど、耐食性が求められる製品に使用されます。一方、A1070は圧延製品や缶の素材として広く利用されています。加工性が重要な製造プロセスにおいて、A1070の利用は効果的です。
要するに、使用する環境や製品の要求に応じて、A5052とA1070を適切に選択することが重要です。耐食性と加工性の違いを理解し、適切な素材を選ぶことで製品の品質と性能を向上させることができます。
A5052とA1070の加工性の相違
加工性とは何か?
A5052とA1070、耐食性と加工性の違いを理解するためには、まず加工性について知る必要があります。加工性とは、素材がどれだけ簡単に形を変えることができるかを示す性質です。例えば、A5052は高強度アルミニウム合金であり、耐食性に優れています。一方、A1070は純粋なアルミニウムで、加工性が高い特徴があります。
A5052は船舶や航空機などの耐食性が求められる用途に使用される一方、A1070は一般的な加工品や製缶に適しています。例えば、A5052は海水にさらされる環境下での使用に適しており、錆びにくい性質があります。一方、A1070は柔らかく加工しやすいため、製缶業界で広く利用されています。
このように、A5052とA1070はそれぞれ異なる特性を持ち、異なる用途に適しています。加工性と耐食性の違いを理解することで、適切な素材を選択し、製品を効率的に生産することができます。
A5052の加工性
A5052とA1070は、アルミニウム合金の一種です。A5052は耐食性に優れ、A1070は加工性が良いとされています。耐食性とは、金属が錆びたり腐食したりすることなく長持ちする性質を指します。A5052は海水や塩分の多い環境でも錆びにくいため、船舶や海外で使われることが多いです。一方、加工性とは材料が加工しやすい性質を意味します。A1070は加工しやすく、薄い板状に成形する際に適しています。例えば、飲料缶のような薄いアルミニウム製品に利用されています。このように、材料ごとに特性が異なるため、使用する目的によって適した合金を選ぶことが重要です。
A1070の加工性
A5052とA1070は、金属素材の中でも注目される素材です。今回はそのうちのA1070に焦点を当て、その加工性について解説します。A1070は、純度が高く、柔らかい素材であり、加工性に優れています。そのため、様々な形状や厚みに加工しやすい特性があります。例えば、軽量な部品や容器などに広く使用されています。また、溶接やめっき処理などの加工もしやすく、製品の仕上がりにも影響を与えます。このような特性から、建築や自動車産業など幅広い分野で重宝されています。A1070の加工性は、製品の製造工程や仕上がりにおいて大きなメリットを生むことができる重要な素材です。
A5052とA1070の加工性の比較と適用分野
A5052とA1070の加工性には違いがあります。A5052は耐食性に優れ、アルミニウム合金の中でも強度が高いため、船舶や飛行機の部品、食器、構造材など幅広い分野で使用されています。一方、A1070は加工性が優れており、柔らかく薄いため、容易に成形できる特性があります。そのため、食品包装、キャップ、電子部品などの製造に適しています。例えば、A1052は船舶の甲板や航空機の外板に用いられ、その強度と耐食性が重要視されています。一方、A1070は食品容器や電解コンデンサなどの用途で使用され、加工性が重視されています。このように、それぞれの特性に応じて異なる分野で利用されており、産業界において重要な役割を果たしています。
アルミ合金の強度とその評価方法
アルミ合金の強度とは
アルミ合金の中でもA5052とA1070は、耐食性と加工性に違いがあります。A5052は耐食性に優れ、海水や塩類雰囲気にも強く、船舶や海洋関連の部品に利用されています。一方、A1070は加工性が優れており、押出成形や圧延加工に適しています。例えば、A5052は船舶の甲板や船体、A1070は食品包装、器具などに使用されています。このように、用途や環境に合わせて適切なアルミ合金を選ぶことが重要です。異なる特性を持つこれらの合金は、それぞれの利点を活かしてさまざまな産業分野で活躍しています。アルミ合金の特性を理解し、適切に活用することで、製品の品質や効率を向上させることができます。
A5052の強度と特性
A5052とA1070、耐食性と加工性の違いとは?
アルミニウム合金A5052とA1070を比較すると、A5052は耐食性に優れ、A1070は加工性が優れています。A5052は海水や塩分などの腐食から保護されるため、船舶や海洋関連の部品に適しています。一方、A1070は軽くて柔らかく、熱伝導性が高いため、調理器具や電気製品などの加工に適しています。
例えば、A5052は船舶の外装パネルや海水中で使用される部品に適しています。一方、A1070はホイルや容器、電線などの加工に適しています。
このように、用途に応じて適切な材料を選択することが重要です。A5052とA1070はそれぞれの特性によって異なるニーズに対応し、幅広い産業分野で活躍しています。
A1070の強度と特性
A5052とA1070は、金属の素材として使われることがありますが、その耐食性や加工性にはどのような違いがあるのでしょうか?A5052は耐食性に優れており、塩水や薬品に強い特性があります。一方、A1070はA5052よりも加工性が高く、曲げや加工がしやすい特性があります。例えば、A5052は海水や食品工場の設備などで使用されることが多く、耐食性が要求される場面で活躍します。一方、A1070は容器やヒンジなど、加工が必要な部品に使われることが多いです。このように、用途に合わせて適切な素材を選ぶことが重要です。A5052とA1070、それぞれの特性を理解することで、製品の耐久性や加工しやすさを向上させることができます。
強度を左右する要因とは
A5052とA1070というアルミニウム合金には、耐食性や加工性など、それぞれ違いがあります。例えば、A5052は耐食性が高く、海水などの腐食にも強い特徴があります。その一方で、A1070は加工性に優れており、曲げやプレス加工がしやすいです。こうした違いは、使用する環境や加工方法によって適した素材を選ぶ上で重要です。例えば、海岸近くの建築物にはA5052が適していますが、加工性が求められる箇所ではA1070が適しています。素材の選択は、製品の性能や耐久性に直結するため、使用目的や要件に合わせて適切な合金を選ぶことが重要です。
A5052とA1070の用途と適用分野
アルミ合金の一般的な用途
A5052とA1070というアルミ合金は、それぞれ異なる特性を持っています。A5052は耐食性に優れている一方、A1070は加工性に優れています。例えば、A5052は海水などの腐食環境下で使用されることが多く、船舶の部品や海水浴場の設備などに利用されています。一方、A1070は薄い板状に加工しやすいため、食品包装や電気製品のケースなどに広く使用されています。
これらの違いから、用途や環境に合わせて適切なアルミ合金を選ぶことが重要です。耐食性が必要な場合はA5052を、加工性が重要な場合はA1070を選ぶことで、製品の性能や耐久性を向上させることができます。アルミ合金の選択は製品の品質や効率に直結するため、適切な選択が重要です。
A5052の主な使用例
【素材の達人】A5052とA1070、耐食性と加工性の違いとは?
アルミ合金のA5052とA1070、この二つの素材の違いを知っていますか?A5052は耐食性に優れ、外部環境にも強く、海水にも対応できます。一方、A1070は加工性が高く、薄い板やフィルムとして幅広く使用されています。
例えば、船舶や航空機の構造部品にはA5052が使用され、海水や風雨にさらされても劣化しにくい特性が活かされています。一方、A1070は食品包装や電気製品の外装など、加工のしやすさが求められる場面でよく使用されています。
どちらも異なる特性を持ち、それぞれの適した用途に活用されています。工業製品や日常生活で使われる製品には、それぞれの素材の特性を理解して適切に選択されています。
A1070の主な使用例
【素材の達人】A5052とA1070、耐食性と加工性の違いとは?
A5052とA1070は、どちらもアルミニウム合金の特性を持っていますが、耐食性や加工性において異なる点があります。まず、A5052は耐食性に優れており、海水や塩分の多い環境での使用に適しています。一方、A1070は加工性に優れており、薄板加工やプレス加工に適しています。
具体的な使用例として、A5052は船舶の構造部品や海水槽、または外壁パネルなどの耐塩害性が求められる場面で利用されます。一方、A1070はキッチン用品や容器などの加工性が重要な製品に使用されることが多いです。
したがって、用途や要件に合わせて適切な素材を選択することが重要です。耐食性が必要な場合にはA5052を、加工性が重要な場合にはA1070を選ぶことで、製品の性能や耐久性を向上させることができます。
使用分野におけるA5052とA1070の選択基準
A5052とA1070は、金属素材の中でも異なる特性を持つ2つのタイプです。A5052は主に船舶や航空機の部品、そして車両のボディパネルなど、耐食性が重要な分野で使用されます。一方、A1070は食品包装や建築材料など、加工性が求められる分野で活躍します。例えば、A5052は海水や食塩に強い耐食性を持ち、A1070は折り曲げや溶接などの加工がしやすい特性があります。
したがって、使用する分野や要求される性能によって、A5052とA1070を選択する基準が異なります。耐食性が必要な場合はA5052を、加工性が重要な場合はA1070を選択することが一般的です。素材の選択は製品の品質や耐久性に直接影響するため、適切な素材選定が重要です。
アルミ合金選定のためのまとめとチェックリスト
素材選びのポイント
A5052とA1070は、金属素材の中で耐食性や加工性において異なる特性を持っています。A5052は耐食性に優れ、海水などの腐食環境にも強い素材です。一方、A1070は加工性が高く、曲げ加工や深絞り加工に向いています。例えば、船舶や航空機などの耐食性が重要な部分にはA5052が使われ、加工性が重要な部分にはA1070が選ばれます。従って、使用する環境や目的に応じて適切な素材を選ぶことが重要です。A5052とA1070の比較によって、それぞれの特性を理解し、適切な用途に活用することが重要です。
用途に応じた素材の選定
A5052とA1070というアルミニウム合金には、耐食性や加工性などの特性の違いがあります。A5052は耐食性に優れ、海洋環境など厳しい条件下でも優れた性能を発揮します。一方、A1070は加工性が高く、曲げや成形などの加工がしやすい特長があります。例えば、船舶や海水中で使用される部品にはA5052が適しており、建築や家電製品などの加工が必要な場面ではA1070が適しています。適切な素材を選択することで製品の性能や品質を向上させることができます。したがって、使用する環境や必要な加工性能に応じて、A5052とA1070の特性を理解し、適切に選定することが重要です。
耐久性とコストパフォーマンスの考慮
A5052とA1070は、金属素材として使われることがありますが、その中でも特に耐食性と加工性の違いが注目されています。A5052は耐食性に優れており、主に船舶や食品加工機器などの耐久性が求められる用途に使用されます。一方、A1070は加工性が高く、主に食器や包装材などの加工がしやすい素材として利用されています。
例えば、A5052は海洋環境下での使用に適しており、錆びにくい性質があります。一方、A1070は軽量かつ加工しやすいため、容器やカバーなどの製造に適しています。それぞれの特性を理解することで、適切な素材を選択する際に役立ちます。耐久性と加工性のバランスを考慮することで、製品の品質やコストパフォーマンスを向上させることができます。
チェックリスト: あなたに最適なアルミ合金は?
A5052とA1070、耐食性と加工性の違いとは?A5052とA1070は、ともにアルミニウム合金ですが、それぞれ異なる特性を持っています。まず、A5052は耐食性に優れており、海水などの腐食環境にも強い特徴があります。一方、A1070は加工性に優れており、曲げ加工や溶接などがしやすいという特性があります。例えば、船舶の部品や車両のボディパネルなどにはA5052が使用されることが一般的です。一方、電気製品のケーシングや包装材など、加工性が重視される場合にはA1070が選ばれることがあります。このように、用途や環境に応じて適したアルミニウム合金を選ぶことが重要です。
まとめ
「素材の達人」では、A5052とA1070の比較を行います。これらの素材はそれぞれ異なる特性を持っており、特に耐食性と加工性において大きな違いがあります。A5052は耐食性が高く、加工性も良好です。一方、A1070は耐食性はやや劣るものの、加工性に優れています。どちらの素材を使用するかは、使用環境や加工方法に合わせて検討する必要があります。
アルミニウム加工に最適!油圧チャックを使った旋盤の選び方
最近、アルミニウム加工に興味を持っているけれど、どのような旋盤が最適なのかお悩みではありませんか?アルミニウムは軽量で耐食性に優れた素材であり、その加工には適切な機器が必要です。特に油圧チャックを使用した旋盤は効率的で正確な加工を実現するため、選び方を知ることが重要です。この記事では、アルミニウム加工における旋盤と油圧チャックの選び方を解説します。加工技術の向上に役立つ情報を提供するので、ぜひご参考にしてください!
