A5083用旋盤加工のコツ!最適なチップ選びとは?
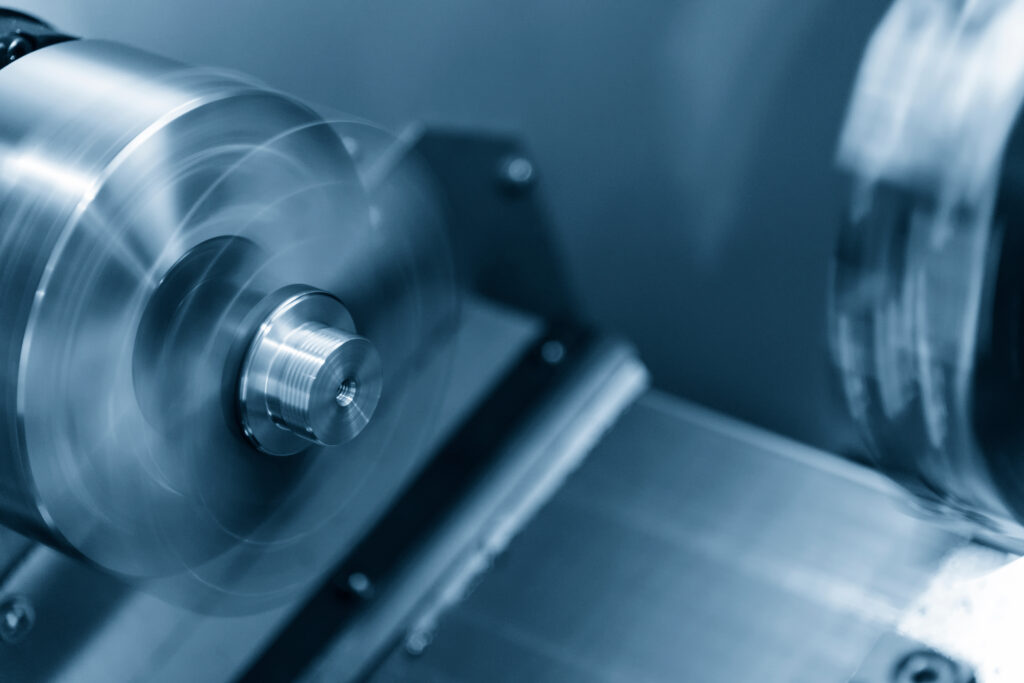
- 加工した製品が設計図面の公差内に収まっているか、測定器具を使用して確認します。
Contents
A5083加工時の注意点
A5083は高強度で耐食性に優れたアルミ合金ですが、加工時に特有の性質を考慮する必要があります。以下に、加工時の注意点をまとめます。加工時の注意点一覧
注意点 | 詳細 |
---|---|
1. 加工硬化への対応 | A5083は加工硬化しやすいため、切削条件を適切に設定し、熱がこもらないようにする必要があります。 |
2. 熱管理 | 切削中に発生する熱を適切に排出するため、冷却液や潤滑剤を十分に使用することが重要です。 |
3. 工具選定 | 耐摩耗性の高い硬質工具や、アルミ用コーティング工具を使用すると加工精度が向上します。 |
4. バリの発生対策 | 切削中にバリが発生しやすいため、工具の刃先を鋭利に保ち、適切な送り速度を設定します。 |
5. 素材の固定 | 剛性が不足すると振動が発生し、加工面に不具合が生じるため、しっかりと固定する必要があります。 |
6. 切削速度と送り速度 | アルミ専用の高回転設定で効率よく加工を行い、送り速度を適切に調整します。 |
7. 表面仕上げ | 良好な仕上げ面を得るために、仕上げ加工では高回転かつ低送りを設定し、仕上げ工具を使用します。 |
詳細情報:加工時の工夫
- 加工硬化対策
- 深切削を避け、複数回に分けて加工を行う。
- 工具を定期的に交換し、鋭利な刃先を維持。
- 冷却と潤滑
- 加工熱が素材に蓄積すると、寸法変化や表面性状に影響が出るため、冷却液を十分に供給する。
- 潤滑剤を使用して摩擦を軽減し、切削性を向上させる。
- バリ対策
- 工具の切れ味を保ち、送り速度を適切に調整することでバリを最小限に抑える。
- バリが発生した場合は、後処理としてデバリング工程を追加。
- 仕上げ精度の向上
- 最終仕上げにはダイヤモンド工具や高品質のエンドミルを使用する。
- 表面に傷がつかないよう、切削後の扱いにも注意。
旋盤チップの役割と種類
A5083用旋盤加工のコツ!最適なチップ選びとは?
旋盤チップは旋盤加工において欠かせない要素です。適切なチップを選ぶことは、作業効率や加工精度に大きな影響を与えます。なぜなら、チップの種類や素材によって、切削力や寿命が異なるからです。 例えば、A5083アルミニウム合金を加工する際には、耐摩耗性や熱伝導性が高いチップが最適です。このように、素材ごとに最適なチップを選ぶことが重要です。 さらに、加工する材料の硬度や形状によってもチップの選択が異なります。そのため、旋盤加工を行う際には、材料や加工条件に合ったチップを選ぶことが成功の鍵となります。適切なチップを選ぶことで、高品質な加工が可能となります。旋盤チップの種類と特徴
旋盤チップは、加工素材や目的に応じて適切な種類を選択することで、加工精度や効率を大幅に向上させることができます。以下は、主な旋盤チップの種類とその特徴をまとめたものです。主な旋盤チップの種類と特徴
種類 | 特徴 | 主な用途 |
---|---|---|
CVDコーティングチップ | 耐摩耗性が高く、高速切削や連続切削に適している。特に鋳鉄や鋼の加工で効果を発揮。 | 鋳鉄、鋼、耐熱合金の加工 |
PVDコーティングチップ | 硬度が高く、切れ味に優れる。仕上げ加工や複雑な形状の加工に適している。 | ステンレス鋼、非鉄金属の加工 |
超硬チップ | 高い硬度と耐摩耗性を持ち、幅広い材料に対応可能。高速切削や荒加工に最適。 | 鋼、ステンレス鋼、非鉄金属の荒加工 |
セラミックチップ | 高温下でも硬度を保持し、熱変形が少ない。仕上げ加工や耐熱材料の加工に向いている。 | 高硬度鋼、耐熱合金、鋳鉄の仕上げ加工 |
CBN(立方晶窒化ホウ素)チップ | 超硬合金よりも高い硬度を持ち、非常に硬い材料の加工に適している。高速切削にも対応。 | 焼入れ鋼、鋳鉄、粉末冶金材の加工 |
ダイヤモンドチップ | 最も硬い素材で、非常に高い耐摩耗性を持つ。非鉄金属やプラスチックの高精度仕上げに適している。 | アルミニウム、銅、プラスチック、炭素繊維の加工 |
詳細情報:各チップの利点と注意点
- CVDコーティングチップ
- 利点: 高い耐摩耗性により長寿命。
- 注意点: 衝撃に弱く、断続切削には不向き。
- PVDコーティングチップ
- 利点: 高い切れ味と幅広い素材対応。
- 注意点: 高速加工時にコーティングが剥がれやすい場合がある。
- 超硬チップ
- 利点: 汎用性が高く、加工条件の幅が広い。
- 注意点: 極端な高温環境では耐久性が低下する。
- セラミックチップ
- 利点: 耐熱性と耐摩耗性が高い。
- 注意点: 衝撃に非常に弱い。
- CBNチップ
- 利点: 焼入れ鋼など硬い材料に最適。
- 注意点: 非鉄金属や軟質材料の加工には適さない。
- ダイヤモンドチップ
- 利点: 非鉄金属や高精度仕上げに最適。
- 注意点: 高温環境や鉄系材料には使用できない。
チップの材質と用途
チップの材料は、旋盤加工において非常に重要です。適切なチップを選ぶことは、作業効率や加工精度に大きな影響を与えます。例えば、A5083というアルミニウム合金を旋盤加工する際には、適切なチップを選ぶことが重要です。 A5083は耐食性や溶接性に優れた素材であり、耐久性も要求されるため、チップの選択は慎重に行わなければなりません。適切な材料やコーティングを持つチップを使用することで、作業中の摩耗や熱への耐性を高めることができます。 つまり、A5083用旋盤加工においては、チップの材料やコーティングを適切に選ぶことがポイントです。正しいチップを選択することで、効率的かつ精密な加工が可能となります。加工の達人に聞いた!A5083旋盤加工のコツ
切削条件の最適化
A5083は高強度のアルミ合金で、耐食性と加工性が良いことから広く使用されていますが、旋盤加工時には特有の注意点があります。以下は、切削条件を最適化するためのポイントをまとめた内容です。切削条件 | 最適化のポイント | 理由 |
---|---|---|
切削速度 | 高速(200~500 m/min)で設定 | アルミは熱伝導性が高いため、高速切削でも熱が集中しにくい。切削面が滑らかになる。 |
送り速度 | 中速(0.1~0.3 mm/rev)を推奨 | 適切な送り速度を維持することで、切削熱を抑え、バリや加工変形を防ぐ。 |
切込み深さ | 小切込み(1~3 mm)から開始し、材料や目的に応じて調整 | 切削抵抗を抑え、仕上げ面の品質を向上させる。過剰な切込みは工具寿命を短くするリスクがある。 |
工具 | 超硬チップまたはPVDコーティングチップを使用 | アルミ特有の粘りや切りくずの付着を防ぎ、高精度な加工を実現する。 |
冷却と潤滑 | 水溶性クーラントを十分に供給 | 切削熱を抑え、工具寿命を延ばすだけでなく、表面仕上げを向上させる効果がある。 |
詳細情報:切削条件最適化の重要なポイント
- 切削速度の設定
- 高速切削が可能なアルミですが、工具の摩耗に注意。
- 工具寿命を延ばすため、加工中に速度調整を行うことが重要。
- 送り速度の調整
- 過度に速い送り速度は表面粗さを悪化させ、遅すぎると熱が集中する可能性がある。
- 切込み深さの選定
- 荒加工では切込みを深く、仕上げ加工では浅くすることで効率と精度を両立。
- 工具の選定
- 特にアルミ用の切削チップを選ぶことで、切りくずの排出性と加工面の美しさが向上。
- 冷却と潤滑の使用
- 冷却液を適切に供給することで、加工中の熱による変形や工具の過剰摩耗を防止。
チップの交換タイミング
チップの交換タイミングは、加工品質や効率に直結する重要なポイントです。チップが摩耗しすぎると精度が落ち、作業時間もかかってしまいます。逆に早すぎる交換も無駄なコストに繋がります。最適なタイミングは、チップの摩耗具合や加工条件によって異なります。加工中にチップの切れ味や状態を常にチェックし、摩耗が進んでいるようなら適切なタイミングで交換しましょう。例えば、A5083用旋盤での加工中に、チップの切れ味が鈍くなってきたら、すみやかに交換することが重要です。適切なチップ選びと交換タイミングを把握することで、効率的な加工が可能となります。長時間加工のための工夫
A5083用旋盤加工をする際、長時間加工するための工夫が重要です。最適なチップ選びが成功の鍵です。なぜなら、適切なチップを選ぶことで切削効率が向上し、作業効率が上がるからです。 理由は、A5083のようなアルミニウム合金は加工が難しい素材であり、適切な切削条件が必要です。例えば、チップの種類や形状、切削速度や切り込み量などが重要な要素となります。よく考えられた切削条件で作業を行うことで、加工精度が向上し、加工時間を短縮できます。 したがって、A5083用旋盤加工を行う際は、適切なチップを選んで切削条件を調整することが重要です。これによって効率的な加工が可能となります。旋盤加工トラブルシューティング
よくある加工トラブルとその対処法
旋盤加工では、作業効率や製品精度を低下させるさまざまなトラブルが発生する可能性があります。以下は、一般的なトラブルとその原因、対処法をまとめた表です。トラブル | 原因 | 対処法 |
---|---|---|
工具摩耗の増加 | – 不適切な切削速度や送り速度 | – 切削条件を見直し、適切な速度と送りに設定 |
– 冷却液や潤滑剤の不足 | – 十分な量の冷却液を供給 | |
