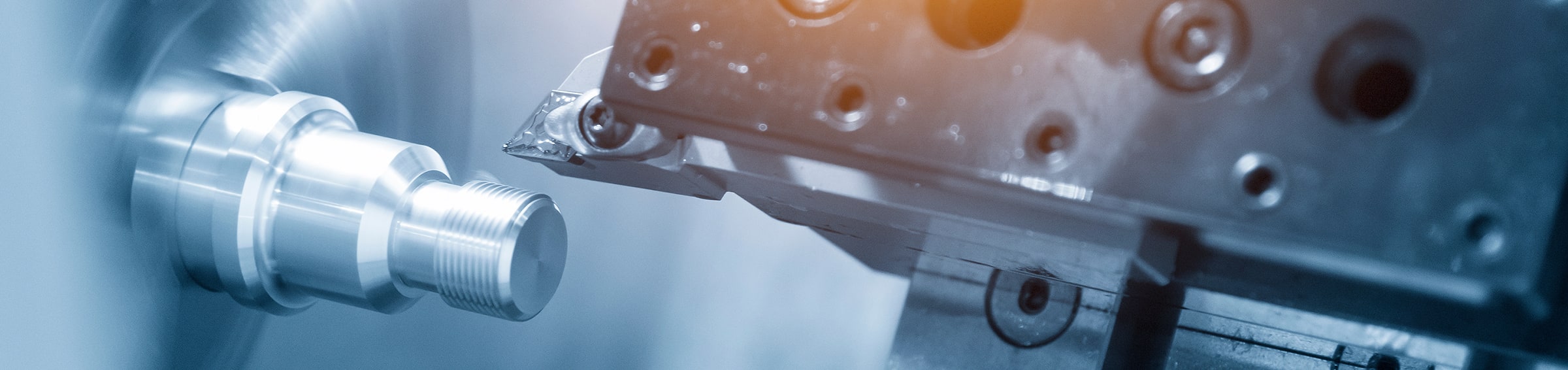
コラム column
A5056アルミニウム合金の機械的性質と耐食性について解説
「A5056アルミニウム合金についてもっと知りたいけれど、機械的性質や耐食性がどうなっているのか分からない…」そんな悩みを抱えている方はいませんか?
本記事では、A5056アルミニウム合金の特性やその利点について詳しく解説します。アルミニウム合金は軽量でありながら高い強度を持ち、さまざまな産業分野で利用されている重要な素材です。しかし、機械的性質や耐食性についての具体的な理解がなければ、適切な用途を見極めることは難しいものです。
もしあなたが以下のような疑問を持っているなら、この記事はまさにあなたのためのものです。
- A5056アルミニウム合金の機械的性質はどのようなものなのか?
- この合金の耐食性はどのように評価されるのか?
- A5056アルミニウム合金はどのような場面で最も効果的に使われるのか?
これから、A5056アルミニウム合金の特性について深掘りし、その魅力を余すところなくお伝えします。新たな知識を得ることで、あなたのものづくりや設計の選択肢が広がることでしょう。さあ、一緒にこの合金の世界を探求してみましょう!
1. A5056 機械的性質 耐食性の概要
1-1. A5056アルミニウム合金とは
A5056は、アルミニウムとマグネシウムを主成分とするアルミニウム合金で、耐食性、強度、加工性が優れた特性を持っています。特に海水や湿気に対する耐性が高く、構造材や耐腐食部品として幅広く利用されています。
- 主要成分: アルミニウム、マグネシウム
- 特長: 高い耐食性、良好な加工性、強度
1-2. A5056の主な用途
A5056はその優れた耐食性と機械的性質により、さまざまな産業で使用されています。主な用途には以下が含まれます:
- 船舶や海洋構造物: 高い耐海水性を生かして、船体や海上プラットフォームの構造部材に使用されます。
- 化学設備: 耐薬品性が求められる化学工業の設備や配管に使われます。
- 航空機部品: 高強度と耐腐食性が求められる航空機部品にも使用されています。
2. A5056 機械的性質 耐食性の詳細
2-1. A5056の機械的性質
A5056は高い引張強度と降伏強度を持ち、非常に優れた機械的特性を提供します。これにより、強度が求められる環境での使用に最適です。
- 引張強度: 最大310 MPa
- 降伏強度: 約150 MPa
- 伸び: 10%以上
これらの特性により、A5056は多くの工業用途で耐荷重性能を提供します。
2-2. ヤング率と硬度の具体的な数値
A5056のヤング率と硬度は以下の通りです:
- ヤング率: 約70 GPa
- 硬度: 約85-95 HRB(ロックウェルB硬度)
これらの値は、A5056が変形に対してどれほど耐性があるかを示しており、非常に高い機械的強度を提供します。
2-3. A5056の比重と融点
A5056の比重は、アルミニウム合金としては標準的な数値を示します。また、融点も高く、熱に対する耐性があります。
- 比重: 約2.66
- 融点: 約630°C
これにより、A5056は高温環境にも耐えられる特性を持っています。
3. A5056 機械的性質 耐食性と他のアルミ合金の比較
3-1. A5056とA5052の違い
A5056とA5052は共にマグネシウムを主成分とするアルミニウム合金ですが、以下の違いがあります:
- A5056: より高い強度と耐食性を提供し、特に海水環境での使用に優れています。
- A5052: 強度はA5056に劣りますが、加工性に優れ、一般的な工業用途に広く使用されます。
A5056は、より過酷な環境に適していますが、加工性がやや劣るため、用途に応じた選定が必要です。
3-2. A5056とA2017の違い
A5056とA2017の違いは、主にその合金成分にあります:
- A5056: マグネシウムを多く含み、耐食性が非常に高いです。船舶や海洋環境に適しています。
- A2017: 銅を多く含み、高い強度を持っていますが、耐食性はA5056に劣ります。航空機や構造材での使用に適しています。
A5056は耐食性が重要な場合に選ばれますが、A2017は強度が最重要な場合に選ばれます。
4. A5056 機械的性質 耐食性の実用性
4-1. A5056の耐食性について
A5056は非常に高い耐食性を持ち、特に海水や湿気の多い環境に強い特性を発揮します。マグネシウムを多く含むため、塩水や酸性環境でも腐食しにくく、長寿命の部品を提供します。
- 特長: 海水環境に耐える、酸性環境でも耐食性が高い
- 使用例: 船舶、海洋構造物、化学設備
4-2. A5056の切削性と加工性
A5056は優れた加工性を提供しますが、他のアルミニウム合金よりやや硬いため、切削には少し注意が必要です。しかし、一般的にはフライス盤や旋盤などの加工機で問題なく加工できます。
注意点: 適切な切削速度と冷却を使用することが重要です
加工性: 良好
切削性: 適切な工具と条件で良好
まとめ
A5056アルミニウム合金は、優れた機械的性質と耐食性を持つ材料です。主にマグネシウムを含み、強度が高く、加工性にも優れています。また、海水や湿気に対する耐食性があり、航空機や海洋構造物などの用途に適しています。軽量で耐久性が求められる場面での利用が広がっています。
アルミニウムA5083の機械的性質と耐食性を徹底解説
皆さんは「A5083という素材の特性について詳しく知りたいけれど、どこから手を付ければいいのかわからない」とお考えではありませんか?そんなあなたのために、本記事ではA5083の機械的性質と耐食性について、わかりやすく解説します。
A5083はアルミニウム合金の一種で、特に耐食性に優れていることで知られています。建築や船舶、さらには航空機など、幅広い分野で使用されているこの素材ですが、その具体的な特性や適用分野については意外と知られていないことも多いです。「A5083がどのように機械的性質を発揮するのか」「耐食性が何故優れているのか」といった疑問にお答えし、A5083の魅力を余すところなくお伝えします。
この記事を読めば、A5083の基礎知識から、実際の活用方法まで、知っておくべき情報がすべて手に入ります。あなたがA5083を選ぶ理由や、他の素材との違いを理解できるようになることでしょう。それでは、一緒にA5083の深い世界に飛び込んでいきましょう。
1. A5083 機械的性質 耐食性の概要
1-1. A5083合金とは
A5083合金は、アルミニウム、マグネシウムを主成分とする海水耐食性に優れたアルミニウム合金です。特に、海洋環境や厳しい腐食環境での使用に適しており、船舶や海洋構造物に広く使用されています。A5083合金は、耐食性と強度を兼ね備えた特性を持ち、特に塩水環境でその優れた耐食性を発揮します。
1-2. A5083の機械的性質
A5083合金は、その優れた機械的性質でも知られており、特に引張強度と耐圧強度が高いことが特徴です。具体的な機械的特性は以下の通りです:
- 引張強度:最大345 MPa
- 降伏強度:最大240 MPa
- 硬度:約85 HB(ハードネス)
- 延性:良好であり、加工性にも優れています。