Contents
アルミニウム旋盤加工の基本
アルミニウム加工の特徴と利点
アルミニウム加工の特徴と利点
アルミニウムは軽くて丈夫で、熱や電気をよく伝導する性質があります。そのため、自動車や航空機、建築など幅広い産業で利用されています。アルミニウムを旋盤加工する際に重要なのが油圧チャックの選び方です。
油圧チャックは固定具として使用され、作業効率を高める役割を果たします。例えば、高精度加工や大型のアルミニウム部品を安定して加工する際に重要です。工具のしっかり固定ができるため、作業中の安全性も向上します。
したがって、アルミニウムを加工する際には適切な油圧チャックを選ぶことが重要です。適切なチャックを使用することで、効率的で安全な加工作業が可能となり、製品の品質向上にもつながります。
NC旋盤とは:基礎知識
アルミニウム加工に最適な旋盤を選ぶ際には、油圧チャックの利用が重要です。油圧チャックは加工物をしっかり固定できるので、精度の高い加工が可能です。例えば、アルミニウムは軽くて加工しやすい素材ですが、加工時に振動が生じやすいため、しっかり固定することが必要です。油圧チャックを使用することで、安定した加工を行うことができます。
さらに、油圧チャックは取り扱いが比較的簡単で効率的です。操作が容易なため、作業効率が向上し、生産性が高まります。アルミニウムなどの軽金属を加工する際には、油圧チャックを備えた旋盤を選ぶことで、効果的な加工作業が可能となります。
旋盤加工の基本的な工程
アルミニウム加工において重要な役割を果たす旋盤には、油圧チャックを使用することが最適です。油圧チャックは安定した保持力と精密な加工を可能にします。例えば、アルミニウムのような軟らかい金属を加工する際に、油圧チャックが安定した保持力を提供し、作業効率を向上させます。このように、油圧チャックを使った旋盤は、加工精度や安全性を高めることができます。適切な油圧チャックを選ぶことで、アルミニウム加工の品質を向上させることができます。したがって、アルミニウム加工においては、油圧チャックを選ぶことが重要です。
アルミニウム加工に適した旋盤の選び方
アルミニウム加工に適した旋盤を選ぶ際には、油圧チャックの利用が重要です。アルミニウムは加工中に振動しやすい素材であり、油圧チャックは強力な保持力を持つため、加工精度を高めることができます。具体的には、アルミニウムの旋盤加工では、油圧チャックがしっかりと素材を保持し、振動を防止することで、仕上がりの品質が向上します。
例えば、油圧チャックを使用せずにアルミニウムを加工すると、加工中に素材がズレる可能性が高くなり、精度の低下や加工品質の悪化が起こります。しかし、油圧チャックを適切に活用することで、このような問題を解決し、効率的かつ精密な加工を実現することができます。そのため、アルミニウム加工を行う際には、油圧チャックを使用した旋盤の選択が重要です。
NC旋盤での油圧チャックの選び方
油圧チャックとは:概要と機能
アルミニウム加工を行う際に重要な役割を果たす油圧チャック。この記事では、油圧チャックの概要と機能について解説していきます。
油圧チャックは、旋盤作業においてアルミニウム材料をしっかりと固定するための装置です。アルミニウムは柔らかい材料であり、正確な加工を行うためには安定した固定が必要不可欠です。
例えば、アルミニウム製の部品を加工する際、油圧チャックを使用することで作業効率が向上し、加工精度も高まります。また、油圧チャックは変則形状の部品でもしっかりと固定することができるため、幅広い用途に対応できるのも特長です。
アルミニウム加工において油圧チャックを選ぶ際には、作業の安全性や効率性、加工精度などを考慮して適切なものを選ぶことが重要です。適切な油圧チャックの選定により、アルミニウム加工の品質向上につながることが期待されます。
油圧チャックの種類と特性
アルミニウム加工に最適な旋盤を選ぶ際に重要なのが、油圧チャックの種類や特性を理解することです。油圧チャックは、アルミニウムのような柔らかい素材をしっかり固定するために使用されます。
油圧チャックには、2つの主要な種類があります。一つはデッドセンタータイプで、もう一つはパワーチャックタイプです。デッドセンタータイプは精度が高く、小さな部品を加工する際に適しています。一方、パワーチャックタイプは高い保持力を持ち、大きな部品を加工する際に適しています。
例えば、アルミニウム製の自動車部品を旋盤加工する場合、パワーチャックタイプの油圧チャックが適しています。これにより、部品が確実に固定され、精密な加工が可能となります。アルミニウム加工を効率的かつ正確に行うためには、適切な油圧チャックを選択することが重要です。
アルミニウム加工に最適な油圧チャックの選定基準
アルミニウム加工に最適な油圧チャックを選ぶ際の基準について考えてみましょう。アルミニウムは加工が繊細なため、適切な油圧チャックを選ぶことが重要です。まず、旋盤の安定性が求められます。油圧チャックはしっかりとアルミニウムを保持し、振動やぶれを最小限に抑える役割を果たします。そのため、高品質で信頼性のある油圧チャックを選ぶことが重要です。
さらに、加工精度も考慮すべき要素です。油圧チャックの精度が高ければ、アルミニウムの加工品質も向上します。たとえば、緻密な部品加工や微細加工にも対応できる油圧チャックが適しています。
つまり、アルミニウム加工においては、安定性と精度を重視した油圧チャックを選ぶことが鍵となります。適切な油圧チャックを選ぶことで、効率的で品質の高い加工作業を行うことができるでしょう。
NC旋盤と油圧チャックの互換性
アルミニウム加工において、油圧チャックを使用した旋盤が最適です。なぜなら、アルミニウムは軽くて加工しやすいため、油圧チャックを使うことで安定した加工が可能となります。例えば、複雑な形状のアルミニウムパーツを精密に加工する際に油圧チャックが重宝されます。油圧チャックは加工物を確実に固定し、回転精度を高めることで、品質の向上につながります。したがって、アルミニウム加工を行う際には、油圧チャックを備えた旋盤を選ぶことが重要です。油圧チャックとNC旋盤の互換性は、高品質なアルミニウム加工を実現するために不可欠です。
旋盤加工におけるチャックの隙間の重要性
チャックの隙間とは
アルミニウム加工に最適な油圧チャックを使用するためには、旋盤の選び方が重要です。油圧チャックは、アルミニウムのような軟らかい素材をしっかりと固定するのに適しています。例えば、アルミニウムの場合、硬い素材よりも切削時に振動しやすいため、しっかりと固定できる油圧チャックが重要です。このような理由から、油圧チャックを使用する際には、旋盤の性能や機能に注意する必要があります。適切な旋盤を選ぶことで、アルミニウム加工がより効率的に行え、高品質な製品を生産することができます。油圧チャックを使用した旋盤の選択は、加工精度や作業効率向上につながる重要なポイントと言えるでしょう。
隙間が加工精度に及ぼす影響
アルミニウム加工において、旋盤を選ぶ際に重要なポイントの一つが油圧チャックの使用です。油圧チャックは、アルミニウムのような軽量で柔らかい素材をしっかりと保持するのに適しています。その理由は、油圧チャックが均一な圧力を加えることができ、加工精度への影響が少ないからです。
具体的な例を挙げると、アルミニウムパーツの精密加工を行う際に、油圧チャックを使用することで加工中の振動やズレを抑えることができます。これにより、仕上がりの品質を向上させることができます。
したがって、アルミニウム加工においては、油圧チャックを使用した旋盤を選ぶことで加工精度を向上させることができます。油圧チャックの適切な使用は、アルミニウム加工における効率性と品質向上に繋がる重要な要素です。
アルミニウム加工での隙間管理方法
アルミニウム加工において、旋盤を選ぶ際に重要なポイントは油圧チャックの利用です。アルミニウムは加工中に熱を発生しやすく、これによって加工精度が損なわれる可能性があります。油圧チャックはその熱を効果的に吸収し、加工中のアルミニウムの変形を最小限に抑えることができます。
例えば、アルミニウムを使った部品加工では、油圧チャックを使用することで加工精度が向上し、作業効率もアップします。特に細かい加工や高精度加工を要求される場合には、油圧チャックを採用することで品質の向上が期待できます。
そのため、アルミニウム加工においては、油圧チャックを利用した旋盤を選ぶことが重要です。加工精度や効率を向上させ、良質な部品加工を実現するために、油圧チャックの適切な選択が欠かせません。
旋盤チャックの選定方法
チャック選定の基準
アルミニウム加工に最適な旋盤を選ぶ際の重要な基準は、油圧チャックの利用が挙げられます。油圧チャックは、加工中に安定した保持力を提供し、精密な加工作業を可能にします。例えば、アルミニウムは加工中に振動しやすい材料であり、油圧チャックを使用することでしっかりと固定することができます。
油圧チャックを選定する際には、耐久性や精度、保持力などの特性を注視する必要があります。また、適切なサイズや形状のチャックを選ぶことも重要です。これらの基準に基づいて、アルミニウム加工に最適な油圧チャックを選定することで、効率的かつ正確な加工作業を実現できます。
アルミニウム加工への適合性
アルミニウム加工を行う際に重要なのは、油圧チャックを使った旋盤の選び方です。アルミニウムは軽量で加工しやすい特性を持ち、さまざまな産業で広く使用されています。油圧チャックは、アルミニウムのような柔らかい素材をしっかり固定するのに適しており、精密な加工を可能にします。
具体的な例を挙げると、自動車産業ではエンジン部品やボディパーツなどにアルミニウムが使われており、高精度な加工が求められています。油圧チャックを使用した旋盤は、これらの部品の加工に適しており、効率的で確実な生産を実現します。
したがって、アルミニウム加工を行う際には、油圧チャックを使用した旋盤を選ぶことが重要です。適切な機械を選択することで、高品質なアルミニウム製品を効率的に製造することができます。
チャックのメンテナンスと寿命
ア ル ミ ニ ウ ム 加工において重要なのは、油圧チャックを使用した旋盤の選び方です。アルミニウムは軽くて強度があり、加工性も良いため、様々な産業で使用されています。油圧チャックはアルミニウムのような軟らかい素材をしっかり固定するために理想的です。
旋盤を選ぶ際には、まずは油圧チャックがサポートされているかどうかを確認しましょう。油圧チャックを使用することで、加工中の振動やズレを最小限に抑えることができます。例えば、精密な加工が必要な場合や大量生産を行う場合には特に重要です。
油圧チャックを使用した旋盤は、効率的にアルミニウム加工を行う上で非常に役立ちます。適切な旋盤を選ぶことで、品質や生産性を向上させることができます。
旋盤加工における生爪の使い方
生爪とは:目的と機能
アルミニウム加工に最適!油圧チャックを使った旋盤の選び方
アルミニウムを加工する際には、油圧チャックを使った旋盤が最適です。このような選択をする理由は、アルミニウムの特性に合わせて正確かつ効率的に加工を行うためです。油圧チャックはしっかりと工件を保持し、高速回転時でも安定した加工を実現します。
例えば、自動車部品や航空機部品など、精密なアルミニウム加工が求められる産業分野で油圧チャックを使用することで、高品質な製品を生産することが可能となります。そのため、アルミニウム加工を行う際には、油圧チャックを使った旋盤を選ぶことで、生産性向上や加工精度の向上につながることが期待されます。
生爪の種類と特徴
アルミニウム加工において重要な役割を果たす旋盤で、油圧チャックの選び方について考えてみましょう。アルミニウムは軽くて丈夫な素材であり、加工時には適切な固定が必要です。そこで、油圧チャックが活躍します。油圧チャックは、精度の高い加工が可能であり、安定した固定力が特徴です。
油圧チャックの選び方には、加工するアルミニウムのサイズや形状に合った適切なサイズを選ぶことが重要です。また、耐久性や保守性も考慮すべきポイントです。例えば、小型のアルミニウムを加工する場合は、小型で使いやすい油圧チャックが適しています。
アルミニウム加工において、油圧チャックの選び方を慎重に検討することで、効率的かつ正確な加工作業が可能となります。適切な油圧チャックを選ぶことで、高品質な加工製品を実現しましょう。
アルミニウム加工での生爪の選び方
アルミニウム加工において、旋盤で生爪を使う際には、油圧チャックが最適です。油圧チャックは強力で安定した保持力を持ちながらも取り外しが容易で、作業効率を高めることができます。例えば、アルミニウムは軽くて加工しやすい素材ですが、扱いが難しいこともあります。そこで、油圧チャックを使用することで、安定した固定が可能となり、作業中に加工精度を保つことができます。また、油圧チャックは振動や衝撃にも強く、長時間の加工作業にも適しています。そのため、アルミニウム加工においては、油圧チャックを使用することで安全かつ効率的な加工が可能となります。
生爪の取り付けと調整方法
アルミニウム加工に最適な旋盤を選ぶ際に重要なポイントは、油圧チャックの利用です。アルミニウムは加工時に振動が発生しやすい素材であるため、安定した固定が必要です。油圧チャックはその点で非常に効果的であり、精度の高い加工を可能にします。
例えば、アルミニウムの円柱を旋盤で加工する場合、油圧チャックを使用することでしっかりと固定し、正確な加工が可能となります。油圧チャックは圧力を加えることで確実に素材を掴み、安定性を提供します。
したがって、アルミニウム加工においては、油圧チャックを使用した旋盤が最適な選択肢と言えます。素材の特性を考慮し、精密な加工を実現するために、適切な機材を選定することが重要です。
油圧チャックを活用したアルミニウム旋盤加工のコツ
正確なチャックの取り付け方
アルミニウム加工において、油圧チャックを使った旋盤の選び方は重要です。油圧チャックはアルミニウムなどの素材をしっかりと固定し、精密な加工を可能にします。そのため、適切な旋盤を選ぶことが生産性や加工精度向上につながります。
まず、旋盤の選択にあたっては、加工するアルミニウムのサイズや形状、必要な加工精度などの要件を明確に把握することが重要です。また、使用する油圧チャックのサイズやタイプにも注目しましょう。例えば、小さな部品を加工する場合は小型の油圧チャックが適しています。
さらに、耐久性や安全性を考慮して、信頼性の高いメーカーから製品を選ぶことも大切です。適切な油圧チャックと旋盤を組み合わせることで、効率的なアルミニウム加工が可能となります。適切な選択を行い、生産性向上につなげましょう。
加工精度を高めるチャックの使用法
アルミニウム加工において、旋盤を選ぶ際に重要な要素の一つが油圧チャックの使用法です。油圧チャックは、アルミニウムなどの素材をしっかりと保持し、安定した加工を可能にします。
油圧チャックの特徴は、その強力な保持力にあります。例えば、複雑な形状や細かい加工が必要な部品でも、油圧チャックを使用すれば安定した加工が行えます。
また、油圧チャックは素早く簡単に取り付けることができるため、生産性の向上にも貢献します。これにより、効率的な生産が可能となります。
したがって、アルミニウム加工においては、油圧チャックを使用した旋盤を選ぶことで、加工精度を高めることができます。油圧チャックの効果を活かし、より品質の高い製品を生産するために、適切な旋盤の選択が肝要です。
長時間加工におけるチャックの管理
アルミニウム加工において、油圧チャックを使用する際の旋盤の選び方についてお伝えします。アルミニウムは軽くて耐食性に優れた材料であり、加工時に適切な工具や設備が必要です。油圧チャックは、アルミニウムのような軟らかい金属をしっかり固定するのに適しています。
まず、油圧チャックを使用する旋盤を選ぶ際には、長時間の加工でも安定した状態を保つことが重要です。油圧チャックはしっかりとした保持力を持ち、加工中に位置がズレにくい特徴があります。例えば、複数のアルミニウム部品を一度に加工する場合でも、油圧チャックを使用することで効率的に作業を進めることができます。
このように、油圧チャックを使用した旋盤を選ぶことで、アルミニウム加工作業をスムーズに行うことができます。適切な機械を選ぶことで、生産性の向上や品質の向上につながることを覚えておきましょう。
よくある問題と対処法
アルミニウム加工に最適な旋盤を選ぶ際、油圧チャックの利用は重要です。アルミニウムは加工が難しい素材の一つであり、油圧チャックを使用することで安定した固定が可能となります。具体的には、油圧チャックは均一な圧力で素材をしっかり固定し、振動や歪みを最小限に抑えます。このような安定した加工状態は、精度の高い仕上がりを実現し、作業効率も向上させます。さらに、アルミニウムのような軟らかい素材を扱う際には、油圧チャックが素材を傷つけることなく確実に加工を行うことができます。したがって、アルミニウム加工においては、油圧チャックを使用した旋盤の選択が重要と言えます。
まとめ
アルミニウム加工に最適な旋盤の選び方を考える際には、油圧チャックの使用が重要になります。アルミニウムは柔らかい金属であるため、適切な固定が必要です。油圧チャックは、しっかりとアルミニウムを保持することができるため、加工精度を高めることができます。また、安定した加工作業が可能となり、効率的な生産が期待できます。適切な油圧チャックを使用することで、アルミニウム加工の作業効率を向上させることができます。
アルミニウム合金A5052とA3003の特性を徹底比較!どっちが適してる?
アルミニウム合金A5052とA3003、どちらがあなたのニーズに適しているのか気になりませんか? 両者の特性を徹底的に比較してみましょう。アルミニウム合金は様々な用途に使用され、それぞれの特性を理解することは重要です。この記事では、A5052とA3003の比較を通じて、どちらがどのような状況に適しているのかを明らかにします。製品選びの際に役立つ情報が満載ですので、ぜひご覧ください!
Contents
アルミニウム合金の基礎知識
アルミニウム合金とは
アルミニウム合金とは、アルミニウムに他の金属を加えて作られる合金のことです。この合金は、通常のアルミニウムよりも強度や耐食性が向上しています。A5052とA3003は日常生活や産業でよく使用されるアルミニウム合金の代表例です。A5052は耐塩水性に優れ、船舶や食品加工業界で使用されることが多い一方、A3003は溶接性が良く、屋根や外壁など建築材料として広く利用されています。
これらの合金の特性を比較すると、用途によって適した合金が異なります。例えば、海洋環境において耐食性が求められる場合はA5052が適していますが、建築材料として使用する際はA3003の方が適しています。要するに、使い方や環境によって最適な合金が異なることを覚えておくと良いでしょう。
アルミニウム合金の一般的な用途
アルミニウム合金は、軽量で強度があり、耐食性にも優れているため、広く様々な分野で使用されています。特に、日本では建築、自動車、航空宇宙、電子機器など幅広い用途において重要な材料として利用されています。
アルミニウム合金A5052とA3003を比較すると、A5052は耐食性に優れ、塩水や海洋環境にも適しています。一方、A3003は加工性に優れており、容易に成形加工ができる特性があります。
例えば、A5052は船舶の外板や車両のボディパネルなど、耐食性が必要な部品に使用されます。一方、A3003は食品容器や電子部品など、加工性が重要な製品に適しています。
したがって、用途や要件に合わせて適切なアルミニウム合金を選択することが重要です。
アルミニウム合金の分類と特性
アルミニウム合金は、様々な種類がありますが、今回はA5052とA3003の特性を比較してみましょう。A5052は、耐食性に優れ、加工性が高い特徴を持っています。一方、A3003は、溶接性に優れ、塑性加工がしやすい特性があります。例えば、A5052は船舶や飛行機の部品、A3003は調理器具や建築材料によく使用されます。
それぞれの特性を考えると、使用する目的や環境によってどちらが適しているかが異なります。例えば、耐食性が必要な場合はA5052、溶接性や塑性加工性が重要な場合はA3003が適しています。適切な合金の選択は製品の品質や性能にも影響を与えるため、しっかりと比較検討することが重要です。
A5052とA3003の特性
A5052の化学成分と物理的特性
アルミニウム合金A5052とA3003を比較すると、A5052はマグネシウムを含んでおり、耐食性や強度が高く、溶接性も優れています。一方、A3003はマンガンが含まれており、加工性に優れていますが、A5052ほどの強度や耐食性はありません。
例えば、A5052は船舶や車両の部品、圧力容器などの製造に使用されています。一方、A3003は調理器具や建築材料などに広く利用されています。
そのため、用途によって選択すべき合金が異なります。耐食性や強度を求める場合はA5052が適していますが、加工性が重要な場合はA3003を選ぶのが良いでしょう。どちらの合金も特性を理解し、適切に選択することが重要です。
A5052とA3003の特性を徹底比較!どっちが適してる?
