「A2017」で旋盤加工する際の効率良い量産方法とは?
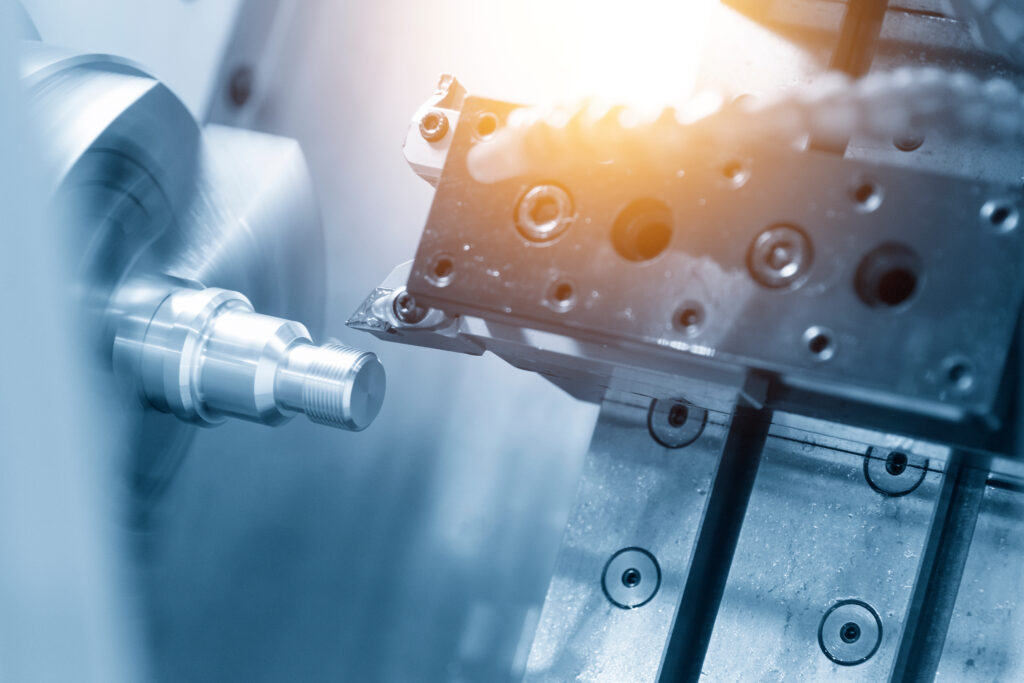
「A2017」を使用した旋盤加工を行う際、効率的な量産方法が何かご存知ですか?本記事では、A2017を使用した旋盤加工の量産における効率的な方法について詳しく解説していきます。旋盤加工や量産に興味がある方は、ぜひご一読ください。
1. 旋盤加工A2017量産の基本概要
「A2017」素材を用いた旋盤加工において、効率的な量産を実現するには、適切な工程設計が不可欠です。まず、A2017はアルミニウム合金であり加工性が良好であるため、量産に向いています。量産を効率化するためには、専用の治具を用いることで、位置決めの時間を大幅に短縮し、一貫した精度を維持することが可能です。また、CNC旋盤を活用することで、プログラムに従った自動加工が行え、手作業による誤差を削減し、同時に複数の工程を処理することができます。実際の事例としては、自動車産業や航空産業での部品製造において、A2017の量産が成功しており、これらの業界では時間とコストの削減が求められています。以上のように、専用治具の使用とCNC旋盤の活用を組み合わせることで、A2017の旋盤加工における効率的な量産が実現されます。
2. NC旋盤加工の基礎知識とA2017への応用
A2017での旋盤加工における効率的な量産方法は、正しい設備とプロセスの選定から始まります。旋盤加工に最適なA2017材料は、その軽量性と強度のバランスが良いため、自動車や航空機産業での需要が高まっています。量産を効率化するためには、まず適切なNC旋盤の選定が重要です。高精度な加工が可能で、かつ繰り返しの精度も維持できる機械を選びましょう。次に、加工プログラムの最適化を行い、無駄な動きを省き、切削時間を削減することが肝要です。例えば、工具の交換回数を減らすためにマルチタスク旋盤を使用することや、カットする工程をシンプルにして加工時間を短縮するといった方法があります。さらに、工具の管理を徹底し、摩耗による加工精度の低下を防ぐことも品質維持には不可欠です。これらの方法を総合的に活用することで、A2017の量産はより効率的となり、コスト削減にも繋がるでしょう。
3. A2017樹脂切削の試作・量産プロセス
旋盤加工におけるA2017使用時の効率的な量産方法は、工具の選定と加工パラメータの最適化にあります。A2017はアルミニウム合金の一種で、その特性を理解することは量産効率を向上させるために不可欠です。具体的には、耐熱性と耐摩耗性に優れた工具を選び、切削速度や送り速度などのパラメータを製品の形状や寸法精度に合わせて調整することが重要です。例えば、A2017の加工にはダイヤモンドコーティングされた工具が推奨され、これにより工具の寿命を延ばし加工精度を保つことができます。また、CNC旋盤を使用することで、一貫した品質の製品を効率よく生産することが可能です。最終的に、これらの措置を講じることでA2017の旋盤加工における量産効率は大幅に向上します。
4. A2017旋盤加工実例とその分析
A2017材料を用いた旋盤加工において効率的な量産を実現するには、工程の最適化が不可欠です。まず、A2017というアルミニウム合金は加工性が良いため、適切な切削条件の選定が重要となります。例えば、切削速度や送り速度、切り込み深さを工夫することで、加工時間の短縮と工具の摩耗を抑え、コスト削減に貢献します。また、専用の治具を用いることで、部品のセットアップ時間を最小限に抑えることができます。さらに、CAD/CAMシステムを活用し、加工プログラムの事前シミュレーションを行うことで、加工ミスを未然に防ぎ、無駄な材料のロスを減らすことが可能です。これらの手法を総合することで、A2017を用いた旋盤加工の量産は、より効率的かつ経済的に行えるのです。
5. 町工場におけるA2017金属切削加工の実践
A2017での旋盤加工において効率的な量産を達成するためには、適切な工具の選択、プログラムの最適化、そして適正な切削条件の設定が重要です。A2017合金は加工性が良く、自動車部品などに広く使用されているため、これらのポイントを抑えることで大量生産におけるコスト削減に繋がります。特に、工具の材質には耐摩耗性を持つものを選定することで、工具の交換頻度を低減し、連続加工時間を長く保つことが可能です。また、CNC旋盤などのプログラムを事前に作成し、試作を重ねることで、加工時間の短縮を図ることができます。適正な切削速度や送り速度を見極め、これを実践することで、A2017のような材料では旋盤加工の効率を格段に上げることができます。最後に、これらの工程を繰り返し行うことで、安定した品質の部品を迅速に供給する体制が整い、効率の良い量産が実現するのです。