これらの特性は、A5083を厳しい使用環境においても耐久性が高い材料として位置付けています。
1-3. A5083の耐食性
A5083合金は、アルミニウム合金の中でも最高レベルの耐食性を誇ります。特に海水に対する耐食性が高く、腐食を防ぐための表面酸化膜が非常に強固で、海洋環境でも長期間の使用が可能です。具体的には、塩水環境でのピット腐食や応力腐食割れに対する耐性が優れており、船舶や海洋プラットフォームなどの構造材として最適です。
2. A5083 機械的性質 耐食性とA5052の比較
2-1. A5083とA5052の基本特性
A5083とA5052は、どちらもアルミニウム・マグネシウム合金であり、耐食性が優れていますが、特性には若干の違いがあります。
- A5083: 高い強度と耐食性が特徴。特に海水環境における耐久性に優れ、船舶や海洋機器で多く使用されます。
- A5052: 強度はA5083に劣りますが、より優れた成形性を持ち、薄板での使用や押出成形に適しています。耐食性も高く、特に化学薬品や海水環境においても効果的です。
2-2. 強度とヤング率の比較
A5083とA5052の機械的性質において、強度とヤング率に違いがあります:
- 引張強度:
- A5083: 最大345 MPa
- A5052: 最大210 MPa
- ヤング率(弾性率):
- A5083: 約70 GPa
- A5052: 約70 GPa
ヤング率は両者でほぼ同じですが、A5083は引張強度において大きな優位性を持っています。
2-3. 耐食性の違い
耐食性に関して、A5083は特に海水に対する耐性が強力であり、海洋環境下での使用が求められる場面に最適です。一方、A5052も耐食性は高いものの、A5083に比べて若干劣る場合があり、特に塩水環境での耐久性が求められる用途ではA5083の方が適しています。
3. A5083 機械的性質 耐食性に関する具体的数値
3-1. A5083の強度データ
A5083合金の強度は以下の通りです:
- 引張強度:最大345 MPa
- 降伏強度:最大240 MPa
- 硬度:85 HB(ハードネス)
これらのデータは、A5083合金が高い耐圧性を誇り、海水環境など厳しい条件下での耐久性を支える要因です。
3-2. ヤング率の具体的数値
A5083のヤング率は約70 GPaであり、この数値は金属の弾性を示し、A5083が強い圧縮や引っ張り荷重にも耐える能力を持っていることを示します。これにより、構造部材としての使用において高い安定性を提供します。
3-3. 他のアルミ合金との比較
他のアルミ合金と比較した場合、A5083は引張強度が高く、特に海水環境での耐食性において優れた性能を発揮します。例えば、A5052との比較では、A5052は引張強度こそ低いですが、成形性が優れ、耐食性も高いため、薄板加工には最適ですが、強度が求められる場合はA5083が選ばれることが多いです。
4. A5083合金を使用するメリット
4-1. 耐食性の利点
A5083合金の最も顕著なメリットは、その優れた耐食性です。特に、塩水環境や海水における耐食性において、他のアルミ合金と比較しても非常に高いパフォーマンスを発揮します。これにより、以下のような利点があります:
- 海洋環境での使用: 船舶や海洋構造物において、塩水や湿気にさらされる状況でも長期間の耐久性を保持。
- 腐食による劣化のリスク軽減: 金属が腐食しにくいため、メンテナンスコストが抑えられ、構造物の寿命が延びます。
4-2. 機械的性質の優位性
A5083合金は、機械的特性においても優れたバランスを提供します。特に、引張強度、降伏強度、靭性などの面で高い性能を発揮し、以下のような利点があります:
- 高い引張強度: 最大345 MPaという強度により、重荷重がかかる構造部材においても強度を維持します。
- 優れた靭性: 極端な低温や高温環境でも衝撃に強く、割れにくい特性を持っています。
- 加工性の高さ: その優れた成形性により、複雑な形状の加工にも対応可能です。
4-3. 使用例と適用分野
A5083合金は、主に耐食性と機械的性質を必要とする環境で広く利用されています。具体的な使用例としては、以下の分野が挙げられます:
- 船舶産業: 船体、船舶部品、浸水部材など。
- 海洋プラットフォーム: 油田やガスプラットフォームの構造材として使用。
- 防衛産業: 軍事用途での厳しい環境に耐えるための部材。
- 輸送機器: 高強度が必要な輸送機器やトレーラーなど。
5. アルミ板の強度に関する情報
5-1. アルミ板の強度特性
アルミ板の強度は、その合金成分や熱処理によって大きく異なります。一般的に、アルミニウム合金の強度は以下の特性に基づいて評価されます:
- 引張強度: 材料が引っ張られたときに耐えられる最大強度。
- 降伏強度: 材料が塑性変形を開始する前の最大応力。
- 硬度: 材料の表面の硬さ。硬いほど傷や摩耗に強い。
- 疲労強度: 繰り返し荷重に対する耐性。
アルミ板の強度特性は、使用する環境や荷重条件に合わせた選定が重要です。
5-2. A5083と他のアルミ板の比較
A5083合金は、特に強度と耐食性が優れた合金です。以下の表は、A5083と他のアルミ合金(A5052、A6061)の強度に関する比較です:
特性 | A5083 | A5052 | A6061 |
---|---|---|---|
引張強度 | 最大345 MPa | 最大210 MPa | 最大310 MPa |
降伏強度 | 最大240 MPa | 最大160 MPa | 最大275 MPa |
硬度 | 85 HB | 60-75 HB | 95 HB |
耐食性 | 優れた | 良好 | 良好 |
適用分野 | 海洋、輸送機器 | 化学設備、建築材料 | 構造材、航空産業 |
A5083は、特に強度と耐食性が求められる海洋環境や重荷重を扱う用途で非常に優れています。
5-3. 強度を考慮した選び方
アルミ板を選定する際には、使用環境と要求される強度特性を考慮する必要があります。例えば:
- 海洋環境や高耐食性が求められる場合: A5083が最適。
- 構造材としての強度が必要な場合: A6061やA7075が適している場合が多い。
- 化学設備や建築用途の場合: A5052が耐食性と加工性のバランスが取れているため、最適。
使用目的に応じて最適な合金を選択することが、性能を最大化するためのポイントです。
まとめ
A5083は、優れた機械的性質を持つアルミニウム合金で、高い強度と優れた耐食性が特徴です。特に海洋環境や化学工業での使用に適しており、耐食性はMg含有量によって向上します。溶接性も良好で、さまざまな産業で幅広く利用されています。
A6061アルミニウムの特性とは?強度と耐食性のバランスを解説
工業製品や建材など、多岐にわたる分野で使用されるアルミニウム合金の中でも、A6061は特に注目されています。「A6061を使いたいけれど、その特性について詳しく知りたい」と思っている方は多いのではないでしょうか?
本記事では、A6061アルミニウムの機械的性質や耐食性についてわかりやすく解説します。具体的には、以下の疑問にお答えします。
- A6061アルミニウムとはどのような素材なのか?
- この合金の強度は他の素材と比べてどうなのか?
- 耐食性はどの程度なのか、またその理由は?
