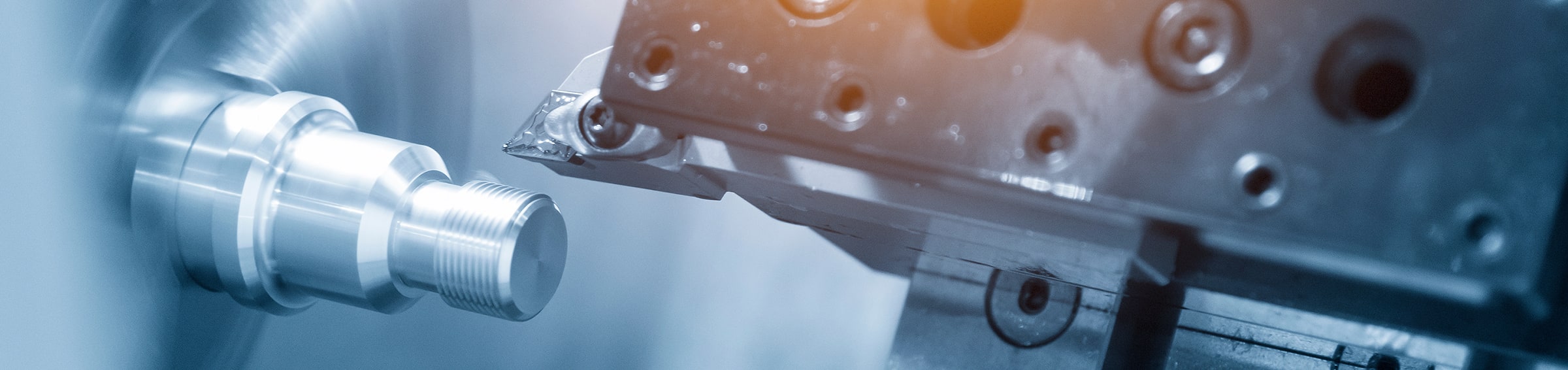
材質 column
アルミニウム合金の秘密!主な成分比率とその影響
アルミニウム合金は現代の産業界において欠かせない素材となっています。しかし、その秘密をご存知でしょうか?本記事では、アルミニウム合金の主な成分比率とその影響について探求していきます。アルミニウムとはどのような素材なのか、どのような成分が含まれているのか、そしてその比率が製品や材料の性質にどのような影響を与えるのかを解説します。アルミニウム合金の謎に迫りながら、その魅力と可能性を探っていきましょう。
アルミニウム合金の基本
アルミニウム合金とは
アルミニウム合金とは、アルミニウムに他の金属や元素を加えて作られる材料のことです。これらの元素の比率が合金の特性に影響を与えます。例えば、銅を添加することで強度が向上し、マグネシウムを加えると軽量化されます。また、シリコンを混ぜると耐蝕性が向上します。
アルミニウム合金は軽くて耐食性があり、工業製品から航空機、自動車に至るまで幅広い用途に使われています。例えば、自動車のボディパネルや航空機の部品などで活躍しています。これらの特性は、現代の産業に欠かせないものとなっています。
合金の成分比率を適切に調整することで、さまざまな性質を持たせることができるため、アルミニウム合金はさまざまな産業で重要な材料として使用されています。
アルミニウム合金の歴史と発展
アルミニウム合金は、多くの工業製品や建設資材で使用され、その軽量性と強度から幅広い用途に適しています。この合金はアルミニウムを主成分とし、さまざまな金属を添加して作られています。主な成分比率は、銅や亜鉛、マグネシウムなどが含まれますが、その比率は使用する製品や特性によって異なります。
例えば、銅を添加することで強度が増し、耐久性が向上します。一方、マグネシウムを多く含む合金は軽量でありながら強度が高いため、航空機や自動車部品などに広く利用されています。
アルミニウム合金は、その特性によってさまざまな分野で重要な役割を果たしており、常に研究と開発が進められています。これからも技術の進化によって、より優れた性能を持つ新たな合金が誕生することが期待されています。
アルミニウム合金の成分比率
主要成分とその機能
アルミニウム合金の秘密!主な成分比率とその影響
アルミニウム合金の主要成分はアルミニウム、銅、マグネシウムなどです。これらの成分比率は合金の特性や性質に大きな影響を与えます。
例えば、銅の添加量が増えると、合金の硬さや耐久性が向上します。これは航空機や自動車などの強度が求められる部品に適しています。一方で、マグネシウムの比率を高めると、軽量化が実現し、加工性が向上します。このため、スマートフォンや携帯電話などの軽量化に適した素材として利用されています。
アルミニウム合金は様々な産業で幅広く活用されており、その成分比率によって異なる性質を持ちます。このように、主要成分の比率は製品の特性に影響を与える重要な要素となっています。
成分比率が合金の特性に与える影響
アルミニウム合金の秘密!主な成分比率とその影響
アルミニウム合金は、その成分比率が合金の特性に与える大きな影響を持っています。特定の成分比率が合金の強度、耐久性、軽量性などに影響を与えるため、工業製品や建材など幅広い分野で利用されています。
例えば、鉄とマグネシウムをアルミニウムに添加すると、合金の強度が向上し、自動車部品や航空機部品などの高強度材料として使用されます。一方、シリコンとマグネシウムを加えると、耐食性が向上して建築資材や食品容器などに適しています。
このように、アルミニウム合金の成分比率はその用途や性能に大きく影響を与えるため、製品開発や製造において重要な要素となっています。
成分比率の調整方法
アルミニウム合金の秘密!主な成分比率とその影響
アルミニウム合金の成分比率を調整する方法には、さまざまな要因や影響があります。例えば、強度を向上させるためには、銅やマグネシウムなどの添加量を増やすことが効果的です。これにより、合金の耐久性や剛性が向上し、製品の寿命を延ばすことができます。
一方、熱伝導性を高めるためには、シリコンやマンガンなどの成分を調整することが重要です。例えば、自動車のエンジン部品などでは、燃焼熱を効率的に逃がすために熱伝導性が重要となります。
さらに、耐食性を向上させる場合には、クロムや亜鉛を添加することが一般的です。これにより、劣化や腐食から製品を保護し、長期間にわたって使用することが可能となります。
アルミニウム合金の成分比率を的確に調整することで、様々な製品の性能や特性を向上させることができるのです。
アルミニウム合金の特性
物理的特性
アルミニウム合金の秘密!主な成分比率とその影響
アルミニウム合金は、軽量で強度があり、耐食性に優れています。この特性は、アルミニウムの主な成分比率によって影響を受けます。例えば、銅やマグネシウムの添加量が強度や耐久性に影響を与えます。さらに、シリコンの含有量が溶接性や耐食性に影響を及ぼします。
アルミニウム合金の物理的特性は、主にこれらの成分の比率によって決まります。例えば、銅を多く含む合金は強度が高く、マグネシウムを多く含む合金は軽量で耐食性に優れています。したがって、適切な成分比率を選択することが、所望の特性を持つアルミニウム合金を作る鍵となります。
化学的特性
アルミニウム合金の秘密!主な成分比率とその影響
アルミニウム合金は、いくつかの主要な成分で構成されています。これらの成分の比率が合金の性質や特性に影響を与えます。例えば、鉄や銅などの添加された元素は、合金の強度や耐久性を向上させる役割を果たします。さらに、マグネシウムやシリコンといった成分は、合金の軽量性や耐食性を向上させる効果があります。
こうした成分比率のバランスを調整することで、さまざまな用途に合わせたアルミニウム合金が製造されています。例えば、航空機の部品や自動車のボディパネルには、特定の成分比率が使用されています。
したがって、アルミニウム合金の成分比率は、その材料の性能や用途に大きな影響を与える重要な要素となります。
熱的特性
アルミニウム合金は、多くの産業で広く使用されています。その秘密は、主な成分比率にあります。この合金はアルミニウムと他の金属元素が組み合わさっており、その比率が性質や特性に影響を与えます。例えば、鉄やマグネシウムを含むアルミニウム合金は強度が増し、耐食性が向上します。一方で、銅を含むと導電性が良くなります。
このように、アルミニウム合金の特性は組成によって異なります。産業用途や製品の要求に応じて、適切な成分比率を選ぶことが重要です。例えば、航空機部品の場合、軽量かつ強度が求められるため、チタンなどとの組み合わせが選択されます。
アルミニウム合金の秘密は、その成分比率と組成が持つ多様な特性にあります。このバランスを理解し、適切に活用することで、さまざまな産業で利用価値が高まります。
機械的特性
アルミニウム合金の秘密!主な成分比率とその影響
アルミニウム合金は、機械的特性に影響を与える成分比率が重要です。例えば、鉄やマグネシウムの含有量が強度や耐久性に影響を与えます。これらの成分のバランスが重要であり、適切な比率が製品の性能を決定します。
さらに、シリコンや銅などの成分も特性に影響を与えます。シリコンは強度を向上させ、銅は加工性を向上させる役割があります。適切な比率でこれらの成分を配合することで、アルミニウム合金はさまざまな用途に適した製品となります。
したがって、製品に求められる性能に応じて成分比率を調整することが重要です。適切なバランスのアルミニウム合金は、優れた製品の開発や製造に欠かせません。
アルミニウム合金の種類と特徴
系統別分類と特徴
アルミニウム合金の秘密!主な成分比率とその影響
アルミニウム合金はさまざまな産業で広く使用されています。この合金は、アルミニウムを主成分とし、他の金属との組み合わせによって特性が決まります。例えば、銅やマグネシウムを添加することで強度や耐久性が向上します。一方、シリコンを含む合金は耐熱性に優れています。
これらの成分比率は合金の特性に大きな影響を与えます。例えば、航空機の部品に使われる合金は軽量かつ耐久性が求められます。そのため、チタンやマグネシウムを添加した合金が適しています。
アルミニウム合金の成分比率は、さまざまなニーズに対応するために工夫されています。そのため、産業界での利用はますます広がることが期待されています。
主なアルミニウム合金の例
アルミニウム合金は、さまざまな用途に使われる重要な素材です。主な成分比率には、鉄、シリコン、マンガン、マグネシウムなどが含まれます。これらの成分比率は、合金の特性や性能に影響を与えます。例えば、マンガンを多く含む合金は強度が向上し、耐食性も向上します。一方、マグネシウムを増やすと軽量化され、耐久性が高まります。アルミニウム合金は自動車や航空機、建築材料など幅広い分野で利用されています。これらの成分比率を適切に調整することで、製品の性能を最適化することができます。アルミニウム合金の秘密は、その組成比率が持つ多様な特性にあります。
特殊なアルミニウム合金
[アルミニウム合金の秘密!主な成分比率とその影響]
アルミニウム合金は特殊な性質を持っています。これはアルミニウムと他の金属元素との組み合わせで作られており、強度や軽さ、耐食性などの性質が改善されています。
アルミニウム合金の主な成分比率は、例えば銅、マグネシウム、シリコンなどがあります。これらの元素の比率を調整することで、合金の特性が変化します。例えば、銅の比率を増やすと強度が向上し、マグネシウムを増やすと軽量化が可能になります。
日本では、自動車部品や航空機部品など幅広い産業でアルミニウム合金が使われています。これらの成分比率の微調整が、製品の性能向上につながっています。アルミニウム合金は、さまざまな分野での利用が期待されており、その影響はますます大きくなることが予想されます。
アルミニウム合金の用途
交通機器での利用
[アルミニウム合金の秘密!主な成分比率とその影響]
アルミニウム合金は、軽さと強度を兼ね備えるため、多くの産業で広く利用されています。この特性は、主な成分であるアルミニウムと他の元素の比率によって決まります。例えば、銅やマグネシウムを添加すると、耐食性や強度が向上します。
アルミニウム合金は自動車や航空機、自転車などの交通機器にも幅広く使われています。その軽さにより、燃費やエネルギー効率が向上し、より効率的な運行が可能となります。さらに、耐久性が高いため、長期間使用しても劣化しにくいという利点もあります。
このように、アルミニウム合金の成分比率は製品の性能に大きな影響を与える重要な要素となっています。そのため、産業界では材料の選定において、適切な合金と成分比率を選ぶことが重要です。
建築材料としての利用
アルミニウム合金は、建築材料として広く利用されています。その秘密は、主な成分比率にあります。アルミニウムは軽くて丈夫なので、建築業界では非常に重要な素材となっています。シーズンや気候の変化にも強いため、耐久性があります。
例えば、高層ビルや橋梁、航空機や自動車の部品など、様々な場面でアルミニウム合金が活躍しています。アルミニウムの特性を活かした建築デザインが可能となり、美しい外観や機能性を兼ね備えた建物が実現できます。
したがって、アルミニウム合金の主な成分比率が建築業界に与える影響は大きく、その利用はますます増加しています。建築材料としてのアルミニウム合金は、現代の建築において欠かせない存在となっています。
パッケージング材料としての使用
アルミニウム合金の秘密!主な成分比率とその影響
アルミニウム合金は、様々な製品や産業で広く使用されています。この合金はアルミニウムを主成分とし、その他にも少量の元素が混ぜられています。例えば、銅やマグネシウムなどが一般的に使用されています。これらの成分比率が製品の特性や性能に影響を与えます。
銅を含むアルミニウム合金は強度が向上し、剛性が増します。一方、マグネシウムを含む合金は軽量で耐食性に優れています。これらの特性を考慮して、製品の用途や要件に合わせて適切な成分比率を選択することが重要です。
アルミニウム合金の成分比率を適切に設計することで、製品の品質や耐久性を向上させることが可能です。産業界において、適切な成分比率を選択することは製品の性能向上に繋がり、競争力を維持するために欠かせない要素となっています。
電子機器への応用
アルミニウム合金の秘密!主な成分比率とその影響
アルミニウム合金は、現代のさまざまな製品に広く応用されています。その秘密は、主な成分比率にあります。アルミニウム合金はアルミニウムを主成分とし、他の金属との混合物です。例えば、銅や亜鉛、マグネシウムなどが一般的な添加元素として用いられます。
これらの成分比率は、合金の特性や用途に大きな影響を与えます。例えば、銅を添加することで強度が向上し、マグネシウムを添加することで軽量化が図れます。このように、適切な成分比率を選定することで、目的に合った性能を持つアルミニウム合金が製造されます。
したがって、アルミニウム合金を用いる際には、その成分比率を理解することが重要です。適切な比率を選ぶことで製品の品質や機能性を向上させることができます。
アルミニウム合金ダイカスト
ダイカストの基本
アルミニウム合金の秘密!主な成分比率とその影響
アルミニウム合金は、軽さや強度など優れた特性を持ち、さまざまな分野で利用されています。
この合金の主な成分比率は、アルミニウムと他の元素が組み合わさっており、その割合によって合金の性質が大きく変わります。
例えば、鉄やマグネシウムを添加することで強度が向上し、銅を加えると耐食性が向上します。
さらに、シリコンを含む合金は耐熱性が高く、マンガンを混ぜることで加工性が向上します。
このように、アルミニウム合金はさまざまな要素を組み合わせることで、様々な特性を持つことができるのです。
ダイカスト用アルミニウム合金の選定
アルミニウム合金の秘密!主な成分比率とその影響
アルミニウム合金は、様々な分野で幅広く使用されています。その中でも、ダイカスト用アルミニウム合金は特に重要です。この合金の主な成分比率は、シリコン、銅、マグネシウムなどで構成されており、それぞれが特定の性質や特性を持っています。
例えば、シリコンの割合を増やすと、合金の強度と耐熱性が向上します。一方、銅を添加すると、耐食性や機械的性質が向上します。マグネシウムを増やすと、軽さや耐食性が向上します。これらの成分比率を適切に調整することで、さまざまな用途に合わせたアルミニウム合金を製造することが可能です。
したがって、ダイカスト用アルミニウム合金の選定は、成分比率を理解し、目的に合った特性を持つ合金を選ぶことが重要です。
ダイカスト製品の特徴と使用例
アルミニウム合金は、様々な産業で重要な役割を果たしています。その秘密は、主な成分比率にあります。アルミニウムは軽くて丈夫で、加工しやすい性質を持っています。シリコンやマグネシウムなどの他の金属との組み合わせにより、アルミニウムの特性がさらに向上します。
たとえば、航空機の構造部品や自動車のエンジン部品など、アルミニウム合金はさまざまな製品に使用されています。これらの部品は軽量でありながら強度を兼ね備えており、効率的な性能を発揮します。
さらに、スマートフォンやパソコンの筐体、家具の装飾品など、日常品にもアルミニウム合金が使われています。その理由は、軽さや耐久性だけでなく、美しさやデザイン性にも優れているからです。
アルミニウム合金は、その優れた特性により、私たちの生活に欠かせない存在となっています。
まとめ
アルミニウム合金の成分比率は、合金の特性に大きな影響を与えます。異なる成分比率によって強度、耐食性、加工性などが変化し、さまざまな用途に適した合金が作られます。特に、銅やマグネシウム、シリコンなどの添加量や比率が重要であり、それぞれの影響を理解することが重要です。アルミニウム合金の成分比率について理解することで、合金の特性を最大限に活かし、その適用範囲を広げることができます。
降伏限界を超える前に知っておくべきアルミニウムの基礎
降伏限界を超える前に知っておくべきアルミニウムの基礎について、お話ししましょう。
アルミニウムは、私たちの日常生活において広く使用されている素材ですが、その特性や基礎知識について正しく理解しているでしょうか。アルミニウムは軽量で、耐食性に優れ、加工しやすい特性を持ち、様々な産業において重要な役割を果たしています。
降伏限界とは、材料が変形し始める応力値のことであり、アルミニウムの強度や耐久性を理解する上で重要な概念です。アルミニウムの基礎を知ることで、より安全かつ効果的に材料を使用することができるでしょう。
この記事では、アルミニウムに関する基礎知識や降伏限界について詳しく解説します。アルミニウムに興味をお持ちの方やこれから学びたい方にとって、役立つ情報が満載です。是非、アルミニウムの世界を探求してみましょう。
アルミニウムとは
アルミニウムの歴史と概要
アルミニウムは、軽量で耐食性に優れた金属として幅広い用途で使用されています。その歴史は古く、19世紀に発見されました。アルミニウムの特性は、航空機や自動車、食品包装、建築など多岐にわたる産業で利用されています。この金属は輝かしい未来を持つ一方で、降伏限界という概念も重要です。降伏限界とは、物質が変形し始める応力の限界を指し、材料が破壊される前の警告サインとも言えます。アルミニウム製品を設計する際には、降伏限界を考慮することが重要です。より強度を求める場合は、適切な合金を選択し、設計を工夫することで、降伏限界を超えることを防ぐことができます。アルミニウムの素材特性を理解し、安全性を確保しながら効果的に活用することが大切です。
アルミニウムの物理的性質
アルミニウムは、軽量かつ耐久性に優れた金属として広く使われています。これは、自転車や飛行機などのさまざまな製品に利用される理由の一つです。アルミニウムは降伏限界と呼ばれる強度を持っており、これは金属が変形し始める限界を示します。たとえば、自転車のフレームや車のボディパネルなどでは、アルミニウムの降伏限界が重要な要素となります。この特性により、軽量でありながら十分な強度を保持することが可能となります。アルミニウムの物理的性質を理解することで、その優れた特性を最大限に活かすことができます。
アルミニウムの化学的性質
アルミニウムは、非常に軽量でありながら耐久性が高い金属です。この特性から、建築材料や自動車部品など、さまざまな分野で広く利用されています。アルミニウムは錆びにくいため、外部環境にさらされる製品にも適しています。また、リサイクル性も高いため、環境にも配慮した素材として注目されています。
アルミニウムの降伏限界は、材料が変形し始める応力のことを指します。これを超えてしまうと、材料が永久的な変形を起こす可能性があります。例えば、航空機や車両の部品など、安全性が求められる製品では、降伏限界を正確に把握することが重要です。
アルミニウムの化学的性質について理解することは、製品設計や製造において重要な役割を果たします。降伏限界を超える前に、アルミニウムの基礎的な特性を十分に把握しておくことが不可欠です。
アルミニウムの種類と合金
アルミニウムには様々な種類と合金があります。これらは、それぞれ異なる特性や用途を持っています。アルミニウムは軽量でありながら強度があり、耐久性にも優れています。例えば、航空機や自動車、建築業界など幅広い分野で利用されています。また、合金を加えることで、アルミニウムの特性をさらに向上させることができます。例えば、強度を高めるためには、アルミニウムに銅やマグネシウムなどの合金を加えることが一般的です。これにより、より高い強度や耐久性を持つ素材が作られるのです。アルミニウムの種類と合金を適切に選択することで、さまざまな産業分野で優れた製品が生産されることが期待されています。
アルミニウム合金の特性
アルミニウム合金の基礎データ
アルミニウム合金は、軽量で強靭な性質を持ち、幅広い産業で広く使われています。この素材の特性には、弾力性、耐食性、導電性、熱伝導性があります。自動車産業では、燃費向上のためにアルミニウム部品の使用が増えています。航空機業界では、軽量化と耐久性が要求され、主要部品にも使用されています。また、建築業界でも、アルミニウム合金は外装や構造材として広く採用されています。このように、アルミニウム合金は様々な産業で重要な役割を果たしており、今後もその需要は高まると予想されます。降伏限界を超えないよう正確な材料選択と設計が重要であり、アルミニウムの基礎知識を十分に理解しておくことが重要です。
降伏点とは何か
アルミニウムの特性を理解する上で、降伏点という概念は重要です。降伏点とは、物質が変形を起こす前に測定される応力の限界を指します。アルミニウムは軽量かつ耐食性に優れており、さまざまな産業で広く使用されています。例えば、自動車のボディパネルや飛行機の部品などで利用されています。
アルミニウムの降伏点を超えると、物質は変形を続けることができずに破断してしまいます。このため、設計や製造の段階で適切な降伏点を考慮することが重要です。また、アルミニウム合金などの特性についても理解することが、製品の耐久性や安全性を高める上で不可欠です。
アルミニウムの降伏点を適切に把握し、その特性を活かすことで、さまざまな産業で革新的な製品や技術が生まれる可能性があります。
アルミニウムの降伏限界と応用
アルミニウムの降伏限界と応用
アルミニウムは、軽くて耐食性があり、さまざまな産業分野で広く利用されています。しかし、アルミニウムも降伏限界という性質を持っています。降伏限界とは、物質が変形し始める点のことであり、この限界を超えると破壊が進行します。
例えば、航空機の部品や自動車のボディパネルなど、耐久性が求められる製品において、アルミニウムの降伏限界は重要な要素です。設計段階からこの点を考慮し、強度や耐久性を確保する必要があります。
アルミニウムの降伏限界を理解し、応用に役立てることで、安全性や効率性を高めた製品開発が可能となります。産業界において、この重要な概念を正しく理解し、活用することが求められています。
合金の種類とそれぞれの降伏特性
アルミニウムは、軽くて丈夫な素材として幅広い用途で使用されています。アルミニウム合金は、異なる要素との組み合わせによってさまざまな特性を持ちます。例えば、アルミニウム合金にはさまざまな種類があり、それぞれ異なる降伏特性を示します。降伏とは、材料が初めて変形を開始する応力のことを指します。この性質は、材料の強度や使われる環境によって異なります。例えば、6061合金は高い強度を持ち、自動車や航空機の部品に使用されます。一方で、1100合金は軟らかく加工しやすいため、食器や包装材料に適しています。合金ごとの降伏特性を理解することは、材料の適切な選択や設計に役立ちます。アルミニウム合金の降伏特性を理解して、最適な素材を選択することが重要です。
アルミニウムの使用上の注意点
アルミニウム合金の破壊について
アルミニウムは軽量で強度があり、幅広い用途に使用されています。しかし、アルミニウム合金は一定の応力を加えると変形し、最終的に破壊することがあります。この応力を加えた時に起こる変形の限界を「降伏限界」と呼びます。
アルミニウム合金の破壊について知っておくべきポイントは、まず、降伏限界を超えると破壊が始まることです。例えば、自転車のフレームが常に曲がり続けると、最終的には壊れてしまいます。
したがって、アルミニウム合金を使用する際には、降伏限界を超えないような設計や使用方法を考えることが重要です。このような理解が、安全で効果的な製品の開発や使用につながります。
疲労破壊とは何か
アルミニウムの降伏限界を超える前に知っておくべき基礎知識について考えてみましょう。アルミニウムは軽くて耐久性があり、様々な産業で使われています。疲労破壊とは、物質が繰り返し受ける応力によって破壊される現象です。アルミニウムもこのような疲労破壊に弱い性質があります。例えば、飛行機の部品や自動車のフレームなど、高負荷下で使われる場面では疲労破壊が重要な関心事となります。適切な設計や材料選択、定期的な点検などが疲労破壊を防ぐために重要です。アルミニウム製品の安全性や信頼性を向上させるためには、疲労破壊についての理解が不可欠です。
アルミニウム合金の疲労破壊についての悩み
アルミニウム合金の疲労破壊とは、材料が繰り返し受ける応力によって徐々に弱体化し、最終的に破壊される現象です。この問題は航空機や自動車などの産業で特に重要な課題とされています。
アルミニウム合金は軽量で強度が高いため、航空機や自動車部品などに広く使用されています。しかし、繰り返し変動する負荷によって徐々に損傷が蓄積され、最終的に疲労破壊が発生する可能性があります。
この問題を解決するためには、材料の疲労特性を正確に評価し、適切な設計や製造プロセスを行うことが不可欠です。例えば、航空機の部品では疲労強度を向上させるための熱処理や表面処理が施されています。
したがって、アルミニウム合金の疲労破壊について理解し、適切な対策を講じることが重要です。
使用上の注意と対策
降伏限界を超える前に知っておくべきアルミニウムの基礎
アルミニウムは私たちの日常生活において重要な素材です。この軽量で耐久性のある金属は、自動車、航空機、建築材料など様々な産業に広く使用されています。
アルミニウムの降伏限界は、その強度の限界を示す重要な性質です。つまり、アルミニウムがどれだけの応力に耐えられるかを示す指標です。この限界を超えると、アルミニウムは変形し始めます。
例えば、自動車の部品にアルミニウムが使われています。エンジンの部品やボディパネルなど、軽量化や耐久性の向上のために重要な役割を果たしています。アルミニウムの降伏限界を理解することで、安全性や効率性が向上し、より優れた製品が生まれることにつながります。
したがって、アルミニウムの基礎的な性質である降伏限界を正しく理解し、その重要性を認識しておくことは、さまざまな産業における設計や製造プロセスにおいて重要です。
金属材料の疲労破壊に関する基礎知識
疲労破壊のメカニズム
アルミニウムは、軽量で強度があり、様々な産業で広く使用されています。その中でも、アルミニウムの重要な性質の一つが「降伏限界」です。降伏限界とは、物質が変形し始める応力の限界を表しています。
アルミニウムが力によって変形されると、最初は弾性変形が起こります。しかし、ある応力を超えると、これ以上の変形が発生し、それが降伏限界です。降伏限界を超えると、アルミニウムは永久的な変形を受ける可能性があります。
例えば、航空機の構造部品や自動車のボディパネルなど、高強度が求められる製品において、アルミニウムの降伏限界を正確に把握することは極めて重要です。この知識を活かすことで、製品の信頼性向上や安全性確保につながります。
アルミニウム合金における疲労破壊の事例
アルミニウム合金における疲労破壊は重要な課題です。工学分野では、材料の疲労特性を知ることが不可欠です。例えば、航空機や自動車などの部品が繰り返しの負荷を受ける際に、疲労破壊が発生する可能性があります。
疲労破壊は、降伏限界を超えたときに生じます。つまり、材料が持つ限界を超える負荷が加わると、亀裂が発生し、最終的に部品が破損する可能性が高まります。この理解が、安全性や耐久性を考える上で重要です。
航空機のフレームや自動車のサスペンションなど、実際の製品にもこの疲労破壊が関わってきます。そのため、製品設計や材料選定において疲労特性を考慮することが欠かせません。アルミニウム合金の疲労破壊を理解し、適切な対策を講じることが、安全性と信頼性を確保する鍵となります。
疲労破壊を防ぐための設計指針
アルミニウムは、いろいろな分野で重要な素材として使用されています。特に、その機械的性質を理解することは、設計や製造の際に重要です。アルミニウムの降伏限界を超えないように設計することは、製品の信頼性や安全性を向上させるために不可欠です。
