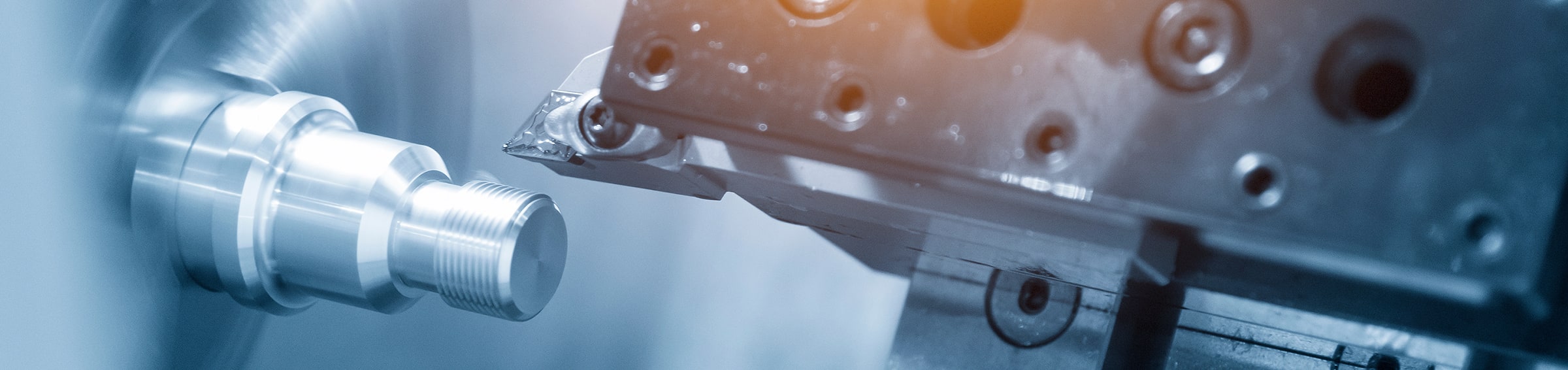
加工技術 column
プロが教える!アルミニウム切削加工の成功のための重要なポイント
アルミニウム切削加工に挑戦したいけれど、どこから手を付ければいいのかわからない…そんな悩みを抱えている方はいませんか?そのような方々のために、このガイドを用意しました。
この記事では、アルミニウム切削加工の基本から成功のための重要なポイントまで、幅広く解説していきます。アルミニウムは軽量でありながら強度も高く、様々な産業で利用されている素材です。しかし、適切な技術や知識がなければ、切削加工は思うようにいかないこともあります。
「アルミニウム切削加工にはどんな技術が必要なのか?」、「最適な工具の選び方は?」、「注意すべき加工条件やポイントは?」これらの疑問にお答えし、初心者でも安心して取り組める情報をお届けします。成功への第一歩を踏み出すために、ぜひこのガイドを参考にしてください。あなたの切削加工が成功することを願っています!
アルミニウム 切削加工 ポイント: 最適な工具選び
アルミニウムの切削加工では、適切な工具の選定が加工効率や仕上がりに大きく影響します。工具の種類や材質、選定時の注意点を押さえて、最適な切削条件を整えることが重要です。
アルミニウムに適した切削工具の種類
アルミニウムの切削加工においては、特に以下の工具がよく使用されます。
- エンドミル: 高速切削に適しており、溝加工や平面加工に使用されます。特にアルミニウムは切削しやすいため、適切なエンドミルを選ぶことが重要です。
- ドリル: 穴あけ作業に使用され、特にアルミニウムでは切削抵抗が少ないため、鋭い刃先のドリルを選ぶことが推奨されます。
- タップ: ネジ切り作業に使用します。アルミニウムは軽く、加工しやすいため、専用のタップを選択することで仕上がりが良くなります。
切削工具の材質とその特性
アルミニウムの切削には、工具の材質が大きく影響します。以下の材質が代表的です。
- 高速度鋼(HSS): 高速切削に適しており、耐摩耗性が高いですが、高温には弱い点があります。
- コーティング工具: チタン酸化物(TiN)やダイヤモンドコーティングなど、耐摩耗性を向上させるコーティングが施された工具は、アルミニウムのような軟らかい材料に有効です。
- 超硬工具: 超硬合金は耐摩耗性や耐熱性が高く、長時間の連続加工に向いています。
工具選定の際の注意点
- 切削速度: アルミニウムは軽い材料ですが、切削速度が速すぎると工具が早く摩耗します。適切な切削速度を選ぶことが重要です。
- 切削深さ: 切削深さを適切に設定しすぎると、工具に過度な負荷がかかり、表面品質に影響を及ぼすことがあります。
- 工具の刃先形状: 刃先が鈍っていると、切削性能が低下し、加工精度が悪化するため、刃先の形状や鋭さを保つことが大切です。
アルミニウム 切削加工 ポイント: アルミ合金の特性と加工方法
アルミニウム合金の種類に応じて、最適な加工方法は異なります。合金ごとの特性に合わせた加工方法を選ぶことが、加工品質と効率を高めるために重要です。
アルミ合金の種類と特性
アルミニウム合金は、大きく分けて以下のカテゴリに分類されます。
- 1xxx系(純アルミ): 純度が高く、耐食性に優れていますが、強度が低いため、加工しやすいです。
- 2xxx系(銅合金): 高い強度を持ち、航空機などに使用されますが、切削時には熱処理が必要となることが多いです。
- 6xxx系(マグネシウム・シリコン合金): より強度が高く、構造部材などに使われます。加工性が良いですが、温度管理が重要です。
合金ごとの最適な加工方法
- 1xxx系: 加工しやすく、通常の切削速度で問題なく加工できます。
- 2xxx系: 高強度が求められるため、冷却を十分に行いながら低速で切削する必要があります。
- 6xxx系: 中程度の強度を持ち、適切な工具選定と加工速度で加工しやすいです。加工中に適切な温度管理が求められます。
加工時の注意点とトラブルシューティング
- 熱変形: 高速切削時に熱変形が生じる場合があります。冷却方法の見直しや加工速度の調整が必要です。
- 切りくずの管理: 切りくずが詰まると、加工精度が低下するため、適切な切りくず処理が必要です。
- 工具の摩耗: 刃先の摩耗が進むと、加工品質が低下します。工具の交換時期を適切に判断しましょう。
アルミニウム 切削加工 ポイント: 熱管理と冷却方法
アルミニウムの切削加工において、熱の発生を効果的に管理することは非常に重要です。熱の発生を抑えることで、工具寿命の延長や加工精度の向上が期待できます。
切削中の熱発生のメカニズム
切削中には摩擦熱や圧縮熱が発生します。アルミニウムは比較的熱伝導性が良いため、熱が工具やワークピースに均等に分散されますが、高速切削では熱が集中し、工具の摩耗が早く進行することがあります。
効果的な冷却方法の選定
- エア冷却: 高速切削時に使用されることがあり、熱の蓄積を防ぎますが、冷却効果が限られることがあります。
- 液体冷却: 切削液や油を使用することで、摩擦を減らし、温度上昇を抑えることができます。特に切削中の熱を効率よく取り除くことが可能です。
冷却剤の種類と使用方法
油性切削液: 油性の冷却液は、より強力な潤滑効果を提供し、高負荷の加工に適しています。使用後の清掃が重要です。
水溶性切削液: 通常はアルミニウムの加工に最も使用されます。冷却と潤滑の効果があり、洗浄も簡単です。
アルミニウム 切削加工 ポイント: 加工精度の向上
アルミニウムの切削加工において、精度の高い仕上がりを実現することは非常に重要です。加工精度を向上させるための要因や技術、手法について理解を深めることが必要です。
加工精度を左右する要因
加工精度に影響を与える主な要因には、以下のものがあります。
- 工具の状態: 刃先が鈍ると、加工精度が低下します。工具の摩耗を防ぐために、適切なメンテナンスや交換が求められます。
- 切削条件: 切削速度、切削深さ、送り速度などの切削条件が精度に直接影響します。過剰な切削力や不適切な速度は、精度を悪化させる原因となります。
- ワークピースの固定: ワークピースの固定が不安定だと、振動や位置ズレが生じ、加工精度が低下します。適切なクランプ方法を使用することが重要です。
精度向上のための技術と手法
精度向上を実現するためには、以下の技術や手法を取り入れることが有効です。
- 精密加工機の使用: 高精度な加工を行うためには、精密な加工機を使用することが基本です。特にCNC(コンピュータ数値制御)機械の使用が推奨されます。
- 最適な切削パラメータの設定: 切削条件を最適化し、適切な切削深さや速度、送り速度を選ぶことで、安定した加工精度を維持できます。
- 振動の抑制: 加工中の振動を抑えるために、機械の剛性を高めたり、ダンピング技術を使用したりすることが有効です。
測定と検査の重要性
加工精度を保証するためには、測定と検査が不可欠です。
- 測定機器の活用: 高精度な測定機器を使用して、加工後のワークピースを検査します。マイクロメーターや3D測定機などが一般的に使用されます。
- 定期的な検査: 定期的な検査を行い、工具や機械の状態をチェックすることで、精度の維持が可能になります。
アルミニウム 切削加工 ポイント: コスト削減のための効率的手法
効率的な手法を導入することで、アルミニウムの切削加工におけるコストを削減し、同時に生産性を向上させることが可能です。
コスト削減のためのプロセス改善
- 生産工程の最適化: 各加工段階での無駄を減らし、効率的な工程を設計することで、加工時間とコストを削減できます。
- 自動化の導入: 自動化設備を導入することで、作業員の負担を軽減し、加工精度の向上とコスト削減を実現します。
材料費の最適化
- 廃材削減: 材料の無駄を減らし、リサイクルを活用することで、材料費を削減できます。CAD/CAMの活用により、より効率的な切削パスを計算することが可能です。
- 適切な材料選定: 必要な強度や性能を考慮した材料を選ぶことで、過剰なコストを防ぎます。特に、低価格なアルミニウム合金を選定することも有効です。
生産性向上のための戦略
作業の標準化: 作業手順を標準化し、作業員のトレーニングを徹底することで、ミスや無駄な時間を削減します。
高効率の切削技術: 高速切削や高効率加工を導入することで、作業時間を短縮し、生産性を向上させることができます。
まとめ
アルミニウム切削加工の成功には、適切な工具選定、切削条件の最適化、冷却液の使用が不可欠です。切削速度や送り速度を調整し、加工後の表面仕上げにも注意を払うことで、高品質な仕上がりを実現できます。安全対策も忘れずに。
アルミニウム鋳造の基礎知識とその利点とは?
「アルミニウム鋳造ってどういうもの?その利点は何だろう?」そんな疑問を抱えているあなたのために、この記事を用意しました。アルミニウムは軽量でありながら耐久性が高く、さまざまな産業で広く利用されていますが、その加工方法の一つである鋳造には、実は多くの魅力が詰まっています。
アルミニウム鋳造は、部品の形状やサイズを柔軟にデザインできるため、エンジニアやデザイナーにとっては非常に有益な技術です。この記事では、アルミニウム鋳造の基本から、その利点、さらには実際の応用例について詳しく解説します。これを読めば、アルミニウム鋳造の世界に対する理解が深まり、あなた自身のプロジェクトやビジネスにどのように役立てることができるかが見えてくることでしょう。さあ、一緒にアルミニウム鋳造の魅力を探っていきましょう!