6. 精密A2017旋盤加工技術の習得
A2017での旋盤加工において効率よく量産を行うためには、正確な工程管理と最適な工具の選定が重要です。まず、A2017はアルミニウム合金であり、熱伝導率が高いため加工時の発熱に注意を払い、冷却液の種類や量を適切に管理することが必要です。さらに、工具の耐久性と切削速度を考慮し、切れ味の良い超硬工具を選択することで、工具の交換頻度を減らし、生産効率を向上させることができます。実際の事例として、高精度を要求されるA2017の加工において、CNC旋盤を用いることで、プログラミングによる精密な加工が可能となり、結果として品質の均一性が保たれ、余計な手直しや材料の無駄が削減されます。よって、精密なA2017の量産には、適切な冷却管理、適切な工具選定、CNC旋盤の活用が効率化の鍵となります。
7. 旋盤加工A2017量産のためのトラブルシューティング
「A2017」を使用した旋盤加工の効率的な量産方法には、いくつかのポイントがあります。まず、A2017材はアルミ合金であるため、他の材料と比べて切削が容易な特徴を持っています。この利点を活かすためには、適切な切削工具の選定と切削条件の最適化が重要です。具体的には、高速度鋼や超硬合金などの耐摩耗性に優れた工具を選び、適切な送り速度と回転数を設定することで、加工精度を保ちつつ生産効率を高めることができます。また、自動化システムを導入することによって、人的ミスを減らし、連続生産を可能にし、さらに効率を上げることもできます。結論として、A2017の旋盤加工で量産を行う場合は、適切な工具の選択、切削条件の調整、自動化の導入が効率的な生産に不可欠であると言えます。この方法を取り入れることで、コスト削減と生産性の向上が期待できます。
8. A2017量産向け旋盤加工の最新技術動向
「A2017」での旋盤加工における量産方法は、コスト削減と効率化が可能です。これは、A2017材料の特性を理解し、適切なツール選定と加工パラメータの最適化によって実現されます。具体的な例として、多刃の切削工具を使用することで一度の加工での切削量を増やし、工数を削減する方法が挙げられます。また、CNC旋盤を活用した自動化は、人的ミスを減らし作業の一貫性を向上させるため、量産において非常に効果的です。さらに、工具の摩耗を定期的にチェックし、交換時期を見極めることで、常に安定した加工精度を保つことができるという利点もあります。このようにして、A2017材料を用いた旋盤加工の量産は、適切な技術選定と管理により、高効率かつ高品質な生産を実現することができます。
9. 旋盤加工A2017量産の経済性とROI
「A2017」を用いた旋盤加工での効率的な量産方法は、生産性の向上とコスト削減に大きく寄与します。まず、この方法の肝は、作業工程の標準化にあります。一つ一つの工程を明確にし、無駄な動作を省くことで、時間当たりの生産量が増え、時間とコストの節約につながります。次に、専用の治具を使用することも重要です。これにより、部品のセットアップ時間が短縮され、精度も向上します。また、A2017材の特性を熟知し、最適な切削条件を見極めることで、工具の摩耗を減らし、長期的なコスト削減に貢献します。例えば、切削速度や送り速度の最適化は、品質の一貫性を保ちつつ、合理的なサイクルタイムの実現を可能にします。これらの方法を統合することで、A2017を使った旋盤加工の量産は、経済性とROI(投資利益率)の双方において、顕著な改善を見せるのです。
10. A2017旋盤加工量産のための最適化戦略
A2017での旋盤加工において効率的な量産を実現するには、事前の計画と適切な工程管理が不可欠です。まず、量産を前提とした製品設計が重要であり、A2017の材質特性を考慮した上で、加工しやすく無駄のない設計にすることが肝要です。次に、装置の選定では、加工精度と生産性を両立させる高性能な旋盤を用いることが求められます。具体的には、複数の工具を同時に使えるマルチタスクマシンの導入や、自動工具交換システムを備えた機種を選ぶことで、作業時間の短縮と効率化を図れます。また、CAD/CAMシステムを活用して事前に加工プログラムを作成し、試作品を作成して最適な加工条件を見つけ出すことも重要です。最終的には、これらの準備を整えてから量産に移行することで、A2017を使用した旋盤加工の効率化と生産性の向上を実現できます。
まとめ
A2017を使用した旋盤加工の際には、材料の特性や工作機械の性能を考慮しながら効率的な量産方法を選択することが重要です。適切な切削速度や切削深さ、工具の選定などを工程に合わせて最適化することで、高品質な部品を効率よく生産することが可能となります。また、工程の見直しや自動化を取り入れることで作業効率を向上させることができます。