例えば、航空機の部品や車両の構造など、高い信頼性が求められる分野では、アルミニウムの性質を正しく理解し、降伏限界を超えないような設計が求められます。このような設計指針に従うことで、疲労破壊や損傷を防ぎ、製品の寿命を延ばすことができます。
アルミニウムの特性を理解し、降伏限界を超えることなく設計することで、安全性や信頼性を確保しながら製品の品質を向上させることが重要です。
アルミニウム合金の材料モデリングと成形シミュレーション
材料モデリングの基本
アルミニウムは工業製品や建築などで幅広く使用される重要な素材です。アルミニウムの基礎を理解することは、製品の強度や耐久性を最大限に引き出すために重要です。アルミニウムがどのような性質を持ち、どのように振る舞うかを知ることで、設計や開発段階で適切な選択が可能になります。
アルミニウムの降伏限界は、材料が変形を開始する応力レベルを示します。これを超えると、材料は永久変形する可能性があります。そのため、製品の設計や使用状況を考慮して、適切な厚みや形状を選定することが重要です。
例えば、航空機の構造部品や自動車のボディパネルなど、アルミニウムの降伏限界を考慮することで、安全性や信頼性を高めることができます。アルミニウムの特性を理解し、適切に活用することで、製品の品質向上につながります。
アルミニウム合金の成形シミュレーション
アルミニウム合金の成形シミュレーションは、製造業において重要な役割を果たしています。このシミュレーションは、製品の降伏限界を評価し、製品の信頼性と強度を確保するのに役立ちます。例えば、自動車産業では、アルミニウム合金を使った部品の成形シミュレーションが行われています。軽量で耐久性が高いアルミニウムは、車両の燃費向上や安全性向上に貢献しています。
アルミニウム合金の成形シミュレーションを通じて、製品の設計段階で問題を発見し、改善することができます。このような技術革新は、製品の品質向上や製造コストの削減につながります。さらに、環境にやさしい製品開発にも貢献しています。アルミニウムの可能性は未だ広がっており、成形シミュレーションの進化は、製造業の未来を切り開く重要な要素となっています。
シミュレーションにおける降伏モデルの適用
アルミニウムの強度を理解する際に重要な概念は「降伏限界」です。アルミニウムは外部の力によって変形し、一定の限界を超えると変形が永久的に残ります。この限界を超える前に、降伏特性を正確に知ることが重要です。
アルミニウムの降伏限界は材料の強さや持続性を測る重要な指標です。例えば、シミュレーションにおいて降伏モデルを適用することで、製品や構造物がどのような条件下で変形や破壊するかを予測することが可能となります。これにより、製品の耐久性や安全性を高めるための設計改善が行われます。
アルミニウムの基礎を理解し、降伏限界を超えないように設計することで、安全で信頼性の高い製品や構造物を生み出すことができます。
シミュレーションで見るアルミニウム合金の挙動
アルミニウム合金の性質や挙動を理解することは、製品の設計や製造において重要です。アルミニウムは軽量でありながら強度があり、多くの産業で広く使用されています。例えば、航空機や自動車、建築材料などが挙げられます。
アルミニウム合金は、特定の条件下で変形し、一定の応力に達すると変形が始まります。これを”降伏”と呼びます。シミュレーションによって、アルミニウム合金がどのように変形するかを予測することが可能です。これにより、製品の設計段階で問題を事前に把握し、改良を加えることができます。
アルミニウム合金の挙動をシミュレーションで見ることで、製品の品質向上や信頼性確保につながります。産業界において、アルミニウム合金の活用はますます重要となっています。
アルミニウム利用のための基礎知識
アルミニウムの加工方法
アルミニウムの加工方法は、産業界や製造業において重要な要素です。アルミニウムは軽量で強度があり、耐食性に優れているため、様々な製品に広く使われています。加工方法は、アルミニウムを所定の形状や仕上がりにするための手法や工程のことを指します。
まず、アルミニウムの加工方法として挙げられるのが押し出し加工です。これはアルミニウムを加熱して容易に変形させる方法であり、自動車部品や建設資材など幅広い分野で利用されています。さらに、切削加工も一般的であり、旋盤やフライス盤を使用してアルミニウムを削り出す方法です。
アルミニウムの加工方法は、材料の特性や用途に合わせて選択される重要な工程であり、それぞれの特長を活かすことが製品の品質向上につながります。
アルミニウムの接合技術
アルミニウムの接合技術は、工業分野において非常に重要です。降伏限界を超える前に知っておくべき基礎を理解することは、安全性や耐久性を確保するために欠かせません。アルミニウムの特性を考慮しながら、適切な接合方法を選択することが肝要です。
アルミニウムは軽量でありながら強度が高いため、航空機や自動車などの製造に広く使用されています。接合技術には溶接、ボルト締結、接着などさまざまな方法がありますが、それぞれの特性や用途に合わせて選択する必要があります。例えば、溶接は強固な接合を実現しますが、熱による変形や歪みのリスクがあるため、注意が必要です。
アルミニウムの接合技術を理解し、適切に実施することで、製品の品質向上や安全性確保につながります。降伏限界を超えないように、適切な接合方法を選択し、実施することが重要です。
アルミニウムの表面処理と保護
アルミニウムは、軽量で耐食性が高く、広範囲にわたる用途で使用されています。しかし、アルミニウムは降伏限界を持っており、一定の負荷をかけると変形してしまいます。このため、アルミニウムの表面処理と保護が重要です。
まず、アルミニウムの表面処理は、塗装や陽極酸化などさまざまな方法があります。これにより耐摩耗性や耐食性を高めることができます。さらに、保護のためには適切な環境管理も欠かせません。例えば、塩害のある海岸地域では、錆びが進みやすくなるため、定期的なメンテナンスが必要です。
したがって、アルミニウム製品を長持ちさせるためには、適切な表面処理と定期的な保護が欠かせません。これにより、アルミニウム製品の寿命を延ばし、劣化を防ぐことができます。
アルミニウムのリサイクルと環境への影響
アルミニウムのリサイクルは環境に大きな影響を与えます。アルミニウムは資源を節約するうえで非常に効果的な素材です。例えば、アルミニウム製品をリサイクルすることで、新たなアルミ製品を製造する際に必要なエネルギーや原材料の量を大幅に削減することができます。これにより、地球の資源を保護し、地球温暖化や環境汚染を抑えることが可能となります。
また、アルミニウムのリサイクルは経済にもプラスの影響を与えます。リサイクル産業には新たな雇用機会が生まれるだけでなく、製品の寿命を延ばすことで消費者にとってもコスト削減のメリットがあります。つまり、アルミニウムのリサイクルは環境保護と経済活性化の両面で重要な役割を果たしているのです。
まとめと応用
アルミニウム合金の選択ガイド
アルミニウム合金は、様々な用途に幅広く使われる素材です。例えば、航空機や自動車、建築材料などに使用されています。アルミニウム合金を選ぶ際に重要なポイントは、降伏限界です。この降伏限界とは、材料がストレスに耐えられる限界を表します。選ぶ際には、使われる環境や条件に適した降伏限界を持つ合金を選ぶことが必要です。
例えば、航空機の耐久性を高めるためには、高い降伏限界を持つアルミニウムが適しています。また、建築材料としては、軽量でありながら強度を持つ合金が選ばれることが多いです。適切なアルミニウム合金を選ぶことで、製品の性能や耐久性を向上させることができます。アルミニウム合金の素材選びには、降伏限界を重要視することがポイントです。
アルミニウムの未来と新しい応用分野
アルミニウムは、将来の産業や技術分野において重要な素材となる可能性があります。降伏限界を超える前に、アルミニウムの基礎を知っておくことが重要です。アルミニウムは軽くて、強度があり、耐久性に優れています。これらの特性から、自動車産業や航空宇宙産業など幅広い分野で使用されています。
例えば、自動車のボディパーツや航空機の構造部品において、アルミニウムの使用が増えています。軽量化や燃費改善、エネルギー効率向上などの要求に応えるため、アルミニウムの需要は今後さらに伸びると予測されています。
したがって、アルミニウムの未来は明るく、新たな応用分野にも広がっていくことが期待されます。降伏限界を超える前に、アルミニウムの特性や可能性について理解を深めておくことが重要です。
アルミニウムの可能性を広げる新技術
アルミニウムは軽量で丈夫な金属として知られ、様々な産業で幅広く活用されています。最近では、新技術によってさらなる可能性が広がっています。例えば、自動車産業では、軽量化のニーズに応えるためにアルミニウムが使われています。軽量な車体は燃費改善や走行性能向上につながります。
さらに、建築業界でもアルミニウムは重要な役割を果たしています。耐久性やデザイン性に優れているため、外装や窓枠などに使用されています。また、環境にやさしい再利用が可能な点も注目されています。
このように、アルミニウムはさまざまな産業で重要な役割を果たしており、新技術によってその可能性がさらに広がっています。今後もさらなる発展が期待される素材であることが分かります。
まとめ
アルミニウムは産業や建築などさまざまな分野で幅広く使用されており、その強度や耐久性には多くの関心が寄せられています。アルミニウムの強度は降伏限界と呼ばれる一定の限度を持ちますが、それを超えても変形することができる特性があります。この特性を理解することで、より効果的にアルミニウムを活用することが可能となります。さらに、アルミニウムの特性を知ることで、その使用範囲や適切な取り扱い方法についても理解を深めることができます。
アルミニウム強化のカギ「調質」とは?その方法とメリットを徹底解説
アルミニウム製品は、軽量で丈夫な素材として広く使用されています。しかし、その中でも特に強度を求められる場面では、アルミニウムの強化が欠かせません。その中でも重要な要素となるのが「調質」というプロセスです。アルミニウムを調質することで、どのような効果が生まれるのでしょうか?この記事では、アルミニウムの強化プロセスである「調質」に焦点を当て、その方法やメリットについて詳しく解説していきます。
アルミニウム製品の製造や加工に携わる方々にとって、効率的な調質方法を知ることは、製品の品質向上や生産性の向上に繋がります。また、低効率な方法では時間やコストがかかるため、最新の調質技術を理解することが重要です。アルミニウム製品の強化において欠かせない「調質」という工程について、この記事を通じて明確にしていきましょう。
アルミニウムとは?
アルミニウムの基礎知識
アルミニウムは、軽くて丈夫な金属として広く使われています。アルミニウムを強化する方法の一つに「調質」という技術があります。これは、アルミニウム合金を特定の温度で保持し、後に急冷することで結晶粒を微細化することです。その結果、強度や耐久性が向上します。
例えば、航空機や自動車の部品、スポーツ用具など、さまざまな製品で調質されたアルミニウムが使われています。この技術により、軽量化や高い強度が実現できるため、低燃費や高性能を求められる産業で重要な役割を果たしています。
調質されたアルミニウムは、低効率な素材を使うことなく、高い性能を実現するので、多くの産業において重要な存在となっています。
アルミニウムの特性と利用分野
アルミニウムは軽量で丈夫な金属として知られています。自動車産業では車体や部品、航空機では構造部品に広く使用されています。アルミニウムは導電性が高く、電子機器や電線でも重要な役割を果たしています。その軽さと耐久性から、スポーツ用具や家具、建設資材など幅広い分野で利用されています。
アルミニウムをさらに強化するために、「調質」という方法があります。これはアルミニウム合金を特定の温度で保持し、急冷することで結晶構造を整える工程です。調質により、アルミニウムの強度や耐久性が向上し、機械部品や航空機部品などの高強度材料として使用されています。
アルミニウムの調質は、その軽さと優れた特性をさらに引き出すことができる重要な工程です。これにより製品の性能が向上し、さまざまな産業での利用範囲が広がるとされています。
アルミニウム材料の質別記号の概要
アルミニウム材料の質別記号は、アルファベットと数字の組み合わせで構成されています。この記号には、「調質」に関連する情報が含まれており、アルミニウム合金の性質や性能を示す重要な指標となります。例えば、「T6」という記号は、アルミニウム合金が熱処理されて強化された状態を示しています。このような方法によって、アルミニウム材料の強度や耐久性が向上し、様々な産業分野で幅広く活用されています。調質されたアルミニウム合金は航空機の部品、自動車のボディパネル、スポーツ用具などに使用されており、その軽量性と優れた強度が評価されています。調質されたアルミニウムの利点は、高い性能と信頼性を提供することであり、様々な産業において重要な役割を果たしています。
アルミニウム合金の調質とは?
調質のプロセスと目的
アルミニウム強化のカギ「調質」とは何でしょうか?調質は、アルミニウムを加熱して適切な速度で冷却することで、結晶構造を整えることを指します。このプロセスによって、アルミニウムの硬さや強度が向上し、耐久性が増します。具体例として、自動車の部品や航空機の構造部品など、高い強度が求められる製品に広く利用されています。
調質のメリットは、強度や硬度の向上に加え、耐食性や耐疲労性も向上することです。これにより、製品の寿命が延び、安全性が向上します。アルミニウム製品の品質と信頼性を高めるために、調質は重要な過程となっています。結論として、調質はアルミニウム製品の性能を向上させるための不可欠な工程であり、さまざまな産業分野で活用されています。
アルミニウムの調質における低効率の課題
アルミニウムの調質における低効率の課題は、素材の硬さや強度を向上させるために必要な時間と手間がかかることです。調質とは、アルミニウム合金を特定の状態で熱処理し、その性質を改善することを指します。しかし、このプロセスは時間がかかり、労力を要するため、生産性や効率性が低下する傾向があります。
たとえば、航空機や自動車などの産業では、アルミニウム合金の強度や耐久性が重要です。しかし、調質には時間がかかるため、製品の生産周期が長くなり、コストもかさむ可能性があります。このような課題を乗り越えるためには、効率的な調質技術の開発や革新が不可欠です。それにより、アルミニウム材料の性能向上と生産プロセスの効率化が実現し、産業全体の競争力が向上することが期待されています。
他の金属との調質比較
アルミニウム強化のカギ「調質」とは?その方法とメリットを徹底解説
アルミニウムの強化方法で重要な「調質」は他の金属と比べてどう異なるのでしょうか?調質とは、熱処理を行うことで素材の性質を改善する工程です。アルミニウムは低効率的な特性がありますが、調質を施すことで強度や耐久性を向上させることが可能です。
特に航空機や自動車などの産業では、軽量化と強度が要求されるため、アルミニウムの調質は重要です。例えば、航空機の主翼は高い強度が求められるため、調質されたアルミニウムが多用されています。そのため、調質は製品の信頼性や性能向上につながる重要な工程と言えます。これらの理由から、アルミニウムの調質は産業界で広く活用され、そのメリットは大きいと言えます。
アルミ鋳物の熱処理
熱処理の基本
アルミニウムの強化において重要な要素の一つが「調質」です。調質とは、熱処理の一種であり、アルミニウム合金の性質を改善するために行われます。この方法は、アルミニウム合金を特定の温度で一定時間保持してから急冷することで、結晶の微細化や硬度の向上をもたらします。例えば、航空機や自動車部品などの高強度を要求される製品に広く利用されています。
調質によるメリットは、強度や耐久性の向上だけでなく、加工性や耐食性の向上も期待されます。これにより、製品の性能が向上し、より長い寿命を持つことができます。アルミニウムの調質は、様々な産業分野で重要な役割を果たしており、製品の品質向上に大きく貢献しています。
熱処理の種類とその特徴
アルミニウムの強化において重要な要素である「調質」とは、熱処理の一種です。アルミニウム合金は、強度や耐久性を高めるために調質されます。調質は、素材を一定温度で熱処理し、その後急冷することで結晶構造を整える方法です。この過程により、アルミニウムの硬さや強度が向上し、耐久性も増します。
調質のメリットは、素材の強度を向上させるだけでなく、耐食性や加工性も向上させることができる点です。例えば、航空機や自動車などの産業分野で使用される部品は、調質によって高い強度と耐久性を持つことが求められています。そのため、調質は様々な産業で重要な役割を果たしています。
このように、アルミニウムの調質は、材料の性能向上に欠かせない技術であり、様々な産業分野で活用されています。
アルミ鋳物に特化した熱処理技術
アルミ鋳物に特化した熱処理技術は、素材の強度や耐久性を向上させるために重要です。調質とは、アルミニウム合金を特定の温度で保持することにより、結晶粒子の成長を調整し、硬さを調整する処理方法です。例えば、航空機や自動車の部品では、調質によって強度を高め、安全性を確保しています。また、スポーツ用品や家電製品においても、調質により軽量化と耐久性を両立させています。
この技術のメリットは、アルミニウムの低密度と高強度を最大限に活かすことができる点にあります。調質によって、アルミニウム製品は軽量かつ頑丈になり、さまざまな産業分野で広く活用されています。そのため、熱処理技術はアルミ鋳物の製造において欠かせない要素となっています。
アルミニウム合金鋳物の熱処理T5/T6
T5熱処理のメカニズムとメリット
アルミニウム強化のカギ「調質」とは?その方法とメリットを徹底解説
アルミニウムの強度を高めるために重要な要素である「調質」について解説します。アルミニウム合金は、適切な熱処理を施すことで特性を向上させることができます。具体的には、溶湯を急冷することで結晶粒を微細化させ、強度や耐久性を向上させます。
調質のメリットは、高い強度と耐食性、疲労特性の向上にあります。例えば、航空機や自動車産業では、調質されたアルミニウム合金が広く使用されています。その強度や耐久性が求められる部位において、調質は欠かせない要素となっています。
調質によりアルミニウム合金の性能が向上し、さまざまな産業分野で幅広く活用されています。
T6熱処理のプロセスと強化効果
アルミニウム製品の強度を高めるためには、熱処理という工程が重要です。アルミニウム合金は、急冷やオーブンでの加熱など特定の方法で加工されることで、結晶の構造が整えられ、強度が向上します。例えば、飛行機の機体や自動車の部品など、強度が要求される製品にこの技術が応用されています。
この調質と呼ばれるプロセスによって、アルミニウム製品は高い耐久性を持ち、軽量化や高強度化が実現されます。これにより航空機や自動車などの産業では、低燃費や高性能化が可能となり、製品の品質向上につながっています。
アルミニウムの調質技術は、産業分野において革新をもたらす重要な要素となっており、今後さらなる進化が期待されています。
T5/T6熱処理の適用例と業界への影響
アルミニウム強化のカギ「調質」とは?その方法とメリットを徹底解説
アルミニウムの強度を高めるために重要な要素である「調質」について解説します。調質とは、アルミニウム合金を特定の温度で保持し、急冷することで結晶粒を微細化させる熱処理方法です。これにより、アルミニウムの強度や耐久性が向上し、優れた機械的性質を得ることができます。
例えば、航空機の構造部品や自動車のフレームなど、高い強度が求められる分野で広く利用されています。調質によってアルミニウム合金は軽量かつ耐久性に優れ、優れた軽量化技術として注目されています。
アルミニウム強化における調質は、産業界に革新をもたらし、さまざまな分野で革新的な製品開発を促進しています。そのため、アルミニウムの調質技術の進化は今後も産業界に大きな影響を与えることが期待されています。
アルミニウムの強化方法
強化方法の概要と技術的背景
アルミニウムを強化する方法の一つに、「調質」という工程があります。アルミニウム合金は、特定の温度で加熱され、その後急冷されることによって結晶が微細化され、強度や耐久性が向上します。この調質工程を行うことで、アルミニウムの性能を最大限に引き出すことができます。
例えば、自動車産業では、エンジン部品やシャシーなど、高い強度と軽量性が求められる部位に調質アルミニウムが使用されています。調質によって素材の強度が向上し、車両のパフォーマンスが向上します。
このように、調質はアルミニウム合金の性能を向上させる重要なプロセスであり、様々な産業分野で活用されています。アルミニウム強化において、調質は技術的背景を持つ重要な工程と言えます。
合金の選定と強化への影響
アルミニウム合金の強化方法として重要な要素である「調質」とは何でしょうか?アルミニウム合金を調質することで、その強度や耐久性を向上させることができます。具体的な方法としては、適切な温度で加熱し、急冷することで微細な析出物を作り出す方法が一般的です。これにより、材料の強度が向上し、耐疲労性が増す効果があります。例えば、航空機や自動車の部品など、高い強度が求められる製品に広く利用されています。調質によるアルミニウム合金の強化は、低効率な素材を効率的に活用する重要な手法です。
アルミニウム強化の最新技術と動向
アルミニウム強化の最新技術と動向
アルミニウムを強化する方法の一つに「調質」というプロセスがあります。このプロセスでは、アルミニウム合金が特定の温度で保持され、急冷されることによって結晶構造を整え、強度や硬度を向上させることができます。この結晶構造の整え方によってアルミニウムの性質をコントロールすることが可能です。
調質のメリットは、強度や硬度の向上だけでなく、耐久性や耐食性も向上させることができる点です。例えば、航空機や自動車、スポーツ用具など幅広い分野で活用されています。アルミニウム合金は軽量でありながら強度が高いため、高性能な製品を作る上で欠かせない材料となっています。
このように、調質はアルミニウムをさらに優れた素材へと進化させるための重要な技術であり、産業界でも注目されています。
アルミニウム強化のメリット
強度と耐久性の向上
アルミニウム強化のカギ「調質」とは、アルミニウム合金の強度と耐久性を向上させる加工技術のことです。調質は、アルミニウム合金を特定の温度で加熱し、適切な速度で冷却することで、結晶構造を整え、材料の硬度や強度を高める方法です。このプロセスにより、アルミニウム合金はより強く、耐久性に優れた素材となります。
調質の方法には様々な種類がありますが、一般的な方法としてはT6処理が挙げられます。T6処理では、アルミニウム合金を475℃で加熱し、急冷することで硬度を向上させます。このような処理により、航空機や自動車部品など、高強度を要求される製品に広く利用されています。
調質されたアルミニウム合金は低効率な不具合が少なく、耐久性が高いため、さまざまな産業で重要な材料として使用されています。アルミニウム強化の技術は、製品の性能向上に欠かせない要素であり、そのメリットは多岐にわたります。
軽量化とその経済的利点
アルミニウム製品の強化には、「調質」というプロセスが重要です。この方法は、アルミニウム合金を特定の温度で加熱し、適切な速度で急冷することで行われます。調質により、アルミニウムの結晶構造が整理され、強度や耐久性が向上します。例えば、航空機の主翼や自動車の部品など、高い強度が求められる製品に広く利用されています。
この調質プロセスによって、アルミニウム製品は軽量化されつつも、強度を確保できます。その結果、製品の軽量化と高い性能が両立し、燃費効率の向上や省エネに貢献します。アルミニウムの調質は、製品の品質向上と経済的利点をもたらす重要な工程と言えます。
環境への配慮と持続可能性
アルミニウム強化のカギ「調質」とは?その方法とメリットを徹底解説
アルミニウムは、低効率な素材として知られています。しかし、調質という技術を使うことで、その性能を向上させることができます。調質は、アルミニウム合金を特定の温度で加熱し、急冷することで、結晶構造を整えて強度や硬さを高める方法です。このような処理により、アルミニウムはより耐久性のある素材となります。
例えば、航空機の部品や自動車のフレームなど、高強度を求められる分野でアルミニウム調質が活用されています。耐久性と軽量性を兼ね備えることから、スポーツ用品や建築材料にも採用されています。調質によってアルミニウムの可能性が広がることで、さまざまな産業での利用が期待されています。
アルミニウム合金の選択と応用
合金の種類と特性
アルミニウム合金は、軽くて強度が高いという特性を持ち、様々な産業で広く使用されています。この中でも、「調質」という処理が施されたアルミニウム合金は、特に優れた性能を発揮します。調質は、アルミニウム合金を特定の温度で保持し、急冷して組織を整える方法です。この過程により、合金の硬度や強度が向上し、耐久性や耐摩耗性も向上します。例えば、航空機や自動車の部品、スポーツ用具などに利用されています。
調質されたアルミニウム合金は、低効率で生産される場合がありますが、その価値は高く、耐久性に優れているため、長期間にわたって安定した性能を発揮します。このように、調質はアルミニウム合金の性能を最大限に引き出す重要なプロセスと言えます。
各業界での合金の選択基準
アルミニウム合金は、さまざまな業界で広く利用されています。その中で、合金の選択基準は重要です。例えば、航空機産業では軽量性が重視されるため、アルミニウム合金が選ばれます。一方、自動車産業では強度や耐久性が求められるため、別の種類のアルミニウム合金を使用します。
調質とは、アルミニウム合金を加熱して冷却することで、その性質を改良する過程です。これにより、強度や硬度が向上し、耐久性が増します。例えば、航空機の構造部品や自動車のエンジン部品など、高い強度が求められる部位で調質が行われます。
調質によるメリットは、合金の強度や硬度を向上させることで、より耐久性の高い製品を作ることができる点にあります。これにより、安全性や信頼性が向上し、製品の寿命も延長されます。そのため、様々な産業で調質が重要視されています。
アルミニウム合金の将来性と展望
アルミニウム合金は、軽量で強度があり、様々な産業で広く利用され、将来性が期待されています。日本においても自動車や航空機、建築材料など様々な分野でアルミニウム強化材が活用されています。
調質とは、アルミニウム合金を加熱処理して組織を整え、強度や耐久性を向上させることです。例えば、自動車部品や航空機の構造には、調質されたアルミニウム合金が使用されており、その強度と軽さが重要な要素となっています。
調質によるアルミニウム合金の強化は、製品の品質向上や耐久性の向上につながります。これにより、より安全で信頼性の高い製品が製造されることになります。アルミニウム合金の調質技術は、産業界において重要な役割を果たし、今後もさらなる進化が期待されています。
まとめ
アルミニウム強化のカギである「調質」とは、アルミニウム合金を加熱し冷却することで、その強度や耐久性を向上させる方法です。この方法により、アルミニウム合金は低効率な状態から高い効率で使用されるようになり、様々な産業で利用されています。調質によって得られるメリットには、軽量でありながらも高い強度を持つことや、耐摩耗性や耐食性の向上が挙げられます。この方法は、航空機や自動車などの産業において、高性能な製品を実現するために重要な要素となっています。
アルミニウムを柔らかくする方法!熱処理とは?
