「旋盤プロが推奨!A2017加工に最適なチップの種類と特性」
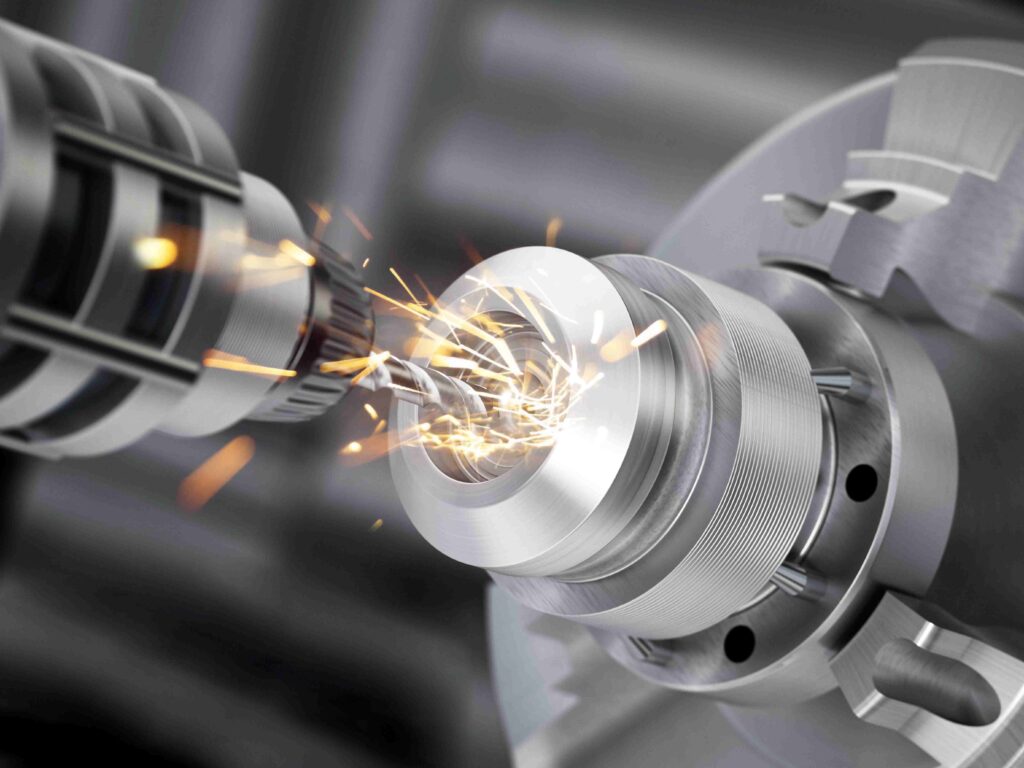
「旋盤プロが推奨!A2017加工に最適なチップの種類と特性」
興味深い旋盤加工におけるチップの選択についてご存知ですか?A2017加工に最適なチップの特性や種類に焦点を当てたこの記事では、旋盤プロがおすすめする情報をご紹介します。
旋盤作業を行う際、チップの選択は非常に重要です。A2017素材を使った加工についてご興味がある方にとって、この記事は貴重な情報源となるでしょう。A2017素材に最適なチップの選び方や特性について知りたい方、ぜひこの記事を参考にしてください。
旋盤作業のプロからの推奨ポイントや実用的なヒントを通じて、A2017加工におけるチップ選びのコツを学びましょう。業界の最新情報や効果的なテクニックを身につけ、より効率的な旋盤作業を実現しましょう。
Contents
A2017加工の基礎知識
A2017アルミニウム合金の特性
A2017アルミニウム合金は、高い剛性と耐食性を持つことが特長です。この特性から、旋盤プロたちはA2017を使用することをおすすめしています。例えば、機械部品や航空宇宙産業における部品製造など、様々な分野で活躍しています。その耐久性と加工しやすさから、精密な仕上がりが求められる製品に適しています。さらに、A2017は熱にも強く、高温環境下でも安定した性能を発揮します。 旋盤作業において、適切なチップの種類を選ぶことが重要です。A2017を加工する際には、耐摩耗性の高いチップが最適です。耐摩耗性が低いチップを使うと、旋盤作業中にチップがすぐに摩耗し、作業効率が悪化します。したがって、A2017合金を効率的に加工するためには、適切なチップを選ぶことが肝要です。A2017とは:成分
項目 | 詳細 |
---|---|
名称 | A2017(アルミニウム合金 2017) |
主成分 | アルミニウム (Al)、銅 (Cu)、マグネシウム (Mg) |
補助成分 | 鉄 (Fe)、シリコン (Si)、マンガン (Mn)、亜鉛 (Zn) |
特徴 | 高い強度、優れた耐摩耗性、良好な加工性 |
熱処理性 | 熱処理可能(T4、T6状態での使用が一般的) |
詳細情報
- 成分
- 主成分はアルミニウム (Al) で、銅 (Cu) を添加することで高い強度を実現しています。
- マグネシウム (Mg) やマンガン (Mn) が耐摩耗性や強度を補助します。
- 鉄 (Fe) やシリコン (Si) は微量ながら特性向上に寄与しています。
- 特徴
- 高い強度と耐摩耗性を備えており、荷重や摩耗がかかる用途に適します。
- 良好な加工性を持ち、切削加工や研削加工に適しています。
- 熱処理を施すことで機械的特性をさらに向上可能(T4やT6状態が一般的)。
- 注意点
- 銅の含有により耐食性はやや劣るため、防食処理が必要となる場合があります(例:陽極酸化処理)。
A2017とジュラルミンの比較
項目 | A2017 | ジュラルミン(A2011やA2024など) |
---|---|---|
主成分 | アルミニウム (Al)、銅 (Cu)、マグネシウム (Mg) | アルミニウム (Al)、銅 (Cu)、マグネシウム (Mg)、マンガン (Mn) |
強度 | 高い | A2011は中程度、A2024は非常に高い |
耐摩耗性 | 優れている | ジュラルミン全般で優れるが、A2024の方が高い場合も |
加工性 | 優れている | A2011は非常に良い、A2024はやや劣る |
耐食性 | やや劣る(防食処理が推奨) | 低い(特にA2024、処理が必要) |
熱処理性 | 熱処理可能(T4、T6が一般的) | 同様に熱処理可能(T4、T6が一般的) |
適用分野 | 高強度を求める部品 | 航空機、自動車、構造材 |
