プロが教えるアルミニウム溶接のコツ:成功するためのポイントまとめ
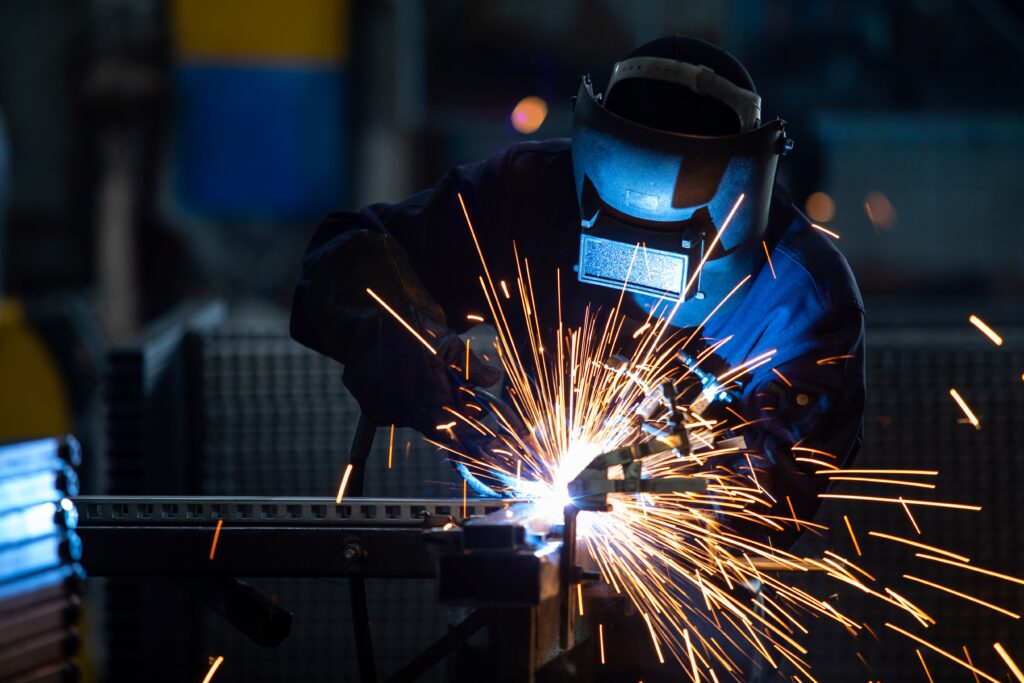
「アルミニウムの溶接を始めたいけれど、正しい方法を知らない…」と悩んでいるあなたへ。アルミニウムは軽量で強度があり、多くの産業で利用されている素材ですが、その特性から溶接が難しいとされています。そこで、今回は「プロが教えるアルミニウム溶接のコツ」をご紹介します。
この記事は、以下のようなお悩みを持つ方にぴったりです。
- アルミニウム溶接の基本が知りたい。
- どんな溶接方法があるのか、選択に迷っている。
- 成功するためのポイントを押さえたい。
アルミニウムの溶接方法には、TIG溶接やMIG溶接など、さまざまな技術が存在します。それぞれの特性や利点、注意点を理解することが、成功への第一歩になります。このガイドでは、初心者からプロを目指す方まで、役立つ情報を幅広くまとめ、ご紹介します。あなたの溶接技術を一段階向上させるための手助けとなることでしょう。
アルミニウムの溶接方法ごとの基本知識
アルミニウムは軽量で耐食性に優れた金属ですが、溶接が難しいことで知られています。そのため、適切な溶接方法を理解し、適用することが重要です。本記事では、アルミニウムの溶接方法の種類や特徴、難しさの要因、対処法について詳しく解説します。
アルミニウムの溶接方法ごとの種類
アルミニウムの溶接にはいくつかの方法があり、それぞれ特徴と適用範囲が異なります。以下の主要な溶接方法を紹介します。
- TIG溶接(Tungsten Inert Gas Welding)
アルミニウムの溶接で最も一般的な方法。アルゴンなどの不活性ガスを使用し、精密な制御が可能で、美しい仕上がりが得られる。 - MIG溶接(Metal Inert Gas Welding)
ワイヤを連続的に供給する半自動溶接方法。作業効率が高く、大量生産向き。 - レーザー溶接
高エネルギーのレーザー光を用いる溶接方法。精密な加工が可能だが、設備コストが高い。 - 抵抗スポット溶接
電流を流して局所的に加熱し、接合する方法。薄板のアルミニウムに適している。
各溶接方法の特徴と利点
溶接方法 | 特徴 | 利点 |
---|---|---|
TIG溶接 | 精密制御が可能 | 仕上がりが美しい |
MIG溶接 | ワイヤ供給で効率的 | 生産性が高い |
レーザー溶接 | 高精度 | 熱影響が少ない |
抵抗スポット溶接 | 電流で接合 | 薄板向け |
アルミニウムの溶接方法ごとの難しさ
アルミニウムの溶接は、鉄やステンレスとは異なる難しさがあります。その理由として、以下の点が挙げられます。
アルミ溶接が難しい理由
- 酸化皮膜の影響
アルミニウム表面には酸化皮膜が形成されやすく、溶接性を低下させる。溶接前に適切な前処理が必要。 - 熱伝導率が高い
鉄の約3倍の熱伝導率があり、急速に熱が拡散するため、溶融池の形成が難しい。 - 溶融金属の流動性
溶融したアルミニウムは粘性が低く、流れやすいため、溶接中にコントロールが難しい。 - ピンホール(気孔)の発生
溶接中に水素が吸収されやすく、気孔ができやすい。
初心者が直面する主な課題
- アークが安定しない
- 溶接中にアルミが溶け落ちる
- ビードの形成が難しい
- 割れやすい
アルミニウムの溶接方法ごとの対処法
アルミニウムの溶接が難しい理由を理解したうえで、適切な対策を講じることで、より良い溶接品質を確保できます。
溶接が上手くいかない場合の具体的な対処法
- 適切な前処理を行う
溶接前に酸化皮膜を除去し、クリーンな表面を確保する。ブラッシングや化学洗浄が有効。 - 適切な溶接機の設定を行う
電流や電圧の設定を適切に調整し、熱影響を最小限に抑える。 - 溶接速度を一定に保つ
アルミニウムは熱伝導率が高いため、適切な速度で均一に溶接することが重要。 - 適切なシールドガスを使用する
アルゴンやヘリウムを使用し、溶融池を安定させる。
よくある失敗とその改善策
- ピンホールが発生する → 溶接環境の湿度を低くし、溶接ワイヤを乾燥させる