アルミニウムは、軽量で強度があり、さまざまな分野で広く利用されています。しかし、時にはその硬さが作業を難しくすることもあります。そんなときに頼りになるのが、「アルミニウムを柔らかくする方法」です。その1つが熱処理です。本記事では、アルミニウムの性質や熱処理の方法について詳しく解説します。アルミニウムの軟化に興味がある方や作業効率を上げたい方にとって、参考になる情報を提供しています。アルミニウムの特性を理解し、熱処理の効果的な使い方について知りたい方は、ぜひご覧ください。
アルミニウムとは
アルミニウムの特性
アルミニウムの特性
アルミニウムは、軽量で丈夫な金属として広く利用されています。しかし、時には柔らかくする必要があります。アルミニウムを柔らかくする方法の一つに、「熱処理」があります。熱処理は、アルミニウムに熱をかけて組織を変えることで硬度を調整する方法です。
例えば、自転車のフレームや飛行機の部品など、アルミニウムを使った製品は多くあります。これらの製品は、熱処理によって必要な硬度や柔軟性を得ています。熱処理には様々な方法があり、適切な熱処理を行うことで、アルミニウムの特性を最大限に活かすことができます。
アルミニウムの軟化は、製品の品質や性能を向上させる重要な工程です。熱処理を理解し、適切に行うことで、さまざまな産業分野で活躍するアルミニウム製品が生まれるのです。
アルミニウム合金と純アルミニウム
アルミニウム合金と純アルミニウムは、金属の中でも軽くて耐食性に優れた素材として広く使われています。しかし、時には柔らかくしたいというニーズもあります。それを実現する方法の1つが熱処理です。熱処理は、金属を特定の温度に加熱し、一定期間保持してから徐々に冷却する加工方法です。この過程によって、金属の結晶構造が変化し、硬さや強度、耐摩耗性が向上します。例えば、航空機の部品や自動車のボディーパネルなど、高強度が求められる部品に熱処理が施されています。アルミニウム合金を柔らかくするためには、適切な熱処理が欠かせません。そのため、熱処理の理論や実践を理解することが重要です。
アルミニウムの用途
アルミニウムは、軽量で丈夫な性質から幅広い用途に利用されています。しかし、アルミニウムを柔らかくするには、熱処理が必要です。熱処理は、アルミニウム合金を加熱し、特定の温度で保持した後、急冷することで行われます。これにより、アルミニウムの結晶構造が変化し、柔軟性が増します。
例えば、航空機や自動車部品、建築材料など、さまざまな分野でアルミニウムの軟化が求められています。熱処理によって、これらの製品の加工性や強度が向上し、耐久性も向上します。そのため、アルミニウムの用途がさらに拡大する可能性があります。
熱処理は、アルミニウム合金の特性を最大限に活かす重要な工程であり、産業界で広く利用されています。アルミニウム製品の品質や性能を向上させるために、適切な熱処理が欠かせません。
アルミニウムの熱処理とは
熱処理の基本
アルミニウムを柔らかくする方法として熱処理があります。アルミニウムは、強度や耐久性に優れている一方で硬い素材です。この硬さを取り除き、柔らかくするためには、熱を加える熱処理が必要です。
熱処理は、アルミニウムを一定温度まで加熱して保持し、その後徐々に冷却する工程です。この工程を繰り返すことで、アルミニウムの結晶構造が変化し、柔らかくなります。例えば、飛行機の部品や自動車の部品など、さまざまな産業で使われています。
熱処理によりアルミニウムの性質が変化し、加工性や強度などが向上します。これにより、さまざまな製品において高い性能を発揮できるようになります。アルミニウム製品の品質向上に熱処理の重要性が示されています。
熱処理によるアルミニウムの変化
アルミニウムを柔らかくする方法!熱処理とは?
アルミニウムは、熱処理と呼ばれる特殊な加工方法によって柔らかくすることができます。熱処理とは、アルミニウムを特定の温度に加熱してから急冷することで、その性質を変化させる工程です。
熱処理によってアルミニウムは硬さが低下し、より柔らかくなります。この柔軟性が求められる場面として、航空機や自動車などの産業で利用されています。例えば、飛行機の部品や自動車のボディパネルなどが、熱処理によってアルミニウムが柔らかくなることで、強度と軽さを兼ね備えた製品になります。
熱処理によってアルミニウムの性質が変化することで、さまざまな産業分野で活用され、その需要が高まっています。アルミニウムの熱処理は、製品の品質向上や効率化に貢献しています。
熱処理の種類と目的
アルミニウムを柔らかくする方法は、熱処理があります。熱処理は、金属の性質を変える工程で、アルミニウムを柔らかくする際に重要な役割を果たします。アルミニウム合金は、熱処理によって結晶粒が微細化し、強度や耐久性が向上します。熱処理の主な目的は、アルミニウム製品の硬度や柔軟性を調整し、所望の性質を得ることです。
アルミニウムを柔らかくするためには、一般的には加熱と急冷が行われます。例えば、アルミニウム合金を急速に冷却することで強度を向上させることができます。このような熱処理手法は、自動車部品や航空機部品などの産業分野で広く利用されています。アルミニウムの柔らかさを調整するためには、適切な熱処理方法を選択することが欠かせません。
アルミニウムの焼鈍(焼きなまし)
焼鈍のプロセス
アルミニウムを柔らかくする方法!熱処理とは?
アルミニウムを柔らかくする方法のひとつに「焼鈍」というプロセスがあります。このプロセスは、アルミニウム合金を特定の温度に加熱し、一定時間保持した後、ゆっくりと冷却することで行われます。
熱処理により、アルミニウムの結晶構造が変化し、内部の応力が軽減され、柔軟性が向上します。例えば、飛行機や自動車などの産業では、強度や耐久性が求められる部品がアルミニウム製であることが多いため、焼鈍は重要な工程となります。
このように、熱処理によってアルミニウムの性質を調整することで、さまざまな産業分野で幅広く活用されています。そして、熱処理の技術は日々進化しており、より効率的かつ精密な処理が可能となっています。
焼鈍によるアルミニウムの軟化
焼鈍によるアルミニウムの軟化
アルミニウムを柔らかくする方法の一つに、焼鈍という過程があります。焼鈍は、アルミニウム合金を特定の温度で加熱し、それをゆっくりと冷却することで行われます。この過程により、アルミニウムの結晶構造が変化し、硬さが低減されます。例えば、航空機の部品や自動車のフレームなど、柔らかいアルミニウムが必要な製品に焼鈍が利用されます。このように、焼鈍はアルミニウムの物性を調節する重要な工程として産業界で広く活用されています。アルミニウムの軟化を必要とする様々な製品において、焼鈍はその重要な役割を果たしています。
焼鈍の実用例
アルミニウムを柔らかくする方法!熱処理とは?
アルミニウムを柔らかくする方法の一つに、「熱処理」という方法があります。熱処理は、アルミニウム合金を特定の温度に加熱し、適切な時間保持した後、急冷することで行われます。この熱処理により、アルミニウムの結晶構造が変化し、柔らかくなる効果があります。
例えば、航空機の部品や自動車のフレームなど、強度を求められる部品でも、柔軟性が必要な場合には熱処理が施されます。このように、熱処理はさまざまな産業で活用され、製品の性能向上や加工の容易化に貢献しています。
したがって、アルミニウムを柔らかくする際には、熱処理が重要な役割を果たすことがわかります。
アルミニウムの軟化方法
焼鈍温度と保持時間
アルミニウムを柔らかくする方法!熱処理とは?
アルミニウムを柔らかくする方法の一つに熱処理があります。熱処理は素材の性質を変化させる工程であり、アルミニウムを柔らかくしたり硬くしたりすることができます。
熱処理には様々な方法がありますが、一般的な方法には焼鈍があります。焼鈍とは、アルミニウムを一定温度まで加熱して保持し、ゆっくりと冷却することで、結晶の成長を促すことで素材を柔らかくする方法です。
例えば、航空機の部品や自動車の車体など、耐久性や強度が求められる製品には熱処理が欠かせません。熱処理によってアルミニウムの特性を最適化し、製品の性能を向上させることができます。
軟化処理後の冷却方法
アルミニウムを柔らかくする方法!熱処理とは?
アルミニウムを柔らかくするためには、熱処理が重要です。熱処理とは、アルミニウムを一定の温度に加熱し、それを適切な速度で冷却することで、結晶構造を調整し、硬さや強度を調整する工程です。
例えば、航空機のエンジン部品や自動車のフレームなど、高い強度が求められる分野では、アルミニウムの熱処理が欠かせません。熱処理後は、適切な冷却が重要となります。急冷することで硬さを高め、ゆっくり冷やすことで柔らかさを保つことが可能です。
アルミニウムの軟化処理後の冷却方法を正しく行うことで、さまざまな産業分野で利用されるアルミニウム製品の品質や性能を向上させることができます。
軟化したアルミニウムの用途
アルミニウムを柔らかくする方法!熱処理とは?
アルミニウムは、硬い性質を持っていますが、熱処理を行うことで柔らかくすることができます。この柔軟性を活かし、さまざまな産業で幅広く利用されています。
例えば、航空機の部品や自動車のボディパネルなどの製造において、柔らかいアルミニウムが使用されています。熱処理によってアルミニウムは弾力性や可塑性が向上し、加工性や耐久性が向上するため、さまざまな製品に活用されています。
熱処理によってアルミニウムを柔らかくすることで、製品の品質や性能を向上させることができ、産業界で広く重要な役割を果たしています。アルミニウムの柔軟性は、様々な分野での革新的な製品開発を可能にし、産業の発展に貢献しています。
アルミニウムの硬化方法
焼き入れとは
アルミニウムを柔らかくする方法!熱処理とは?
アルミニウムは強度が高くて軽い素材として知られていますが、時には柔らかくしたい場面もあります。アルミニウムを柔らかくする方法の一つに「熱処理」という方法があります。熱処理は、アルミニウム合金を加熱して適切な温度で保持し、それから急冷することで素材の性質を変える方法です。
熱処理によってアルミニウムの硬さや強度を調整することができ、さまざまな産業で利用されています。例えば、航空機や自動車の部品、建築材料などがその一例です。熱処理は、アルミニウムの特性を最大限に引き出すための重要な工程であり、正しい方法で行うことが製品の品質向上につながります。
焼き戻しとは
アルミニウムを柔らかくする方法!熱処理とは?
アルミニウムを柔らかくする方法の一つに「焼き戻し」という熱処理方法があります。この方法は、アルミニウム合金を高温で加熱して、急冷することで硬さを取り除き、柔らかくするプロセスです。
アルミニウム合金は強度を持つ素材ですが、硬さが欠点となる場合があります。例えば、航空機や自動車の部品など、寸法精度や形状が重要な場面で、柔らかさが求められることがあります。そんな時に焼き戻しを行うことで、アルミニウムの柔軟性を取り戻すことができます。
熱処理技術の進歩により、アルミニウム合金の柔軟性を細かく調整することが可能になり、様々な産業で活用されています。焼き戻しは、アルミニウムの特性を最大限引き出す重要な工程として、製造業界で広く利用されています。
硬化処理の効果
アルミニウムを柔らかくするためには、熱処理が必要です。アルミニウムは強靭で軽量な金属ですが、柔らかさが求められる場面もあります。この場合、熱処理を行うことでアルミニウムの性質を変化させ、柔らかくすることが可能です。
熱処理は、アルミニウムを一定温度に加熱し、それを保持した後、徐々に冷却する工程です。これにより、アルミニウムの結晶構造が変化し、柔らかさが向上します。例えば、航空機の部品や自動車の軽量化部品など、さまざまな産業で利用されています。
熱処理によってアルミニウムを柔らかくすることで、より幅広い用途に活用することが可能となります。そのため、熱処理はアルミニウム加工の重要な工程であり、今後もさらなる技術の進化が期待されています。
アルミ合金の調質
調質の種類と特徴
アルミニウムを柔らかくする方法!熱処理とは?
アルミニウムを柔らかくする方法の一つに、「熱処理」という手法があります。熱処理は、アルミニウムの物理的性質を変化させることで、硬度を調整し、加工しやすくする方法です。例えば、アルミニウム合金は、加熱と急冷を繰り返すことで結晶が微細化し、柔らかくなる特徴があります。
このような熱処理は、航空機や自動車などの産業分野で広く活用されています。アルミニウム製品の強度や耐久性を向上させるために欠かせない技術と言えるでしょう。熱処理によってアルミニウムの特性を適切に調整することで、さまざまな製品の製造に役立てることができます。
調質による性質の変化
アルミニウムを柔らかくする方法!熱処理とは?
アルミニウムを柔らかくするためには、熱処理が有効です。熱処理は、アルミニウム合金を特定の温度に加熱し、一定期間保持した後、適切な速度で冷却する加工方法です。この過程により、アルミニウムの結晶構造が変化し、硬さや強度が調整されます。
例えば、航空機や自動車の部品など、高い強度と柔軟性が求められる製品に熱処理は必要不可欠です。アルミニウム合金製品は、熱処理によって耐久性や加工性が向上し、さまざまな産業で広く活用されています。
まとめると、アルミニウムを柔らかくするためには、熱処理が重要な役割を果たします。適切な熱処理によって、アルミニウム製品の性質を効果的に調整できるため、製品の品質向上や用途拡大につながります。
合金元素と調質の関係
アルミニウムを軟化させる方法の1つは、熱処理です。これは、アルミニウム合金を特定の温度に加熱し、適切な時間保持した後、急冷することで行われます。このプロセスにより、アルミニウムの結晶構造が変化し、より柔らかくなります。熱処理は、アルミニウム合金の機械的性質や加工性を向上させるために広く使用されています。
例えば、航空機や自動車などの産業では、強度や耐久性を保ちつつも加工しやすいアルミニウム合金が重要です。そのため、熱処理によってアルミニウムの性質を調整することが重要となります。アルミニウム合金はさまざまな用途で使用されており、その柔軟性や軽さが求められています。熱処理は、その要求に応えるための重要なプロセスと言えるでしょう。
アルミ合金鋳物の熱処理
鋳物の熱処理の必要性
アルミニウムを柔らかくする方法として、熱処理が重要です。熱処理には、アルミニウムの結晶構造を変えて強度や耐久性を向上させる効果があります。例えば、アルミニウム合金は、急冷することで硬くなりますが、その後の適切な熱処理によって柔らかくすることができます。熱処理を行うことで、アルミニウム製品の加工性や強度が向上し、さまざまな産業で幅広く活用されています。アルミニウム製の自動車部品や航空機部品などは、熱処理によって高い品質と性能が実現されています。熱処理は、アルミニウム製品の品質向上や性能向上に欠かせない重要な工程です。
鋳物の硬化メカニズム
【アルミニウムを柔らかくする方法!熱処理とは?】
アルミニウムを柔らかくする方法の一つに熱処理があります。熱処理は、アルミニウム合金を特定の温度に加熱し、その後徐々に冷却することで行われます。この過程により、結晶構造が変化し、アルミニウムの硬さや強度が変わります。
理由は、熱処理によりアルミニウムの結晶が再配置されるからです。具体例として、航空機の構造材料であるアルミニウム合金は、熱処理によって強度を向上させ、重要な部品の製造に使われています。
熱処理は、さまざまな産業分野で幅広く利用され、アルミニウムの特性を適切に調整する重要な工程となっています。アルミニウムの柔軟性を引き出す熱処理の技術は、製品の品質向上や新たな用途の開発にも貢献しています。
鋳物熱処理の実際
アルミニウムを柔らかくする方法として、熱処理があります。熱処理とは、金属を特定の温度に加熱し、それを一定時間保持してから徐々に冷やす加工法のことです。この過程により、アルミニウムの結晶構造が変化し、より柔らかくなります。例えば、自動車部品や航空機の構造部品など、強度と柔軟性が求められる製品に広く利用されています。アルミニウム合金は機械的性質を向上させるために熱処理が欠かせない素材であり、適切な熱処理を施すことで、製品の性能を向上させることが可能です。熱処理は製品の品質向上に欠かせない工程であり、アルミニウムの軟化に重要な役割を果たします。
熱処理に関する注意点と問題解決
熱処理時の注意事項
アルミニウムを柔らかくするための一つの方法が熱処理です。熱処理とは、アルミニウムを特定の温度で保持し、それから徐々に冷やすことで、結晶構造を整えて硬さや強さを調整する加工方法のことです。この熱処理には、いくつかの注意点があります。
まず、適切な温度管理が重要です。温度が高すぎるとアルミニウムが溶けてしまい、低すぎると効果が得られません。また、冷却速度も影響を与えます。適切な冷却速度を保つことが、アルミニウムの性質を正しく調整するポイントです。
例えば、航空機の部品や自動車のエンジン部品など、高い強度が求められる製品では熱処理が欠かせません。熱処理を適切に行うことで、アルミニウム製品の性能を向上させることができます。アルミニウム製品をより効果的に活用するために、熱処理の方法と注意点を把握しておくことが重要です。
一般的な問題と対策
アルミニウムを柔らかくする方法として、熱処理が用いられます。この熱処理は、アルミニウム合金を高温で保持し、適切な速度で冷却することで行われます。熱処理により、アルミニウムの結晶粒が粗大化し、柔らかくなります。
例えば、自動車部品や航空機の構造部品など、強度が求められる製品において、アルミニウムを柔らかくすることで加工しやすくなり、さらに強度も向上します。熱処理を行うことで、アルミニウムの性質を適切に調整し、様々な産業分野で幅広く活用されています。
熱処理は、アルミニウムの物性を変化させる方法として重要であり、製品の品質向上や生産性の向上に寄与しています。そのため、アルミニウムを柔らかくする際には、熱処理が欠かせない重要な工程となります。
熱処理施設と安全管理
アルミニウムを柔らかくする方法!熱処理とは?