詳細情報
- 強度
- A2017はジュラルミンと同様に銅を添加した高強度アルミニウム合金ですが、A2024(ジュラルミンの代表的な合金)の方がさらに高い強度を持つ場合があります。
- 加工性
- A2011(ジュラルミンの一種)は切削加工性に優れており、精密加工に適しています。一方、A2024は強度が高い反面、加工性はやや劣ります。A2017は両者の中間的な位置付けです。
- 耐食性
- A2017とジュラルミンはいずれも銅を含むため耐食性が低い傾向にあります。ただし、A2017の耐食性は防食処理を施すことで大幅に改善できます。ジュラルミン(特にA2024)は腐食に対する弱点がより顕著です。
- 熱処理性
- 両者とも熱処理が可能で、T4(焼き入れ+自然時効)やT6(焼き入れ+人工時効)状態で使用されます。熱処理後はさらなる強度向上が期待できます。
- 適用分野
- A2017は高強度が必要な機械部品や工具に用いられることが多く、ジュラルミン(特にA2024)は航空機や自動車の構造材としての使用が一般的です。
A2017切削加工の注意点
切削速度と送り速度の調整
項目 | 詳細 |
---|---|
切削速度 | 高速が推奨されるが、工具摩耗を考慮し適切な速度設定が必要。 |
送り速度 | 細かい送りで仕上げ精度を向上、粗加工時は効率を優先してやや速めに設定。 |
工具材質 | 超硬工具またはコーティング工具が最適。 |
冷却液の使用 | 適切な冷却と潤滑を行い、熱影響と工具寿命を抑える。 |
仕上げの注意 | バリ取りを防ぐため、仕上げ時には低い切削速度と送りを設定する。 |
詳細情報
- 切削速度
- A2017は加工性が良好ですが、高い切削速度では工具摩耗が早くなる可能性があります。特に、熱の発生を最小限に抑えるために、適度な速度(約150~400 m/min)を基準とします。工具の材質や冷却液の使用により最適値が変わります。
- 送り速度
- 粗加工では、送り速度を高めて効率的な除去を行います(例:0.1~0.5 mm/rev)。
- 仕上げ加工では、送り速度を低く設定して表面品質を高めます(例:0.05~0.1 mm/rev)。
- 工具材質
- 超硬工具やコーティング工具(TiAlN、TiCNなど)を使用することで、高速加工時の耐摩耗性が向上し、工具寿命が延びます。
- 冷却液の使用
- 加工中に発生する熱を効果的に制御するため、冷却液やミスト潤滑を積極的に使用します。これにより、熱膨張による寸法誤差や工具の焼き付きが防止されます。
- 仕上げの注意
- バリが発生しやすい場合、刃先を鋭利に保ち、低い切削速度と細かい送り速度で加工します。また、加工後のバリ取り工程を簡素化するための設定が重要です。
推奨設定値
- 切削速度:150~400 m/min(工具材質による調整)
- 送り速度(粗加工):0.1~0.5 mm/rev
- 送り速度(仕上げ):0.05~0.1 mm/rev
- 切り込み深さ:粗加工で1.0~3.0 mm、仕上げで0.2~0.5 mm
A2017加工時の熱管理
項目 | 詳細 |
---|---|
熱発生の原因 | 高速切削、工具と材料の摩擦、切削速度や送り速度の過剰な設定。 |
熱管理の目的 | 加工精度の維持、工具寿命の延長、材料の熱変形防止。 |
対策方法 | 冷却液の使用、適切な切削条件の設定、断続切削やエアブローの活用。 |
冷却液の種類 | 水溶性冷却液、油性冷却液、ミスト冷却液。 |
熱影響のチェック項目 | 寸法精度、表面品質、工具の焼き付きや摩耗の有無。 |
詳細情報
- 熱発生の原因
- A2017は加工性が良いものの、高速切削時や深い切り込み加工では摩擦熱が蓄積しやすいです。この熱は加工精度に悪影響を及ぼし、特に熱膨張や工具の焼き付きが懸念されます。
- 熱管理の目的