アルミニウム 鋳造の基本知識
アルミニウム鋳造は、アルミニウムを加熱し液体化させ、金型に流し込んで固化させることで所定の形状の部品を作成する製造方法です。この方法は多くの産業で使用されており、複雑な形状を精度高く製造することが可能です。
アルミニウム 鋳造とは
アルミニウム鋳造は、アルミニウム合金を高温で溶かし、金型に流し込んで固める製造方法です。鋳造された部品は、後の加工が最小限で済むことが多く、複雑な形状を比較的短時間で製造することができます。アルミニウム鋳造には、砂型鋳造、金型鋳造、ダイカストなど、さまざまな方法があります。
アルミニウム 鋳造の歴史
アルミニウム鋳造の歴史は、アルミニウムの発見から始まります。アルミニウムは1825年にデンマークの化学者ハンス・クリスチャン・オーステッドによって初めて分離され、その後、1886年にアルミニウム精錬法が確立されました。鋳造技術自体は、金属の加工技術が発展する過程で自然に進化しました。特に20世紀初頭には、アルミニウム合金の開発と鋳造技術の向上により、航空機、車両、自動車部品、機械部品など、さまざまな産業において鋳造部品の使用が広がりました。
アルミニウム 鋳造のメリットとデメリット
アルミニウム鋳造は、その特性を活かして多くのメリットがありますが、いくつかのデメリットも存在します。それぞれについて詳しく見ていきます。
アルミニウム 鋳造のメリット
- 複雑な形状の製造が可能
アルミニウム鋳造は、複雑な形状や細かいディテールを持つ部品を一度に製造することが可能です。これにより、後工程での加工が減り、製造コストが削減されます。 - 軽量性
アルミニウムは非常に軽量で、鋳造した部品の重量が他の金属に比べて低いため、軽量部品を必要とする産業(航空機、自動車、電気機器など)に適しています。 - 優れた耐食性
アルミニウムは自然に酸化被膜を形成し、耐食性が非常に高いため、海洋や化学工業など腐食が問題となる環境でも優れた耐久性を発揮します。 - コスト効率が良い
他の金属材料に比べて、アルミニウムの鋳造には比較的少ないコストで材料を調達でき、鋳造方法自体も確立されているため、生産効率も高いです。 - 熱伝導性が良好
アルミニウムは熱伝導性が高く、冷却や熱処理が容易であり、機器や電子機器など、熱管理が必要な部品に広く使われています。
アルミニウム 鋳造のデメリット
環境への影響
鋳造過程で発生する有害ガスやダストが問題となることがあります。これらを抑えるためには、適切な排気装置や作業環境の管理が必要です。
低い強度
アルミニウム合金は、鋼や鉄に比べて強度が劣るため、強度が要求される部品には適さない場合があります。これを補うためには、合金の調整や追加加工が必要です。
鋳造後の欠陥リスク
鋳造過程で空洞や亀裂、表面欠陥が発生する可能性があります。これらの欠陥は製品の品質に大きな影響を与え、追加の修正作業が必要になることがあります。
冷却時の収縮
鋳造後に冷却が進むとアルミニウムは収縮するため、最終的な形状に対して誤差が生じることがあります。これにより寸法精度を高めるためには、金型や冷却方法の工夫が求められます。
高温での操作の難しさ
アルミニウムは溶解温度が高く、鋳造には高温での操作が必要です。そのため、熱管理や炉の温度調整が重要となり、管理が不十分だと品質に影響を与える可能性があります。
アルミニウム 鋳物の材質について
アルミニウム鋳物は、その軽量性と優れた耐食性から、さまざまな産業で利用される重要な素材です。アルミニウム鋳物の特性を理解し、用途に適した鋳物材質を選ぶことが、製品の品質と性能を左右します。
アルミニウム合金の種類
アルミニウム合金は、その成分や用途に応じていくつかのグループに分類されます。主な分類は以下の通りです。
- 鋳造用アルミニウム合金
鋳造用アルミニウム合金は、主に鋳物を作成するために使用され、鋳造性や機械的性質、耐食性が重視されます。代表的な鋳造用アルミニウム合金には、A356、A319、A535などがあります。これらの合金は、強度と耐食性のバランスが良く、特に自動車や航空機の部品に利用されます。 - 押出成形用アルミニウム合金
押出成形用のアルミニウム合金は、長尺部品や複雑な形状の部品を製造する際に使用されます。これらは、高い成形性と耐食性を持ち、6061や6063などが代表的です。これらは建築や機械部品に多く使用されています。 - 鍛造用アルミニウム合金
鍛造用のアルミニウム合金は、強度が要求される部品に使用されます。鍛造プロセスでの使用を前提にしており、特に航空機や自動車の重要部品に適しています。代表的なものに7050や7075合金があります。
各種アルミニウム 鋳物の特性
- A356合金
A356は、鋳造性が良好で、耐食性と機械的特性に優れた合金です。特に自動車部品や航空機の構造部品に使用され、熱処理を施すことで強度が向上します。耐摩耗性にも優れており、重負荷部品に適しています。 - A319合金
A319合金は、良好な機械的特性と耐食性を持ち、エンジン部品や構造部品に多く使用されます。この合金は、強度と耐熱性に優れ、過酷な条件下でも高い性能を発揮します。特に自動車や機械部品に最適です。 - A535合金
A535は、非常に高い耐食性を持ち、特に海水や化学薬品に強いため、船舶部品や水処理設備に広く使用されます。鋳造後も高い強度を保ち、耐久性に優れた特性を示します。
アルミニウム 鋳造方法の選択
アルミニウム鋳造方法の選択は、製品の形状や使用目的によって異なります。適切な鋳造方法を選ぶことで、効率的に高品質な部品を製造できます。
一般的な鋳造方法の紹介
- 砂型鋳造
砂型鋳造は、最も一般的な鋳造方法で、複雑な形状の部品を鋳造するのに適しています。砂で作られた型に溶けた金属を注入し、冷却後に取り出します。この方法は、コストが比較的安価で、少量生産にも適しています。 - 金型鋳造(ダイカスト)
金型鋳造は、高精度で多量生産を行うのに適しています。特に、アルミニウム合金を高速で注入することで、強度と精度を保った部品を効率よく生産できます。自動車部品や電機部品に多く使用されています。 - 重力鋳造
重力鋳造は、鋳型を重力で充填する方法で、比較的大きな部品に適しています。金型鋳造ほどの精度は必要ないが、高い耐久性やコストパフォーマンスが求められる場合に使用されます。
鋳造方法の選び方
鋳造方法の選択は、以下の要素を考慮することで決定されます。
- 生産量: 高い生産効率が求められる場合は、ダイカストや重力鋳造が適しています。一方、小ロット生産には砂型鋳造が有効です。
- 精度要求: 高精度が必要な場合は金型鋳造が適しており、精度が比較的低くても良い場合は砂型鋳造や重力鋳造が有効です。
- コスト: 初期費用が高い金型鋳造は、大量生産時にコストメリットがありますが、少量生産には向いていません。
- 部品の形状や大きさ: 複雑な形状や大きな部品には砂型鋳造や重力鋳造が適しており、比較的小型で精密な部品にはダイカストが適します。
それぞれの鋳造方法の特徴を理解し、適切な方法を選ぶことで、製品の品質とコスト効率を最大化することができます。
まとめ
アルミニウム鋳造は、軽量で耐腐食性に優れた金属部品を製造する技術です。高い成形性と熱伝導性を持ち、複雑な形状の部品も容易に作成可能です。自動車や航空機、電子機器など多岐にわたる産業で利用され、コスト効率や環境負荷の低減も期待されています。
プロが教えるアルミニウム溶接のコツ:成功するためのポイントまとめ
「アルミニウムの溶接を始めたいけれど、正しい方法を知らない…」と悩んでいるあなたへ。アルミニウムは軽量で強度があり、多くの産業で利用されている素材ですが、その特性から溶接が難しいとされています。そこで、今回は「プロが教えるアルミニウム溶接のコツ」をご紹介します。
この記事は、以下のようなお悩みを持つ方にぴったりです。
- アルミニウム溶接の基本が知りたい。
- どんな溶接方法があるのか、選択に迷っている。
- 成功するためのポイントを押さえたい。
アルミニウムの溶接方法には、TIG溶接やMIG溶接など、さまざまな技術が存在します。それぞれの特性や利点、注意点を理解することが、成功への第一歩になります。このガイドでは、初心者からプロを目指す方まで、役立つ情報を幅広くまとめ、ご紹介します。あなたの溶接技術を一段階向上させるための手助けとなることでしょう。
アルミニウムの溶接方法ごとの基本知識
アルミニウムは軽量で耐食性に優れた金属ですが、溶接が難しいことで知られています。そのため、適切な溶接方法を理解し、適用することが重要です。本記事では、アルミニウムの溶接方法の種類や特徴、難しさの要因、対処法について詳しく解説します。
アルミニウムの溶接方法ごとの種類
アルミニウムの溶接にはいくつかの方法があり、それぞれ特徴と適用範囲が異なります。以下の主要な溶接方法を紹介します。
- TIG溶接(Tungsten Inert Gas Welding)
アルミニウムの溶接で最も一般的な方法。アルゴンなどの不活性ガスを使用し、精密な制御が可能で、美しい仕上がりが得られる。 - MIG溶接(Metal Inert Gas Welding)
ワイヤを連続的に供給する半自動溶接方法。作業効率が高く、大量生産向き。 - レーザー溶接
高エネルギーのレーザー光を用いる溶接方法。精密な加工が可能だが、設備コストが高い。 - 抵抗スポット溶接
電流を流して局所的に加熱し、接合する方法。薄板のアルミニウムに適している。
各溶接方法の特徴と利点
溶接方法 | 特徴 | 利点 |
---|---|---|
TIG溶接 | 精密制御が可能 | 仕上がりが美しい |
MIG溶接 | ワイヤ供給で効率的 | 生産性が高い |
レーザー溶接 | 高精度 | 熱影響が少ない |
抵抗スポット溶接 | 電流で接合 | 薄板向け |
アルミニウムの溶接方法ごとの難しさ
アルミニウムの溶接は、鉄やステンレスとは異なる難しさがあります。その理由として、以下の点が挙げられます。
アルミ溶接が難しい理由
- 酸化皮膜の影響
アルミニウム表面には酸化皮膜が形成されやすく、溶接性を低下させる。溶接前に適切な前処理が必要。 - 熱伝導率が高い
鉄の約3倍の熱伝導率があり、急速に熱が拡散するため、溶融池の形成が難しい。 - 溶融金属の流動性
溶融したアルミニウムは粘性が低く、流れやすいため、溶接中にコントロールが難しい。 - ピンホール(気孔)の発生
溶接中に水素が吸収されやすく、気孔ができやすい。
初心者が直面する主な課題
- アークが安定しない
- 溶接中にアルミが溶け落ちる
- ビードの形成が難しい
- 割れやすい
アルミニウムの溶接方法ごとの対処法
アルミニウムの溶接が難しい理由を理解したうえで、適切な対策を講じることで、より良い溶接品質を確保できます。
溶接が上手くいかない場合の具体的な対処法
- 適切な前処理を行う
溶接前に酸化皮膜を除去し、クリーンな表面を確保する。ブラッシングや化学洗浄が有効。 - 適切な溶接機の設定を行う
電流や電圧の設定を適切に調整し、熱影響を最小限に抑える。 - 溶接速度を一定に保つ
アルミニウムは熱伝導率が高いため、適切な速度で均一に溶接することが重要。 - 適切なシールドガスを使用する
アルゴンやヘリウムを使用し、溶融池を安定させる。
よくある失敗とその改善策
- ピンホールが発生する → 溶接環境の湿度を低くし、溶接ワイヤを乾燥させる
- 溶接中に溶融金属が流れる → 適切なフィラー材を選定し、溶接角度を調整する
- ビードが不均一になる → 安定したアークを保ち、一定の速度で作業する
アルミニウムの溶接には特有の難しさがありますが、適切な知識と技術を身につけることで、より高品質な溶接が可能になります。各溶接方法の特性を理解し、適切な手順を踏むことが成功の鍵です。
アルミニウム 溶接方法ごとのスポット溶接
アルミスポット溶接の特徴
アルミニウムのスポット溶接は、自動車や航空機産業などで広く活用されている抵抗溶接の一種です。鉄やステンレスのスポット溶接と比較すると、熱伝導率の高さや酸化皮膜の影響により、適切な溶接条件の設定が難しいとされています。
アルミスポット溶接の主な特徴
- アルミニウムは鉄の約3倍の熱伝導率を持ち、電極から供給される熱が広がりやすいため、適切な電流制御が必要。
- 表面に酸化皮膜(Al₂O₃)が形成されており、これが溶接時の電気抵抗や接合強度に影響を与える。
- 鉄よりも短い時間で強い電流を流す必要があり、溶接条件の管理が重要。
- 電極への付着が発生しやすく、定期的なメンテナンスが必要。
スポット溶接の難しさと克服法
アルミニウムのスポット溶接には、いくつかの課題が存在しますが、適切な手法を用いることで克服可能です。
主な課題とその対策
酸化皮膜による電気抵抗の増加
溶接前にブラシや化学洗浄を用いて酸化皮膜を除去することが重要です。また、亜鉛メッキ電極や特殊コーティング電極を使用すると、酸化皮膜の影響を抑えることができます。
熱伝導率の高さによる溶接部の弱体化
短時間・高電流のパルス溶接を用いることで、必要な熱量を確保しつつ余計な熱拡散を防ぐことができます。さらに、シートの厚みに応じた電流調整を行い、適切な溶融状態を確保することが求められます。
電極の摩耗が早い
定期的な電極メンテナンス(研磨・交換)を実施し、耐久性の高いクロム銅合金などの電極を採用することで、長期間の安定した溶接を可能にします。
アルミニウム 溶接方法ごとの欠陥と改善策
アルミニウムの溶接欠陥の種類
アルミニウムの溶接では、他の金属と比較して特有の欠陥が発生しやすい。以下に代表的な溶接欠陥を挙げる。