アルミニウムは非常に軽くて丈夫な金属ですが、時には柔らかくして使いやすくする必要があります。その際に利用される方法の一つが「熱処理」です。
熱処理とは、アルミニウムを特定の温度に加熱し、それを保持した後、適切な速度で冷却することで、結晶構造を変えて硬さや強さを調整する方法です。例えば、飛行機の部品や自動車の部品など、高強度を要求される製品の製造に広く利用されています。
熱処理によりアルミニウムの性質を調整することで、様々な産業で幅広く用いられています。これにより、アルミニウムの柔軟性や耐久性を向上させ、さまざまな製品の製造に貢献しています。
アルミニウムの熱処理を行う際の機器と技術
必要な機器とその機能
アルミニウムを柔らかくする方法!熱処理とは?
アルミニウムを柔らかくする方法の一つに、熱処理があります。熱処理は、金属を加熱してから急冷することで、結晶粒を微細化して硬さを調整する方法です。例えば、航空機のエンジン部品や自動車の構造部品など、高強度かつ軽量なアルミニウム製品を作る際に熱処理が重要です。
熱処理には種類があり、一般的には焼なまし、焼入れ、焼戻しなどがあります。このような熱処理工程を組み合わせることで、アルミニウムの硬さや耐久性を調整することが可能です。
熱処理は、アルミニウム製品の品質や性能を向上させる重要な工程であり、様々な産業分野で広く活用されています。
熱処理技術の進歩
アルミニウムを柔らかくする方法!熱処理とは?
アルミニウムは強度が高く、軽い素材として知られています。しかし、時には柔軟性を増す必要があります。その際に利用されるのが「熱処理」です。熱処理は、アルミニウムを高温で保持し、適切な速度で冷却することで、結晶構造を変化させ、柔らかさを持たせる方法です。
たとえば、航空機の軽量化を図るために、アルミニウム合金の部品を柔らかくする必要があります。このような要求に応えるために熱処理技術が進化しています。また、自動車産業でも、車体の軽量化や強度向上のために熱処理が重要な役割を果たしています。
このように、熱処理は様々な産業分野で利用され、アルミニウムの性質を柔らかくするだけでなく、強度や耐久性を調整することができます。
熱処理サービスと業者選びのポイント
アルミニウムを柔らかくする方法!熱処理とは?
アルミニウムを柔らかくする方法の一つに「熱処理」という方法があります。この技術は、アルミニウム合金を特定の温度で加熱し、適切な速度で冷却することで行われます。熱処理により、アルミニウムの硬さや強度を調整することが可能となります。
例えば、航空機の部品や自動車のエンジン部品など、高強度を要求される製品では、アルミニウム合金を熱処理することで必要な強度を得ることができます。このように、熱処理はさまざまな産業分野で重要な役割を果たしています。
熱処理を正確に行うためには、熱処理サービスを提供する業者の選定が重要です。業者の技術力や信頼性、施設の設備などを注意深く検討し、適切な業者を選ぶことが大切です。アルミニウム製品の品質や性能向上を目指す際には、適切な熱処理が欠かせません。
ケーススタディ:アルミニウム熱処理の成功例
自動車産業における応用
アルミニウムを柔らかくする方法は、熱処理によって行われます。熱処理は、アルミニウム合金を特定の温度に加熱して保持し、その後徐々に冷却する工程です。この過程により、アルミニウムの結晶構造が変化し、硬さや強度が調整されます。
例えば、航空機のエンジン部品や自動車のシャシーなど、高強度を要求される部品において、アルミニウム合金の硬さを調整するために熱処理が行われます。このような部品は、適切な硬さを持つことで安全性や信頼性を確保するために重要です。
したがって、アルミニウムを柔らかくする方法として熱処理が重要な役割を果たしており、産業分野において広く活用されています。
航空宇宙産業での熱処理技術
アルミニウムを柔らかくする方法!熱処理とは?
アルミニウムは、様々な産業で広く使用される重要な金属です。しかし、一部の場合、アルミニウムは硬くて加工が難しいことがあります。そんな時に利用されるのが「熱処理」という技術です。
熱処理は、アルミニウムを特定の温度に加熱し、その後徐々に冷却することで、材料の組織や硬さを変化させる方法です。例えば、航空機の部品や自動車のエンジン部品など、高い強度と耐久性が求められる製品に熱処理が利用されます。
このように、熱処理はアルミニウムの性質を変えて、さまざまな産業で活躍する製品へと生まれ変わらせる重要な技術なのです。
日常生活製品への影響
アルミニウムを柔らかくする方法!熱処理とは?
アルミニウムは、硬い素材であることで知られていますが、この硬さを柔らかくする方法として熱処理があります。熱処理は、アルミニウムを一定の温度で加熱し、それを急冷することで行われます。これにより、結晶粒が整列され、強度が向上し、同時に柔らかさも増します。
例えば、自転車のフレームや航空機の部品など、アルミニウム製品は熱処理を受けることで、耐久性や加工性が向上します。熱処理はアルミニウム製品の性能を向上させる重要な工程であり、様々な産業で活用されています。
熱処理によってアルミニウムの柔らかさを調整することで、さまざまな製品の品質や性能が向上し、多くの場面で活躍しています。
まとめ
アルミニウムの強さを高めるための熱処理方法があります。アルミニウムは、非常に軽量でありながらも強度が高いため、さまざまな用途に使用されています。熱処理によって、アルミニウムを柔らかくしたり、逆に硬くしたりすることが可能です。このような熱処理は、アルミニウムを加工する際に重要な要素となります。
アルミニウムの特性解説:軟化温度が与える影響とは
アルミニウムは、私たちの日常生活に欠かせない素材の一つです。その軽量性や耐食性から、様々な産業分野で幅広く使用されています。しかし、アルミニウムの特性の中でも、軟化温度は重要な要素の一つです。軟化温度が与える影響について詳しく解説していきます。アルミニウムがどのように軟化し、それが製品や材料の性能にどのような影響を与えるのか。本記事では、アルミニウムの特性に焦点を当て、軟化温度の重要性を明らかにします。アルミニウムに関心をお持ちの方や、その特性について詳しく知りたい方にとって、貴重な情報を提供します。
アルミニウムの基本と軟化温度の概要
アルミニウムの物理的特性
アルミニウムの特性には、軟化温度が与える影響が重要です。アルミニウムは融点が低く、軟化温度が近づくと柔らかくなります。例えば、溶接作業では、アルミニウムが溶ける前に加熱し、軟化させてから接合する必要があります。軟化温度は加工性や強度にも影響を与えます。一般的に、高温で軟化する金属ほど加工が容易で、低温で軟化する金属ほど強度が高い傾向があります。アルミニウムは軽量で耐食性に優れ、多くの産業で幅広く使われています。したがって、軟化温度の理解は、アルミニウムの適切な加工や利用に重要な役割を果たします。
アルミニウム合金とは
アルミニウムの特性解説:軟化温度が与える影響とは
アルミニウム合金は、軽量で強度があり、耐食性にも優れた金属です。この中でも軟化温度は重要な特性の一つです。軟化温度とは、高温になると材料が柔らかくなる温度のことを指します。
軟化温度が低い合金は、高温で変形しやすくなります。一方、軟化温度が高い合金は、高温になっても強度を維持しやすい特性があります。例えば、航空機や自動車の部品など、高温環境で使用される部品は、軟化温度が高いアルミニウム合金が選ばれます。
したがって、アルミニウム合金の軟化温度はその材料の適用範囲や使用環境に影響を与える重要な要素となります。考える際に軟化温度を理解することは、材料の適切な選択や設計に役立ちます。
軟化温度とその重要性
軟化温度とその重要性
アルミニウムの特性の一つである軟化温度は、材料がどれくらいの温度で柔らかくなるかを示す重要な指標です。この軟化温度が低いほど、アルミニウムは熱により早く軟化しやすくなります。例えば、高温で使用される材料の場合、軟化温度が高いアルミニウムを選択することが重要です。
アルミニウム合金の軟化温度は、その特性や用途によって異なります。例えば、航空機の構造部品に使用されるアルミニウム合金は、高い軟化温度を持つことが求められます。一方、加工性を重視する場合には、低い軟化温度のアルミニウム合金が適しています。
したがって、アルミニウムの軟化温度を理解し、適切に選択することは、材料の性能や耐久性を向上させる上で重要な要素となります。
アルミニウムと他の金属との比較
[アルミニウムの特性解説:軟化温度が与える影響とは]
アルミニウムは軽量で耐食性に優れ、熱伝導率が高いという特性を持っています。そして、その中でも重要な特性の一つが軟化温度です。この軟化温度とは、金属が熱を加えられて柔らかくなり、変形しやすくなる温度のことです。
軟化温度が高いほど、アルミニウムは高温環境においても強度を維持しやすくなります。逆に軟化温度が低い場合、熱によって変形しやすくなります。例えば、航空機のエンジン部品や自動車のエンジンブロックなど、高温の環境下で使用される部品では、高い軟化温度を持つアルミニウムが選ばれることが多いです。
したがって、アルミニウムの軟化温度は、その材料がどのような環境や用途で使用されるかに大きな影響を与える重要な要素と言えます。
機械設計者のためのアルミニウム基礎知識
アルミニウムの選択基準
[アルミニウムの特性解説:軟化温度が与える影響とは]
アルミニウムは軽量で丈夫な金属として幅広い用途で使用されています。軟化温度は、アルミニウムが熱を加えられた際に柔らかくなる温度を示します。この特性は加工や成形の際に重要であり、軟化温度が高いほど高温で安定した形状を保ちます。
例えば、航空機の構造に使用されるアルミニウムは高い軟化温度を持つことが求められます。これにより、高温での飛行中にも安定した性能を発揮し、安全性を確保します。一方、食器や缶の製造に使用されるアルミニウムは比較的低い軟化温度を持ち、容易に成形が可能です。
結論として、アルミニウムの軟化温度はその用途に合わせて選択される重要な要素であり、機能や安全性に直結することを理解することが大切です。
アルミニウム合金の種類と用途
アルミニウム合金は、様々な種類がありますが、それぞれ異なる用途に活用されています。例えば、航空機や自動車、建築材料など幅広い分野で利用されています。中でも重要なのが、アルミニウム合金の軟化温度です。この軟化温度が与える影響は大きく、高い温度で軟化する合金は高温での使用に適しています。逆に低い温度で軟化する合金は、一般的な温度範囲での利用に適しています。例えば、航空機用の合金は高温に耐える性質が重要であり、建築材料用の合金は通常の気候条件下での強度が求められます。そのため、適切な軟化温度を持つ合金を選択することが重要です。アルミニウム合金の特性を理解し、適切な用途に活用することが、効果的な製品開発や設計の鍵となります。
設計上の考慮事項とアルミニウムの利点
アルミニウムは軽量でありながら、強度や耐食性に優れている特性を持っています。このため、航空機や自動車、建築など幅広い産業で使用されています。アルミニウムの特性の一つに軟化温度があります。この軟化温度は、アルミニウムが熱を加えられると軟化し始める温度を示します。
軟化温度が重要な理由は、例えば自動車のエンジン部品など高温で使用される箇所では、アルミニウムが軟化してしまうと機能を果たせなくなります。そのため、設計や製造段階で適切な軟化温度を考慮することが重要です。例えば、航空機の機体部品では、高温になる環境下での強度維持が求められるため、適切なアルミニウム合金を選定することが必要です。
このように、アルミニウムの軟化温度は製品の信頼性や耐久性に影響を与える重要な要素となります。
アルミニウム使用時の注意点
[アルミニウムの特性解説:軟化温度が与える影響とは]
アルミニウムは軽量で耐食性に優れた金属であり、多くの産業で広く使用されています。しかし、アルミニウムは軟化温度が比較的低く、熱によって軟化してしまう性質を持っています。
例えば、高温環境で使用する場合、アルミニウム製品は軟化して機械的強度が低下する可能性があります。これは航空機や自動車など、高温にさらされる環境での安全性に影響を与える重要な要素です。
したがって、アルミニウム製品を設計や選定する際には、その軟化温度に注意を払うことが重要です。適切な材料を選択することで、製品の性能や耐久性を向上させることができます。アルミニウムの特性を理解し、適切に活用することが生産性向上や安全性確保につながります。
アルミフレームの耐熱性
耐熱性の定義と評価方法
アルミニウムの特性解説:軟化温度が与える影響とは
アルミニウムは、軟化温度という重要な特性を持っています。この温度は、アルミニウムが加熱されると柔らかくなる温度を示します。軟化温度が高いほど、アルミニウムの耐熱性が高くなります。
例えば、自動車のエンジンブロックは高い軟化温度を持つアルミニウム合金で作られています。これにより、エンジンが高温になっても変形することなく安定した性能を保つことができます。
一方、一般家庭用の調理器具などは低い軟化温度のアルミニウムが使われています。これにより、簡単に加工できるだけでなく、熱を素早く伝導して料理を効率よく調理することができます。
したがって、アルミニウムの軟化温度は製品の用途や性能に大きく影響を与える重要な要素と言えます。
アルミフレームにおける耐熱性の重要性
アルミニウムの特性解説:軟化温度が与える影響とは
アルミフレームにおける耐熱性の重要性は、製品の安定性や耐久性に直結します。アルミニウムは比較的低い軟化温度を持ち、高温で変形や強度の低下が起こります。例えば、自動車や航空機の部品に使用されるアルミニウム合金は、高速で移動する際に高温に晒されるため、適切な軟化温度が必要です。特にエンジン部品や構造材料など、高温環境での使用において耐熱性が求められます。そのため、アルミフレームの設計や材料選定において、軟化温度の影響を理解し、適切な対策を講じることが重要です。耐熱性に優れたアルミフレームは、安全性や信頼性を確保し、製品の性能向上に貢献します。
熱処理による耐熱性の向上
アルミニウムの特性解説:軟化温度が与える影響とは
アルミニウムは軽量で耐食性に優れ、多くの産業で広く使用されています。アルミニウムの特性の1つに軟化温度があります。軟化温度とは、ある温度を超えるとアルミニウムの強度が急激に低下することを示します。
この軟化温度の影響は重要であり、例えば航空機や自動車の部品製造では、正確な温度管理が欠かせません。軟化温度を超えると部品が変形しやすくなり、安全性や信頼性が損なわれる可能性があります。
したがって、アルミニウム製品を製造する際には、軟化温度を考慮して適切な熱処理を行うことが不可欠です。適切な熱処理によって耐熱性が向上し、製品の品質や性能を確保することができます。
アルミニウム合金の溶接と軟化温度の関係
溶接プロセスとアルミニウムの挙動
アルミニウムの特性解説:軟化温度が与える影響とは
アルミニウムの挙動において、重要な要素の一つが軟化温度です。アルミニウムは特定の温度以下では硬い物質として振る舞いますが、一定の温度を超えると急速に柔らかくなります。この軟化温度を理解することで、加工や溶接などの工程において適切な温度管理が重要となります。
例えば、アルミニウム製品を溶接する際には、軟化温度を適切に管理することで溶接に必要な強度を確保することができます。逆に、軟化温度を超えてしまうと溶接部の強度が低下し、品質に問題が生じる可能性があります。
したがって、アルミニウムの軟化温度を把握し、それに基づいた適切な加工を行うことが製品の品質や性能を確保するうえで重要です。
熱影響部の軟化現象
アルミニウムの特性解説:軟化温度が与える影響とは
アルミニウムは軽量で耐食性に優れ、幅広い産業で使用されています。しかし、高温下ではアルミニウムは軟化しやすくなります。軟化温度が重要な影響を与えます。例えば、飛行機のエンジン部品や自動車のエンジンブロックなど、高温で使用される部品では軟化温度を考慮することが必須です。アルミニウム合金は、適切な軟化温度を保つことで、安全性と耐久性が確保されます。産業分野において、軟化温度が適切に管理されることで製品の性能向上につながります。したがって、アルミニウムの軟化温度を理解し、適切に制御することは重要です。
溶接後の機械的性質の変化
アルミニウムの特性解説:軟化温度が与える影響とは
アルミニウムは軽量で耐久性があり、多くの産業で幅広く利用されています。アルミニウムの特性の一つに軟化温度があります。この軟化温度は、アルミニウムが加熱されるときに硬度が低下する温度を指します。軟化温度が重要な理由は、加工や溶接などの熱処理が必要な工程でアルミニウムの性質が変化するからです。
例えば、溶接後のアルミニウムは熱によって軟化し、強度が低下する可能性があります。このため、溶接時の温度管理や冷却方法が重要となります。軟化温度を理解することで、アルミニウム製品の品質や耐久性を向上させることができます。
アルミニウムの特性をしっかりと把握し、適切な加工方法を選択することで、より安全で信頼性の高い製品を提供することができます。
溶接条件の最適化
[アルミニウムの特性解説:軟化温度が与える影響とは]
アルミニウムの特性について理解するために、軟化温度が非常に重要です。軟化温度とは、材料が柔らかくなり始める温度のことで、加工性や強度に大きな影響を与えます。
軟化温度が低いアルミニウムは、比較的低い温度でも柔らかくなるため、加工が容易です。一方、軟化温度が高いアルミニウムは、高温でないと柔らかくならず、強度が保たれます。
例えば、航空機の構造材料として使われるアルミニウムは、高い軟化温度を持つことが求められます。これにより、高温にさらされる状況下でも十分な強度を維持できるのです。
軟化温度の理解は、アルミニウムを適切に扱い、適切な用途に活用するために重要です。
極低温下でのアルミニウム合金の特性
極低温環境における物質の行動
アルミニウムの特性解説:軟化温度が与える影響とは
アルミニウムは、軽くて丈夫な材料として幅広い分野で使われています。軟化温度とは、物質が柔らかくなり始める温度のことです。アルミニウムの軟化温度が与える影響は重要です。例えば、極低温環境では、アルミニウムは脆くなり、強度が低下します。これは航空機や自動車などの安全性に影響を与える可能性があります。一方、高温環境では、アルミニウムはより柔らかくなり、変形しやすくなります。このため、製品の設計や素材選定において、アルミニウムの軟化温度を考慮することが大切です。アルミニウムの特性を正しく理解して活用することで、安全性や信頼性を高めることができます。
アルミニウム合金の低温での機械的性質
アルミニウムの特性解説:軟化温度が与える影響とは
アルミニウム合金は、低温での機械的性質に影響を受けます。軟化温度とは、材料が軟らかくなり始める温度のことを指します。この温度以下では、アルミニウムの強度が低下し、変形が容易になります。例えば、冷間加工されたアルミニウム合金は、軟らかい状態から急激に硬くなることが知られています。そのため、製品の設計や加工時には、この軟化温度を考慮することが重要です。
また、航空機の構造部品や自動車のボディパネルなど、多くの産業でアルミニウム合金が使用されています。軟化温度を理解することで、適切な処理や製造工程を設計し、製品の強度や耐久性を確保することができます。アルミニウム合金の特性を理解することは、産業界において重要な課題となっています。
極低温用途におけるアルミニウム合金の選択
アルミニウム合金は、さまざまな用途に幅広く使用されています。その中でも、極低温で使用される環境では、アルミニウム合金の軟化温度が重要な要素となります。軟化温度とは、金属が熱を加えられたときに柔らかくなる温度のことを指します。
極低温で使用される場合、アルミニウムの軟化温度が低い合金を選択することが重要です。なぜなら、軟化温度が高い合金は、低温下での強度や耐久性が損なわれる可能性があるからです。
例えば、液体窒素のような極低温環境で使用されるアルミニウム合金は、軟化温度が低いものが適しています。これにより、金属の強度を維持しつつ、適切な性能を発揮することができます。したがって、極低温環境におけるアルミニウム合金の選択は、軟化温度を考慮する重要なポイントとなります。
アルミニウム合金の応用と未来
現代技術におけるアルミニウム合金の役割
アルミニウム合金は現代技術において重要な役割を果たしています。その特性の一つに、軟化温度があります。アルミニウムは比較的低い温度で軟化しやすい性質を持っています。この軟化温度は加工や成形の際に重要な要素となります。例えば、アルミニウム合金は加熱によって容易に成形できるため、航空機や自動車などの軽量化に活用されています。
さらに、軟化温度が低いため、溶接などの加工も比較的容易に行うことができます。これにより、アルミニウム合金は様々な産業分野で幅広く使用されています。
したがって、アルミニウム合金の軟化温度は、その加工性や応用範囲に大きな影響を与えています。現代技術において欠かせない素材として、アルミニウム合金は多岐にわたる分野で活躍しています。
アルミニウム合金の新たな開発動向
アルミニウムは多くの工業製品で使用される重要な材料です。特に、アルミニウムの軟化温度はその特性に影響を与えます。軟化温度とは、高温での変形や成形が容易になる温度のことです。例えば、飛行機の部品や自動車部品など、高温での加工が必要な製品では、軟化温度が重要な要素となります。
最近の開発動向では、アルミニウム合金の軟化温度を向上させる研究が進められています。これにより、より高温での加工が可能となり、製品の強度や耐久性が向上すると期待されています。
このように、アルミニウムの特性である軟化温度の向上は、さまざまな産業分野において革新的な製品開発や生産性向上に貢献する可能性があります。
環境と持続可能性への寄与
[アルミニウムの特性解説:軟化温度が与える影響とは]
アルミニウムは、軽量で耐食性に優れ、工業製品の製造に広く使用されています。その特性の中でも、軟化温度は重要な要素です。軟化温度とは、高温に加熱することで物質が柔らかくなる温度のことです。
この軟化温度が与える影響は大きく、例えば航空機や自動車などの高温にさらされる部品においては、軟化温度が高いアルミニウム合金が求められます。逆に、低い軟化温度のアルミニウムは、溶接時に使用されるなど、柔らかくする必要がある場面で活躍します。
軟化温度の理解は製品の設計や製造において不可欠であり、適切なアルミニウム合金の選択につながります。したがって、アルミニウムの特性に関する知識は産業界において重要な要素となっています。
まとめ
アルミニウムの特性には、軟化温度が重要な影響を与えます。この温度は、材料が軟らかくなり始める温度を示しており、これを超えると強度が低下します。アルミニウム製品を製造する際には、この軟化温度を考慮することが不可欠です。また、アルミニウムは軽量で耐食性に優れており、多くの産業で幅広く利用されています。その特性を理解し、適切に取り扱うことが重要です。
アルミニウムの軟化温度を理解する!使い方と注意点
アルミニウムは、私たちの日常生活において広く使用されている素材の一つです。しかし、その性質や特性を理解することは重要です。特に、アルミニウムの軟化温度は、その使い方や取り扱いにおいて重要なポイントとなります。本記事では、アルミニウムの軟化温度に焦点を当て、その理解や使い方、注意点について詳しく解説していきます。アルミニウムの素材特性に興味をお持ちの方や、その取り扱いに不安を感じている方にとって、役立つ情報が満載です。さあ、アルミニウムとその軟化温度について一緒に探求してみましょう。