– 工具材質が被加工材に適していない | – 対応する工具(超硬合金やコーティングチップ)に交換 | |
加工面の粗さが悪い | – 切削速度や送り速度が不適切 | – 送りを遅くし、切削速度を適切に調整 |
– 工具が摩耗している | – 工具を交換または再研磨 | |
– 被加工材の振動 | – 加工物をしっかりと固定し、振動を抑える | |
バリの発生が多い | – 過剰な切削速度や切込み深さ | – 切込みを適切に調整し、送り速度を安定させる |
– 工具の形状や切れ味の不良 | – 鋭利な工具に交換 | |
寸法精度のばらつき | – 被加工材の熱膨張 | – 冷却液を適切に使用し、加工中の温度上昇を抑える |
– 主軸のぶれまたは機械のガタつき | – 主軸と工具の調整を確認し、必要であれば修理 | |
切りくずの排出不良 | – 切削条件が適切でない | – 切削速度や送りを調整し、切りくずが詰まりにくい条件に設定 |
– 工具形状が被加工材に適合していない | – 溝や排出性に優れた工具を使用 |
詳細情報:主なトラブルへの対応のポイント
- 工具摩耗の抑制
- 冷却液の使用と切削速度の適切な設定が摩耗防止の鍵です。
- 特に硬い材料を加工する場合は、工具の材質選定を慎重に行います。
- 加工面粗さの改善
- 工具の取り付け精度や工具の状態を確認し、振動を最小限に抑える工夫が必要です。
- バリ対策
- 仕上げ加工用の切削条件を設定し、工具の刃先形状を適切に選びます。
- 加工後の仕上げ処理としてエッジ研磨を検討します。
- 寸法精度の向上
- 定期的な機械の点検を行い、振動やガタつきを防ぎます。
- 加工中の温度変化を抑え、環境管理を徹底します。
- 切りくず管理
- 切りくずの巻き付きを防止する工具形状を採用し、加工中の排出がスムーズになるよう設計します。
- 切削油を適切に使い、切りくずの滑りを良くする工夫をします。
A5083加工時の特有の問題点
アルミ合金A5083は高い強度と耐腐食性を持つ一方で、加工時には特有の問題が発生することがあります。以下は主な問題点とその原因、対策を表にまとめたものです。問題点 | 主な原因 | 対策 |
---|---|---|
切削面の粗さが悪い | – 材料の柔らかさと粘性 | – 高速切削に適した工具を使用 |
– 工具の摩耗または不適切な工具形状 | – 超硬工具やコーティング工具を選定し、摩耗時には交換 | |
バリの発生 | – 材料の柔らかさによる切りくずの巻き付き | – 鋭利な刃先の工具を使用し、切削速度を最適化 |
– 工具の取り付け角度が不適切 | – 適切な取り付け角度(正面切削の場合5°~15°程度)を設定 | |
加工中の変形 | – 高温による材料の熱膨張 | – 切削条件を調整し、冷却液を適切に使用 |
– 加工物の固定が不十分 | – しっかりとした治具を使用し、振動を抑制 | |
切りくずの排出不良 | – 切削条件が適切でない | – 切りくず排出性の高い工具を選定 |
– 切削油の供給不足 | – 冷却・潤滑性の高い切削油を十分に供給 | |
寸法精度のばらつき | – 温度変化による膨張 | – 加工環境を管理し、温度変化を最小限に抑える |
– 機械のガタつきや工具の振動 | – 定期的な機械点検と調整を実施 |
詳細情報:主な問題への対応のポイント
- 切削面の粗さ改善
- A5083の粘性に適応した高回転速度の工具を使用します。
- 摩耗した工具は早めに交換し、常に鋭利な状態を保つことが重要です。
- バリ対策
- 工具刃先の角度を適切に設定し、加工速度と送りを最適化します。
- 仕上げ加工の際に低速で丁寧に作業を行い、バリの発生を抑えます。
- 変形防止策
- 加工中の温度管理が重要で、冷却液の使用量を増やし、熱膨張を抑えます。
- 強固な固定治具を用いて、振動や変形のリスクを軽減します。
- 切りくず管理
- 切りくずの形状が加工に影響を与えやすいため、排出性の高い工具形状を選択します。
- 定期的な切削油の補充と供給状態の確認を行います。
- 寸法精度の確保
- 精密加工には、機械と工具の状態を頻繁にチェックし、微調整を実施します。
- 環境温度が安定した作業空間を確保することで、熱膨張の影響を最小限に抑えます。
トラブルを避けるためのチェックリスト
A5083の加工時にトラブルを避けるため、以下の項目を確認してください。加工開始前、加工中、加工後に分けて管理することで、効率的かつ安定した加工が可能になります。加工開始前のチェックリスト
項目 | チェック内容 | 状態 |
---|---|---|
工具の状態確認 | 工具が摩耗していないか、刃先が鋭利かを確認 | ☐ |
機械の設定確認 | 回転速度、送り速度、切削深さが適切かを確認 | ☐ |
材料の固定 | 加工物がしっかり固定され、振動しない状態になっているか | ☐ |
切削油の準備 | 適切な切削油が十分に供給される準備ができているか | ☐ |
加工プログラム確認 | 加工データが正確に入力され、編集ミスがないか確認 | ☐ |
加工中のチェックリスト
項目 | チェック内容 | 状態 |
---|---|---|
切削音の確認 | 異常な切削音や振動が発生していないか | ☐ |
切りくずの排出 | 切りくずがスムーズに排出されているか | ☐ |
工具温度の確認 | 工具が過熱していないか、冷却が十分かを確認 | ☐ |
寸法精度の中間確認 | 加工途中で寸法精度が確保されているかを確認 | ☐ |
加工後のチェックリスト
項目 | チェック内容 | 状態 |
---|---|---|
加工表面の仕上がり | 表面が滑らかでバリがないか確認 | ☐ |
寸法精度の最終確認 | 図面通りの寸法になっているか測定 | ☐ |
工具の状態 | 工具が摩耗していないか、次回使用可能な状態か確認 | ☐ |
機械のメンテナンス | 機械内部に切りくずが残っていないか清掃 | ☐ |
詳細情報:チェックリスト活用のポイント
- 一貫性を保つ
- 毎回の加工で同じ手順を繰り返し、トラブルの発生を抑制します。
- 記録の保持
- チェックリストに問題点や気付きを記録し、次回の作業に反映させます。
- 工具と機械の保守
- 定期的な工具交換と機械のメンテナンスを徹底します。
まとめとしてのチェックポイント
A5083加工における安定性と効率を確保するための重要なチェックポイントを以下にまとめました。チェックポイント一覧
- 工具の適正使用
- 摩耗した工具を使用しない。加工材に適した刃物を選定する。
- 加工条件の最適化
- 切削速度、送り速度、切削深さを材料特性に応じて設定する。
- 切削油の使用
- 適切な冷却と潤滑を確保し、工具寿命を延ばす。
- 材料の固定
- 加工物がしっかり固定され、振動や位置ずれを防ぐ。
- 寸法精度の中間確認
- 作業途中で寸法測定を行い、加工精度を維持する。
- 切りくず処理
- 切りくずが詰まらないように、定期的に除去する。
- 工具の温度管理
- 工具が過熱しないように冷却システムを活用する。
- 加工後の仕上げ確認
- バリや表面仕上げをチェックし、必要に応じて仕上げ工程を追加する。
- 定期的な機械メンテナンス
- 機械の清掃、点検を行い、長期的な安定稼働を実現する。
実行のポイント
- チェックリストを活用し、加工プロセスを標準化する。
- 定期的な記録と振り返りを行い、トラブルの原因を分析する。
- 加工環境全体を整えることで、安全かつ高精度な作業を確保する。
- 加工した製品が設計図面の公差内に収まっているか、測定器具を使用して確認します。
A5083加工時の注意点
A5083は高強度で耐食性に優れたアルミ合金ですが、加工時に特有の性質を考慮する必要があります。以下に、加工時の注意点をまとめます。加工時の注意点一覧
注意点 | 詳細 |
---|---|
1. 加工硬化への対応 | A5083は加工硬化しやすいため、切削条件を適切に設定し、熱がこもらないようにする必要があります。 |
2. 熱管理 | 切削中に発生する熱を適切に排出するため、冷却液や潤滑剤を十分に使用することが重要です。 |
3. 工具選定 | 耐摩耗性の高い硬質工具や、アルミ用コーティング工具を使用すると加工精度が向上します。 |
4. バリの発生対策 | 切削中にバリが発生しやすいため、工具の刃先を鋭利に保ち、適切な送り速度を設定します。 |
5. 素材の固定 | 剛性が不足すると振動が発生し、加工面に不具合が生じるため、しっかりと固定する必要があります。 |
6. 切削速度と送り速度 | アルミ専用の高回転設定で効率よく加工を行い、送り速度を適切に調整します。 |
7. 表面仕上げ | 良好な仕上げ面を得るために、仕上げ加工では高回転かつ低送りを設定し、仕上げ工具を使用します。 |
詳細情報:加工時の工夫
- 加工硬化対策
- 深切削を避け、複数回に分けて加工を行う。
- 工具を定期的に交換し、鋭利な刃先を維持。
- 冷却と潤滑
- 加工熱が素材に蓄積すると、寸法変化や表面性状に影響が出るため、冷却液を十分に供給する。
- 潤滑剤を使用して摩擦を軽減し、切削性を向上させる。
- バリ対策
- 工具の切れ味を保ち、送り速度を適切に調整することでバリを最小限に抑える。
- バリが発生した場合は、後処理としてデバリング工程を追加。
- 仕上げ精度の向上
- 最終仕上げにはダイヤモンド工具や高品質のエンドミルを使用する。
- 表面に傷がつかないよう、切削後の扱いにも注意。
旋盤チップの役割と種類
A5083用旋盤加工のコツ!最適なチップ選びとは?