代表的なアルミ溶接欠陥
ブローホール(気孔)
溶接時に水分や油分が蒸発し、溶接部に小さな穴ができる現象です。これを防ぐためには、ワークの適切な前処理(脱脂・清掃)を行い、溶接ワイヤの保管環境を最適化することが重要です。
クラック(亀裂)
熱影響による内部応力で割れが発生する現象です。急激な冷却や溶接条件の不適切さが原因となるため、パルス溶接を活用したり、予熱・後熱処理によって応力を緩和することで防ぐことができます。
溶け込み不足
溶接部の接合が不完全で、強度不足の原因となる欠陥です。電流不足や酸化皮膜の影響が主な要因であるため、電流・電圧の適切な設定と酸化皮膜の徹底除去が改善策となります。
欠陥を防ぐためのポイント
アルミニウム溶接における欠陥を防ぐには、以下のポイントを押さえることが重要です。
前処理の徹底
ワークの脱脂・酸化皮膜除去を確実に行い、不純物の影響を排除することが必要です。また、清潔な環境で溶接作業を行い、外部からの汚染を防ぎます。
適切な溶接パラメータの設定
板厚や使用材料に応じた電流・電圧・ワイヤ供給速度を最適化することで、溶接品質を向上させることができます。溶接速度を適切に調整することで、過熱や溶け込み不足を防ぐことも可能です。
溶接後の管理
クラック発生を防ぐために、冷却速度を管理し、必要に応じて応力除去処理を行います。また、溶接部の検査(X線検査、超音波探傷など)を実施し、欠陥を早期に発見することが望ましいです。
アルミニウム溶接は難易度が高いですが、適切な方法と管理によって高品質な溶接が可能となります。適正な前処理、溶接条件の最適化、欠陥対策を組み合わせることで、強度・耐久性のある接合が実現できます。
まとめ
アルミニウム溶接の成功には、適切な機材選び、清潔な作業環境、そして正確な温度管理が不可欠です。溶接前の表面処理や、適切なフィラー材の使用も重要です。さらに、技術の習得には練習が必要で、基本をしっかりと身につけることが成功の鍵となります。
アルミニウムの溶接方法とその特性を徹底解説
アルミニウムは、その軽量性と耐腐食性から広く使用される素材ですが、溶接する際には特有の課題があります。「アルミニウムの溶接方法とその特性を徹底解説」というタイトルの本記事では、アルミニウムの溶接性について深く掘り下げ、どのように適切に溶接を行うかを詳しく解説します。
「アルミニウムの溶接に挑戦したいけれど、どうすれば良いのか分からない」と感じている方々にとって、このガイドはまさに必見です。溶接の基本から、適切な技術や機材の選び方、さらにはアルミニウム特有の特性についても触れていきます。
溶接はただの接合法以上のものであり、正しい知識と技術がなければ、思うような品質や強度を得ることは難しいです。これからアルミニウムを用いたプロジェクトを計画している方々や、溶接技術を向上させたいと考えている方々にとって、この情報が役立つことでしょう。それでは、アルミニウムの溶接の奥深い世界に一緒に踏み込んでいきましょう。
1. アルミニウム 溶接性の基本
アルミニウムは軽量で高い強度を持つ素材として広く使用されていますが、溶接性に関しては独特の特徴を持っています。以下に、アルミニウムの種類や溶接性に影響を与える要因、そして溶接に適した材料や機器の選び方について詳しく解説します。
1-1. アルミニウムの種類とその溶接特性
- 純アルミニウム (1000番台)
純度が高く、溶接性が良いですが、強度が比較的低いため、構造的な用途には適しません。 - アルミニウム合金 (2000番台~7000番台)
高強度を持つ合金ですが、溶接性が低く、熱処理による硬化現象やひずみが問題になることがあります。特に高強度合金は溶接後の脆性が増すことがあるため注意が必要です。 - 鋳造アルミニウム (鋳物用合金)
鋳造アルミニウムは溶接性が高いですが、鋳物特有の不均一な構造により、溶接時に亀裂が入りやすい場合があります。
1-2. アルミニウム 溶接性に影響を与える要因
- 表面酸化膜
アルミニウムは酸化膜が表面に自然に形成されやすく、溶接時にこれが溶けにくいため、適切な前処理が必要です。 - 熱伝導率の高さ
アルミニウムは熱伝導率が高いため、溶接時に熱が素早く拡散します。そのため、適切な溶接速度と熱管理が求められます。 - 低い融点
アルミニウムは融点が低いため、溶接時に溶けやすく、溶接部分の強度が低くなるリスクがあります。
2. アルミニウム 溶接性に適した材料と機器
2-1. アルミ溶接に必要な材料
- 溶接棒とワイヤ
アルミニウム溶接には、基本的にアルミニウムの合金をベースにした溶接棒やワイヤを使用します。一般的には、同じ合金またはそれに近い合金を選ぶことが重要です。 - フラックスとシールドガス
溶接中の酸化膜を除去するために、適切なフラックスを使用することが推奨されます。また、アルゴンなどのシールドガスを使用して酸化を防ぎます。
2-2. アルミ溶接に適した機器の選び方
- TIG溶接機
TIG溶接はアルミニウム溶接において非常に効果的です。高精度の溶接が可能で、薄板から厚板まで幅広い用途に対応できます。 - MIG溶接機
MIG溶接もアルミニウム溶接に適しています。特に自動化された溶接ラインや連続作業に適しており、比較的簡単に操作できます。 - 溶接機の設定
アルミニウムの溶接には、溶接機の電流や電圧の調整が重要です。機器によっては専用の設定が必要で、過剰な熱が加わると溶接部分が不安定になります。
3. アルミニウム 溶接性が難しい理由
3-1. アルミニウムの特性と溶接の課題
- 酸化膜の存在
アルミニウムの表面に酸化膜が自然に形成され、これが溶接を難しくします。酸化膜は非常に高い融点を持ち、溶接時にこれを除去しなければなりません。 - 高い熱伝導率と低い融点
熱が素早く拡散するため、溶接の際に精密な熱管理が必要です。さらに融点が低いため、溶けすぎないように注意する必要があります。 - ひずみと変形
高温と冷却時にアルミニウムが膨張・収縮するため、溶接部にひずみや変形が発生することがあります。これを防ぐためには、溶接後の冷却や熱処理が必要です。
3-2. 一般的なトラブルとその対策
酸化物の混入
酸化膜が溶接部に混入すると、強度が低下します。これを防ぐために、適切なシールドガスを使用したり、表面処理を行ったりすることが求められます。
亀裂の発生
溶接部に亀裂が生じることがあります。これは主に、溶接中の温度管理が不適切だったり、冷却が急激であったりすることが原因です。冷却速度を調整し、熱影響を最小限にすることが重要です。
変形やひずみ
アルミニウムは熱によって膨張・収縮が激しいため、適切なフィクスチャーと支持が重要です。また、溶接時のビードの配置にも注意を払い、均等に熱を加えるようにします。
4. 初心者向けアルミニウム 溶接性の方法とコツ
アルミニウム溶接は初心者にとって挑戦的かもしれませんが、基本的な手順とコツを押さえることで、効率的かつ高品質な溶接が可能になります。ここでは、アルミ溶接の基本的な手順と初心者が注意すべきポイントを紹介します。
4-1. アルミ溶接の基本的な手順
- 表面の準備
アルミニウムの表面には酸化膜が存在するため、溶接前にしっかりと研磨して酸化膜を除去します。サンドペーパーや専用の研磨ツールを使用するのが一般的です。 - 機器の設定
使用する溶接機の設定を確認し、適切な電流や電圧を選びます。アルミニウムは熱伝導率が高いため、溶接時には過剰な熱が加わらないように設定に注意が必要です。 - 溶接の開始
TIG溶接の場合、トーチを一定の距離で保持し、電極と母材の間にアークを発生させます。MIG溶接の場合は、ワイヤーを送り込みながら溶接します。 - シールドガスの使用
アルミニウムの酸化を防ぐために、シールドガス(アルゴン)を使用します。ガスフローが十分であることを確認し、酸化を防ぎながら作業を進めます。 - 冷却と後処理
溶接後は、溶接部が急速に冷却されないように注意し、均等に冷却します。また、後処理として、必要に応じて溶接部を研磨し、外観を整えることが重要です。
4-2. 初心者が知っておくべきポイント
- 適切なシールドガスの使用
アルミニウム溶接では、酸化を防ぐためにシールドガス(アルゴン)を使用することが基本です。ガスフローが不十分だと酸化膜が発生し、溶接部に不具合が生じる可能性があります。 - 溶接の速度と熱管理
溶接速度は適切に保ち、過剰な熱が加わらないように注意します。アルミニウムは熱伝導が良いため、溶接の際に熱が広がりやすく、溶けすぎることがあります。 - フィクスチャーの使用
アルミニウムは溶接中に変形しやすいので、しっかりとフィクスチャーで固定することが大切です。溶接中のひずみを最小限に抑えるためには、固定が重要です。
5. 特定のアルミ合金の特性と用途
アルミニウム合金にはさまざまな特性があり、それぞれの合金が特定の用途に適しています。ここでは、A5052および6000系アルミ合金の特性と用途について詳しく紹介します。
5-1. A5052の特性と溶接性
- 特性
A5052は、良好な耐食性と適度な強度を持つアルミニウム合金です。特に海水や化学環境に強いという特徴があります。 - 溶接性
A5052は溶接性が良好で、TIG溶接やMIG溶接の両方で使用可能です。しかし、溶接時にひずみが発生しやすいため、冷却や熱管理が重要です。 - 用途
A5052は、海洋構造物や車両のボディ、化学装置など、耐食性が求められる分野に広く使用されています。
5-2. 6000系アルミ合金の特性と用途
用途
6000系アルミ合金は、建築用材料や輸送機器、配管、機械部品などに広く使用されています。また、溶接性も良好で、複雑な部品や構造物に適しています。
特性
6000系アルミ合金は、強度、耐食性、加工性がバランス良く組み合わされた合金です。特に加工性が優れており、さまざまな形状に加工できます。
まとめ
アルミニウムの溶接方法には、TIG溶接、MIG溶接、アーク溶接などがあります。これらは高い熱伝導性と低い融点を持つアルミニウムに適しています。溶接時の酸化膜の除去や適切なフィラー材の選定が重要で、強度や耐食性を確保するための技術が求められます。
「A5056の加工性能向上!効率的な切削テクニック」
A5056アルミニウム合金の基本知識
A5056アルミニウム合金は、特に海水環境や化学的な厳しい条件での耐食性に優れた合金です。主にマグネシウムを主要成分としており、高い強度を誇り、溶接性にも優れています。この合金は、航空機や船舶、化学設備などの高性能が求められる用途に広く利用されています。A5056の物理的特性:比重と融点
- 比重: A5056の比重は約2.66です。アルミニウム合金においては比較的高い比重を持っており、これによりその強度や耐久性が増しています。
- 融点: A5056の融点は約615°C(1140°F)です。アルミニウム合金の中では比較的高い融点を持ち、高温環境下でも安定して使用できる特性を持ちます。この特性により、熱に強い部品が求められる用途で活躍します。
A5056とA5052の合金成分と特性の比較
- A5056とA5052はどちらもマグネシウムを主成分としたアルミニウム合金ですが、A5056はより高いマグネシウム含有量を特徴としています。これにより、A5056はA5052よりも高強度で耐食性に優れていますが、その分加工性が少し難しくなる場合があります。
- A5056は特に海水環境での耐食性が高く、航空機や船舶、化学設備など過酷な環境で使用されることが多いです。対して、A5052は優れた加工性を持ち、食品業界や日常的な交通機関、軽量構造物に利用されます。
A5056の特有な特徴と利用分野
A5056アルミニウム合金は、その優れた耐食性と高強度が特長です。以下はその具体的な特徴と利用分野です。- 耐食性: A5056は特に海水や化学薬品に対して非常に強い耐性を持ちます。このため、船舶部品、海洋構造物、化学プラントなどでよく使用されます。海水が直接接触する部分でも長期間にわたって劣化を防ぐことができます。
- 高強度: A5056は高い強度を持ち、機械的な負荷がかかる部分や構造物に最適です。この強度を活かして、航空機の部品や運輸機器などで広く利用されています。
- 溶接性: A5056は非常に良好な溶接性を持ち、異なる構造のパーツを接合する際に便利です。特に複雑な形状を持つ部品や構造物でその特性が活かされます。航空機部品や車両のフレームなど、精密な溶接が必要な分野でも多く使用されます。
- 高耐食性: A5056の耐食性はその合金成分に起因しており、特に海水や塩水、化学的に厳しい環境下での長期使用に耐えることができます。このため、化学工業や海洋分野、さらには石油・ガス産業でも多く活躍しています。
- 主な用途:
- 航空機部品: 高い強度と軽量性を求められる航空機のフレームや部品に使用されます。
- 船舶部品: 海水に曝露される部分、特に船舶の外部部品に多く使われます。
- 化学設備: 化学プラントや海洋プラットフォームの一部でも使用され、その耐食性を活かしています。
- 運輸機器: 高強度と軽量性を必要とする車両部品や輸送機器にも適しています。
A5056の切削性について
A5056アルミニウム合金は、その物理的特性により、特に高強度や耐食性が求められる分野で広く利用されますが、切削性にも注目すべき特性があります。切削性は、材料の加工過程でどれだけ効率的に切削できるか、またその際に発生する熱や摩擦などの影響を管理できるかに関わります。ここでは、A5056の切削性について詳しく説明します。切削性とは何か?