アアルミニウムの基本的な特性
アルミニウムの物理的性質
特性 | 詳細説明 |
---|---|
密度 | 約2.7 g/cm³ |
融点 | 約660°C |
熱伝導率 | 237 W/m·K |
電気伝導率 | 約37.7 × 10⁶ S/m |
比熱容量 | 約0.897 J/g·K |
強度 | 引張強さは約70-700 MPa(合金による) |
膨張係数 | 22.2 × 10⁻⁶ K⁻¹ |
アルミニウムの物理的性質に関する説明
- 軽量性: アルミニウムは密度が約2.7 g/cm³であり、非常に軽量です。これにより、航空機や自動車、建材などでの使用が推奨されます。
- 優れた熱・電気伝導性: 熱伝導率は237 W/m·K、電気伝導率は約37.7 × 10⁶ S/mと、高い導電性を誇ります。冷却システムや電気機器に最適です。
- 加工性: 融点が約660°Cで比較的低く、加工が容易です。これにより、複雑な形状に成型する際にも利便性があります。
- 強度: アルミニウムは軽量でありながら、強度が高い(合金による)が、純粋なアルミニウムよりも合金を加えることで更に強度を向上させます。
アルミニウムの化学的性質
特性 | 詳細説明 |
---|---|
酸化皮膜 | 空気中で酸化皮膜を形成し、腐食を防止 |
耐腐食性 | 良好であり、海水や湿気にも耐性がある |
反応性 | 酸やアルカリとの反応は少ないが、高温下では酸化物が形成されやすい |
アルミニウムの化学的性質に関する説明
- 酸化皮膜: アルミニウムは空気中で酸化皮膜(酸化アルミニウム)を形成し、金属自体を保護します。この特性により、長期間にわたって錆びにくいです。
- 耐腐食性: アルミニウムは優れた耐腐食性を持ち、特に海水や湿気などの厳しい環境でも使用できます。このため、航空機や建築材料に使用されることが多いです。
- 高温での酸化: アルミニウムは高温下で酸化しやすいため、高温環境で使用する際には注意が必要です。
アルミニウム合金とは
特性 | 詳細説明 |
---|---|
合金の種類 | アルミニウム合金には多種多様な種類(鋳造用、圧延用など)がある |
強度 | 1xxx, 2xxx, 7xxxなどのシリーズによって強度が異なる |
成形性 | 合金の種類によって、鍛造や押出成形に適したものがある |
使用例 | 航空機、自動車、建材、電気機器など |
アルミニウム合金の軟化温度
軟化温度とは
軟化温度とは、金属が加熱されることでその硬度が低下し、塑性変形が容易になる温度のことを指します。アルミニウム合金の軟化温度は、金属がどのような状態で使用されるか、またどのような加工を施すかに大きく影響します。軟化温度に達すると、金属はその強度や硬度を失い、構造的な安定性が損なわれるため、使用環境を考慮した温度管理が必要です。
アルミニウム合金の軟化温度の範囲
合金の種類 | 軟化温度の範囲(℃) |
---|---|
純アルミニウム (1xxx系列) | 約 400~500°C |
2xxx系列 (銅合金) | 約 450~540°C |
5xxx系列 (マグネシウム合金) | 約 450~500°C |
6xxx系列 (シリコン-マグネシウム合金) | 約 430~500°C |
7xxx系列 (亜鉛合金) | 約 480~540°C |
アルミニウム合金の軟化温度に関する説明
- 純アルミニウム (1xxx系列): 軟化温度は比較的低く、約400~500°Cの範囲です。これは純度が高いため、加工がしやすく、主に建材や電気機器に使用されます。
- 2xxx系列 (銅合金): 銅を加えた合金は、アルミニウムよりも高い軟化温度を持ち、約450~540°Cであるため、高強度が要求される部品(航空機など)に適しています。
- 5xxx系列 (マグネシウム合金): マグネシウムを加えた合金は、約450~500°Cの範囲で軟化します。優れた耐腐食性と良好な溶接性を持ち、海洋や化学産業向けに利用されます。
- 6xxx系列 (シリコン-マグネシウム合金): シリコンとマグネシウムを含んだ合金で、軟化温度は約430~500°Cで、建材や構造部品に多く使用されています。
- 7xxx系列 (亜鉛合金): 亜鉛を加えた合金は最も高い軟化温度を持ち、約480~540°Cの範囲です。この合金は、航空機や高強度部品に適しており、強度と耐久性が非常に高いです。
合金の種類による軟化温度の違い
アルミニウム合金の軟化温度は、合金に含まれる他の金属成分によって大きく異なります。銅、マグネシウム、シリコン、亜鉛などが加わることで、金属の強度や耐熱性が向上し、その軟化温度も高くなります。特に、銅や亜鉛を多く含む合金(2xxx、7xxx系列)は、耐熱性が求められる用途に適しており、より高い軟化温度を示します。
アルミ箔の軟化品質
アルミ箔の特性と用途
特性 | 説明 |
---|---|
軽量かつ強度あり | アルミ箔は非常に軽量で、強度があり加工が容易です。 |
用途 | 食品包装、断熱材、電子部品など、さまざまな用途に使用されています。 |
軟化温度と取り扱い
アルミ箔は約600°Cで溶け始めるため、高温の環境では変形しやすいです。例えば、オーブンでの調理や溶接作業などの高温条件では注意が必要です。アルミ箔を使用する際には、その軟化温度を考慮して適切な環境で取り扱うことが重要です。安全性を確保するためには、アルミ箔の特性と使用方法を正しく理解しておくことが必要です。
軟化温度がアルミ箔の品質に与える影響
要素 | 説明 |
---|---|
軟化温度の影響 | 軟化温度を超えるとアルミ箔が軟化し、形を崩す性質があります。 |
用途別要求 | 高温で保存される食品のパッケージングには、軟化温度が高いものが求められます。 |
品質確保のための理解
アルミ箔の品質を確保するためには、軟化温度を正確に把握することが重要です。高温にさらされる用途には、高い軟化温度を持つアルミ箔が適しています。一方で、薄いアルミ箔を使用する場合は、比較的低い軟化温度が適しています。これにより、製品の品質や安全性を高めることができます。
軟化温度を考慮したアルミ箔の取り扱い方
注意点 | 説明 |
---|---|
取り扱い温度 | アルミ箔は比較的低い温度で軟化しやすいため、適切な取り扱いが必要です。 |
調理時の注意 | オーブンで使用する場合は、適切な温度と時間を守ることが重要です。 |
適切な取り扱い
アルミ箔をオーブンで使用する際には、軟化温度を考慮し、適切な温度や時間を守ることで変形を防ぎます。料理に使う場合も、アルミニウムの特性を理解し、適切な使い方をすることで、安全に利用できます。軟化温度を守ることで、アルミ箔を効果的に使い、安全に料理を楽しむことができます。
アルミ鋳物の熱処理
熱処理の目的と基本的な流れ
目的 | 詳細説明 |
---|---|
強度の向上 | アルミ鋳物を熱処理することで、結晶構造を改善し、強度を向上させます。 |
耐腐食性の改善 | 熱処理によって表面の酸化皮膜が強化され、耐腐食性が向上します。 |
機械的特性の調整 | 延性や靭性などの機械的特性を調整し、最適な性能を引き出します。 |
内部応力の除去 | 熱処理により、鋳物内に残った内部応力を除去します。 |
熱処理の基本的な流れ
- 加熱: アルミ鋳物を一定の温度まで加熱し、金属の結晶構造を変更します。
- 保持: 目標温度に達したら、一定時間保持して金属内部の構造を安定化させます。
- 冷却: 急冷または徐冷により、金属を目的の硬度や強度に調整します。
アルミ鋳物における熱処理の種類
熱処理方法 | 詳細説明 |
---|---|
アニーリング (焼鈍) | 鋳物を一定の温度で加熱し、急冷後に再結晶化させ、延性を向上させます。 |
固溶化処理 | 高温で加熱し、合金元素を溶解させた後、急冷して固溶体を形成します。 |
時効処理 | 固溶化処理後に一定の温度で保持し、析出硬化を促進して強度を向上させます。 |
焼きなまし (焼戻し) | 金属を加熱して軟化させ、後の加工を容易にします。 |
油冷処理 | 高温で加熱した鋳物を油で冷却して、強度と硬度を向上させます。 |
アルミ鋳物における熱処理方法の選択
- アニーリングは、延性を向上させるために使用され、鋳物の硬さを低下させることなく加工性を向上させます。
- 固溶化処理は、高強度を必要とする部品に用いられ、特に航空機や自動車の部品に多く使用されます。
- 時効処理は、鋳物における強度を最大化するために行い、特に強度が要求される部品に適しています。
- 焼きなましは、加工性を向上させるために使用される方法です。
軟化温度を考慮した熱処理の実践
合金の種類 | 軟化温度(℃) | 熱処理方法 | 目的 |
---|---|---|---|
純アルミニウム (1xxx系列) | 約 400~500°C | アニーリング、固溶化処理、焼きなまし | 加工性の向上、延性の向上 |
2xxx系列 (銅合金) | 約 450~540°C | 固溶化処理、時効処理 | 高強度化、耐腐食性の向上 |
5xxx系列 (マグネシウム合金) | 約 450~500°C | 固溶化処理、時効処理 | 強度向上、耐腐食性の向上 |
6xxx系列 (シリコン-マグネシウム合金) | 約 430~500°C | 固溶化処理、時効処理 | 強度と加工性のバランス向上 |
7xxx系列 (亜鉛合金) | 約 480~540°C | 固溶化処理、時効処理 | 高強度化、耐摩耗性の向上 |
軟化温度を考慮した熱処理の実践
アニーリングや焼きなましは、軟化温度が低い合金に使用され、加工を容易にするために行います。
アルミ鋳物の軟化温度は、約400~540°Cの範囲であり、これに基づき適切な熱処理方法を選択することが重要です。例えば、銅合金(2xxx系列)や亜鉛合金(7xxx系列)は比較的高い軟化温度を持ち、固溶化処理や時効処理が効果的です。
固溶化処理は、合金を高温に加熱し、合金元素を溶解させた後に急冷することで、高強度化を図ります。その後、時効処理を施すことで、さらに強度を高めることができます。
アルミニウムの特性とその活用
アルミニウムはその軽量性と強度、耐食性から、さまざまな分野で幅広く活用されています。ここでは、アルミニウムの基本的な特性と、それを活かした具体的な利用例について詳しく紹介します。
アルミニウムの耐食性とその向上方法
アルミニウムは自然に酸化皮膜を形成し、高い耐食性を持っていますが、特定の用途ではさらなる耐食性の向上が求められます。アルミニウムの耐食性を向上させる方法とその技術について説明します。
特性 | 詳細説明 |
---|---|
耐食性の高さ | アルミニウムは自然に酸化皮膜(酸化アルミニウム)を形成し、耐腐食性が非常に高いです。 |
アルミニウムの酸化皮膜 | アルミニウムが酸化することで表面にできる酸化アルミニウムは、非常に硬く耐久性があります。 |
耐食性向上方法 | 1. 陽極酸化:酸化皮膜を人工的に強化し、耐食性を高めます。 2. 合金化:マグネシウムやシリコンを含む合金を使用することで、耐食性を改善します。 3. コーティング:フッ素樹脂やエポキシ樹脂によるコーティングが有効です。 |
アルミニウムの耐食性向上方法
- 陽極酸化:アルミニウム表面に電気化学的な方法で酸化膜を形成し、その膜を強化することで耐食性や耐摩耗性を向上させます。
- 合金化:特に5xxx系のマグネシウムを含むアルミニウム合金は海水や塩分を含む環境での耐食性が優れています。
- コーティング:表面にフッ素樹脂やエポキシ樹脂を塗布し、外的環境から保護することで耐食性を向上させます。
アルミニウムの強度と軽量性
アルミニウムの強度と軽量性は、航空機や自動車など、強度と軽さを両立させたい用途に最適です。アルミニウム合金の強度を高める方法や、軽量性の利点について解説します。
特性 | 詳細説明 |
---|---|
強度 | アルミニウムの強度は純アルミニウムよりも合金にすることで向上します。例えば、2xxx系や7xxx系のアルミニウム合金は強度に優れています。 |
軽量性 | アルミニウムは非常に軽い金属で、密度は約2.7g/cm³です。これにより、軽量化が求められる用途で非常に有利です。 |
強度向上方法 | 1. 合金化:銅、マグネシウム、シリコンなどを加えることで、アルミニウム合金の強度を大幅に向上させます。 2. 熱処理:固溶化処理や時効処理によって、さらに強度を高めることができます。 |
強度と軽量性のバランス
- 強度向上: 銅やマグネシウムを含むアルミニウム合金は、特に航空機や自動車産業において、強度と軽量性を兼ね備えた材料として利用されています。
- 軽量性: アルミニウムは軽量で、輸送機器や構造材、パイプラインなど、多くの軽量化が求められる分野で利用されています。
特性を活かしたアルミニウムの革新的な用途
アルミニウムの特性を活かした革新的な用途は、航空機や自動車、建築分野などでますます増加しています。軽さ、強さ、耐食性を活かしたさまざまな応用例について紹介します。
用途 | 詳細説明 |
---|---|
航空機・宇宙産業 | アルミニウム合金は軽量で強度が高いため、航空機の構造材やエンジン部品に広く使用されています。 |
自動車産業 | 軽量化と強度向上を目指して、アルミニウム合金が車体やエンジン部品に活用されています。 |
建築業 | アルミニウムの耐腐食性と加工性を活かして、外壁パネルや窓枠に使用され、耐久性と美観を提供します。 |
再生可能エネルギー産業 | 太陽光パネルのフレームや風力タービンの部品など、耐久性と軽さが求められる分野で使用されています。 |
食品業界 | アルミ箔や缶の素材として、軽量で衛生的な特性を活かした製品が提供されています。 |
アルミニウムの革新的な用途
再生可能エネルギー産業: 太陽光発電システムや風力タービンの部品にはアルミニウムが使われ、耐久性と軽さがエネルギーの効率的な生成を支えています。
航空機・宇宙産業: アルミニウム合金は軽量でありながら高強度を持つため、航空機の構造やエンジン部品に使用されています。これにより燃費向上や運搬効率の改善が実現しています。
自動車産業: 車体部品やエンジン部品にアルミニウムが使用されることで、車両の軽量化が進み、燃費の向上や環境への負荷軽減に寄与しています。
建築業: アルミニウムの耐食性とデザイン性を活かして、外装や内装の建材として使用され、長寿命で美しい建築物が作られています。アルミニウム合金の軟化温度に関するQ&A
アルミニウム合金の軟化温度は、加工や使用において重要な要素となります。以下では、軟化温度に関するよくある質問とその解説、誤解を解くためのポイント、専門家からのアドバイスを紹介します。
軟化温度に関するよくある質問
軟化温度に関しては、使用する合金や加工方法によって異なるため、よく誤解されがちです。以下はよく寄せられる質問とその回答です。
質問 | 回答 |
---|---|
アルミニウム合金の軟化温度はどれくらいか? | アルミニウム合金の軟化温度は合金の種類によって異なりますが、一般的には400℃〜650℃の範囲です。 |
軟化温度が高いほど強度が増すのか? | 軟化温度が高いからと言って必ずしも強度が増すわけではなく、合金の組成や熱処理によって異なります。 |
軟化温度を知ることはなぜ重要か? | 軟化温度を把握することで、適切な加工方法や熱処理方法を選択し、製品の品質を確保することができます。 |
軟化温度はどのように測定するのか? | 軟化温度は、熱的な変化を測定する装置(例えば、熱分析装置)を使用して測定します。 |
軟化温度に関するよくある質問のまとめ
- 軟化温度は合金の種類により異なる: アルミニウム合金は、使用する元素(シリコン、銅、マグネシウムなど)によって軟化温度が変動します。
- 軟化温度の高低が強度に直結しない: 合金の組成や熱処理条件が強度に大きな影響を与えるため、軟化温度だけでは強度を判断できません。
- 適切な測定が重要: 軟化温度を正確に把握するためには、専門的な装置を使って測定することが必要です。
軟化温度に関する誤解と正しい理解
アルミニウム合金の軟化温度に関しては、誤解が多くあります。以下に誤解とその正しい理解を示します。
誤解 | 正しい理解 |
---|---|
軟化温度が高いほど強度が高い | 軟化温度が高いだけでは強度が高いわけではなく、合金成分や熱処理条件が強度に影響を与えます。 |
軟化温度を無視しても加工できる | 軟化温度を無視すると、加工中に変形や損傷が発生する可能性があるため、正確な理解と管理が必要です。 |
すべてのアルミニウム合金の軟化温度は同じだ | アルミニウム合金の軟化温度は、成分によって異なるため、合金ごとに適切な温度管理が求められます。 |
軟化温度に関する誤解と正しい理解
- 誤解1: 軟化温度が高いほど強度が高い。
正解: 強度は合金の成分や熱処理に依存し、軟化温度だけでは決まりません。 - 誤解2: 軟化温度を無視しても加工できる。
正解: 軟化温度を無視すると、加工中に金属が不均一に変形したり、品質が低下するリスクがあります。 - 誤解3: すべてのアルミニウム合金の軟化温度は同じ。
正解: アルミニウム合金の軟化温度は合金の成分や製造方法によって異なります。
専門家による軟化温度に関するアドバイス
専門家は、軟化温度を正しく理解し、適切な熱処理を行うことが製品の品質向上に繋がると述べています。以下はそのアドバイスです。
アドバイス | 詳細 |
---|---|
熱処理の温度管理を徹底する | 熱処理時に温度を適切に管理し、軟化温度を越えないように注意します。 |
合金の種類に応じた適切な軟化温度の選定 | 合金ごとに軟化温度が異なるため、使用する合金に応じて適切な温度を選定します。 |
適切なテスト機器の使用 | 軟化温度を正確に測定するために、高精度な熱分析装置を使用します。 |
軟化温度に関する専門家のアドバイス
テスト機器の使用: 熱処理の精度を高めるために、専用のテスト機器を使って軟化温度を正確に測定することを推奨します。
温度管理の重要性: 熱処理を行う際は、軟化温度を超えないように温度管理を徹底することが重要です。
合金別の温度選定: 合金の成分や用途に合わせて、適切な軟化温度を選ぶことで、より良い加工結果が得られます。
アアルミニウム合金の安全な取り扱いと保管
アルミニウム合金は、その軽さや強度から多くの産業で利用されていますが、安全に取り扱うためには適切な対策が必要です。また、長期保管時にも注意点があります。以下では、アルミニウム合金の安全な取り扱いと保管に関するポイントを紹介します。
アルミニウム合金の取り扱い時の安全対策
アルミニウム合金を安全に取り扱うためには、特にその物理的な特性や熱処理を行う際に注意が必要です。以下の表に、取り扱い時の安全対策をまとめました。
対策 | 詳細 |
---|---|
保護具の着用 | アルミニウム合金の加工時には、手袋や安全メガネ、保護服を着用し、火傷や怪我を防止します。 |
加工場所の換気 | 加工中に発生する粉塵やガスが有害な場合があるため、十分な換気を確保します。 |
高温での取扱い時の注意 | 熱処理や溶接など高温の作業では、アルミニウム合金が軟化するため、取り扱いに十分な注意が必要です。 |
取扱い時の滑り止め対策 | アルミニウム合金は表面が滑りやすいため、滑り止めを施した工具や装置を使用することが推奨されます。 |
アルミニウム合金の取り扱い時の安全対策まとめ
- 保護具の着用: 作業者の安全を確保するために、適切な保護具を常に使用します。
- 換気の確保: 有害なガスや粉塵を防ぐため、作業環境の換気を徹底します。
- 高温での作業時注意: 熱処理や溶接作業を行う際には、アルミニウム合金が軟化する可能性があるため、温度管理に特に注意します。
長期保管における注意点
アルミニウム合金を長期間保管する場合、以下のポイントに留意することが大切です。
注意点 | 詳細 |
---|---|
湿気と腐食の防止 | 湿気が原因でアルミニウム合金が腐食する可能性があるため、乾燥した環境で保管します。 |
直射日光の避ける | 直射日光にさらされると、アルミニウム合金の表面に不均一な熱影響が出ることがあるため、日陰で保管します。 |
温度管理 | 長期間の保管時には温度が高すぎないように管理し、アルミニウム合金が軟化しないように注意します。 |
衝撃や圧力からの保護 | 長期間にわたる圧力や衝撃によって変形する可能性があるため、積み重ねる際には衝撃を避けるようにします。 |
長期保管における注意点まとめ
- 湿気の管理: 湿気が原因となる腐食を防ぐため、乾燥した環境で保管します。
- 温度と直射日光の管理: 高温や直射日光にさらさないようにし、アルミニウム合金の品質を保持します。
- 衝撃からの保護: 保管中に変形しないように、適切な方法で取り扱い、圧力や衝撃から保護します。
軟化温度を考慮した保管条件の最適化
アルミニウム合金の保管においては、軟化温度を考慮した管理が重要です。軟化温度を超えると合金の強度や形状に悪影響を及ぼすため、以下の条件での保管が推奨されます。
保管条件 | 詳細 |
---|---|
最適な温度範囲の確保 | アルミニウム合金の軟化温度は約400℃〜650℃であるため、これを超えない温度で保管します。 |
温度の変動を抑える | 温度の急激な変動を避け、保管時の温度を安定させることで合金の特性を保ちます。 |
低温での保管を避ける | 低温環境でも問題は少ないですが、極端な寒冷環境は金属の脆化を引き起こす場合があるため注意が必要です。 |
軟化温度を考慮した保管条件の最適化まとめ
低温環境の注意: 極端な寒冷環境もアルミニウム合金に影響を与える可能性があるため、注意が必要です。
温度管理: 軟化温度を超えないように、保管場所の温度を適切に管理します。
温度変動の抑制: 急激な温度変動を避け、安定した環境で保管することが重要です。
アルミニウムを強くする熱処理の基礎知識
アルミニウムは、私たちの日常生活に欠かせない素材です。その軽さや耐久性から、建築や自動車産業をはじめ、さまざまな産業で広く使用されています。アルミニウムがさらに強くなる秘密の一端を担うのが「熱処理」です。熱処理は、材料の特性や用途に合わせて、アルミニウムの硬さや耐久性を向上させる方法です。本記事では、アルミニウムを強くする熱処理の基礎知識について探求していきます。アルミニウムについてさらに深く理解し、その魅力を知るために、ぜひご覧ください。
アルミニウムとは
アルミニウムの特性
アルミニウムの特性は軽量でありながら堅牢な素材であることから、多くの分野で利用されています。このアルミニウムをさらに強化する為に欠かせないのが熱処理です。熱処理によってアルミニウムの物理的な性質を改善し、硬度や強度を向上させることが可能です。
例えば、航空機の構造部品や自動車のフレームなどの高強度部品に使用される航空用アルミニウム合金は、特に熱処理が欠かせません。熱処理を施すことで、これらの部品は高い耐久性と信頼性を得ることができます。
したがって、アルミニウムの熱処理は、その用途に応じて異なる方法が用いられる重要な工程であり、素材の特性を最大限に引き出すための基本的な知識が求められます。
アルミニウム合金の種類と用途