旋盤チップは旋盤加工において欠かせない要素です。適切なチップを選ぶことは、作業効率や加工精度に大きな影響を与えます。なぜなら、チップの種類や素材によって、切削力や寿命が異なるからです。 例えば、A5083アルミニウム合金を加工する際には、耐摩耗性や熱伝導性が高いチップが最適です。このように、素材ごとに最適なチップを選ぶことが重要です。 さらに、加工する材料の硬度や形状によってもチップの選択が異なります。そのため、旋盤加工を行う際には、材料や加工条件に合ったチップを選ぶことが成功の鍵となります。適切なチップを選ぶことで、高品質な加工が可能となります。旋盤チップの種類と特徴
旋盤チップは、加工素材や目的に応じて適切な種類を選択することで、加工精度や効率を大幅に向上させることができます。以下は、主な旋盤チップの種類とその特徴をまとめたものです。主な旋盤チップの種類と特徴
種類 | 特徴 | 主な用途 |
---|---|---|
CVDコーティングチップ | 耐摩耗性が高く、高速切削や連続切削に適している。特に鋳鉄や鋼の加工で効果を発揮。 | 鋳鉄、鋼、耐熱合金の加工 |
PVDコーティングチップ | 硬度が高く、切れ味に優れる。仕上げ加工や複雑な形状の加工に適している。 | ステンレス鋼、非鉄金属の加工 |
超硬チップ | 高い硬度と耐摩耗性を持ち、幅広い材料に対応可能。高速切削や荒加工に最適。 | 鋼、ステンレス鋼、非鉄金属の荒加工 |
セラミックチップ | 高温下でも硬度を保持し、熱変形が少ない。仕上げ加工や耐熱材料の加工に向いている。 | 高硬度鋼、耐熱合金、鋳鉄の仕上げ加工 |
CBN(立方晶窒化ホウ素)チップ | 超硬合金よりも高い硬度を持ち、非常に硬い材料の加工に適している。高速切削にも対応。 | 焼入れ鋼、鋳鉄、粉末冶金材の加工 |
ダイヤモンドチップ | 最も硬い素材で、非常に高い耐摩耗性を持つ。非鉄金属やプラスチックの高精度仕上げに適している。 | アルミニウム、銅、プラスチック、炭素繊維の加工 |
詳細情報:各チップの利点と注意点
- CVDコーティングチップ
- 利点: 高い耐摩耗性により長寿命。
- 注意点: 衝撃に弱く、断続切削には不向き。
- PVDコーティングチップ
- 利点: 高い切れ味と幅広い素材対応。
- 注意点: 高速加工時にコーティングが剥がれやすい場合がある。
- 超硬チップ
- 利点: 汎用性が高く、加工条件の幅が広い。
- 注意点: 極端な高温環境では耐久性が低下する。
- セラミックチップ
- 利点: 耐熱性と耐摩耗性が高い。
- 注意点: 衝撃に非常に弱い。
- CBNチップ
- 利点: 焼入れ鋼など硬い材料に最適。
- 注意点: 非鉄金属や軟質材料の加工には適さない。
- ダイヤモンドチップ
- 利点: 非鉄金属や高精度仕上げに最適。
- 注意点: 高温環境や鉄系材料には使用できない。
チップの材質と用途
チップの材料は、旋盤加工において非常に重要です。適切なチップを選ぶことは、作業効率や加工精度に大きな影響を与えます。例えば、A5083というアルミニウム合金を旋盤加工する際には、適切なチップを選ぶことが重要です。 A5083は耐食性や溶接性に優れた素材であり、耐久性も要求されるため、チップの選択は慎重に行わなければなりません。適切な材料やコーティングを持つチップを使用することで、作業中の摩耗や熱への耐性を高めることができます。 つまり、A5083用旋盤加工においては、チップの材料やコーティングを適切に選ぶことがポイントです。正しいチップを選択することで、効率的かつ精密な加工が可能となります。加工の達人に聞いた!A5083旋盤加工のコツ
切削条件の最適化
A5083は高強度のアルミ合金で、耐食性と加工性が良いことから広く使用されていますが、旋盤加工時には特有の注意点があります。以下は、切削条件を最適化するためのポイントをまとめた内容です。切削条件 | 最適化のポイント | 理由 |
---|---|---|
切削速度 | 高速(200~500 m/min)で設定 | アルミは熱伝導性が高いため、高速切削でも熱が集中しにくい。切削面が滑らかになる。 |
送り速度 | 中速(0.1~0.3 mm/rev)を推奨 | 適切な送り速度を維持することで、切削熱を抑え、バリや加工変形を防ぐ。 |
切込み深さ | 小切込み(1~3 mm)から開始し、材料や目的に応じて調整 | 切削抵抗を抑え、仕上げ面の品質を向上させる。過剰な切込みは工具寿命を短くするリスクがある。 |
工具 | 超硬チップまたはPVDコーティングチップを使用 | アルミ特有の粘りや切りくずの付着を防ぎ、高精度な加工を実現する。 |
冷却と潤滑 | 水溶性クーラントを十分に供給 | 切削熱を抑え、工具寿命を延ばすだけでなく、表面仕上げを向上させる効果がある。 |
詳細情報:切削条件最適化の重要なポイント
- 切削速度の設定
- 高速切削が可能なアルミですが、工具の摩耗に注意。
- 工具寿命を延ばすため、加工中に速度調整を行うことが重要。
- 送り速度の調整
- 過度に速い送り速度は表面粗さを悪化させ、遅すぎると熱が集中する可能性がある。
- 切込み深さの選定
- 荒加工では切込みを深く、仕上げ加工では浅くすることで効率と精度を両立。
- 工具の選定
- 特にアルミ用の切削チップを選ぶことで、切りくずの排出性と加工面の美しさが向上。
- 冷却と潤滑の使用
- 冷却液を適切に供給することで、加工中の熱による変形や工具の過剰摩耗を防止。
チップの交換タイミング
チップの交換タイミングは、加工品質や効率に直結する重要なポイントです。チップが摩耗しすぎると精度が落ち、作業時間もかかってしまいます。逆に早すぎる交換も無駄なコストに繋がります。最適なタイミングは、チップの摩耗具合や加工条件によって異なります。加工中にチップの切れ味や状態を常にチェックし、摩耗が進んでいるようなら適切なタイミングで交換しましょう。例えば、A5083用旋盤での加工中に、チップの切れ味が鈍くなってきたら、すみやかに交換することが重要です。適切なチップ選びと交換タイミングを把握することで、効率的な加工が可能となります。長時間加工のための工夫
A5083用旋盤加工をする際、長時間加工するための工夫が重要です。最適なチップ選びが成功の鍵です。なぜなら、適切なチップを選ぶことで切削効率が向上し、作業効率が上がるからです。 理由は、A5083のようなアルミニウム合金は加工が難しい素材であり、適切な切削条件が必要です。例えば、チップの種類や形状、切削速度や切り込み量などが重要な要素となります。よく考えられた切削条件で作業を行うことで、加工精度が向上し、加工時間を短縮できます。 したがって、A5083用旋盤加工を行う際は、適切なチップを選んで切削条件を調整することが重要です。これによって効率的な加工が可能となります。旋盤加工トラブルシューティング
よくある加工トラブルとその対処法
旋盤加工では、作業効率や製品精度を低下させるさまざまなトラブルが発生する可能性があります。以下は、一般的なトラブルとその原因、対処法をまとめた表です。トラブル | 原因 | 対処法 |
---|---|---|
工具摩耗の増加 | – 不適切な切削速度や送り速度 | – 切削条件を見直し、適切な速度と送りに設定 |
– 冷却液や潤滑剤の不足 | – 十分な量の冷却液を供給 | |
– 工具材質が被加工材に適していない | – 対応する工具(超硬合金やコーティングチップ)に交換 | |
加工面の粗さが悪い | – 切削速度や送り速度が不適切 | – 送りを遅くし、切削速度を適切に調整 |
– 工具が摩耗している | – 工具を交換または再研磨 | |
– 被加工材の振動 | – 加工物をしっかりと固定し、振動を抑える | |
バリの発生が多い | – 過剰な切削速度や切込み深さ | – 切込みを適切に調整し、送り速度を安定させる |
– 工具の形状や切れ味の不良 | – 鋭利な工具に交換 | |
寸法精度のばらつき | – 被加工材の熱膨張 | – 冷却液を適切に使用し、加工中の温度上昇を抑える |
– 主軸のぶれまたは機械のガタつき | – 主軸と工具の調整を確認し、必要であれば修理 | |
切りくずの排出不良 | – 切削条件が適切でない | – 切削速度や送りを調整し、切りくずが詰まりにくい条件に設定 |
– 工具形状が被加工材に適合していない | – 溝や排出性に優れた工具を使用 |
詳細情報:主なトラブルへの対応のポイント
- 工具摩耗の抑制
- 冷却液の使用と切削速度の適切な設定が摩耗防止の鍵です。
- 特に硬い材料を加工する場合は、工具の材質選定を慎重に行います。
- 加工面粗さの改善
- 工具の取り付け精度や工具の状態を確認し、振動を最小限に抑える工夫が必要です。