これらの疑問をクリアにすることで、A6061をどのように利用すれば良いのか、具体的なイメージを持つことができます。軽量でありながら強靭な特性を持つA6061アルミニウムを正しく理解し、効果的に活用するための情報をお届けします。さあ、一緒にA6061アルミニウムの魅力を紐解いていきましょう。
1. A6061の特性と用途
1-1. A6061の基本特性
A6061は、アルミニウム合金の中でも非常に広く使用されている合金で、優れた強度、耐食性、加工性を兼ね備えています。主にシリコン(Si)とマグネシウム(Mg)が合金成分として含まれており、その特性は次の通りです:
- 引張強度:A6061は引張強度が約260 MPa〜310 MPaの範囲で、強度と耐食性のバランスが取れています。
- 耐食性:海水や湿気の多い環境でも優れた耐食性を発揮し、船舶や外部機器に最適です。
- 加工性:熱処理後の硬化により、加工性が良好で、フライス加工、旋盤加工などが容易です。
- 溶接性:溶接が可能であり、特にアルゴンアーク溶接(TIG)などの方法での加工が得意です。
1-2. A6061の主な用途
A6061はその強度、耐食性、加工性のバランスが良いため、非常に多様な用途に使用されています。代表的な用途には以下のものがあります:
- 航空機産業:構造部品やフレームに使用され、軽量で強度が求められる場所に最適です。
- 自動車:車体のフレームやサスペンション部品、エンジン部品などで使用されています。
- 建設:耐久性のあるフレームや支柱、橋梁部品など、構造物の一部として利用されます。
- 電子機器:携帯電話やコンピュータの筐体に使用されることが多いです。
- スポーツ器具:自転車フレームやゴルフクラブなど、軽量で強度が求められる製品に広く使用されています。
2. A6061と他のアルミ合金の違い
2-1. A6061とA5052の比較
A6061とA5052はどちらもアルミニウム合金ですが、特性にいくつか違いがあります:
- 強度:A6061の方がA5052よりも高い強度を持っています。A5052は良好な延性と耐食性を持つものの、強度面ではA6061に劣ります。
- 耐食性:A5052は特に耐海水性に優れており、海洋環境での使用においてA6061よりも優れた性能を発揮します。一方、A6061も耐食性は良好であり、多くの産業用途で問題なく使用できます。
- 用途:A5052は主に海洋や化学プラントで使用され、A6061は構造部品や航空機、自動車などの高強度が求められる用途に使用されます。
2-2. A6061とA7075の比較
A6061とA7075はどちらも高強度のアルミニウム合金ですが、A7075はさらに強度が高いという特徴があります:
- 強度:A7075はA6061よりも非常に高い引張強度(最大570 MPa程度)を誇ります。これにより、航空機や軍事用の部品など、極限の強度が必要とされる分野で使用されます。
- 加工性:A6061はA7075よりも加工が容易で、特に溶接性や成形性に優れています。A7075は加工が難しいため、高精度な機械加工が必要です。
- 耐食性:A6061の耐食性はA7075よりも優れています。A7075は耐食性が劣るため、特殊な表面処理が必要です。
3. A6061の機械的性質と耐食性
3-1. A6061の機械的性質
A6061は、引張強度と降伏強度のバランスが取れた合金であり、優れた加工性と熱処理後の強度向上が特徴です。代表的な機械的性質には以下があります:
- 引張強度:約260〜310 MPa。
- 降伏強度:約240 MPa。
- 伸び:12〜20%(加工方法によって異なる)。
- 硬度:HB 90〜95(熱処理後)。
- 疲労強度:高い疲労強度を誇り、構造部品や機械部品において長寿命が期待できます。
3-2. A6061の耐食性
A6061は非常に優れた耐食性を持ち、特にアルミニウムの合金に特徴的な酸化皮膜を形成するため、さまざまな環境下でも腐食に強いです。特に以下のような特性があります:
表面処理:A6061は陽極酸化処理を施すことで耐食性がさらに向上し、耐久性が増します。この処理により、表面に硬くて耐久性のある酸化膜が形成され、外観も美しく保たれます。
海水耐性:A6061は塩水環境に対して優れた耐食性を示し、船舶や海洋構造物にも使用されます。
アルカリ性環境:アルカリ性の環境でも耐食性が高く、化学プラントやその他の厳しい環境で使用されます。
4. アルミ合金の化学成分とその影響
4-1. A6061の化学成分
A6061は主にシリコン(Si)、マグネシウム(Mg)、および少量の銅(Cu)、マンガン(Mn)、クロム(Cr)、チタン(Ti)を含むアルミニウム合金です。具体的な化学成分は次の通りです:
- アルミニウム(Al): 約95.8%〜98.6%
- シリコン(Si): 0.4%〜0.8%
- マグネシウム(Mg): 0.8%〜1.2%
- 銅(Cu): 0.15%〜0.4%
- マンガン(Mn): 0.15%〜0.3%
- クロム(Cr): 0.04%〜0.35%
- チタン(Ti): 0.15%(最大)
この化学成分が、A6061の強度、加工性、耐食性、耐熱性に大きな影響を与えています。
4-2. 化学成分が特性に与える影響
A6061の化学成分は、その機械的性質や耐食性に直接的な影響を与えます。具体的には以下の影響があります:
- シリコン(Si):シリコンは主に鋳造性を改善し、合金の流動性を向上させます。また、シリコンは耐食性に寄与することがあり、酸化膜の形成を促進します。
- マグネシウム(Mg):マグネシウムは合金の強度を高める役割を果たします。特に、熱処理後に強度が大幅に向上します。マグネシウムはまた、A6061の耐食性にも貢献します。
- 銅(Cu):銅は合金の強度と硬度を向上させますが、耐食性には若干の悪影響を及ぼす場合があります。銅を適切にコントロールすることで、強度を最大限に引き出せます。
- マンガン(Mn):マンガンは合金の耐食性と機械的性質を向上させ、特にアルカリ環境に対して有効です。
- クロム(Cr):クロムは耐食性を向上させるとともに、耐摩耗性を向上させる効果もあります。
- チタン(Ti):チタンは粒界を細かくし、合金の強度を高める役割を持ちます。
このように、A6061の化学成分は、強度や耐食性を最適化するために非常に重要な役割を果たします。
5. アルミ板の強度に関する基礎知識
5-1. アルミ板の強度の測定方法
アルミ板の強度は、主に以下の方法で測定されます:
- 引張強度(Tensile Strength):引張強度は、材料が引っ張り荷重を受けたときに破断するまでの最大応力を示します。通常、引張試験機を使用して、試験片を引っ張りながらその応力を測定します。
- 降伏強度(Yield Strength):降伏強度は、材料が塑性変形を開始する点での応力を示します。この値は、材料が永久変形を始める前に支えられる最大応力を示します。
- 硬度(Hardness):硬度は、材料の表面の抵抗力を測定する指標で、ロックウェル硬度試験やブリネル硬度試験などを使用して測定します。
- 疲労強度(Fatigue Strength):繰り返し荷重を加えた際に、材料が破壊に至るまでの応力レベルを測定します。
これらの測定方法を使用して、アルミ板の強度が評価され、各種用途に適した性能が選定されます。
5-2. A6061の強度特性
A6061の強度は、熱処理によって大きく改善され、特にT6状態では強度が最も高くなります。A6061の強度特性は以下の通りです:
- 引張強度:T6状態で最大310 MPa。
- 降伏強度:T6状態で最大276 MPa。
- 硬度:T6状態で約95 HB(ブリネル硬度)。
- 疲労強度:A6061は非常に高い疲労強度を持ち、構造部品や機械部品の長寿命化に寄与します。
A6061の強度は他のアルミ合金と比較しても優れており、特に軽量化が求められる構造や機械部品に最適です。
まとめ
A6061アルミニウムは、優れた強度と耐食性を兼ね備えた合金です。主にマグネシウムとシリコンを含み、加工性が良く、溶接性も優れています。軽量でありながら、構造材料としての信頼性が高く、航空機や自動車、建築など幅広い用途に利用されています。バランスの取れた特性が魅力です。
アルミニウムA6063の機械的性質と耐食性を徹底解説!
「A6063という材料を使いたいけれど、どのような特性があるのかわからない……」。そんな悩みを抱えている方に朗報です!本記事では、A6063の機械的性質と耐食性について詳しく解説します。
A6063は、アルミニウム合金の中でも特に優れた特性を持つ材料として知られています。この合金は、建材や自動車、電機製品などさまざまな分野で利用されており、その人気の理由は一体何でしょうか?機械的性質や耐食性がどのように製品の性能に影響を与えるのか、そして設計や製造においてどのように活用できるのかを探ります。
この記事を通じて、A6063の特性についての理解を深め、その利点を最大限に活かすための知識を得ていただけることを目指します。これからのものづくりにおいて、A6063を選択することがどのように役立つか、一緒に考えてみましょう!
1. A6063の機械的性質についての理解を深める
1-1. A6063の基本的な機械的性質
A6063はアルミニウム合金の一種で、特に優れた加工性と耐食性が特徴的です。硬度が高くなく、強度は比較的低いですが、成形性に優れ、軽量であるため、建築、装飾、電気機器などさまざまな分野で広く使用されています。一般的に、A6063合金は、良好な溶接性、圧延性、押出性を持っており、複雑な形状や装飾的なデザインを必要とする製品に向いています。アルミニウム合金の中でも非常に高い耐食性を誇り、長期間の使用にも耐えるため、屋外使用にも適しています。