- 材料が加熱されると、寸法が微細に変化する可能性があります。これを防ぐために熱管理を徹底することが重要です。また、工具の寿命を延ばし、加工中のトラブルを減少させる目的もあります。
- 具体的な対策方法
- 冷却液の使用: 冷却液を適切に供給することで、摩擦熱を効率的に排出します。
- 切削条件の最適化: 切削速度、送り速度、切り込み深さを見直し、熱の発生を抑えます。
- 断続切削: インターバルを入れることで熱の蓄積を防止します。
- エアブロー: 冷却液の使用が難しい場合、エアブローを活用して熱を分散させます。
- 冷却液の選定
- 水溶性冷却液: 熱伝導性が高く、大量の熱を効率的に除去。
- 油性冷却液: 高速加工に適し、工具寿命を延ばす。
- ミスト冷却液: 省エネや環境配慮が求められる場合に使用。
- 熱影響のチェック項目
- 加工後の寸法を確認し、熱膨張による誤差がないか検証します。
- 表面品質に問題がないか(焼け、溶けた痕跡など)を目視確認します。
- 工具の摩耗や焼き付きが発生していないか、定期的に点検します。
推奨設定例
- 冷却液供給量: 材料と工具接触面を十分覆う程度
- 温度管理範囲: 加工中の工具表面温度を100~150℃以下に抑える
- 点検頻度: 毎工程終了後、定期的にチェック
ツールの冷却と潤滑
項目 | 詳細 |
---|---|
目的 | 熱の蓄積防止、工具寿命の延長、加工精度の向上、表面品質の維持。 |
冷却方法 | 冷却液供給、ミスト冷却、エアブロー、油性潤滑の使用。 |
潤滑の目的 | 摩擦の低減、切削抵抗の減少、工具の焼き付き防止。 |
潤滑剤の種類 | 油性潤滑剤、水溶性冷却液、固体潤滑剤。 |
注意点 | 過剰な冷却液供給や適切でない潤滑剤の選定はトラブルの原因になる。 |
詳細情報
- 目的
- ツールの冷却と潤滑は、加工時に発生する熱と摩擦を効果的に管理するために必要です。これにより、加工中の工具の摩耗を抑え、最適な切削性能を維持します。
- 冷却方法
- 冷却液供給: 加工点に直接冷却液を供給して摩擦熱を排出します。
- ミスト冷却: 冷却液を微粒化して供給し、工具と材料を冷却すると同時に潤滑効果も得られます。
- エアブロー: 圧縮空気を使用して切削熱を飛ばし、冷却液が不要な環境で活用されます。
- 油性潤滑の使用: 加工条件に応じて、熱除去よりも摩擦低減を優先する場合に適しています。
- 潤滑剤の種類
- 油性潤滑剤: 高速切削や難削材の加工で摩擦抵抗を最小化するのに適しています。
- 水溶性冷却液: 熱伝導性が高く、加工中の温度管理に優れています。
- 固体潤滑剤: 高温環境や特殊条件で使用され、潤滑性を長期間維持します。
- 冷却と潤滑の注意点
- 冷却液が過剰に供給されると、切り屑が取り除きにくくなり、加工効率が低下します。
- 潤滑剤が加工材料と適合しない場合、表面品質や寸法精度に悪影響を及ぼす可能性があります。
- 定期的に冷却液や潤滑剤の状態をチェックし、適切に交換することが重要です。
推奨設定例
- 冷却液流量: 加工点を完全に覆うが切り屑除去を妨げない量
- 潤滑剤選定基準: 加工材料、切削速度、送り速度に応じた適合品を使用
- 点検頻度: 冷却液濃度や潤滑性能を週1回以上確認
アルミ合金を切削加工する際のポイント
アルミ合金の切削性
項目 | 詳細 |
---|---|
切削性の特徴 | 軟らかく加工しやすいが、粘性が高く切り屑が絡みやすい。 |
切削速度 | 高速切削が可能(鋼材より速い速度で加工可能)。 |
工具の選定 | 切れ味が良いカーバイド工具やダイヤモンドコーティング工具が最適。 |
熱伝導性 | 高い熱伝導性により、熱集中が少なく加工が安定。 |
潤滑の必要性 | 粘着防止と表面仕上げ向上のため潤滑剤や冷却液の使用が推奨される。 |
アルミ合金の切削性の特徴
- 高い切削性