アルミニウム合金は、自動車や航空機など多くの産業で使用されており、軽量かつ強度が高い特性が魅力です。熱処理は、アルミニウム合金の強度や耐久性を向上させる重要な工程です。例えば、溶解処理により合金内の不純物を取り除き、固溶処理で固溶体を作ります。さらに、時効硬化処理により微細な析出体を形成し、強度を向上させます。これにより、アルミニウム合金はより強く、耐久性に優れた材料となります。熱処理は製品の品質向上だけでなく、使用する環境や目的に応じて異なる処理が必要となります。アルミニウム合金の熱処理を理解することで、より効果的に材料を活用し、耐久性や性能を向上させることができます。
アルミニウム鋳物の基本
アルミ鋳物とは
熱処理は、アルミニウムの強度や耐久性を向上させる重要なプロセスです。アルミ鋳物は、アルミニウム合金を鋳造して作られた製品であり、様々な工業製品に広く使用されています。熱処理には、加熱、保持、そして冷却の段階が含まれます。例えば、T6処理では、アルミニウムを500℃以上に加熱し、一定時間保持した後、急冷することで強度を向上させます。このような処理によって、アルミニウムの結晶構造が整い、強度が増します。アルミ鋳物の品質や特性を向上させるために、正確な熱処理が欠かせません。熱処理によってアルミニウム製品の性能が高められ、製品の耐久性や信頼性が向上します。
アルミ鋳造方法の概要
アルミ鋳造方法の概要
アルミニウムは軽量で耐久性があり、様々な産業で利用されています。強度を高めるために、アルミニウム製品は熱処理を受けることが一般的です。熱処理は、アルミニウム合金を加熱し、適切な速度で冷却することで素材の性質を改良します。
熱処理にはいくつかの方法があります。例えば、固溶処理は合金を加熱し、その後急冷することで強度を向上させます。また、時効硬化は合金を加熱した後、一定時間保持して硬さを増す方法です。
アルミニウム製品の性能を最大限に引き出すためには、適切な熱処理が欠かせません。熱処理の選択は製品の用途や求める性能に合わせて行われるべきです。
アルミニウム熱処理の目的
アルミの熱処理による強化メカニズム
アルミの熱処理による強化メカニズム
アルミニウム製品を強化するために熱処理が行われます。この過程では、アルミニウム合金の結晶構造や組織が変化し、強度や耐久性が向上します。熱処理は冷却速度や加熱温度などの条件を変えることで、材料の性質に異なる影響を与えます。
例えば、固溶処理は、アルミニウム合金の固溶体を形成し、硬度を向上させます。その後、時効硬化を行うことで微細な析出体を生成し、強度を増加させることができます。このような熱処理工程が組み合わさることで、アルミニウム製品の性能が向上し、さまざまな産業で広く活用されています。
アルミニウムの機械的性質向上
アルミニウムの機械的性質を向上させるためには、熱処理が重要です。アルミニウム合金は、その組織を調整することで硬さや強度を向上させることができます。熱処理には、加熱と冷却のプロセスが含まれますが、適切な温度管理が不可欠です。
例えば、強度を向上させるためには、固溶処理と過飽和固溶処理が一般的に行われます。固溶処理では、合金を十分に加熱し溶解させ、その後急冷することで原子を均一に配置します。過飽和固溶処理では、余分な元素を添加した後、急冷することで元素を固溶させます。
これらの熱処理により、アルミニウム合金はより強く、耐久性が向上します。熱処理は、様々な産業界で重要な技術であり、アルミニウム製品の品質向上に欠かせない要素となっています。
アルミ熱処理の種類と特徴
焼き入れ(Quenching)
アルミニウムを強くするためには、熱処理が重要です。熱処理にはいくつかの手法がありますが、その中で焼き入れ(Quenching)があります。焼入れは素材を急速に冷却することで硬度を高めるプロセスです。具体的な例を挙げると、自動車のエンジン部品や航空機の構造部品など、高い強度が求められる製品に焼入れが用いられます。アルミニウムの強度を向上させるためには、適切な焼入れ処理が必要です。このように、熱処理は素材の特性を最大限に引き出すために欠かせない工程となっています。アルミニウム製品の品質向上や耐久性を高めるために、熱処理の基礎知識は重要です。
焼き戻し(Tempering)
アルミニウムを強化する熱処理の基礎知識
アルミニウムは軽量で耐食性に優れた金属です。その特性をさらに向上させるために使われる熱処理の1つに「焼き戻し」があります。焼き戻しは、アルミニウム合金を高温で加熱し、急冷して硬くし、その後適切な温度で保持して強度と耐久性を高める工程です。
この熱処理がなぜ重要かという理由は、例えば航空機の部品や自動車のエンジン部品など、高強度を要求される部品において、アルミニウムの性能を最大限に引き出すために必要不可欠な過程です。また、スポーツ用具や工業製品など、さまざまな分野で利用されています。
このように、焼き戻しという熱処理工程は、アルミニウムの強化において欠かせない重要なプロセスとなっています。
アニーリング(Annealing)
アルミニウムを強化するために重要な「アニーリング(Annealing)」とは、熱処理の一種であります。この工程では、アルミニウムを高温で加熱し、続いて徐々に冷却することで結晶構造を整え、材料の強度や耐久性を向上させることが可能です。
アニーリングの理由は、アルミニウムに内在する不純物や結晶欠陥を取り除き、より均質な材料を作ることが挙げられます。例えば、航空機の部品や自動車のフレームなどの高強度を要求される部品において、アニーリングは欠かせない工程となります。
アニーリングはアルミニウムだけでなく、他の金属材料にも広く応用される重要な処理方法であり、その効果は材料の特性向上に大きな影響を与えます。アルミニウム製品の品質向上や機能性向上を目指す際には、アニーリングの理解が不可欠です。
ソリューション処理(Solution Treatment)
アルミニウムを強くする熱処理の基礎知識
アルミニウムを強化する方法の一つに、ソリューション処理があります。ソリューション処理は、アルミニウム合金を高温で溶かし、それを急冷することで行われます。この過程により、合金内の不純物や析出物が均一に溶解し、結晶構造が整えられます。これにより、アルミニウムの強度や耐久性が向上します。
具体例として、航空機の部品や自動車のエンジン部品など、高い強度が要求される製品においてソリューション処理が広く利用されています。例えば、飛行機の翼やエンジン部品は、高い強度が必要ですが同時に軽量である必要があります。ソリューション処理によって、アルミニウム合金はこれらの要件を満たすことができます。
総じて、ソリューション処理はアルミニウム製品の機械的性質を向上させる重要なプロセスであることがわかります。
エイジング処理(Aging)
アルミニウムを強くする熱処理の基礎知識
アルミニウム合金は、様々な目的に合わせて熱処理されます。その中で重要なプロセスの一つがエイジング処理(Aging)です。エイジング処理は、アルミニウム合金を解固化させ、硬さと強度を向上させる方法です。
熱処理は、まず固溶処理を行い、その後急冷して結晶粒を微細化させます。次にエイジング処理を行うことで、微細化された結晶粒同士が結合し、合金全体の硬度が向上します。これにより、アルミニウム合金は強度や耐食性などの特性が向上し、さまざまな産業で幅広く使用されています。
エイジング処理は、適切な温度と時間で行うことが重要です。例えば、航空機の部品や自動車のフレームなど、高い強度が求められる製品では、適切なエイジング処理が欠かせません。アルミニウム合金を効果的に強化するためには、エイジング処理の理解が欠かせません。
アルミニウム合金鋳物のT5/T6熱処理
T5熱処理プロセス
アルミニウムを強くする熱処理の基礎知識
アルミニウム製品を強くする熱処理は、その特性を改善し、耐久性を高めるために重要です。熱処理は、素材内部の結晶構造を変化させることで硬さや強度を調整します。例えば、アルミニウム合金は、固溶処理や時効硬化などの熱処理プロセスを経て強度を向上させます。
固溶処理では、アルミニウム合金を高温で溶かし、急冷することで溶解された元素を均一に分散させます。それに対し、時効硬化では、固溶処理後に再加熱することで微細な析出物を生成し、結晶粒界を強化します。
熱処理は製品の用途や要求される性能に合わせて選択される必要があります。適切な熱処理を施すことで、アルミニウム製品の強度や耐久性を向上させることができます。
T6熱処理プロセス
アルミニウムを強化するためには、T6熱処理プロセスが重要です。このプロセスはアルミニウム合金を硬くし、強度を向上させる方法です。まず、アルミニウム合金を高温で加熱し、ある程度の時間保持します。その後、急速に冷却することで、結晶粒が微細化され、強度が向上します。
この熱処理プロセスは航空機の部品、自動車のフレームなど、高強度が求められる製品に広く利用されています。例えば、航空機の翼やエンジン部品は、T6熱処理を施すことで耐久性が向上し、安全性が確保されます。
アルミニウム合金の熱処理には様々な方法がありますが、T6処理はその中でも特に強化効果が高いとされています。アルミニウムを強化するためには、適切な熱処理プロセスを選択し、実施することが重要です。
T5/T6処理後の特性比較
[アルミニウムを強くする熱処理の基礎知識]
アルミニウムを強くするためには、T5処理やT6処理などの熱処理が重要です。T5処理では、アルミニウム合金を加熱して急冷することで硬さを向上させ、同時に強度を高める効果があります。一方、T6処理では、加熱後に急冷を行い、その後再度加熱をすることで硬さと強度をさらに向上させることができます。
例えば、自動車や航空機などの産業では、これらの熱処理が施されたアルミニウム合金が多く使用されています。その理由は、熱処理によってアルミニウムの強度や耐久性が向上し、高いパフォーマンスが得られるからです。これにより、安全性や信頼性が求められる製品において、アルミニウム合金が広く活用されています。
したがって、アルミニウムを強化し、特性を向上させるためには、適切な熱処理が欠かせない要素となります。熱処理の基礎知識を理解し、適切に施すことで、アルミニウム合金の性能を最大限に引き出すことが可能となります。
熱処理によるアルミニウム鋳造品の性能改善
強度と硬さの向上
アルミニウムを強くするためには、熱処理が重要です。熱処理は、アルミニウムの強度と硬さを向上させる方法の一つです。このプロセスでは、素材を特定の温度で加熱し、急冷することで結晶構造を変化させます。これにより、アルミニウムの硬度が高まり、強度も向上します。
例えば、航空宇宙産業では、アルミニウム合金を使った部品が頻繁に使用されます。これらの部品は高い強度が求められるため、熱処理が欠かせません。適切な熱処理を施すことで、航空機の安全性や信頼性を向上させることができます。
したがって、アルミニウムの強度と硬さを向上させるためには、適切な熱処理が欠かせないと言えます。熱処理を正しく行うことで、さまざまな産業でのアルミニウム製品の耐久性や品質が向上し、安全性が確保されます。
疲労強度の改善
アルミニウムを強くする熱処理の基礎知識
アルミニウム合金は、疲労強度を改善するために熱処理が重要です。疲労強度は、材料が繰り返し受ける応力に対する耐性を示す性質であり、熱処理によってこの性能を向上させることができます。
疲労強度を改善するためには、まずアルミニウム合金の組織を調整する必要があります。適切な熱処理を行うことで、結晶粒の大きさや分布を制御し、材料の強度や耐久性を向上させることができます。
例えば、航空機の部品や自動車のフレームなど、高い疲労強度が求められる場合には、適切な熱処理が欠かせません。熱処理を通じてアルミニウムの性能を最大限に引き出し、安全性や信頼性を高めることが重要です。
熱処理による応力緩和
アルミニウムを強化するための熱処理は、重要な工程です。熱処理によって、アルミニウム合金の結晶構造を整え、内部応力を緩和させることができます。具体的には、高温で加熱し、適切な速度で冷却することで、材料の硬さや強度を向上させることが可能です。
例えば、航空機の部品や自動車のボディパネルなど、高い強度が求められる製品において、熱処理は欠かせない工程となっています。アルミニウム合金は軽量で耐久性に優れているため、さまざまな産業において広く使用されています。
したがって、熱処理によってアルミニウムの特性を最大限に引き出し、製品の品質や性能を向上させることができるのです。アルミニウムの熱処理は、製品の信頼性向上に欠かせない要素と言えます。
熱処理プロセスの実施方法
熱処理設備と温度管理
アルミニウムを強化するには、適切な熱処理が重要です。熱処理は、アルミニウム合金の組織や性質を改善し、硬度や耐久性を向上させます。例えば、固溶処理は合金を加熱して溶解し、急冷して硬度を向上させる方法です。また、時効硬化は固溶処理後に適切な温度で保持することで、微細な析出物を形成し、強度を高めます。
熱処理設備と温度管理は、熱処理の成功に不可欠です。温度や保持時間の適切な制御によって、望ましい結晶や相の形成を促し、アルミニウムの性能を最大限に引き出します。特に、高温時の均一な加熱や急冷の処理は、製品の品質や性能に大きな影響を与えます。
要するに、熱処理はアルミニウム材料の強度や硬度を向上させる重要なプロセスです。適切な熱処理法を選択し、適切な温度管理を行うことで、優れた性能を持つアルミニウム製品を製造することが可能となります。
熱処理サイクルの選定
アルミニウムを強くするための熱処理は重要です。熱処理サイクルの選定にはいくつかの要素があります。まず、アルミニウム合金の組成や硬度などの特性を理解することが必要です。続いて、適切な熱処理法を選択します。例えば、固溶処理や時効硬化などがあります。これらの過程では、アルミニウム合金の微細な組織が変化し、強度や耐久性が向上します。また、過程中の温度制御や保持時間も重要です。例えば、急冷を行うことで硬度を向上させることができます。最終的に、適切な熱処理サイクルを選定することで、アルミニウムの性能を最大限に引き出すことが可能となります。
品質管理と検査手順
アルミニウムは、熱処理によって強度を向上させることができます。熱処理は、金属を加熱して適切な温度に保ち、それを急冷する工程です。この過程によって、アルミニウムの結晶構造が整理されて強度が向上します。
例えば、航空機の部品や自動車のエンジン部品など、高強度を求められる製品には、熱処理が欠かせません。また、スポーツ用具や自転車フレームなど、軽さと強度を両立させるためにも熱処理が重要です。
熱処理は、製品の使用環境や求められる性能に合わせて適切に行うことが重要です。アルミニウム材料の強度向上において熱処理は欠かせない要素であり、正確な処理が製品の品質向上に繋がります。
アルミニウム合金の熱処理に関する注意点
熱処理変形のリスク
アルミニウム製品を強化するためには、熱処理が欠かせません。熱処理は、アルミニウム合金の結晶構造を変え、硬度や強度を向上させます。しかし、熱処理には変形のリスクがあります。急激な冷却や適切でない温度制御が行われると、アルミニウム製品は歪んでしまう可能性があります。例えば、航空機の部品や自動車のエンジン部品など、高精度を要求される製品では、熱処理による変形は致命的な欠陥となり得ます。したがって、正確な温度管理と適切な冷却方法を用いることが重要です。アルミニウム製品の品質向上と安定した製品供給のために、熱処理プロセスには細心の注意が必要です。
熱処理条件の最適化
アルミニウムを強くするには、熱処理が重要です。熱処理は、アルミニウム合金の構造や性質を改善し、強度や耐久性を向上させるプロセスです。例えば、アルミニウム合金を高温で加熱して急冷すると強度が向上します。このような熱処理は、アルミニウム製品の品質と信頼性を高めるために欠かせません。
また、熱処理には異なる条件があります。例えば、アルミニウム合金の種類や用途によって最適な熱処理条件が異なります。そのため、熱処理条件の最適化は重要です。適切な熱処理条件を選択することで、アルミニウム製品の性能を最大限に引き出すことができます。
アルミニウム製品の強さや耐久性を向上させるためには、適切な熱処理が必要不可欠です。熱処理の重要性を理解し、適切な条件で行うことが製品の品質向上につながります。
熱処理後の処理と保護
アルミニウムを強くする熱処理の基礎知識
熱処理後の処理と保護
熱処理はアルミニウムの強度や耐久性を向上させる重要なプロセスです。熱処理後は、適切な処理と保護が必要です。処理の一環として、冷却や成形が行われ、その後の保護工程に移ります。例えば、表面に保護皮膜を施すことで、耐食性や耐摩耗性を向上させることができます。さらに、適切な保存方法も重要です。アルミニウム製品は湿気や腐食から守るために、適切な環境で保管する必要があります。
熱処理後の適切な処理と保護は、アルミニウム製品の性能や寿命を向上させる上で欠かせない要素となります。そのため、製品の取り扱いや管理には注意が必要です。
熱処理済みアルミニウム鋳物の応用例
自動車産業における応用
アルミニウムは軽量で耐食性に優れた素材ですが、強度を向上させるためには熱処理が欠かせません。熱処理はアルミニウム合金の結晶構造を変化させ、硬さや強度を向上させるプロセスです。
熱処理にはいくつかの方法がありますが、一般的なものには時効硬化や固溶処理などがあります。例えば、航空機の部品や自動車のフレームなど、高強度を要求される部品は熱処理が必須です。
アルミニウムの熱処理を理解することで、製品の性能や耐久性を向上させることができます。自動車産業など幅広い分野でアルミニウム製品が活用されており、熱処理の基礎知識を身につけることは重要です。
航空宇宙産業における応用
アルミニウムを強化するためには、熱処理が重要な基礎知識となります。熱処理は、アルミニウム合金の組織を変化させ、硬さや強度を向上させる過程です。例えば、アルミニウム合金を加熱して急冷することで、強度を高めることができます。このような熱処理は航空宇宙産業でも広く応用されています。航空機の構造部品やエンジン部品など、高い強度と軽量性が求められる部位において、熱処理を施すことで耐久性や性能を向上させることができます。航空宇宙産業において、アルミニウム合金の熱処理は欠かせない技術であり、安全性や信頼性を確保する上で重要な役割を果たしています。
高性能スポーツ用品における応用
アルミニウムを強化する熱処理は、高性能スポーツ用品において重要な基礎知識です。アルミニウムは軽くて耐久性がありますが、熱処理によってさらに強度や耐久性を向上させることができます。たとえば、自転車や釣り竿、テニスラケットなどのスポーツ用品では、強靭なアルミニウム合金が求められます。熱処理を行うことで、これらのアイテムの性能が向上し、より長く使えるようになります。さらに、熱処理によってアルミニウムの特性を最大限に活かすことができるため、スポーツ愛好家やプロ選手にとって重要な要素となっています。高性能スポーツ用品の製造においては、熱処理の技術が欠かせません。
まとめと今後の展望
アルミニウム熱処理技術の現状
アルミニウム熱処理技術の現状
アルミニウムを強化する熱処理は、金属製品の強度や耐久性を向上させるために重要です。この技術では、アルミニウム合金を特定の温度で保持し、適切な速度で冷却することが必要です。
熱処理にはいくつかの種類があります。例えば、固溶処理は合金を均一化し、強度を高めるための手法です。さらに、時効硬化では、合金を特定の温度と時間で保持し、硬度を調整します。
この技術は自動車や航空宇宙産業など幅広い分野で利用されており、製品の品質向上に貢献しています。アルミニウム熱処理技術の進化は、製造業における競争力を高めるために不可欠です。
熱処理技術の進歩と未来動向
アルミニウムを強くするためには、適切な熱処理が不可欠です。熱処理は、アルミニウム合金の結晶構造を変化させ、硬さや耐久性を向上させるプロセスです。例えば、固溶処理は、アルミニウム合金を高温で溶かし、急冷することで強度を高める方法です。さらに、時効硬化処理は、アルミニウム合金を高温で保持し、時間をかけて結晶を細かくすることで強度を増します。
これらの熱処理技術の進歩により、アルミニウム製品の強度や耐久性が向上し、さまざまな産業で幅広く活用されています。将来的には、さらなる研究と技術革新によって、より効率的な熱処理方法が開発されることが期待されます。アルミニウムの熱処理技術の発展は、産業界における革新と競争力の向上に貢献することでしょう。
まとめ
アルミニウム合金を強くするためには、熱処理が重要です。熱処理は材料の組織変化をもたらし、機械的性質を改良します。加えて、適切な熱処理を施すことで、アルミニウム合金の耐久性や強度を向上させることが可能です。熱処理はアルミニウム合金を用いた製品や構造物の品質を向上させるために必須であり、その基礎知識を理解することは重要です。
アルミニウムの比熱がもたらす驚くべき特性と利用法
アルミニウムは、私たちの日常生活において幅広く利用されている素材ですが、その特性や利用法についてご存知ですか?アルミニウムの比熱がもたらす驚くべき特性と利用法について、この記事では探っていきます。熱伝導率の高さや軽量さから、さまざまな産業や製品において重要な役割を果たしています。アルミニウムが持つ特性を理解することで、その可能性を最大限に活かす方法についてもご紹介します。アルミニウムの比熱がもたらす魅力と可能性に迫ります。
アルミニウムの基本と比熱の理解
アルミニウムとは
アルミニウムとは、非常に軽くて丈夫で、熱をよく伝導する金属です。この特性は、自動車や飛行機などの軽量化や高速化に重要な役割を果たしています。さらに、アルミニウムの比熱という特性は、熱を含みやすく、放出しやすいことを示します。つまり、急激な温度変化に対しても素早く対応できるメリットがあります。
例えば、アルミニウム製の調理器具は、加熱後の冷却が速く、熱が均一に伝わるため、料理の調理時間が短縮されます。さらに、アルミニウムを使用した太陽光発電パネルは、日中の熱を効率よく吸収し、エネルギーを生産するのに適しています。アルミニウムの比熱は、さまざまな産業や日常生活に応用され、その優れた特性を生かし、私たちの生活に多くの利益をもたらしています。
比熱とは何か?
アルミニウムの比熱とは、物質が温度変化に対してどれだけ熱を吸収または放出するかを表す性質です。具体的には、アルミニウムは非常に高い比熱を持っているため、熱エネルギーを多く吸収することができます。この性質から、アルミニウムは熱伝導性が良く、加熱や冷却が迅速に行われるため、様々な産業分野で幅広く利用されています。
例えば、アルミニウム製の調理器具は、熱を均等に伝導し、食材が焦げ付きにくい特性があります。また、自動車の部品や航空機の構造部品などでも、その軽量性と高い熱伝導性から優れた性能を発揮します。アルミニウムの比熱がもたらすこの特性は、現代の産業技術において欠かせないものとなっています。
アルミニウムの比熱の基礎データ
アルミニウムの比熱とは、この物質が温度変化に対してどれだけ熱を吸収する能力を示す指標です。アルミニウムは比熱が小さいため、熱を効率的に吸収し、放出することができます。この特性から、アルミニウムは熱伝導性が高く、加工しやすい金属として広く利用されています。例えば、アルミニウム製の調理器具は熱を素早く均一に伝えることができるため、調理に便利です。
また、アルミニウムの比熱が小さいことから、軽量化や省エネ効果を生かした製品開発にも貢献しています。自動車部品や航空機の材料としても重宝されており、高速で燃料効率の良い車両や航空機の開発に欠かせない素材です。アルミニウムの比熱は、その多彩な利用法や産業への貢献を支える重要な要素となっています。
アルミニウムの熱伝導率の特性
熱伝導率とは?