アルミニウム合金A5052とA3003は、異なる特性を持っています。例えば、A5052はマグネシウムとクロムを含んでおり、耐食性や強度に優れています。一方、A3003はマンガンを主成分としており、加工性や溶接性に優れています。これらの特性を比較することで、用途に応じてどちらが適しているかを選択できます。
例えば、A5052は海水や塩害に強いため、船舶や海洋関連の部品に適しています。一方、A3003は腐食に強いため、建築や食品加工など幅広い分野で使用されています。どちらの特性も重要であり、使用する目的や環境に合わせて適切な合金を選択することが重要です。
A5052とA3003の比較
アルミニウム合金A5052とA3003は、どちらがより適しているのでしょうか?A5052は強度が高く、耐食性に優れています。一方、A3003は加工性に優れ、溶接や曲げ加工に向いています。例えば、航空機の部品や自動車のボディパネルにはA5052が使用されることが一般的です。一方、A3003は圧力容器や調理器具などに良く使われます。
要するに、使用する用途や要件に応じて、どちらの合金が適しているかが異なります。A5052は強度と耐食性が重要な場面で、A3003は加工性が重要な場面で活躍します。適切な選択を行うためには、それぞれの特性を理解し、目的に合った合金を選定することが重要です。
アルミニウム合金A5052の利点と欠点
A5052の利点
A5052の利点
アルミニウム合金A5052は、優れた耐食性や溶接性、加工性を持ち、軽量でありながら強度も必要とされる場面で活躍します。海水や塩分の影響を受ける環境にも適しており、船舶の建造や車両部品などに広く使用されています。また、航空宇宙産業でも重要な材料として利用されています。A5052は、高い耐食性と強度を兼ね備えた信頼性の高い素材であり、幅広い産業で重要な役割を果たしています。これらの特性から、A5052はさまざまな分野で幅広い用途に適していると言えます。
A5052の欠点
アルミニウム合金A5052とA3003の特性を比較してみましょう。A5052は強度が高く、耐食性に優れていますが、溶接性がやや劣る欠点があります。一方、A3003は加工がしやすく、溶接もしやすいのが特徴です。たとえば、A5052は船舶や航空機の部品、A3003は調理器具や食品容器によく使用されます。しかし、使用目的や環境によって適した合金は異なります。A5052は強度が必要な場面に、A3003は加工性が重要な場面に適しています。つまり、どちらが適しているかは使用する状況によって異なります。ご自身のニーズに合わせて適切な合金を選択することが大切です。
A5052の適切な用途
アルミニウム合金A5052とA3003を比較する際には、それぞれの特性を把握することが重要です。A5052は耐食性や機械加工性に優れており、船舶や車両の部品などに広く使用されています。一方、A3003は加工性に優れており、圧力容器や調理器具などに適しています。このように、用途に合わせて選択することが重要です。
例えば、A5052は海洋環境下での使用に適しており、塩害に強い特性を持っています。これに対してA3003は食品加工業界で広く利用されており、食品との相性が良いと言えます。両合金の特性を理解することで、最適な用途に適した材料を選択することができます。合金の特性をしっかり把握して、使用する場面に応じて適切に選択しましょう。
アルミニウム合金A3003の利点と欠点
A3003の利点
アルミニウム合金A3003には、さまざまな利点があります。まず、A3003は耐食性に優れており、錆びにくい特性があります。このことから、屋外で使用される製品や建築材料に好適です。さらに、A3003は加工が容易であり、加工性に優れています。そのため、製品の形状を細かく変える必要がある場合や複雑な形状に加工する際に適しています。例えば、キッチン用具や装飾品など幅広い製品に利用されています。これらの利点から、A3003は多くの産業分野で重宝されています。
A3003の欠点
アルミニウム合金A5052とA3003の特性を徹底比較!どっちが適してる?
A5052とA3003はどちらも一般的に使われるアルミニウム合金ですが、それぞれの特性を比較すると、使いどころが異なります。A3003の欠点は、[ここにA3003の欠点について具体的に記載します]。一方、A5052は[ここにA5052の利点について詳しく述べます]。例えば、[具体的な例を挙げます]。これによって、どちらがどのような状況で適しているかが明確になります。最終的には、使用目的や条件によって選択肢が異なるため、自分のニーズに合ったアルミニウム合金を選ぶことが重要です。
A3003の適切な用途
アルミニウム合金A5052とA3003を比較するとき、それぞれの特性を理解することが重要です。A5052は耐久性が高く、海水にも耐性があります。一方、A3003は加工性が優れており、溶接や曲げ加工に適しています。例えば、A5052は船舶の部品や液晶テレビのケースなどに使用される一方、A3003は調理器具や食品包装などに利用されています。用途によって適した材質が異なるため、プロジェクトや製品の要件に合わせて選択することが大切です。総じて言えることは、A5052は強度が必要な場面で適しており、一方でA3003は加工性が求められる場面で適しています。自身の目的に合った特性を持つ合金を選択することで、より効果的な使用が可能となります。
アルミニウム合金の選択基準
材料選定における考慮事項
アルミニウム合金の材料選定において、A5052とA3003の特性を比較することは重要です。A5052は強度と耐食性に優れており、主に船舶や飛行機などの産業分野で使用されます。一方、A3003は加工性に優れており、食品容器や建築材料などに広く利用されています。例えば、A5052は海水や塩分の多い環境で使用され、腐食に強い性質が求められます。一方で、A3003は折り曲げやプレス加工が容易なため、製品の形状変更が頻繁に行われる場合に適しています。材料の選定は使用用途に合わせて行うことが重要であり、それぞれの特性を検討することで最適な選択が可能となります。
A5052とA3003の用途に基づく選択
アルミニウム合金A5052とA3003はどちらも優れた特性を持っていますが、用途によって適しているものが異なります。まず、A5052は耐食性が高く、海水や塩水環境において優れた性能を発揮します。このため、船舶や海洋関連の部品によく使用されています。一方、A3003は加工性が優れており、曲げ加工やプレス加工に向いています。そのため、板金加工や製缶業界で広く使用されています。
例えば、A5052は海水での腐食に強いため、船舶の船体やデッキ部分に使用されます。一方、A3003は加工性が良いため、食品容器や工業製品の製造に適しています。用途に応じて適切な合金を選択することが重要です。
コストと性能のバランス
アルミニウム合金A5052とA3003を比較すると、どちらが適しているかを考えてみましょう。まず、A5052は耐食性や加工性に優れています。これは海水などの腐食に強く、船舶や飛行機の部品によく使われています。一方、A3003は溶接性や曲げ加工性に優れており、食品容器や建材に利用されています。例えば、A5052は船舶の甲板や航空機の胴体に使用され、A3003は調理用具や屋根材などに使われています。このように、使用する用途によってどちらの合金が適しているかが変わってきます。したがって、ユーザーのニーズや使用環境に合わせて適切な合金を選ぶことが重要です。
アルミニウム合金の加工方法
アルミニウム合金の一般的な加工技術
アルミニウム合金A5052とA3003の特性を徹底比較!どっちが適してる?
アルミニウム合金A5052とA3003は、どちらも優れた特性を持っていますが、それぞれの適応範囲や強度に違いがあります。まず、A5052は耐食性に優れており、海水や塩分の影響を受けにくい特長があります。一方、A3003は加工性に優れており、曲げや成形が容易です。
例えば、建築材料としてA5052は外壁や屋根などで使用されることが多いです。一方、A3003は食品容器や包装材などによく用いられます。どちらの合金も自動車部品や航空機部品としても利用されていますが、使用する環境や要求される条件によって適した合金を選択することが重要です。
要するに、A5052とA3003はそれぞれの特性を生かして様々な分野で活躍しています。状況や用途に応じて適切な合金を選ぶことが大切です。
A5052の加工方法
A5052とA3003のアルミニウム合金を比較すると、A5052は耐食性に優れ、A3003は曲げ加工に適しています。A5052は船舶や車両の部品、A3003は調理器具や鍋などに使用されます。A5052は強度が高く、耐食性があるため、海洋環境や屋外での利用に適しています。一方、A3003は柔軟性に富んでおり、曲げや深絞り加工に向いています。どちらの特性を活かすかによって、最適な用途が決まります。例えば、A5052は耐食性が必要な場面で優れた性能を発揮し、A3003は曲げ加工が必要な製品に適しています。したがって、使用目的や要件に応じて適切な合金を選択することが重要です。
A3003の加工方法
アルミニウム合金A5052とA3003の特性を徹底比較!どっちが適してる?
アルミニウム合金A5052とA3003を比較する際に注目すべき点は何でしょうか。まず、A5052は耐食性が高く、海水などの腐食環境に適しています。一方、A3003は加工性に優れ、曲げ加工や深絞り加工に向いています。
具体例として、A5052は船舶の船体や飛行機の部品など、耐食性が必要な部分に使用されます。一方、A3003は圧力容器や調理器具など、加工性が重要な製品に利用されています。
総括すると、どちらの合金が適しているかは使用する用途によります。耐食性が必要な場合はA5052を選び、加工性が優先される場合はA3003が適しています。適切な合金を選択することで、製品の品質と効率を向上させることができます。
加工方法による材料特性への影響
アルミニウム合金A5052とA3003の特性を徹底比較!どっちが適してる?アルミニウム合金A5052とA3003は両方とも優れた特性を持ちますが、それぞれ異なる用途に向いています。A5052は耐食性に優れ、海水などの腐食環境下での使用に適しています。一方、A3003は溶接性が高く、加工性に優れています。例えば、A5052は船舶や海洋構造物、A3003は食品容器や建築用材料などに適しています。用途や環境に合わせて適切な合金を選択することが重要です。これらの特性を考慮して、製品の耐久性や効率性を向上させるために、正しい合金を選択することが必要です。
A5052とA3003の選択ガイド
各合金の適切な加工方法と用途のマッチング
アルミニウム合金A5052とA3003は、それぞれ異なる特性を持っています。A5052は耐食性が高く、海洋環境にも適していますが、一方でA3003は高い溶接性を持ち、加工しやすい特性があります。
例えば、A5052は船舶や航空機の部品、車両のボディパネルなど、耐食性が求められる場面で活躍します。一方、A3003は圧力容器や一般的な食器、調理器具などの製造に適しています。
それぞれの合金は異なる用途に向いており、加工方法や使用環境に合わせて適切な選択が重要です。このように、A5052とA3003の特性を理解し、適切な用途に活用することで、効率的な加工や製品の耐久性向上が図れるでしょう。
どちらのアルミニウム合金が適しているかの判断基準
アルミニウム合金A5052とA3003の特性を比較する際に、適しているかどうかを判断するための基準があります。まず、強度や耐食性、加工性などの特性を考慮します。A5052は強度が高く、耐食性も優れています。一方、A3003は加工性に優れており、容易に成形できます。次に、使用目的に合わせて選択することが重要です。例えば、船舶や航空機などの耐久性が求められる場面ではA5052が適しています。一方、食品容器や建築材料などの加工性が重要な場合には、A3003が適しています。したがって、どちらの合金が適しているかは、使用する環境や要件によって異なります。そのため、適切な合金を選択するためには、使用目的や必要な特性をよく考慮することが重要です。
最終製品に求められる特性と合金選択
アルミニウム合金A5052とA3003を比較する際に、最終製品に求められる特性を考えることが重要です。A5052は耐食性が高く、海洋環境などの厳しい条件下でも優れた性能を発揮します。一方、A3003は加工性に優れ、曲げや成形が比較的容易です。例えば、A5052は船舶や車両の外装パーツに適しており、A3003は食品容器や家庭用品などの加工に適しています。製品の使用目的や環境に応じて、どちらの特性がより適しているかを考慮することが重要です。このように、A5052とA3003の特性を比較し、製品の要件に適した合金を選択することが製造業における重要な判断基準となります。
まとめ
アルミニウム合金A5052とA3003は、それぞれ異なる特性を持っています。これらの特性を比較することで、どちらが特定の用途に適しているかが明確になります。この比較を通じて、どの合金が最も適しているかを見極めることが重要です。特性や特性に基づいて、それぞれの利点や欠点を理解し、適切に利用することが重要です。
油圧チャックのメリットとアルミニウム旋盤加工のポイント
お待たせしました。本日のテーマは「油圧チャックのメリットとアルミニウム旋盤加工のポイント」です。皆さんはアルミニウムの旋盤加工を行ったことがありますか?そして、その際に油圧チャックを使用した経験はいかがでしょうか。
アルミニウムは軽くて加工しやすい素材として知られていますが、その加工方法には様々なポイントが存在します。特に、油圧チャックの利点を活かすことで、より効率的かつ正確な加工が可能となります。
本記事では、油圧チャックのメリットやアルミニウム旋盤加工のポイントについて網羅的にご紹介します。アルミニウム加工における新たな視点や技術を学びたい方、また油圧チャックを活用してより高度な加工を目指す方にとって、貴重な情報となることでしょう。
それでは、早速油圧チャックの魅力とアルミニウム旋盤加工のポイントについて、深堀りしていきましょう。楽しい学びと新たな発見が待っています。
Contents
アルミニウム旋盤加工における基本
旋盤加工の概要
油圧チャックは、アルミニウム旋盤加工において重要な役割を果たします。油圧チャックのメリットは、作業効率を向上させることにあります。例えば、油圧チャックを使用することで、作業者は素早く工作物を固定し、高精度で加工を行うことができます。これにより、生産性が向上し、作業時間が短縮されます。さらに、油圧チャックは安定性が高く、加工中に工作物がズレることを防ぎます。
アルミニウム旋盤加工において、油圧チャックを効果的に活用するポイントは、適切なチャックの選択と適切な設定です。適切なチャックを選ぶことで、加工精度を向上させることができます。また、適切な設定を行うことで、安全性を確保しつつ効率的な加工が可能となります。油圧チャックを正しく活用することで、アルミニウム旋盤加工の品質と効率を向上させることができます。
アルミニウムの物性と加工の利点
アルミニウムは軽量で耐食性に優れ、熱伝導性も高いため、様々な産業で広く使用されています。これらの物性に加え、アルミニウムの旋盤加工には油圧チャックを使用することで効率的かつ精密な加工が可能です。油圧チャックは加工時に安定した保持力を提供し、作業効率を向上させます。
例えば、自動車部品製造ではアルミニウムの旋盤加工に油圧チャックが欠かせません。このシステムを使用することで、加工品質が向上し、生産性が向上します。また、精密な部品加工や複雑な形状への対応も可能となります。
アルミニウムの物性と油圧チャックを組み合わせることで、製品の品質向上や加工効率化が可能となります。これらのポイントを抑えることで、産業界での競争力を高めることができるでしょう。
旋盤加工の基礎知識
油圧チャックのメリットとアルミニウム旋盤加工のポイントについてご説明します。油圧チャックは工作物を確実に固定し、高い精度で加工することができる優れた装置です。このチャックを使用することで作業効率が向上し、品質の向上にもつながります。
アルミニウム旋盤加工では、素材特性を理解し、適切な切削条件を設定することが重要です。アルミニウムは軽量で加工しやすい素材ですが、刃物の選定や切削速度などのパラメーターを適切に調整することで、より高い加工精度を実現できます。
例えば、アルミニウムの旋盤加工において、適切な刃物と切削速度を選定することで、スムーズな加工が可能となります。油圧チャックを使用することで、作業効率が向上し、加工精度も向上します。このように、油圧チャックと適切な加工条件を組み合わせることで、アルミニウム旋盤加工を効果的に行うことができます。
汎用旋盤の選定ポイント
油圧チャックはアルミニウム旋盤加工において重要な役割を果たします。油圧チャックのメリットは、高い保持力と安定性が挙げられます。これにより、加工中に素材がズレることなく精密な加工が可能となります。例えば、アルミニウムの旋盤加工において、油圧チャックを使用することで、加工対象のアルミニウムが確実に固定され、高精度な加工が実現できます。したがって、油圧チャックは加工効率を向上させるだけでなく、品質を確保する点でも重要です。アルミニウムの旋盤加工においては、油圧チャックを適切に選定することがポイントとなります。そのため、油圧チャックのメリットを理解し、正しく活用することが重要です。
汎用旋盤の選定ポイントと注意点
汎用旋盤とは
油圧チャックのメリットとアルミニウム旋盤加工のポイント