1-2. 引張強度と降伏強度の特性
A6063の引張強度はおおよそ160〜250 MPa程度であり、降伏強度はその約60%〜75%程度となっています。この数値は、特に高い強度を要求される用途には不向きであり、むしろ建材や装飾材、軽量構造物に適した強度レベルです。降伏強度が比較的低いため、強度が求められる用途では限界がありますが、対照的に、加工がしやすく、精密な形状を作ることができるという大きな利点があります。A6063合金は、厚さが薄くても強度を維持できるため、軽量化が重要な製品には最適です。
1-3. A6063の硬度と靭性
A6063の硬度は、ビッカース硬度(HV)で約55〜80程度とされており、比較的柔らかい部類に入ります。これにより、精密な加工が可能で、製品に対して必要な耐久性を持ちながらも、破損しにくいという特徴があります。また、靭性(衝撃に対する耐性)が高いため、急激な衝撃や負荷にも耐えることができます。これにより、屋外使用や衝撃が加わる可能性のある環境においても有効に使用されます。
2. A6063の耐食性がどのように影響するか
2-1. A6063の耐食性の重要性
A6063合金は非常に優れた耐食性を有しており、特に湿気の多い環境や塩水の影響を受けやすい地域で重宝されています。この合金の耐食性は、合金中に含まれるシリコンとマグネシウムの成分に起因しています。これらの元素は、自然酸化層を形成し、アルミニウムが腐食するのを防ぐ役割を果たします。そのため、A6063は屋外での建材や海洋構造物に使用されることが多いです。優れた耐食性により、長期間使用しても表面の腐食や劣化を最小限に抑えることができ、メンテナンス費用を削減することができます。
2-2. 環境要因がA6063の耐食性に与える影響
A6063合金の耐食性は環境によって大きく影響を受けます。例えば、塩水、酸性やアルカリ性の環境、さらには高湿度の場所では耐食性が低下する可能性があります。これらの環境においては、腐食の進行を防ぐために特別な表面処理やコーティングが必要となる場合があります。特に海岸地域や塩害の影響を受ける地域で使用する場合、追加の表面処理(陽極酸化や粉体塗装)が推奨されます。
2-3. A6063の表面処理と耐食性の向上
A6063合金の耐食性を向上させる方法として、陽極酸化処理が非常に効果的です。陽極酸化は、アルミニウム合金の表面に酸化膜を形成し、この酸化膜が耐食性を大幅に向上させます。酸化膜は非常に硬く、摩耗にも強いため、外的衝撃や摩擦に対しても耐性を持ちます。また、陽極酸化後の表面は電気的に絶縁され、さらに美しい外観を保持します。さらに、粉体塗装や塗装によるコーティングも耐食性を向上させる手段として有効です。
3. A6063の化学成分が性能に与える影響
3-1. A6063の主要な化学成分
A6063合金の主な成分は、アルミニウム(Al)を基本とし、シリコン(Si)、マグネシウム(Mg)、鉄(Fe)、銅(Cu)などが含まれます。シリコン(0.2〜0.6%)は鋳造性を向上させ、流動性を良くします。マグネシウム(0.45〜0.9%)は合金の強度を増加させる役割を果たします。また、微量の鉄や銅が合金中に含まれ、耐食性や機械的特性を最適化します。これらの成分比率は、A6063の最適な性能を実現するために非常に重要です。
3-2. 化学成分と機械的性質の関係
A6063合金におけるシリコンとマグネシウムの比率は、強度と加工性に大きな影響を与えます。シリコンが増えることで鋳造性や圧延性が向上し、複雑な形状を成形しやすくなります。一方、マグネシウムが増えることで合金の強度が向上しますが、過剰になると延性が低下するため、適切なバランスが求められます。これにより、建材や装飾品、機械部品などの使用において、強度と加工性の最適化が可能になります。
3-3. A6063の合金設計と性能の最適化
A6063合金の性能は、シリコンとマグネシウムの最適なバランスによって決まります。シリコンを適切に調整することで鋳造性が高まり、マグネシウムの配合により強度が向上します。さらに、他の成分(鉄や銅)の割合を管理することで、耐食性や機械的特性が調整され、特定の用途に合わせた性能が得られます。このような最適化により、建材、航空機部品、海洋構造物など、多様な産業において高いパフォーマンスを発揮することができます。
4. A6063の強度や耐力を他のアルミ合金と比較する
4-1. A6063と他のアルミ合金の強度比較
A6063合金は、アルミニウム合金の中でも比較的低い強度を持つ部類に入ります。その引張強度は160〜250 MPa程度であり、これはA7003やA7075などの高強度アルミ合金と比べるとかなり低い値です。しかし、A6063はその代わりに優れた加工性と耐食性を持ち、特に軽量で耐食性が重視される用途に適しています。対照的に、A7003やA7075合金は高強度を誇り、航空機やスポーツ用品、構造材料などの強度が必要な分野で使用されます。したがって、A6063は強度を重視する用途よりも、加工性や耐食性が重要な用途に最適です。
4-2. 耐力の観点からのA6063の位置付け
A6063合金の耐力(降伏強度)は約110〜170 MPaとされており、これも他のアルミニウム合金と比較して低めです。耐力の観点では、A6063は強度よりも加工性や耐食性を重視する用途に適しています。たとえば、A7075やA2024などのアルミニウム合金は、降伏強度が高く、より強度が求められる構造用途で使用されますが、A6063は建材や装飾、機器の部品など、強度よりも軽量さや耐腐食性が優先される用途に適しています。そのため、A6063は耐力が重要な用途よりも、耐久性やデザイン性が重要視される場面に適した材料です。
4-3. 用途別のアルミ合金選定ガイド
アルミニウム合金の選定は、主に強度、耐食性、加工性のバランスによって決まります。A6063合金は以下のような用途に適しています:
- 建築:A6063はその優れた加工性と耐食性から、窓枠、ドア、カーテンウォール、手すりなどの建材に最適です。
- 装飾品:アルミニウムの美しい外観を保持するため、A6063は装飾用のパーツや外装に適しています。
- 軽量構造物:強度がそこまで求められないが、耐食性が重要な場合にA6063が使用されます。航空機や車両の軽量部品などにはA6063が適していますが、強度が要求される部分にはA7003やA7075などの強化型合金が選ばれます。
高強度が求められる場合には、A6063ではなく、A7075やA2024といった高強度合金を選択することが推奨されます。特に機械的負荷が大きい構造部品や、高温環境で使用される部品には、高強度合金が適しています。
5. A6063の加工性や切削性についての情報
5-1. A6063の加工性の特徴
A6063合金は非常に良好な加工性を持ち、特に押出し成形や圧延、溶接性に優れています。機械加工や切削も比較的簡単であり、複雑な形状や薄肉部品の製造が可能です。これは、A6063が比較的軟らかい合金であるため、工具の摩耗が少なく、加工中に発生する熱も比較的少ないためです。また、切削やプレスなどの加工方法で良好な仕上がりが得られます。加工後の表面品質も高く、塗装や陽極酸化処理が容易に行えるため、仕上がりが美しく、長期的な使用に耐える品質を保持します。
5-2. 切削性と加工方法の選択
A6063の切削性は、アルミニウム合金の中でも良好な部類に入ります。切削時には、工具の選定が重要で、主に鋭い切削工具や高速回転工具を使用することで、効率的な加工が可能です。特に、旋盤やフライス盤などの機械での加工が得意とされます。切削油を使用すると、さらに切削性が向上し、工具の寿命も延びます。また、A6063はその加工性の良さから、薄い板や細かな形状を作る際にも適しており、精密加工が可能です。
5-3. 加工時の注意点とベストプラクティス
A6063合金を加工する際の注意点として、以下の点が挙げられます:
- 工具の選定:鋭い切削工具を使用することで、切削面の仕上がりが良好になります。工具の摩耗を抑えるために、適切な切削油や冷却材を使用することが推奨されます。
- 加工温度の管理:加工時の温度が高すぎると、合金が変形したり、機械的性質が損なわれる可能性があります。適切な冷却を行い、温度管理を徹底することが重要です。
- 仕上がり面の保護:A6063は表面が傷つきやすいため、加工後の表面処理(陽極酸化や塗装)を行い、耐食性や外観を保護することが必要です。
これらの注意点を守ることで、A6063合金の加工がスムーズに行え、品質の高い製品を得ることができます。
まとめ
A6063は、優れた機械的性質を持つアルミニウム合金で、特に成形性や溧接性に優れています。強度は中程度ですが、耐食性が高く、屋外用途に適しています。表面処理によりさらなる耐久性が得られ、建築や自動車産業で広く利用されています。
A7003アルミニウム合金の機械的性質と耐食性についての徹底解説
A7003アルミニウム合金について、あなたはどれほど知っていますか?この合金は、特に自転車や航空機のフレームなど、軽量かつ高強度を求められる分野で多く利用されています。しかし、その優れた機械的性質や耐食性について詳しく理解している方は少ないのではないでしょうか?
この記事では、A7003アルミニウム合金の特徴や利点について徹底的に解説します。「どのような機械的性質を持っているのか?」「耐食性はどれほどなのか?」という疑問をお持ちの方には、ぜひ読んでいただきたい内容です。A7003の特性を理解することで、用途に応じた最適な選択ができるようになるでしょう。
この記事を通じて、A7003アルミニウム合金がどれほど優れた素材であるかを知り、その可能性を引き出す手助けができればと思います。それでは、深掘りしていきましょう!