アルミニウムの比熱は、物質が熱を吸収する能力を示します。アルミニウムは非常に高い比熱を持つため、急激な温度変化に対しても安定した反応を示す特性があります。例えば、アルミ製の調理器具は、加熱後も長時間温かさを保つことができるのは、この高い比熱によるものです。また、車や電化製品など多くの製品にもアルミニウムが使用されており、その特性を活かした製品が多数存在します。
アルミニウムの比熱の特性を理解することで、さまざまな分野での利用法が広がっています。例えば、熱伝導率が高いことから、冷却フィンや熱交換器としても利用されています。さらに、自動車のエンジン部品や建築材料など、幅広い分野でアルミニウムの優れた性質が活かされています。アルミニウムの比熱は、その利用範囲の広さと革新性を示す重要な特性と言えるでしょう。
アルミニウムの熱伝導性のメカニズム
アルミニウムの比熱がもたらす驚くべき特性と利用法
アルミニウムは、金属の中でも比熱が高い性質を持っています。比熱とは、物質が熱を吸収する能力を表す指標であり、アルミニウムは熱をたくさん吸収できるため、急激な温度変化を和らげるのに役立ちます。この特性から、アルミニウムはさまざまな分野で幅広く活用されています。
例えば、アルミニウム製の調理器具は、熱が均等に伝わり、料理がムラなく調理できるため人気があります。また、自動車や航空機の部品にも使用されることが多く、軽量で強度もあります。さらに、建築や工業分野でもアルミニウムの比熱の特性が生かされており、耐熱性や耐食性に優れています。
アルミニウムの比熱がもたらすこのような優れた特性は、私たちの日常生活や産業活動に欠かせないものとなっています。
他の金属との比較
アルミニウムは、他の金属と比べて非常に軽量でありながら、高い比熱を持つ特性があります。比熱とは、物質が熱を吸収する能力のことであり、アルミニウムは多くの熱を吸収することができます。このため、アルミニウムは熱を効率よく保持することができる金属として広く利用されています。
例えば、アルミニウム製の保温容器は、保温性能が高く軽量で取り扱いやすいため、キャンプやアウトドア活動などで重宝されています。また、アルミニウム製の自動車パーツは軽量でありながら高い強度を持ち、燃費向上に貢献しています。
アルミニウムの比熱がもたらす優れた特性は、さまざまな産業で幅広く活用されており、その軽量かつ高い熱伝導性から注目を集めています。
アルミニウムの比熱が及ぼす影響
日常生活における比熱の役割
アルミニウムの比熱は、日常生活において驚くべき特性と利用法をもたらします。比熱とは、物質が熱を吸収して温度が上昇する際に必要な熱量のことを指します。アルミニウムは比熱が小さく、熱を素早く伝導する特性を持っています。このため、アルミニウム製の調理器具や自動車部品などが広く利用されています。
例えば、アルミニウム製の鍋は熱が均等に伝わり、料理を効率よく調理することができます。また、自動車のエンジン部品にも利用されており、軽量で熱を効率よく放出する性質から燃費の向上に貢献しています。
アルミニウムの比熱は、我々の日常生活を快適で効率的にするために欠かせない重要な特性として活躍しています。
工業分野での応用
アルミニウムの比熱は、その驚くべき特性と利用法に注目が集まっています。アルミニウムは熱を吸収しやすく、そして同時に放出もしやすい性質を持っています。この特性を活かし、アルミニウムは工業分野で幅広く利用されています。例えば、航空機の構造材料や自動車の部品、またはコンピューターの冷却装置など、さまざまな製品にアルミニウムが使われています。アルミニウムの比熱が高いことから、熱を効率的に蓄えることができるため、エネルギー効率の良い製品を作るのに適しています。工業分野におけるアルミニウムの利用は、製品の軽量化や高性能化に貢献しています。アルミニウムの比熱がもたらすこれらの特性は、今後もさらなる技術革新や産業の発展に向けて重要な役割を果たすことが期待されています。
エネルギー効率と環境への影響
アルミニウムの比熱は、その驚くべき特性と利用法をもたらしています。比熱とは、物質が温度変化する際に吸収または放出する熱の量を表す指標です。アルミニウムは非常に高い比熱を持つため、熱を効率的に蓄えることができます。この性質を活かし、アルミニウムはさまざまな分野で幅広く利用されています。
例えば、自動車産業ではアルミニウムが軽量でありながら高い強度を持つため、燃費向上や安全性の向上に貢献しています。また、建築業界でもアルミニウムの優れた伝熱性や耐久性が活かされ、耐久性のある窓枠や外装材として利用されています。
アルミニウムの比熱は、環境への影響も考慮され、エネルギー効率の向上にも貢献しています。そのため、今後もさらなる技術革新や利活用が期待されています。
アルミニウムの物理的性質への理解を深める
物理的性質の概要
アルミニウムは比熱が高いという特性を持っています。比熱とは、物質が熱エネルギーを吸収する能力のことで、アルミニウムは熱をたくさん吸収できます。この性質から、アルミニウムは熱伝導がよく、急激な温度変化にも強いと言われています。例えば、自動車のエンジン部品や調理器具など、さまざまな製品で活用されています。アルミニウムの比熱が高いことで、熱を効率的に取り扱うことができるため、エネルギーの消費量を抑えることができる利点もあります。このように、アルミニウムの比熱は、さまざまな産業分野で重要な特性として活用されています。
比熱と熱伝導率の関係性
アルミニウムの比熱と熱伝導率には密接な関係があります。比熱とは、物質が熱を吸収する際に必要な熱量のことを指し、アルミニウムは高い比熱を持つ特性があります。これは、アルミニウムが急激な温度変化に強いことを意味します。一方、熱伝導率とは、物質内で熱がどれだけ速く伝わるかを示す指標であり、アルミニウムは優れた熱伝導率を持ちます。例えば、アルミニウム製の調理器具は、短時間で均一に加熱されるため、料理の調理時間を短縮することができます。このように、アルミニウムの比熱と熱伝導率が優れていることから、様々な分野で活用されています。
物性データの読み解き方
アルミニウムの比熱とは、この金属が熱エネルギーをどれだけ吸収するかを表す重要な物性データの一つです。比熱が高いほど、熱を吸収しやすく、熱を貯めるのに適しています。例えば、アルミニウム製の調理器具は比熱が高いため、均一に熱を伝えることができ、料理を均等に加熱するのに適しています。また、アルミニウムは軽量で強度もあるため、自動車や航空機などの交通機器にも広く利用されています。
このように、アルミニウムの比熱はさまざまな製品や産業で重要な役割を果たしています。我々の日常生活においても、アルミニウムの比熱がさまざまな利便性をもたらしていることが分かります。アルミニウムの特性を理解することで、その効果的な利用法を考えることができ、より良い製品やサービスの開発につながるでしょう。
アルミニウムの特性データベース
特性データベースの重要性
アルミニウムの比熱とは、熱を蓄える能力を表す重要な特性です。この比熱の大きさにより、アルミニウムは熱を素早く吸収し、また放出することができます。例えば、アルミニウム製の鍋は、均一な熱の伝導性により料理を均等に加熱することができます。またアルミニウム箔は食品を包んで冷蔵庫に入れると、食材の冷却効率を高めることができます。このように、アルミニウムの比熱は様々な日常生活での利用法に活かされています。アルミニウム製品の多くは軽量でありながら強靭な特性を持ち、比熱を活かした革新的な製品が次々と登場しています。アルミニウムの比熱を理解することで、その驚くべき特性を最大限に活用できるでしょう。
データベースの活用方法
アルミニウムは、比熱という特性からさまざまな利用法が注目されています。比熱とは、物質が温度変化する際に必要な熱の量を表す指標で、アルミニウムは非常に高い比熱を持っています。
この特性から、アルミニウムは熱を効率的に吸収・放出する素材として利用されています。例えば、熱交換器や冷却装置、さらには調理器具など幅広い分野で活躍しています。
アルミニウムの比熱が高いことによって、省エネ効果や耐久性の向上など、さまざまな利点がもたらされています。これらの特性を活かして、アルミニウム製品のさらなる発展が期待されています。
アルミニウムのデータベースの例とアクセス方法
アルミニウムは熱を吸収しにくい性質を持っています。この性質は比熱として知られ、物質が熱を吸収する能力を示します。アルミニウムの比熱が高いため、急激な温度変化に対して安定した振る舞いを示します。例えば、アルミ製の調理器具は均一に熱を伝導し、料理を均等に加熱できます。
さらに、比熱が高いことから、アルミニウムは航空機や自動車などの軽量かつ耐熱性が求められる産業で広く使用されています。その軽量性と熱伝導性能から、燃費やパフォーマンスの向上に寄与しています。
アルミニウムの比熱はその多彩な利用法に影響を与え、産業や日常生活において重要な存在です。その特性を理解することで、より効率的な製品やシステムの開発につながる可能性があります。
アルミニウムの比熱に関する疑問点の解消
比熱にまつわる一般的な疑問
アルミニウムの比熱とは、物質が温度を変化させる際に必要な熱の量を示す性質です。この比熱はアルミニウムが熱をよく吸収し、また放出しにくい特性を持つことを示しています。具体的には、アルミニウム製の鍋は素早く熱を伝導し、料理を一定の温度に保つのに適しています。また、軽量でありながら高い強度を持つため、自動車や航空機の部品としても広く利用されています。
このように、アルミニウムの比熱がもたらす特性は非常に利便性が高く、さまざまな分野で活用されています。例えば、建築材料や電子機器、さらには医療機器に至るまで、幅広い用途で使用されています。アルミニウムの比熱を活かした製品は、私たちの日常生活において欠かせない存在となっています。
アルミニウムの比熱に特有な疑問点
アルミニウムの比熱に特有な疑問点
アルミニウムは、その比熱の特性からさまざまな利用法が可能となっています。比熱とは、物質が温まる際に必要なエネルギーの量を示す指標です。アルミニウムは比熱が小さいため、熱を素早く吸収し、また放出する性質があります。この特性を活かして、アルミニウムは熱伝導性に優れ、冷却材や加熱装置などの製品に広く使用されています。例えば、自動車のエンジン部品や調理器具などにアルミニウムが採用されているのは、その優れた比熱の特性が影響しています。アルミニウムの比熱がもたらす驚くべき特性は、さまざまな産業分野で重要な役割を果たしています。
疑問を解消するためのリソース
アルミニウムは、その特有の比熱からさまざまな特性を持っています。比熱とは、物質が熱を吸収する能力のことであり、アルミニウムの高い比熱は様々な利用法を可能にしています。
例えば、アルミニウム製の調理器具は、熱を均等に分散させることができるため、料理を効率よく調理するのに適しています。また、自動車のエンジン部品や飛行機の構造部品にも利用されており、軽量かつ高い耐熱性が求められる場面で重宝されています。
アルミニウムの比熱がもたらす驚くべき特性と多彩な利用法は、私たちの日常生活や産業に欠かせないものとなっています。そのため、アルミニウムは現代社会において重要な素材の一つと言えるでしょう。
アルミニウムの利用とその未来
現代におけるアルミニウムの利用法
アルミニウムは、軽量で強度があり、熱伝導率が高い特性を持つため、多くの産業で広く利用されています。例えば、自動車産業では、車体やエンジン部品などに使用されています。その理由は、アルミニウムが軽くて丈夫なため、燃費を向上させることができるからです。また、建築業界では、外壁や屋根などにも使用され、軽量化と耐久性を兼ね備えています。
比熱という性質は、アルミニウムをさらに魅力的な素材にしています。比熱とは、物質が吸収した熱エネルギーをどれだけ保持しやすいかを示す指標です。アルミニウムは高い比熱を持つため、熱を吸収しても急速に放出せず、温度を一定に保つことができます。この特性を活かし、アルミニウム製の調理器具や加熱装置が使われています。
このように、アルミニウムはその特性を活かした様々な製品に使われており、現代の様々な産業に貢献しています。
比熱を活かした新しい技術開発
アルミニウムの比熱がもたらす驚くべき特性と利用法
アルミニウムは、比熱という性質によってさまざまな革新的な技術開発が進んでいます。比熱とは、物質が熱を吸収して温度変化する際に必要な熱量のことです。アルミニウムは非常に高い比熱を持っており、急速な冷却や加熱にも耐えることができます。
この特性を活かして、アルミニウムは自動車産業や航空宇宙産業などさまざまな分野で利用されています。例えば、軽量でありながら高い強度を持つため、自動車の軽量化や燃費向上に貢献しています。さらに、アルミニウムの比熱を利用して、高速列車のブレーキディスクや電子機器の放熱材などにも活用されています。
アルミニウムの比熱は、さまざまな産業の技術革新に貢献し、未来のさらなる発展が期待されています。
持続可能な社会への貢献
アルミニウムは、比熱という性質から驚くべき特性を持っています。比熱とは、物質が温度変化に対してどれだけのエネルギーを吸収または放出するかを示す指標です。アルミニウムは比熱が高いため、熱をよく保持し、急激な温度変化から物を守る働きがあります。この特性から、アルミニウムは航空機や自動車などの軽量で耐久性が必要な産業で広く利用されています。また、アルミニウム箔は食品の包装にも使われ、食品の新鮮さや保存性を保つのに役立っています。アルミニウムの優れた熱伝導性と軽さは、さまざまな産業での利用法につながっています。そのため、アルミニウムの比熱はさまざまな分野での革新的な応用に貢献しています。
まとめ
アルミニウムはその高い比熱という特性からさまざまな利用法があります。この物質は熱を効率的に吸収し、放出することができるため、断熱材や熱交換器などの建築材料として利用されています。また、アルミニウム製の調理器具は、食材を均一に加熱するのに適しています。さらに、この金属は軽量でありながら強度があり、航空機や自動車などの産業製品にも広く使用されています。そのため、アルミニウムの特性を活かしたさまざまな製品が生まれています。
「A5052アルミ合金の腐食問題と対策ガイド」
A5052アルミ合金とは
A5052アルミ合金の特性
特性 | 詳細 |
---|---|
耐食性 | 海水や塩素などの腐食性環境に強く、耐食性が高い。 |
軽量 | 軽量であり、多くの製品において重要な材料として利用される。 |
加工性 | 加工性に優れ、製造コストも比較的低い。 |
使用例 | 海上コンテナ、車両部品、建築材料などで広く使用される。 |
酸化皮膜 | 長期間使用すると表面に酸化皮膜が形成される可能性がある。 |
腐食対策 | 適切な塗装や表面処理、定期的な点検が必要。 |
詳細な説明
A5052アルミ合金は、その優れた耐食性によって多くの産業で利用されています。特に海水や塩素などの腐食性環境に対して強く、海上コンテナや車両部品、建築材料などで使用されています。また、軽量で加工性も良く、製造コストが比較的低いため、様々な製品で重要な材料として活用されています。 しかし、長期間使用すると表面に酸化皮膜が形成されることがあります。この酸化皮膜が欠陥を持つと、腐食が進行する可能性があるため、定期的なメンテナンスや適切な処理が必要です。具体的には、適切な塗装や表面処理、定期的な点検などが推奨されます。これらの対策を講じることで、A5052アルミ合金の耐久性を向上させることができます。A5052合金の産業での利用
A5052アルミ合金は自動車部品や建築材料など幅広い産業で利用されています。しかし、この合金は腐食に弱いという問題があります。例えば、海洋環境や塩害のある地域では特に腐食が進みやすくなります。このような腐食を防ぐためには、適切な塗装や表面処理が欠かせません。また、定期的なメンテナンスや環境管理も重要です。産業用途でのA5052アルミ合金の使用を考える際には、腐食対策をしっかりと考慮することが重要です。腐食が進行すると合金の強度や耐久性が低下し、安全性や品質にも影響を及ぼす可能性があります。したがって、適切な腐食対策を行うことは産業におけるA5052アルミ合金の長寿命化や効率的な利用につながるでしょう。アルミニウムの腐食についての基礎
腐食とは何か
腐食とは、金属や合金が環境要因によって劣化する現象を指します。A5052アルミ合金は、軽量で強度があり、一般的に使用される素材ですが、腐食に弱い特性があります。海水や酸性雨などの湿気の多い環境下では、A5052アルミ合金は腐食しやすくなります。 この問題に対処するためには、適切な防食処理が重要です。例えば、塗装やめっきなどの表面処理を施すことで、A5052アルミ合金の腐食を防ぐことができます。定期的なメンテナンスや環境管理も、腐食対策には欠かせません。 したがって、A5052アルミ合金を使用する際には、腐食のメカニズムを理解し、適切な対策を講じることが重要です。適切な手入れと管理を行うことで、合金の寿命を延ばし、安全性を確保することができます。アルミニウムの腐食メカニズム
特性 | 詳細 |
---|---|
腐食の原因 | 塩分による電気化学的な反応が主な原因。 |
反応の過程 | 塩分がアルミニウム表面に吸着し、酸化反応を促進。 |
影響 | 腐食が進むと、機械的強度や見た目に影響を与える可能性がある。 |
対策 | 塩害の予想される場所での遮断保護や、定期的なメンテナンスが有効。 |
詳細な説明
A5052アルミ合金は、特に海水や塩分の高い環境下で腐食しやすいです。腐食のメカニズムは、塩分がアルミニウム表面に吸着し、酸化反応を促進することによって起こります。この電気化学的な反応により、アルミ合金の腐食が進行します。 この問題に対処するためには、適切な防食処理が必要です。具体的には、塩害が予想される場所では、アルミ合金に対して塩分からの遮断保護を行うことが効果的です。また、塩分を含む環境で使用する場合は、定期的なメンテナンスや塩害のチェックが推奨されます。 腐食が進行すると、アルミ合金の機械的強度や外観に悪影響を与える可能性があるため、適切な対策を講じることが重要です。腐食の種類と影響
腐食の種類 | 詳細 |
---|---|
湿気による腐食 | 湿気が原因でアルミ合金の表面が腐食しやすくなる。 |
塩分による腐食 | 塩分が電気化学的反応を促進し、腐食が進行する。 |
化学物質による腐食 | 化学物質がアルミ合金に直接的な攻撃を与える。 |
温度変化による腐食 | 温度の変化が腐食を加速させることがある。 |
詳細な説明
A5052アルミ合金は、一般的に優れた耐食性を持っていますが、さまざまな環境要因によって腐食の影響を受ける可能性があります。腐食は、金属が外部要因によって化学的に攻撃されるプロセスであり、以下の要因が腐食を促進します。- 湿気: 湿気は、アルミ合金の表面に水分を供給し、腐食を引き起こすことがあります。
- 塩分: 塩分は電気化学的な反応を促進し、腐食が進行する原因となります。
- 化学物質: 化学物質が直接的にアルミ合金に攻撃を加え、腐食を引き起こすことがあります。
- 温度変化: 温度の変化が腐食の進行を加速させる場合があります。
A5052アルミ合金の耐食性
耐食性とは
A5052アルミ合金は、耐食性に優れた素材です。耐食性とは、金属が錆びない性質のことを指します。A5052アルミ合金は、錆びにくく、劣化しにくい特徴を持っています。この特性から、建築、船舶、輸送機器など幅広い分野で使用されています。例えば、海水にさらされる船舶の部品や、屋外で使用される建築材料などに適しています。そのため、A5052アルミ合金は長期間耐久性を維持し、メンテナンスの頻度が低いという利点があります。このように、A5052アルミ合金の耐食性は、さまざまな産業で重要な役割を果たしています。A5052合金の耐食性の特徴
特徴 | 詳細 |
---|---|
耐食性の優れた点 | 塩水や酸性溶液に対して高い耐性を持つ。 |
使用分野 | 船舶建造、食品加工業界、建設業などで使用される。 |
腐食リスク | 塩分の多い海洋環境や化学物質が多い施設ではリスクが高い。 |
対策 | 定期的なメンテナンスや防食処理が重要。 |
詳細な説明
A5052合金は、その高い耐食性によって多くの産業分野で利用されています。この合金は、塩水や酸性溶液に対しても高い耐性を持ち、長期間使用しても錆びにくい特性があります。そのため、船舶建造や食品加工業界、建設業などで広く使用され、信頼性が高く評価されています。 ただし、環境や使用条件によっては腐食が進行する可能性があります。特に塩分の多い海洋環境や化学物質が多く存在する産業施設では、腐食のリスクが高まります。これを防ぐためには、適切なメンテナンスや防食処理が必要です。 産業界では、A5052合金の耐食性を活かした対策や管理方法が積極的に取り入れられています。定期的な点検や適切な塗装を行うことで、合金の寿命を延ばし、安全性を確保する取り組みが進められています。耐食性に影響を与える要因
要因 | 詳細 |
---|---|
環境要因 | 湿潤な気候、化学物質、塩分が腐食を引き起こす。 |
製造過程 | 製造時の不良が腐食を促進する可能性がある。 |
取り扱い方法 | 保管時の湿気や海洋環境での塩分が影響を与える。 |
詳細な説明
A5052アルミ合金の耐食性は、様々な要因から影響を受けます。主要な要因としては以下のようなものがあります:- 環境要因: 日本の湿潤な気候は、金属部品に腐食を引き起こしやすくします。また、化学物質や塩分などの外部要因も腐食の進行を促進します。これらの要因は、アルミ合金の耐食性に大きな影響を与えるため、適切な防食処理が重要です。
- 製造過程: 製造時の不良が原因で、金属の表面に欠陥が生じることがあります。これにより、腐食が進行しやすくなります。また、製造後の保管時に湿気が溜まると、さらに腐食が進行する可能性があります。
- 取り扱い方法: 海洋環境での使用では、塩分が直接アルミ合金に影響を与えるため、定期的な洗浄や塩分除去が必要です。取り扱いや保管の際には、湿気や汚れを防ぐための細心の注意が求められます。
A5052アルミ合金の腐食問題
A5052合金の腐食原因
腐食原因 | 詳細 |
---|---|
環境要因 | 湿気や塩分が多い環境で腐食しやすい。 |
海岸近くや塩害地域 | 腐食リスクが高まりやすい。 |
詳細な説明
A5052アルミ合金の腐食原因は主に環境要因によるものです。この合金は比較的高い耐食性を持っていますが、湿気や塩分が多い環境では錆びやすくなります。特に、海岸近くや塩害のある地域では、腐食のリスクが高まります。 腐食を防ぐためには、定期的なメンテナンスや塗装が重要です。適切なコーティングを施すことで耐久性を向上させることができます。例えば、海水や塩害にさらされる建造物では、定期的なクリーニングや特殊なコーティングが効果的な腐食対策となります。 しっかりとした管理と保守を行うことで、A5052アルミ合金の腐食を最小限に抑えることができます。環境に適した対策を講じることで、合金の耐久性を高め、長期間にわたり使用することが可能となります。湿潤環境下での脆化特性
特性 | 詳細 |
---|---|
腐食の影響 | 湿潤環境下で金属が酸素や水と反応して劣化する。 |
定期的なメンテナンス | 塗装や被覆の点検と損傷部分の修復が重要。 |
防錆コーティング | 湿気や塩分の多い環境での効果的な対策。 |
使用例 | 海洋近くの建造物や自動車部品など。 |
詳細な説明
A5052アルミ合金は、湿潤環境下で腐食に弱い性質があります。腐食は金属が酸素や水と反応して劣化する現象で、特に湿気や塩分が多い環境では腐食が進行しやすくなります。この問題に対処するためには、適切な対策が必要です。- 定期的なメンテナンス: 合金表面の塗装や被覆を定期的に点検し、損傷部分を迅速に修復することが重要です。これにより、腐食の進行を防ぎます。
- 防錆コーティング: 湿気や塩分の多い環境では、防錆コーティングの施工が効果的です。これにより、合金の表面を保護し、腐食リスクを低減します。
- 使用例: 特に海洋近くの建造物や自動車部品など、湿潤環境下で使用される製品では、腐食対策が重要です。適切な対策を講じることで、A5052アルミ合金の耐久性を高め、製品の寿命を延ばすことができます。
腐食による問題事例
A5052アルミ合金は、優れた特性を持つ素材ですが、腐食による問題が発生することがあります。海洋や工業環境など、腐食の影響を受けやすい状況では、この合金が劣化しやすくなります。たとえば、海水中で使用される船舶や構造物は、長期間の使用によって腐食が進行し、安全性に問題を引き起こす可能性があります。 これを防ぐためには、定期的なメンテナンスや適切な塗装、腐食防止処理が必要です。また、使用環境に応じた適切な保護措置を講じることが重要です。例えば、腐食しやすい箇所には定期的な点検を行い、早めの対処をすることで、合金の劣化を防ぐことができます。 腐食は予測困難な問題ですが、適切な管理と対策を講じることで、A5052アルミ合金の長寿命化と安全性確保が可能です。アルミ合金の腐食対策
腐食対策の基本
A5052アルミニウム合金は腐食耐性に優れていますが、特定の環境条件下では腐食する可能性があります。腐食をしっかり防ぐためには、適切な対策が必要です。まず、定期的なメンテナンスや清掃が重要です。さらに、塗装や表面処理を施すことで耐久性を高めることができます。 例えば、海岸近くや工業地域など腐食のリスクが高い場所では、定期的な塗装や防錆処理を行うことが重要です。また、適切な保管方法や環境管理も腐食を防ぐために重要です。 腐食問題を未然に防ぐことで、A5052アルミ合金の寿命を延ばし、安全性を確保することができます。適切な腐食対策を行うことは、材料の劣化を防ぎ、コストを節約する重要な手段となります。A5052アルミ合金の保護方法