油圧チャックは、工作機械の精密加工において重要な役割を果たします。そのメリットは、高い保持力と安定性が挙げられます。アルミニウム旋盤加工において、油圧チャックを使用することで、作業効率が向上し、加工精度も高まります。具体的なポイントとしては、アルミニウムの柔らかさや軽さを考慮して、適切な圧力と保持力を設定することが重要です。さらに、油圧チャックを正しくセッティングすることで、加工中の振動やズレを最小限に抑えることができます。これにより、アルミニウム素材の繊細な加工も安定して行うことができます。油圧チャックを効果的に活用することで、アルミニウム旋盤加工の品質向上と効率化が期待できます。
旋盤の選定ポイント
油圧チャックの利点は、加工効率の向上と加工精度の向上です。油圧チャックは、加工物をしっかり保持し、回転させることができるため、作業効率を高めることができます。例えば、アルミニウムを旋盤加工する際に、油圧チャックを使用すると、加工途中で部品がずれるリスクが低減され、より精密な加工が可能となります。
アルミニウム旋盤加工において、油圧チャックは特に重要です。アルミニウムは軽くて加工しやすい素材ですが、加工中に振動や変形が起こりやすい特性があります。そのため、油圧チャックを用いることで、しっかりと部品を保持し、安定した加工を行うことができます。
以上のように、油圧チャックはアルミニウム旋盤加工において重要なポイントとなります。加工効率や精度を向上させるために、油圧チャックの適切な選定が必要です。
旋盤の種類とその特徴
[油圧チャックのメリットとアルミニウム旋盤加工のポイント]
アルミニウムの旋盤加工において、油圧チャックは重要な役割を果たします。油圧チャックの主なメリットは、安定した保持力と素早い取り付け、取り外し可能です。これにより、作業効率が向上し、高精度な加工が可能となります。例えば、アルミニウムの旋盤加工において、油圧チャックを使用することで、精密な部品や繊細な形状を効果的に加工することができます。さらに、油圧チャックは耐久性に優れており、長期間安定した性能を維持することができます。アルミニウムの旋盤加工において、油圧チャックを選択することで、効率的かつ品質の高い加工が可能となります。
加工材料に応じた旋盤の選び方
油圧チャックは、アルミニウム旋盤加工において重要な役割を果たします。油圧チャックのメリットは、しっかりと素材を固定できることです。これにより、精密な加工作業が可能となります。例えば、アルミニウムのような軟らかい金属でも、油圧チャックがしっかりと保持することで、高い精度で加工することができます。油圧チャックは安定性が高く、作業効率を向上させます。
また、アルミニウム旋盤加工においてポイントとなるのは、素材の特性を理解し適切な切削条件を設定することです。アルミニウムは熱や切削力に敏感なため、適切な冷却や切削速度が重要です。加工精度や作業効率を高めるために、素材に合わせた最適な旋盤を選ぶことが大切です。油圧チャックを使用することで、より品質の高いアルミニウム加工が可能となります。
旋盤チャックの種類とその特長
旋盤チャックの基本
油圧チャックは、アルミニウム旋盤加工において重要な役割を果たします。油圧チャックのメリットは、しっかりと工件を固定できることです。例えば、高速回転中でも安定した加工が可能となります。さらに、精度の高い加工が期待できるので、作業効率が向上します。また、アルミニウムなどの柔らかい素材にも適しており、加工の幅が広がります。
アルミニウム旋盤加工において、油圧チャックのポイントは工件をしっかりと保持することです。このことにより、加工時の振れやズレを最小限に抑えることができ、高品質な加工が可能となります。さらに、安定した加工状態を維持できるため、作業効率が向上します。油圧チャックを適切に使用することで、アルミニウム旋盤加工の品質向上や生産性の向上が期待できます。
油圧チャックのメリット
アルミニウム旋盤加工において、油圧チャックは重要な役割を果たします。油圧チャックのメリットは、しっかりと加工物を固定し、高い精度で加工を行うことができる点です。例えば、アルミニウムの旋盤加工において、加工物がしっかりと固定されることで、加工中にズレや揺れを防ぎ、精密な加工を実現します。また、油圧チャックは操作が簡単で効率的なため、作業効率が向上します。
さらに、油圧チャックは耐久性に優れており、長期間安定した性能を保つことができます。これにより、継続的な使用にも適しています。アルミニウムの旋盤加工においては、油圧チャックの導入が品質向上や生産性の向上につながるポイントと言えるでしょう。
その他のチャックの種類と特徴
油圧チャックは、アルミニウムの旋盤加工において重要な役割を果たします。油圧チャックのメリットは何でしょうか?それは、しっかりと工件を固定し、高い精度で加工作業を行うことができることです。例えば、アルミニウムのような軟らかい材料でも、油圧チャックを使用することで安定して加工できます。
アルミニウム旋盤加工において、油圧チャックを使用することで作業効率が向上し、高品質な製品を生産することができます。油圧チャックは安全性も考慮されており、作業者の安全を確保します。そのため、油圧チャックはアルミニウム旋盤加工において重要なポイントとなります。
以上から、油圧チャックはアルミニウムの旋盤加工において必要不可欠であり、高い精度と安全性を提供する点がポイントと言えます。
チャック選択時の考慮点
油圧チャックのメリットとアルミニウム旋盤加工のポイントについて考える際に重要なポイントがあります。油圧チャックは、安定した保持力や高い精度を提供することで知られています。これにより、加工作業中に工件がズレることなく安定して加工することが可能です。例えば、アルミニウムのような軟らかい素材を正確に加工する際には、油圧チャックの利点がより顕著に現れます。油圧チャックを使用することで、作業効率が向上し、加工精度も向上します。そのため、アルミニウム旋盤加工において油圧チャックの選択は重要です。油圧チャックを選択する際には、保持力や精度だけでなく、耐久性やメンテナンス性も考慮することがポイントとなります。
油圧チャックとアルミニウム旋盤加工のポイント
油圧チャックの構造と動作原理
油圧チャックは、アルミニウム旋盤加工において重要な役割を果たします。油圧チャックは、加工物をしっかりと固定するための装置であり、その構造と動作原理は非常に重要です。
油圧チャックの主なメリットは、高い保持力と安定性です。これにより、加工物が正確に固定され、加工精度が向上します。具体的なポイントとして、油圧シリンダーによって均一な力が加えられるため、歪みやズレを最小限に抑えることができます。
さらに、油圧チャックは操作が簡単で効率的です。加工物の着脱がスムーズであり、作業効率が向上します。そのため、アルミニウム旋盤加工において油圧チャックの活用は欠かせません。油圧チャックの優れた構造と動作原理により、効果的な加工を実現することができます。
アルミニウム加工における油圧チャックの利用
アルミニウム旋盤加工において、油圧チャックの利用は重要です。油圧チャックは、素材をしっかりと固定することができるため、高精度な加工が可能となります。例えば、アルミニウムは比較的柔らかい素材であり、加工中に歪みが生じやすい特性があります。しかし、油圧チャックを使用することで、素材のズレや振動を最小限に抑えることができます。
さらに、油圧チャックは作業効率も向上させます。素早く正確に素材を固定できるため、加工の時間を短縮し、生産性を向上させることができます。このように、油圧チャックを利用することで、アルミニウム旋盤加工の品質向上や効率化が期待できます。
高精度加工のための油圧チャック技術
アルミニウムの旋盤加工において、高精度な加工を行うために重要な要素の一つが油圧チャック技術です。油圧チャックは、加工対象物をしっかりと保持するため、加工精度を向上させることができます。例えば、アルミニウムのような軟らかい素材を正確に加工する際には、しっかりと固定されていることが必須です。
油圧チャックを使用することで、加工品質が向上し、作業効率も向上します。また、油圧チャックは自動化されたプロセスにも適しており、生産性の向上にも繋がります。このように、油圧チャック技術はアルミニウムの旋盤加工において欠かせない要素となっています。高精度な加工を実現するために、油圧チャックの効果的な活用が重要です。
アルミニウム加工におけるトラブルシューティング
アルミニウム旋盤加工において、油圧チャックを使用することで効率的に加工作業を行うことができます。油圧チャックのメリットは、確実な固定力で作業効率が向上し、加工精度も高くなります。例えば、アルミニウムの薄い板を旋盤で加工する際、油圧チャックは適切な圧力を加えてしっかりと固定することができます。これにより、削り残しなどのトラブルを未然に防ぐことができます。さらに、油圧チャックは作業効率を向上させるため、製品の生産性向上にも繋がります。アルミニウム旋盤加工においては、油圧チャックの適切な活用がポイントとなります。
高精度アルミニウム旋盤加工のためのチャック技術
精度向上のためのチャック選択
油圧チャックは、アルミニウム旋盤加工において精度向上に大きなメリットをもたらします。油圧チャックは、高い保持力と安定した加工品質を実現するための重要な要素です。例えば、アルミニウムは比較的軟らかい素材であるため、正確な加工が求められます。油圧チャックは強固な保持力を持ち、加工中のずれや歪みを最小限に抑えることができます。その結果、仕上がりの品質が向上し、作業効率も向上します。
アルミニウム旋盤加工において、油圧チャックの選択は精度向上のために欠かせないポイントと言えます。正確な保持力と安定性を持つ油圧チャックは、高品質な加工品を実現し、生産性を向上させます。油圧チャックを適切に選択することで、アルミニウム加工の品質と効率を飛躍的に向上させることが可能です。
高精度加工のためのチャックの取り扱い
油圧チャックは、アルミニウム旋盤加工において重要な役割を果たします。なぜなら、油圧チャックは精度を高めるだけでなく、作業効率も向上させるからです。アルミニウムは比較的柔らかい素材であり、正確な加工をするためにはしっかりと固定することが欠かせません。油圧チャックはその点で頼りになります。
具体例を挙げれば、アルミニウムの円柱を旋盤で加工する際に、油圧チャックを使用すると、素材がしっかりと固定され、正確な切削が可能となります。このように、チャックの取り扱いが適切であれば、高精度なアルミニウム加工が実現できるのです。結論として、油圧チャックはアルミニウム旋盤加工において重要なツールであり、適切に取り扱うことで高品質な加工が可能となります。
チャックと工具の精度との関係
油圧チャックは、アルミニウム旋盤加工において重要な役割を果たします。油圧チャックのメリットの一つは、高い精度を保つことができることです。この精度は、加工物を確実に保持し、正確な切削を可能にします。例えば、アルミニウムのような柔らかい素材をしっかりと固定する際に、油圧チャックが非常に効果的です。また、油圧チャックは作業効率を向上させるため、多くの工場で重宝されています。そのため、アルミニウム旋盤加工において、油圧チャックは欠かせない存在と言えます。工具と精度の関係を考えると、油圧チャックはアルミニウム加工において信頼性の高い選択肢となるでしょう。
NC旋盤の種類と旋盤用チャック・周辺機器
NC旋盤の基本と種類
油圧チャックは、アルミニウム旋盤加工において重要な役割を果たします。油圧チャックのメリットは、安定した保持力と高い精度が挙げられます。回転する加工物を確実に保持し、正確な加工を可能にします。この安定性と精度は、加工過程での効率性を向上させるだけでなく、仕上がりの品質も高めます。例えば、厚さの異なるアルミニウム材料を同じくらいの精度で旋削する際には、油圧チャックが重宝されます。また、油圧チャックは耐久性にも優れており、長期間安定した性能を提供します。したがって、油圧チャックはアルミニウム旋盤加工において信頼性の高いソリューションとして重要な要素となります。
NC旋盤用チャックの種類と特徴
油圧チャックは、アルミニウム旋盤加工において重要な役割を果たします。油圧チャックのメリットは、高い保持力と安定性です。これにより、加工中に素材がズレたり、振動したりすることを防ぎます。具体的には、アルミニウムのような柔らかい素材でも確実に固定できるため、高精度な加工が可能となります。さらに、油圧チャックは作業効率を向上させることもできます。例えば、交換作業が簡単なため、作業時間が短縮されます。その結果、生産性が向上し、コスト削減にもつながります。アルミニウム旋盤加工において油圧チャックを使用することで、安定性と効率性を高めることができます。
旋盤用周辺機器とその役割
油圧チャックは、アルミニウム旋盤加工において重要な役割を果たします。油圧チャックのメリットは、素早く正確な工作物の固定が可能であることです。このように、作業効率を向上させることができます。例えば、アルミニウムの旋盤加工において、素材が柔らかいため、しっかりと固定することが求められます。油圧チャックは、その強力な保持力により、高精度で安定した加工を実現します。さらに、素材の変形を最小限に抑えることができるため、仕上がりの品質も向上します。アルミニウムのような特性を持つ素材の加工においては、油圧チャックが適していると言えます。そのため、油圧チャックを活用することで、アルミニウム旋盤加工の品質向上と効率化が期待できます。
NC旋盤の選び方と活用ポイント
油圧チャックのメリットとアルミニウム旋盤加工のポイント
油圧チャックは工作機械で使われる部品固定装置であり、安定した加工を可能にします。アルミニウム旋盤加工において、油圧チャックは重要な役割を果たします。
まず、油圧チャックのメリットは、素早く簡単に部品を固定できることです。これにより、作業効率が向上し、高精度な加工が可能となります。例えば、複雑な形状のアルミニウム部品を正確に加工する際には、油圧チャックの使用が適しています。
さらに、油圧チャックは安定した保持力を持ち、部品の振動やズレを最小限に抑えます。これにより、加工品質の向上と加工時間の短縮が実現できます。
アルミニウム旋盤加工において、油圧チャックを活用することで、効率的な加工が可能となるのです。
アルミニウム旋盤加工における最新技術とトレンド
アルミニウム加工技術の進化
油圧チャックのメリットとアルミニウム旋盤加工のポイント
油圧チャックは、アルミニウム旋盤加工において重要な役割を果たします。油圧チャックの主なメリットは、高い精度と安定性を提供することです。アルミニウムは柔らかい素材であるため、安定した保持力が必要です。油圧チャックは、この点で優れた性能を発揮し、加工品質を向上させます。
さらに、油圧チャックは作業効率も向上させます。素早く簡単に加工物をセットアップできるため、生産性が向上します。例えば、複数の部品を連続して加工する場合でも、油圧チャックを使用することで作業時間を短縮できます。
アルミニウムの軽量性や耐食性を生かした高度な加工技術が求められる中、油圧チャックはアルミニウム旋盤加工において欠かせないポイントとなっています。
業界における新たな旋盤技術のトレンド
油圧チャックのメリットとアルミニウム旋盤加工のポイント
油圧チャックは、アルミニウム旋盤加工において重要な役割を果たしています。油圧チャックの一つのメリットは、高い精度で作業が行えることです。これは、加工時にしっかりと固定されるため、作業効率が向上します。さらに、油圧チャックは安定性が高く、振動が少ないのも特徴です。
例えば、アルミニウム素材を使用した部品加工の際、油圧チャックを使用することで、素材の繊細な加工もスムーズに行えます。加工精度が要求される部品でも、油圧チャックを使用すれば高い精度で加工することが可能です。
したがって、油圧チャックはアルミニウム旋盤加工において重要なツールであり、作業効率や加工精度の向上に貢献しています。
持続可能な製造技術とアルミニウム加工
油圧チャックは、アルミニウム旋盤加工において重要な役割を果たします。このチャックの最大のメリットは、高い安定性と精度を提供することです。油圧チャックは、加工中にしっかりと素材を固定し、振動やずれを最小限に抑えます。これにより、加工精度が向上し、製品の品質が向上します。
アルミニウム旋盤加工において、油圧チャックを使用することで、ワークピースを確実に固定できるため、加工効率が向上します。例えば、精密な部品や複雑な形状を加工する際に特に重要です。油圧チャックは、しっかりとワークピースを保持することで、作業者の安全性も高めます。
したがって、油圧チャックを使用することで、アルミニウム旋盤加工の効率性や品質が向上し、生産性が向上します。これは製造業において重要な要素であり、持続可能な製造技術の確立に貢献します。
まとめ
油圧チャックは、アルミニウム旋盤加工において効率的なツールとなります。そのメリットは、高い保持力と素早い装着が可能なことです。また、アルミニウムの特性を活かした正確な加工を実現するためには、適切な切削速度と切削深さに注意することが重要です。これにより、高品質な仕上がりを得ることができます。
「A5052とA3004アルミニウム合金の徹底比較!選ぶべき理由とは?」
アルミニウム合金を選ぶ際に、A5052とA3004という二つの選択肢があります。果たしてどちらを選ぶべきなのでしょうか?本記事では、A5052とA3004アルミニウム合金を徹底比較し、それぞれの選ぶべき理由について解説します。アルミニウムは軽い素材でありながら、強度や耐久性に優れています。そんな中、どちらの合金が自分のニーズに最適か知りたいと思っている方には、この情報が役立つでしょう。A5052とA3004、二つのアルミニウム合金の特性を理解し、自分に最適な素材を選ぶためのヒントを見つけてみましょう。
Contents
アルミニウム合金とは?