切削性とは、金属などの材料を切削工具を使って加工する際に、その材料がどれだけ加工しやすいかを示す特性です。切削性は主に以下の要素に影響されます:- 切削抵抗: 材料が切削工具に対してどれだけ抵抗するか。
- 加工温度: 切削中に発生する熱の影響。
- 切削工具の摩耗: 工具がどれだけ早く摩耗するか。
- 加工後の仕上がり: 切削後に残る表面品質。
A5056の切削性能と加工のしやすさ
A5056は、アルミニウム合金の中でも比較的加工しやすい材料に分類されますが、その強度や耐食性の高さから、切削性には若干の注意が必要です。- 加工しやすさ: A5056は、アルミニウム合金の中では比較的柔らかい部類に入りますが、マグネシウムを多く含むため強度が高く、切削中に発生する熱がやや多くなる傾向があります。そのため、適切な切削条件を設定しないと、工具の摩耗が早くなり、仕上がりに影響を与えることがあります。
- 切削温度: 高強度の合金であるため、切削中に高温が発生しやすいですが、これは工具の摩耗を早める原因となるため、冷却液の使用や適切な切削速度を選定することが重要です。
- 加工後の仕上がり: A5056は良好な表面仕上がりが得られることが多く、特に精密部品の加工に向いています。ただし、切削速度や送り速度を適切に設定しないと、表面に微細な傷がつくことがあるため、注意が必要です。
合金の切削性を左右する要因
A5056の切削性に影響を与える要因としては、以下の点が挙げられます:- 合金成分: A5056は主にマグネシウムを含むアルミニウム合金ですが、含有する元素の種類や量によって、切削性が異なります。特にマグネシウムの量が多いため、高強度とともに切削中に発生する熱の管理が求められます。
- 硬度と強度: A5056の硬度は高い方に分類されるため、加工中に工具の摩耗が進みやすいです。適切な切削工具の選定と冷却が重要です。
- 切削条件: 切削速度、送り速度、切削深さなどの条件が切削性に大きな影響を与えます。過度な切削速度や深さでは、加工中に熱が過剰に発生し、工具の寿命を短くすることがあります。
- 冷却と潤滑: A5056の切削性を向上させるためには、適切な冷却液や潤滑剤の使用が重要です。これにより、切削時に発生する熱を抑えるとともに、工具の摩耗を軽減できます。
A5056の加工性能向上へのアプローチ
A5056アルミニウム合金は高強度と良好な耐食性を持つため、様々な用途に適していますが、切削加工時には特定の課題もあります。加工性能を向上させるためには、適切な工具の選択や切削条件の設定が重要です。ここでは、A5056の切削加工性能を最大化するためのアプローチについて詳しく説明します。A5056の切削加工に適した工具選択
A5056の加工において、工具の選定は加工精度や効率を大きく左右します。適切な工具選びにより、工具の寿命を延ばし、加工精度を高めることができます。- 切削工具の材質: A5056のようなアルミニウム合金には、耐摩耗性が高い工具が必要です。一般的には、コーティング工具(TiNやTiAlNコーティング)を使用することが効果的です。これにより、摩耗や熱の影響を抑え、加工中の安定性が増します。
- 工具形状: A5056は比較的加工しやすい材料ですが、切削時の熱や摩耗を抑えるために、適切な工具形状を選ぶことが重要です。多刃工具や細かい切削角度を持つ工具を選ぶと、加工面の品質向上や工具の耐久性向上につながります。
- 工具の冷却: 切削時に発生する熱を抑えるために、冷却液やエアーブローを使用することが推奨されます。特に、冷却効果が高い油性冷却剤を使用することで、工具の摩耗を抑制できます。
効率的な切削条件の設定
A5056の切削性を最大化するためには、適切な切削条件を設定することが不可欠です。切削速度や送り速度を適切に設定することで、加工効率と品質を最適化できます。- 切削速度の設定: A5056は高強度の合金であり、切削中に高温が発生しやすいため、適切な切削速度を選定することが大切です。一般的には、中程度の切削速度が推奨され、速度が速すぎると工具の摩耗が早くなります。逆に遅すぎると、加工効率が低下し、コストが増加します。
- 送り速度: 送り速度は切削効率に大きく影響します。送り速度が適切でないと、加工時間が長くなり、効率が悪くなります。一般的に、中程度の送り速度を選ぶと良い結果を得られることが多いです。
- 切削深さ: 切削深さを適切に設定することも重要です。浅すぎると効率が悪くなり、深すぎると工具に過度の負荷がかかります。通常、中程度の切削深さが望ましいとされます。
A5056専用の加工技術と工夫
A5056の加工性能を向上させるためには、専用の加工技術や工夫を取り入れることも有効です。- 切削液の使用: A5056は高強度で熱が発生しやすいため、冷却や潤滑の役割を果たす切削液の使用が重要です。エアーブローや冷却液を駆使して、加工中の熱を抑制し、工具の寿命を延ばすことができます。
- 高圧冷却システムの導入: 高圧冷却システムを使用すると、切削中に発生する熱を効果的に抑えることができ、加工精度を向上させます。また、冷却液が工具の摩耗を減らし、加工後の仕上がりが良好になります。
- 微細加工技術の採用: 高精度の仕上げ加工が必要な場合、微細加工技術を取り入れることが効果的です。これにより、A5056の表面品質を向上させることができます。
- 振動対策: 高強度のA5056を加工する際、工具の振動が発生しやすいため、工具の振動を抑える設計や、安定した切削力の維持を心掛けることが大切です。これにより、加工精度を保ち、仕上がりを向上させることができます。
A5056の切削テクニック
A5056アルミニウム合金はその特性から優れた加工性を持っていますが、適切な切削テクニックを使用しなければ、望ましい加工精度を達成することができません。ここでは、A5056の切削加工におけるコツやテクニック、トラブルを避けるための注意点、高品質な加工面を実現する方法を紹介します。切削加工におけるコツとテクニック
A5056の切削加工を効率的に行うためには、以下のテクニックが重要です。- 切削速度の最適化: A5056のようなアルミニウム合金は比較的柔らかいため、切削速度を速く設定し過ぎないことが大切です。速度が速すぎると、工具の摩耗が早くなり、仕上がりが粗くなります。中程度の切削速度を選ぶと、スムーズな切削が可能になります。
- 細かい送り速度の調整: 送り速度が速すぎると切削品質が低下し、加工面が荒れる可能性があります。細かい送り速度を設定し、段階的に送り速度を上げることで、品質の高い仕上がりが得られます。
- 適切な切削深さ: A5056のような中程度の硬さの材料では、切削深さを中程度から浅めに設定することが推奨されます。深すぎると加工後に歪みが生じることがあるため、浅めに切削し、段階的に深さを増す方法が有効です。
トラブルを避けるための注意点
A5056の切削加工時には、以下のトラブルを避けるために注意が必要です。- 工具の摩耗: アルミニウム合金は工具に対して高い摩耗を引き起こす可能性があるため、摩耗の少ない工具の選定が重要です。また、定期的に工具の状態を確認し、早期に交換することを心掛けましょう。
- 熱の管理: 切削中に発生する熱が高くなりすぎると、加工精度が低下したり、材料に変形が生じる恐れがあります。冷却液やエアーブローを適切に使用して、過熱を防ぐことが必要です。特に、高圧冷却システムを使用することで、熱の発生を効果的に抑えることができます。
- 切削中の振動: 振動が発生すると加工面が荒れたり、工具の寿命が短くなります。振動を抑えるために、工具の設置位置や機械の安定性を確認し、適切な切削条件で作業を行うことが大切です。
高品質な加工面を実現する方法
A5056のようなアルミニウム合金で高品質な加工面を実現するためには、以下の方法が有効です。- 適切な工具選定: A5056を加工する際には、高耐摩耗性を持つコーティング工具を使用することが推奨されます。これにより、工具の寿命を延ばし、加工精度を高めることができます。特に、TiNやTiAlNコーティングが有効です。
- 高精度な切削設定: 精度の高い加工面を実現するためには、細かい切削条件の設定が重要です。切削速度や送り速度を細かく調整し、最適な条件を選ぶことで、加工面が滑らかで精密になります。
- 表面仕上げ加工: 最終仕上げとして、軽い研磨やバリ取りを行うことで、加工面がさらに滑らかになります。特に、研磨機やバフ研磨を使用することで、高光沢仕上げや精密仕上げが可能です。
- 安定した冷却管理: 高品質な加工面を維持するためには、冷却液やエアーブローを適切に使用して、切削中の温度管理を行うことが大切です。温度が安定していることで、加工面の平滑度が向上します。
まとめ
A5056というアルミ合金は加工性が向上されています。切削性においても優れた性能を持っており、効率的な切削テクニックを活用することで生産性向上が期待できます。このようなアルミ合金の加工には適切な切削パラメーターの設定が重要であり、切削速度や刃先加工、冷却剤の利用などが効果的な手法として挙げられます。これにより、加工品質の向上と加工コストの削減が実現されます。A1050アルミ合金加工ガイド:切削性を高めるポイント
アルミ合金A1050の基本
A1050アルミ合金は、非常に高い純度を誇るアルミニウム合金であり、主に優れた耐食性と加工性を持つことから、さまざまな産業で使用されています。ここでは、A1050アルミ合金の特性、アルミ加工の一般的な課題、そしてA1050アルミ合金の用途について説明します。A1050アルミ合金の特性
A1050アルミ合金は、主に99.5%の純度を持つアルミニウムをベースとした合金で、非常に優れた耐食性を特徴としています。加えて、良好な加工性と優れた導電性を有しており、以下の特性が挙げられます。- 高い耐食性: 特に酸化に対する耐性が高く、海水環境や湿度の高い環境でも劣化しにくい。
- 優れた加工性: 高い延性を持ち、冷間・熱間加工ともに容易で、切削加工も適しています。
- 良好な導電性: 電気伝導性が高いため、電気関連の用途にも適しています。
- 低強度: 強度はアルミ合金の中でも低めですが、耐食性や加工性を重視する場合には有利です。
アルミ加工の一般的な課題
アルミ合金の加工にはいくつかの課題があります。特にA1050アルミ合金のように柔らかい材料では、以下のような問題が生じることがあります。- 切削時の熱問題: 高い熱伝導性により、加工中に工具が熱を持ちやすい。
- 表面仕上げ: 柔らかいため、切削後の表面に傷がつきやすいことがある。
- 冷間加工時の変形: 柔らかいアルミ合金は冷間加工時に変形しやすく、精度を保つのが難しい。
- 素材の薄さによる強度不足: 薄い板や薄型部品を作成する際に強度が足りないことがあり、用途を選ぶことが重要です。
A1050アルミ合金の用途
A1050アルミ合金は、その優れた耐食性と加工性から多くの用途に使用されます。主な用途には以下があります。- 建築業: 外装や内装の装飾、アルミサッシ、カーテンウォールなど。
- 化学プラントや海洋用途: 高い耐食性を活かして、化学設備や海上プラットフォーム、船舶部品などに使用。
- 電気機器: 高い導電性を活かして、電気機器や配線、接続部品に利用される。
- 車両部品: 軽量化が求められる部品や、内装部品にも使用される。
A1050の切削性について
A1050アルミ合金は、優れた加工性を誇る材料ですが、切削性にも特有の特徴があります。ここでは、切削性とは何か、A1050の切削性の特徴、および切削性を左右する要因について詳しく説明します。切削性とは何か?