- バリ対策
- 仕上げ加工用の切削条件を設定し、工具の刃先形状を適切に選びます。
- 加工後の仕上げ処理としてエッジ研磨を検討します。
- 寸法精度の向上
- 定期的な機械の点検を行い、振動やガタつきを防ぎます。
- 加工中の温度変化を抑え、環境管理を徹底します。
- 切りくず管理
- 切りくずの巻き付きを防止する工具形状を採用し、加工中の排出がスムーズになるよう設計します。
- 切削油を適切に使い、切りくずの滑りを良くする工夫をします。
A5083加工時の特有の問題点
アルミ合金A5083は高い強度と耐腐食性を持つ一方で、加工時には特有の問題が発生することがあります。以下は主な問題点とその原因、対策を表にまとめたものです。問題点 | 主な原因 | 対策 |
---|---|---|
切削面の粗さが悪い | – 材料の柔らかさと粘性 | – 高速切削に適した工具を使用 |
– 工具の摩耗または不適切な工具形状 | – 超硬工具やコーティング工具を選定し、摩耗時には交換 | |
バリの発生 | – 材料の柔らかさによる切りくずの巻き付き | – 鋭利な刃先の工具を使用し、切削速度を最適化 |
– 工具の取り付け角度が不適切 | – 適切な取り付け角度(正面切削の場合5°~15°程度)を設定 | |
加工中の変形 | – 高温による材料の熱膨張 | – 切削条件を調整し、冷却液を適切に使用 |
– 加工物の固定が不十分 | – しっかりとした治具を使用し、振動を抑制 | |
切りくずの排出不良 | – 切削条件が適切でない | – 切りくず排出性の高い工具を選定 |
– 切削油の供給不足 | – 冷却・潤滑性の高い切削油を十分に供給 | |
寸法精度のばらつき | – 温度変化による膨張 | – 加工環境を管理し、温度変化を最小限に抑える |
– 機械のガタつきや工具の振動 | – 定期的な機械点検と調整を実施 |
詳細情報:主な問題への対応のポイント
- 切削面の粗さ改善
- A5083の粘性に適応した高回転速度の工具を使用します。
- 摩耗した工具は早めに交換し、常に鋭利な状態を保つことが重要です。
- バリ対策
- 工具刃先の角度を適切に設定し、加工速度と送りを最適化します。
- 仕上げ加工の際に低速で丁寧に作業を行い、バリの発生を抑えます。
- 変形防止策
- 加工中の温度管理が重要で、冷却液の使用量を増やし、熱膨張を抑えます。
- 強固な固定治具を用いて、振動や変形のリスクを軽減します。
- 切りくず管理
- 切りくずの形状が加工に影響を与えやすいため、排出性の高い工具形状を選択します。
- 定期的な切削油の補充と供給状態の確認を行います。
- 寸法精度の確保
- 精密加工には、機械と工具の状態を頻繁にチェックし、微調整を実施します。
- 環境温度が安定した作業空間を確保することで、熱膨張の影響を最小限に抑えます。
トラブルを避けるためのチェックリスト
A5083の加工時にトラブルを避けるため、以下の項目を確認してください。加工開始前、加工中、加工後に分けて管理することで、効率的かつ安定した加工が可能になります。加工開始前のチェックリスト
項目 | チェック内容 | 状態 |
---|---|---|
工具の状態確認 | 工具が摩耗していないか、刃先が鋭利かを確認 | ☐ |
機械の設定確認 | 回転速度、送り速度、切削深さが適切かを確認 | ☐ |
材料の固定 | 加工物がしっかり固定され、振動しない状態になっているか | ☐ |
切削油の準備 | 適切な切削油が十分に供給される準備ができているか | ☐ |
加工プログラム確認 | 加工データが正確に入力され、編集ミスがないか確認 | ☐ |
加工中のチェックリスト
項目 | チェック内容 | 状態 |
---|---|---|
切削音の確認 | 異常な切削音や振動が発生していないか | ☐ |
切りくずの排出 | 切りくずがスムーズに排出されているか | ☐ |
工具温度の確認 | 工具が過熱していないか、冷却が十分かを確認 | ☐ |
寸法精度の中間確認 | 加工途中で寸法精度が確保されているかを確認 | ☐ |
加工後のチェックリスト
項目 | チェック内容 | 状態 |
---|---|---|
加工表面の仕上がり | 表面が滑らかでバリがないか確認 | ☐ |
寸法精度の最終確認 | 図面通りの寸法になっているか測定 | ☐ |
工具の状態 | 工具が摩耗していないか、次回使用可能な状態か確認 | ☐ |
機械のメンテナンス | 機械内部に切りくずが残っていないか清掃 | ☐ |
詳細情報:チェックリスト活用のポイント
- 一貫性を保つ
- 毎回の加工で同じ手順を繰り返し、トラブルの発生を抑制します。
- 記録の保持
- チェックリストに問題点や気付きを記録し、次回の作業に反映させます。
- 工具と機械の保守
- 定期的な工具交換と機械のメンテナンスを徹底します。
まとめとしてのチェックポイント
A5083加工における安定性と効率を確保するための重要なチェックポイントを以下にまとめました。チェックポイント一覧
- 工具の適正使用
- 摩耗した工具を使用しない。加工材に適した刃物を選定する。
- 加工条件の最適化
- 切削速度、送り速度、切削深さを材料特性に応じて設定する。
- 切削油の使用
- 適切な冷却と潤滑を確保し、工具寿命を延ばす。
- 材料の固定
- 加工物がしっかり固定され、振動や位置ずれを防ぐ。
- 寸法精度の中間確認
- 作業途中で寸法測定を行い、加工精度を維持する。
- 切りくず処理
- 切りくずが詰まらないように、定期的に除去する。
- 工具の温度管理
- 工具が過熱しないように冷却システムを活用する。
- 加工後の仕上げ確認
- バリや表面仕上げをチェックし、必要に応じて仕上げ工程を追加する。
- 定期的な機械メンテナンス
- 機械の清掃、点検を行い、長期的な安定稼働を実現する。
実行のポイント
- チェックリストを活用し、加工プロセスを標準化する。
- 定期的な記録と振り返りを行い、トラブルの原因を分析する。
- 加工環境全体を整えることで、安全かつ高精度な作業を確保する。
- 素材の固定
- 素材がしっかりと固定されていないと加工精度が低下し、安全性が損なわれる可能性があります。
- チャックの締め付けや芯出しの精度を確認することが重要です。
- 切削条件の選定
- 回転速度や切削深さが適切でないと、加工面にバリや歪みが生じることがあります。
- 素材や工具に適した条件を選ぶ必要があります。
- 工具の選定と管理
- 工具の摩耗や刃の欠けは加工面に影響するため、定期的に工具を点検・交換します。
- 加工後の検査
- 加工した製品が設計図面の公差内に収まっているか、測定器具を使用して確認します。
A5083加工時の注意点
A5083は高強度で耐食性に優れたアルミ合金ですが、加工時に特有の性質を考慮する必要があります。以下に、加工時の注意点をまとめます。加工時の注意点一覧
注意点 | 詳細 |
---|---|
1. 加工硬化への対応 | A5083は加工硬化しやすいため、切削条件を適切に設定し、熱がこもらないようにする必要があります。 |
2. 熱管理 | 切削中に発生する熱を適切に排出するため、冷却液や潤滑剤を十分に使用することが重要です。 |
3. 工具選定 | 耐摩耗性の高い硬質工具や、アルミ用コーティング工具を使用すると加工精度が向上します。 |
4. バリの発生対策 | 切削中にバリが発生しやすいため、工具の刃先を鋭利に保ち、適切な送り速度を設定します。 |
5. 素材の固定 | 剛性が不足すると振動が発生し、加工面に不具合が生じるため、しっかりと固定する必要があります。 |
6. 切削速度と送り速度 | アルミ専用の高回転設定で効率よく加工を行い、送り速度を適切に調整します。 |
7. 表面仕上げ | 良好な仕上げ面を得るために、仕上げ加工では高回転かつ低送りを設定し、仕上げ工具を使用します。 |
詳細情報:加工時の工夫
- 加工硬化対策
- 深切削を避け、複数回に分けて加工を行う。
- 工具を定期的に交換し、鋭利な刃先を維持。
- 冷却と潤滑
- 加工熱が素材に蓄積すると、寸法変化や表面性状に影響が出るため、冷却液を十分に供給する。
- 潤滑剤を使用して摩擦を軽減し、切削性を向上させる。
- バリ対策
- 工具の切れ味を保ち、送り速度を適切に調整することでバリを最小限に抑える。
- バリが発生した場合は、後処理としてデバリング工程を追加。
- 仕上げ精度の向上
- 最終仕上げにはダイヤモンド工具や高品質のエンドミルを使用する。
- 表面に傷がつかないよう、切削後の扱いにも注意。
旋盤チップの役割と種類
A5083用旋盤加工のコツ!最適なチップ選びとは?