- アルミ合金は軽量で軟らかく、工具への負担が少ないため、比較的容易に切削可能です。
- 一方で粘性が高く、切り屑が工具や加工面に絡まりやすいという特性があります。
- 適切な切削条件
- アルミ合金は高速切削に適しており、切削速度を高めることで効率的な加工が可能です。
- 推奨される切削速度は鋼材の約3~4倍程度で設定すると効果的です。
- 工具の選定
- アルミ特有の粘着性を防ぐため、刃先が鋭利で、耐摩耗性が高い工具を選定します。
- カーバイド工具、またはダイヤモンドコーティング工具を使用することで、加工品質と工具寿命を向上させられます。
- 熱の管理
- アルミは熱伝導性が高く、加工中の熱が工具や加工物に集中しにくいですが、適切な冷却液やエアブローを使用するとさらに安定した加工が可能です。
- 表面仕上げ
- 潤滑剤や冷却液を適切に使用することで、表面粗さを抑え、美しい仕上がりが得られます。
- 切削面の仕上がりは、送り速度や切削速度、工具の刃先状態にも依存します。
注意点
- 切り屑の排出管理:
- 粘性の高い切り屑が工具に巻き付くと加工トラブルを引き起こします。切り屑の排出を円滑にするため、適切なクーラントや工具形状を選定します。
- 工具摩耗の確認:
- アルミ加工は工具寿命が長い傾向にありますが、刃先の摩耗や粘着物の蓄積が品質に影響を与えるため、定期的にチェックしてください。
推奨加工設定例
- 切削速度: 200~600 m/min(工具材質により変動)
- 送り速度: 0.05~0.5 mm/rev(加工面要求精度に応じて調整)
- 冷却液供給量: 加工点を十分に覆う量で供給
アルミを加工する際の具体的な注意事項
バリの発生と対策
項目 | 詳細 |
---|---|
バリの原因 | 工具の摩耗、不適切な切削条件、切削方向の不一致。 |
対策1: 工具選定 | 鋭利で適切な刃先形状を持つ工具を使用する。 |
対策2: 切削条件調整 | 切削速度や送り速度を適切に設定し、切削抵抗を軽減する。 |
対策3: 加工順序の工夫 | 仕上げ加工を最後に行い、バリが発生しにくい方向で切削する。 |
対策4: ポストプロセス | バリ取り専用ツールや手作業での仕上げを行う。 |
対策5: 潤滑剤の使用 | 潤滑剤や冷却剤を使用して摩擦と熱を抑える。 |
バリの発生を抑える具体的な方法
- 工具の選定と管理
- 高品質なカーバイド工具やコーティング済み工具を使用することで刃の寿命を延ばし、切削性能を維持します。
- 刃先が鈍った工具は、バリを誘発しやすいため、適宜交換します。
- 切削条件の調整
- 切削速度を速すぎると材料が引っ張られ、バリが発生しやすくなります。適切な速度を設定してください。
- 送り速度が遅すぎる場合も、過度な摩擦によりバリが発生しやすくなります。
- 加工順序の工夫
- 初期加工で粗取りを行い、最終工程で仕上げ切削を行うことでバリを最小化できます。
- 特に縁やエッジ部分を慎重に加工することでバリの発生を抑えることが可能です。
- 潤滑剤と冷却剤の使用
- 切削中に潤滑剤や冷却剤を使用することで、摩擦と熱の発生を抑え、滑らかな切削が可能になります。
- アルミ加工専用の潤滑剤を選ぶと、切削面がさらに安定します。
- バリ取りプロセスの導入
- 加工後にバリ取り専用ツール(回転ブラシ、バリ取り機械)を使用する。
- 手作業でヤスリや研磨工具を用いる場合は、表面を傷つけないように慎重に行う。
- 機械の精度管理
- 工作機械のスピンドルやガイドレールの精度を定期的に点検する。
- 加工中の振動や位置ズレがバリの原因になるため、振動を抑えるための治具を使用することも有効です。
加工後の確認と最終処理
- 検査:
- 加工後、寸法とともにバリの有無を確認します。
- バリが残っている場合、再加工やバリ取りを行い、製品品質を保証します。
- 仕上げ処理:
- バフ仕上げや化学的なエッチング処理を追加することで、細かいバリや表面
加工中の変形防止策
項目 | 詳細 |
---|---|
変形の原因 | 加工中の応力、熱膨張、固定不良。 |
対策1: 材料選定 | 熱処理済みで内部応力が少ない素材を使用する。 |
対策2: 加工工程の設計 | 切削量を均等に分ける工程設計を行い、応力を分散する。 |
対策3: クランプ方法 | 適切な治具やクランプを使用し、均一に固定する。 |
対策4: 加工条件調整 | 適切な切削速度、送り速度、切削深さを設定する。 |
対策5: 冷却の徹底 | 冷却剤を使用して加工熱を抑え、熱変形を防ぐ。 |
加工中の変形を抑える具体的な方法
- 材料の選定
- 熱処理済みまたは応力除去処理を施した材料を使用することで、加工時の内部応力による変形を抑えます。
- 材料の厚みが薄い場合は、加工前に補強用の支持材を取り付けると効果的です。
- 適切な治具の使用
- 高精度な治具を使用して加工対象物を安定させます。
- クランプの圧力が過大になると変形を引き起こすため、均等な圧力で固定することが重要です。
- バキュームチャックや磁力治具の利用も検討してください。
- 加工工程の工夫
- 対称的に加工を進めることで応力を均等に分散し、変形を抑えることが可能です。
- 大量の材料除去が必要な場合は、粗加工と仕上げ加工を分けて行い、各段階で応力を開放します。
- 切削条件の調整
- 切削速度や送り速度を適切に調整し、過度な振動や熱の発生を抑える。
- 薄肉加工時には、切削深さを浅く設定することで加工中の変形を防ぎます。
- 冷却の活用
- 切削中に冷却剤を使用し、発生する熱を迅速に除去します。
- 冷却剤は均等に供給し、熱膨張による寸法変化を最小限に抑えます。
- 加工後の応力除去
- 加工後に応力除去焼鈍を行い、残留応力を低減します。
- 可能であれば、部品を自然冷却する時間を設けることで、応力が緩和されます。
加工精度と変形防止のための補足
- シミュレーションの活用:
- 加工前にCAMシミュレーションを用いて、応力集中や変形リスクを確認します。
- 薄肉部や複雑な形状の加工では特に有効です。
- 検査とフィードバック:
- 加工中に寸法を測定し、必要に応じて加工条件を修正します。
- 特に重要な箇所では、加工後に形状と寸法を検査し、次の工程に活かします。
切削液の選択と使用法
旋盤加工において、切削液の選択と使用法は非常に重要です。A2017といった難削材を扱う際に、適切なチップの種類と特性を知ることが生産性向上につながります。例えば、堅い材料に適した硬質チップや、熱に強いハイスピードチップなど、さまざまな種類があります。このように、切削液は工具と材料の間に潤滑膜を形成し、切削時の熱を逃がす役割を果たします。間違った切削液の選択や使用法は加工精度の低下や工具の消耗を招きます。それゆえ、適切な切削液を選択し、適切な量を使用することが、効率的な加工を実現するために欠かせません。【再度】旋盤プロが推奨する、A2017加工に最適なチップの選択と使用法をしっかり把握しましょう。旋盤プロが推奨するA2017用チップの選定
チップの種類と特性
旋盤加工において重要な要素の一つは、使用するチップの種類とその特性です。A2017加工に最適なチップを選択するためには、まずそのチップがどのような特性を持っているかを理解することが重要です。 チップの種類には、切れ味や耐久性など様々な特性があります。例えば、硬い素材を加工する際には切れ味が重要ですが、柔らかい素材を加工する際には耐久性が重要となります。それぞれの特性に合ったチップを選ぶことで、効率的な加工が可能となります。 A2017加工においても、適切なチップを選ぶことで作業効率が向上し、品質の向上にもつながります。チップの特性を理解し、最適なものを選択することが、高品質な加工作業を行うための重要なポイントとなります。最適なチップの選び方