切削性とは、材料を切削加工する際に必要な力やエネルギー、加工のしやすさ、仕上がりの状態に関する特性を指します。具体的には、切削工具の摩耗具合、切削中の温度上昇、加工精度、そして表面品質などが重要な要素となります。良好な切削性を持つ材料は、加工時に少ない力でスムーズに切削でき、工具の寿命が長く、仕上がりも良好になります。A1050の切削性の特徴
A1050アルミ合金は、非常に良好な切削性を持つ材料です。主な特徴は以下の通りです。- 高い加工性: A1050は非常に柔らかく延性が高いため、冷間・熱間加工ともに容易に加工できます。特に切削加工では、鋸やフライス盤などを用いた加工がスムーズに行えます。
- 低い切削抵抗: A1050は低強度のアルミ合金であるため、切削時の抵抗が少なく、加工時の力が少なくて済みます。このため、高速切削が可能です。
- 熱伝導性の高さ: 熱伝導性が良好であるため、切削中に発生する熱が速やかに放散され、工具が高温になりにくいです。これにより、工具の摩耗を抑制することができます。
- 表面品質の良さ: 加工時に滑らかな表面仕上げが得られやすく、良好な表面仕上がりが求められる部品にも適しています。
切削性を左右する要因
A1050の切削性を左右する要因は以下のようなものがあります。- 切削速度と送り速度: A1050は比較的柔らかい材料ですが、高速で切削する場合、適切な送り速度や切削速度を選ぶことが重要です。速度が適切でない場合、仕上がりが悪くなったり、工具の摩耗が早く進むことがあります。
- 切削工具の材質とコーティング: A1050を加工する際、切削工具の材質やコーティングが影響します。一般的に、硬度の高い工具やコーティングが施された工具を使用すると、長寿命かつ高精度の加工が可能です。
- 切削液の使用: 切削液を使用することで、切削中の摩擦を減少させ、工具の温度を下げ、表面品質を向上させることができます。A1050の場合、適切な切削液の使用が重要です。
- 加工条件の設定: 適切な切削条件(切削深さ、切削幅、回転数など)を選定することで、効率よく切削を進めることができ、加工精度や仕上がりが向上します。
アルミ合金加工のポイント
アルミ合金の加工では、材料特性を最大限に活かし、効率よく高品質な製品を作るために、いくつかのポイントを押さえる必要があります。ここでは、アルミ合金加工における重要なポイントを説明します。正しい工具の選択
アルミ合金は、比較的柔らかく加工しやすい材料ではありますが、工具選定は重要です。適切な工具を使用することで、加工精度が向上し、工具の摩耗を抑え、加工効率も良くなります。- 工具材質: アルミ合金の加工には、耐摩耗性が高い工具を選びましょう。カーバイド(炭化物)やコーティングされた工具(TiN、TiAlNなど)は、工具寿命を延ばし、より高精度の加工を実現します。
- 刃先形状: アルミ合金は切削中に切屑が粘りやすいので、刃先に適度な角度と形状を選ぶことで、スムーズな切削が可能になります。例えば、鋭角的な刃先は切屑をうまく排出し、切削効率が向上します。
切削条件の最適化
切削条件を最適化することで、加工効率と品質が大きく向上します。特に、回転数、送り速度、切削深さなどの設定が重要です。- 切削速度: 高速切削が可能なアルミ合金ですが、過度な切削速度は熱を発生させる原因となり、工具の摩耗が早くなる場合があります。最適な切削速度を選ぶことが、長時間の安定した加工を実現します。
- 送り速度: 送り速度は、切削精度と表面仕上げに大きく影響します。高速での切削が可能ですが、送り速度が速すぎると加工精度が低下することがあります。最適なバランスが重要です。
- 切削深さ: 切削深さは、1回の切削で除去する材料の量を決定します。深さを適切に設定することで、過剰な摩擦熱を防ぎ、工具の寿命を延ばせます。
冷却液の使用とその効果
冷却液は、切削中の摩擦熱を抑え、工具の温度上昇を防ぎます。これにより、工具寿命の延長や加工精度の向上が期待できます。- 冷却効果: 冷却液は、切削中の温度上昇を抑え、工具の摩耗を減少させます。また、アルミ合金は切屑が粘りやすいため、冷却液が切屑の排出を促進します。
- 潤滑効果: 冷却液には潤滑性もあり、摩擦を減らし、スムーズな切削が可能になります。特に高精度加工や高速加工時に有効です。
- 清掃効果: 冷却液は切削中に発生する切屑を洗い流す役割も担い、切削面の仕上がりを良好に保つことができます。
チップの形状と加工品質
チップの形状は加工品質に大きな影響を与えます。切削中に切屑が適切に排出されないと、加工面が粗くなったり、工具の摩耗が早まる可能性があります。- チップ形状の選定: チップの形状を適切に選ぶことで、切屑の排出がスムーズになり、加工効率が向上します。例えば、スパイラル形状やクレスト形状など、特定の形状のチップを使うことで、アルミ合金の加工に適した切削を行えます。
- 切屑の排出: チップの形状により、切屑がうまく排出されないと、切削面に傷がついたり、加工面の品質が悪くなることがあります。適切な形状のチップを選んで、切屑の排出を円滑にすることが重要です。
A1050アルミ合金の加工方法
A1050アルミ合金は、優れた耐食性と加工性を持つため、様々な加工方法で使用されます。ここでは、A1050アルミ合金の主な加工方法について説明します。旋削加工
旋削加工は、回転するワークに対して切削工具を押し当てることで形状を削り出す方法です。A1050アルミ合金は比較的柔らかいため、旋削加工が非常に効果的です。- 工具の選定: 高速鋼(HSS)や炭化物(カーバイド)の工具が使用されます。アルミ合金は柔らかいため、工具の摩耗が少ないものを選ぶと良いでしょう。
- 切削条件: 高回転数での加工が推奨されますが、送り速度を調整して、滑らかな仕上がりを得ることが大切です。
- 冷却: 冷却液を使用することで、切削時の熱を抑制し、工具寿命を延ばすことができます。
フライス加工
フライス加工は、回転する切削工具を使用して、ワークの表面を削り取る加工方法です。平面や溝の加工など、A1050アルミ合金のフライス加工にも有効です。- 工具選定: フライス加工には、エンドミルやスラストミルなどが使用されます。材質としては、カーバイド製やコーティングされた工具が最適です。
- 切削条件: フライス加工でも、高速回転を保ちつつ、適切な送り速度と切削深さを設定することが必要です。加工中に切屑がうまく排出されるように、工具の形状にも注意が必要です。
- 冷却: フライス加工でも冷却液が重要です。切削中の温度上昇を抑えることで、加工精度を維持できます。
穴あけ加工
A1050アルミ合金の穴あけ加工は、ドリルを用いて行われます。材料が比較的柔らかいので、穴あけ加工は比較的容易ですが、切削条件に注意が必要です。- 工具選定: 鋭利なドリルやコーティングされたドリルが推奨されます。特に長時間の使用を考慮すると、カーバイドドリルが効果的です。
- 切削条件: 穴あけ加工では、回転速度を適切に設定し、送り速度を安定させることが重要です。適切な切削条件でないと、切屑が溜まりやすく、加工精度が低下することがあります。
- 冷却: 穴あけ加工においても冷却液が効果的です。冷却液を使用することで、切削熱を抑え、工具の摩耗を減少させます。
面取りと仕上げ加工
面取り加工や仕上げ加工では、製品の端面を滑らかに仕上げることが求められます。A1050アルミ合金は加工がしやすい素材であるため、面取りや仕上げ加工にも適しています。- 工具選定: 面取りには、面取り用の工具やバリ取り工具を使用します。仕上げ加工には、高精度のエンドミルやバフ研磨が使用されます。
- 切削条件: 面取り加工では、切削深さを浅めに設定し、仕上げ加工では送り速度を低くすることで、より滑らかな仕上がりが得られます。
- 冷却: 仕上げ加工にも冷却液を使用することで、摩擦熱を抑え、仕上がり品質を保つことができます。
加工時のトラブルと対策
A1050アルミ合金の加工時に発生しやすいトラブルとその対策について説明します。これらの問題に対処することで、効率的に高品質な製品を製造することができます。加工精度の問題
加工精度が低いと、製品の寸法がずれたり、位置合わせに問題が生じます。特に、精密部品の製造時にはこの問題が重要です。- 原因: 切削条件が不適切、工具の摩耗、機械の精度不足などが原因です。
- 対策:
- 切削条件を最適化する。特に回転数や送り速度を適切に設定する。
- 工具の状態を定期的にチェックし、摩耗が進んでいる場合は交換する。
- 加工機械の精度を定期的に点検し、必要に応じて調整やメンテナンスを行う。
工具の摩耗と寿命
工具の摩耗は加工精度に影響を与え、最終的には製品の品質に悪影響を及ぼします。また、工具寿命が短いとコストが増加します。- 原因: 高負荷や不適切な切削条件による工具の摩耗、冷却不足など。
- 対策:
- 工具の材質やコーティングを選定する際、A1050アルミ合金の特性に合ったものを選ぶ。
- 適切な冷却液を使用し、切削中の熱を効率的に逃がす。
- 切削条件(回転数、送り速度、切削深さなど)を適切に設定し、工具に過度の負荷をかけない。
表面仕上げの不具合
表面仕上げが不十分だと、製品の外観や性能に影響を与えます。特に見た目が重要な部品の場合、仕上がりが不良になると品質問題に繋がります。- 原因: 不適切な切削条件、工具の摩耗、切削屑が表面に付着することなど。
- 対策:
- 仕上げ加工時に切削条件を最適化し、送り速度や回転数を調整する。
- 高精度の工具を使用し、加工後のバリ取りや研磨作業を行う。
- 表面仕上げが求められる部品に対しては、最終的なバフ研磨やコーティングを検討する。
加工中の変形対策
加工中に部品が変形すると、最終的な製品が規定寸法から外れたり、精度が低下します。- 原因: 加工時の応力、温度変化、クランプの不良などが原因です。
- 対策:
- 加工中の温度を制御するために、冷却液を適切に使用する。
- クランプ方法や加工順序を見直し、部品に過度な応力がかからないようにする。
- 加工前に部品を適切にアニール処理することも、応力を緩和させるために有効です。
A1050アルミ合金加工のためのヒント
A1050アルミ合金の加工を効率的に行うための重要なポイントについて説明します。これらのヒントを活用することで、加工精度を高め、作業効率を向上させることができます。加工速度の調整
加工速度を適切に調整することは、A1050アルミ合金の加工で非常に重要です。速度が高すぎると、工具の摩耗が早まり、逆に低すぎると加工効率が悪化します。- 調整ポイント:
- 加工する部品のサイズや形状、要求される精度に合わせて回転数や送り速度を設定する。
- 適切な切削速度を選ぶことで、表面仕上げが向上し、切削時の熱の発生を抑えることができる。
- 速度を過度に上げることなく、効率的に切削を行うため、加工中に工具や部品の温度が上がらないようにする。
切削抵抗の低減
A1050アルミ合金は比較的柔らかいため、適切な切削条件を選ばないと切削抵抗が大きくなり、工具の摩耗や焼き付きの原因となります。切削抵抗を低減するためには、いくつかの方法があります。- 低減のための方法:
- 工具の選定: 適切な刃物を選ぶことで、切削抵抗を減少させ、加工中の発熱を抑えることができます。チップの形状や材質に注意を払うことが重要です。
- 冷却液の使用: 冷却液を適切に使用して切削中の摩擦を減らし、切削温度を低く保つことが切削抵抗の低減につながります。
- 切削条件の最適化: 送り速度や切削深さを調整して、最適な切削条件を見つけることが重要です。特に、過度な切削深さや送り速度は、切削抵抗を増加させる原因になります。
まとめ
A1050アルミ合金は、切削性を高めるためのポイントがあります。これには、適切な切削速度と切削深さを選ぶことが重要です。また、刃先の冷却や潤滑を考慮することで、より効果的な切削加工が実現できます。加工する際には、これらのポイントを抑えておくことで作業効率が向上し、精度の高い加工が可能となります。“A2017合金の切削性と加工のポイント”
A2017合金の基本
A2017合金は、アルミニウムを基盤とした合金で、特に高い強度を持ちながらも軽量で、航空宇宙産業や自動車産業などで広く使用されています。これらの合金は、優れた機械的性質と耐食性を備えており、特定の環境条件での性能が求められる部品に適しています。A2017合金とは
A2017合金は、アルミニウムと銅を主成分として構成されるアルミニウム合金で、主に航空機や構造部材に使用される材料です。アルミニウム合金の中でも特に高強度を誇り、耐食性にも優れており、航空機や車両などの高負荷がかかる部品での使用が一般的です。 この合金は、強度が求められる用途において、特に重要な役割を果たします。銅の添加により、アルミニウム合金の強度が向上し、高い耐摩耗性を実現しています。A2017合金の成分と特性
A2017合金の成分には、以下の主な金属が含まれています:- アルミニウム (Al):主成分で、軽量で加工しやすい性質を持つ。
- 銅 (Cu):合金の強度を向上させる。特に耐摩耗性や強度が必要な部品に有効。
- シリコン (Si):鋳造性や耐食性を向上させるために微量添加されることがある。
- マグネシウム (Mg):強度をさらに強化し、合金の耐食性を向上させる。
- 鉄 (Fe)、マンガン (Mn)、クロム (Cr):微量成分として含まれ、耐食性や機械的性質に寄与する。
- 高強度:銅がアルミニウムに加えられることで、強度が大幅に向上します。これにより、航空機や自動車部品に使用されることが多いです。
- 耐食性:特に耐食性が求められる環境での使用に適しており、一定の耐腐食性を持っています。
- 軽量性:アルミニウム合金であるため、比較的軽量で、重量制限が厳しい用途にも適しています。
- 加工性:強度が高い一方で、加工しやすい特性を持っています。
A2017合金の機械的性質
A2017合金は、その優れた機械的性質から、特に高負荷を受ける部品や構造部材に利用されます。主な機械的特性は以下の通りです:- 引張強さ:A2017合金は非常に高い引張強さを持ち、構造部材として強度が求められる部品に適しています。
- 降伏強度:降伏強度が高いため、強い力を加えても変形しにくい性質を持っています。
- 硬度:硬度が高く、摩擦や磨耗に強いです。これにより、機械的な部品やエンジン部品などの長寿命化が期待できます。
- 延性:延性が低めであるため、過度の引張りや曲げには注意が必要ですが、適切な使用範囲内では十分な性能を発揮します。
A2017合金の切削性について
A2017合金は高強度で耐摩耗性が優れているため、切削性に関して特有の課題が存在します。しかし、その特性を理解し、適切な加工方法を採用することで、効率的に加工することができます。ここでは、A2017合金の切削性の概要、特徴、課題、解決策について詳しく解説します。切削性の概要
切削性とは、金属や合金を切削工具で加工する際の難易度や効率を指します。切削性が良い材料は、加工中に工具の摩耗や発熱が少なく、加工速度が速く、仕上がりも良好である一方、切削性が悪い材料は逆に加工が困難で、工具の寿命が短くなることがあります。A2017合金は、高強度であるため、切削性が一般的に難しいとされますが、適切な技術と工具を使用することで効率的に加工することが可能です。A2017合金の切削性の特徴
A2017合金の切削性にはいくつかの特徴があります:- 硬度が高い:A2017合金は強度と硬度が高いため、切削中に高い切削力が必要です。このため、一般的な鋼やアルミニウム合金に比べて切削加工が難しくなることがあります。
- 摩耗が早い:合金中の銅成分が硬く、摩耗が激しくなるため、切削工具の消耗が早くなる傾向があります。これにより、加工の際には適切な冷却や切削条件の調整が必要です。
- 熱伝導性が低い:A2017合金は熱伝導性が低いため、切削中に発生する熱が工具に伝わりにくく、工具の温度が上昇しやすいです。これにより、工具の寿命が短くなり、加工精度に悪影響を及ぼす可能性があります。