旋盤チップは旋盤加工において欠かせない要素です。適切なチップを選ぶことは、作業効率や加工精度に大きな影響を与えます。なぜなら、チップの種類や素材によって、切削力や寿命が異なるからです。 例えば、A5083アルミニウム合金を加工する際には、耐摩耗性や熱伝導性が高いチップが最適です。このように、素材ごとに最適なチップを選ぶことが重要です。 さらに、加工する材料の硬度や形状によってもチップの選択が異なります。そのため、旋盤加工を行う際には、材料や加工条件に合ったチップを選ぶことが成功の鍵となります。適切なチップを選ぶことで、高品質な加工が可能となります。旋盤チップの種類と特徴
旋盤チップは、加工素材や目的に応じて適切な種類を選択することで、加工精度や効率を大幅に向上させることができます。以下は、主な旋盤チップの種類とその特徴をまとめたものです。主な旋盤チップの種類と特徴
種類 | 特徴 | 主な用途 |
---|---|---|
CVDコーティングチップ | 耐摩耗性が高く、高速切削や連続切削に適している。特に鋳鉄や鋼の加工で効果を発揮。 | 鋳鉄、鋼、耐熱合金の加工 |
PVDコーティングチップ | 硬度が高く、切れ味に優れる。仕上げ加工や複雑な形状の加工に適している。 | ステンレス鋼、非鉄金属の加工 |
超硬チップ | 高い硬度と耐摩耗性を持ち、幅広い材料に対応可能。高速切削や荒加工に最適。 | 鋼、ステンレス鋼、非鉄金属の荒加工 |
セラミックチップ | 高温下でも硬度を保持し、熱変形が少ない。仕上げ加工や耐熱材料の加工に向いている。 | 高硬度鋼、耐熱合金、鋳鉄の仕上げ加工 |
CBN(立方晶窒化ホウ素)チップ | 超硬合金よりも高い硬度を持ち、非常に硬い材料の加工に適している。高速切削にも対応。 | 焼入れ鋼、鋳鉄、粉末冶金材の加工 |
ダイヤモンドチップ | 最も硬い素材で、非常に高い耐摩耗性を持つ。非鉄金属やプラスチックの高精度仕上げに適している。 | アルミニウム、銅、プラスチック、炭素繊維の加工 |
詳細情報:各チップの利点と注意点
- CVDコーティングチップ
- 利点: 高い耐摩耗性により長寿命。
- 注意点: 衝撃に弱く、断続切削には不向き。
- PVDコーティングチップ
- 利点: 高い切れ味と幅広い素材対応。
- 注意点: 高速加工時にコーティングが剥がれやすい場合がある。
- 超硬チップ
- 利点: 汎用性が高く、加工条件の幅が広い。
- 注意点: 極端な高温環境では耐久性が低下する。
- セラミックチップ
- 利点: 耐熱性と耐摩耗性が高い。
- 注意点: 衝撃に非常に弱い。
- CBNチップ
- 利点: 焼入れ鋼など硬い材料に最適。
- 注意点: 非鉄金属や軟質材料の加工には適さない。
- ダイヤモンドチップ
- 利点: 非鉄金属や高精度仕上げに最適。
- 注意点: 高温環境や鉄系材料には使用できない。
チップの材質と用途
チップの材料は、旋盤加工において非常に重要です。適切なチップを選ぶことは、作業効率や加工精度に大きな影響を与えます。例えば、A5083というアルミニウム合金を旋盤加工する際には、適切なチップを選ぶことが重要です。 A5083は耐食性や溶接性に優れた素材であり、耐久性も要求されるため、チップの選択は慎重に行わなければなりません。適切な材料やコーティングを持つチップを使用することで、作業中の摩耗や熱への耐性を高めることができます。 つまり、A5083用旋盤加工においては、チップの材料やコーティングを適切に選ぶことがポイントです。正しいチップを選択することで、効率的かつ精密な加工が可能となります。加工の達人に聞いた!A5083旋盤加工のコツ
切削条件の最適化
A5083は高強度のアルミ合金で、耐食性と加工性が良いことから広く使用されていますが、旋盤加工時には特有の注意点があります。以下は、切削条件を最適化するためのポイントをまとめた内容です。切削条件 | 最適化のポイント | 理由 |
---|---|---|
切削速度 | 高速(200~500 m/min)で設定 | アルミは熱伝導性が高いため、高速切削でも熱が集中しにくい。切削面が滑らかになる。 |
送り速度 | 中速(0.1~0.3 mm/rev)を推奨 | 適切な送り速度を維持することで、切削熱を抑え、バリや加工変形を防ぐ。 |
切込み深さ | 小切込み(1~3 mm)から開始し、材料や目的に応じて調整 | 切削抵抗を抑え、仕上げ面の品質を向上させる。過剰な切込みは工具寿命を短くするリスクがある。 |
工具 | 超硬チップまたはPVDコーティングチップを使用 | アルミ特有の粘りや切りくずの付着を防ぎ、高精度な加工を実現する。 |
冷却と潤滑 | 水溶性クーラントを十分に供給 | 切削熱を抑え、工具寿命を延ばすだけでなく、表面仕上げを向上させる効果がある。 |
詳細情報:切削条件最適化の重要なポイント
- 切削速度の設定
- 高速切削が可能なアルミですが、工具の摩耗に注意。
- 工具寿命を延ばすため、加工中に速度調整を行うことが重要。
- 送り速度の調整
- 過度に速い送り速度は表面粗さを悪化させ、遅すぎると熱が集中する可能性がある。
- 切込み深さの選定
- 荒加工では切込みを深く、仕上げ加工では浅くすることで効率と精度を両立。
- 工具の選定
- 特にアルミ用の切削チップを選ぶことで、切りくずの排出性と加工面の美しさが向上。
- 冷却と潤滑の使用
- 冷却液を適切に供給することで、加工中の熱による変形や工具の過剰摩耗を防止。
チップの交換タイミング
チップの交換タイミングは、加工品質や効率に直結する重要なポイントです。チップが摩耗しすぎると精度が落ち、作業時間もかかってしまいます。逆に早すぎる交換も無駄なコストに繋がります。最適なタイミングは、チップの摩耗具合や加工条件によって異なります。加工中にチップの切れ味や状態を常にチェックし、摩耗が進んでいるようなら適切なタイミングで交換しましょう。例えば、A5083用旋盤での加工中に、チップの切れ味が鈍くなってきたら、すみやかに交換することが重要です。適切なチップ選びと交換タイミングを把握することで、効率的な加工が可能となります。長時間加工のための工夫
A5083用旋盤加工をする際、長時間加工するための工夫が重要です。最適なチップ選びが成功の鍵です。なぜなら、適切なチップを選ぶことで切削効率が向上し、作業効率が上がるからです。 理由は、A5083のようなアルミニウム合金は加工が難しい素材であり、適切な切削条件が必要です。例えば、チップの種類や形状、切削速度や切り込み量などが重要な要素となります。よく考えられた切削条件で作業を行うことで、加工精度が向上し、加工時間を短縮できます。 したがって、A5083用旋盤加工を行う際は、適切なチップを選んで切削条件を調整することが重要です。これによって効率的な加工が可能となります。旋盤加工トラブルシューティング
よくある加工トラブルとその対処法
旋盤加工では、作業効率や製品精度を低下させるさまざまなトラブルが発生する可能性があります。以下は、一般的なトラブルとその原因、対処法をまとめた表です。トラブル | 原因 | 対処法 |
---|---|---|
工具摩耗の増加 | – 不適切な切削速度や送り速度 | – 切削条件を見直し、適切な速度と送りに設定 |
– 冷却液や潤滑剤の不足 | – 十分な量の冷却液を供給 | |
– 工具材質が被加工材に適していない | – 対応する工具(超硬合金やコーティングチップ)に交換 | |
加工面の粗さが悪い | – 切削速度や送り速度が不適切 | – 送りを遅くし、切削速度を適切に調整 |
– 工具が摩耗している | – 工具を交換または再研磨 | |
– 被加工材の振動 | – 加工物をしっかりと固定し、振動を抑える | |
バリの発生が多い | – 過剰な切削速度や切込み深さ | – 切込みを適切に調整し、送り速度を安定させる |
– 工具の形状や切れ味の不良 | – 鋭利な工具に交換 | |
寸法精度のばらつき | – 被加工材の熱膨張 | – 冷却液を適切に使用し、加工中の温度上昇を抑える |
– 主軸のぶれまたは機械のガタつき | – 主軸と工具の調整を確認し、必要であれば修理 | |
切りくずの排出不良 | – 切削条件が適切でない | – 切削速度や送りを調整し、切りくずが詰まりにくい条件に設定 |
– 工具形状が被加工材に適合していない | – 溝や排出性に優れた工具を使用 |
詳細情報:主なトラブルへの対応のポイント
- 工具摩耗の抑制
- 冷却液の使用と切削速度の適切な設定が摩耗防止の鍵です。
- 特に硬い材料を加工する場合は、工具の材質選定を慎重に行います。
- 加工面粗さの改善
- 工具の取り付け精度や工具の状態を確認し、振動を最小限に抑える工夫が必要です。
- バリ対策
- 仕上げ加工用の切削条件を設定し、工具の刃先形状を適切に選びます。
- 加工後の仕上げ処理としてエッジ研磨を検討します。
- 寸法精度の向上
- 定期的な機械の点検を行い、振動やガタつきを防ぎます。
- 加工中の温度変化を抑え、環境管理を徹底します。
- 切りくず管理
- 切りくずの巻き付きを防止する工具形状を採用し、加工中の排出がスムーズになるよう設計します。
- 切削油を適切に使い、切りくずの滑りを良くする工夫をします。
A5083加工時の特有の問題点
アルミ合金A5083は高い強度と耐腐食性を持つ一方で、加工時には特有の問題が発生することがあります。以下は主な問題点とその原因、対策を表にまとめたものです。問題点 | 主な原因 | 対策 |
---|---|---|
切削面の粗さが悪い | – 材料の柔らかさと粘性 | – 高速切削に適した工具を使用 |