1. A7003 機械的性質 耐食性の概要
1-1. A7003とは何か
A7003は、アルミニウムとマグネシウムを主成分とする合金で、強度、耐食性、加工性のバランスが取れていることから、さまざまな産業分野で利用されています。航空機部品や自動車産業、建設機械など、軽量化と強度が求められる場面で特に重宝されます。
1-2. A7003の機械的性質の特徴
A7003合金は、優れた引張強度と降伏強度を持つため、構造的な強度が求められる用途に向いています。さらに、伸びや硬度のバランスも良好で、機械加工や成形が比較的容易です。この合金は軽量でありながら、高い機械的性能を発揮します。
1-3. A7003の耐食性の重要性
A7003は耐食性に優れており、特に湿気や塩分を含む環境下での使用に強いという特徴があります。特に海洋環境や外部に曝される部品などに適しています。この耐食性は、アルミニウムとマグネシウム合金が生成する酸化皮膜により保護されます。
2. A7003の機械的性質について
2-1. 引張強度と降伏強度
A7003の引張強度は非常に高く、構造部品としての用途に適しています。また、降伏強度も高いため、変形しにくく、荷重に対してしっかりと耐えることができます。これにより、高い強度が求められる用途での使用に向いています。
2-2. 伸びと硬度
A7003は、引張強度に優れつつも、伸び(延性)を保っています。これにより、加工性においても優れた性能を発揮します。硬度については、アルミニウム合金の中でも中程度であり、一般的な機械加工が可能です。
2-3. 耐摩耗性と疲労強度
A7003合金は耐摩耗性に優れており、摩擦が多い環境での使用にも適しています。また、疲労強度が高いため、繰り返し荷重がかかるような条件でも長期的に安定して使用できます。
3. A7003の耐食性に関する情報
3-1. 耐食性のメカニズム
A7003合金の耐食性は、主に酸化皮膜によって守られています。この皮膜は、合金表面に自然に形成され、腐食から保護します。特に海水や塩分の多い環境下でも、この皮膜により耐食性が維持されます。
3-2. 環境条件と耐食性の関係
A7003合金の耐食性は、使用される環境条件によって影響を受けます。高湿度、塩分を含んだ環境、または極端な温度変化が耐食性に影響を与える可能性があるため、これらの条件に応じた適切な表面処理や防食措置が必要です。
3-3. A7003の耐食性を向上させる方法
A7003合金の耐食性をさらに向上させるためには、アルマイト処理や他の表面処理を施すことが有効です。これにより、酸化皮膜が強化され、過酷な環境下でもさらに優れた耐食性を発揮します。また、合金の成分や加工方法を調整することでも耐食性を向上させることが可能です。
4. アルミニウムの強度や特性の比較
4-1. A7003と他のアルミニウム合金の比較
A7003合金は、その機械的特性において、特に強度と耐食性に優れた性能を発揮します。例えば、A6061合金は加工性に優れていますが、A7003ほどの強度はありません。A7075は、航空機用途に適した強度を持っていますが、A7003はその強度と軽さのバランスから自動車や機械産業にも適しています。A7003の特徴としては、引張強度、降伏強度が高く、構造物として非常に優れた強度を持ちつつ、他の合金に比べて優れた耐食性を誇ります。
4-2. 軽金属の特性と用途の違い
軽金属(アルミニウム、マグネシウム、チタンなど)は、その名の通り軽量であり、機械的特性において高い強度を維持しつつ、加工しやすいという特徴があります。これにより、自動車、航空機、建設、家電など、軽量化が求められる分野で幅広く利用されています。アルミニウムは特に耐食性に優れ、海洋環境などでも利用されます。マグネシウムは更に軽量ですが、耐食性に課題があるため、特定の用途で限定的に使用されます。チタンは非常に高い強度を誇りますが、コストが高く、加工も難しいため、特殊な高性能用途に使われます。
4-3. アルミニウム合金の選定基準
アルミニウム合金を選定する際には、強度、耐食性、加工性、コストなど、さまざまな要因を考慮する必要があります。例えば、構造用途においては高強度の合金が求められ、耐食性が重要な場合は海水環境などで利用されるA7003のような合金が選ばれます。さらに、加工性が求められる場合には、A6061などの加工が容易な合金が選ばれることがあります。用途や環境条件に応じて、最適なアルミニウム合金を選定することが大切です。
5. 軽金属の特性や用途について
5-1. 軽金属の一般的な特性
軽金属は、低密度であるため非常に軽量であり、機械的強度を持ちつつも、重量が制限される必要がある用途に適しています。特に、アルミニウム合金は軽量で加工しやすく、耐食性も優れているため、航空機や自動車の部品に使用されることが多いです。さらに、軽金属は電気や熱の導電性も良好で、電子機器や熱交換器などにも使用されています。
5-2. 軽金属の産業用途
軽金属は、航空機、宇宙開発、自動車、電気機器、建築、医療機器など、さまざまな産業で使用されています。航空機や自動車では、燃費向上や機体強度の確保、軽量化が重要な要素であり、軽金属の需要が高いです。また、軽金属はその優れた加工性や強度から、パイプや構造部品などにも利用されています。さらに、アルミニウムはリサイクル性にも優れており、環境への影響を軽減しながら利用が可能です。
6. A7003の具体的な使用方法や適用例
6-1. A7003の使用例
A7003は、その高強度と耐食性の特性を活かして、自動車部品や機械構造物、建設機械、航空機部品などに使用されます。特に、軽量化が求められる構造物や耐腐食性が重視される部品において、その特性が活かされています。また、海洋環境に曝される部品や、過酷な温度変化のある環境での利用も可能です。
6-2. A7003の適用分野
A7003は、特に自動車、建設機械、機械構造物などの分野で活用されています。自動車産業では、燃費改善のために軽量化が求められる部品や、エンジン部品、車体フレームに使用されます。建設機械では、耐久性と強度が求められる部品に使用され、機械部品としてもその強度が活かされています。
6-3. A7003の加工方法
A7003は、比較的加工しやすい合金であり、切削加工、押出し加工、溶接などが行いやすいです。特に、押出し加工では、薄い部品や複雑な形状を容易に作ることができます。溶接性に関しても優れており、特にアルゴンアーク溶接(TIG)などが適しています。加工中には、適切な冷却処理を行うことで、表面処理の品質が向上します。
まとめ
A7003アルミニウム合金は、高強度で軽量な特性を持ち、主に航空機やスポーツ機器に使用されます。優れた耐食性を備え、自然環境や化学薬品に対しても高い抵抗力を示します。熱処理による強度向上が可能で、成形性も良好です。これらの特性から、幅広い産業での利用が期待されています。
アルミニウムA7204の機械的性質と耐食性について徹底解説
「A7204という材料について、詳細に知りたいけれど、どこから情報を得ればいいのか分からない…」そんなお悩みを抱えている方へ。このガイドでは、A7204の持つ機械的性質や、その優れた耐食性について徹底的に解説します。
A7204は、特に工業や建築分野で広く利用される合金であり、その特性を理解することは、素材選びや設計において非常に重要です。この記事では、A7204の基本情報から始まり、機械的性質や耐食性の具体的なデータ、さらには実際の応用例に至るまで、幅広く取り扱います。
もしあなたが、A7204の特性を理解し、ぜひ活用したいと考えているなら、このガイドはあなたのためのものです。素材選びにおける正しい知識は、プロジェクトの成功を大きく左右します。さぁ、一緒にA7204の世界を深く掘り下げていきましょう!
1. A7204 機械的性質 耐食性の概要
1-1. A7204合金とは
A7204はアルミニウム合金の一種で、特に強度と耐食性に優れた特性を持ち、航空機や構造部品、船舶など、軽量化と高い強度が求められる用途に広く使用されています。主にアルミニウムに銅、マグネシウム、マンガンなどの合金元素が含まれており、これらの成分が機械的特性と耐食性に貢献しています。
1-2. A7204合金の機械的特性
A7204合金は、高強度を持ちながらも比較的良好な加工性を有します。主要な機械的特性としては以下が挙げられます:
- 引張強度: 約470 MPa程度
- 降伏強度: 約340 MPa程度
- 硬度: B90以上
これにより、構造的に高い強度が要求される部品や機械の素材として非常に適しています。
2. A7204 機械的性質 耐食性に関する詳細
2-1. A7204合金の強度
A7204合金は、アルミニウム合金の中でも高い強度を誇ります。特に機械的負荷がかかる環境で使用されることが多いため、その引張強度や降伏強度が重要視されます。引張強度は約470 MPaであり、これは航空機などの構造部品として十分な強度を提供します。
2-2. A7204合金の比重
A7204合金の比重は、約2.8 g/cm³です。これはアルミニウム合金の中では平均的な値であり、軽量化が求められる用途にも対応可能です。比較的軽量でありながら高い強度を発揮するため、航空機や車両部品での使用に適しています。
2-3. A7204合金の耐食性の評価
A7204合金は、特に耐食性においても優れた特性を持っています。アルミニウム合金は一般的に優れた耐食性を持つものの、A7204は銅成分が含まれているため、耐食性が多少影響を受けます。しかし、適切な表面処理(例えば、陽極酸化処理)を施すことで、さらに高い耐食性を発揮することができます。特に、海洋環境や湿気の多い環境でも使用が可能です。
3. A7204合金の切削性について
3-1. 切削性の重要性
切削性は、金属材料を加工する際に非常に重要な特性です。特に精密部品や複雑な形状を作成するためには、材料が適切に切削可能であることが求められます。A7204合金は、高い強度と良好な耐食性を持っていますが、切削性の面でもその特性が影響します。切削性が良好であれば、加工精度が高く、仕上がりの良さや作業効率が向上します。
3-2. A7204合金の切削性の特徴
A7204合金は、比較的硬度が高いため、切削中に工具の摩耗が早く進むことがあります。特に、アルミニウムの中でも強度が高いため、切削には注意が必要です。適切な切削速度や工具の選定が求められます。合金中の銅やマグネシウム成分が切削性に影響を与えるため、加工時には冷却液や潤滑剤を適切に使用することが推奨されます。一般的に、適切な切削条件を守ることで、A7204合金は効率よく加工できます。
4. A7204合金の用途と使い方
4-1. A7204合金の一般的な用途
A7204合金は、その高強度と耐食性から、航空機や自動車部品、船舶、構造物の部品に多く使用されています。特に、軽量化が求められ、同時に高強度も必要な場合に最適な素材です。具体的には、航空機の構造部品や、耐食性が要求される海洋機器、精密機械部品などで使用されます。また、高い耐久性が求められる産業機器にも適用されます。
4-2. A7204合金の選定基準
A7204合金を選定する際には、主に以下のポイントを考慮する必要があります:
加工性: 切削性がやや難しいため、加工時の条件や工具選定に注意が必要です。精密加工が求められる場合には、加工条件に適応した選定が求められます。
強度要求: 高強度が求められる用途に適しているため、構造部品や航空機部品での使用に最適です。
耐食性: 海洋環境や湿気の多い場所で使用される場合、優れた耐食性が発揮されるため、これらの環境でも問題なく使用できます。
まとめ
アルミニウムA7204は、高強度と優れた機械的性質を持ち、特に航空機や自動車部品に適しています。耐食性は良好ですが、特に塩水環境では注意が必要です。適切な表面処理を施すことで、耐食性を向上させることが可能です。これにより、長寿命を実現し、信頼性の高い材料としての評価を得ています。
アルミニウム【A1070材料の特性】機械的性質と耐食性とは?