アルミニウム合金の基本
A5052とA3004アルミニウム合金は、どちらも異なる特性や用途を持っています。まず、A5052は耐食性、溶接性、可鍛性に優れており、主に船舶や薄板加工に使用されます。一方、A3004は耐食性や溶接性が高く、食品や飲料の容器、建築材料などに適しています。例えば、A5052は海洋環境に強いため、船舶の建造に適しています。一方、A3004は食品容器の製造に向いており、食品の安全性を保つ役割を果たします。選ぶ際には、使用する環境や材料の特性に応じて適切な合金を選択することが重要です。このように、A5052とA3004はそれぞれの特性を活かして異なる分野で重要な役割を果たしています。
アルミ材の種類とその用途
A5052とA3004のアルミニウム合金は、両方とも一般的なアルミ材ですが、それぞれ異なる特性を持っています。A5052は耐食性に優れ、海水などの腐食環境にも適しています。一方、A3004は耐食性や加工性に優れ、屋根や外壁など建築材料として広く使用されています。用途に合わせて選ぶことが重要です。例えば、船舶や海洋関連の部品にはA5052が適していますが、建築物の外装や缶などにはA3004が適しています。これらのアルミニウム合金は日常生活から産業用途まで幅広く使用されており、選ぶ理由は使用環境や目的によって異なります。
アルミ合金の特徴と分類
A5052とA3004アルミニウム合金を比較する際に重要なポイントは何でしょうか?まず、特徴と分類から始めましょう。A5052とA3004はどちらも主に建築、自動車、航空宇宙など幅広い産業で使われるアルミニウム合金です。A5052は耐久性に優れ、海水にも強いため、船舶の建造に適しています。一方、A3004は耐食性に優れており、食品容器や建築材料として好まれます。例えば、A5052は海外での海洋関連プロジェクトや造船業界における使用に適しています。一方、A3004は食品業界での使用が適しており、高い耐久性と加工性を備えています。合金選択の際には、用途に応じて適切な特性を考慮することが重要です。
A5052とA3004の基本特性
A5052アルミニウム合金の特徴
A5052アルミニウム合金は、強度や耐食性に優れる特徴を持っています。この合金は、船舶や航空機などの軽量かつ頑丈な部品に広く使用されています。一方、A3004アルミニウム合金は、耐食性や加工性に優れ、缶や屋根などに広く利用されています。このように、それぞれの合金には特徴があり、用途によって選ぶべき合金が異なります。
例えば、A5052は船舶や飛行機の構造部品に最適であり、A3004は缶や建物の屋根などの外観に重要です。選択する際には、使用環境や要求される性能に合わせて適切な合金を選ぶことが重要です。したがって、A5052とA3004アルミニウム合金を徹底比較し、適切な合金を選択することが大切です。
A3004アルミニウム合金の特徴
A5052とA3004アルミニウム合金を比較する際、A5052は耐食性に優れる一方、A3004は耐食性と加工性のバランスが特徴です。例えば、A5052は海洋環境下での使用に向いており、船舶の一部や海洋関連製品に利用されています。一方、A3004は缶詰や建築材料など様々な用途に適しています。加工性に優れるA3004は、建築業界では加工が必要な部品に好んで使用されています。製品の用途や環境に応じて適切なアルミニウム合金を選ぶことが重要です。このように、A5052とA3004はそれぞれ特徴が異なるため、使用目的に合わせて適切な合金を選ぶことが選択する理由となります。
A5052とA3004の比較
化学成分の違い
A5052とA3004アルミニウム合金を比較すると、どちらを選ぶべきか迷うことがありますね。この2つの合金の違いを理解することで、適切な選択ができます。
まず、A5052は強度と耐食性に優れており、主に船舶や航空機などの産業で使用されています。一方、A3004は耐蝕性に優れ、建築や食品加工業界で重宝されています。
例えば、A5052は海水や塩分などの腐食環境に適しており、海洋関連の製品に活用されます。一方、A3004は食品の保存容器や建物の外装などで使われ、食品安全や耐候性を重視する場面で重宝されています。
したがって、使用する環境や目的によって適した合金を選ぶことが重要です。両者の違いを理解し、お使いになる用途に合ったアルミニウム合金を選ぶことで、より効果的に活用できるでしょう。
機械的性質の比較
A5052とA3004アルミニウム合金を比較すると、それぞれの選び方には理由があります。まず、A5052は耐食性に優れ、海洋環境などで使用するのに適しています。一方、A3004は塗装加工がしやすく、外観を重視する場面で適しています。例えば、A5052は海洋プラントや船舶の部品に使用され、A3004は建築材料や飲料缶などに適しています。どちらも優れた特性を持ちますが、使用する環境や目的によって適した合金を選ぶことが重要です。したがって、使用目的や環境に応じて、A5052とA3004の性質を比較し、適切な選択をすることが大切です。
耐食性の比較
A5052とA3004アルミニウム合金の徹底比較!選ぶべき理由とは?アルミニウム合金はさまざまな用途に使用されますが、A5052とA3004は特に人気があります。耐食性は重要な要素であり、A5052は海水に対して優れた耐性を持ちます。これは、海洋環境での使用や船舶部品などに適しています。一方、A3004は耐食性に優れるだけでなく、塗装がしやすい特性があり、建築や車両の外装などで広く使用されています。具体例として、A5052は船舶のデッキや船体に使用され、A3004は建築材料や車両の外板に採用されています。お好みや使用目的によって適した合金を選ぶことが重要です。これらの比較を元に、適切な材料を選択し、製品の性能や耐久性を向上させることができます。
加工性の比較
アルミニウム合金の加工性は重要です。A5052とA3004の比較では、A5052が一般的に加工性に優れています。 例えば、A5052は曲げ加工や深絞り加工に向いており、船舶や航空機の製造などで幅広く使用されています。一方、A3004は耐食性に優れており、屋外での使用に適しています。
具体例を挙げると、 A5052は船舶の船体や航空機の部品などによく使われます。これは、軽量かつ強度が必要な場面での加工性が高いためです。一方、A3004は食品容器や外装パネルなどに使用され、耐久性が求められる環境で優れた性能を発揮します。
したがって、 使用目的や環境に応じて、A5052とA3004の加工性の違いを考慮することが重要です。どちらの合金も特性を活かし、最適な用途に活かすことで、効果的な素材選択が可能となります。
各合金の応用分野
A5052の応用例
アルミニウム合金は、様々な用途で使われていますが、A5052とA3004はどちらを選ぶべきか悩むこともあります。A5052は耐食性に優れ、塩水環境に適しています。一方、A3004は耐食性がやや劣りますが、塗装がしやすく、美観を重視する場合に向いています。
例えば、船舶の造船や建築材料にはA5052が適しており、海洋環境下での使用に強いことが挙げられます。一方、建物の外装パネルや食品容器など、見た目の美しさが求められる用途にはA3004が適しています。
用途や環境によって適した合金を選ぶことで、耐久性や効率性を向上させることができます。自身のニーズに合ったアルミニウム合金を選ぶ際には、この比較を参考にしてみてください。
A3004の応用例
A5052とA3004アルミニウム合金を比較する際、選ぶべき理由について考えてみましょう。A5052は耐食性が高く、A3004は耐食性と耐食性が高いという特徴があります。例えば、A5052は船舶や航空機の部品、A3004は飲料缶や建材に使用されます。A5052は主に耐久性が必要な場面で使われ、一方でA3004は加工性に優れ、柔軟に形状を変えられるため、製品の見た目や機能を重視する場面で活躍します。
このように、用途や特性に応じて選ぶことが重要です。どちらの合金も優れた性能を持ちながら、異なる分野で使われています。選択する際には、製品の要求仕様や環境に合わせて適切な合金を選ぶことがポイントです。A5052とA3004を比較し、適切な選択をすることで、製品の品質や耐久性を向上させることができます。
アルミ合金選定のポイント
プロジェクトに最適なアルミ合金の選び方
A5052とA3004アルミニウム合金を比較することに興味を持っていますか? どちらを選ぶべきか理由を探ってみましょう。まず、A5052は耐食性に優れ、海水環境などの外部要因にも強い特徴があります。一方、A3004は加工性が良く、外観仕上げに向いています。例えば、A5052は船舶や自動車の部品によく使用され、A3004は缶や屋根材などに使われています。したがって、使用する環境や目的によって選択が変わります。最終的に、どちらを選ぶにせよ、適切なアルミニウム合金を選ぶことが重要です。
コストパフォーマンスの考慮
A5052とA3004アルミニウム合金の比較を考える際に重要なのは、そのコストパフォーマンスです。A5052は耐食性に優れ、海水や化学薬品にも強いため、造船業や海洋関連産業で広く利用されています。一方、A3004は塗装処理が容易で美観性に優れており、建築や外装材料として好まれています。比較的軽量でありながら強度があり、加工もしやすい点も両合金の特徴です。このような特性を踏まえ、使用目的や環境に応じて適切な合金を選択することが重要です。そして、製品の耐久性や外観などの要素を総合的に考え、最適な選択を行うことが、コストパフォーマンスを高め、製品の満足度を向上させるポイントとなります。
アルマイト処理と合金選定の関係
A5052とA3004のアルミニウム合金にはそれぞれ異なる特性があります。例えば、A5052は耐食性に優れており、海洋環境などの厳しい条件下でも優れたパフォーマンスを発揮します。一方、A3004は塗装性が高く、外部環境に適しています。それぞれの合金には適した用途がありますので、使用目的や環境によって選択することが重要です。
例えば、建築材料として使用する場合、A5052の耐食性が重要となるでしょう。一方、外装パネルなどの塗装が必要な場合は、A3004が適しています。合金を選定する際には、使用環境や必要な特性に合わせて適切なものを選ぶことが重要です。信頼性や耐久性を求める場合には、合金の選定に注意が必要です。
専門家が語るアルミ材の選び方
アルミニウム合金選定の基準
アルミニウム合金を選ぶ際の基準について考えてみましょう。A5052とA3004の比較を行うことで、適切な選択ができるでしょう。
まず、材料の特性や用途によって選定を行うことが重要です。例えば、A5052は耐食性や溶接性に優れており、建築や船舶などに適しています。一方、A3004は強度や加工性に優れていて、食品容器や自動車部品などに使用されます。
選択の際には、予算や製品の要件も考慮する必要があります。例えば、A5052は耐食性が高いため耐久性を求める場面で活躍します。
このように、目的や要件に合わせて適切なアルミニウム合金を選定することが、製品の品質向上やコスト削減につながります。
A5052とA3004の選択基準
アルミニウム合金の中でも、A5052とA3004は人気の高い素材です。どちらを選ぶべきか、理由を見ていきましょう。まず、A5052は耐久性に優れ、湿気や塩分に強い特徴があります。一方、A3004は耐食性に優れ、塗装がしやすいという利点があります。例えば、A5052は海岸近くの建物や自動車部品に、A3004は外装パネルや食品缶によく使用されています。選択のポイントは、使用目的や環境によって異なりますが、耐久性が必要な場合はA5052を、塗装性が重要な場合はA3004を選ぶのが良いでしょう。しっかりとした選択基準を持って、最適な素材を選ぶことが大切です。
アルミニウム合金の未来動向
A5052とA3004アルミニウム合金の徹底比較!選ぶべき理由とは?
アルミニウムは軽量で耐食性があり、幅広い用途に使用されています。A5052とA3004は、どちらも一般的なアルミニウム合金であり、それぞれ特徴が異なります。
まず、A5052は強度が高く、船舶や車両の構造部材などに適しています。一方、A3004は耐食性に優れ、缶や包装材料などに広く用いられています。
例えば、A5052は海洋環境下での使用に適しており、船舶の耐食性パーツとして重宝されています。一方、A3004は食品包装や建築材料など、耐食性が要求される分野に適しています。
したがって、使用目的に応じて適切なアルミニウム合金を選択することが重要です。A5052とA3004の特性を理解し、適切な材料を選ぶことで、製品の性能を最大限に引き出すことができます。
まとめと選択ガイド
A5052とA3004、どちらを選ぶべきか
アルミニウム合金の中でもA5052とA3004は人気のある素材です。この2つの合金を比較するときに考慮すべき重要な要素があります。例えば、強度や耐食性、加工性などがあります。A5052は耐食性に優れ、海洋環境などで使用されることが多い一方、A3004は加工性が高く、製造プロセスでの柔軟性が求められる場面で重宝されます。具体例を挙げると、A5052は船舶の製造によく利用され、A3004は缶詰用の容器などによく使われています。したがって、選ぶべき合金は使用する環境や用途によって異なります。自動車や建設業界ではA5052が好まれる一方、食品工業ではA3004が好まれます。用途や要件に合わせて適切な合金を選択することが重要です。
合金選定のチェックリスト
A5052とA3004のアルミニウム合金を比較する際、選ぶべき理由は何でしょうか?A5052は耐食性があり、海水や食品加工において重宝されています。一方、A3004は塗料やコーティングに適しており、外装用途に広く使われています。このように、用途に応じて使い分けることが大切です。例えばA5052は船舶や飛行機の部品に、A3004は建築や家具に活用されます。合金選定を間違えると、耐久性や性能に影響を及ぼす可能性があります。そのため、正確な材料選定が重要です。用途や環境に合わせて最適な合金を選ぶことで、製品の品質と性能を向上させることができます。
購入前の注意点
A5052とA3004アルミニウム合金の比較について、どちらを選ぶべきか考える上で重要なポイントを見ていきましょう。まず、A5052は耐食性に優れ、A3004は耐食性と加工性が高いです。例えば、A5052は海水にも強く、A3004は曲げ加工や溶接に向いています。高い耐食性が必要な場合はA5052を、加工性が求められる場合はA3004を選択することがポイントです。つまり、使用する環境や加工方法によって最適な選択肢が異なります。徹底した比較を行い、目的に合ったアルミニウム合金を選ぶことが重要です。
まとめ
アルミニウム合金の中でもA5052とA3004は一般的に使用されるものです。これらの素材の比較によって、それぞれの特性や適用範囲を理解することが重要です。使用する環境や条件に合わせて最適な素材を選ぶことが大切です。どちらの素材も様々な産業で使用されており、その特性や利点を把握することで適切な選択が可能となります。
アルミニウム加工の秘訣!旋盤での精密加工テクニック
アルミニウム加工は、製造業において重要な技術の一つです。特に、旋盤を使用した精密加工技術は、製品の品質や精度向上に欠かせません。本記事では、アルミニウム加工の秘訣である旋盤を使った精密加工テクニックに焦点を当て、その重要性や具体的な方法について詳しく解説します。アルミニウム材料の特性や旋盤の使い方、リーマを活用した加工のポイントなど、初心者から上級者まで役立つ情報が満載です。これを読んで、あなたもアルミニウム加工のプロに一歩近づけるかもしれません。
Contents
アルミニウム加工の基本
アルミニウムの特性と加工の難しさ
アルミニウムは軽くて丈夫な特性を持ち、様々な産業で利用されています。しかし、その特性ゆえ加工が難しく、特に旋盤による精密加工は技術と知識が必要です。アルミニウムは柔らかく、熱や振動に敏感なため、適切な切削条件や冷却が重要です。例えば、アルミニウムのリーマ加工では、適切な刃先形状や刃先の材質が要求されます。旋盤操作においても、切削速度や切削深さを適切に設定することが肝要です。これらの技術を習得することで、アルミニウムを効率よく加工することが可能となります。アルミニウム加工は繊細であるが、正確なテクニックを身につけることで高品質な製品を生産できるでしょう。
旋盤加工の原理とは
アルミニウム加工において、旋盤を使用する精密加工テクニックの秘訣について考えてみましょう。旋盤加工は、工作物を回転しながら切削加工を行うことで、高精度な加工が可能となります。例えば、アルミニウムの部品を作る際には、旋盤を使用することで細かい加工ができ、耐久性や精度が向上します。
旋盤の原理は、刃物を加工物に対して摺動させることで削り取るというものです。この方法により、円筒形や円錐形などの部品を効率的に加工できるのです。また、旋盤はリーマと組み合わせて使用することで、更なる精密加工が可能になります。
アルミニウム加工において、旋盤を活用することで、高品質な部品の製造や精密な加工が可能となります。そのため、旋盤加工はアルミニウム加工における重要なテクニックと言えるでしょう。
アルミニウム加工における工具の役割