– 工具の摩耗または不適切な工具形状 | – 超硬工具やコーティング工具を選定し、摩耗時には交換 | |
バリの発生 | – 材料の柔らかさによる切りくずの巻き付き | – 鋭利な刃先の工具を使用し、切削速度を最適化 |
– 工具の取り付け角度が不適切 | – 適切な取り付け角度(正面切削の場合5°~15°程度)を設定 | |
加工中の変形 | – 高温による材料の熱膨張 | – 切削条件を調整し、冷却液を適切に使用 |
– 加工物の固定が不十分 | – しっかりとした治具を使用し、振動を抑制 | |
切りくずの排出不良 | – 切削条件が適切でない | – 切りくず排出性の高い工具を選定 |
– 切削油の供給不足 | – 冷却・潤滑性の高い切削油を十分に供給 | |
寸法精度のばらつき | – 温度変化による膨張 | – 加工環境を管理し、温度変化を最小限に抑える |
– 機械のガタつきや工具の振動 | – 定期的な機械点検と調整を実施 |
詳細情報:主な問題への対応のポイント
- 切削面の粗さ改善
- A5083の粘性に適応した高回転速度の工具を使用します。
- 摩耗した工具は早めに交換し、常に鋭利な状態を保つことが重要です。
- バリ対策
- 工具刃先の角度を適切に設定し、加工速度と送りを最適化します。
- 仕上げ加工の際に低速で丁寧に作業を行い、バリの発生を抑えます。
- 変形防止策
- 加工中の温度管理が重要で、冷却液の使用量を増やし、熱膨張を抑えます。
- 強固な固定治具を用いて、振動や変形のリスクを軽減します。
- 切りくず管理
- 切りくずの形状が加工に影響を与えやすいため、排出性の高い工具形状を選択します。
- 定期的な切削油の補充と供給状態の確認を行います。
- 寸法精度の確保
- 精密加工には、機械と工具の状態を頻繁にチェックし、微調整を実施します。
- 環境温度が安定した作業空間を確保することで、熱膨張の影響を最小限に抑えます。
トラブルを避けるためのチェックリスト
A5083の加工時にトラブルを避けるため、以下の項目を確認してください。加工開始前、加工中、加工後に分けて管理することで、効率的かつ安定した加工が可能になります。加工開始前のチェックリスト
項目 | チェック内容 | 状態 |
---|---|---|
工具の状態確認 | 工具が摩耗していないか、刃先が鋭利かを確認 | ☐ |
機械の設定確認 | 回転速度、送り速度、切削深さが適切かを確認 | ☐ |
材料の固定 | 加工物がしっかり固定され、振動しない状態になっているか | ☐ |
切削油の準備 | 適切な切削油が十分に供給される準備ができているか | ☐ |
加工プログラム確認 | 加工データが正確に入力され、編集ミスがないか確認 | ☐ |
加工中のチェックリスト
項目 | チェック内容 | 状態 |
---|---|---|
切削音の確認 | 異常な切削音や振動が発生していないか | ☐ |
切りくずの排出 | 切りくずがスムーズに排出されているか | ☐ |
工具温度の確認 | 工具が過熱していないか、冷却が十分かを確認 | ☐ |
寸法精度の中間確認 | 加工途中で寸法精度が確保されているかを確認 | ☐ |
加工後のチェックリスト
項目 | チェック内容 | 状態 |
---|---|---|
加工表面の仕上がり | 表面が滑らかでバリがないか確認 | ☐ |
寸法精度の最終確認 | 図面通りの寸法になっているか測定 | ☐ |
工具の状態 | 工具が摩耗していないか、次回使用可能な状態か確認 | ☐ |
機械のメンテナンス | 機械内部に切りくずが残っていないか清掃 | ☐ |
詳細情報:チェックリスト活用のポイント
- 一貫性を保つ
- 毎回の加工で同じ手順を繰り返し、トラブルの発生を抑制します。
- 記録の保持
- チェックリストに問題点や気付きを記録し、次回の作業に反映させます。
- 工具と機械の保守
- 定期的な工具交換と機械のメンテナンスを徹底します。
まとめとしてのチェックポイント
A5083加工における安定性と効率を確保するための重要なチェックポイントを以下にまとめました。チェックポイント一覧
- 工具の適正使用
- 摩耗した工具を使用しない。加工材に適した刃物を選定する。
- 加工条件の最適化
- 切削速度、送り速度、切削深さを材料特性に応じて設定する。
- 切削油の使用
- 適切な冷却と潤滑を確保し、工具寿命を延ばす。
- 材料の固定
- 加工物がしっかり固定され、振動や位置ずれを防ぐ。
- 寸法精度の中間確認
- 作業途中で寸法測定を行い、加工精度を維持する。
- 切りくず処理
- 切りくずが詰まらないように、定期的に除去する。
- 工具の温度管理
- 工具が過熱しないように冷却システムを活用する。
- 加工後の仕上げ確認
- バリや表面仕上げをチェックし、必要に応じて仕上げ工程を追加する。
- 定期的な機械メンテナンス
- 機械の清掃、点検を行い、長期的な安定稼働を実現する。
実行のポイント
- チェックリストを活用し、加工プロセスを標準化する。
- 定期的な記録と振り返りを行い、トラブルの原因を分析する。
- 加工環境全体を整えることで、安全かつ高精度な作業を確保する。
アルミニウム合金の基礎知識
アルミニウムの種類とその特性
A5083は、航空宇宙、自動車、建築など幅広い産業で使用される強靭なアルミニウム合金です。旋盤加工において、適切なチップの選択が重要です。なぜなら、正しいチップを選ぶことで、作業効率が向上し、品質の高い仕上がりを実現できるからです。例えば、A5083は熱処理されたアルミニウム合金であり、硬度が高いため、適切な切削条件やチップの材質が求められます。 したがって、A5083用旋盤加工を行う際には、チップの種類や切削速度、切削深さなどを慎重に検討することが重要です。適切なチップを選んで適切な切削条件を設定することで、効率的かつ安定した加工が可能となります。これにより、生産性向上や加工精度の向上が期待できます。A5083合金の特徴
A5083合金は、耐食性や溶接性に優れた特徴を持っています。この合金は船舶や航空機、自動車などさまざまな産業で幅広く使用されています。A5083合金は、軽量でありながら強度も兼ね備えているため、高い性能が求められる部品や構造物に理想的です。 旋盤加工において、最適なチップ選びは重要です。例えば、A5083合金を効率よく削るためには、適切なチップ形状や切削速度を選択する必要があります。また、切削油の適切な使用や冷却方法も加工品質に影響を与えます。 適切なチップ選びや工具の適切な取り扱いは、加工効率や品質向上につながります。A5083用旋盤加工を行う際には、これらのポイントに注意して作業を行うことで、より良い加工結果を得ることができます。A5052とA5083の比較
A5052とA5083は、どちらもアルミニウム合金であり、耐食性と加工性に優れた材料です。ただし、それぞれ特性や用途が異なります。以下に、化学成分、機械的性質、用途などを比較した表を示します。A5052とA5083の比較表
項目 | A5052 | A5083 |
---|---|---|
主な成分 | Mg: 2.2-2.8%、Cr: 0.15-0.35% | Mg: 4.0-4.9%、Mn: 0.4-1.0%、Cr: 0.05-0.25% |
耐食性 | 非常に高い | 特に海水や化学環境に強い |
強度 | 中程度 | 高強度 |
溶接性 | 優れる | 優れる |
成形性 | 非常に良好 | 良好 |
硬度 (HB) | 約60 | 約75 |
引張強度 (MPa) | 210-260 | 275-350 |
用途 | 車両、船舶部品、建材、電子機器など | 船舶、化学タンク、圧力容器など |
加工性 | 曲げや成形加工が容易 | 高剛性が求められる場合に適する |
詳細情報
- 化学成分
- A5052: マグネシウムとクロムを含む耐食性に優れた合金で、軽量かつ加工性に優れています。
- A5083: マグネシウム含有量が高く、海水や高塩分環境での使用に適しています。
- 耐食性 A5052もA5083も耐食性が高いですが、特にA5083は塩水や化学薬品に対して優れた耐久性を示します。
- 強度と硬度 A5083はA5052よりも高い引張強度と硬度を持ち、より負荷のかかる用途に適しています。
- 用途の違い
- A5052: 軽量かつ耐食性が必要な自動車部品や電子機器などに使用されます。
- A5083: 船舶や圧力容器など、高い剛性と耐久性が求められる用途で使用されます。
A5083旋盤加工の基本
A5083の加工性について
A5083は高い強度と耐食性を備えたアルミニウム合金ですが、加工性においては他の合金と比べていくつかの注意点があります。以下に、加工性の特性と加工時のポイントをまとめました。A5083の加工性に関する特性
項目 | 詳細 |
---|---|
成形加工性 | 中程度。薄板加工や曲げ加工には適しているが、過剰な変形には注意が必要。 |
切削加工性 | 他のアルミニウム合金(例:A6061)と比較するとやや難しい。 |
溶接性 | 優れており、特にTIG溶接やMIG溶接に適している。 |
表面仕上げ性 | 良好。研磨や仕上げ処理で高い光沢を得ることが可能。 |
加工硬化性 | 加工による硬化が発生しやすいため、加工後の特性変化に注意。 |
加工性に影響を与える要因
- 高いマグネシウム含有量
- 耐食性を向上させる反面、加工時の熱変形や切削面の仕上がりに影響を与える場合があります。
- 引張強度と硬度
- 引張強度が高いため、切削工具に負荷がかかりやすく、適切な切削条件を設定することが重要です。
- 熱伝導性
- 熱伝導性が高いため、加工時に発生する熱を効率よく管理する必要があります。