A5052アルミ合金の腐食問題は重要です。腐食は金属が酸素や水と反応して劣化する現象です。この問題を解決するために、適切な対策が必要です。例えば、塗装や表面処理を行うことでアルミ合金の保護が可能です。さらに、定期的なメンテナンスや保護フィルムの使用も効果的です。これらの対策を実施することで、アルミ合金の寿命を延ばし、安全性を向上させることができます。腐食防止は重要なテーマであり、適切な対策を取ることで長期的な利用が可能となります。A5052アルミ合金を効果的に保護するためには、腐食のメカニズムを理解し、適切な対策を講じることが不可欠です。環境因子の管理
管理方法 | 詳細 |
---|---|
表面処理やコーティング | 適切な処理を施すことで腐食を防ぐ。 |
定期的な点検 | 定期的な点検とメンテナンスが重要。 |
厳しい環境下の対策 | 海岸付近や工業地帯などではより注意が必要。 |
詳細な説明
A5052アルミ合金の腐食問題は、主に環境因子によって引き起こされます。湿気や塩分、化学物質などがアルミ合金に影響を与え、腐食を進行させる可能性があります。これらの要因に対処するためには、以下の管理方法が重要です:- 表面処理やコーティング: 適切な表面処理やコーティングを施すことで、アルミ合金の腐食を効果的に防ぐことができます。防錆コーティングや特殊な塗装が推奨されます。
- 定期的な点検: 定期的な点検とメンテナンスを行うことで、腐食の兆候を早期に発見し、対策を講じることができます。点検を怠ると、腐食が進行し、修復が困難になる可能性があります。
- 厳しい環境下の対策: 海岸付近や工業地帯など、腐食リスクが高い環境では、特に注意が必要です。これらの環境下では、より強力な防食対策を講じることが求められます。
アルミニウム加工時の変色防止
加工時の変色とは
【A5052アルミ合金の腐食問題と対策ガイド】 A5052アルミ合金は、耐食性が高い素材として知られています。しかし、特定の環境下では腐食が進行することがあります。腐食の要因としては、湿気や酸性の溶液、塩分などが挙げられます。こうした環境が長時間にわたって作用すると、表面に変色やダメージが生じる可能性があります。 それを防ぐためには、定期的なメンテナンスや適切な処理が必要です。例えば、塗装やめっきを施すことで腐食を防ぐことができます。また、アルミ合金を使用する際には、環境に応じた適切な保護処置を行うことが重要です。適切な予防策を講じることで、A5052アルミ合金の腐食を抑えることが可能です。変色防止のための処理方法
処理方法 | 詳細 |
---|---|
アルマイト処理 | 耐蝕性を向上させるための表面処理。 |
塗装 | 腐食から保護するための手段。 |
めっき処理 | 防錆効果を持つコーティング。 |
適切な保管方法 | 湿気や塩分の多い環境から遠ざける。 |
定期的な清掃・メンテナンス | 清掃と点検を行い、腐食の兆候を早期に発見する。 |
詳細な説明
A5052アルミ合金は優れた性能を持つものの、腐食や変色の問題に直面することがあります。これらの問題に対処するためには、以下の処理方法が有効です:- アルマイト処理: アルマイト処理は、アルミニウム表面に酸化膜を形成し、耐蝕性を向上させるための処理方法です。この処理により、アルミ合金の耐久性が増し、変色を防ぐことができます。
- 塗装: アルミ合金の表面に塗装を施すことで、腐食から保護することができます。適切な塗料を選ぶことで、耐蝕性を高め、外観を保つことが可能です。
- めっき処理: めっき処理は、防錆効果を持つコーティングを施す方法で、アルミ合金の耐蝕性を向上させます。亜鉛メッキやクロムメッキなどが一般的です。
- 適切な保管方法: 湿気や塩分の多い環境からアルミ合金を遠ざけることで、腐食リスクを低減できます。適切な保管方法を選ぶことが重要です。
- 定期的な清掃・メンテナンス: 定期的な清掃とメンテナンスを行い、腐食の兆候を早期に発見して対処することが大切です。
変色防止のための保管と取り扱い
A5052アルミ合金は耐食性に優れているが、腐食には注意が必要です。腐食を防ぐためには、適切な保管と取り扱いが重要です。まず、アルミ合金は湿気や塩分を避けることが重要です。例えば、海辺で使用した後は、きちんと乾かしてから保管することが大切です。また、アルミ合金を他の金属と接触させることも避けるべきです。異なる金属同士が接触することで腐食のリスクが高まります。例えば、A5052アルミ合金と鉄を一緒に保管することは避けましょう。適切な保管と取り扱いを行うことで、アルミ合金の腐食を効果的に防ぐことができます。実践ガイド
日常的な腐食対策
A5052アルミ合金の腐食問題は重要な課題です。この合金は、海洋環境や化学物質などにさらされることが多く、腐食が進行しやすい特性があります。腐食を防ぐためには、適切な対策が必要です。 まず、塗装やめっき処理などの表面処理を施すことが有効です。これにより、アルミ合金の表面が保護され、腐食から守られます。さらに、定期的な点検やメンテナンスを行うことも重要です。腐食が進行する前に早めに発見し、対処することで長い寿命を持続させることができます。 例えば、海洋プラントや自動車部品など、さまざまな産業分野でA5052アルミ合金が使用されています。これらの分野では、腐食対策が欠かせません。適切な対策を講じることで、合金の性能を最大限に引き出し、安全性と耐久性を確保することができます。長期にわたる保護策
A5052アルミ合金の腐食問題は重要な課題です。腐食は、アルミ合金が金属として持つ弱点であり、特に海洋環境や化学物質の影響を受けやすいです。この問題に対処するためには、適切な対策が必要です。 まず、定期的なメンテナンスと清掃が欠かせません。塩分や酸性の影響を受けやすい箇所は特に注意が必要です。さらに、特殊なコーティングや防食処理を施すことで、腐食を防ぐことができます。例えば、耐食性が高い塗装や被覆材を使用することで、アルミ合金の耐久性を向上させることができます。 このような対策を講じることで、A5052アルミ合金の腐食を防ぎ、長期的な保護を確保することが可能です。腐食問題に早めに対処することで、機器や構造物の寿命を延ばし、安全性を確保することが重要です。腐食対策のトラブルシューティング
A5052アルミ合金の腐食問題は、金属部品や構造物に深刻な損害をもたらす可能性があります。この問題を解決するためには、腐食対策が重要です。腐食は、金属が酸素や水などの環境条件と反応して変質する現象です。この問題を防ぐためには、防食処理や定期的な保守点検が重要です。例えば、A5052アルミ合金の表面に保護膜を形成することで腐食を防ぐことができます。また、塩分の多い環境下では腐食が進みやすいため、海岸地域などでは特に注意が必要です。腐食対策を怠ると、損害が拡大し修復コストがかさんでしまう可能性があります。したがって、定期的な点検と適切な腐食対策を行うことが重要です。まとめと今後の展望
A5052アルミ合金腐食対策の重要性
A5052アルミ合金は、腐食が問題になることがあります。この腐食対策は非常に重要です。例えば、A5052アルミ合金が使用される建物や構造物は、長期間にわたって安全性を保つ必要があります。腐食が進行すると、強度が低下し、構造物の安全性が損なわれる可能性があります。 腐食対策にはさまざまな方法があります。例えば、適切な塗装やコーティングを施すことで、アルミ合金表面を保護することができます。定期的な点検やメンテナンスも欠かせません。これにより、腐食の早期発見や対処が可能となります。 したがって、A5052アルミ合金を使用する場合は、腐食対策を適切に行うことが重要です。安全性を確保し、長寿命化を図るためにも、定期的な管理とメンテナンスを積極的に行いましょう。今後の技術開発と予測
【A5052アルミ合金の腐食問題と対策ガイド】 A5052アルミ合金は軽くて強度があり、多くの分野で使用されています。しかし、腐食が問題となることもあります。この腐食の原因は、主に環境中の酸素や湿気、塩分などが挙げられます。腐食により、合金の性能が低下し、寿命が短くなる可能性があります。 この腐食問題に対処するためには、適切な防止策が必要です。例えば、塗装やめっき、陽極酸化処理などの表面処理が有効です。定期的なメンテナンスや環境管理も重要です。特に海洋や塩害のある場所では、注意が必要です。 A5052アルミ合金の腐食を防ぐためには、適切な管理と保守が欠かせません。適切な対策を講じることで、合金の耐久性を向上させ、安全性を確保することができます。まとめ
アルミニウム合金A5052は、耐食性に優れた材料ですが、腐食の問題が発生することがあります。そのため、適切な対策を講じることが重要です。腐食を回避するためには、定期的なメンテナンスや適切な塗装が必要となります。また、アルミニウム合金に関する正しい知識を持つことも重要です。 腐食対策には、環境の影響を受けにくい素材を使用することや、腐食の原因となる化学物質から材料を保護することなどがあります。定期的な点検と保守が、アルミニウム合金の腐食対策において不可欠です。腐食問題に対する適切な対策を講じることで、材料の耐久性を向上させることができます。腐食に強い!アルミニウム製品の長持ちさせるコツ
アルミニウム製品は軽量で丈夫、そしてお手入れが比較的簡単という利点がありますが、長く使い続けるためには腐食に気を付ける必要があります。この記事では、アルミニウム製品を長持ちさせるためのコツをご紹介します。アルミニウム製品を日常的に使用している方や、これから使おうと考えている方にとって役立つ情報が満載です。さあ、アルミニウム製品の持続可能な使い方について一緒に探求していきましょう。
アルミニウム製品とは
アルミニウムの特性
アルミニウムは腐食に強い特性を持つ金属で、その長所を活かすことで製品の寿命を延ばすことができます。この特性は、湿気の多い環境や塩分の多い場所でも優れています。例えば、船舶や建物の外装、自転車のフレームなど、様々な製品で広く利用されています。アルミニウム製品を長持ちさせるコツは、定期的な清掃と塗装が重要です。塗装はアルミニウム表面を保護し、腐食や劣化を防ぎます。さらに、製品に傷やへこみがある場合は修理を早めに行うことも大切です。これらの対策をしっかりと行うことで、アルミニウム製品を長く美しく使い続けることができます。
アルミニウム製品の一般的な使用例
アルミニウム製品は、腐食に強い特性を持っています。この特性を活かして製品を長持ちさせるコツを紹介します。まず、アルミニウム製品を清潔に保つことが重要です。定期的な掃除や乾拭きで、付着した汚れや水分を取り除きましょう。また、塗装や表面処理が施されている場合は、定期的なメンテナンスが欠かせません。腐食が進む前に修繕することで、製品の寿命を延ばすことができます。
さらに、アルミニウム製品を屋外で使用する場合は、適切な保管方法も重要です。雨や湿気の影響を受けないようにカバーするなど、環境に配慮した保管を心掛けましょう。これらのコツを守ることで、アルミニウム製品を長く美しく使い続けることができます。
アルミニウムの腐食とは
アルミニウムの腐食とは、アルミニウム製品が錆びや劣化することを指します。この腐食を防ぐためには、いくつかのポイントがあります。まず、定期的な清掃と乾燥が重要です。湿気や汚れが付着すると、腐食が進行しやすくなります。また、アルミニウム表面に保護膜を形成する塗料やコーティングを施すことも効果的です。これによって、外部からの侵害を防ぎ、耐久性を高めることができます。例えば、屋外で使用するアルミニウム製品は、風雨や紫外線から保護するために定期的なメンテナンスが必要です。腐食に強いアルミニウム製品を長持ちさせるためには、適切な手入れと保護が欠かせません。
アルミニウム製品のお手入れ方法
日常的なお手入れの基本
[腐食に強い!アルミニウム製品の長持ちさせるコツ]
アルミニウム製品は軽量で丈夫であり、多くの場面で活躍しています。しかし、長く使い続けるためには適切なお手入れが欠かせません。腐食はアルミニウム製品が劣化する主な要因の一つですが、適切な手入れを行うことでその寿命を延ばすことができます。
まず、アルミニウム製品を使った後は、水で優しく洗い、その後すぐに乾かすことが大切です。特に塩分や汚れがついた場合は、早めに取り除くことが腐食の予防につながります。また、定期的にワックスや専用のプロテクターを使って保護することも効果的です。
これらの基本的なお手入れを怠らずに行うことで、アルミニウム製品の腐食を防ぎ、長く美しい状態を保つことができます。
洗浄剤の選び方と使用方法
アルミニウム製品を長持ちさせるためのコツは、腐食に強い洗浄剤を選ぶことです。アルミ製品は、長期間使っていると酸や塩分などの腐食物質が付着しやすくなります。このため、適切な洗浄剤を使って定期的にお手入れすることが重要です。
一般的な家庭用洗剤や重曹を使うと、アルミニウム表面が傷ついてしまうことがあります。そこで、専用のアルミニウム向きの洗浄剤を使用することで、効果的に汚れを落としつつ、表面を傷つけずにきれいに保つことができます。
例えば、市販されているアルミニウム用の洗浄剤は、塗布後しばらく放置してから軽くこすって洗い流すことで、効果的に汚れを落とすことができます。このように、適切な洗浄剤を使用して正しい方法でお手入れすることで、アルミニウム製品の耐久性を高めることができます。
お手入れにおけるNG行為
[腐食に強い!アルミニウム製品の長持ちさせるコツ]
アルミニウム製品は軽量で丈夫な素材ですが、腐食に弱い性質も持っています。長く使いたい方は、適切なお手入れが必要です。
まず、アルミニウム製品を長持ちさせるためには、水や湿気を避けることが重要です。湿気が付着すると腐食が進みやすくなります。次に、洗った後は十分に乾かすことも大切です。水滴が残っていると、腐食の原因となります。
また、定期的なメンテナンスも欠かせません。汚れや塗装の傷は腐食の進行を早める可能性があるため、定期的に清掃や塗装のリペアを行いましょう。
これらのコツを守ることで、アルミニウム製品を長く美しく使うことができます。お手入れを怠らず、大切に扱うことで、アルミニウム製品の寿命を延ばすことができるでしょう。
アルミニウム製品の腐食対策
腐食の原因と予防
アルミニウム製品は腐食に強い特性を持っています。腐食の主な原因は、湿気や化学物質、塩分などの外部要因によるものです。腐食を予防するためには、定期的な清掃や保護コーティングの施工が重要です。例えば、外部要因から保護するために、アルミニウム製品に特殊な塗料を塗布することで耐久性を向上させることができます。さらに、湿気の多い環境では、湿気を吸収するシリカゲルを使用することで腐食を防ぐことができます。これらの対策を行うことで、アルミニウム製品の寿命を延ばすことができます。腐食を予防することで、アルミニウム製品の美しさや機能性を長く保つことができます。
保管時の注意点
[腐食に強い!アルミニウム製品の長持ちさせるコツ]
アルミニウム製品を長持ちさせるためには、腐食に気をつけることが重要です。アルミニウムは錆びにくい素材ですが、適切な手入れが必要です。例えば、アルミニウム製品を使用した後は、水で洗い、よく乾かすことが大切です。特に塩分を含む環境で使用した場合は、こまめに洗浄してください。さらに、アルミニウム製品を長期間保管する際は、湿気を避け、直射日光や高温を避けることもポイントです。例えば、屋外で使用した調理器具は、きちんと乾かしてから収納することが重要です。これらのコツを守ることで、アルミニウム製品を長く美しく使用することができます。
腐食を防ぐためのコーティング方法
アルミニウム製品の腐食を防ぐためには、適切なコーティングが重要です。腐食はアルミニウム製品にとって大敵であり、錆が出ると耐久性が低下します。例えば、自動車や家具、建築資材などのアルミニウム製品は、長期間美しさを保つためにコーティングが必要です。
コーティング方法の一つには、耐久性が高く広く使われている陽極酸化処理があります。この処理は、アルミニウム表面に酸化皮膜を形成し、耐蝕性や耐摩耗性を向上させます。他にも、塗装や合金化などの方法もありますが、適切な方法を選択することが重要です。
アルミニウム製品を長持ちさせるためには、定期的なメンテナンスや適切なコーティングが欠かせません。これらの対策を講じることで、アルミニウム製品の寿命を延ばし、美しさを保つことができます。
アルミ製品の耐食性向上
耐食性を高めるアルミニウム合金
腐食に強い!アルミニウム製品の長持ちさせるコツ
アルミニウム合金は、軽量で丈夫な素材ですが、腐食に弱いという欠点もあります。腐食を防ぐためには、適切な手入れが必要です。まず、アルミニウム製品を清潔に保つことが重要です。定期的な洗浄と乾燥を行うことで、錆や腐食を防げます。さらに、塗装やクリアコートの施工を行うことで、表面を保護することができます。
例えば、自転車や車のホイールなど、外部環境にさらされる製品は特に腐食しやすいです。こうした製品は、こまめなメンテナンスを行い、保護フィルムなどを使用して対策をすると長持ちさせることができます。
アルミニウム製品を長持ちさせるためには、定期的な手入れと適切な保護が欠かせません。腐食を防ぎ、製品の寿命を延ばすために、細心の注意を払いましょう。
表面処理による耐食性の向上
アルミニウム製品は、腐食に強い特性を持っています。この耐食性を長持ちさせるためのコツは、適切な表面処理をすることです。アルミニウムの表面処理によって、耐食性が向上し、製品の寿命が延びます。
なぜなら、アルミニウムはそのままでは酸化しやすく、腐食しやすい性質を持っているからです。しかし、表面処理をすることでこの問題を解決できます。例えば、アルマイト処理や塗装を施すことで、アルミニウム製品の表面を保護し、耐久性を高めることができます。
したがって、アルミニウム製品を長持ちさせるためには、定期的なメンテナンスや適切な表面処理が重要です。適切な手入れを行うことで、アルミニウム製品の美しさと機能性を長く保つことができます。
環境因子と耐食性の関係
アルミニウム製品を長持ちさせるためのコツは、腐食に強い素材であることです。アルミニウムは軽くて丈夫な素材であり、さまざまな製品に広く使用されています。その秘訣は、環境因子と耐食性の関係にあります。アルミニウムは酸化被膜を形成する特性があり、この被膜が腐食から保護してくれます。例えば、屋外で使用されるアルミニウム製品は、雨や風などの自然の影響を受けますが、その耐久性から長く美しい状態を保つことができます。
そのため、アルミニウム製品を長持ちさせるには、定期的な清掃とメンテナンスが重要です。適切な手入れを行うことで、腐食を防ぎ、製品の寿命を延ばすことができます。アルミニウム製品はその特性を活かして長くご利用いただくために、丁寧な管理が必要です。
アルミニウム製品の長持ちさせるコツ
定期的なメンテナンスの重要性
アルミニウム製品を長持ちさせるコツは、腐食に強いことを活かすことです。アルミニウムは錆びにくい性質を持っていますが、定期的なメンテナンスが欠かせません。例えば、アルミニウム製品を清潔に保つことや、汚れや塩分をこまめに拭くことで腐食を防ぐことができます。さらに、アルミニウム製品を保管する際は湿気や直射日光を避けることも重要です。たとえば、外部のアルミ製品を定期的に洗浄し、コーティング剤を使用して保護することが効果的です。このように、腐食に強いアルミニウム製品を長持ちさせるためには、定期的なメンテナンスと適切な保管方法が欠かせません。
長期保存のためのベストプラクティス
アルミニウム製品を長持ちさせるためのコツは、腐食に強いという特性を活かすことです。アルミニウムは錆びにくい素材であり、適切なケアをすることで長期保存が可能です。例えば、アルミニウム製品を使用した後は、水で優しく洗い、乾燥させることが大切です。また、塩分や化学物質から保護するために定期的なメンテナンスが欠かせません。例えば、アルミニウム製の調理器具は、洗った後に乾燥させると長持ちします。また、野外で使用するアルミニウム製品は、使用後にしっかりと清潔にし、湿気を避けるように保管することが大切です。これらのコツを守ることで、アルミニウム製品の劣化を防ぎ、長くお使いいただけます。
アルミニウム製品の修理と再生方法
アルミニウム製品を長持ちさせるためのコツを紹介します。アルミニウムは軽くて丈夫な金属ですが、腐食に弱い性質を持っています。そのため、定期的なお手入れや適切な管理が重要です。まず、腐食を防ぐために、定期的に掃除を行い、水分や汚れを取り除きましょう。また、アルミニウム用の防錆剤やコーティング剤を使用することも効果的です。
例えば、屋外で使用するアルミニウム製品は、雨や風にさらされることが多いため、特に注意が必要です。定期的なメンテナンスを怠らず、劣化や腐食の兆候を見逃さないようにしましょう。これにより、アルミニウム製品の寿命を延ばし、美しさを保つことができます。腐食に強いアルミニウム製品を長く楽しむために、適切なお手入れが大切です。
よくある質問とトラブルシューティング
腐食に関するQ&A
[腐食に強い!アルミニウム製品の長持ちさせるコツ]
アルミニウム製品が腐食に強い理由は、アルミニウムが表面を酸化させることで、腐食から保護されるからです。アルミニウムは酸素と反応して表面に酸化皮膜を形成し、これが腐食を防ぐバリアとなります。この特性を活かして、アルミニウム製品を長持ちさせるためには、定期的な清掃と保護が重要です。
例えば、外部のアルミサッシやアルミ屋根は、汚れや塩分などが付着することで酸化皮膜が傷つきやすくなります。定期的な洗浄とコーティングによって、酸化皮膜を補修し、長期間美しさを保つことができます。また、塩害の強い海岸部などでは、さらに頻繁なメンテナンスが必要です。
アルミニウム製品の特性を理解し、適切なメンテナンスを行うことで、その耐久性を高め、長く利用することが可能です。
トラブル時の応急処置
[腐食に強い!アルミニウム製品の長持ちさせるコツ]
アルミニウム製品は軽くて耐久性があり、さまざまな場面で活躍します。しかし、腐食に弱いという特性も持っています。腐食を防ぐためには、適切な手入れが欠かせません。まず、アルミニウム製品を使った後は、水で洗ってからよく乾かすことが重要です。特に海水や塩分の多い場所では、こまめな洗浄が必要です。さらに、腐食を防ぐためには、定期的なメンテナンスが欠かせません。専用のクリーナーや保護剤を使って、表面を保護しましょう。これらのコツを守ることで、アルミニウム製品の寿命を延ばし、美しさを保つことができます。しっかりとした手入れをすることで、長く使えるアイテムとして愛用することができます。
専門家に相談すべき状況とは
【腐食に強い!アルミニウム製品の長持ちさせるコツ】
アルミニウム製品は軽くて丈夫であり、さまざまな用途に使われています。しかし、アルミニウムは腐食しやすい素材でもあります。なぜなら、湿気や塩分などにさらされると、表面に酸化皮膜ができ、腐食が進行します。アルミニウム製品を長持ちさせるためには、定期的なメンテナンスが不可欠です。例えば、定期的な洗浄や軽い油膜の塗布が効果的です。さらに、アルミニウム製品を保管する際には、湿気の多い場所や塩分の多い環境を避けることも重要です。これらのコツを実践することで、アルミニウム製品を美しく長持ちさせることができます。
まとめと次のステップ
アルミニウム製品の長持ちさせるためのチェックリスト
アルミニウム製品を長持ちさせるためには、腐食に強い対策が重要です。まず、定期的な清掃が欠かせません。汚れや塩分などが付着すると、腐食が進みやすくなります。次に、保管方法も大切です。湿気や塩分の多い環境では腐食が進行しやすいため、乾燥させたり、適切な保管方法を心がけましょう。さらに、使用後はしっかりと乾かすことも大切です。水分が残ったままになると、腐食を促進する恐れがあります。このように、丁寧な清掃と適切な保管、そして使用後の乾燥がアルミニウム製品の長持ちの秘訣です。腐食に強い対策をしっかりと実践して、製品を大切に保つことが大切です。
継続的な学びと情報収集の重要性
アルミニウム製品を長持ちさせるためには、腐食に注意することが重要です。アルミニウムは軽くて丈夫な素材ですが、腐食に弱い性質も持っています。そのため、定期的な手入れや保管方法を工夫することが必要です。
まず、アルミニウム製品を使用した後は、水で洗い清潔に保ちましょう。特に塩分や化学物質が付着している場合は、しっかりと洗い流すことが重要です。また、乾いた布で拭いてから保管することで、腐食を防ぐことができます。
例えば、アルミニウム製の調理器具や庭具などは、定期的に手入れをしてあげることで長く使うことができます。腐食が進行すると見た目が悪くなるだけでなく、使い勝手も悪くなるため、日常的なメンテナンスを心がけましょう。
アルミニウム製品を大切に扱い、腐食を防ぐことで、長くその美しさや機能を楽しむことができます。是非、これらのコツを実践して、アルミニウム製品を長持ちさせてください。
まとめ
アルミニウム製品の長持ちさせるコツ
アルミニウム製品は腐食に強い特性を持っています。これをさらに長持ちさせるには、定期的な手入れと保管方法に注意することが重要です。アルミニウム表面には酸化被膜が形成されるため、この被膜を傷つけないように清掃することが大切です。また、湿気や塩分の多い環境では腐食が進みやすいため、保管場所を選ぶこともポイントです。アルミニウム製品を長く美しい状態で保つためには、これらのコツを実践してください。