アルミニウム加工における工具の役割は非常に重要です。旋盤やリーマなどの専門的な工具を使用することで、アルミニウムの精密加工が可能となります。旋盤は円筒状の加工物を回転させ、刃物を対角線方向に進めることで形状を作り出すことができます。一方、リーマは穴を精密に仕上げるための工具であり、高い精度を要求される部品の加工に欠かせません。
例えば、自動車部品や航空機部品の製造では、アルミニウム加工に旋盤やリーマを使用して高い精度を達成しています。これらの工具を適切に扱うことで、耐久性や精度の高い製品が生産されます。アルミニウム加工において工具の適切な選択と使用は、製品の品質向上に直結する重要な要素と言えるでしょう。
アルミ加工の基礎知識とその重要性
アルミニウム加工は、産業界で重要な役割を果たしています。特に、旋盤による精密加工技術は、アルミ部品の製造に欠かせません。アルミニウムは軽量で耐久性に優れ、さまざまな産業分野で利用されています。旋盤は、アルミニウムの切削や形成を可能にし、精密な仕上がりを実現します。
例えば、自動車産業ではエンジン部品やボディパーツにアルミニウムが多用されており、その精密加工が必要不可欠です。また航空宇宙産業や医療機器産業でも、アルミ部品の高精度加工が求められています。このように、旋盤を使用した精密加工技術は、さまざまな分野で重要な役割を果たしています。
アルミニウム加工の重要性を理解し、旋盤による精密加工技術を習得することで、産業界での競争力を高めることができます。アルミ部品の需要が高まる現代において、この技術を習得することはさらなる成長と成功につながるでしょう。
アルミニウム旋盤加工の工具選び
旋盤用切削工具の種類
アルミニウム加工において、旋盤での精密加工テクニックの秘訣をご紹介します。旋盤はアルミニウムを切削する際に欠かせない工具であり、切削工具の種類は様々です。例えば、リーマという工具は穴を精密に仕上げる際に使われます。このような工具を正しく使うことで、アルミニウムの加工精度を高めることができます。
アルミニウムは軽くて丈夫な素材であり、様々な産業で使用されています。旋盤を使った精密加工は、航空機や自動車などの製造業において重要な役割を果たしています。精密加工を行う際には、適切な切削工具を選び、正確な加工技術を身につけることが必要です。
アルミニウム加工における旋盤のテクニックを習得することで、さまざまな製品の製造に貢献することができます。正確な加工技術を身につけ、高品質な製品を作るために、旋盤での精密加工をマスターしましょう。
アルミニウム加工に適した工具の選定基準
アルミニウム加工に適した工具の選定基準
アルミニウムは非常に軽量でありながらも強度があり、加工しやすい素材です。アルミニウムを旋盤で精密加工する際には、適切な工具を選ぶことが重要です。例えば、リーマと呼ばれる工具は、穴を精密に仕上げるために使用されます。精密な仕上がりが求められる場合には、リーマを使うことで高い精度を保つことができます。
また、旋盤でのアルミニウム加工においては、切削速度や切削量などの加工条件も重要です。適切な加工条件を設定することで、作業効率を向上させることができます。工具の選定と加工条件の最適化を行うことで、アルミニウム加工の精度や効率を向上させることができます。
リーマを使用するメリットと特徴
アルミニウム加工の秘訣!旋盤での精密加工テクニック
アルミニウムは軽くて強い素材で、様々な産業で使われています。旋盤という工具を使うことで、アルミニウムを精密に加工することができます。先端工具であるリーマを使用することで、さらに加工精度を高めることができます。
リーマを使用するメリットと特徴
リーマは穴や筒状の加工物の内径を精密に仕上げるための工具です。リーマを使用することで、加工物の表面仕上げが向上し、寸法精度も高まります。また、リーマは刃先が砥石で研がれているため、長期間にわたって高い加工品質を保つことができます。
アルミニウム加工においてリーマを使用することで、高品質な仕上がりと精密な寸法管理が可能となります。是非、旋盤での精密加工にリーマを活用してみてください。
精密なアルミニウム旋盤加工テクニック
旋盤設定の基本
アルミニウム加工の秘訣!旋盤での精密加工テクニック
旋盤設定の基本を理解することは、アルミニウム加工で重要です。旋盤は円柱状の材料を回転させ、切削工具を使って形を整える工作機械です。アルミニウムは軽くて加工しやすい特性がありますが、正確な加工を行うためには正しい旋盤設定が必要です。
まず、適切な切削速度や切削深さを設定することが重要です。アルミニウムは熱に敏感な素材なので、適切な切削条件を維持することで加工精度を高めることができます。また、リーマを使用して穴を精密に仕上げる際にも、適切な回転速度や進数を設定することがポイントです。
正確な旋盤設定を行うことで、アルミニウムの精密加工がより効率的に行えるだけでなく、製品の品質も向上します。これらの基本的なテクニックをマスターすることで、より良い加工結果を得ることができるでしょう。
加工速度と送り速度の最適化
アルミニウム加工において、旋盤を使用する際に重要なのは加工速度と送り速度の最適化です。旋盤を使用することで、精密な加工が可能となります。例えば、アルミニウムを旋盤で加工する際には、適切な加工速度と送り速度を設定することで、品質の高い製品を生産することができます。加工速度が速すぎると加工精度が低下し、送り速度が遅すぎると加工効率が悪くなる可能性があります。そのため、適切なバランスを見極めることが重要です。アルミニウム加工において、旋盤を使う際は、加工速度と送り速度を適切に調整することで、より効率的に精密加工を行うことができます。
切削液の利用とその効果
アルミニウム加工の秘訣!旋盤での精密加工テクニック
アルミニウムを加工する際に重要なのが、旋盤を使った精密加工です。旋盤は素材を回転させながら切削加工を行う工作機械で、アルミニウムの精密加工に適しています。例えば、旋盤を使用することで、アルミニウムを円筒状に加工したり、複雑な形状を作ることが可能です。
精密加工を行う際には、切削液の利用が効果的です。切削液は切削時に生じる熱を逃がし、切削工具と加工部品の摩擦を減らす役割があります。これにより、加工品質を向上させ、工具の寿命を延ばすことができます。
アルミニウム加工においては、旋盤を上手に活用し、切削液を適切に使用することが重要です。これらのテクニックをマスターすることで、より精密な加工が可能となります。
工具の正確な取り付けと調整
アルミニウム加工の秘訣!旋盤での精密加工テクニック
アルミニウムを工作する際に欠かせないのが、正確な工具の取り付けと調整です。旋盤を使用する際には、正確な取り付けが必要です。例えば、リーマを用いて穴を拡大する場合、適切な回転数や進み方を工具に適用することが重要です。これにより、アルミニウムを綺麗に加工することができます。
また、リーマの使い方を誤ると、加工精度が下がり、仕上がりに影響を与えかねません。そのため、正確な取り付けや適切な調整が必須です。このように、旋盤での精密加工においては、工具の取り付けと調整が成功の鍵となります。
アルミ切削加工のポイント
アルミニウム切削の際の注意点
アルミニウム加工の際には、旋盤を使用した精密加工が重要です。旋盤は、回転させながら切削加工を行う機械で、アルミニウムのような柔らかい金属を高精度に加工するのに適しています。例えば、アルミニウムのリーマ加工は、旋盤を使用して内部の穴を綺麗に仕上げるために重要です。リーマは、穴の仕上げや精度向上に役立ちます。
このように、旋盤を使ったアルミニウム加工は、精密さや効率性を求める際に欠かせないテクニックです。アルミニウムの特性を理解し、適切な旋盤テクニックを駆使することで、高品質なアルミニウム加工が可能となります。アルミニウムを扱う際には、旋盤の技術を磨き、精密な加工を実現することが重要です。
表面仕上げのコツ
アルミニウム加工において、旋盤を使用した精密加工のテクニックには、いくつかの秘訣があります。まずは、リーマを使用して正確に穴を開けることが重要です。リーマを使うことで、きめ細やかな仕上がりを実現し、加工精度を高めることができます。
さらに、アルミニウムの特性を理解し、適切な切削速度や刃先の設定を行うこともポイントです。適切な工具や刃物を使用することで、加工品質を向上させることができます。
これらのテクニックをマスターすることで、アルミニウム加工における精密加工をより効果的に行うことができます。しっかりとした技術と知識を身につけることで、高品質な製品を生産することが可能となります。
精度を高めるための工夫
アルミニウム加工の秘訣!旋盤での精密加工テクニック
精度を高めるための工夫は、アルミニウム加工において非常に重要です。旋盤を使用する際、リーマなどの道具を使って正確な仕上がりを目指します。例えば、加工するアルミニウムの種類や硬さに合わせて適切な刃物を選ぶことがポイントです。また、適切な切削速度や刃先の角度を調整することで、加工過程での摩耗を抑え、精密加工を実現します。
さらに、作業中には適切なクーリング液を使うことで熱を逃がし、アルミニウム材料の変形や変質を防ぎます。これらの工夫を取り入れることで、旋盤を使用したアルミニウム加工において高い精度を実現することが可能となります。
アルミ加工での変形を低減する技術
加工中のアルミの変形原因
アルミニウム加工の秘訣!旋盤での精密加工テクニック
アルミニウムの変形原因は、主に切削時の摩擦熱による熱膨張と、材料自体の軽さからくる振動です。これらの要因から、アルミニウムの旋盤加工においては、高速回転による作業や冷却材の使用が重要となります。
例えば、リーマを使用する際には、正確な切削条件と十分な冷却が必要です。旋盤でのアルミニウム加工においては、適切な工具選定や工程管理が不可欠であり、特に微細な部品の場合は、さらなる注意が必要です。
したがって、アルミニウム加工においては、慎重かつ正確な作業が求められます。正しいテクニックを用いることで、高品質な加工が可能となります。
変形を低減するための加工手順
【アルミニウム加工の秘訣!旋盤での精密加工テクニック】
アルミニウムは軽くて耐食性に優れ、さまざまな産業で使われる重要な素材です。アルミニウムを旋盤で加工する際、変形を低減するためにはいくつかの工程を遵守することが重要です。
まず、正確な計測が必要です。アルミニウムは熱に敏感な素材であり、旋盤での作業中に熱を生じます。したがって、事前に正確な寸法を計測しておくことで、加工途中での変形を最小限に抑えることができます。
次に、適切な切削速度と切削量を設定します。旋盤の切削工具がアルミニウムと適切な速度で接触することで、加工精度が向上し、変形リスクを抑えることができます。
これらの工程を遵守することで、アルミニウムの旋盤加工において変形を低減し、精密な加工を実現できます。
熱処理による変形防止
アルミニウムの旋盤加工において、精密な加工を行うための秘訣を紹介します。旋盤を使用する際には、高度な技術と正確な計測が不可欠です。例えば、リーマを使用して穴の精度を高めることが重要です。アルミニウムは柔らかい材料であるため、加工時に熱が発生しやすく、変形のリスクがあります。そのため、熱処理を行うことで変形を防止することが重要です。このように、適切な工程と技術を駆使することで、アルミニウムの旋盤加工において高品質な仕上がりを実現できます。
精密加工における冷却技術
アルミニウム加工における冷却技術は、旋盤での精密加工において重要なポイントです。アルミニウムは加工中に熱を持ちやすいため、冷却技術を適切に行うことが精密加工の鍵となります。冷却技術を使う理由は、アルミニウムの熱伝導率が高いため、工具や加工部分が過熱しやすいからです。
冷却技術の具体例として、リーマを使用することが挙げられます。リーマは、精密な穴加工に使用され、加工した穴の仕上がりをきれいにします。リーマを使用する際には、適切な冷却液を使うことで、アルミニウム材料を効果的に冷却しながら、精密な加工を行うことができます。
冷却技術を十分に理解し、適切に活用することで、アルミニウム加工において高品質な成形が可能となります。
アルミニウム旋盤加工の応用例
精密部品製造における事例紹介
アルミニウム加工の秘訣!旋盤での精密加工テクニック
アルミニウムの精密加工は、旋盤を使用することで高度な技術と技巧が必要とされます。旋盤は、回転する切削工具を用いて金属を削る工作機械で、精密な加工が可能です。アルミニウムは軽量で耐食性に優れ、機械加工に向いています。そのため、航空機や自動車などの産業で広く使用されています。
例えば、アルミニウムリートと呼ばれる部品は、旋盤を使用して精密に加工されます。この部品は、高温環境において耐久性が求められるため、精密な仕上げが重要です。旋盤を駆使して、微細な加工を行うことで、高品質なアルミニウム部品を製造することが可能です。
アルミニウム加工は、技術と経験が重要な要素となります。旋盤を用いた精密加工は、産業界において欠かせない技術であり、高い技術力を持つ職人が求められています。
旋盤加工技術の業界別応用
アルミニウム加工の秘訣!旋盤での精密加工テクニック
旋盤は、金属加工において精密な加工が可能な機械です。アルミニウムのような軽くて耐食性に優れた素材を旋盤で加工することで、さまざまな産業で幅広く活用されています。例えば、航空機産業ではエンジン部品やフレームなどにアルミニウムが使われ、その精密加工が求められています。
さらに、自動車産業ではエンジン部品やホイールなどにもアルミニウムが使用されており、旋盤による精密加工が欠かせません。アルミニウムは軽量で強度もあり、熱伝導率が高いため、多くの産業で重要な素材として利用されています。そのため、旋盤での精密加工技術は産業界全般において重要な技術となっています。
リーマを使用した加工事例
アルミニウム加工の秘訣!旋盤での精密加工テクニック
アルミニウムの加工には、旋盤を使用することが重要です。旋盤を使うことで、アルミニウムを精密に加工することが可能となります。例えば、リーマを使用することで、穴の精度を高めることができます。リーマは、穴の内側を磨いて拡大させる道具であり、アルミニウムの表面を滑らかに仕上げることができます。
アルミニウムは軽量で耐食性に優れており、さまざまな産業で広く使用されています。そのため、旋盤を使った精密加工は、航空宇宙、自動車、電子機器などの分野で重要な役割を果たしています。アルミニウム加工の技術を磨くことで、製品の品質向上や生産効率の向上につながるため、産業界での需要が高まっています。
アルミニウム旋盤加工のトラブルシューティング
よくある加工問題とその解決策
アルミニウム加工における旋盤を使った精密加工技術の秘訣についてご紹介します。アルミニウムは軽量で耐食性に優れ、機械加工に適しています。しかし、加工時に生じるチップの問題や工程の効率化が求められます。
まず、旋盤を使用することで、精密な形状を作ることが可能です。旋盤は回転する切削工具を用いて素材を削り、加工精度を高めます。さらに、リーマを使用して穴の仕上げを行うことで、精度の高い穴加工が可能となります。
このように、旋盤とリーマを駆使することで、アルミニウムの精密加工を行う際の技術的なポイントを押さえることが重要です。工程ごとに適切な道具やテクニックを駆使することで、効率よく高品質な加工が実現できます。
工具のメンテナンスと寿命延長
アルミニウム加工の秘訣!旋盤での精密加工テクニック
アルミニウムは軽くて丈夫な素材であり、旋盤を使用して精密加工する際にはいくつかのポイントがあります。旋盤を使用することで、アルミニウムを正確に形作ることが可能となります。例えば、旋盤を使用することで円柱や円錐などの形状を作り出すことができます。また、リーマを使って穴を拡大するなど、精密な加工が可能です。
アルミニウムの精密加工は、正確な計測と技術力が求められます。素材の特性を理解し、適切な切削速度や刃先の選択が重要です。旋盤を使いこなすことで、アルミニウム加工の可能性が広がります。
これらのテクニックをマスターすることで、アルミニウム加工の品質と効率を向上させることができます。
加工精度を落とさないためのチェックリスト
アルミニウム加工の秘訣!旋盤での精密加工テクニック
アルミニウムの加工は非常に繊細な作業です。旋盤を使った精密加工は、その中でも特に重要です。旋盤を用いることで、アルミニウムの部品を高い精度で加工することが可能となります。
まず、旋盤を使用する際には、リーマを適切に使用することが重要です。リーマは穴を精密に仕上げるための工具であり、正しいリーマを選択し、適切に使用することで加工精度を向上させることができます。
さらに、加工中には適切な切削速度や切削深さを設定することも大切です。これらのパラメータを適切に調整することで、アルミニウムの加工精度を落とさずに効率的に作業を行うことができます。
その結果、旋盤を上手に活用することで、アルミニウムの精密加工をより効果的に行うことが可能となります。
まとめ
アルミニウム加工の際には、旋盤を使用して精密加工を行うことが重要です。アルミニウムは軽量でありながらも強靱な性質を持ち、旋盤による精密加工に適しています。また、リーマを使用することで、加工面の仕上げをより滑らかにすることができます。これによって、製品の品質や精度を高めることができます。これらのテクニックを駆使することで、アルミニウム加工における高い精度と品質を実現することができます。
アルミニウム加工の秘訣!旋盤用リーマの最適回転数とは?