加工時の注意点
- 切削工具の選定
- 硬度が高いため、耐摩耗性に優れた切削工具(超硬工具など)を使用します。
- 切削刃の鋭利さを維持することで加工面の品質を向上させます。
- 切削条件の設定
- 低速から中速の切削速度を設定し、送り速度も適切に調整することで加工面の仕上がりを改善します。
- 冷却剤を十分に使用し、熱の蓄積を防ぎます。
- 曲げ加工
- 曲げ加工ではクラックの発生を防ぐため、適切な曲げ半径を設定します。
- 加工前に予熱を行うことで割れを防止します。
- 溶接加工
- 溶接部での強度を確保するため、適切な溶接方法とフィラー材を選択します。
旋盤加工の一般的な流れ
旋盤加工は、素材を回転させながら工具を使用して加工を行う工程です。以下は、旋盤加工の基本的な流れをまとめたものです。
一般的な旋盤加工の工程
工程 | 詳細 |
---|---|
1. 設計・図面作成 | 加工する部品の形状、寸法、公差などを設計し、図面を作成する。 |
2. 材料選定 | 加工に適した材料(例: 金属、樹脂など)を選定する。 |
3. 加工プログラム作成 | NC旋盤の場合、Gコードなどを使用して加工プログラムを作成する。 |
4. セットアップ | 素材をチャックに固定し、センター出しや芯合わせを行う。 |
5. 切削条件の設定 | 回転速度、送り速度、切削深さなどの条件を機械に設定する。 |
6. 荒加工 | 余分な材料を大まかに削り取り、形状の基礎を作る。 |
7. 中仕上げ加工 | 荒加工後の形状を整え、寸法を図面に近づける。 |
8. 仕上げ加工 | 表面を滑らかにし、寸法や形状を高精度で仕上げる。 |
9. 検査・測定 | 加工後の製品を測定し、設計図面と一致しているかを確認する。 |
10. 表面処理・仕上げ | 必要に応じて表面処理(研磨、塗装など)を施し、完成品に仕上げる。 |
旋盤加工の要点と注意点
- 素材の固定
- 素材がしっかりと固定されていないと加工精度が低下し、安全性が損なわれる可能性があります。
- チャックの締め付けや芯出しの精度を確認することが重要です。
- 切削条件の選定
- 回転速度や切削深さが適切でないと、加工面にバリや歪みが生じることがあります。
- 素材や工具に適した条件を選ぶ必要があります。
- 工具の選定と管理
- 工具の摩耗や刃の欠けは加工面に影響するため、定期的に工具を点検・交換します。
- 加工後の検査
- 加工した製品が設計図面の公差内に収まっているか、測定器具を使用して確認します。
A5083加工時の注意点
A5083は高強度で耐食性に優れたアルミ合金ですが、加工時に特有の性質を考慮する必要があります。以下に、加工時の注意点をまとめます。加工時の注意点一覧
注意点 | 詳細 |
---|---|
1. 加工硬化への対応 | A5083は加工硬化しやすいため、切削条件を適切に設定し、熱がこもらないようにする必要があります。 |
2. 熱管理 | 切削中に発生する熱を適切に排出するため、冷却液や潤滑剤を十分に使用することが重要です。 |
3. 工具選定 | 耐摩耗性の高い硬質工具や、アルミ用コーティング工具を使用すると加工精度が向上します。 |
4. バリの発生対策 | 切削中にバリが発生しやすいため、工具の刃先を鋭利に保ち、適切な送り速度を設定します。 |
5. 素材の固定 | 剛性が不足すると振動が発生し、加工面に不具合が生じるため、しっかりと固定する必要があります。 |
6. 切削速度と送り速度 | アルミ専用の高回転設定で効率よく加工を行い、送り速度を適切に調整します。 |
7. 表面仕上げ | 良好な仕上げ面を得るために、仕上げ加工では高回転かつ低送りを設定し、仕上げ工具を使用します。 |
詳細情報:加工時の工夫
- 加工硬化対策
- 深切削を避け、複数回に分けて加工を行う。
- 工具を定期的に交換し、鋭利な刃先を維持。
- 冷却と潤滑
- 加工熱が素材に蓄積すると、寸法変化や表面性状に影響が出るため、冷却液を十分に供給する。
- 潤滑剤を使用して摩擦を軽減し、切削性を向上させる。
- バリ対策
- 工具の切れ味を保ち、送り速度を適切に調整することでバリを最小限に抑える。
- バリが発生した場合は、後処理としてデバリング工程を追加。
- 仕上げ精度の向上
- 最終仕上げにはダイヤモンド工具や高品質のエンドミルを使用する。
- 表面に傷がつかないよう、切削後の扱いにも注意。
旋盤チップの役割と種類
A5083用旋盤加工のコツ!最適なチップ選びとは?
旋盤チップは旋盤加工において欠かせない要素です。適切なチップを選ぶことは、作業効率や加工精度に大きな影響を与えます。なぜなら、チップの種類や素材によって、切削力や寿命が異なるからです。 例えば、A5083アルミニウム合金を加工する際には、耐摩耗性や熱伝導性が高いチップが最適です。このように、素材ごとに最適なチップを選ぶことが重要です。 さらに、加工する材料の硬度や形状によってもチップの選択が異なります。そのため、旋盤加工を行う際には、材料や加工条件に合ったチップを選ぶことが成功の鍵となります。適切なチップを選ぶことで、高品質な加工が可能となります。旋盤チップの種類と特徴
旋盤チップは、加工素材や目的に応じて適切な種類を選択することで、加工精度や効率を大幅に向上させることができます。以下は、主な旋盤チップの種類とその特徴をまとめたものです。主な旋盤チップの種類と特徴
種類 | 特徴 | 主な用途 |
---|---|---|
CVDコーティングチップ | 耐摩耗性が高く、高速切削や連続切削に適している。特に鋳鉄や鋼の加工で効果を発揮。 | 鋳鉄、鋼、耐熱合金の加工 |
PVDコーティングチップ | 硬度が高く、切れ味に優れる。仕上げ加工や複雑な形状の加工に適している。 | ステンレス鋼、非鉄金属の加工 |
超硬チップ | 高い硬度と耐摩耗性を持ち、幅広い材料に対応可能。高速切削や荒加工に最適。 | 鋼、ステンレス鋼、非鉄金属の荒加工 |
セラミックチップ | 高温下でも硬度を保持し、熱変形が少ない。仕上げ加工や耐熱材料の加工に向いている。 | 高硬度鋼、耐熱合金、鋳鉄の仕上げ加工 |
CBN(立方晶窒化ホウ素)チップ | 超硬合金よりも高い硬度を持ち、非常に硬い材料の加工に適している。高速切削にも対応。 | 焼入れ鋼、鋳鉄、粉末冶金材の加工 |
ダイヤモンドチップ | 最も硬い素材で、非常に高い耐摩耗性を持つ。非鉄金属やプラスチックの高精度仕上げに適している。 | アルミニウム、銅、プラスチック、炭素繊維の加工 |
詳細情報:各チップの利点と注意点
- CVDコーティングチップ
- 利点: 高い耐摩耗性により長寿命。
- 注意点: 衝撃に弱く、断続切削には不向き。
- PVDコーティングチップ
- 利点: 高い切れ味と幅広い素材対応。
- 注意点: 高速加工時にコーティングが剥がれやすい場合がある。
- 超硬チップ
- 利点: 汎用性が高く、加工条件の幅が広い。
- 注意点: 極端な高温環境では耐久性が低下する。
- セラミックチップ
- 利点: 耐熱性と耐摩耗性が高い。
- 注意点: 衝撃に非常に弱い。
- CBNチップ
- 利点: 焼入れ鋼など硬い材料に最適。
- 注意点: 非鉄金属や軟質材料の加工には適さない。
- ダイヤモンドチップ
- 利点: 非鉄金属や高精度仕上げに最適。
- 注意点: 高温環境や鉄系材料には使用できない。
チップの材質と用途
チップの材料は、旋盤加工において非常に重要です。適切なチップを選ぶことは、作業効率や加工精度に大きな影響を与えます。例えば、A5083というアルミニウム合金を旋盤加工する際には、適切なチップを選ぶことが重要です。 A5083は耐食性や溶接性に優れた素材であり、耐久性も要求されるため、チップの選択は慎重に行わなければなりません。適切な材料やコーティングを持つチップを使用することで、作業中の摩耗や熱への耐性を高めることができます。 つまり、A5083用旋盤加工においては、チップの材料やコーティングを適切に選ぶことがポイントです。正しいチップを選択することで、効率的かつ精密な加工が可能となります。加工の達人に聞いた!A5083旋盤加工のコツ
切削条件の最適化
A5083は高強度のアルミ合金で、耐食性と加工性が良いことから広く使用されていますが、旋盤加工時には特有の注意点があります。以下は、切削条件を最適化するためのポイントをまとめた内容です。切削条件 | 最適化のポイント | 理由 |
---|---|---|
切削速度 | 高速(200~500 m/min)で設定 | アルミは熱伝導性が高いため、高速切削でも熱が集中しにくい。切削面が滑らかになる。 |
送り速度 | 中速(0.1~0.3 mm/rev)を推奨 | 適切な送り速度を維持することで、切削熱を抑え、バリや加工変形を防ぐ。 |
切込み深さ | 小切込み(1~3 mm)から開始し、材料や目的に応じて調整 | 切削抵抗を抑え、仕上げ面の品質を向上させる。過剰な切込みは工具寿命を短くするリスクがある。 |
工具 | 超硬チップまたはPVDコーティングチップを使用 | アルミ特有の粘りや切りくずの付着を防ぎ、高精度な加工を実現する。 |
冷却と潤滑 | 水溶性クーラントを十分に供給 | 切削熱を抑え、工具寿命を延ばすだけでなく、表面仕上げを向上させる効果がある。 |
詳細情報:切削条件最適化の重要なポイント
- 切削速度の設定
- 高速切削が可能なアルミですが、工具の摩耗に注意。
- 工具寿命を延ばすため、加工中に速度調整を行うことが重要。
- 送り速度の調整
- 過度に速い送り速度は表面粗さを悪化させ、遅すぎると熱が集中する可能性がある。
- 切込み深さの選定