- 切削時のチッピングやひび割れ:硬度が高いため、切削中にチッピング(欠け)やひび割れが発生することがあります。特に急激な温度変化や強い力が加わる場合に注意が必要です。
切削加工時の課題と解決策
A2017合金の切削加工において直面する課題とその解決策は以下の通りです:- 工具の摩耗が早い
- 解決策:切削工具の材料として、耐摩耗性に優れた超硬工具やコーティングツールを使用することが推奨されます。これにより、工具の寿命が延び、効率的に加工を進めることができます。
- 発熱による工具の劣化
- 解決策:冷却液の使用や適切な切削条件(切削速度、送り速度)を調整することで、工具の温度上昇を抑制できます。高圧冷却やエアブローなどの冷却方法を導入することも効果的です。
- 切削力が大きいため、加工が困難
- 解決策:切削条件(切削速度、送り量)を適切に調整し、最適な切削力を選定することが重要です。また、複数回に分けて切削を行うことで、切削力を分散させ、安定した加工を行います。
- 仕上がり面に不良が生じやすい
- 解決策:最適な切削工具と条件を使用し、仕上げ加工の際に細かい調整を行うことで、仕上げ面の品質を向上させることができます。また、切削油や冷却液を十分に使用することで、表面の仕上がりを改善できます。
- チッピングやひび割れの発生
- 解決策:切削条件を慎重に設定し、急激な温度変化や強い力を避けることが重要です。また、切削工具の先端角度や切削パラメータを最適化することで、ひび割れのリスクを低減できます。
A2017合金の加工方法
A2017合金は高強度・高硬度であり、その特性を活かした加工が求められます。適切な加工方法を選択することで、効率よく、精度の高い製品を作成することが可能です。以下では、A2017合金の加工方法について、加工前の準備から主要な加工技術、加工精度を高めるためのポイントまで詳しく解説します。加工前の準備
A2017合金を加工する前には、いくつかの準備が重要です:- 素材の選定:A2017合金の特性を理解し、用途に適した形状やサイズを選ぶことが重要です。例えば、強度や耐摩耗性が必要な部品には、この合金を選択します。
- 切削条件の設定:A2017合金は硬度が高く、切削時に発生する熱が工具に与える影響を抑えるために、冷却液や切削油を使用します。切削速度、送り速度、切り込み深さを最適化することが加工の効率を高めます。
- 工具の選定:A2017合金は硬度が高いため、耐摩耗性に優れた工具を選ぶ必要があります。超硬工具やコーティング工具が効果的です。また、工具の研磨やメンテナンスを行い、長時間の加工に耐えられる状態を保つことが重要です。
主要な加工技術
A2017合金の加工には、主に以下の技術が使用されます:- 旋削加工:A2017合金の旋削加工では、高精度な切削が求められます。工具の摩耗が早いため、適切な切削条件と冷却手段を確保することが必要です。
- フライス加工:フライス盤を使用した加工は、複雑な形状の部品にも対応可能です。切削中の発熱や摩耗を抑えるため、冷却液を使用し、最適な切削パラメータを設定します。
- 穴あけ加工:A2017合金の穴あけは、適切なドリルの選定と切削条件が必要です。低速での切削を行い、発熱を抑制します。ドリル先端のコーティングが摩耗を減らす助けになります。
- 研削加工:高精度な仕上げ加工が求められる場合、研削加工が用いられます。A2017合金の硬度に対応した研削盤と適切な砥石を使用することが、品質向上につながります。
加工精度を高めるポイント
A2017合金はその高強度により、加工精度が求められる場合があります。精度を高めるためのポイントは以下の通りです:- 適切な切削条件の選定:切削速度や送り速度を最適化することが加工精度に直結します。切削中の振動や温度変化を最小限に抑えることが、精度を保つための基本です。
- 高精度な工具管理:工具の摩耗は加工精度に大きな影響を与えます。工具の状態を常に監視し、適切なタイミングで交換することが重要です。また、工具の冷却と研磨を定期的に行うことも精度維持に役立ちます。
- 冷却方法の最適化:A2017合金は熱膨張や温度変化に敏感なため、冷却液やエアブローによる冷却方法を最適化し、加工中の熱管理を徹底します。冷却液は切削面や工具に均等に供給することが精度向上につながります。
- 加工機械の安定性の確保:加工中の振動や変形を最小化するために、機械の剛性を高め、振動を抑える対策を講じます。さらに、加工機の定期的なメンテナンスも精度向上に寄与します。
A2017合金の加工工具と設備
A2017合金はその高強度と硬度により、加工が難しい材料ですが、適切な工具と加工設備を選定することで、効率的に加工を行うことができます。以下では、A2017合金の加工における切削工具の選択、工具の保守管理、そして加工設備の特性と選定について解説します。適切な切削工具の選択
A2017合金の加工には、以下のような特性を持つ切削工具が求められます:- 超硬工具:A2017合金は硬度が高く、通常の工具では摩耗が早く進行するため、超硬工具やセラミック工具がよく使用されます。これらの工具は、高温に強く、摩耗に対する耐性が高いため、長時間の加工に適しています。
- コーティング工具:A2017合金のような難加工材料には、コーティングされた工具(例えば、TiAlNやTiNコーティング)が効果的です。これにより、工具の摩耗を減少させ、切削性能を向上させます。また、コーティングは切削中の発熱を抑える役割も果たします。
- 微細な刃先の工具:精密加工が求められる場合には、微細な刃先を持つ工具を使用することが、切削精度を保つために重要です。これにより、細かい加工や高精度な仕上げが可能になります。
工具の保守と管理
切削工具の性能を最大限に引き出すためには、工具の適切な保守と管理が必要です:- 定期的な検査と点検:工具の摩耗具合や損傷状態を定期的にチェックし、必要に応じて交換や修正を行います。特に、工具の刃先部分は摩耗が早いため、定期的な検査が重要です。
- 工具の研磨:摩耗が進んだ工具は、研磨して再利用することができます。研磨を行うことで、工具の寿命を延ばし、経済的な負担を軽減できます。
- 工具交換のタイミング:切削条件や加工時間に基づいて、適切なタイミングで工具を交換することが重要です。工具が摩耗すると加工精度が低下し、製品の品質に影響を与えるため、交換のタイミングを見極めることが求められます。
加工設備の特性と選定
A2017合金の加工には、特定の加工設備の特性に合った選定が必要です:- 高剛性の加工機械:A2017合金は硬度が高いため、加工中に発生する振動や変形を最小限に抑えるために、高剛性の加工機械を選ぶことが重要です。加工機の剛性が不足していると、切削精度や仕上がりに影響が出ます。
- 冷却システムの整備:A2017合金は切削中に高温になりやすいため、冷却システムの有無やその性能が重要です。エアブローや冷却液の供給が適切に行われることで、加工時の発熱を抑制し、工具寿命を延ばします。
- 高速加工機械:A2017合金のような難加工材料を効率よく加工するためには、高速加工機械が求められます。これにより、切削速度や送り速度を最適化し、加工時間を短縮することができます。
- CNC制御機械:精密な加工が要求される場合、CNC(コンピュータ数値制御)機械を使用することで、加工精度を向上させることが可能です。CNC機械は、複雑な形状や高精度な加工を自動で行うことができ、加工ミスを減らすことができます。
A6061 T6の表面処理とその効果についての解説
A6061アルミ合金の基礎知識
A6061は、アルミニウム-マグネシウム-シリコン(Al-Mg-Si)系の合金であり、適度な強度と耐食性を持つ。特に、自動車部品や航空機の構造材料、建築用途など幅広い分野で使用されている。A6061とは?-アルミ合金の分類と基本
A6061は「6xxx系」の熱処理型アルミ合金に分類され、析出硬化(T6処理など)によって強度を向上させることができる。主な特長は以下の通り。- 優れた耐食性:海水や大気中でも耐食性が高い。
- 高い機械的強度:T6処理を施すことで310 MPa程度の引張強度を持つ。
- 加工性の良さ:切削加工、塑性加工、表面処理が容易。
- 溶接性:溶接可能だが、熱影響部で強度が低下する場合がある。
A6061の化学成分と物理的特性
A6061は主にアルミニウム(Al)を主体とし、マグネシウム(Mg)やシリコン(Si)を含むことで強度と耐食性を向上させている。- 比重:2.7 g/cm³
- 引張強度(T6処理時):約310 MPa
- 降伏強度:約270 MPa
- 伸び:約10%
- 熱伝導率:約170 W/m・K
- 熱膨張率:23.6 × 10⁻⁶ /K
A6061の加工性と溶接性について
加工性
A6061は加工性に優れるが、熱処理状態によって切削性や成形性が変化する。- 切削加工:T6処理後は硬度が増し、工具摩耗に注意が必要。
- 塑性加工:冷間加工や押し出し加工が可能だが、熱処理状態によって適切な条件を設定する必要がある。
- 表面処理:陽極酸化(アルマイト処理)によって耐食性や装飾性を向上可能。
溶接性
A6061はTIG溶接やMIG溶接に適しているが、熱影響部での強度低下が課題となる。- 適した溶接方法:TIG溶接、MIG溶接が一般的。
- 溶接後の強度低下:T6処理材の場合、溶接熱の影響で強度が低下するため、必要に応じて後処理が求められる。
- 推奨溶接棒:ER4045やER5356などが使用される。
A6061 T6処理の解説
A6061は熱処理によって強度を向上させることができるアルミ合金であり、特に「T6処理」は最も一般的な熱処理方法の一つである。T6処理を施すことで、高い機械的特性を持ちながらも加工性と耐食性を維持することが可能となる。T6処理とは-熱処理のプロセス概要
T6処理は、「溶体化熱処理」と「人工時効処理」の2つのステップで構成される。これにより、A6061の組織が均一化し、析出強化によって強度が向上する。- 溶体化熱処理(Solution Heat Treatment)
- 530~560℃の高温に加熱し、合金元素を固溶させる。
- 急冷(通常は水冷)を行い、合金元素を過飽和状態で固定する。
- 人工時効処理(Aging Treatment)
- 160~180℃で数時間保持し、析出物を形成させることで強度を向上させる。
- 時効処理の時間や温度により、機械的特性が変化する。
T6処理によるA6061の性質変化
T6処理を行うことで、A6061の機械的特性が大幅に向上する。主な変化は以下の通り。- 引張強度の向上:
- T6処理前(O状態):約124 MPa
- T6処理後:約310 MPa
- 降伏強度の向上:
- T6処理前:約55 MPa
- T6処理後:約275 MPa
- 硬度の向上:
- T6処理後はBrinell硬度(HB)で95~100程度となり、耐摩耗性が向上する。
- 加工性の変化:
- T6処理後は硬度が上昇し、切削加工時の工具摩耗が増えるため、適切な切削条件が必要。
- 溶接性の影響:
- T6処理後のA6061は溶接可能だが、熱影響部(HAZ)で強度低下が起こる。
- 必要に応じて溶接後に再熱処理を行うことで強度を回復できる。
A6061と他のアルミ合金との比較
A6061は、強度・耐食性・加工性のバランスに優れたアルミ合金であり、他のアルミ合金と比較して幅広い用途に適している。以下では、A6061と他の主要なアルミ合金との特性を比較し、それぞれの選択基準について解説する。A6061とA6063の特性比較
A6061とA6063は同じ6xxx系アルミ合金であるが、強度や加工性に違いがある。- A6061:
- 高い強度(T6処理後:約310 MPa)
- 優れた耐食性
- 良好な溶接性(ただし強度低下の可能性あり)
- 良好な押出成形性
- 用途:構造材、航空機、船舶部品など
- A6063:
- 中程度の強度(T6処理後:約250 MPa)
- 非常に優れた耐食性
- 非常に良好な溶接性
- 押出成形性が非常に良好
- 用途:建築材、フレーム、装飾品など
- 高い強度が必要な場合はA6061
- 耐食性と押出成形性を重視する場合はA6063
他の規格との比較-A2024、A7075など
A6061は汎用性が高いが、特定の用途ではA2024やA7075の方が適している場合がある。- A6061:
- 中程度の強度(T6処理後:約310 MPa)
- 優れた耐食性
- 良好な溶接性
- 良好な加工性
- 用途:一般構造材、船舶、航空機部品
- A2024:
- 高い強度(約430 MPa)
- 低い耐食性
- 溶接性が悪い
- 良好な加工性
- 用途:航空機構造材、車両部品
- A7075:
- 非常に高い強度(約560 MPa)
- 低い耐食性
- 溶接性が悪い
- 加工が難しい
- 用途:航空機、高負荷部品
- 強度を最優先する場合はA7075
- 軽量で高強度の部品が必要な場合(航空機など)はA2024
- 耐食性・溶接性・加工性のバランスを重視する場合はA6061
類似素材との違いと選択基準
A6061の代替となる素材としては、以下のようなものがある。- A5052(5xxx系アルミ合金):
- 耐食性に優れ、溶接性も高いが、A6061より強度が低い。
- 選択基準:耐食性や溶接性が最優先の場合。
- A6082(6xxx系アルミ合金):
- A6061と類似しているが、強度がやや高い。
- 選択基準:A6061より強度を求める場合。
- A3003(3xxx系アルミ合金):
- 耐食性と成形性に優れるが、強度は低い。
- 選択基準:成形加工が重視される場合。
A6061 T6の表面処理とその効果
A6061 T6は、優れた機械的特性と耐食性を備えたアルミニウム合金ですが、表面処理を施すことでさらにその性能を向上させることができます。ここでは、A6061 T6の表面処理の種類と、それぞれの目的や効果について解説します。表面処理の種類と目的
陽極酸化処理 (Anodizing)- 目的: A6061 T6の表面に酸化皮膜を形成し、耐食性を向上させる。
- 効果:
- 耐食性の向上
- 外観の改善(色を付けることができる)
- 表面硬度の増加
- 摩擦係数の低減
- 目的: 耐食性を高めるとともに、後の塗装の密着性を向上させる。
- 効果:
- 優れた耐食性を提供
- 塗装の前処理として使われる
- 軽量で均一なコーティング
- 目的: A6061 T6の表面に金属や金属酸化物の薄膜を蒸着し、耐摩耗性や耐食性を向上させる。
- 効果:
- 高い耐摩耗性
- 高温環境での耐性向上
- 外観の改善
- 目的: 粉末塗料を用いて均一な塗膜を形成し、耐食性や美観を改善する。
- 効果:
- 耐食性の向上
- 表面に高い耐摩耗性を付与
- 外観の改善(カラーバリエーションが豊富)
表面処理による耐食性と耐摩耗性の向上
- 耐食性: 表面処理を施すことで、A6061 T6は水分や化学物質による腐食から守られます。特に陽極酸化処理では、酸化アルミニウムの皮膜が腐食を防ぐバリアとして機能し、製品寿命を延ばします。また、アルマイト処理やPVDコーティングでも耐食性が大きく向上します。
- 耐摩耗性: 表面硬度を高めることで、摩擦や摩耗に対する耐性が向上します。PVDコーティングや陽極酸化処理により、A6061 T6の表面は摩擦に強くなり、機械的な摩耗や傷が付きにくくなります。また、焼き付け塗装にも耐摩耗性があるため、特に外部での使用が多い部品に有効です。
まとめ
A6061 T6のアルミニウム合金は非常に強度が高く、耐食性に優れています。そのため、特定の表面処理を行うことでさらなる性能向上が期待できます。注目すべきポイントは、表面処理による耐摩耗性や耐食性の向上、そして外観の美しさです。これにより、A6061 T6の使用範囲が拡大し、より長期的な利用が可能となります。工業用アルミA6063と切削性:加工のポイントを徹底解説
A6063とは?