アルミニウム加工とは?
アルミニウムの特性と加工の基礎知識
アルミニウムは軽くて丈夫な特性を持つため、様々な産業で広く使用されています。このような特性を活かすためには、旋盤用リーマという工具が重要です。アルミニウムを正確に加工するためには、リーマの適切な回転数を知ることが欠かせません。 まず、アルミニウムは柔らかい金属であり、高速で加工することができます。そのため、旋盤用リーマの回転数は比較的高めに設定することが効果的です。例えば、直径10mmのリーマを使用する場合、適切な回転数は600から800回転/分程度とされています。 このように、リーマの適切な回転数を把握することで、効率的なアルミニウム加工が可能となります。旋盤作業においては、適切な回転数を設定して素早く正確に加工を行うことが重要です。旋盤加工の概要とアルミニウムへの適用
アルミニウム加工において、旋盤用リーマの最適な回転数は非常に重要です。適切な回転数を設定することで、アルミニウム素材を効率的に加工することが可能となります。例えば、高速回転数では切削時の振動が少なくなり、表面仕上げが向上します。一方、低速回転数では切削時の粒子の飛散が抑えられ、加工精度が向上します。 具体的には、アルミニウムの硬さや種類によって適切な回転数が異なります。例えば、柔らかいアルミニウム合金では高速回転数が適していますが、硬いアルミニウム合金では低速回転数が適しています。そのため、素材の特性に合わせて適切な回転数を選択することが重要です。 適切な回転数を設定することで、アルミニウム加工の効率と品質を向上させることができます。回転数の最適化は、高品質な製品を生産するために欠かせない要素と言えるでしょう。リーマ加工の役割と重要性
アルミニウム加工において、旋盤用リーマの最適な回転数は非常に重要です。リーマは加工時に素材の精度を高め、滑らかな仕上がりを実現します。適切な回転数を選択することで、アルミニウム材料が劣化することなく効果的に加工されます。 例えば、高速回転の場合、加工が早くなりますが、材料が熱を持ちやすくなる可能性があります。一方、低速回転では加工時間がかかりますが、材料への負荷が少なくなる利点があります。 したがって、リーマの最適な回転数は、加工対象のアルミニウムの硬さや形状などによって異なります。適切な回転数を選定することで、効率的かつ品質の高い加工が可能となります。アルミ板の穴あけ加工の注意点
アルミ板の穴あけ前の準備
アルミニウムを旋盤で加工する際、リーマの最適な回転数が重要です。理想的な回転数を選定することで、アルミニウム板への穴あけ作業をスムーズに行うことができます。まず、リーマの回転数を決定する際に考慮すべきポイントがあります。アルミニウムの種類やサイズ、旋盤の種類などを考慮し、適切な回転数を設定することが重要です。 具体的な例を挙げると、アルミニウム合金を穴あけする場合、高速鋼製リーマを使用し、適切な回転数を設定することが効果的です。例えば、直径10mmのアルミニウム板を加工する場合、適切な回転数はXXXX rpm程度となります。 以上のように、適切な回転数を選定することで、アルミニウム加工作業を効率的に行うことができます。適切な準備と注意を払いながら、リーマを使用することで、きれいな穴あけ加工が可能となります。アルミ板の穴あけ加工の注意点
注意点 | 説明 |
---|---|
適切な工具の選定 | アルミ専用のドリルビットを使用すること。 |
切削速度の調整 | 適切な回転数を選び、過熱を避ける。 |
冷却剤の使用 | 加工中の温度上昇を防ぐため、冷却剤を使用。 |
固定の重要性 | 板をしっかり固定し、振動を抑える。 |
穴の位置決め | 精密な位置決めを行い、正確な穴あけを。 |
正しい穴あけ手順
- 設計図の確認:
- 穴の位置やサイズを確認する。
- 材料の固定:
- クランプやバイスを使ってアルミ板を固定する。
- ドリルビットの選定:
- アルミ用のドリルビットを取り付ける。
- 回転数の設定:
- ドリルの回転数を調整する。
- 穴あけ開始:
- ドリルをゆっくりと押し当て、真っ直ぐに穴をあける。
- 冷却剤の適用:
- 必要に応じて冷却剤をかけながら作業する。
- 穴あけ完了後:
- 穴のバリを取り除く。
- 最終確認:
- サイズや位置を再確認する。
まとめ
- 注意点を守りながら、正しい手順で作業を行うことで、精度の高い穴あけが可能になります。
穴あけ時の一般的なトラブルと対処法
トラブル | 原因 | 対処法 |
---|---|---|
ドリルビットの摩耗 | 不適切な速度、冷却不足 | 回転数を調整し、冷却剤を使用する。 |
穴のズレ | 不正確な位置決め、固定不良 | 位置を再確認し、しっかり固定する。 |
バリの発生 | 高速回転、切削不良 | 切削速度を下げ、バリ取りを行う。 |
加工面の傷 | 不適切な工具や材料の固定 | 適切な工具を選び、材料をしっかり固定。 |
穴の形状不良 | ドリルビットの不良、圧力不足 | 新しいビットに交換し、適切な圧力をかける。 |
オーバーヒート | 過度な摩擦、冷却剤不足 | 冷却剤を追加し、作業速度を見直す。 |
ドリルビットの折れ | 過剰な圧力、誤った進行方向 | 適切な圧力をかけ、真っ直ぐ進行する。 |
まとめ
- トラブルを未然に防ぐため、適切な工具選定や加工条件の確認が重要です。トラブル発生時は、原因を特定し、適切な対処を行うことで改善できます。
リーマ加工の基礎
リーマとは?-その種類と特徴
アルミニウム加工において、旋盤用リーマは重要な役割を果たします。リーマとは、穴の形状や精度を整える工具のことです。適切な回転数を知ることは、品質の向上につながります。たとえば、高速回転によってアルミニウムが適切に加工され、スムーズな仕上がりを実現します。一方、低速回転だと加工精度が低下し、仕上がりに影響を及ぼす可能性があります。 アルミニウムの旋盤加工において、適切な回転数を設定することは重要です。リーマの種類や特性を理解し、それに合った最適な回転数を見極めることが生産性向上につながります。正しい回転数でリーマを使用することで、効率的かつ高品質な加工が可能となります。リーマ加工の基本手順
アルミニウム加工において、旋盤用リーマの最適な回転数をご存知ですか?リーマ加工の基本手順を理解することが重要です。リーマとは、穴を正確な寸法や仕上がりに加工する工具のことです。旋盤用リーマの回転数は、加工する素材や穴の大きさによって異なります。例えば、アルミニウムの場合は、適切な回転数を設定しないと加工精度が落ちる恐れがあります。リーマ加工を行う際には、素材の特性や工具の使い方を考慮し、適切な回転数を設定することが重要です。正しい回転数を設定することで、効率的に穴加工が行えます。これにより、高品質なアルミニウム加工製品が作られることにつながります。リーマ加工の流れとコツ
リーマを使用する前の準備
アルミニウムを旋盤加工する際、リーマの最適な回転数が重要です。リーマを使用する前の準備には、まず適切な回転速度を設定することがポイントです。アルミニウムの特性やリーマの種類によって最適な回転数は異なります。例えば、高速鋼製のリーマを使用する場合は、適切な回転数を保つことが切削品質や工具寿命に影響します。 回転数が速すぎるとリーマや加工物が損傷する可能性があります。逆に回転数が遅すぎると加工時間が長引いたり、切削品質が低下する可能性があります。したがって、リーマを効果的に活用するためには、適切な回転数を知ることが重要です。リーマの種類やアルミニウムの材質を考慮して、最適な回転数を設定しましょう。リーマ作業のステップバイステップ
アルミニウムの旋盤加工において、リーマ作業は非常に重要です。リーマの最適な回転数を知ることは、品質の向上につながります。まず、なぜ回転数が重要なのかを考えてみましょう。リーマが適切な回転数で使用されることで、アルミニウム材料が適切に削られ、仕上がりの精度が高まります。 具体的な例を挙げると、適切な回転数でリーマを使用することで、加工面の表面仕上げが滑らかになり、寸法精度も向上します。逆に回転数が速すぎると加工面に傷がついてしまったり、リーマの寿命が短くなる可能性があります。 したがって、アルミニウム加工においてリーマ作業を行う際には、適切な回転数を設定することが不可欠です。このように、リーマの最適な回転数を把握することは、加工品質の向上に繋がります。リーマ加工の際のコツと注意点
アルミニウム加工において、旋盤用リーマの最適な回転数は重要です。旋盤用リーマを効果的に使用するためには、正しい回転数を選択することがポイントです。例えば、アルミニウムの場合、適切な回転数を知っておくことで加工品質を向上させることができます。リーマが高速で回転すると、適切な切削速度が得られ、加工面の仕上がりが向上します。一方、低速で回転させると、加工表面の仕上がりが荒くなります。したがって、アルミニウムを効率的に加工するためには、材料の性質やリーマの種類に応じて適切な回転数を選択することが必要です。適切な回転数を選択することで、品質向上や効率化につながることが期待できます。旋盤用リーマの最適回転数
回転数の決定要因
アルミニウム加工において、旋盤用リーマの最適な回転数を決定する要因は様々です。まず、アルミニウムの硬度やリーマの材質、加工する穴の大きさなどが影響を与えます。特に重要なのは適切な切削速度を保つことです。適切な回転数を設定することで、アルミニウムの加工精度が向上し、工具の寿命も延ばすことができます。例えば、アルミニウムの旋盤加工において、過剰な回転数を設定すると刃先の摩耗が早まり、加工面の質が低下します。逆に、適切な回転数を設定することで、効率的かつ品質の高い加工が可能となります。したがって、アルミニウム加工においては、適切な回転数の設定が重要であることがわかります。材料と回転数の関係
アルミニウム加工の際に旋盤用リーマの最適な回転数を知ることは非常に重要です。アルミニウムは柔らかい金属であり、適切な回転数を使用しないと品質や効率に影響がでます。リーマは工具の一種で、穴の精度を高めるために使用されます。アルミニウムの場合、適切な回転数は一般的に高速ですが、素材の厚さやリーマのサイズによって異なります。 例えば、直径5mmのリーマを使用する場合、適切な回転数は1000回転/分程度であることが多いです。これにより、きれいで正確な穴を効率的に作ることができます。リーマの回転数を正しく設定することで、アルミニウム加工の品質を向上させることができます。適切な回転数を知り、工程を丁寧に行うことが重要です。アルミニウム用リーマの推奨回転数
アルミニウムを旋盤加工する際に、リーマの最適な回転数は非常に重要です。アルミニウムは比較的柔らかい金属であるため、適切な回転数で加工することがポイントです。リーマの回転速度が速すぎると、アルミニウムが破損する可能性があります。逆に遅すぎると、きれいな仕上がりが得られません。 一般的に、アルミニウム用リーマの推奨回転数は、500〜3000回転/分の範囲内とされています。これは加工するアルミニウムの硬度やリーマのサイズによって異なりますが、初めは適切な範囲内で試行錯誤してみることが大切です。 例えば、直径10mmのアルミニウムを加工する場合、1000〜1500回転/分程度が良いかもしれません。このように、適切な回転数を見極めることで、効率的かつ綺麗な仕上がりが期待できます。是非、アルミニウム加工に挑戦してみてください。穴径の精度を上げるリーマ加工方法
穴径精度を左右する要素
アルミニウム加工において、旋盤用リーマの最適な回転数は非常に重要です。回転数が適切でないと、穴の精度が損なわれる可能性があります。例えば、回転数が速すぎると加工面に過度の摩擦が生じ、加工精度が低下します。逆に、回転数が遅すぎると切削速度が不足し、加工が不十分になることがあります。 したがって、アルミニウム加工においては、旋盤用リーマの最適な回転数を設定することがカギとなります。適切な回転数を見極めるには、材料の種類や加工方法、リーマの仕様などを考慮する必要があります。最終的に、穴の精度を左右する要素は回転数と密接に関連しており、適切なバランスを見極めることが重要です。精度向上のためのリーマの選び方
アルミニウム加工において、旋盤用リーマの最適な回転数は何でしょうか?リーマの選び方において重要なポイントを解説します。アルミニウムの旋盤加工において、リーマの回転数は加工精度に直結します。リーマの回転数が速すぎると、加工表面の仕上がりが悪くなる可能性があります。逆に遅すぎると、加工時間がかかり生産性が低下します。 適切な回転数は材料やリーマの径によって異なります。一般的には、アルミニウムの場合は高速回転が適しています。例えば、直径10mmのリーマであれば、約3000〜4000rpm程度が良いとされています。このように、適切な回転数を選ぶことで、効率的な加工が可能となります。 したがって、アルミニウム加工においては、適切なリーマの回転数を選ぶことが重要です。加工精度を向上させるために、リーマの回転数に注意を払いましょう。穴径精度を高めるためのリーマの使い方
アルミニウムの加工において、旋盤用リーマの最適な回転数を知ることは非常に重要です。アルミニウムは柔らかい金属であり、正しい回転数を設定することで穴径の精度を高めることができます。 まず、リーマの回転数が速すぎると、アルミニウムが過剰な熱を受けて変形する可能性があります。逆に、回転数が遅すぎると、きれいな仕上がりを得ることができない恐れがあります。 例えば、旋盤用リーマを使う際には、アルミニウムの種類や加工する穴の大きさに合わせて適切な回転数を設定する必要があります。これによって、精度の高い加工が可能となり、作業効率も向上します。 つまり、適切な回転数を設定することで、アルミニウム加工における穴径精度を高めることができるのです。効果的なリーマ加工のためのアドバイス
リーマ加工の事前チェックリスト
アルミニウム加工において、旋盤用リーマの最適な回転数を知ることは重要です。リーマ加工の事前チェックリストを確認することで、作業の効率性や品質を向上させることができます。まず、旋盤用リーマの適切な回転数を決定するためには、加工するアルミニウムの種類やサイズ、加工状態などを正確に把握することがポイントです。例えば、硬度の異なるアルミニウム合金を加工する場合は、適切な回転数を変える必要があります。適切な回転数を設定することで、リーマの寿命を延ばし、加工精度を高めることができます。つまり、正しい回転数を選択することで、アルミニウム加工の品質向上につながるのです。加工中のリーマの状態監視
アルミニウム加工において、旋盤用リーマの適切な回転数は重要です。リーマとは、穴の内側を整える工具であり、正確な回転数で使用することが加工精度に直結します。例えば、高速回転させすぎると工具が破損しやすくなり、逆に低すぎると加工精度が低下します。適切な回転数を設定することで、アルミニウム加工の効率性と品質を向上させることができます。 加工中のリーマの状態監視も大切です。リーマが摩耗している場合は交換が必要です。定期的な点検と適切なメンテナンスを行うことで、リーマの寿命を延ばし、安定した加工品質を保つことができます。旋盤用リーマの最適な回転数と定期的なメンテナンスによって、アルミニウム加工の効率と品質を確保しましょう。リーマのメンテナンスと寿命管理
アルミニウム加工において、旋盤用リーマの最適な回転数について知識を得ることは重要です。リーマのメンテナンスと寿命管理は、加工精度や作業効率に直結します。正しい回転数を選ぶことで、アルミニウムの加工品質を向上させることができます。 理想的な回転数は、リーマの種類や加工条件によって異なります。適切な回転数を選ぶためには、リーマメーカーの推奨値や実際の加工結果を参考にすることが重要です。例えば、高速回転数での加工は、加工時間を短縮することができますが、適切な冷却や潤滑が必要です。 したがって、リーマのメンテナンスと寿命管理には、適切な回転数の選択が欠かせません。正しい回転数を選択することで、アルミニウム加工における効率と品質を向上させることができます。よくある質問とその回答
アルミニウム加工でのリーマ選択基準は?
アルミニウム加工でのリーマ選択基準は、旋盤用リーマの最適回転数がポイントです。アルミニウムは比較的柔らかい材料なので、回転数を適切に設定することが重要です。回転数が速すぎると切削力が増し、逆に遅すぎると切りくずの排出がうまくいかない可能性があります。例えば、直径10mmのアルミニウム材料に対しては、適切な回転数は約2000rpm程度です。これにより、切削効率を最大化し、加工品質を向上させることができます。適切な回転数を選択することで、アルミニウム加工の効率と品質を高めることができます。リーマ加工での切削油の役割は?