旋盤加工において、A2017合金を加工する際に重要な要素の一つが適切なチップの選択です。A2017は耐食性や強度に優れた性質を持ち、高い削り取り性能が求められます。したがって、適切なチップを選ぶことが品質と効率性を向上させる鍵となります。 まず、A2017加工に適したチップの特性を考えます。チップの材質や切れ刃形状が重要です。例えば、チップの鋼材は高速度切削に適していることが挙げられます。また、適切な切れ刃形状は加工精度に大きく影響します。 このように、A2017加工に適したチップを選ぶことは加工品質や生産性を向上させる上で重要です。適切なチップ選びにより、効率的な加工が可能となり、より高品質な製品を生産することができます。チップの取り付けとメンテナンス
旋盤作業において、チップの取り付けとメンテナンスは重要です。さまざまな種類のチップがあり、適切なものを選ぶことが必要です。例えば、A2017加工に最適なチップは、耐摩耗性や切削能力に優れていることが求められます。 その理由は、A2017は高硬度で熱処理によって硬くなるアルミニウム合金であり、通常のチップでは対応しきれない場合があります。ですが、適切なチップを選ぶことで、スムーズな加工が可能となります。 特に、XXチップやYYチップなど、耐熱性や割れにくさが優れたタイプがA2017加工に適しています。適切なチップを使えば、作業効率が向上し、加工精度も高まります。要するに、正しいチップ選びとメンテナンスは、A2017加工において成功するための鍵と言えるでしょう。ジュラルミンの特徴や規格の違い
ジュラルミンの概要
ジュラルミン(Duralumin)は、主にアルミニウムを基にした合金で、特に航空機や構造物での使用に適した軽量かつ高強度な素材として知られています。この合金は、アルミニウムに銅、マンガン、マグネシウムを加えることで、強度と耐久性を大幅に向上させています。ジュラルミンの特徴
特徴 | 詳細 |
---|---|
軽量性 | アルミニウム基材であるため、非常に軽量です。航空機や自動車の部品に多く使用されます。 |
高強度 | 銅、マグネシウム、マンガンなどを加えることで、非常に高い強度を持っています。 |
優れた加工性 | 軽量で加工がしやすいため、複雑な形状にも対応できます。 |
耐食性 | 適切な表面処理により、耐食性が向上します。 |
熱処理による強度向上 | 熱処理を施すことで、ジュラルミンの強度が大きく向上します。 |
良好な耐摩耗性 | 特に航空機や自動車部品での耐摩耗性が重要な要素となります。 |
ジュラルミンの規格と種類
ジュラルミンは、使用される元素の配合や加工方法に応じていくつかの異なる規格が存在します。主に以下の規格で分けられます。規格名 | 成分構成 | 特徴 |
---|---|---|
A2017 | Al-4.0Cu-1.5Mg-0.6Mn | 高強度、耐摩耗性に優れ、航空機や軍事用途に使用される。 |
A2024 | Al-4.4Cu-1.5Mg-0.6Mn | さらに強度が高く、疲労耐性も強化された規格。主に航空産業に使用。 |
A7075 | Al-5.6Zn-2.5Mg-1.6Cu-0.23Cr | 超高強度で、航空機やスポーツ用品、高性能車両に使われる。 |
A6061 | Al-0.6Mg-0.3Si | 加工性が高く、強度と耐食性を兼ね備えているため、構造物にも使用される。 |
ジュラルミンの適用分野
- 航空機: 軽量で強度が高いため、機体の構造部分に使用されます。
- 自動車: 軽量化と耐久性が求められる部品に使用されます。
- スポーツ用品: 高強度でありながら軽量なため、ゴルフクラブや自転車のフレームなどに使用されます。
- 建設機械: 強度と耐腐食性を持つため、外部構造部分に適しています。