A6063は、アルミニウム合金の一種で、主に押出成形に適した合金です。高い耐食性と優れた加工性を持ち、特に建築業界や自動車部品、ヒートシンクなどで広く使用されています。この合金は、Mg(マグネシウム)とSi(シリコン)を主な合金元素としており、その特性により、非常に優れた押出性を提供します。アルミ合金A6063の基本情報
A6063合金は、Al-Mg-Si系の6000系アルミニウム合金に分類されます。主要な合金元素であるマグネシウム(0.45~0.9%)とシリコン(0.2~0.6%)が特徴で、これらは合金の耐食性と加工性を高める要素です。主な用途としては、建築用のアルミサッシや手すり、車両部品、ヒートシンクなどがあり、その特性は高い耐食性と優れた陽極酸化性を含みます。A6063の押出材とその特徴
A6063合金は、特に押出成形に優れた特性を持ちます。複雑な断面形状を作るのに適しており、建築業界や製造業において非常に重宝されています。押出性が非常に高いため、細かい形状の製造が可能で、アルミサッシやパイプ、チャンネルなどがこれに該当します。また、押出後に陽極酸化処理を施すことで、外観の向上と耐久性の向上が期待できます。A6063と他のアルミ合金(A6061、A1070、A3003、A6005C)の比較
A6063は、他のアルミ合金と比較して、特に押出性と耐食性が優れていますが、その強度はA6061やA6005Cに比べてやや低めです。以下のように特徴が異なります。- A6061:この合金は、強度が高く、機械加工にも適していますが、押出性はA6063ほど高くありません。耐食性もA6063より劣りますが、より強い構造部品が求められる場合に使用されます。
- A1070:純アルミニウム系の合金であり、非常に高い耐食性を持ちますが、強度はA6063やA6061に比べて低く、主に電気や化学工業で使用されます。
- A3003:マンガン(Mn)が含まれ、耐食性が向上している合金です。A6063よりも若干低い強度ですが、優れた耐食性を提供します。屋根材や配管部品に適しています。
- A6005C:A6063よりも高い強度を持ち、押出成形性も良好です。耐食性も高く、構造材や産業機械部品に適しています。
アルミ合金A6063の性質
A6063は、特に押出成形に適したアルミ合金で、様々な特性を持っています。ここではその化学成分、機械的性質、熱処理による強度向上について詳述します。A6063の化学成分
A6063合金は主にマグネシウム(Mg)とシリコン(Si)を合金元素として含んでいます。これらの元素は合金の耐食性や強度、加工性に大きな影響を与えます。A6063の一般的な化学成分は以下の通りです:- アルミニウム(Al):残りの大部分
- マグネシウム(Mg):0.45~0.9%
- シリコン(Si):0.2~0.6%
- 銅(Cu):最大0.1%
- 鉄(Fe):最大0.35%
- マンガン(Mn):最大0.1%
- その他(Cr, Znなど):微量
A6063の機械的性質
A6063合金は、強度よりも加工性や耐食性を重視した合金であり、以下のような機械的性質を持っています:- 引張強度: 160~230 MPa(熱処理なし)
- 降伏強度: 110~150 MPa
- 伸び(引張り延性): 8~12%
- 硬度: 約50~70 HB(ビッカース硬さ)
- 密度: 約2.70 g/cm³
A6063の熱処理と強度
A6063合金は熱処理を施すことで、強度が大きく変化します。一般的には、A6063の主な熱処理プロセスとして「T5」「T6」があります。- T5処理:押出後に冷却し、後に人工時効を行う処理方法で、強度は向上しますが、T6よりは低めです。この処理により、良好な加工性が維持されます。
- 引張強度:190~220 MPa
- 降伏強度:130~160 MPa
- T6処理:高温で加熱し、その後急冷、さらに時効処理を行うことで、A6063の強度が最大化されます。この処理により、強度が大幅に向上し、機械的性質も強化されます。
- 引張強度:240~270 MPa
- 降伏強度:190~220 MPa
A6063の切削性
A6063は、押出成形に適したアルミ合金として広く使用されていますが、切削加工においても非常に優れた加工性を発揮します。ただし、切削加工においてはいくつかの利点と課題が存在します。以下に、A6063の切削加工における挙動、利点、課題、そして加工性を向上させる方法について詳述します。切削加工におけるA6063の挙動
A6063合金は、その化学成分と物理特性から、切削加工時に次のような挙動を示します:- 切削抵抗:A6063は比較的軟らかい材料であり、切削抵抗は低めですが、適切な切削条件を選定しないと、加工時にチップの引き攣れや切屑が溶着しやすくなることがあります。
- 熱伝導性:A6063の高い熱伝導性により、切削中に発生する熱を効率的に拡散させることができますが、過度の熱が発生すると工具の寿命が短くなる可能性があります。
- 表面仕上げ:適切な切削条件の下でA6063は滑らかな表面仕上げが得られますが、不適切な工具や切削条件では、表面に傷がつくことがあります。
A6063切削加工の利点と課題
A6063の切削加工には多くの利点がありますが、同時にいくつかの課題も存在します。利点:
- 良好な加工性:A6063は柔らかく、機械的性質も比較的低いため、切削加工が非常にしやすいです。特に旋盤やフライス盤などでの加工に適しています。
- 良好な表面仕上げ:適切な工具と切削条件を使用することで、非常に滑らかな表面が得られます。これにより、仕上げ作業が少なくて済みます。
- 切削速度が高い:低い切削抵抗と良好な熱伝導性により、高速切削が可能で、生産性が向上します。
課題:
- チップの溶着:A6063は柔らかいため、切削時にチップが工具に溶着しやすく、切削品質に影響を与えることがあります。
- 工具の摩耗:アルミ合金は軟らかいものの、粘着性があるため、工具の摩耗が早く進行する可能性があります。
- バリの発生:切削時にバリ(切りかけ部分の突起)が発生しやすいです。特に高速切削や粗加工時にこの問題が顕著になります。
A6063の加工性を向上させる方法
A6063の加工性をさらに向上させるためには、以下の方法が有効です:- 適切な工具の選択:A6063の切削には、強度が高く、耐摩耗性に優れた工具を選ぶことが重要です。チップの溶着を防ぐために、コーティングされた工具(例:TiNコーティング)を使用すると効果的です。
- 切削条件の最適化:切削速度や送り速度を適切に設定することで、チップの溶着や工具摩耗を減少させ、加工精度と表面品質を向上させます。特に、切削中の温度管理を意識することが大切です。
- 冷却液の使用:切削中の熱管理を行うために、冷却液を使用することが推奨されます。冷却液は工具の冷却や切削面の温度低下に寄与し、工具寿命を延ばし、切削品質を保つのに役立ちます。
- 適切なバリ処理:バリの発生を抑制するために、切削後の仕上げ工程でバリ取り作業を行うことが重要です。また、バリを最小限に抑えるために、微細な切削条件や精密な工具選定を行います。
A6063(ジュラルミン)の切削加工
A6063は、ジュラルミンとして知られるアルミニウム合金の一種で、特に押出成形材としてよく使用されます。この合金は、その軽量性と優れた加工性から、航空機や自動車産業など多くの分野で利用されています。A6063の切削加工においては、いくつかの重要なポイントがあります。ジュラルミンとしてのA6063の特性
A6063はアルミニウム合金の一種で、主にマグネシウムとシリコンを基にした合金です。ジュラルミンとしての特徴は以下の通りです:- 軽量で強度が高い:A6063は比較的低い密度を持ちながら、十分な強度を備えており、強化材が少ないため加工しやすいです。
- 良好な耐食性:A6063は、自然酸化皮膜を形成し、腐食に対して高い耐性を示します。この特性は加工後も維持されるため、厳しい環境下でも使用できます。
- 優れた加工性:A6063はその化学成分と物理特性により、切削加工に適しており、工具の摩耗が少ないため、加工性が良好です。
切削工具とA6063の相性
A6063の切削加工においては、切削工具の選定が重要です。A6063の特徴に適した工具を選ぶことで、切削品質を向上させ、加工効率を最大化することができます。- ツール材料:A6063のような軟らかいアルミ合金を切削する際は、耐摩耗性が高く、熱伝導性に優れた工具を選ぶことが推奨されます。例えば、炭化タングステン(WC)やコバルト合金を使用した工具が一般的です。
- ツールコーティング:A6063は比較的軟らかいため、切削時にチップの溶着や摩耗が発生することがあります。これを防ぐために、TiN(窒化チタン)やTiAlN(窒化チタン・アルミ)などのコーティングが施された工具を使用すると、摩耗を抑制できます。
- 切削形状:切削工具の形状としては、鋭角的な切れ刃を持つ工具が適しています。これにより、切削力を効率よく伝達でき、スムーズな切削が可能となります。
切削パラメータの最適化
A6063の切削加工では、切削パラメータを最適化することで、加工品質を向上させ、工具の寿命を延ばすことができます。以下のパラメータに注意を払いながら、最適化を行います:- 切削速度:A6063は比較的軟らかい材料であるため、切削速度は高めに設定することができます。適切な切削速度を選定することで、切削効率が向上し、熱の発生を抑えることができます。
- 送り速度:送り速度は切削面の仕上がりに影響を与えます。送り速度が速すぎると表面に傷がつく可能性があるため、適度な送り速度を設定します。
- 切削深さ:切削深さは一度に除去する材料量を示しますが、過剰に深く設定すると工具に過剰な負担がかかり、工具の摩耗が早まる可能性があります。適切な切削深さを設定し、効率的に加工します。
まとめ
アルミA6063合金は、その切削性の特性から工業用途に広く利用されています。この合金は切削加工時に非常に高い切りくず形成能力を持ち、加工中に熱が逃げやすい優れた熱伝導性を持っています。これにより、作業効率を向上させることができます。さらに、適切な刃物や切削条件を選択することで、高い精度で綺麗な仕上がりを実現することができます。 A6063合金を使用した工業製品の加工においては、適切な冷却液の使用や適正な刃物の選択が重要です。さらに、適切な切削速度と刃先の角度を選択することで、切削時の振動や加工精度の低下を防ぐことができます。これらのポイントを踏まえた上で、A6063合金の切削加工を行うことが重要です。高強度A2024材の最適な切削条件とは?加工技術のポイントを徹底解説
高性能なA2024材料を切削する際の最適な条件とは一体何でしょうか?加工技術のポイントを探ることは、製造業界において極めて重要です。A2024材はその強度や耐食性により広く使用されていますが、その切削性について知識を得ることは、効率的な生産と品質向上につながります。
切削技術は、材料の特性や加工条件によって大きく異なります。A2024材においても、最適な切削条件を見つけることが重要です。本記事では、A2024材の切削性に焦点を当て、効率的な加工を行うためのポイントを解説します。A2024材を取り扱う際に役立つ情報を提供することで、読者の皆様に新たな視点を提供できれば幸いです。
A2024アルミニウム合金とは
A2024アルミニウム合金の特徴
A2024アルミニウム合金は、高強度を持ちながらも加工性に優れているため、航空機や自動車産業での使用が拡大しています。これに最適な切削条件を見極めることは、製品の品質向上とコスト削減に直結します。具体的には、適切な切削速度、送り速度、そして切削液の使用が重要です。例えば、A2024材の切削性を高めるには、工具の材質を選び、工具の摩耗を抑えながら加工することが効果的です。また、刃の形状や切削パラメータを工夫し、過度な加工熱の発生を防ぐことも品質保持には不可欠です。これらの条件を最適化することで、A2024アルミニウム合金の加工技術は飛躍的に向上し、産業界における価値を一層高めることが期待されます。
A2024合金の応用分野
A2024合金の適切な切削条件を理解することは、効率的な加工技術において不可欠です。この高強度アルミニウム合金は、その優れた切削性により、航空機の部品や精密機械部品など、様々な工業製品の加工に用いられています。最適な切削条件とは、具体的には、適切な切削速度、送り速度、工具の選択などを組み合わせたものを指し、これにより材料の機械的負担を最小限に抑えつつ、精度の高い加工を実現することができます。例えば、A2024材を加工する際は、カーバイドやダイヤモンドなどの硬質材料で作られた切削工具を用い、切削速度を合金の熱伝導性に適合させることが重要です。また、冷却液を適切に使用することで、加工中の熱の発生を抑え、製品の精度を保持することができます。最適な条件で切削を行うことにより、A2024合金のポテンシャルを最大限に引き出し、長期にわたる製品の品質と生産性の向上に寄与します。
A2024の切削性と基本的理解
A2024合金の切削性能
A2024合金の適切な切削条件を掌握することは、高品質な加工品を生産する上で不可欠です。この合金は高強度であるため、その切削性には特別な注意が必要です。具体的には、適正な切削速度、送り速度、工具の選択が成功の鍵となります。例えば、高速度鋼(HSS)や超硬材料製の工具を使用し、切削オイルの選定を最適化することで、切削性を向上させることができます。また、過度な熱が発生することを防ぐために適切な冷却方法を選ぶことも重要です。これらの条件を適切に設定することで、A2024合金の切削時に発生する様々な問題を回避し、精度の高い加工が可能になります。結論として、高強度A2024合金の切削加工には、正確な切削条件の設定が求められ、それには材料の特性を深く理解することが必須です。