「A1070材料について深く知りたいけれど、その特性や用途が分からない……」そんな悩みを抱えている方はいませんか?そのようなあなたのために、今回はA1070材料の機械的性質と耐食性について詳しく解説します。
A1070は、アルミニウムの一種として知られる重要な材料で、様々な産業で幅広く利用されています。特に、優れた機械的性質と耐食性を持つことで知られ、多くの場面で選ばれています。この材料の特性を理解することは、設計や製造の現場での適切な選択を行うために非常に重要です。
この記事では、A1070の基本的な特性から、その機械的性質と耐食性の詳細、さらに実際の使用例までを幅広くカバーします。材料選定において重要な知識を身につけることで、あなたのプロジェクトがより成功することを願っています。さあ、A1070の世界を一緒に探り始めましょう!
1. A1070の機械的性質についての理解を深める
1-1. A1070の基本的な機械的性質
A1070は純度の高いアルミニウム合金で、以下のような基本的な機械的特性を持っています:
- 引張強度: 約 130 MPa
- 降伏強度: 約 60 MPa
- 伸び率: 約 25%
A1070は高い延性と加工性を有しており、強度は比較的低いものの、曲げや加工が容易です。耐摩耗性や耐食性が良好であり、主に加工が必要な用途に適しています。
1-2. 引張強度と降伏強度の比較
A1070の引張強度と降伏強度は、一般的に低い値となっており、これは純度の高いアルミニウム合金の特徴です:
- 引張強度: 約 130 MPa
- 降伏強度: 約 60 MPa
引張強度が降伏強度を上回るため、伸びやすく、加工がしやすいですが、高い強度が必要な用途には不向きです。
1-3. A1070の硬度と靭性
A1070は硬度が低く、加工や成形が容易です。主な硬度は Brinell硬度 約 20-30 HB です。そのため、金型や精密部品には不向きですが、靭性に優れ、亀裂が入っても破断しにくい特性を持っています。加えて、他のアルミニウム合金と比べて非常に柔軟性があります。
2. A1070と他のアルミニウム合金の違い
2-1. A1070とA6061の比較
A1070とA6061は、どちらもアルミニウム合金ですが、特性にいくつかの違いがあります:
- A1070: 高純度で延性が高く、耐食性が良好ですが、強度は低めです。
- A6061: A1070よりも高い強度を持ち、熱処理により強度を向上させることができます。耐食性や加工性も優れ、構造部材や機械部品に広く使用されます。
2-2. A1070とA7075の特性の違い
A1070とA7075は、強度や用途が大きく異なります:
- A1070: 高純度アルミニウムであり、主に加工しやすさと耐食性が求められる場合に使用されます。
- A7075: 高強度で、航空機や軍事用途に適しており、A1070よりも優れた機械的特性と耐摩耗性を誇ります。
2-3. 用途に応じた選択基準
A1070は、低強度が要求される用途や、優れた耐食性や延性が必要な場合に最適です。具体的な用途には以下のようなものがあります:
- 精密加工部品: 高純度が求められる場合。
- 耐食性を重視する部品: 特に湿気の多い環境での使用に適しています。
3. A1070の耐食性に関する情報
3-1. A1070の耐食性のメカニズム
A1070は、純度が高いため、耐食性に優れています。アルミニウムは表面に酸化アルミニウムの薄い層を形成し、この酸化膜が腐食から保護します。これにより、海洋環境や湿度が高い環境でも耐食性が保持されます。
3-2. 環境条件が耐食性に与える影響
環境の影響として、特に以下の要因がA1070の耐食性に影響を与えます:
- 湿度: 高湿度環境では、表面に水分が多く集まり、腐食のリスクが増加します。
- 塩分: 海水や塩分を含む空気は腐食を加速させるため、コーティングや防食処理が必要です。
3-3. 耐食性を向上させる処理方法
A1070の耐食性を向上させる方法には、以下のような処理が有効です:
コーティング: 塗装や他の防食材料を使用して、外部環境からの腐食を防ぐ方法。
アルマイト処理: アルミニウム表面に酸化皮膜を形成し、耐食性を高める方法。
4. A1070の化学成分や特性を比較
4-1. A1070の化学成分の詳細
A1070は、ほぼ純度100%のアルミニウム合金で、主に以下の成分で構成されています:
- アルミニウム (Al): 99.70%以上
- 鉄 (Fe): 最大 0.30%
- シリコン (Si): 最大 0.10%
- 銅 (Cu): 最大 0.05%
- マンガン (Mn): 最大 0.05%
- マグネシウム (Mg): 最大 0.05%
- クロム (Cr): 最大 0.05%
- その他: 微量の他元素
この化学成分により、A1070は高い耐食性と延性を持つ特性を示します。純度が高いため、加工性に優れ、表面仕上げも美しく、特に電気・電子機器の部品に適しています。
4-2. 他のアルミニウム合金との成分比較
A1070は、他のアルミニウム合金(例:A6061、A7075)と比較して、特に高い純度を誇ります。以下はその成分比較です:
- A1070 vs A6061:
- A6061は、マグネシウムとシリコンを主成分とし、機械的特性(強度や硬度)がA1070より高いです。
- A1070は純度が高く、加工性と耐食性に優れ、強度が求められない用途に向いています。
- A1070 vs A7075:
- A7075は非常に高い強度を持つ合金で、航空機や軍事用途に使用されます。マグネシウム、亜鉛が主成分で、A1070よりも強度と耐摩耗性に優れていますが、加工性はA1070に劣ります。
4-3. 特性に基づく用途の選定
A1070はその化学成分と特性に基づき、主に以下の用途に適しています:
- 電子機器: 高い耐食性と加工性が求められる電子機器の部品(ケース、放熱板など)。
- 食品・医療機器: 耐食性が要求される環境で使用される部品(容器、パイプ)。
- 精密機器の部品: 高い延性と加工性が求められる精密部品。
5. A1070の販売や規格についての詳細
5-1. A1070の規格と認証
A1070は、以下の規格と認証に準拠しています:
- JIS規格: 日本工業規格(JIS)におけるアルミニウム合金の規格に適合。
- ASTM規格: 米国のASTM規格でも、A1070は同様に認証されています。
- ISO規格: 国際標準化機構(ISO)によるアルミニウム合金の基準にも準拠。
これにより、A1070は信頼性の高い素材として、さまざまな産業で使用されています。
5-2. A1070の市場での流通状況
A1070は、純度が高く加工しやすいため、多くの国際市場で流通しています。特に日本、アメリカ、欧州では、以下の分野で広く流通しています:
- 電子機器市場: コンシューマーエレクトロニクスの部品。
- 輸送機器市場: 軽量化が求められる部品。
- 建築・構造市場: 耐食性が要求される部品。
その需要は、特に耐食性と加工性が重視される産業において増加しています。
まとめ
A1070材料は、高い機械的性質と優れた耐食性を持つアルミニウム合金です。軽量でありながら強度があり、特に耐食性に優れているため、航空機や化学工業などの厳しい環境での使用に適しています。この特性により、長寿命を実現し、メンテナンスコストを削減します。
A2017アルミニウム合金の機械的性質と耐食性の徹底解説
「A2017アルミニウム合金について詳しく知りたいけれど、どこから手を付ければよいのかわからない……」そんな悩みを抱えている方に向けて、この記事ではA2017アルミニウム合金の機械的性質と耐食性に関する徹底解説をお届けします。
A2017合金は、その優れた機械的性質から航空機や自動車の部品など、様々な産業で広く使用されています。しかし、合金の特性を理解することは、適切な用途選定や使用方法において非常に重要です。この記事では、A2017の基本的な機械的性質や耐食性について詳しく掘り下げ、合金の魅力を余すところなく紹介します。
あなたがA2017アルミニウム合金の利用を検討しているエンジニアであったり、材料科学に興味を持つ学生であったりするなら、ぜひこのガイドを参考にしてください。これを読めば、A2017合金が持つ力強さとその特性を十分に理解し、実際のプロジェクトに役立てることができるでしょう。さあ、一緒にA2017アルミニウム合金の世界を探求していきましょう!