- 荒加工では切込みを深く、仕上げ加工では浅くすることで効率と精度を両立。
- 工具の選定
- 特にアルミ用の切削チップを選ぶことで、切りくずの排出性と加工面の美しさが向上。
- 冷却と潤滑の使用
- 冷却液を適切に供給することで、加工中の熱による変形や工具の過剰摩耗を防止。
チップの交換タイミング
チップの交換タイミングは、加工品質や効率に直結する重要なポイントです。チップが摩耗しすぎると精度が落ち、作業時間もかかってしまいます。逆に早すぎる交換も無駄なコストに繋がります。最適なタイミングは、チップの摩耗具合や加工条件によって異なります。加工中にチップの切れ味や状態を常にチェックし、摩耗が進んでいるようなら適切なタイミングで交換しましょう。例えば、A5083用旋盤での加工中に、チップの切れ味が鈍くなってきたら、すみやかに交換することが重要です。適切なチップ選びと交換タイミングを把握することで、効率的な加工が可能となります。長時間加工のための工夫
A5083用旋盤加工をする際、長時間加工するための工夫が重要です。最適なチップ選びが成功の鍵です。なぜなら、適切なチップを選ぶことで切削効率が向上し、作業効率が上がるからです。 理由は、A5083のようなアルミニウム合金は加工が難しい素材であり、適切な切削条件が必要です。例えば、チップの種類や形状、切削速度や切り込み量などが重要な要素となります。よく考えられた切削条件で作業を行うことで、加工精度が向上し、加工時間を短縮できます。 したがって、A5083用旋盤加工を行う際は、適切なチップを選んで切削条件を調整することが重要です。これによって効率的な加工が可能となります。旋盤加工トラブルシューティング
よくある加工トラブルとその対処法
旋盤加工では、作業効率や製品精度を低下させるさまざまなトラブルが発生する可能性があります。以下は、一般的なトラブルとその原因、対処法をまとめた表です。トラブル | 原因 | 対処法 |
---|---|---|
工具摩耗の増加 | – 不適切な切削速度や送り速度 | – 切削条件を見直し、適切な速度と送りに設定 |
– 冷却液や潤滑剤の不足 | – 十分な量の冷却液を供給 | |
– 工具材質が被加工材に適していない | – 対応する工具(超硬合金やコーティングチップ)に交換 | |
加工面の粗さが悪い | – 切削速度や送り速度が不適切 | – 送りを遅くし、切削速度を適切に調整 |
– 工具が摩耗している | – 工具を交換または再研磨 | |
– 被加工材の振動 | – 加工物をしっかりと固定し、振動を抑える | |
バリの発生が多い | – 過剰な切削速度や切込み深さ | – 切込みを適切に調整し、送り速度を安定させる |
– 工具の形状や切れ味の不良 | – 鋭利な工具に交換 | |
寸法精度のばらつき | – 被加工材の熱膨張 | – 冷却液を適切に使用し、加工中の温度上昇を抑える |
– 主軸のぶれまたは機械のガタつき | – 主軸と工具の調整を確認し、必要であれば修理 | |
切りくずの排出不良 | – 切削条件が適切でない | – 切削速度や送りを調整し、切りくずが詰まりにくい条件に設定 |
– 工具形状が被加工材に適合していない | – 溝や排出性に優れた工具を使用 |
詳細情報:主なトラブルへの対応のポイント
- 工具摩耗の抑制
- 冷却液の使用と切削速度の適切な設定が摩耗防止の鍵です。
- 特に硬い材料を加工する場合は、工具の材質選定を慎重に行います。
- 加工面粗さの改善
- 工具の取り付け精度や工具の状態を確認し、振動を最小限に抑える工夫が必要です。
- バリ対策
- 仕上げ加工用の切削条件を設定し、工具の刃先形状を適切に選びます。
- 加工後の仕上げ処理としてエッジ研磨を検討します。
- 寸法精度の向上
- 定期的な機械の点検を行い、振動やガタつきを防ぎます。
- 加工中の温度変化を抑え、環境管理を徹底します。
- 切りくず管理
- 切りくずの巻き付きを防止する工具形状を採用し、加工中の排出がスムーズになるよう設計します。
- 切削油を適切に使い、切りくずの滑りを良くする工夫をします。
A5083加工時の特有の問題点
アルミ合金A5083は高い強度と耐腐食性を持つ一方で、加工時には特有の問題が発生することがあります。以下は主な問題点とその原因、対策を表にまとめたものです。問題点 | 主な原因 | 対策 |
---|---|---|
切削面の粗さが悪い | – 材料の柔らかさと粘性 | – 高速切削に適した工具を使用 |
– 工具の摩耗または不適切な工具形状 | – 超硬工具やコーティング工具を選定し、摩耗時には交換 | |
バリの発生 | – 材料の柔らかさによる切りくずの巻き付き | – 鋭利な刃先の工具を使用し、切削速度を最適化 |
– 工具の取り付け角度が不適切 | – 適切な取り付け角度(正面切削の場合5°~15°程度)を設定 | |
加工中の変形 | – 高温による材料の熱膨張 | – 切削条件を調整し、冷却液を適切に使用 |
– 加工物の固定が不十分 | – しっかりとした治具を使用し、振動を抑制 | |
切りくずの排出不良 | – 切削条件が適切でない | – 切りくず排出性の高い工具を選定 |
– 切削油の供給不足 | – 冷却・潤滑性の高い切削油を十分に供給 | |
寸法精度のばらつき | – 温度変化による膨張 | – 加工環境を管理し、温度変化を最小限に抑える |
– 機械のガタつきや工具の振動 | – 定期的な機械点検と調整を実施 |
詳細情報:主な問題への対応のポイント
- 切削面の粗さ改善
- A5083の粘性に適応した高回転速度の工具を使用します。
- 摩耗した工具は早めに交換し、常に鋭利な状態を保つことが重要です。
- バリ対策
- 工具刃先の角度を適切に設定し、加工速度と送りを最適化します。
- 仕上げ加工の際に低速で丁寧に作業を行い、バリの発生を抑えます。
- 変形防止策
- 加工中の温度管理が重要で、冷却液の使用量を増やし、熱膨張を抑えます。
- 強固な固定治具を用いて、振動や変形のリスクを軽減します。
- 切りくず管理
- 切りくずの形状が加工に影響を与えやすいため、排出性の高い工具形状を選択します。
- 定期的な切削油の補充と供給状態の確認を行います。
- 寸法精度の確保
- 精密加工には、機械と工具の状態を頻繁にチェックし、微調整を実施します。
- 環境温度が安定した作業空間を確保することで、熱膨張の影響を最小限に抑えます。
トラブルを避けるためのチェックリスト
A5083の加工時にトラブルを避けるため、以下の項目を確認してください。加工開始前、加工中、加工後に分けて管理することで、効率的かつ安定した加工が可能になります。加工開始前のチェックリスト
項目 | チェック内容 | 状態 |
---|---|---|
工具の状態確認 | 工具が摩耗していないか、刃先が鋭利かを確認 | ☐ |
機械の設定確認 | 回転速度、送り速度、切削深さが適切かを確認 | ☐ |
材料の固定 | 加工物がしっかり固定され、振動しない状態になっているか | ☐ |
切削油の準備 | 適切な切削油が十分に供給される準備ができているか | ☐ |
加工プログラム確認 | 加工データが正確に入力され、編集ミスがないか確認 | ☐ |
加工中のチェックリスト
項目 | チェック内容 | 状態 |
---|---|---|
切削音の確認 | 異常な切削音や振動が発生していないか | ☐ |
切りくずの排出 | 切りくずがスムーズに排出されているか | ☐ |
工具温度の確認 | 工具が過熱していないか、冷却が十分かを確認 | ☐ |
寸法精度の中間確認 | 加工途中で寸法精度が確保されているかを確認 | ☐ |
加工後のチェックリスト
項目 | チェック内容 | 状態 |
---|---|---|
加工表面の仕上がり | 表面が滑らかでバリがないか確認 | ☐ |
寸法精度の最終確認 | 図面通りの寸法になっているか測定 | ☐ |
工具の状態 | 工具が摩耗していないか、次回使用可能な状態か確認 | ☐ |
機械のメンテナンス | 機械内部に切りくずが残っていないか清掃 | ☐ |
詳細情報:チェックリスト活用のポイント
- 一貫性を保つ
- 毎回の加工で同じ手順を繰り返し、トラブルの発生を抑制します。
- 記録の保持
- チェックリストに問題点や気付きを記録し、次回の作業に反映させます。
- 工具と機械の保守
- 定期的な工具交換と機械のメンテナンスを徹底します。
まとめとしてのチェックポイント
A5083加工における安定性と効率を確保するための重要なチェックポイントを以下にまとめました。チェックポイント一覧
- 工具の適正使用
- 摩耗した工具を使用しない。加工材に適した刃物を選定する。
- 加工条件の最適化
- 切削速度、送り速度、切削深さを材料特性に応じて設定する。
- 切削油の使用
- 適切な冷却と潤滑を確保し、工具寿命を延ばす。
- 材料の固定
- 加工物がしっかり固定され、振動や位置ずれを防ぐ。
- 寸法精度の中間確認
- 作業途中で寸法測定を行い、加工精度を維持する。
- 切りくず処理
- 切りくずが詰まらないように、定期的に除去する。
- 工具の温度管理
- 工具が過熱しないように冷却システムを活用する。
- 加工後の仕上げ確認
- バリや表面仕上げをチェックし、必要に応じて仕上げ工程を追加する。
- 定期的な機械メンテナンス
- 機械の清掃、点検を行い、長期的な安定稼働を実現する。
実行のポイント
- チェックリストを活用し、加工プロセスを標準化する。
- 定期的な記録と振り返りを行い、トラブルの原因を分析する。
- 加工環境全体を整えることで、安全かつ高精度な作業を確保する。