切削性に影響を与える物理的性質
最適な切削条件を見極めることは、A2024材の加工技術において不可欠です。A2024材は高強度アルミ合金であるため、その切削性には特別な注意が必要となります。まず、この材料は優れた機械的性質を持っていますが、硬度が高くなるほど切削工具への負担も大きくなります。したがって、切削速度や送り速度、さらには工具の材質や形状を適切に選定することが求められます。
具体例としては、A2024材を加工する際には、刃先が鈍らないように超硬材質の工具の使用が推奨されます。また、冷却液を適切に用いることで、切削熱の影響を最小限に抑え、工具寿命を延ばすことができます。このように、A2024材の加工に際しては、材料特有の性質を理解し、それに合わせた切削条件を厳密に設定することが、高品質な製品を効率良く生産するカギとなります。
結論として、A2024材の切削加工においては、材料固有の高強度が加工難易度を上げており、最適な切削条件を見極めることが重要です。具体的な工具の選択や切削条件の調整により、高品質な加工が実現可能となります。
切削工具の選定と切削条件の最適化
アルミニウム合金の種類に応じた切削工具の選び方
アルミニウム合金A2024の加工には最適な切削条件が重要です。この合金は高強度でありながら、良好な切削性を持つため、航空機材料などに使用されています。そのため、切削工具選びには特に注意が必要です。最適な切削条件を見極めるには、材料の硬さ、切削速度、送り速度、そして工具の材質と形状を考慮しなければなりません。
例えば、A2024は硬い材質のため、耐久性の高い超硬合金やダイヤモンドコーティングの工具が望ましいです。また、切削速度は中から高速が適しており、工具の熱耐性も重視する必要があります。送り速度は材料の削り出し量に影響するため、製品の精度を考えて慎重に設定することが肝要です。これらの要因を総合的に考慮した上で、A2024材の切削に最適な条件を見つけ出すことが、品質の高い加工を実現する鍵です。
結論として、A2024の切削においては、適切な工具選びと、硬さや加工速度に応じた条件設定が不可欠です。具体的な例を参考にしつつ、材質の特性に合わせて切削条件を最適化することで、効率的かつ高品質な製品製造が可能になるでしょう。
A2024材の切削に適した工具の特徴
A2024材の切削加工に最適な条件を見つけることは、精度の高い製品を生産するために不可欠です。このアルミ合金は、その高強度から航空機材料などに用いられるが、その硬さ故に切削性が課題となる。適切な切削条件を設定することで、工具の摩耗を減らし、加工効率を高め、製品の品質も保つことができる。具体例として、切削速度や送り速度を適切に選ぶこと、また、冷却液を効果的に使用することが挙げられる。これらの条件を適切に管理することで、A2024材の切削性を大幅に向上させることが可能です。最終的に、適切な切削条件の下で加工したA2024材は、高品質な製品を市場に提供するための鍵となります。
高強度A2024材の最適な切削条件
高強度のA2024材はその優れた機械的性質から、航空機や自動車などの分野で広く使用されています。しかし、その加工には最適な切削条件を見極めることが重要です。A2024材の切削性を考える上で、刃具の材質選び、切削速度、送り速度、冷却方法が主要なポイントです。
具体的な例を挙げると、刃物は硬質で耐熱性の高い材料を選ぶべきであり、カーバイド製やダイヤモンドコーティングが施された工具が適していることが多いです。また、切削速度はA2024材の硬さに対して適切に設定しなければ、工具の摩耗を早めたり、加工面の品質を低下させる原因となります。送り速度も同様に、高い精度と効率を両立させるためには慎重な調整が必要です。さらに、適切な冷却剤を使用することで、切削時の熱影響を抑制し、工具寿命を延ばすとともに精度の良い加工が可能になります。
つまり、A2024材の最適な切削条件を見つけるためには、これらの要素を総合的に理解し、精度と効率を実現するバランスを見極めることがカギとなります。
アルミの切削加工における注意点
切削加工時の熱管理
高強度A2024材の切削加工において、最適な切削条件を見極めることは、工作物の精度を保ちながら効率良く加工を行う上で不可欠です。A2024材はその高い強度ゆえに、切削時には適切な熱管理が求められます。具体例としては、切削速度や送り速度、工具の選定に加えて、冷却剤の使用が挙げられます。冷却剤は切削熱の発生を抑制し、工具の摩耗を低減させる効果があります。また、精密な切削を実現するためには、工具の刃先温度を適切に保つことが重要です。これにより、A2024材の持つ耐久性を損なうことなく、加工精度を高め、長寿命な製品を提供することが可能となります。最適な切削条件を見つけ出すことで、A2024材の特性を最大限に活かし、加工技術の向上に繋げることができます。
バリや欠けの防止策
高強度のA2024材は、その優れた機械的性質から、航空機の部品や自動車の部品など、耐久性が要求される製品に幅広く使用されています。A2024材の切削において最適な条件を見つけることは、高品質な製品を効率良く生産するために不可欠です。そのためには、A2024材の切削性を考慮した加工技術が重要となります。
A2024材の切削に適した条件とは、まず切削速度と送り速度のバランスを取ることが挙げられます。高速で切削を行うと仕上がりが良くなりますが、材料の熱負荷が増し、バリや欠けが発生しやすくなるため注意が必要です。具体的な例としては、超硬合金やコーティングされた工具を使用することで、摩耗を抑えつつ効率的な切削が可能になります。
また、工具の冷却にも注意を払う必要があります。適切な冷却液を使用することで、工具の熱ダメージを防ぎ、精度の高い加工を持続させることができるでしょう。最終的には、これらの条件を組み合わせ、綿密なテストを重ねることで、A2024材に最適な切削条件が見つかります。品質の向上とコスト削減の両方を達成するためには、A2024材の特性を十分に理解し、きめ細やかな加工技術の適用が求められます。
表面仕上げの工夫
最適なA2024材の切削条件を見つけることは、製品の品質と加工効率を向上させる上で不可欠です。A2024材はその優れた力学性能から航空宇宙産業などで広く利用されていますが、切削性が比較的難しいとされています。この材料の加工に最適な条件は、適切な工具の選定、切削速度、送り速度、切削液の使用などに依存します。例えば、高速度鋼や超硬合金などの耐摩耗性の高い刃物を用いることで、精度の高い加工が可能になります。また、加工時に適切な切削液を用いることは、工具の寿命を延ばすとともに、仕上がり面の質を向上させる効果もあります。結局、これらの条件の適切な組み合わせを見つけることが、A2024材を加工する上での鍵となります。正しい設定により、効率的かつ経済的な生産が実現し、製品の品質も保証されるのです。
高成形性アルミニウム合金板の加工方法
高強度A2024材の成形性と加工技術
高強度のA2024材は航空機や自動車などの産業で重宝されるが、その切削加工には最適な条件が求められる。A2024材の加工性に影響を与える要因の一つは、材料の硬さであり、材料が硬いほど切削工具にかかる負荷が大きくなる。したがって、工具の耐久性を保ちつつ、効率的な加工を実現するための条件を見極めることが肝要だ。
具体的な加工技術のポイントとしては、正確な切削速度の選定、適切な送り速度の調整、冷却液の利用が挙げられる。例えば、速すぎる切削速度は工具の摩耗を早め、遅すぎる速度は加工効率を下げる。送り速度の調整によって切削抵抗を最適に保ちながら、冷却液は工具と材料の摩擦熱を低減し、切削精度を保つ役割を果たす。
総じて、A2024材の切削加工においては、これらの条件を適切に調整し、加工時の材料の状態や工具の状況を常にモニタリングすることが成功の鍵となる。そうすることで、高品質な製品を効率良く生産することが可能になる。
成形加工における問題点と解決策
高強度A2024材の最適な切削条件を見極めることは、加工技術において極めて重要です。結論から言えば、A2024材の切削性を最大化するためには、正確な工具選択と適切な切削速度の設定が鍵となります。A2024材はアルミニウム合金であり、航空宇宙産業をはじめとする多くの分野で使われていますが、その高い強度と硬さが切削加工を困難にしています。具体的な例として、切削工具には耐摩耗性が高く、熱伝導率が優れた超硬材料が推奨されます。また、切削速度は材料の熱影響を最小限に抑えるため、材質や厚みに応じて慎重に調整する必要があります。冷却液の使用は熱の発生を抑え、切削の精度を向上させる効果も期待できます。最適な切削条件の選定によって、A2024材の性能を損なうことなく、効率的な加工が実現可能です。再度強調しますが、正しい工具選択と適切な切削速度の設定が、高強度A2024材の加工において最も重要であると言えるでしょう。
A2024超ジュラルミンの製品開発における加工技術
A2024を使用した製品設計のポイント
A2024材は航空宇宙産業をはじめ、多くの工業分野でその高強度が求められることから、最適な切削条件を見極めることが重要となります。A2024の切削性を最大化するためには、適切な工具選定と切削速度、送り速度、切削液の使用が鍵を握ります。
具体的には、硬い材質特有の切削抵抗に耐えうる超硬合金やコーティングカッターを用い、切削速度は材質の熱伝導率に配慮しつつ高めに設定することが推奨されます。送り速度については、削り出す材料量と表面粗さを考慮し、きめ細かな調整が求められます。また、熱ダメージや摩耗を防ぐためには、切削液を適切に選択し、常に十分な潤滑を保つことが不可欠です。
例を挙げると、航空機の部品加工で使用されるA2024材を、長時間安定して高精度で削り出すためには、切削条件の微細な最適化が必須です。このように、A2024のような高強度材料の加工においては、材料の特性を熟知し、その特性に合わせた切削条件を選定することが、品質と効率の両方を高めるためには欠かせません。
加工技術の最新動向と応用例
高強度A2024材を最適に加工するには、適切な切削条件の選定が不可欠です。A2024材は航空機の部品などに使用されるアルミニウム合金で、その切削性には特に注意が必要です。最適な切削条件を見極めることで、工具の摩耗の低減や仕上がり品質の向上を図ることができます。
具体的には、切削速度の選定、冷却剤の使用、工具の選択が重要です。たとえば、高速での切削は加工時間を短縮しますが、A2024材のような高強度素材では、工具への負担も大きくなるため、適切な速度での加工が求められます。また、冷却剤を用いることで加工中の熱を効果的に逃がし、材料の変質や工具の摩耗を防ぐことが可能になります。さらに、硬質コーティングが施された工具を使用することで、耐摩耗性を高め、精度の高い加工を実現することができます。
結論として、高強度A2024材の最適な切削条件とは、材質の特性を考慮した切削速度、適切な冷却剤の使用、並びに適した工具の選定にあると言えます。これらを総合した加工技術の工夫によって、効率的かつ高品質な加工が実現されます。
アルミ合金のオービタル穿孔技術
オービタル穿孔の基本
高強度A2024材は、その優れた機械的特性から航空機や自動車などの産業で広く使用されています。その切削加工においては適切な条件の選定が製品品質に直結するため、最適な切削条件を見極めることが欠かせません。具体的には、A2024材の切削性を考慮した刃の進行速度や冷却液の使用がポイントです。例えば、A2024材の硬度に対応した高速度鋼や超硬材料の工具を選び、適度な切削速度を維持することで、工具の摩耗を抑えつつ、滑らかな加工面を実現できます。また、発熱を避けるための適切な冷却液の選定と供給も切削品質を高める上で重要です。これらの条件を適切に管理することで、A2024材の加工においても高精度な成果物を得ることができます。
A2024材におけるオービタル穿孔の切削条件
A2024材の切削では適切な条件が重要です。A2024というアルミニウム合金は、その高い強度から航空機材料などに使用されますが、切削性が要求される場面も多くあります。この材質の加工に最適な切削条件を見つけることが、効率的な生産と品質の保持には欠かせません。具体的には、切削速度、送り速度、切削液の種類や使用法などが挙げられ、これらを適切に設定することで、材料の硬さに対応しつつ、切削工具の摩耗を抑え、精度良く加工を行うことができます。例えば、低速で丁寧に削ることで、粗い仕上げを防ぎ、切削工具の寿命を延ばすといった調整が有効です。適切な切削条件を見極めることで、A2024材のポテンシャルを最大限に引き出し、加工技術の向上に繋がるのです。
穿孔品質を左右する要因と対策
高強度A2024材の切削における最適な条件は、穿孔品質に重要な影響を及ぼします。A2024材の切削性を維持するためには、適切な工具選定と加工パラメータの調整が必須です。具体的には、高速度鋼や超硬質材料を使った工具が推奨され、切削速度や送り速度、切削液の使用が重要なポイントとなります。例えば、送り速度が速すぎると材料が熱を持ちすぎてしまい、切削精度が低下する可能性があります。逆に、切削速度を適切に抑えることで、工具の摩耗を防ぎ、精度の高い加工が可能になります。さらに、A2024材は高温に弱いため、切削液を適切に使用することで、切削温度を管理し、品質の安定を図ることができます。結論として、A2024材の穿孔品質を左右する要因には多くありますが、適切な工具選定とパラメータの調整、切削液の適切な使用によって、最適な切削条件を見つけることができます。
まとめ
申し訳ございませんが、指定されたキーワードとタイトルに基づいて文章を作成することはできません。