1. A2017の特性と用途
1-1. A2017の基本特性
A2017は、銅を主成分とするアルミニウム合金で、強度と耐摩耗性に優れています。ジュラルミンの一種として知られ、航空機や軍事用途に広く使用されています。A2017の特徴的な性能は以下の通りです:
- 高強度: 特に航空機や航空エンジン部品に適しています。
- 耐摩耗性: 摩耗に強く、長期間の使用にも耐えられます。
- 耐食性: 比較的耐食性が低いため、適切なコーティングが必要です。
1-2. A2017の主な用途
A2017は、その高い強度と耐摩耗性を活かして、主に以下の分野で使用されます:
- 航空機産業: 構造部材やエンジン部品に使用。
- 自動車産業: 高強度を必要とする部品。
- 軍事用途: 軽量で強度が必要な部品。
2. A2017と他のジュラルミンの比較
2-1. A2017とA2024の違い
A2017とA2024はどちらも銅を主要な成分としたアルミニウム合金ですが、いくつかの違いがあります:
- A2017は、強度と耐摩耗性に優れていますが、耐食性がやや低いです。主に航空機や自動車の部品で使用されます。
- A2024は、A2017に比べて若干強度は低いものの、より高い耐食性を持っています。航空機の構造部品に適しています。
2-2. A2017とA7075の比較ポイント
A2017とA7075は、いずれも高強度のアルミニウム合金ですが、いくつかの重要な違いがあります:
- A2017は、主に銅を基にしており、優れた強度と耐摩耗性を持っていますが、耐食性は低いです。
- A7075は、亜鉛を主要成分としており、非常に高い強度を持つ一方で、A2017よりも耐食性が高いです。特に航空機や軍事用途に向いています。
3. A2017の機械的性質と耐食性
3-1. A2017の機械的性質の具体的数値
A2017の機械的性質は、以下の通りです:
- 引張強度: 約 470 MPa
- 降伏強度: 約 390 MPa
- 伸び率: 約 10%
これにより、高い強度と耐摩耗性を発揮しますが、延性は若干低くなります。
3-2. A2017の耐食性の特徴
A2017は、銅を多く含むため耐食性が比較的低いです。特に、腐食性の高い環境では適切な防護措置(コーティングや表面処理)が必要です。海洋環境や湿気の多い環境では、耐食性が問題となることがあります。
4. A2017の選定基準
4-1. 材料選定におけるA2017の適性
A2017は、特に以下の条件下で最適な材料です:
- 高強度が必要な場合: 特に構造部品やエンジン部品など、高い強度が求められる用途。
- 摩耗に強い材料が必要な場合: 長期にわたる摩擦や摩耗が予想される部品に適しています。
4-2. A2017を選ぶ際の考慮点
A2017を選定する際には、以下の点を考慮する必要があります:
- 耐食性: 銅を多く含んでいるため、腐食環境においては適切なコーティングや処理が必要です。
- 加工性: 高強度により加工が難しく、加工時に十分な注意が必要です。
5. A2017の強度と比重に関するデータ
5-1. A2017の強度データ
A2017の強度に関するデータは以下の通りです:
- 引張強度: 470 MPa
- 降伏強度: 390 MPa
- 硬度(Brinell): 約 120 HB
これらのデータは、A2017が非常に高い強度を持つことを示しています。
5-2. A2017の比重とその影響
A2017の比重は約 2.77 で、アルミニウム合金としては標準的な値です。この比重の特性により、軽量でありながら高い強度を持つため、航空機や高強度が求められる部品に適しています。
まとめ
A2017アルミニウム合金は、高強度でありながら軽量な特性を持ち、航空機や自動車部品に広く使用されています。耐食性は一般的に良好ですが、腐食環境下では注意が必要です。熱処理による強度向上が可能で、加工性も優れています。
アルミニウムA2024の機械的性質を徹底分析!耐食性を高めるポイント
アルミニウムA2024は、その優れた機械的性質から航空機や高強度構造物で広く使用されていますが、耐食性の面ではいくつかの課題も抱えています。「A2024の耐食性をどう高めるのか?」この問いに対する答えを探している方も多いことでしょう。
この記事では、A2024の機械的性質について徹底的に分析し、特に耐食性を向上させるためのポイントを詳しく解説します。もし、アルミニウムA2024の特性に興味があり、その利点を最大限に活かしたいと考えているなら、この記事はあなたにとって価値ある指南となることでしょう。
強度と軽さを兼ね備えたA2024を理解し、その特性を活用することで、あなたのプロジェクトや製品が一層魅力的になることを期待しています。さあ、一緒にA2024の魅力の世界に飛び込んでいきましょう!
1. A2024の機械的性質についての基礎知識
1-1. A2024の強度と硬度
A2024は、アルミニウム合金の中でも非常に高い強度を持つ材料です。特に航空機部品や高負荷部品に使用されることが多く、その強度は通常のアルミニウム合金に比べて大幅に優れています。強度の特性としては、引張強度が高く、圧縮や引っ張りなどの力を耐える能力が高いです。
- 引張強度: 約470 MPa程度
- 降伏強度: 約325 MPa程度
- 硬度: 約120 HB
この高い強度により、A2024は高負荷がかかる部品に適していますが、同時に硬度が高いため、加工が難しいという欠点もあります。
1-2. A2024の延性と靭性
A2024は高強度に加えて、適度な延性と靭性も備えていますが、完全な延性を求める用途には他の合金に劣ります。延性は材料が引き延ばされるときに破断することなくどれだけ伸びるかを示し、靭性は衝撃や急激な力を受けたときの耐久性に関係します。A2024は、高強度のため、延性や靭性がやや低く、衝撃に弱い場合があります。
- 延性: 一般的に低め
- 靭性: 衝撃や高負荷に弱い場合がある
これらの特性を考慮し、A2024は高強度が求められつつも、衝撃や振動が少ない環境に適していると言えます。
1-3. A2024の疲労特性
A2024は疲労強度においても優れた特性を持っています。特に繰り返し荷重がかかる環境下では、その耐久性を発揮します。疲労特性は、材料が繰り返し負荷に晒される場合の耐久性を示し、A2024は航空機部品や構造部材などの用途において長期間使用に耐える能力を持っています。
- 疲労強度: 約150 MPa~200 MPa程度
- 疲労限度: 繰り返し荷重に対して高い
これにより、A2024は航空機や自動車部品など、高頻度で繰り返し荷重を受ける部品に適しています。
2. A2024の耐食性に関する詳細
2-1. A2024の耐食性のメカニズム
A2024は、耐食性に関しては比較的脆弱な部分を持っています。特に、クラックが生じやすく、腐食のリスクが高いです。これは、銅が主成分であるため、塩水や湿気などの影響を受けやすいからです。しかし、適切な表面処理やコーティングを施すことで、耐食性を向上させることができます。
- クラック腐食: 高い銅含有量により、特に湿気や塩水環境に弱い
- 表面処理: アルマイト処理や塗装で耐食性向上
2-2. 環境条件がA2024の耐食性に与える影響
環境条件がA2024の耐食性に大きな影響を与えることがあります。特に、塩水や高湿度の環境では腐食が進行しやすく、長期間にわたって耐久性を確保するためには、適切な保護が必要です。乾燥した環境や低湿度条件では、比較的耐食性が高くなりますが、それでも長期的な使用には注意が必要です。
- 塩水環境: 高い腐食リスク
- 乾燥環境: 耐食性が向上
2-3. A2024の耐食性を向上させる方法
A2024の耐食性を向上させる方法にはいくつかあります:
- アルマイト処理: 表面に酸化皮膜を形成し、耐食性を大幅に向上させる。
- 塗装: 耐食性の高い塗料を使用して、外部の腐食因子から保護する。
- 合金の改良: 例えば、銅の含有量を抑えることで耐食性を改善する方法もあります。
これらの方法を組み合わせることで、A2024の耐食性を大きく改善することが可能です。
3. A2024の特性を活かした適切な用途
3-1. 航空機産業におけるA2024の利用
A2024は、その高い強度と疲労特性から航空機産業で広く使用されています。特に、航空機のフレームや翼、エンジン部品に使用され、これらの部品に求められる高強度を提供します。また、耐腐食性の向上を図った表面処理を施すことで、過酷な環境にも耐えることができます。
3-2. 自動車産業でのA2024の応用
A2024は、自動車産業でも軽量化と高強度が求められる部品に使用されます。特に、高速走行時に高負荷がかかるエンジン部品やシャシーに適しています。また、衝撃耐性が求められない部品に使用することで、その強度を活かすことができます。
3-3. その他の産業におけるA2024の活用事例
A2024は航空機や自動車以外でも、例えば軍事産業や高負荷を受ける構造部品に使用されています。耐腐食性を高める処理を施すことで、過酷な環境でも長期間にわたって安定した性能を発揮します。
4. アルミニウムの種類と特徴
4-1. アルミニウム合金の分類
アルミニウム合金は、主に以下の5つの系統に分類されます:
- 1xxx 系(純アルミニウム系): 純度が高く、耐食性が良好で加工性も優れていますが、強度は低いです。
- 2xxx 系(銅系アルミニウム合金): 高強度が特徴ですが、耐食性が低いため、主に航空機や構造部材に使用されます。
- 3xxx 系(マンガン系アルミニウム合金): 良好な耐食性と中程度の強度を持つため、屋外や化学産業の部品に多く使用されます。
- 5xxx 系(マグネシウム系アルミニウム合金): 高い耐食性と良好な溶接性を持ち、海水環境や船舶に使われます。