アルミニウム加工において、旋盤用リーマの最適な回転数は非常に重要です。リーマは加工時に素材を滑らかに整え、精度を高める役割を果たします。適切な回転数を選ぶことで、効率的かつ正確な加工が可能となります。 例えば、アルミニウムを旋盤で加工する際、リーマの適切な回転数は材料の種類や硬さ、加工する穴の大きさなどによって異なります。一般的には遅すぎず、速すぎずの回転数を選ぶことが重要です。遅すぎると加工が遅れ、速すぎるとリーマの寿命が短くなる可能性があります。 したがって、リーマ加工を行う際には適切な回転数を設定し、素材や加工条件に合わせて適切な選択を行うことが大切です。これにより、効率的な加工が可能となり、高品質な製品を生産することができます。アルミニウム加工での仕上げ面の改善方法は?
アルミニウム加工での仕上げ面の改善方法には、旋盤用リーマの最適な回転数を知ることが重要です。アルミニウムは柔らかく、熱に敏感な素材であり、適切な回転数を選ばないと加工面の仕上がりに影響が出ます。 旋盤用リーマを使用する際に、適切な回転数を見極めるポイントは何でしょうか?まず、加工するアルミニウムの種類や硬度、およびリーマの種類を考慮することが重要です。一般的に、高速度で回転させると表面が滑らかに仕上がりますが、過度な回転数は素材を損傷させる可能性があります。 例えば、アルミニウム合金の場合、適切な回転数は500〜3000 RPMの範囲で選択すると良いでしょう。リーマの刃先が素材にしっかりと切り込むように微調整することで、きめ細かな仕上げ面を実現できます。適切な回転数を見極めることで、アルミニウム加工における仕上げ面の品質向上が期待できます。まとめ
アルミニウム加工において、旋盤用リーマの最適な回転数が重要です。適切な回転数を使用することで、加工精度を高めることができます。アルミニウムの特性やリーマの材質などを考慮し、最適な回転数を見極めることが必要です。異なる材料やリーマに対しては異なる回転数が求められますので、注意が必要です。また、適切な潤滑剤を使用することで、加工時の摩擦を減らし、作業効率を向上させることができます。A5052とA7204の徹底比較!どっちがあなたに最適?
アルミニウムとは
アルミニウムの基本情報
A5052とA7204は、アルミニウム合金の中でも人気のあるタイプです。A5052は強度があり、耐食性にも優れていることから、船舶や飛行機などの構造部品に幅広く使用されています。一方、A7204は耐食性に優れており、熱伝導率が高いため、家電製品や自動車の部品などによく用いられます。どちらも優れた特性を持ちますが、用途や環境によって最適な合金が異なります。 例えば、A5052は塩水に曝される海洋環境下での使用に適していますが、A7204は高温での使用に適しています。つまり、使用する環境や条件によって適した合金を選択することが重要です。 したがって、船舶や飛行機の構造部品を作る場合はA5052が適していますが、家電製品や自動車の部品を作る際にはA7204が最適です。用途に合わせて適切なアルミニウム合金を選ぶことで、製品の性能や耐久性を向上させることができます。アルミニウム合金の一般的な特徴
A5052とA7204を徹底比較して、どちらがあなたに最適か考えてみましょう。アルミニウム合金は、軽量で耐食性に優れているため、さまざまな産業で広く使用されています。A5052は、強度が高く、溶接性に優れており、船舶や自動車などの製造に向いています。一方、A7204は、耐食性に優れていて、塩水環境にも適しています。例えば、海洋装置や飛行機部品に使用されることがあります。どちらも優れた性能を持っていますが、使用する環境や用途によって適した合金が異なります。あなたのニーズに最適なアルミニウム合金を選ぶ際には、これらの特性を考慮して、しっかりと比較検討することが大切です。アルミニウムの用途と適性
アルミニウムは、その軽量性、耐食性、加工性に優れた特性から、幅広い用途で使用されています。用途に応じて、様々なアルミニウム合金が選ばれ、特定の機械的・化学的特性を持つ合金が適用されます。主な用途と適性
用途 | 適性と選ばれる理由 | 代表的なアルミ合金 |
---|---|---|
自動車部品 | 軽量で燃費向上、耐食性に優れ、衝撃吸収性が高い | A5052、A6061 |
航空機部品 | 高強度・軽量で、耐食性が求められる | A2024、A7075 |
建築材料 | 耐久性・加工性・美観に優れ、耐食性が高い | A3003、A6063 |
包装材料 | 軽量、耐食性、耐熱性に優れ、加工が容易 | A1100、A8011 |
電気機器 | 電気伝導率が高く、軽量で熱伝導性も良好 | A1350、A6061 |
船舶構造材 | 軽量で耐食性が非常に高く、特に海水環境に強い | A5056、A5083 |
家庭用品 | 軽量で耐久性があり、加工が容易 | A1050、A3003 |
各分野での適性
- 自動車部品:
- アルミニウムは鉄よりも軽量で、燃費向上に寄与します。また、耐食性があるため、外装部品やエンジン部品に広く使用されています。
- 航空機部品:
- 高強度で軽量なアルミニウム合金(A2024やA7075など)は、航空機の構造材や内部部品で使用されています。これにより、重量を抑えながらも機体の強度を維持できます。
- 建築材料:
- サッシや外装パネル、屋根材などにアルミニウムが使用されています。耐候性が高く、メンテナンスの頻度を減らすことができるため、長期使用に向いています。
- 包装材料:
- アルミホイルや飲料缶に使われるアルミニウムは、軽量で加工が容易であり、さらに食品との反応が少なく、安全性も高いため、包装材として優れています。
- 電気機器:
- アルミニウムは銅に次いで電気伝導率が高い素材であり、軽量化が求められる電力機器や電子部品に利用されています。
- 船舶構造材:
- 海水への耐食性が高いA5056やA5083が、船舶の外装材や構造材に使われています。軽量でありながら耐久性に優れ、海上環境に適しています。
まとめ
アルミニウムの用途は多岐にわたり、軽量であること、耐食性が高いこと、加工性に優れていることが選ばれる理由です。用途に応じて適切なアルミ合金を選ぶことで、製品の性能や耐久性を最適化できます。アルミニウム合金A5052の特徴
A5052の化学成分と物理的性質
化学成分(%)
元素 | 含有量(%) |
---|---|
アルミニウム (Al) | 残り (バランス) |
マグネシウム (Mg) | 2.2 – 2.8 |
クロム (Cr) | 0.15 – 0.35 |
鉄 (Fe) | 0.40 以下 |
シリコン (Si) | 0.25 以下 |
銅 (Cu) | 0.10 以下 |
亜鉛 (Zn) | 0.10 以下 |
マンガン (Mn) | 0.10 以下 |
チタン (Ti) | 0.05 以下 |
物理的性質
性質 | 値 |
---|---|
密度 | 2.68 g/cm³ |
引張強度 (UTS) | 210 – 260 MPa |
耐力 (0.2%耐力) | 130 MPa (代表値) |
伸び率 (50mm) | 12 – 20 % |
硬度 (ビッカース硬度) | 約 60 HV |
熱伝導率 | 約 138 W/m·K |
電気伝導率 | 約 33% IACS |
熱膨張係数 | 23.8 × 10⁻⁶ /K |
溶解温度 | 607°C |
特徴
A5052はマグネシウムを主合金元素とするアルミニウム合金であり、優れた耐食性と中程度の強度を特徴としています。加工性や溶接性が高く、特に海洋環境や化学工業分野での使用に適しています。また、軽量でありながら比較的強度が高く、幅広い用途で利用されています。A5052の加工性と耐食性
加工性
加工方法 | 特性 |
---|---|
曲げ加工 | 容易に曲げることができ、複雑な形状にも対応可。亀裂が入りにくい。 |
深絞り加工 | 深絞り加工に適しており、大型部品にも対応可能。 |
溶接 | アーク溶接やスポット溶接に適しており、溶接後も強度を保つ。 |
切削加工 | 柔らかいが、高速切削可能。工具の切れ味と加工液の使用が重要。 |
耐食性
環境 | 耐性 |
---|---|
海洋環境 | 塩水環境で高い耐食性を持ち、船舶や海洋構造物に適用。 |
化学薬品 | 酸・塩基などの化学薬品に対する耐性があり、化学工業で利用。 |
大気腐食 | 屋外使用でも大気腐食に強く、建築材料として長寿命を発揮。 |
A5052の主な利用分野と事例
A5052とA7204の比較を考える際、それぞれの素材がどのような特徴を持っているかを理解することが重要です。A5052は強度が高く、耐久性に優れています。これは主に航空機や自動車の部品、さらには建築材料などに広く利用されています。一方、A7204は耐食性に優れており、食品加工業や海洋関連の部品などに適しています。 特に、A5052は航空機の胴体や翼、自動車のホイールなど、高い強度が必要な部位で使用されています。一方、A7204は海水や食品と接する箇所で優れた耐食性を発揮し、長期間の使用にも適しています。 このように、用途や環境に応じて使い分けることで、それぞれの特長を最大限に活かすことができます。最適な材料を選択するためには、要件と目的に合った素材を適切に選定することが肝要です。アルミニウム合金A7204の特徴
A7204の化学成分と物理的性質
化学成分(%)
元素 | 含有量(%) |
---|---|
アルミニウム (Al) | 残り (バランス) |
亜鉛 (Zn) | 5.1 – 6.1 |
マグネシウム (Mg) | 2.1 – 2.9 |
銅 (Cu) | 1.2 – 2.0 |
鉄 (Fe) | 0.50 以下 |
シリコン (Si) | 0.50 以下 |
マンガン (Mn) | 0.30 以下 |
クロム (Cr) | 0.10 – 0.25 |
チタン (Ti) | 0.20 以下 |
その他 | 各 0.05 以下 |
物理的性質
性質 | 値 |
---|---|
密度 | 2.80 g/cm³ |
引張強度 (UTS) | 480 – 540 MPa |
耐力 (0.2%耐力) | 380 MPa 以上 |
伸び率 (50mm) | 約 10 – 15 % |
硬度 (ビッカース硬度) | 約 160 HV |
熱伝導率 | 約 130 W/m·K |
電気伝導率 | 約 30% IACS |
熱膨張係数 | 23 × 10⁻⁶ /K |
溶解温度 | 477 – 635°C |
特徴
A7204は、亜鉛を主な合金元素とする高強度アルミニウム合金です。高い強度と耐久性を持ちながら、比較的軽量であり、特に航空宇宙産業や自動車部品に利用されています。引張強度が高く、応力がかかる部分でも優れた性能を発揮しますが、耐食性は他のアルミ合金に比べて低いため、表面処理が必要になることが多いです。A7204の強度と加工性
強度
性質 | 値 |
---|---|
引張強度 (UTS) | 480 – 540 MPa |
耐力 (0.2%耐力) | 約 380 MPa 以上 |
伸び率 (50mm) | 約 10 – 15 % |
硬度 (ビッカース硬度) | 約 160 HV |
加工性
加工方法 | 加工性 |
---|---|
曲げ加工 | 強度が高いためやや難しい |
切削加工 | 中程度の切削性 |
溶接 | 熱処理後の溶接は難しい |
プレス加工 | 加工には特別な対策が必要 |
A7204の主な利用分野と事例
利用分野
分野 | 特徴・理由 |
---|---|
航空宇宙産業 | 高い強度と軽量性により、航空機の構造部品に適用。 |
自動車産業 | 軽量化を図りつつ、強度を確保するために使用される。 |
スポーツ用品 | 軽量で高強度な性質から、ゴルフクラブや自転車フレームなどに利用。 |
軍需産業 | 高強度・耐久性を持つため、軍用車両や装甲材などに使用。 |
エレクトロニクス | 熱伝導性の高さから、放熱部品や冷却システムに使用される。 |
A5052とA7204の徹底比較
A5052とA7204の化学成分と物理的性質の比較
化学成分の比較
成分 | A5052 (%) | A7204 (%) |
---|---|---|
アルミニウム (Al) | 余剰 | 余剰 |
マグネシウム (Mg) | 2.2 – 2.8 | 1.2 – 2.0 |
クロム (Cr) | 0.15 – 0.35 | – |
銅 (Cu) | 0.1以下 | 1.2 – 2.0 |
亜鉛 (Zn) | – | 5.1 – 6.1 |
マンガン (Mn) | 0.1以下 | 0.3 |
鉄 (Fe) | 0.4以下 | 0.5以下 |
シリコン (Si) | 0.25以下 | 0.5以下 |
- A5052はマグネシウムを主成分とし、耐食性に優れたアルミニウム合金です。
- A7204は亜鉛を含む高強度合金で、銅も含まれているため強度が高い一方で、耐食性はやや劣ります。
物理的性質の比較
性質 | A5052 | A7204 |
---|---|---|
引張強度 (UTS) | 約 210 – 260 MPa | 約 480 – 540 MPa |
耐力 (0.2%耐力) | 約 130 – 195 MPa | 約 380 MPa 以上 |
伸び率 (50mm) | 約 12 – 20 % | 約 10 – 15 % |
硬度 (ビッカース硬度) | 約 60 – 80 HV | 約 160 HV |
密度 | 2.68 g/cm³ | 2.80 g/cm³ |
耐食性 | 優れている | 中程度 |
- A5052は耐食性や加工性に優れ、軽量で多用途に使用されますが、強度はそれほど高くありません。
- A7204は非常に高い強度を持つため、航空機や自動車など、応力がかかる部分に使用されますが、耐食性はA5052ほど高くありません。
加工性と耐食性の比較
A5052とA7204の比較において、加工性と耐食性が重要な要素となります。まず、A5052は溶接性が高く、加工しやすい特徴を持っています。一方、A7204は強度が高く、耐食性に優れています。例えば、建築材料としてA5052は曲げ加工やプレス加工に適しており、建築業界で広く使用されています。一方、A7204は海洋環境に耐える必要がある構造物や船舶部品に適しています。したがって、使用する環境や目的に応じて適切な材料を選択することが重要です。総じて言えることは、A5052は加工性が高く、一方、A7204は耐食性に優れているという点です。どちらが最適かは使用する場面や条件によって異なりますが、適切な比較を行い、最適な選択をすることが大切です。強度と軽量化設計への影響
強度と軽量化設計への影響を考えると、A5052とA7204は重要な選択肢です。例えば、A5052は耐久性に優れ、船舶や航空機などの産業で広く使用されています。一方、A7204は溶接性に優れ、建築や自動車部品などで好まれています。 A5052は海水などの腐食に強いため、海洋関連の構造物に適しています。一方、A7204は強度が高く、耐久性が求められる自動車のフレームなどに最適です。 それぞれの特性を比較し、使用する環境や要件に合わせて適切な素材を選択することが重要です。最終的には、どちらが最適かは使用目的や条件によって異なるため、慎重な検討が必要です。A5052とA7204のコストと利用分野における適性比較
コストの比較
合金 | コスト (相対的) | 理由 |
---|---|---|
A5052 | 低~中 | 一般的なアルミニウム合金であり、材料費が安価で、大量生産が可能なため。 |
A7204 | 高 | 高強度で特化した用途向けの合金であり、製造コストが高く、素材の希少性が影響。 |
- A5052は、コストパフォーマンスに優れ、汎用的な用途に広く使用されています。
- A7204は、特殊用途向けの高強度合金で、コストが高いため、予算に限りがある場合は制約があります。
利用分野における適性比較
分野 | A5052の適性 | A7204の適性 |
---|---|---|
建築材料 | 高:耐食性が必要な建築材料に適している。 | 低:高強度が必要な用途であれば適用可能。 |
自動車部品 | 中:軽量かつ耐食性が求められる部品に適している。 | 高:シャーシやホイールなど高強度が必要な部品に最適。 |
航空機産業 | 低:強度不足。 | 高:高強度が必要な航空機の構造部品に最適。 |
船舶・海洋産業 | 高:耐食性に優れ、海水環境に適している。 | 中:特に高強度が求められる箇所に適用。 |
電子機器・放熱部品 | 高:優れた加工性と放熱性で放熱部品に使用可能。 | 中:強度が必要な箇所に限られる。 |
スポーツ用品 | 中:耐久性と軽量性が求められる用途に適している。 | 高:高強度が必要なスポーツ用品に最適。 |
- A5052は耐食性、軽量性、加工性に優れ、広範な用途で利用されています。特に建築材料や船舶産業など、耐食性が重要な分野に適しています。
- A7204は高強度を活かして、航空宇宙産業や自動車産業など、過酷な条件下で使用される製品に適しています。コストが高いため、高強度が絶対的に必要な場合に限定されることが多いです。