- 溶接中に溶融金属が流れる → 適切なフィラー材を選定し、溶接角度を調整する
- ビードが不均一になる → 安定したアークを保ち、一定の速度で作業する
アルミニウムの溶接には特有の難しさがありますが、適切な知識と技術を身につけることで、より高品質な溶接が可能になります。各溶接方法の特性を理解し、適切な手順を踏むことが成功の鍵です。
アルミニウム 溶接方法ごとのスポット溶接
アルミスポット溶接の特徴
アルミニウムのスポット溶接は、自動車や航空機産業などで広く活用されている抵抗溶接の一種です。鉄やステンレスのスポット溶接と比較すると、熱伝導率の高さや酸化皮膜の影響により、適切な溶接条件の設定が難しいとされています。
アルミスポット溶接の主な特徴
- アルミニウムは鉄の約3倍の熱伝導率を持ち、電極から供給される熱が広がりやすいため、適切な電流制御が必要。
- 表面に酸化皮膜(Al₂O₃)が形成されており、これが溶接時の電気抵抗や接合強度に影響を与える。
- 鉄よりも短い時間で強い電流を流す必要があり、溶接条件の管理が重要。
- 電極への付着が発生しやすく、定期的なメンテナンスが必要。
スポット溶接の難しさと克服法
アルミニウムのスポット溶接には、いくつかの課題が存在しますが、適切な手法を用いることで克服可能です。
主な課題とその対策
酸化皮膜による電気抵抗の増加
溶接前にブラシや化学洗浄を用いて酸化皮膜を除去することが重要です。また、亜鉛メッキ電極や特殊コーティング電極を使用すると、酸化皮膜の影響を抑えることができます。
熱伝導率の高さによる溶接部の弱体化
短時間・高電流のパルス溶接を用いることで、必要な熱量を確保しつつ余計な熱拡散を防ぐことができます。さらに、シートの厚みに応じた電流調整を行い、適切な溶融状態を確保することが求められます。
電極の摩耗が早い
定期的な電極メンテナンス(研磨・交換)を実施し、耐久性の高いクロム銅合金などの電極を採用することで、長期間の安定した溶接を可能にします。
アルミニウム 溶接方法ごとの欠陥と改善策
アルミニウムの溶接欠陥の種類
アルミニウムの溶接では、他の金属と比較して特有の欠陥が発生しやすい。以下に代表的な溶接欠陥を挙げる。
代表的なアルミ溶接欠陥
ブローホール(気孔)
溶接時に水分や油分が蒸発し、溶接部に小さな穴ができる現象です。これを防ぐためには、ワークの適切な前処理(脱脂・清掃)を行い、溶接ワイヤの保管環境を最適化することが重要です。
クラック(亀裂)
熱影響による内部応力で割れが発生する現象です。急激な冷却や溶接条件の不適切さが原因となるため、パルス溶接を活用したり、予熱・後熱処理によって応力を緩和することで防ぐことができます。
溶け込み不足
溶接部の接合が不完全で、強度不足の原因となる欠陥です。電流不足や酸化皮膜の影響が主な要因であるため、電流・電圧の適切な設定と酸化皮膜の徹底除去が改善策となります。
欠陥を防ぐためのポイント
アルミニウム溶接における欠陥を防ぐには、以下のポイントを押さえることが重要です。
前処理の徹底
ワークの脱脂・酸化皮膜除去を確実に行い、不純物の影響を排除することが必要です。また、清潔な環境で溶接作業を行い、外部からの汚染を防ぎます。
適切な溶接パラメータの設定
板厚や使用材料に応じた電流・電圧・ワイヤ供給速度を最適化することで、溶接品質を向上させることができます。溶接速度を適切に調整することで、過熱や溶け込み不足を防ぐことも可能です。
溶接後の管理
クラック発生を防ぐために、冷却速度を管理し、必要に応じて応力除去処理を行います。また、溶接部の検査(X線検査、超音波探傷など)を実施し、欠陥を早期に発見することが望ましいです。
アルミニウム溶接は難易度が高いですが、適切な方法と管理によって高品質な溶接が可能となります。適正な前処理、溶接条件の最適化、欠陥対策を組み合わせることで、強度・耐久性のある接合が実現できます。
まとめ
アルミニウム溶接の成功には、適切な機材選び、清潔な作業環境、そして正確な温度管理が不可欠です。溶接前の表面処理や、適切なフィラー材の使用も重要です。さらに、技術の習得には練習が必要で、基本をしっかりと身につけることが成功の鍵となります。