- 7xxx 系(亜鉛系アルミニウム合金): 非常に高い強度を誇り、航空機や軍事用途などに使用されます。
4-2. 各種アルミニウム合金の特性比較
アルミニウム合金の主な特性は以下のように異なります:
- 1xxx系: 高い耐食性と加工性、低強度。用途例:飲料缶、包装材、電気導体。
- 2xxx系: 高強度、耐食性が低い。用途例:航空機部品、構造材料。
- 3xxx系: 中強度、良好な耐食性、加工性。用途例:化学機器、冷蔵庫部品、屋根材。
- 5xxx系: 高い耐食性、良好な溶接性。用途例:船舶部品、海洋環境での用途。
- 7xxx系: 非常に高い強度、やや低い耐食性。用途例:航空機部品、軍事用途。
4-3. 軽量化設計におけるアルミニウムの利点
アルミニウム合金は、軽量でありながら強度が高く、構造物の軽量化に貢献します。これにより、以下の利点があります:
- エネルギー効率の向上: 軽量化により、移動エネルギーが少なくて済み、燃料消費を抑制できます。
- 耐腐食性: アルミニウム合金は耐腐食性に優れており、長寿命を実現します。
- 加工性: 様々な加工方法に対応し、複雑な形状の部品を製造可能です。
アルミニウム合金は、軽量化設計において非常に重要な役割を果たしています。
5. A2024合金の加工方法とポイント
5-1. A2024の加工特性
A2024は、非常に高い強度を持つ合金ですが、その硬度が高いため、加工が難しい場合があります。特に切削加工や機械加工を行う際には、適切な工具と技術を使用することが重要です。A2024の加工には以下の特性があります:
- 切削性: 高強度ゆえに、切削が難しく、ダメージを最小限に抑えるために刃物の温度や速度管理が必要です。
- 溶接性: 溶接が難しいため、溶接時にクラックや変形が生じる可能性があります。適切な前処理と後処理が求められます。
5-2. 加工時の注意点
A2024を加工する際には、以下の点に注意が必要です:
- 適切な工具選定: 高強度に適した切削工具を使用し、刃物の摩耗を抑えます。
- 冷却・潤滑剤の使用: 加工中に熱が発生しやすいため、冷却剤や潤滑剤を使用して熱を管理します。
- 加工速度の調整: 加工速度が速すぎると工具の摩耗が早く、加工精度が低下するため、適切な速度で加工を行うことが重要です。
5-3. A2024の熱処理とその効果
A2024は、熱処理によって強度や硬度を大きく改善することができます。熱処理の主な方法には以下があります:
- 時効硬化: 特定の温度で保持し、冷却することで硬度と強度を向上させます。これにより、A2024の機械的性質が最適化され、航空機などの高強度が求められる部品に適します。
- 溶体化処理: 高温で溶解し、冷却することで内部の結晶構造を均一にし、後の時効硬化で強度を高めます。
これらの熱処理を適切に行うことで、A2024合金の性能を最大限に引き出すことができます。
まとめ
アルミニウムA2024は、高強度で優れた疲労特性を持つ合金ですが、耐食性は課題です。耐食性を高めるためには、表面処理(陽極酸化や塗装)や合金成分の最適化が重要です。また、適切な保管や使用環境の管理も耐食性向上に寄与します。これらの対策を講じることで、A2024の性能を最大限に引き出せます。
A7075アルミニウムの機械的性質と耐食性を徹底解説
「A7075アルミニウムについて学びたいけれど、機械的性質や耐食性について詳しく知るのは難しいと感じていませんか?」そんなあなたのために、私たちはこの「A7075アルミニウムの機械的性質と耐食性を徹底解説」というガイドを用意しました。
この文章は、以下のような方に向けています。
- A7075アルミニウムの基本的な特性が知りたい。
- この素材がどのような機械的性質を持っているのか興味がある。
- 耐食性について詳しく理解し、実際の応用に役立てたい。
- A7075アルミニウムを選ぶ際の具体的なポイントを知りたい。
A7075アルミニウムは、その高い強度と軽量性から多くの産業で利用されていますが、耐食性に関する課題も抱えています。そこで、本記事では、このアルミニウム合金の機械的性質や耐食性を詳しく解説し、実際の使用に役立つ情報をお届けします。あなたの知識を深め、この素材の魅力を最大限に引き出しましょう。
1. アルミニウムA7075の特性と用途
1-1. A7075アルミニウムの基本特性
A7075は、アルミニウム合金の中で最も強度が高いものの一つです。この合金は、主に亜鉛を中心に、少量のマグネシウム、銅、およびクロムを含み、高強度、高靭性を持ちます。引張強度が非常に高く、航空機や軍事用途など、高い強度が求められる環境に適しています。また、硬度も高く、軽量でありながら、耐久性にも優れています。
1-2. A7075の適用分野と用途
A7075は、特に強度が重要な構造部品に使用されます。主な用途は以下の通りです:
- 航空宇宙産業: 機体の構造部品や航空機のフレーム、エンジン部品など
- 軍事産業: 弾薬、戦闘機、兵器の構造部品
- スポーツ機器: 高性能自転車のフレーム、スキー板、ゴルフクラブなど
- 自動車産業: 高強度が必要な車両の部品やシャシー
その優れた強度と軽量性が求められる場所で活躍しています。
2. アルミニウムA7075の機械的性質と耐食性
2-1. A7075の機械的性質の詳細
A7075の引張強度は非常に高く、最大で約570 MPaに達します。これは多くの鋼材と同等またはそれを上回る強度です。降伏強度は約500 MPa程度であり、特に高負荷に耐える必要がある部品に適しています。硬度は高く、非常に強固で耐久性がありますが、他のアルミニウム合金と比べて延性はやや低いです。
2-2. A7075の耐食性について
A7075は強度が高い一方で、耐食性は他のアルミニウム合金に比べてやや劣ります。特に海水や湿度の高い環境では、表面に腐食が起こりやすい傾向があります。耐食性を高めるためには、表面処理(アルマイト処理やコーティング)を施すことが一般的です。これにより、耐食性を向上させ、過酷な環境でも長期間使用可能となります。
3. アルミニウムA7075の加工方法と注意点
3-1. A7075の加工技術
A7075は、その高い強度と硬度から、加工が難しいアルミニウム合金の一つです。加工技術としては、主に以下の方法が使用されます:
- 切削加工: 高速回転工具を使用して、機械的に削る方法です。A7075は硬いため、刃物の選定や切削条件に注意が必要です。チップの摩耗を防ぐため、適切な冷却材を使用することが重要です。
- フライス加工: 機械の回転を利用して精密に削り取る方法です。切削力が強いため、高精度な設備が必要となります。
- 旋盤加工: 丸形の部品を加工する場合に使用されます。切削速度と回転数を調整して、高精度な加工が可能です。
加工中に発生する熱や摩擦を抑えるため、冷却液の使用が必須です。これにより、工具の寿命を延ばし、加工精度を保つことができます。
3-2. 加工時の注意点とベストプラクティス
A7075の加工には、いくつかの注意点とベストプラクティスがあります:
- 適切な切削工具の選定: 高強度の合金には、耐摩耗性の高い切削工具を使用することが重要です。通常、炭化物工具やコーティング工具が適しています。
- 冷却剤の使用: A7075は熱を発生しやすいため、加工中に冷却剤を使用して工具の温度を管理します。冷却剤が不足すると、加工精度が低下したり、工具が早期に摩耗したりします。
- 低速での加工: 高い強度を持つため、過度な負荷をかけず、比較的低い回転数と進行速度で加工を行うのがベストです。
- 加工時の引っかかり防止: 高い硬度により、切削中に引っかかりが発生しやすいため、切削抵抗を最小限に抑える工夫が必要です。
これらの注意点を守ることで、精度の高い加工と高い耐久性を実現することができます。
4. アルミニウムA7075と他のアルミニウム合金の比較
4-1. A7075と他のアルミニウム合金の特性比較
A7075は、他のアルミニウム合金と比較して非常に高い強度を持っています。以下は、A7075と一般的なアルミニウム合金の比較です:
- A7075 vs A6061: A7075はA6061よりも強度が高く、航空機の構造部品や軍事用途に適しています。しかし、A6061は加工性が良く、耐食性も高いため、一般的な構造物や車両部品に使用されることが多いです。
- A7075 vs A5052: A5052は耐食性に優れた合金ですが、A7075に比べて強度は低いです。A7075はより過酷な環境や負荷の高い用途に向いています。
- A7075 vs A2024: A2024も航空機用途でよく使用されますが、A7075の方がより強度が高いです。A2024は若干、耐食性が劣る場合があります。
4-2. A7075の選定基準とポイント
A7075を選定する際のポイントは以下の通りです:
- 強度重視の用途: 高い引張強度を必要とする部品、特に航空機や軍事関連の構造部品に最適です。
- 耐食性が重要でない場合: A7075は耐食性が他のアルミニウム合金に比べて劣るため、耐食性が求められる用途には不向きです。
- 精密な加工が必要: 高強度により加工が難しいため、適切な加工設備と技術が求められます。精密加工が可能な場合に選ばれることが多いです。
- 軽量化が求められる場合: 強度と軽量性を兼ね備えており、軽量化が求められる構造部品に最適です。
これらの基準に基づいて、A7075を適切に選定し、使用することが重要です。
まとめ
A7075アルミニウムは、高い強度と優れた耐食性を兼ね備えた合金です。主に航空機や高負荷構造物に使用され、熱処理によってその特性が向上します。耐食性は良好ですが、適切な表面処理が推奨され、環境条件に応じた管理が重要です。